Extending the Life of Bell Cups
In a typical automotive plant, bell cups must be replaced every three to four months. As a result, an automotive plant using 50 rotary bell atomizers might incur replacement costs for bell cups totaling approximately $300,000 per year. An advanced coating technology can extend the life of paint bell cups and offer a dramatic cost savings for rotary paint atomizer users.
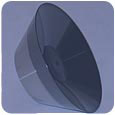
It’s not often that an equipment investment produces a payback in six months, with direct cost savings amounting to more than 20 times the initial expenditure. But these are the results that a space-age ceramic coating for paint bell atomizers is achieving for Ford Motor Co.
Paint rotary bell atomizers have been improved over the last two decades, but the abrasive wear to the bell cups has been a lingering technical problem. With the introduction of high-solids metallic paint technologies and mica flakes to achieve brighter colors and shimmering, reflective surfaces, the useful life of bell cups has been shortened even further. It is well known and documented throughout the coatings industry that highly pigmented and aluminum-containing surface coatings are extremely aggressive on painting equipment.
In a typical automotive plant, bell cups must be replaced every three to four months. As a result, an automotive plant using 50 rotary bell atomizers might incur replacement costs for bell cups totaling approximately $300,000 per year. Moreover, bell cup failure occurs unpredictably, ruining the part’s paint finish and causing the waste of 150-200 parts per year. In addition, the process of changing the bell cups causes costly production downtime.
The key technical challenge was to find a new bell cup coating that would extend the useful life of the bell cup without causing any detrimental impact on the performance of the rotary paint atomizer.
The negative electrostatic charge helps attract the paint to the workpiece, which is grounded or positively charged. An additional effect of the negative electrostatic charge of the paint particles is that it causes further atomization, as the charged particles repel each other to form an even finer cloud of spray.
The high transfer efficiency of the fine, electrostatically charged spray results in paint savings of 30 to 40% over electrostatic spray guns, and the cycle time for painting each workpiece is shortened. Rotary atomizers also enable a reduction in compressed air usage of more than 20%.
In addition, the high transfer efficiency of rotary atomizers ensures excellent quality and consistent results. The environment also benefits because of the reduced paint consumption and lowered volatile organic compound (VOC) emissions.
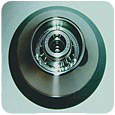
Ford Global Paint Engineering and Ford Scientific Research Laboratories, divisions of Ford Motor Co., took on the challenge of locating and testing a low-cost, durable surface coating that would not degrade over time, reduce overall transfer efficiency, compromise customer quality or impair the mechanical functionality of the paint equipment.
The laboratories investigated the use of silicon doped amorphous carbon surface coating, a material patented by Ford. With near-diamond hardness and the conductivity of the base metal, this material proved to be ideally suited to the paint bell cup application.
The Diamonex Products Division of Morgan Advanced Ceramics worked with the Ford laboratories to enhance the coating and application processes. Morgan Advanced Ceramics applies the material with its patented plasma chemical vapor deposition (CVD) process to achieve a consistent 3-micron-thick coating that does not interfere with the mechanical or electrostatic functions of the original equipment.
The coating has resulted in a significant decrease in expenditures on replacement bell cups. Ford has also documented direct improvements in painting process uniformity and vehicle quality (measured by Ford as an increase in FTT, or “First Time Through,” and a reduction in TGW, or “Things Gone Wrong”), as well as reductions in the maintenance costs relating to paint bell cups.
Ford has teamed up with Morgan Advanced Ceramics to make the ceramic coating available to original equipment manufacturers and rotary paint atomizer users. While the coating represents a slightly higher initial investment, adding 15 to 25% to the cost of a new bell cup, it can extend the life of bell cups more than 1,000% - a return on investment that is hard to match.
For more information about the new ceramic coating, call 800.433.0638, e-mail ussales@morganadvancedceramics.com or visit www.morganadvancedceramics.com.
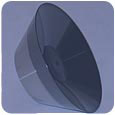
It’s not often that an equipment investment produces a payback in six months, with direct cost savings amounting to more than 20 times the initial expenditure. But these are the results that a space-age ceramic coating for paint bell atomizers is achieving for Ford Motor Co.
Paint rotary bell atomizers have been improved over the last two decades, but the abrasive wear to the bell cups has been a lingering technical problem. With the introduction of high-solids metallic paint technologies and mica flakes to achieve brighter colors and shimmering, reflective surfaces, the useful life of bell cups has been shortened even further. It is well known and documented throughout the coatings industry that highly pigmented and aluminum-containing surface coatings are extremely aggressive on painting equipment.
In a typical automotive plant, bell cups must be replaced every three to four months. As a result, an automotive plant using 50 rotary bell atomizers might incur replacement costs for bell cups totaling approximately $300,000 per year. Moreover, bell cup failure occurs unpredictably, ruining the part’s paint finish and causing the waste of 150-200 parts per year. In addition, the process of changing the bell cups causes costly production downtime.
The key technical challenge was to find a new bell cup coating that would extend the useful life of the bell cup without causing any detrimental impact on the performance of the rotary paint atomizer.
Rotary Paint Atomizer Performance
Rotary atomizers are designed to maximize transfer efficiency, which measures the percentage of paint that ends up on the workpiece. The paint enters from the back of the bell, transfers to the wall of the bell and is electrostatically charged prior to being atomized at the edge of the spinning bell cup. The high speeds of the turbine-driven bell (spinning at 25,000 to 60,000 rpm) particulate the paint into a fine, uniform spray. Typically, titanium bell cups are used for waterborne and powder slurries, and aluminum is used for clearcoats.The negative electrostatic charge helps attract the paint to the workpiece, which is grounded or positively charged. An additional effect of the negative electrostatic charge of the paint particles is that it causes further atomization, as the charged particles repel each other to form an even finer cloud of spray.
The high transfer efficiency of the fine, electrostatically charged spray results in paint savings of 30 to 40% over electrostatic spray guns, and the cycle time for painting each workpiece is shortened. Rotary atomizers also enable a reduction in compressed air usage of more than 20%.
In addition, the high transfer efficiency of rotary atomizers ensures excellent quality and consistent results. The environment also benefits because of the reduced paint consumption and lowered volatile organic compound (VOC) emissions.
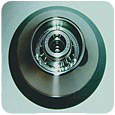
The ceramic coating protects the bell cup, even with today’s most abrasive paints.
A Space-Age Ceramic Solution
Many tribological and surface coating solutions have been tested in an effort to improve bell cup life, but all have met with limited success. The surface coatings have degraded quickly, reduced the transfer efficiency or impaired the mechanical function of the rotary atomizers.Ford Global Paint Engineering and Ford Scientific Research Laboratories, divisions of Ford Motor Co., took on the challenge of locating and testing a low-cost, durable surface coating that would not degrade over time, reduce overall transfer efficiency, compromise customer quality or impair the mechanical functionality of the paint equipment.
The laboratories investigated the use of silicon doped amorphous carbon surface coating, a material patented by Ford. With near-diamond hardness and the conductivity of the base metal, this material proved to be ideally suited to the paint bell cup application.
The Diamonex Products Division of Morgan Advanced Ceramics worked with the Ford laboratories to enhance the coating and application processes. Morgan Advanced Ceramics applies the material with its patented plasma chemical vapor deposition (CVD) process to achieve a consistent 3-micron-thick coating that does not interfere with the mechanical or electrostatic functions of the original equipment.
Dramatic Cost Savings
The success of the silicon-doped amorphous carbon surface coating has exceeded all expectations, extending the life of the atomizers almost indefinitely. Ford still has one of the original bell cups in production, and it has been in continuous and trouble-free use for more than five years. The coating protects the bell cup, even with today’s most abrasive paints.The coating has resulted in a significant decrease in expenditures on replacement bell cups. Ford has also documented direct improvements in painting process uniformity and vehicle quality (measured by Ford as an increase in FTT, or “First Time Through,” and a reduction in TGW, or “Things Gone Wrong”), as well as reductions in the maintenance costs relating to paint bell cups.
Ford has teamed up with Morgan Advanced Ceramics to make the ceramic coating available to original equipment manufacturers and rotary paint atomizer users. While the coating represents a slightly higher initial investment, adding 15 to 25% to the cost of a new bell cup, it can extend the life of bell cups more than 1,000% - a return on investment that is hard to match.
For more information about the new ceramic coating, call 800.433.0638, e-mail ussales@morganadvancedceramics.com or visit www.morganadvancedceramics.com.
Looking for a reprint of this article?
From high-res PDFs to custom plaques, order your copy today!