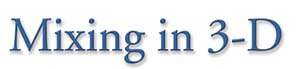
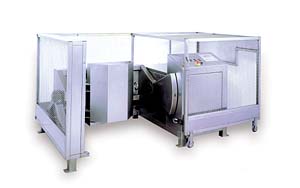
Recently, a new mixer* has become available to the North American market that promises to change the way the mixing process is accomplished. The mixer rotates the material on three separate axes, reducing mixing times and resulting in a superior blend. It can handle any size or shape of container, and its fully programmable operation allows mixing to be customized for each product. With the new mixer, manufacturers can quickly and thoroughly mix a wide variety of materials.
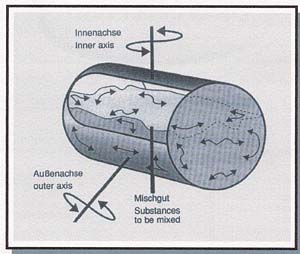
Principle of Operation
The new mixer is based on the same operation principle as a gravity mixer, in which the mixing vessel circulates around one axis to achieve a mix that is often referred to as “free-falling.” Designed primarily for free-flowing formulations, gravity mixers use the force of gravity, rather than an external mechanism, to pull and blend the mix.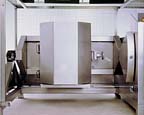

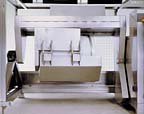
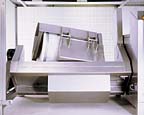
Customized Mixing
In addition to its optimized mixing design and flexibility, the new mixer is also fully programmable. The user programs the rotating speed of both axes into an operating panel, which is affixed to the machine. The mixing action can be customized for each product by adjusting the speed, direction and time on each individual axis, and these predetermined parameters help develop the optimal mixing program for each product. For example, products that tend to agglomerate can undergo a high speed process, while very sensitive products or viscous blends might only be subjected to a gentle cycle.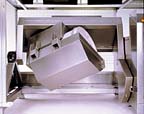
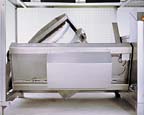

Automated Material Handling
For manufacturers who regularly handle large, heavy batches of material, the new mixer can also be equipped with an automatic lifting scaffold to enable the mixing containers to be changed within a short period of time and with minimal effort (see Figure 4). The user simply transports the mixing container to the mixer using a wagon or lift truck and places it into the scaffold. With the touch of a button, the scaffold lifts the container into the mixer and locks it into place, ready for the mixing process to begin. After the mixing cycle is complete, the scaffold automatically moves the vessel into its final position in the holder, and the holder descends and places the vessel on the ground or on a wheeled base. The container can then be moved manually or automatically for further processing.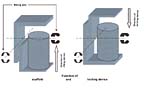
Enhanced Mixing Efficiency
Due to its versatile nature, the new mixer can be used to enhance mixing capabilities in a variety of applications. Available in sizes ranging from 50-1200 liters, the mixer is primarily designed to mix solids, such as pigments, metals and oxides, with different sizes, shapes, densities and flow characteristics. However, it can also successfully handle emulsions (liquid-liquid) and dry powder or granulates mixed with a small amount of water, thin liquid oils or solvents, as long as the product on the whole remains dry. The system’s intense mixing action and atomization capabilities ensure that the product is moistened homogeneously, making it useful for chemical additives, dopants and other dry-liquid applications (see Figure 5).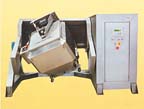
For more information about mixers, contact Leslie Horn at Glen Mills Inc., 395 Allwood Rd., Clifton, NJ 07012; phone 973/777.0777; fax 973/777.0070; e-mail leslie@glenmills.com; or visit www.glenmills.com.