Improved Corrosion Resistance in Powder Coatings
via Microencapsulated Self-Healing Agents

Judging from the amount of research activity spawned in academia, and efforts in industry since White et al. reported the first self-healing polymeric material system,1 there is little doubt that designers of novel polymeric materials find the potential of self-healing functionality intriguing. In White’s system, microencapsulated dicyclopentadiene (DCPD) and Grubbs’ catalyst particles were embedded into a bisphenol-A/epichlorohydrin epoxy resin (EPON 828) cured with diethylenetriamine. Damage to the cured resin ruptured the microcapsules, releasing the DCPD into the site of damage, where upon contact with the catalyst, a ring opening metathesis polymerization was initiated, restoring structural continuity to the polymerized resin. With a view towards increasing compatibility with other polymer matrix materials, decreasing cost and minimizing toxicity, White and others have developed additional self-healing chemistries based on condensation and addition polymerization of silicone resins,2-4 epoxy resin chemistry,4,5 reaction of isocyanates,6 and free-radical-initiated polymerization of acrylates,7 to cite a few examples.
Although some of the academic research in the area of self-healing materials has moved on towards other approaches such as designing self-healing functionality into materials via microvascular networks or leveraging supramolecular interactions,3 microcapsules remain the most viable option where protective coatings are concerned. Unlike the use of microvascular networks or supramolecular functionality that might require the design of completely new classes of resins or fundamentally change the way coatings are designed, manufactured and applied, microcapsules can be incorporated into a coating with minimal adjustments to the batch-making process.
Protective coatings for metal substrates stand to benefit significantly from microcapsule-based self-healing chemistries as part of an improved anticorrosion solution. Although protective coating performance continues to improve via the design of more effective resins, pigments, additives and improved formulation techniques, a major challenge to the performance of protective coatings is the exposure of the substrate after damage. Once exposed, the substrate succumbs to corrosion at the exposed site and creep at the coating substrate interface, compromising the coating’s ability to protect the underlying substrate. The benefit of self-healing functionality in a coating was evident in the use of hexavalent chromium-based additives as anticorrosion pigments in protective coatings. When such coatings were damaged in service, the hexavalent chromium leached out of the coating into the site of damage where it was reduced to form a new trivalent chromium oxide layer, which passivated the damaged area and delayed the corrosion of the underlying metal substrate.8 With the prohibition of the use of hexavalent chromium compounds in many applications due to their toxicity and carcinogenicity, the most widely used protective coatings can no longer call on the benefit of the functional response it affords for corrosion resistance.
As part of a solution that includes improvement in standard binder, pigment and additive technologies, novel microcapsule-based self-healing systems have the potential to fill the void left by the phasing out of hexavalent chromium additives, and a number of chemistries have been evaluated to this end. However, much of the reported efforts toward adopting self-healing technologies in protective coatings have focused on liquid coatings. Examples of these efforts include the use of polydimethylsiloxane (PDMS)9,10 and isocyanate-based chemistries.11,12 Very little work however has been reported on efforts toward designing self-healing functionality into powder coatings.
Growing at an annual rate of 7.6%,13 powder coatings represent an increasingly significant segment of the protective coatings market. Like liquid coatings, the performance of protective powder coatings depends on their ability to remain undamaged on the substrate they protect. Upon damage, however, the underlying substrate is exposed to the environment. Once exposed, the onset of corrosion processes on the substrate can be rapid, and the propagation of corrosion at the coating-substrate interface can significantly compromise the coating’s adhesion to the substrate and its ability to protect it. As such, like liquid coatings, powder coatings stand to benefit from microcapsule-based self-healing technologies and their potential to add self-healing functionality to the corrosion-resistance mechanism of the coating.
Microencapsulated Healing Agents for Powder Coatings
The design of powder coatings with self-healing functionality based on microencapsulated healing agents presents a different set of challenges than liquid coatings due to the nature of their application and curing processes. For starters, although microcapsules can be made to be quite robust, the mechanical properties required for microcapsules to survive the typical extrusion and milling processes associated with the preparation of powder coatings and those required for microcapsules to be readily ruptured in response to damage to the coating are likely mutually exclusive. As such, formulations incorporating microencapsulated healing agents must account for addition of the microcapsules at a later stage via dry blending or co-fluidization processes. Secondly, precisely because dry blending or co-fluidization is likely the most effective method for the incorporation of microcapsules into powder coatings, the shell wall of the microcapsules must be fairly rigid, as softer shell walls may promote agglomeration via coalescence and sintering. Thirdly, the capsules must be readily electrostatically chargeable along with the powder particles in the coating during the application process or must already carry a charge of compatible polarity. Finally, the shell wall must be robust enough to survive curing temperatures as high as 200 ºC for times in excess of 30 min in some instances. These requirements essentially eliminate shell wall chemistries based on gelatin and thermoplastics. While common shell wall materials such as polyurea, polyurethane, polyoxymethylene urea and polyoxymethylene melamine rarely exhibit decomposition below about 300 ºC, the internal phase of the microcapsule must also exhibit stability at a minimum of 200 ºC for the microcapsule to be stable enough for powder coating applications.
This article reports on our evaluation of AMPARMOR™ 2000, an additive designed to impart self-healing functionality to fusion-bonded epoxy (FBE) and epoxy powder primer coatings, and AMPARMOR 3000, designed as an option for nonepoxy coatings. AMPARMOR 2000 is comprised of a microencapsulated epoxy-based formulation capable of forming a protective film at the site of damage by a combination of coalescence of powder particles and crosslinking reactions with residual unreacted or partially reacted accelerants and curatives present in the coating. AMPARMOR 3000 is comprised of a microencapsulated functionalized alkyd-based formulation capable of forming a protective film at the site of damage by a combination of coalescence of powder particles and crosslinking reactions of unsaturated functionality present in the alkyd. Both products are spray-dried with an average particle size of 5 to 10 microns. At this average size, the particles comprising these additives are smaller than the average particle size of most powder coatings, thereby facilitating coalescence of powder particles around the additive particles during curing. Both products can be blended with powder coating formulations and applied via electrostatic spray or fluidized bed application processes. Below, we discuss the respective thermal stabilities of these products, followed by an assessment of their anticorrosion performance as additives post-added to a commercially available FBE coating and epoxy primers in the case of AMPARMOR 2000, and in a polyester powder coating in the case of AMPARMOR 3000, while addressing the role of surface preparation and pretreatment chemistry on coating system performance where relevant.
Thermal Stability
An important first step in the evaluation of microcapsule-based self-healing additives for powder coating applications is an assessment of their thermal stability. To this end, samples of AMPARMOR 2000 and 3000 were evaluated via thermogravimetric analysis (TGA) using a method in which the samples were heated from 25 ºC to 650 ºC at a rate of 10 ºC/min in a Mettler Toledo TGA/DSC 1. For both products, microcapsule rupture was not observed until well above 200 ºC, while the onset of shell wall decomposition did not occur until above 300 ºC. These results suggest adequate thermal stability for most fusion-bonded epoxies and powder coatings, which generally require curing temperatures that top out at about 400 ºF (204 ºC) for generally no longer than 30 min. In instances where the recommended cure schedules require higher temperatures, cure times tend to be shorter. In general, various types and combinations of shell wall materials can be employed to achieve the desired thermal stability for typical FBE and powder coating cure schedules.
Performance in Fusion-Bonded Epoxy Coatings
To assess the performance of AMPARMOR 2000 in an FBE coating, 5wt% of the additive microcapsules were blended with a commercially available FBE coating by agitation in a sealed, air-filled container. The resulting powder coating formulation was then applied using an ITW-GEMA Optiflex powder application gun and cured at 450 ºF (232 ºC) for 2.5 min. The performance of steel substrates coated with coating systems incorporating AMPARMOR 2000 were compared to those coated with the standard FBE coating. The coating systems evaluated are shown in Figure 1. For each test panel, a total cured film thickness of 9 mils (225 microns) of the coating was applied. For the control (Figure 1a), no additive was added, and the coating was applied in one coat to a dry film thickness of 9 mils. For the modified versions of the FBE coating incorporating 5wt% of AMPARMOR 2000, the coating was applied as two separate systems for comparison. In the first system (Figure 1b), the coating was applied in one coat to a total DFT of 9 mils. For the second system (Figure 1c), the coating was applied in two coats, with the first coat containing 5wt% additive applied at a DFT of about 4.5 mils, followed by a second coat of the standard FBE coating excluding the additive product, also applied at about 4.5 mils. The first coat was cured and allowed to cool to room temperature prior to application of the second coat.
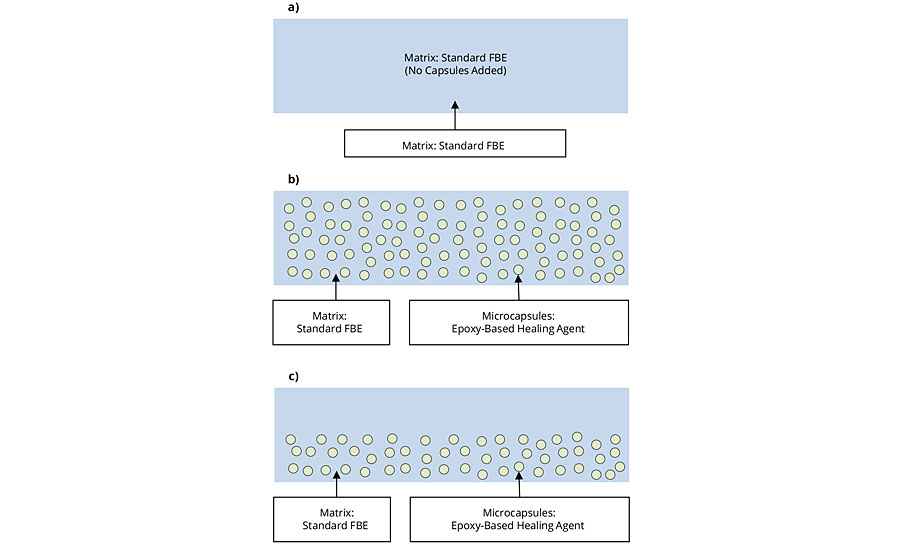
FIGURE 1 »FBE coating systems evaluated.
The resulting coated test panels were then scribed down to the underlying substrate using a 500-micron scribe tool. After allowing the panels to equilibrate at room temperature for 24 hrs, the scribed samples were then exposed to ASTM B117 conditions in a salt fog chamber. A combination of what we refer to as static and dynamic exposure/evaluation test protocols were performed on the exposed samples. For a static exposure/evaluation protocol, the panels were exposed to the salt fog for a specified period of time (e.g. 1,000 hrs) prior to evaluation of the scribed area by vigorously scraping as described in ASTM 1654 (Procedure A, Method 2). While commonly used for the evaluation of coated test panels, beyond benchmarking performance, this approach is only helpful in simulating service conditions in which after damage the coated substrate is not exposed to any significantly traumatic events. The dynamic exposure/evaluation protocol was designed to simulate more aggressive service conditions. Consider, for example, damage to the coating on a snowplow, the trailer hitch of a vehicle or to a coated pipe in transit prior to installation. In all these cases, the damaged coating is likely to experience ongoing trauma (e.g. additional abrasion, impact etc.) at the site of damage, and typical static exposure/evaluation protocols do not adequately simulate these conditions. For the dynamic exposure/evaluation protocol, the FBE-coated steel panels were exposed to ASTM B117 conditions in a salt fog chamber for 250 hrs, after which the specimens were removed from the chamber and evaluated by vigorous scraping as described above for the static approach. The panels were then returned to the salt fog for continuation of the exposure. This cycle of exposure followed by evaluation by scraping was repeated every 250 hrs up to a specified total exposure time (e.g. 2,000 hrs).
A summary of the results obtained for the static evaluation of FBE-coated cold-rolled steel (CRS) panels is shown in Figure 2. As expected, the control exhibited increasing coating adhesion loss or creep from scribe with increasing salt fog exposure time. Remarkably, no adhesion loss was observed for either of the coating systems containing AMPARMOR 2000 up to 1,000 hrs of ASTM B117 exposure. For panels exposed for 1,500 hrs, those coated with one coat of the FBE modified with 5wt% of the additive exhibited adhesion loss of 60% less than the control, while those coated with one coat of the modified FBE followed by a second coat of the standard FBE exhibited no loss of adhesion. This difference in performance between the samples coated with the modified FBE in one coat (Figure 1b) and those coated with the modified FBE followed by the standard FBE (Figure 1c) persisted in spite of the fact that the total DFT for both these coating systems as well as that of the control were identical.
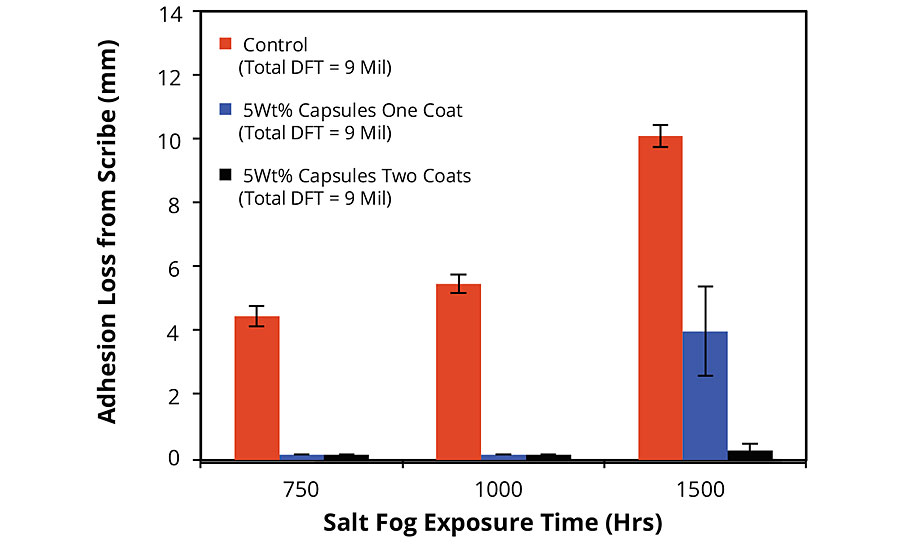
FIGURE 2 » Adhesion loss from scribe for FBE-coated CRS panels after salt fog exposure. Summary of results of static exposure/evaluation protocol.
Presumably, the difference in performance between these systems containing the AMPARMOR 2000 additive is due to the fact that for the version with only the modified FBE applied in one coat, the additive is blended with an already optimized coating formulation, resulting in a formulation with a pigment volume concentration (PVC) significantly greater than that of the standard coating. Such an increase in PVC may compromise coalescence of the powder particles and increase porosity in the coating. Applying a layer of the standard FBE over a first coat of the modified FBE allows for the more optimal, standard FBE to be the exterior coat immediately exposed to the environment, while the modified FBE layer closest to the metal substrate responds to damage extending to the substrate by releasing healing agent at the site of damage close to the substrate where it polymerizes and arrests corrosion creep. Since only half of the total 9 mil DFT contains the additive, the effective concentration of the additive in the total 9 mil coating stack for the panels coated first with the modified FBE, followed by the standard FBE is only 2.5wt%, compared to 5wt% for the samples coated in one coat by the modified FBE. Application in two coats as shown in Figure 1c or pairing with a suitable topcoat is therefore the most expedient approach to adopting the self-healing functionality as part of a set of standard protective coating solutions already in use. For applications limited to only one coat, appropriate accommodation of the increased pigment volume resulting from the addition of the additive is required.
Similar results were observed via the dynamic exposure/evaluation protocol for FBE-coated CRS panels. As shown in Figure 3 (pg. 52), none of the panels exhibited any adhesion loss until the evaluation after 750 hrs of total salt fog exposure. As expected, since the dynamic exposure/evaluation approach is more aggressive relative to the static version, the control exhibited 25% more adhesion loss after 750 hrs of salt fog exposure. Panels coated with systems incorporating AMPARMOR 2000 in either the entire coating stack (Figure 1b) or the half of the coating stack closest to the substrate (Figure 1c) exhibited significant improvement in adhesion maintenance and corrosion resistance over the control, with the latter exhibiting practically no loss of adhesion after 750 hrs of salt fog exposure (see Figure 4 for corresponding images).
FBE-coated blasted steel panels exhibited similar trends with the distinction that all test panels exhibited improved adhesion after damage in the dynamic exposure/evaluation testing protocol. For example, while values for average adhesion loss from scribe after 750 hrs of salt fog exposure of 5.55 mm (control), 1.95 mm (one coat modified FBE) and 0 mm (modified FBE for the first coat and standard FBE for the second coat) were recorded for the FBE applied to CRS substrates (Figure 3), 3.20 mm (control), 0.81 mm (one coat modified FBE) and 0 mm (modified FBE for the first coat and standard FBE for the second coat) were recorded for FBE-coated blasted steel substrates (Figure 5). After a total of 2,000 hrs of salt fog exposure, the modified FBE/standard FBE coating system (Figure 1c) exhibited creep from scribe of 6.23 mm compared to 28.58 mm for the standard FBE coating system. Images comparing the FBE-coated blasted steel substrates are shown in Figure 6. Interestingly, the 6.23 mm of creep recorded for the modified FBE/standard FBE coating system after 2,000 hrs of salt fog exposure is less than the 6.96 mm recorded for the standard FBE coating (control) after 1,000 hrs of salt fog exposure, indicating a life extension of over 100% in the dynamic exposure/evaluation testing protocol.
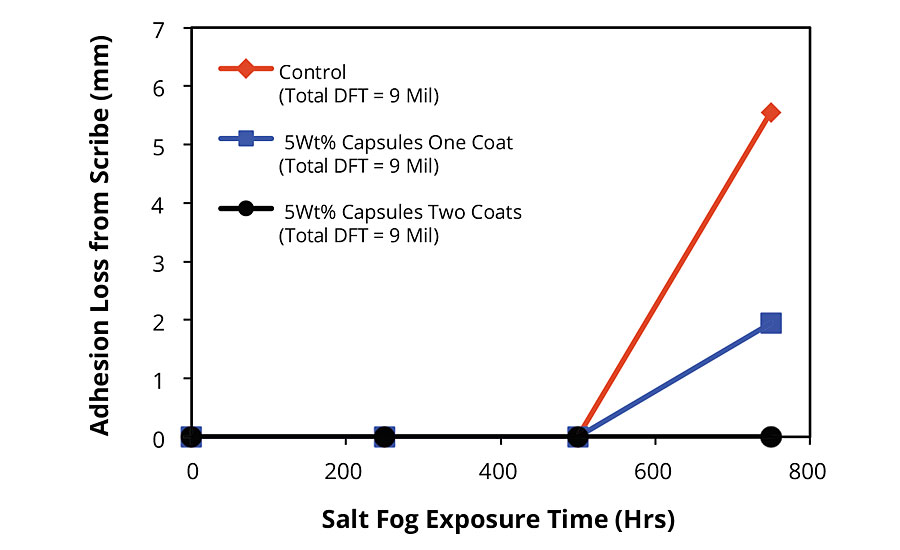
FIGURE 3 » Adhesion loss from scribe for FBE-coated CRS panels after salt fog exposure. Summary of results of dynamic exposure/evaluation protocol.
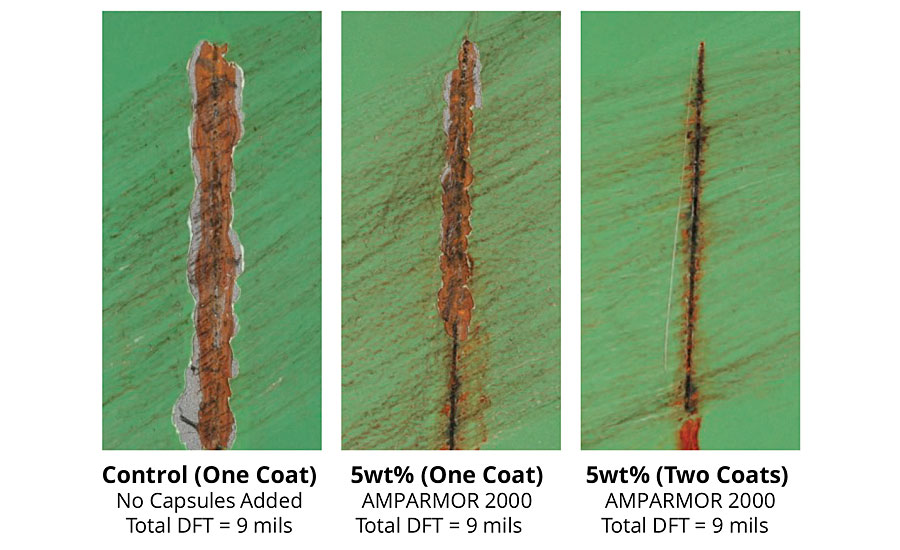
FIGURE 4 » Adhesion loss from scribe for FBE-coated CRS panels after salt fog exposure. Images acquired after dynamic exposure/evaluation protocol.
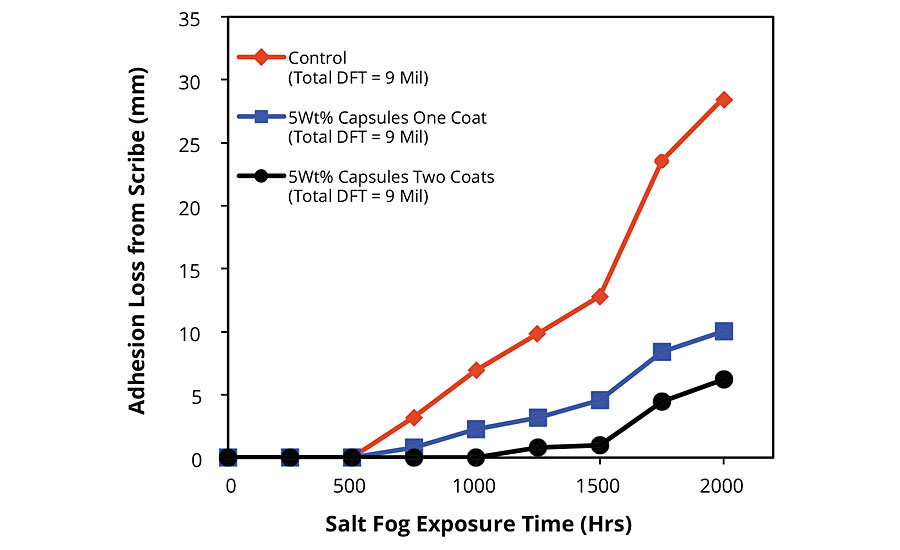
FIGURE 5 » Adhesion loss from scribe for FBE-coated blasted steel panels after salt fog exposure. Summary of results of dynamic exposure/evaluation protocol.
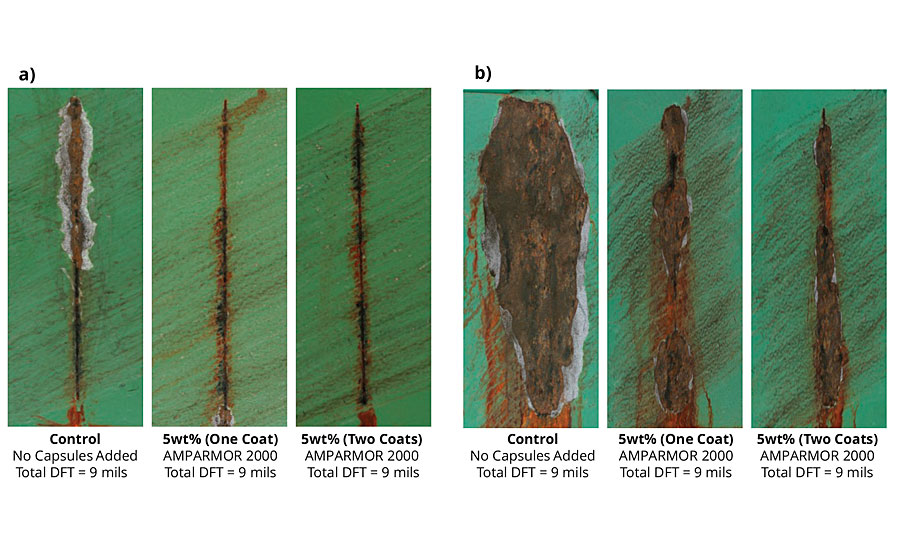
FIGURE 6 » Adhesion loss from scribe for FBE-coated blasted steel panels after salt fog exposure. Images acquired after dynamic exposure/evaluation protocol; (a) after 750 hrs of salt fog exposure, (b) after 2,000 hrs of salt fog exposure.
Evaluation of Performance in Epoxy Primers
AMPARMOR 2000 has also been evaluated in a variety of standard epoxy powder coatings, typically as part of a system incorporating a polyester topcoat. In these evaluations, the additive was blended with the epoxy powder coating via co-fluidization in an air-filled container. The resulting modified powder coating was then applied to either standard CRS panels or Bonderite® 1000 (B1000) pretreated CRS panels via an electrostatic spray gun and cured at 400 ºF (204 ºC) for 10 min, followed by application of a standard polyester topcoat and curing for an additional 10 min. The epoxy primer layer and the polyester topcoat were both applied to a DFT of 4 mils (100 microns) each for a total DFT of 8 mils (200 microns). The coated samples were then scribed using a 500-micron scribe tool and allowed to equilibrate at room temperature for 24 hrs, after which the samples were exposed to ASTM B117 conditions and evaluated using the dynamic exposure/evaluation protocol described above. A summary of the results obtained after 1,000 hrs of salt fog exposure is shown in Figure 7. For standard CRS substrates, the results were significantly dependent on the concentration of AMPARMOR 2000 incorporated into the primer. At the lowest concentration used (2wt%), the incorporation of the additive into the primer resulted in a 70% decrease in adhesion loss creep from scribe from 14.1 mm for the control to 4.4 mm for the primer modified with 2wt% additive (Figures 7 and 8). Although adhesion loss was minimal for all samples applied on B1000 pretreated CRS panels, substrates coated with systems incorporating the additive into the primer all exhibited significantly less adhesion loss from the scribe relative to the control (Figures 7 and 9). With a creep from scribe failure specification of 0.25 inches in mind, the coated B1000 pretreated CRS panels were tested past 3,500 hrs. While the control samples exhibited adhesion loss from scribe of greater than 0.25 inches (6.35 mm) prior to 2,500 hrs of salt fog exposure, the best-performing system incorporating AMPARMOR 2000 exhibited less than 1.5 mm of adhesion loss from scribe after 3,500 hrs of salt fog exposure (Figure 10).
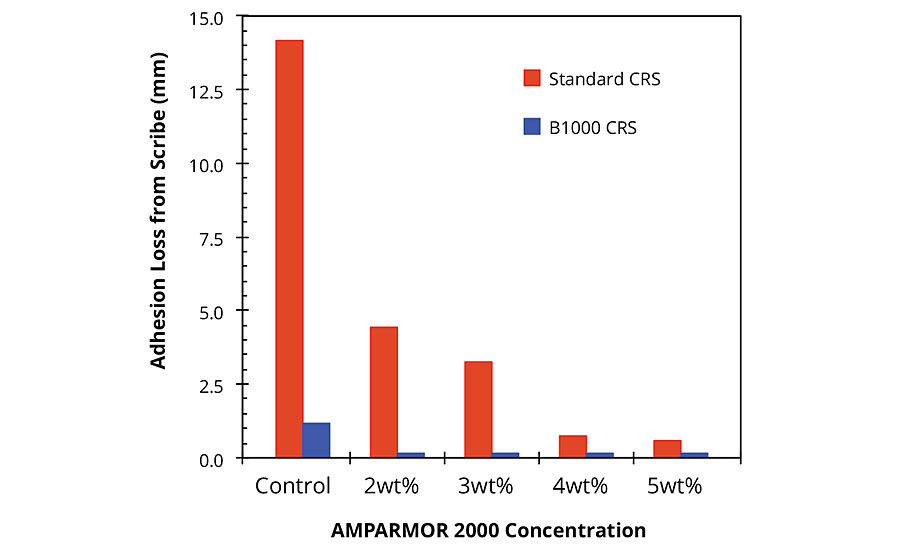
FIGURE 7 » Adhesion loss from scribe for coated standard and B1000 pretreated CRS panels after salt exposure. Summary of results of dynamic exposure/evaluation protocol.
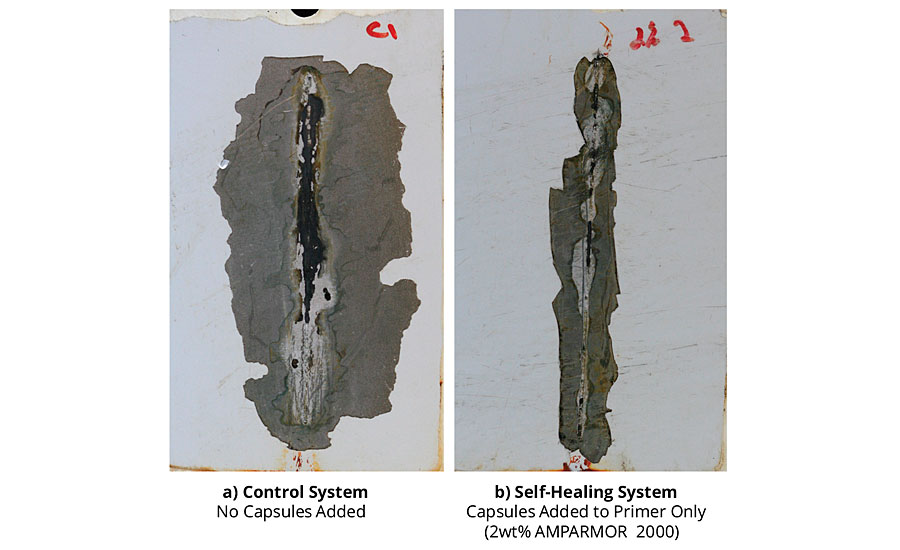
FIGURE 8 » Adhesion loss from scribe for coated standard CRS panels after 1,000 hrs of salt fog exposure.
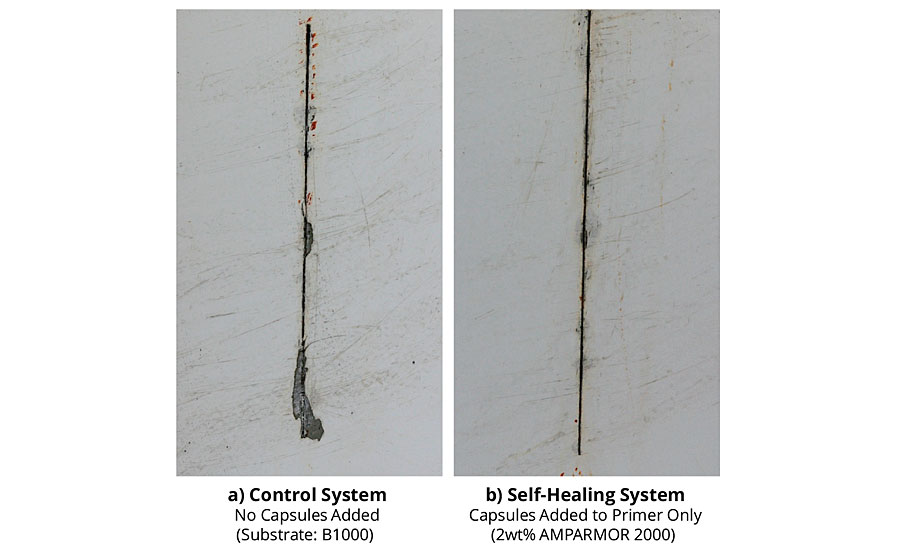
FIGURE 9 » Adhesion loss from scribe for coated B1000 pretreated CRS panels after 1,000 hrs of salt fog exposure.
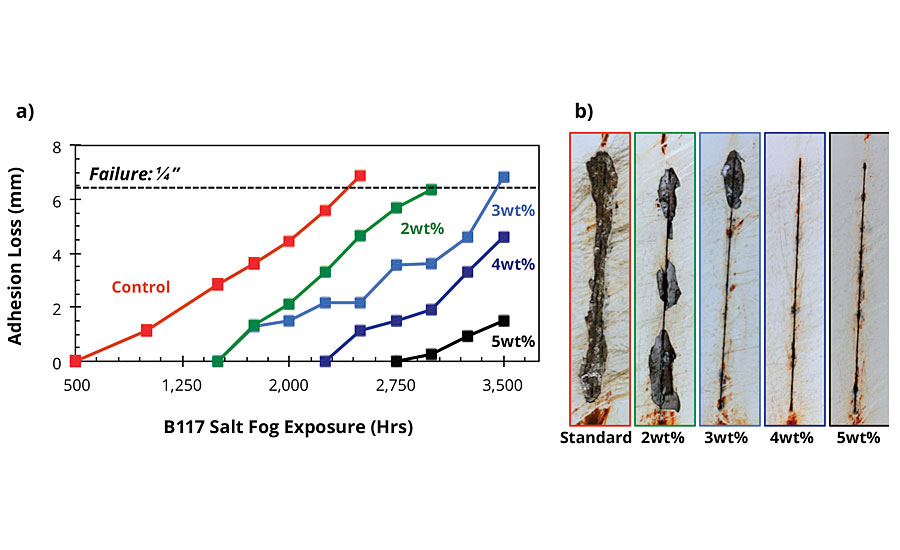
FIGURE 10 » Adhesion loss from scribe for coated B1000 pretreated CRS panels as a function of salt fog exposure. (a) Summary of adhesion loss results (b) corresponding images of the scribed areas after 2,000 hrs.
The concentration dependence of the corrosion resistance exhibited by systems incorporating AMPARMOR 2000 has important implications for designing anticorrosion solutions optimized for performance and added cost. Remarkably, samples coated with systems incorporating the additive at a concentration of 5wt% did not fail until beyond 7,000 hrs of salt fog exposure, representing life extension of close to 300% via the dynamic exposure/evaluation testing protocol. An identical system incorporating a green polyester topcoat, as opposed to the white used in the evaluations discussed so far, exhibited an improvement over a leading epoxy powder coating of over 300% in the same dynamic exposure/evaluation testing protocol (Figure 11). The epoxy primer containing AMPARMOR 2000 was recently commercialized by AmeriCoats, Inc. under the trade name AMERIGARD™ Plus.
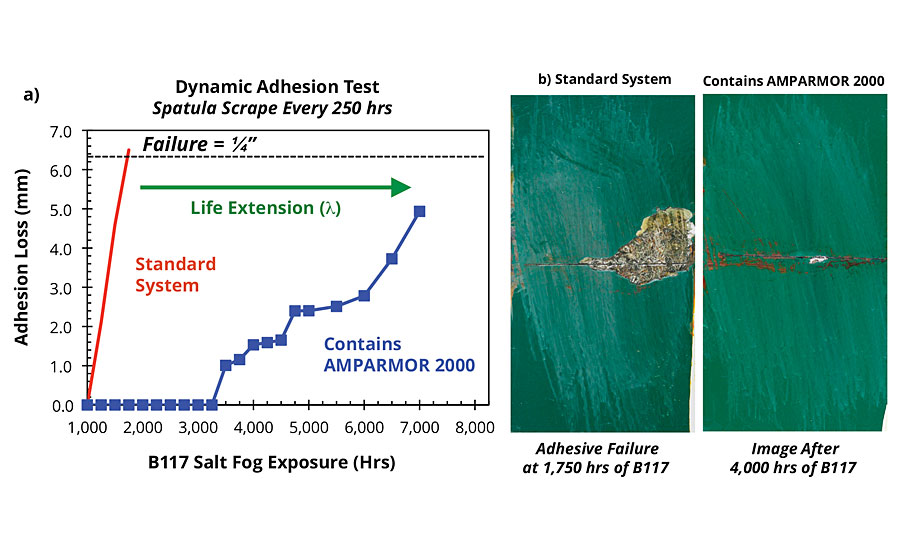
FIGURE 11 » Adhesion loss from scribe for coated B1000 pretreated CRS panels as a function of salt fog exposure. (a) Summary of adhesion loss results (b) corresponding images of the scribed areas after 2,000 hrs
Performance in Other Systems
Evaluations of additional powder coating systems incorporating various combinations of epoxy and polyester primers and topcoats revealed excellent consistency in the performance improvement observed when self-healing additives were included relative to otherwise identical systems excluding the additives. Results for additional epoxy primer/epoxy topcoat systems and polyester primer/polyester topcoat systems applied on panels with various surface preparation and pretreatment protocols are summarized in Table 1 along with results for the FBE and epoxy coating systems discussed above for reference. Incorporation of either AMPARMOR 2000 or AMPARMOR 3000 additives into the powder coating systems consistently resulted in significant minimization of adhesion loss from the scribe regardless of coating manufacturer (Epoxy 1 vs. Epoxy 2) or coating chemistry (epoxy vs. polyester).

Table 1 » Comparison of adhesion loss from scribe for various powder coating systems incorporating self-healing additives relative to their corresponding controls. Panels were all scribed using a 500-micron scribe tool and evaluated using a dynamic exposure/evaluation protocol.
Conclusions
Key takeaways from our evaluation of microencapsulated healing agents for improved corrosion resistance in FBE, epoxy and polyester powder coatings are as follows:
- The incorporation of microencapsulated self-healing agents into powder coatings results in remarkable improvement in corrosion resistance;
- Microencapsulated healing agents can be formulated to exhibit a level of thermal stability that is compatible with the typical cure schedules of FBE, epoxy and polyester powder coatings;
- Although PVC adjustment is recommended to accommodate the additional pigment volume resulting from the addition of microcapsules to an optimized powder coating, post-adding microcapsules to a powder coating as a way to deploy the technology in a quicker time frame could yield excellent results if the target application can support the application of a second coat;
- Surface preparation and pretreatment protocols can be synergistic with the improvement in corrosion resistance afforded by the self-healing additives so long as the encapsulated healing agents do not exhibit incompatibility with the resulting surface. The results reported here suggest that while increasing surface profile by blasting or pretreatment via iron phosphate or electroless nickel plating minimizes adhesion loss from scribe for the corresponding controls, coating systems containing microencapsulated healing agents exhibit commensurate performance improvement.
References
1 White, S. R.; Sottos, N. R.; Geubelle, P. H.; Moore, J. S.; Kessler, M. R.; Sriram, S. R.; Brown, E. N.; Viswanathan, S. Autonomic Healing of Polymer Composites, Nature, 2001, 409, 794-797.
2 Wilson, G. O.; Andersson, H. M.; White, S. R.; Sottos, N. R.; Moore, J. S.; Braun, P.V.; Self-Healing Polymers, Encyclopedia of Polymer Science and Technology, John Wiley & Sons, Inc., 2010, 1-33.
3 Blaiszik, B. J.; Kramer, S. L. B.; Olugebefola, S. C.; Moore, J. S.; Sottos, N. R.; White, S. R. Self-Healing Polymers and Composites, Annual Review of Materials Research, 2010, 40, 179-211.
4 Caruso, M. M; Blaiszik, B. J.; White, S. R.; Sottos, N. R.; Moore, J. S. Full Recovery of Fracture Toughness Using a Non-Toxic Solvent-Based Self-Healing System, Advanced Functional Materials, 2008, 18, 1898-1904.
5 Jin, H.; Mangun, C. L.; Stradley, D. S.; Moore, J. S.; Sottos, N. R.; White, S. R. Self-Healing Thermoset Using Encapsulated Epoxy-Amine Healing Chemistry, Polymer, 2012, 53, 581-587.
6 Yang, J.; Keller, M.W.; White, S R.; Sottos, N.R. Microencapsulation of Isocyanates for Self-Healing Polymers, Macromolecules, 2008, 41, 9650 - 9655.
7 Caruso, M. M.; Silvia, A. W.; McIntire, P. J.; Wilson, G. O.; Sottos, N. R.; White, S. R.; Moore, J. S. A Self-Healing Biomaterial Based on Free-Radical Polymerization, Journal of Biomedical Materials Research Part A, 2014, 102, 3024-3032.
8 Paint and Coatings, Applications and Corrosion Resistance; Schweitzer, P.A., Ed.; CRC Press, Taylor and Francis Group, Boca Raton, 2006.
9 Cho, S.; White, S. R.; Braun, P. V. Self-Healing Polymer Coatings Advanced Materials, 2009, 21, 645-649.
10 Wilson, G. O.; Andersson, H. M. Self-Healing Systems for High-Performance Coatings, Paint and Coatings Industry, May, 2012.
11 Huang, M.; Yang, J. Facile Microencapsulation of HDI for Self-Healing Anticorrosion Coatings, Journal of Materials Chemistry, 2011, 21, 11123-11130.
12 Baird, L. M.; Breidenich, J. L.; Benkoski, J. J.; Deacon, R. M.; LaBarre, E. D.; Maisano, A. J.; Ott, E. W.; Rhim, Y. R.; Patchan, M. W. Self-Healing Coatings with Galvanic Protection, Paint and Coatings Industry, March, 2012.
13 Pasatta, J. Improving Epoxy Powder Coating Durability, Paint and Coatings Industry, March, 2016.
Looking for a reprint of this article?
From high-res PDFs to custom plaques, order your copy today!