Performance Benefits of Incorporating a New Aliphatic Urethane Tetraacrylate in UV Coatings
As a result of identifying an existing market need for a flexible, scratch-resistant aliphatic urethane tetraacrylate, Surface Specialties, Inc., has developed Ebecryl
Product Characterization
As with all beginning inquiries into new chemistries, it is important to identify how the product was evaluated and under which conditions it performed well. In this screening, commercial aliphatic urethane acrylates were used for direct comparison. Film application data was generated comparing Ebecryl 8405 (aliphatic urethane tetraacrylate) with- Ebecryl 284 (aliphatic urethane diacrylate),
- Ebecryl 8301 (aliphatic urethane hexaacrylate),
- A 50: 50 blend of the above two commercial materials.
Application Test Substrates
Accelerated Weathering - Instrumentation and Recordable Values
Application Instrumentation/Equipment
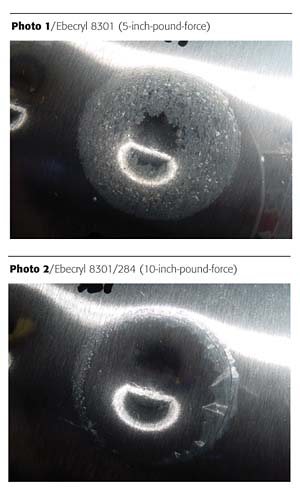
Sample Preparation
With the exception of Instron specimens, test films in this study were subjected to the same sample preparation. UV dosage was kept at a constant level, irrespective of the individual chemistries, to allow for the most direct comparison possible between oligomers with dissimilar functionality.The oligomer content of each test formula was 70% of the total composition. Those samples, which contained some portion of diluting monomers, were balanced out to the 30% monomer content with HDODA. Each formulation incorporated 2 phr of Ciba Specialty Chemicals' Irgacure 184.
To assure similar coat thickness for applications testing, a #5 wound wire bar was used to form a final film thickness of 0.5 mil. Application test samples were cured using a Fusion EPIQ 6000 UV unit employing 2-H lamps with a variable power supply at 100% power level at 600 watts energy. Each test specimen was passed through the unit three times, for a total irradiation of 1767 mJ/cm2 and a line speed of 72 ft per minute (with the exception of tensile samples - see additional information regarding sample prep below). The irradiation dose was measured with an IL 390c Light Bug.
Upon completion of cure, a Gardco Minitest 100-N coating thickness gauge was used to check film thickness. Each material was prepared in triplicate to allow for statistical variation in the sample preparation.
Free film samples for tensile testing were drawn down using an unwound bar. Formulations were placed between two sheets of Mylar film with a 5-mil spacer in between, for appropriate cured film thickness for testing. All Instron film sample data was generated using a 2-phr level of Irgacure 184. The drawn films were then passed through the Fusion unit using 1-H lamp at 75% power level and 300 fpm. The semi-cured films were then cut to sample size and finished curing on the Fusion unit using 2-H lamps at 100% power at 72 fpm.
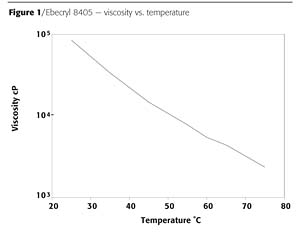
Viscosity and Diluting Monomers
Because product viscosity plays a role in the selection, handling and end use of any product, it should be noted that Ebecryl 8405, by nature of its chemical backbone, has a high molecular weight. The oligomer viscosity can be controlled either by temperature and/or diluting monomers. In a spray application, the neat form of Ebecryl 8405 is much too viscous for ease of handling and use. A diluting monomer might be desired to improve handling. Figure 1 examines the effect of temperature on viscosity.As seen in Figure 1, the reduction in viscosity of the 8405 is inversely proportional to the increase in temperature. Another method to reduce the viscosity would be with the addition of diluting monomers.
What must be seriously considered prior to selecting any of these diluting monomers is the end use of the coating and the importance of service life as depicted by either natural or accelerated weathering. Each ingredient will bring its own performance characteristics, and the impact will be dependent upon the level at which it is incorporated.
In Figure 2, HDODA has greater diluting efficiency than the other monomers. It has minimal impact on altering the final performance of the oligomer (including being the best diluting monomer for weathering). TMPTA-N (triacrylate) has the least diluting power and in regard to weathering performance, should not be the monomer of choice.
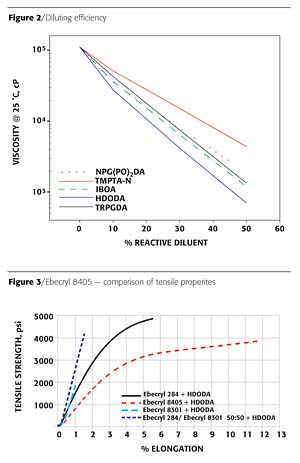
Results
Instron/Application Graphs - 70:30 Oligomer:Monomer BlendsThe oligomer level used in this screening work was established at the oligomer to monomer (HDODA) ratio of 70:30.
The data displayed in Figure 3 depicts the Instron performance characteristics for all four of the test samples. The curves shown were chosen to be representative of the samples tested. The hexafunctional Ebecryl 8301 is very brittle with little or no elongation and very low tensile properties. With the addition of equal proportions of the difunctional Ebecryl 284 to the hexafunctional Ebecryl 8301, there is some improvement with regard to tensile strength but the characteristic brittleness remains.
Difunctional Ebecryl 284 displays the highest tensile value of all of the samples within this study. The 8405 displays a final tensile strength value slightly lower than 284 at break. The elongation and toughness (area under the curve) of the 8405 is twice that of the diacrylate, Ebecryl 284.
Overall, Ebecryl 8405 is close to the tensile strength of the difunctional 284 and exceeds the performance of the overall tensile of the hexafunctional Ebecryl 8301 and the 50:50 blend of the Ebecryl 284 and 8301.
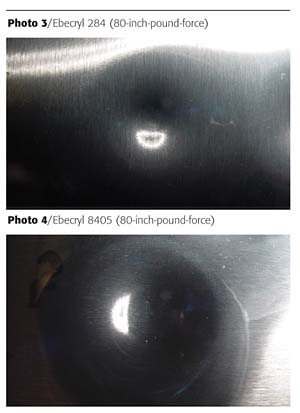
Direct Impact
Another key parameter for many end-use applications is impact - direct and indirect. This test was performed using a Gardner Impact Tester. Each of the cured oligomers remained overnight under standard laboratory conditions prior to testing.Photographs of direct impact testing of the various films coated at a thickness of 0.5 mil on CRS show the differing performance characteristics. The digital photograph of Ebecryl 8301 (Photo 1) shows how 5-inch-pound-force affects the high functionality and crosslink density of the film. The force of the weight shattered the film, and the brittleness of the hexafunctional material is observed.
A 50:50 blend of Ebecryl 284 and 8301 shows a slight improvement on the impact performance (Photo 2). However, the blend also fails direct impact but at 10-inch-pound-force. The addition of Ebecryl 284 has improved the overall performance, but it still fails.
Ebecryl 284 and 8405 display similar performance at the weight of 80-inch-pound-force. There is a slight marring of the Ebecryl 284 (Photo 3, 3 o'clock position). The integrity of the film is still intact.
In the digital image of the Ebecryl 8405 (Photo 4), there is a slight haloing effect on the right side of the impact area. There was no breach in the film integrity even at the higher crosslink density of the cured film.
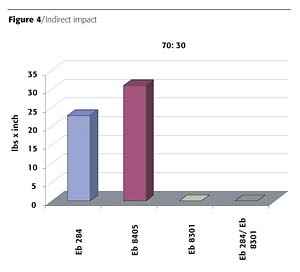
Indirect Impact
A more discriminating performance characteristic for film is indirect (or reverse) impact. The same equipment is used but the sample substrate/film is struck from the reverse (backside) of the substrate (in the test protocol, cold rolled steel).Ebecryl 8301 and the blend of Ebecryl 8301 and 284 both failed at less than 2-inch-pound-force. All of the samples were tested multiple times and each time failed at the same level of force. Clearly this higher crosslink density system does not have the resiliency to withstand this type of deformation.
Ebecryl 284 demonstrated excellent reverse impact due to its elongation characteristics and excellent flexibility. Surprisingly, the higher functionality of the 8405 surpassed the reverse impact number generated by the difunctional material. The flexibility of the tetraacrylate is once again demonstrated to be superior to the 50:50 blend of the di- and hexafunctional materials (Figure 4).
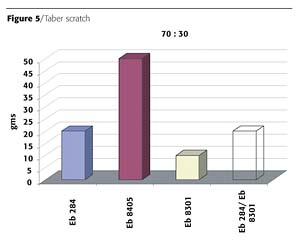
Taber Scratch
For some end-use markets, surface hardness and resistance to scratch is of the utmost importance in the final film. Samples were prepared on Leneta paper approximately 0.5 mil in thickness. The samples are placed in a conditioning room, set at 72 ºF and 50% RH overnight prior to testing. Taber scratch resistance was determined by using a Taber scratch tester with a conical diamond tool. The scratch resistance was recorded as the weight required to break through the cured film.The highly crosslinked 8301 displayed poor resistance to the Gardner scratch when compared to the other materials on test. The addition of a difunctional material does improve the scratch resistance but not to the greater extent as when the di- or tetrafunctional material is tested alone.
The value generated for the 284 shows that flexibility improves the resistance to the weight of the diamond tip to create a scratch in the surface. Once again, however, the 8405-based film exhibits more than twice the scratch resistance than that of the difunctional material (Figure 5).
Accelerated Weathering and the Impact of Stabilization
Service life predictability is yet another of the key determining factors used in many markets. It has been proven repeatedly in various studies that over time the higher the crosslink density of a film the less likely it will be able to withstand the effect of UV exposure over time. Without stabilization, the higher functional materials will begin to show signs of physical stress early as compared to a less functional material.Multiple sample specimens of each of the four formulations were cast onto white, thermal powder coated, aluminum panels at the approximate cured film thickness of 0.5 mil. After initial readings were conducted, the samples were placed under QUV-A (340 nm) accelerated exposure conditions. The settings were 8-hour light at 60 ºC and 4 hours of darkness with condensation at 45 ºC. The three main categories recorded were
2500 hours of total exposure time were allotted for this study, regardless if all of the films reached complete physical degradation or not.
Color
In reporting the change in color, it is helpful to understand some of the basics. The color system consists of two axis, a* and b*, which are at right angles and represent the hue dimension. The third axis is the lightness (L*) and is perpendicular to the a*b* plane. DE* is commonly used to represent a color difference. The calculation of DE* is the square root of [(DL*)2 + (Da*)2+ (Db*)2], where L* = white/ black, a* = red/green and b* = yellow/ blue changes. These factors combined make up the overall color of the coating.Upon reviewing the final results for color change alone, there was little differentiation among the samples for DE* values, regardless of the composition. Slight fluctuations are noticeable due to reporting the average readings on variation locations within the exposure window (Figure 6).
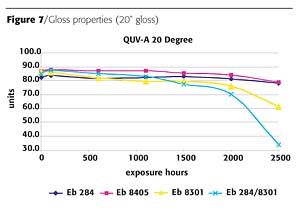
Gloss/Physical Degradation
Gloss is a visual concept or impression resulting from surface evaluation. Smooth surfaces reflect images distinctly, and the incident light is directly reflected on the surface. On rough, cracked surfaces, the quality of the images are diminished and the surface appears dull or eroded. The more the light is scattered, the duller the surface will appear. Physical degradation includes not only cracking and delamination but also surface erosion over time. This characteristic of surface erosion will also dull the gloss of the film surface.Our targeted goal was to have gloss retention over the course of the exposure remain as high as possible. A reduction in gloss over 15% from the original reading is considered a failure. Gloss readings of both 20º and 60º were recorded. For a high gloss, 60º value is to be >70 units, using 20º geometry, while a semi-gloss is a 60º value of 20 - 70 units, measured by 60º geometry.
The values for gloss and visual degradation characteristics tend to further define and separate the products (Figure 7). The test specimens for Ebecryl 8301 (hexafunctional) and the 50:50 blend of the 284: 8301 began to show signs of physical distress and loss in gloss retention at approximately 500 - 750 hours into the accelerated exposure period. This is also reflected in the fluctuation observed in the DE* values.
Ebecryl 284 and 8405 maintained their gloss properties over the 2500-hour accelerated QUV-A exposure for both the 20º and 60º gloss.
The reduction in gloss appears to be directly correlated to the physical degradation of the test specimens. Surface cracking (primarily as the appearance of "crowfoot" pattern) is evident in both the EB 8301 and physical blend product. Upon further visual inspection, the sample specimens appear to display traces of surface erosion, which added to the reduction in gloss retention values. At the edge of the cracking there can also be seen slight delamination due to film shrinkage (Figure 8).
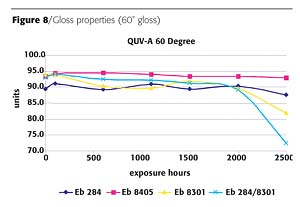
Stain Resistance
Stain resistance is another property that is important when selecting a new material for certain applications. Films of all four test materials were cast onto Leneta paper and cured at the approximate film thickness of 0.5 mil. Approximately five drops of six different stain-producing materials (mustard, ketchup, vinegar, red lipstick, brown shoe polish and oil) were placed onto the cured films. These materials were then covered and allowed to remain undisturbed on the films for a period of 24 hours. After the test period, the stain materials were removed from the sample films with moistened cheesecloth and examined.
The lipstick and mustard stains were the only two materials that breached the films' integrity. The other materials had no effect on the surface of the cured films. With regard to depth of staining, the mustard was the harshest. The tetrafunctional Ebecryl 8405 far surpassed the resistance to mustard or lipstick than did the higher crosslinked Ebecryl 8301 or the blend of the di- and hexafunctional sample.
Conclusions
Ebecryl 8301 displayed the fastest cure response of the oligomers tested. Ebecryl 8405 has a unique blend of properties and displays excellent overall performance characteristics. When compared to either the difunctional Ebecryl 284 or the hexafunctional Ebecryl 8301, or with a 50:50 blend of the two materials, the benefits of the Ebecryl 8405 are as follows:
This study clearly shows the high performance of the Ebecryl 8405. The unique balance of hardness, toughness and excellent weatherability make this oligomer ideally suited for the most rigorous applications.
Looking for a reprint of this article?
From high-res PDFs to custom plaques, order your copy today!