A Major Breakthrough in Corrosion Resistance for Automobiles
The goals in electrocoat development are technological innovation that offers improved corrosion resistance, greater environmental protection (and the consequent compliance with environmental regulations) and greater economy. Specifically, achieving these goals requires improving corrosion resistance along the edges of body components, optimizing material consumption, increasing efficiency in the application process, and reducing solvent content and emission of volatile organic compounds (VOCs). Moreover, the entire painting process demands a material that has optimum performance and application properties, including excellent flow characteristics.
A Major Breakthrough in Electrocoat
With the introduction of the CathoGuard 500 line, we have achieved a major breakthrough in our quest for an electrocoat that meets these objectives. By designing a pigment gradient into the baked electrocoat film, BASF technicians have enabled defined rheological properties to be utilized in different ways at various depths of the film. Defining the rheology of the material in a very precise manner allows an optimal, uniform coating layer to be produced, even at such critical locations as very sharp edges. In addition, the flow characteristics of the electrocoat have been optimized in the CathoGuard 500 line. This combination of previously incompatible properties makes it possible, for the first time, to obtain both good corrosion resistance and outstanding surface quality. Equally important, the CathoGuard 500 technology line also ensures first-rate throwing power - in other words, the ability to deliver optimal coating in interior regions of the vehicle body.From an environmental standpoint, the new CathoGuard 500 technology line of cathodic electrocoat materials is not only lead-free, but also meets U.S. standards for hazardous air pollutants (HAPs). In addition, solvent content has been further reduced compared to existing technologies.
With this technology line, we offer a series of cutting-edge, lead-free electrocoat products that deliver a combination of advanced technology, environmental protection and economy that was not previously available. In addition to the base version, the line also contains the tin-free variant CathoGuard 520, as well as CathoGuard 560 as a future low-bake solution (with an underbake tolerance down to 150 ºC/302 ºF).
Early Developments
Coating automotive bodies and other industrial products using an immersion process is one of the oldest known coating methods. The process is easy to automate, and material yield is high. Emissions are low, and since the introduction of ultrafiltration, material utilization efficiency is excellent (> 99%), which makes electrocoating very environmentally friendly.Intensive work on developing commercial electrocoats began in the late 1950s at Ford Motor Company in the United States. In Europe, the first electrodeposition coatings were commercialized in 1963, using the anodic process. Anodic electrocoating, in which the object that is to be coated is connected to a positive electrical potential, uses acrylates, epoxy polyesters and polybutadiene oils as the base resins.
Cathodic electrodeposition systems, based on epoxies and polyurethanes, were developed in parallel. In 1971, the first small-part tanks were used in general industrial applications. Before long, the process was also adopted in the automotive industry. Today, cathodic electrocoating is considered to be the more modern process, based on a technology that delivers better quality. Early cathodic electrocoats, however, contained significant amounts of toxic metals such as lead and, in some cases, strontium. Moreover, the bath typically contained 3 to 5 percent solvent - usually one of the glycol ethers, which are considered a health risk. For reasons of paint stabilization, and to achieve reliable corrosion protection, the products generally required an ultrafiltration drain and a final rinse with de-ionized water, as well as a chrome-containing passivation re-rinse as a pretreatment step.
State of the Art
Current cathodic electrocoats have the following individual environmental advantages.- No lead pigment (in compliance with European Union Directive, effective July, 2005).
- No toxic solvents (such as glycol ethers).
- No use of HAP compounds (as defined by the U.S. EPA's hazardous air pollutants list).
- Low solvent content: < 1% in bath (VOC < 0.6 lbs/gal).
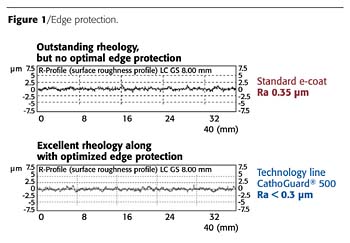
'Throwing Power' as a Measure of Quality
The increasing electrical resistance that occurs as the coating layer builds up, along with the reduced current flow, causes the thickness of the electrocoat layers to first build up uniformly on the outer surfaces of the body. After the specified layer thickness has been reached, the electrical flux lines migrate into the interior spaces and cavities. Although electrical currents always follow the path of least resistance, this path can also be relatively long. Coating deposition does not stop until the electrical resistance of the bath becomes too high to achieve an adequate current density."Throwing power" refers to the ability to establish a resistance on the exterior of the part in such a way that the flux lines are forced to "migrate" into the interior and, thus, ensure that the interior areas can be coated. Among other things, throwing power is an indicator of the quality and efficiency of an electrocoat material.
The main purpose of cathodic electrocoating in the automotive industry is to provide reliable and long-lasting corrosion resistance on exterior and interior body surfaces. Modern electrocoat materials ensure good corrosion resistance at a layer thickness as low as 8 to 10 µm. However, in order to achieve this value in cavities and on interior surfaces that have complicated geometries, a thickness of 20 to 22 µm must have been deposited on the exterior surfaces before the coating begins to migrate into the interior (Figure 1). This is because - for process-related reasons - the coating is not deposited uniformly on interior surfaces, but rather as a "wedge" that is represented by a mathematical function of electrical resistance and current flow. Therefore, precisely defined hole configurations (hole patterns and gaps) must be provided in the design so that the flux lines can penetrate into the interior in a predictable manner and to ensure a better deposition of film on the interior surfaces.
The present goal, therefore, is to reduce exterior film deposition - and, consequently, material consumption - without reducing interior deposition in cavities, and without affecting corrosion resistance along edges. The CathoGuard 500 technology line achieves precisely this goal.
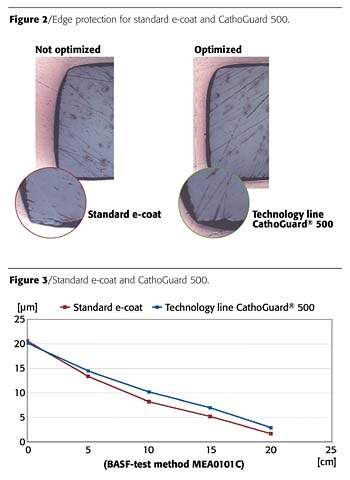
Balancing Good Edge Coating and Optimal Surface Flow
Corrosion resistance on automotive bodies is defined by two functional areas: surface corrosion resistance and edge corrosion resistance. Today, homogeneous body surfaces no longer constitute a significant challenge for the coating process, but, before the development of CathoGuard 500 technology, edge coating still needed to be optimized further (Figures 2 and 3).In cathodic electrocoating, the flux lines preferably are concentrated at edges and ridges. In the subsequent baking process, the film changes rheologically, becoming less viscous and drawing away from the edges.
The flowing, leveling, and solidification of the surface structure are further important functions of the coating. In order to achieve an adequate surface texture on the object that is to be protected, the electrocoat material must be able to compensate for small "irregularities," sand scratches, etc., and smooth them out and generally improve the quality of the surface (as indicated by a low surface roughness value). For this reason, paint formulations are designed to be "flowable."
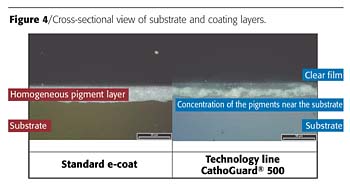
No More Balancing Required
The previous state-of-the-art electrocoating technology did not allow simultaneous achievement of edge protection and optimal flow, since the rheological properties of the coating had to be optimized for either one goal or the other.Once BASF Coatings was able to remove the lead pigment from the cathodic electrocoat and to have the resin system itself take over the corrosion-resistance properties, a new degree of freedom became available. Now, the pigments can be used to modify the rheology of the deposited but not-yet-baked film. With the CathoGuard 500 technology line, it became possible to concentrate the pigments along the substrate surface and to greatly reduce their presence near the surface of the paint film - in other words to keep this plane free of pigments (Figure 4). This results in optimal flow, while at the same time the tendency of the paint to pull away from edges is prevented at the substrate. Thus, for the first time, edge protection and good flow can be achieved simultaneously.
The combination of performance characteristics that previously were mutually exclusive is setting new standards in automotive painting. State-of-the-art CathoGuard 500 systems are helping to meet the crucial challenges facing the modern automobile industry. They truly constitute a new generation of electrocoat technology.
Looking for a reprint of this article?
From high-res PDFs to custom plaques, order your copy today!