Extending the Life of Precision Components in Demanding Applications

Although bearings, gears, rollers, and other precision components are generally made of hardened steel or metal alloys, those utilized in high-load applications still can fail due to excessive wear, surface fatigue, pitting, galling, and corrosion.
This is exacerbated in applications with metal-to-metal interaction, repetitive friction at high speeds, or where little-to-no lubrication is present. Other factors include the presence of contaminants, the prevailing service temperatures, the loads applied, and loading modes such as sliding, rolling, oscillating, and pulsating.
To address this problem, product engineers and component manufacturers often turn to specialized PVD (physical vapor deposition) coatings that can be applied in thicknesses of 0.5 to 5 micrometers (µm) to further harden the surface of these parts.
By applying coatings optimized for these types of punishing environments, components benefit from increased surface hardness and a much lower coefficient of friction (COF). As a result, these critical parts do not have to be replaced as frequently, if at all, reducing maintenance and unplanned downtime, while improving machinery performance.
Today, these coated components are utilized for a variety of applications from performance automotive and racing to wind turbine shaft bearings and planetary gears; stainless steel cutting blades and piston pumps for food processing; and sliding components in filling and bottling operations. The coatings are also a proven technique for upgrading critical rotating parts in hydraulic drives, pumps, and valves.
Hardened Components and Alternative Coating Techniques
Many components are not coated at all. Instead, these parts are often made of heat-treated, nitrided or case-hardened steels, along with durable, high-performance materials such as titanium or nickel-based alloys. Even those used in high-load, high-wear applications are subject to wear and premature failure under poor lubrication. Some industries allow no lubrication at all, such as cryogenic and vacuum systems, clean rooms, food, and pharmaceutical equipment.
When this is the case, engineers often turn to a variety of coating, plating, or nitriding options to modify the surface to improve wear and corrosion resistance. Examples include coating the parts with black oxide. Black oxide is a coating produced by a chemical reaction between the iron on the surface of a ferrous metal and oxidizing salts. After a post-treatment with oil, the surface provides protection against corrosion, improved lubricity, and prevents galling during metal-to-metal interactions.
However, black oxide is not very durable and can be worn away quickly in repetitive, high-load applications.
PTFE (polytetrafluorethylene), another popular coating alternative, is known for its low coefficient of friction but is not recommended for high-load applications where it, too, can wear away.
Hard chrome and chemical nickel plating are often specified, as well, to provide protection against wear and corrosion. Although hard chrome is suitable for components that experience abrasive wear, micro-cracking inherent to the process limits its use against corrosion. Although this can be addressed with thin coatings that increase surface hardness, these solutions only offer limited wear resistance.
Chemical nickel can be applied over a range of hardnesses. However, the maximum is only 600 HV (Vickers pyramid number). Concerns over polluting compounds, emissions, or residues are also associated with these plating techniques.
Specialized PVD Coatings
Physical vapor deposition (PVD) describes a variety of vacuum deposition methods that can be used to produce thin coatings. PVD is typically used to coat components at relatively low coating temperatures of 200-500 °C. These temperatures are ideal because they are below the tempering temperature of steels so as to avoid altering the fundamental material properties.
Fortunately, there are several carbon-based coatings available that provide a unique combination of extreme surface hardness, low-friction coefficient and anti-corrosion properties like those provided by global coating provider Oerlikon Balzers.
According to Dr. Florian Rovere, Head of Product Line Service Components at Oerlikon, the company’s BALINIT® C coating is a WC/C ductile carbide-carbon coating that is highly resistant to adhesive wear (scuffing), in particular. It has a high load-bearing capacity, even under conditions of deficient lubrication or dry contact. Due to its low-friction coefficient, it acts to reduce pitting and fretting corrosion.
Another example is the BALINIT DLC coating, a metal-free, carbon-based coating that is even more durable. Applied through plasma-assisted chemical vapor deposition (PACVD), this coating is designed for more severe-wear conditions and high relative sliding speeds to protect against abrasion, scuffing, and cold welding.
These and other coatings within the BALINIT family that are tailored to specific requirements can be applied to a variety of case-hardened or tempered steels, austenitic stainless steel as well as nickel, titanium, copper, magnesium, and aluminium alloys.
“These materials provide an excellent combination of low coefficient of friction like PTFE, but with the hardness of a ceramic,” explains Rovere.
The coatings also have the advantage of being thin, typically 0.5-5 μm. This feature, in conjunction with close tolerancing, means that the component retains its form, fit, and dimensions after coating, without the need for re-machining.
Potential Applications
Bearings
Bearings often suffer from severe and disproportionately distributed abrasive wear. A coating such as BALINIT C is particularly suitable for case hardening, as well as ball- and roller-bearing steels because it can be applied at temperatures under 200 °C.
The PVD coating can be applied not only to inner and outer races and cylinders, but also to the balls in ball bearings in a highly uniform coating thickness of 0.5-1 μm. The slight increase in roughness is offset by the good burnishing qualities of the coating, which smooths the raceway of the inner and outer rings, providing additional protection against scuffing and pitting.
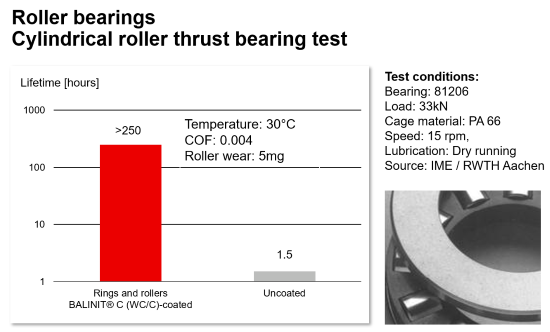
Bearings in the soft calendar rolls of paper machines frequently experience smearing. Not only does PVD coating reduce the possibility of smearing, but by making the bearings harder with coating, it has been shown that the life of these parts can be increased by a factor of three or four. As a result, paper mills are able to hold off on bearing replacement until the calendar roll needs regrinding, significantly reducing costly production downtime.
Similarly, cylindrical roller bearings in compressors are often exposed to low loads and vibrations, causing potential smearing. Applying PVD coating to the bearings removes any such possibility.
Gears
Gears experience similar wear conditions. The PVD coating significantly reduces scuffing and pitting in gear as well. In fact, BALINIT C has been shown to quadruple the service life of high-speed gears.
The standard FZG C test shows that the fatigue strength is increased by 10-15% over case-hardened but uncoated gears. In the test, the failure criterion for gear service life was defined as single-tooth wear of 4% due to pitting.
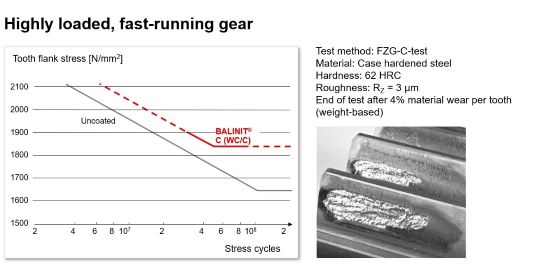
The main factors in these improved figures were the lower local surface pressure (Hertzian pressure), which resulted from reduced friction in the rolling contact, and the superior running-in behaviour of BALINIT C.
Coatings can also benefit worm gears, where lubrication is not always enough to protect helical-gear transmissions against friction and wear. The sliding motion and the force between the worm and gear faces make it difficult for a lubricant film to form. For this reason, the gear is most often made of bronze in order to avoid scuffing.
In service, however, the teeth of the bronze gear wear away quickly and the gear must be realigned or replaced. Coating the steel worm with a carbon-based coating can improve reliability and performance by reducing wear on both the worm and the bronze gear.
Pumps, Compressors
Screw spindle-, vane-, gear-, lobe- and centrifugal pumps often function in abrasive and poorly lubricating media. This may be cooling media in grinding machines such as screw pumps and internal gear pumps. BALINIT-coated screws provide the ideal combination of hardness and low friction for preventing wear in such poorly lubricated conditions.
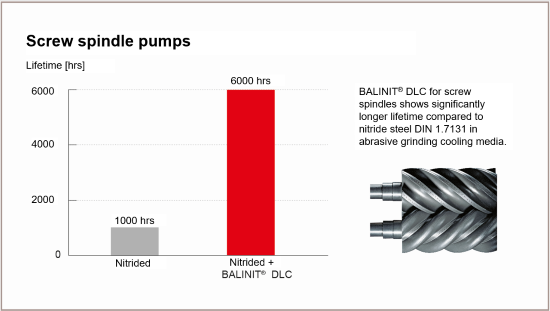
Similarly, industrial compressor components, such as reciprocating pistons, screws, or valve plates can undergo extensive wear when oil-free operation, dry gases, refrigerants, high or low temperature limit the use of lubricants.
Customized Solutions
Coating solutions can be tailored to meet unique requirements. In addition to coating thickness and hardness, properties such as structure, chemical and temperature resistance, and adhesion can be precisely controlled.
In most cases, no alteration of the formula for the coatings is required, as it is already optimized for high-load, high-friction environments. “I find engineers are most surprised about two factors when learning about these specialized PVD coatings,” says Rovere. First, that the coating can be applied in a thickness as low as 0.5 or 1 micrometers. The other is that these coatings can last the lifetime of the machine or systems they are in, despite the difficult operating conditions.”
For more information about coating solutions for components with Oerlikon Balzers, e-mail: balzers.components@oerlikon.com; or visit www.oerlikon.com/balzers.
Looking for a reprint of this article?
From high-res PDFs to custom plaques, order your copy today!