Applications of Novel Photo-Curing Oligomer Resins: Generation Two

Recently published papers1,2 have discussed novel self-initiating resins that UV-cure with no or very little added photoinitiator. These resins contain a unique chromophore that becomes part of the resin/oligomer structure through the Michael addition reaction between b-diketones, b-ketoesters and/or b-ketoanilides with common acrylates. During the reaction, new covalent bonds are formed between the activated methylene carbon of the Michael donor and the terminal carbons of the acrylate double bonds. The new product molecule features a ketone moiety attached to a fully substituted carbon atom. This bond is inherently photolabile and provides the unique photosensitivity of this class of resins. An example of the Michael addition oligomer resin is depicted in Figure 1.
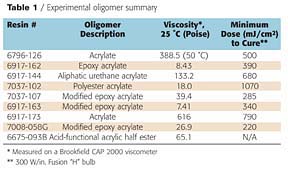
Claims about the versatility of this new technology are based on the experience of creating many, many unique materials. While the methodology to synthesize these novel resins has been refined to create robust ‘products' from almost any raw materials, distinct trends in structure-property relationships have been gleaned from a substantial database of new materials. Novel, self-initiating acrylic oligomer resins have been created from every class of starting material - epoxies, urethanes, polyesters, melamines, silicones, fluorocarbon acrylates, etc.
Resins chosen for benchmarking in the current study were often taken ‘off of the shelf' as drop-ins for similar commercial materials. However, as some were simply better performers than others, they were utilized more extensively in comparative formulations. Table 1 describes the oligomers employed and summarizes their viscosities and minimum dose to cure tack-free/mar-free. These are not products, per se, but rather starting points in identifying materials of commercial significance.
Benchmarking Experimental Coatings
The most direct way to determine the viability of this new photoinitiating chemistry was to benchmark the new materials against "standard" formulations. The following examples, segregated by substrate type, were all compiled by a similar process. Published starting-point formulations were obtained from the open literature (Sartomer Technical Bulletins 4/02, 5/02, 6/02; "How to Formulate UV-Curing Coatings" by R.C.W. Zwanenburg, Cray Valley Internet publication) or vendor catalogues. The goal of this comparative exercise was to replace oligomeric resins comprising the body of the published coating formulation with Michael addition resins where practical, quantify the degree of photoinitiator reduction benefit realized by this substitution, and verify that other measured coating properties remained intact.A second objective was to substitute oligomers of similar composition to create formulations with viscosity as close to the benchmark formulations as possible. In some cases, formulation viscosity is significantly higher, but deemed to be within a workable window for application to the experimental substrate.
Coating cure was effected by either a 300W/in or 600 W/in Fusion "H" bulb as indicated in each example. All exposures were measured with an IL393 "Light Bug" (International Light), inclusive of wavelengths from 250 to 400 nm. Minimum dose to achieve a "5" cure (tack-free/mar-free) on our qualitative 1-5 scale is recorded in each formulation table. Coatings were then tested for adhesion, solvent resistance and gloss or hardness, where applicable. Michael addition oligomer formulations were run with additional photoinitiator where indicated. Mar was determined by firmly rubbing the surface of the freshly cured coating with a cotton swab.
Plastic Substrates
Several plastic substrates were evaluated. Summary data are only included here for polyester and high-density polyethylene (HDPE) substrates due to the practical limitation of the length of this paper. However, results not detailed for polyethylene, OPP, ABS, vinyl (flexible sheet and rigid) and polycarbonate were all outstanding, consistent with those shown in detail for the following substrates.Polyester
The benchmark formulation for rigid polyester substrate was duplicated from the Sartomer Technical Bulletin (5/02) for polycarbonate. Various coatings were applied to 5-mil-thick Polyester S sheets. This is biaxially oriented polyester similar to Mylar*. Coating thickness ranged from 6 to 10 microns.
Michael addition and standard formulations for polyester were run with photoinitiator, where indicated. Darocur** 1173 (3.8 phr) and Irgacure** 184 (1.0 phr) or fractions of this blend were utilized.
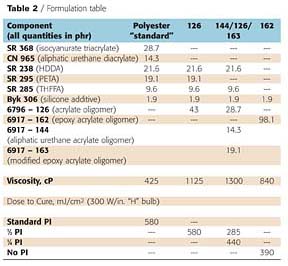
Cure Summary
Formulations containing Michael addition oligomers showed a significant reduction in photoinitiator required for tack-free cure (Table 2). Formulation "162" with no photoinitiator (PI) added cured faster than the benchmark control at full PI loading, though viscosity was double. Likewise, formulation 144/126/163 with one half PI loading cured at 50% of the energy required to cure the standard.Final viscosities were significantly higher than the control in the first two experimental formulations because of Resin 126, a first-generation resin product. Resin 162 is a second-generation product with greatly improved properties, allowing for nearly 100% utilization in formulation three.
All test formulations containing the various Michael addition oligomers, when cured tack-free, passed the following tests: MEK double rubs (>200), 180 degree fold (no cracking or delamination) and nail scratch adhesion.
Adhesion to polyester S was relatively easy to realize provided that good wetting was assured and thin coatings (less stress during cure) were applied. No special substrate pretreatment was necessary. Polyester S was used as received for adhesion testing.
Cross-hatch and direct tape application, as well as two tape types (Permacel* 99 or "aggressive" 3M 600) were tested. Direct tape application resulted in 5B adhesion for both tapes. Cross-hatch adhesion with 3M 600 tape was not achieved for any of the formulations tested, including the standard. The polyester benchmark and all Michael oligomer formulations exhibited essentially the same adhesion.
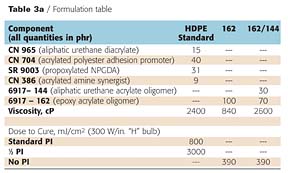
High-Density Polyethylene (HDPE) Substrate
The benchmark formulation was duplicated from "How to Formulate UV-Curing Coatings", by R.C.W. Zwanenburg. The various coatings were applied to HDPE sheets (~575 microns, treatment as indicated in Table 3a). Both sides of the HDPE sheets were slightly textured. The less-textured, matte-finish side was used for coating. Coating thicknesses ranged from 6 to 10 microns.
Michael addition and standard formulations for HDPE were run with photoinitiator, where indicated. Benzophenone (4.0 phr) and Irgacure 184 (1.0 phr) or fractions of this blend were utilized.
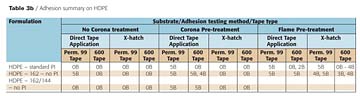
Cure Summary
Michael oligomer-based formulas cured faster without any photoinitiator present than the benchmark HDPE formulation with a full complement of PI and had better film integrity than the benchmark formulation. Resin 162, which is a neat oligomer, cured very fast without any PI added. The addition of 30% 6917-144 to enhance adhesion and flexibility did not decrease the observed cure speed.
All test formulations containing the various Michael addition oligomers, when cured tack-free, passed the tests shown in Table 4.
Note the poor solvent and nail scratch performance of the standard, even with a full photoinitiator package.
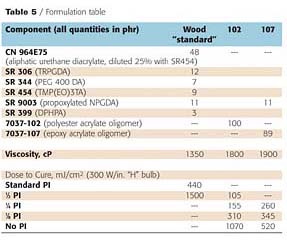
Wood
The benchmark formulation for comparison on wood, "Non-Yellowing Wood Coating," was from the Sartomer Technical Bulletin (06/02). Coatings were applied in two coats. A 2-mil coat was applied and cured immediately, followed by another 2-mil coat. Wood substrates were red oak or poplar.
Michael addition and standard formulations for wood substrates were run with photoinitiator, where indicated (Table 5). SR 1129 (5.0 phr) and SR 1137 (3.0 phr), supplied by Sartomer, or fractions of this blend were utilized.
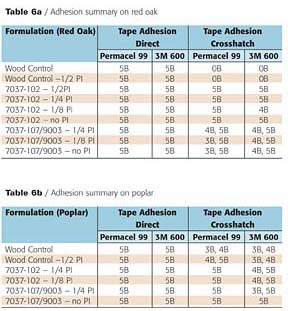
Cure Summary
The Michael addition resins with modest levels of photoinitiator cured at considerably lower doses than the control. For example, at 1⁄8 the photoinitiator level, both 7037-102 and 7037-107/9003 required ~20-30% less dose than the control (with full PI) to cure tack-free. With zero photoinitiator, the experimental resins still cured faster than the control with half photoinitiator. Viscosities for the experimental formulations, however, were roughly 50% higher.Adhesion testing was performed as in the previous section. Tables 6a and 6b summarize performance for both red oak and poplar substrates:
Both 7037-102 and 7037-107/9003 resins showed good to excellent cross-hatch adhesion to red oak compared to the control, which was poor. Direct tape adhesion for both the control and the Ashland resins was excellent. Both 7037-102 and 7037-107/9003 resins showed good to excellent cross-hatch adhesion to poplar. The control showed good adhesion to poplar.
All test formulations containing the various Michael addition oligomers, when cured tack-free, passed the tests shown in Table 7.
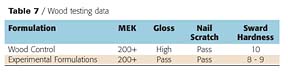
Metal
The benchmark formulation was found in the Sartomer publication, "Chemical Resistant UV-Curable Coatings for Steel." Test substrates included steel, aluminum and tinplate "Q" panels. Coatings were applied using a zero drawdown bar with coating thickness ranging from about 10-16 microns.
Michael addition and standard formulations for metal were run with photoinitiator, where indicated. Benzophenone (2.5 phr) and Irgacure 184 (5.0 phr) or fractions of this blend were utilized.
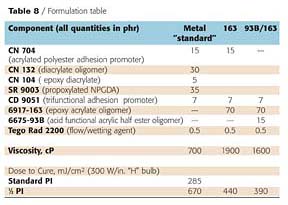
Cure Summary
Michael oligomer formulations with 1/2 PI cured at lower doses than the control with 1/2 PI loading (Table 8). The 163-based Ashland formulation cured at ~440 mJ/cm2 versus ~670 mJ/cm2 for the control, comprising a 33% improvement. Adding 6675-93B to replace the major adhesion promoter component in the 163 formulation further lowered the cure dose required for tack-free cure to 390 mJ/cm2. In terms of cure speed, the 93B/163 formulation with half the photoinitiator level is nearly as fast as the metal control with full photoinitiator level. The Michael oligomer formulations were considerably higher in viscosity and would require some reworking for application suitability.All test formulations containing the various Michael addition oligomers, when cured tack-free, passed MEK double rubs (>200) and nail scratch. Gloss was high and Sward hardness was roughly 30% higher for the experimental systems.
In terms of adhesion on steel Q panels, the metal control and the Michael oligomer formulations performed equally. Direct adhesion using either Permacel 99 or 3M 600 tape was excellent for both the metal control and the Michael formulations with all showing 5B. Cross-hatch adhesion for Permacel 99 tape was nearly as good exhibiting 4B-5B performance. Cross-hatch adhesion for the more aggressive 3M 600 tape was poor for all formulations. The addition of 93B adhesion promoter to the 163 formulation did not appear to improve adhesion.
On aluminum panels, the metal control and the Michael oligomer formulations performed equally. Direct adhesion with both Permacel 99 and 3M 600 tape was excellent for all the formulations. Cross-hatch adhesion was good for Permacel 99 tape while it was poor for 3M 600 tape.
On tinplate steel, the metal control and Michael oligomer formulations performed equally. Direct adhesion for Permacel 99 and 3M 600 tape was excellent. However, cross-hatch adhesion failed with both tapes in all formulations.
Summary
Across a variety of substrates, including both low- and high-energy surfaces, novel self-initiating Michael addition polyacrylate oligomers perform at levels comparable to and often exceeding published controls. In almost every case, however, substantially less photoinitiator is needed to achieve acceptable cure speeds and cured film performance. In many cases, no photoinitiator is required at all. This remarkable feature underscores both the novelty and utility of this new resin chemistry.The architectural control inherent in the Michael addition synthetic method allows for tailoring of resins to meet almost any required performance parameter. Commercial "target space" for products based on this new resin technology includes applications such as food and medical products packaging, where traditional photoinitiators cannot be used.
As seen in some of the examples, the great design flexibility associated with Michael addition oligomer resins also may allow for creation of simplified formulations consisting of essentially a single resin component.
Performance data were not included for several plastic and wood substrates and for glass in an effort to keep this summary article brief. However, performance in each case met or exceeded the control formulations in performance with equivalent or better cure using less or no photoinitiator in every case.
Acknowledgements
The authors would like to recognize the substantial contributions of Nathan M. Ebert, Timothy A. Ropp, Amy J. Gran, Ayleen Zaranec and Drew R. Hysell.
References
1 Sheridan, M.; Moy, T.; Gould, M.; Narayan-Sarathy, S.; Marino, T.; Mejiritski, A.; and Martin, D. "Novel Resins that Cure Without Added Photoinitiator", RadTech 2002 Technical Conference Proceedings, pp.462-473.
2 Narayan-Sarathy, S.; Gould, M.; Zaranec, A.; and Hahn, L. "Radiation-Curable Inks and Coatings from Novel Multifunctional Acrylate Oligomers", American Ink Maker, March/April 2004.
Looking for a reprint of this article?
From high-res PDFs to custom plaques, order your copy today!