Have Tank, Will Travel
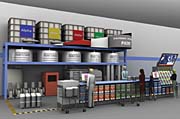
Well, not quite. The can - or for that matter the 5-gal pail - is by no means an endangered commodity in Smiland's L.A. paint-production plant. But a partnership formed by MicroBlend and Smiland has created a mini-revolution in the manufacturing of waterborne architectural paint that the two venture partners say could generate maximum returns as the technology evolves and expands, and eventually accounts for a sizable portion of Smiland's paint volume.
The MicroBlend-Smiland Paint venture represents the first commercial application of a patented paint-manufacturing process developed over a period of several years by MicroBlend Technologies, a business founded by Danny McClain, who previously had developed a similar processing system in Arizona for the manufacture of elastomeric materials. McClain, Micro Blend president, spent several years perfecting the process, in which paint is actually mixed and packaged at the retail outlet rather than the manufacturing plant.
In the process developed by the MicroBlend-Smiland team, the paint components are manufactured at Smiland's Los Angeles coatings plant using conventional production processes. But instead of mixing all the paint constituents and packaging the finished product in cans or pails at the plant, the major components of the paint are kept segregated in five different 275-gal tote tanks. The tanks are shipped to the retail site - in Smiland's case, to three company paint stores in Los Angeles, San Francisco and Napa, CA.
At the paint store, the five tanks are integrated into the MicroBlend system, a machine that mixes material from the tanks into the finished product, with the mix automatically determined by a menu-driven selection process. The finished paint is then dispensed into a 1- or 5-gal container, weighed gravimetrically, tinted manually, and shaken in a conventional paint shaker. The lid is placed on the container, and a label - which is automatically printed when the formula is entered - is manually applied.
Essentially, a sizable portion of the production process has been transferred from the plant to the retail outlet. The paint goes from the tote tank to the customer's car trunk in just a few minutes, say the developers of the system. The process, said Smiland Paint Co. President Bob Smiland, opens up the possibility of the "inventory-less" paint store - not counting unfilled paint containers, of course.
Next thing you know, those trendsetters on the West Coast will be selling paint at drive-through windows.
"The system can make a high-durability, high-gloss exterior gallon of paint in as little as 25 seconds. A five-gallon pail takes about one minute," McClain said. The development partners are at work on the addition of an automatic tint system that would incorporate the tinting segment of the process into the blend.
The paints are currently being sold under Smiland's Morwear brand; nearly 15,000 gal have been produced and sold since the system went into operation late last spring. The process possesses the capability to produce the entire range of interior and exterior waterborne architectural paint products offered by Smiland Paint - from flat to gloss finish, in all grades and in all the shades of the company's color spectrum - nearly 3,000.
MicroBlend representatives, citing the proprietary nature of their system, decline to say precisely what is contained in each of the five tote tanks that feed into the mixing system. But McClain says generally that the tanks supply resins, pigments, extenders, additives and water.
MicroBlend owns the technology, patents and formulas. Smiland provides manufacturing, sales and distribution, and also is involved in development of the production process and coatings formulation.
The MicroBlend developers say expansion figures prominently in their plans - regionally, nationally and overseas. "Evolving a strategic partnership with Smiland Paint Co. has been very key," David Philbrook, MicroBlend's vice president, Sales & Marketing, said of the company's growth objectives.
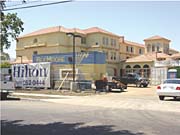
Smiland: As Technology Evolves, Volumes Will Expand
Bob Smiland is greatly impressed with the initial results of the venture with MicroBlend, and said he envisions that the technology will eventually account for a significant share of the company's waterborne paint production.He said the paint is made using the same mills, dispersers and other manufacturing equipment found in any paint-manufacturing facility. Instead of being handled "numerous times" as the paint makes its way from tank to container, the product is kept in the five major components, emptied into totes and shipped to stores. "There is no canning line, no label line. It takes a third of the personnel," Smiland said. "We use the exact same equipment.
"The QC requirements are more stringent than with our regular paint operation, because we insist the accuracy be there," he said.
Each of the five components is designed to retain a shelf life - or in this case a "tank life" - of six to nine months, with no need to mix or circulate the materials, McClain said. "It's designed to stay homogenous." Still, the MicroBlend developers say the process should be looked to as a candidate for relatively high sales volumes, since the shelf life is not completely without limits.
Smiland calls advantages for both the manufacturer and the retailer "significant."
"Currently two-thirds of my space goes to the process of putting paint into the can and the can into a carton. And about two-thirds of our operating capital is tied up in packaging." The payoff for the initial investment, Smiland said, is quite modest. He said production of just 25 gal a day will pay for the system.
"What I hope to happen is that Smiland Paint will eventually operate a smaller manufacturing facility. We'll go from 1,000 SKUs (product units) to five SKUs, I hope. Eighty percent of what we make can be made with these five components." The company's existing operations include a manufacturing plant in Los Angeles and a 110,000-square-foot warehouse in nearby Alhambra, CA.
Currently, the MicroBlend system accounts for a very small share of Smiland's volume - perhaps only 1%. "But we expect to open a much larger number of locations. We'd like to have 50% of our manufacturing in this process by 2005," Smiland said. "The system eliminates the barriers of entry into the retail paint market. You can open an inventory-less paint store." The cost, the venture partners say, is approximately the same as a high-quality, high-end automatic tinting machine.
Smiland said the biggest challenge to making the system work in a commercial application was the learning curve to scale up the technology for a high-volume paint store - adjusting pump and line sizes and making other modifications.
The stringent QC procedures, "combined with the technology's accuracy, allow us to make paint at a retail store or job site equal to or better than at a paint factory," he said. "That's probably the thing that will surprise most people. This applies to color as well. We have perfected the ability to match colors in the store, certainly up to the standards that exist today.
"It's no more complicated, maybe one step easier, than an ATM (automatic teller) machine."
Smiland said he initially turned down a proposal from MicroBlend representatives three years ago, then decided to give it another look last year after overtures from Philbrook and a visit to MicroBlend's pilot-plant operation in Arizona.
Philbrook, who displays a high level of enthusiasm in his role as chief salesman and cheerleader for the MicroBlend process, unabashedly calls the process a "revolutionary breakthrough in how paint is made.
"In a small batch operations, you do have a scenario of tanks with tint bases," he said. "But we produce interior and exterior products of any sheen level, in multiple-quality grades, and all at the point of sale - from five simple components."
Even at the retail location, Philbrook said the labor involved in selling the can of paint is really no greater than conventional methods. "Even now, someone has to get the base, add the tint and shake it. With our operation, the operator automatically selects the base, the label is added, and the paint is tinted and shaken. The time is actually less from order to completion. It's all right there."
The process will become simpler and involve even fewer steps "once we get the color-dispensing integrated with the paint-dispensing," he said.
Looking for a reprint of this article?
From high-res PDFs to custom plaques, order your copy today!