Practical Parameters Affecting Opacity
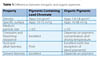
While the search for alternatives to lead-chromate pigmentation systems began in the 1970s, lead-free pigments remained the exception for many years. There are several reasons for this, the most prevalent being the technical and physical differences in the two pigment classes (Table 1), and subsequent difficulties in their processing and application. In many areas the potential of lead-chromate-containing pigments has been largely exhausted.
Today lead-chromate pigments encounter two problems. Current environmental standards require pigmentation systems that are free of heavy metals. The inadequate acid and alkali resistance of inorganic pigments is also problematic because they cannot withstand the increasing "acid rain" in industrialized countries, nor do they resist the alkali pH range of waterborne systems which, out of ecologic considerations, have become the preferred choice today.
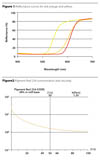
The Challenge - Achieving Opacity
When switching from inorganic to organic pigments in general, the core of the problem is the light-scattering and light-absorbing properties of the compounds. These two parameters are crucial for the opacity of a color. Light scattering and light absorbing are two fundamentally different properties. Depending on the color range and depth, they contribute to a different extent to the opacity of the color.For example, in pastel colors the opacity is primarily based on the very good light-scattering properties of the titanium dioxide, which is added to brighten the shade. In dark blue and green shades, on the other hand, it is especially the very good light absorption of the blue and green pigments that is responsible for a very high degree of opacity. For that reason it is possible to produce coatings in both color ranges using lead-free pigment systems.
The situation is different for red, orange and yellow. In the short-wavelength spectrum for example (ranging between 400 and 520 nm), a yellow pigment absorbs approximately 95% of the incident light. That means the contribution to opacity caused by absorbance in the visible wavelength area is good. Yet the long-wave spectrum (ranging from 520 to 700 nm) has an "absorption window" where the incident light is absorbed only to about 10%. The result is that adding a light-scattering pigment does not contribute to the opacity.
The situation is similar for all yellow, orange and red shades, as can be seen in the reflectance curves in Figure 1. It is only the slope of the reflectance curve that shifts to higher wavelengths when the amount of red is increased. It can therefore be established as a rule that the absorption window - and thus the area of insufficient light absorption - decreases with the redness of the color.
One possibility to indirectly influence this parameter is to add inorganic color pigments when formulating shades. Due to a refraction index that is higher than the one of organic pigments, a higher light scattering can be achieved, and thus better coating opacity. But this possibility has its shortcomings, as the result is often a shade that is lighter or duller than the original - brilliance and purity can be affected.
Despite these physical difficulties there are many high-performance organic pigments available today that provide suitable alternatives to pigments based on lead, chromate or mercury. Intensive research and development revealed the crucial parameters that determine opacity: optimized particle size and distribution, the coloristic properties of the individual pigment class, and the flowability properties and pigment load of the coating system. Clariant undertook systematic research to investigate in detail how these factors influence red-pigment coatings systems, and whether they offer the possibility to influence the opacity. The most important results of this comprehensive research are described below.
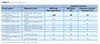
Pigment Content and Viscosity - A Decisive Interrelation
In all tests, the same formula was used. The binding agent was a standard system for industrial coatings, consisting of a non-drying alkyd resin based on a synthetic fatty acid with a highly reactive melamine resin. Several different established pigment classes with optimized particle size were used for coloration (Table 2).The binding agent and a pigment were mixed and the viscosity was determined depending on the pigment concentration. Figure 2 shows the measurements for the Pigment Red 254. For all pigments listed in Table 2 the interrelation between pigment concentration and viscosity was recorded in a curve, with variations in the curves depending on the pigment type.
The crucial factor is the pigment load of the mixture at a mill base viscosity of 1.5 Pa*s. This level of viscosity is relevant for a smooth processing of the coatings. Therefore the pigment content varies depending on the pigment types. For the red pigments in the tests, the pigment load ranges between 24% and 38% (Table 2).
In the next step the color mixture with a mill base viscosity of 1.5 Pas*s was diluted with suitable solvents to obtain spraying viscosity, and the resulting pigment content was measured. The coating was applied onto sheet steel metal with a black/white chart on top for measuring purposes.
After drying, the individual film thickness was determined, and a contrast measurement was done (DE in CIELAB units). Figure 3 shows a semi-logarithmic line chart, with the DE results in the logarithmic scale, in relation to the film thickness in arithmetic scale. The chart shows clearly that the opacity of the Pigments P.R. 254 (both grades), as well as P.R. 170 and P.R. 178, by far exceeds the other pigments, such as P.R. 188. This pigment only achieves the sufficient opacity at a film thickness of 110 µm, which does not meet the film thickness standards.

Meeting Industry Requirements
In the coating industry, the standard film thickness is 55 µm. For this reason, the organic dulling pigment C.I. Pigment Green 36 was added to the test coatings until a level of opacity was reached that was considered sufficient, while the film thickness was still deemed practically acceptable. Due to its high light absorption, Pigment Green 36 is as suitable as a dulling agent as carbon black. But since Pigment Green 36 also contributes to the color, it can generate shades with much higher purity than carbon black. The color measurements in Figure 4 show the opacity potential of different pigments.The best results were obtained by the two diketopyrrolopyrrole pigments P.R. 254. Not only are they very pure, but these two red pigments also feature very high opacity. It is sufficient to add small amounts of Pigment Green 36 to produce a coating with optimal opacity and 55-µm film thickness. With the addition of a small amount of dulling pigment, the coloristic properties of these pigments do not change, or change only to a negligible extent.
The total opposite is true for Naphthol AS/Monoazo Pigment P.R. 188, which is also known for its purity and brilliance. However, because its opacity is significantly lower than the two DPP pigments, it requires large amounts of dulling pigment, with the result of decreasing color quality. Compared to all other red test pigments, P.R. 188 had the least satisfactory results.
Conclusion
The goal of the above tests undertaken by Clariant was to provide a systematic study of all practical parameters affecting opacity. While individual parameters had been the subject of studies before, this was the first time all relevant parameters have been studied as an entity. The results show that assessing the coloristic potential of a pigment in an objective manner can only be done by taking into consideration important process-relevant factors, such as viscosity and pigment concentration. Although the focus of the study was not on showing the superiority of DPP pigments, their prime properties became obvious once again. The outstanding opacity of the high-performance red pigments provide the best conditions for a purely colored, brilliant coating that meets the most sophisticated requirements.This article is based on the paper presentation by Wilker, Gerhard, "Obtaining Opacity", 9th International Abrafati Congress, São Paulo, Brazil, September 2005.
For further information, contact gerhard.wilker@clariant.com.
Looking for a reprint of this article?
From high-res PDFs to custom plaques, order your copy today!