Tailoring TiO2 Treatment Chemistry To Achieve Desired Performance Properties
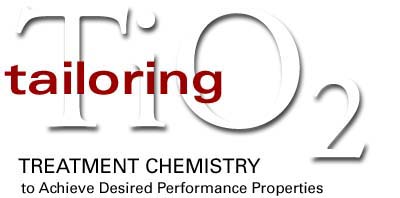
Titanium dioxide pigments are used in a variety of applications, all of which have different sets of performance requirements. As a result, the pigments designed for the various applications are different. Generally, the properties of a pigment are determined by the particle size distribution of the base pigment, the chemical composition and the morphology of the surface treatment. Although these properties are listed separately, there is some influence of one upon the other. For instance, the chemical composition can affect the dispersion characteristics and the particle size distribution in the specific application.
TiO2 pigment properties are determined by the base pigment and finishing process. The base pigment is affected by the manufacturing process, the crystal structure, the particle size distribution and the additives during manufacture. The pigment produced in both the chloride and sulfate processes is also agglomerated during particle size development. Usually milling steps take place during the finishing process to produce a pigment with the best possible particle size. Finishing also includes an inorganic treatment and, for many pigment grades, an organic treatment step. During inorganic treatment, pigment properties are affected not only by the amounts of the various chemicals but also by the conditions under which the treatment is deposited. Temperature, pH, deposition rate, source chemicals and other factors can influence the morphology or crystal structure of the treatment layers. The morphology of the treatment layers can, in turn, have an effect on the final properties of the pigment.
Base Pigment Selection
Titanium dioxide can be produced in either anatase or rutile crystal form. Both can be made by the older sulfate process. The chloride process produces only the rutile crystal form. The rutile crystal form exhibits better durability than the anatase, making rutile a better choice for pigments requiring weatherability and lightfastness. Rutile TiO2 produces higher opacity and greater scatter than anatase pigments since the rutile crystal has a higher index of refraction. However, anatase TiO2 is less abrasive than rutile. This property is particularly important for paper and fiber applications. Anatase is also used with UV brighteners, since rutile reduces the efficiency of the brighteners due to UV absorption in the same wavelength range. Generally, rutile TiO2 would be the preferred crystal form for coatings due to its higher opacity.In the sulfate process, ilmenite or slag ore is reacted with sulfuric acid to produce a solution of titanyl sulfate. This solution is then settled to remove insoluble material. If ilmenite ore is used excess iron is removed from solution as ferrous sulfate, or copper as crystals. The titanyl sulfate solution is thermally hydrolyzed to precipitate hydrous titanium dioxide. The precipitate is filtered, washed and leached to remove any traces of iron that could severely degrade the pigmentary properties, especially brightness and color. Additionally, any crystal growth regulators or other chemicals are added at this point. Potassium and phosphorous are added for particle size control. Aluminum can be added for durability and to counteract the color from any remaining niobium that was not removed during washing. The resulting hydrate paste is converted to titanium dioxide pigment during calcination. Conditions during hydrolysis and calcination determine the particle size and crystal structure of the titanium dioxide pigment.
In the chloride process, the ore - usually synthetic or natural rutile or slag - is reacted with chlorine in the presence of coke to produce impure titanium tetrachloride. The titanium tetrachloride is condensed and purified by distillation and chemical treatment. Impurities can be easily reduced to ppm levels by this method. The colloidal precipitate of the sulfate process is much more difficult to purify. The titanium tetrachloride is heated and reacted with oxygen in an oxidizer. A small amount of aluminum chloride is typically oxidized with the titanium tetrachloride as a rutile promoter and to add photostability to the pigment. Minor amounts of metal ions are added for particle size control. Potassium or cesium are the most common metal ions used. After exiting the oxidizer, the titanium dioxide particles are cooled and sent to finishing.
The particle size distribution of the base pigment particles is determined at the oxidation stage in the chloride process, and at the hydrolysis and calcination stages in the sulfate process. The particle size distribution has a significant effect on many titanium dioxide pigment properties. Light scattering is affected by the mass of titanium dioxide particles between approximately 0.1 and 0.5µm in size. The optimum size for the scattering of visible light is about 0.2µm. Light scattering affects tinting strength, undertone and hiding power. The gloss is degraded by the small fraction of particles larger than about 0.5µm. Dispersibility and fineness of grind are detrimentally affected by very small numbers of particles with sizes larger than about 5 µm.
As an example for choosing a base pigment, an exterior coating grade will be used. The example will assume that all the options are available, and that best quality is the only reason for any choice. In reality, this will not be the case, as production cost can be a major factor in development decisions. An exterior grade must exhibit durability. Therefore, a rutile pigment would be the best choice, since anatase is most photoactive. The rutile pigment could be produced using either the chloride or the sulfate process, but the pigment brightness and color are better in typical chloride pigments. To produce a pigment with the best possible durability, the base titanium dioxide should contain at least 1% alumina. The particle size distribution should be chosen to provide the optimum light scattering for best hiding power unless the undertone must be different to match the competition.
Finishing
Titanium dioxide pigments are generally coated to improve their performance in many end-use applications. Some pigment grades are not inorganically treated. These pigments are often either left unmilled or are milled in the dry state. In many titanium dioxide operations, a milling step precedes any inorganic treatment steps. The uncoated base pigment from the chloride oxidizer or the sulfate calciner is slurried in water with or without a dispersing agent. Milling of the slurry is typically accomplished in a media mill, a ball mill or sand mill. This step reduces or eliminates the agglomerates in the base pigment, which are formed during oxidation or calcination. The media milling before treatment reduces the intensity of final milling, which is needed to produce optimum pigment properties.Coating the pigment is accomplished by precipitating white hydrated oxides onto the pigment surface. These precipitation processes can be strongly influenced by the conditions during treatment. Thus the pH, temperature, reagents, order of addition and other factors can affect product characteristics. Optimum treatment conditions need to be determined after the surface treatment chemicals have been selected.
The most common surface treatments are silica, alumina, zirconia and hydrous titania. A number of other treatments have been used or patented for specialty applications. These treatments include tin oxide, zinc oxide, cerium oxide, phosphate and nitrate. These treatments are most commonly precipitated in layers. However, some of the components can be co-precipitated to alter the pigment characteristics.
Hydrous titanium dioxide is typically precipitated from aqueous titanium tetrachloride solution or from aqueous titanyl sulfate solution. Hydrous titania is believed to promote the adhesion of subsequent treatment to the base pigment. If present, this treatment is often the first layer applied to the surface. Hydrous titania has also been found to cause moderate durability in some pigments, perhaps by promoting adhesion of subsequent treatment.
Zirconia treatment is added to the surface of titanium dioxide pigment to promote durability. Durability is typically in the moderate to high category, depending on the amount of zirconia and the other treatment chemicals. Most zirconia-treated pigments on the market are "universal" grades with very good gloss and moderate durability. The presence of other chemicals that promote durability can increase the durability of the pigment. The presence of both zirconia and tin oxide produces a pigment that can be used in automotive topcoats. The great advantage of zirconia is its ability to promote durability without significantly impacting the optical properties of the titanium dioxide pigment.
Silica treatment can produce very disparate pigment characteristics, depending on the silica precipitation conditions. Silica treatment can produce a durable pigment or a high dry-hiding pigment. If silica is deposited at acidic or neutral pH, it is deposited as submicroscopic particles joined together in a gel-like structure. This "fluffy" coating provides better spacing and optical efficiency, increases oil absorption, and decreases gloss. These pigments are used in matte, dry-hiding formulations.
Silica treatments can also be deposited as a dense, glassy shell that encapsulates the particle and provides the highest durability available in titanium dioxide pigments. Dense silica is deposited slowly at basic pH. The dense silica shell does not increase the oil absorption of the titanium dioxide. Durable silica treatment does tend to reduce the gloss of pigments, probably by making it more difficult to develop gloss through the final milling step. The durability of the silica layer and the amount of energy needed to develop gloss are proportional to the amount of silica in the layer.
Hydrous aluminum oxide is probably the most common treatment on titanium dioxide pigments. It can be deposited from sodium aluminate, which is reacted with acid; or aluminum sulfate, which is reacted with a base. Alumina can also be deposited from a combination of sodium aluminate and aluminum sulfate, which neutralize one another. The morphology of the alumina coating depends on the deposition conditions. The alumina tends to deposit as pseudoboehmite in basic solutions. Alumina deposits in an amorphous form in the acid solutions. The transition pH is temperature-sensitive and tends to shift to lower pH at higher temperature.
The hydrous alumina particles on the pigment surface reduce the particle-particle attractive forces and improve dispersibility. The alumina also acts as a spacer for the particles and improves gloss and opacity of the pigment. The amorphous alumina can provide a moderate amount of durability, and does not seem to provide as effective spacing as the pseudoboehmite alumina. When multiple treatment layers are deposited on a pigment, alumina is most often the final layer.
Many pigments are treated with an organic coating, but some pigments contain no organic treatment. This treatment can be added into the wet washed pigment before drying, onto the dry pigment, or onto the pigment during the final milling step. The organic materials used are most often polyols, amines or amine salts. Silicones and siloxanes are commonly used to produce hydrophobic pigments for plastics applications. Organic treatments are used to improve compatibility with the coating or plastic and to improve dispersion. Organic coatings also reduce agglomeration during storage of the titanium dioxide. They reduce water absorption on the titanium dioxide surface, which leads to a lower volatile content for plastics processing.
After pigment treatment is complete, the pigment is typically subjected to a final milling step. This is normally fluid energy milling, or micronization. The intensity of milling that is needed to produce the optimum pigment properties depends on the base pigment, initial milling, and treatment. If initial milling is used, this step serves to break up the agglomerates formed during treatment. Without initial milling, micronization must be intense enough to break up agglomerates formed in the oxidizer or calciner.
Example
The development of an exterior coatings grade will be used as an example. For this application, the most important targets to be determined are gloss and durability. If an extremely durable pigment is needed, the treatment will need to be a heavy dense silica treatment. This treatment is likely to yield only a moderately high gloss. A highly durable pigment will require a smaller amount of dense silica treatment and will yield a high-gloss pigment. A universal-grade pigment with moderate durability and excellent gloss would be best treated with zirconia. We will assume that the grade under development needs to have both high gloss and high durability. Therefore, a dense silica treatment would be a good starting point. About 50-60% of the silica found in the most durable grades develops the best gloss with this level of silica, intense pre- and post-treatment milling should be used.Alumina would be chosen as the final layer over the silica treatment. The level of alumina would depend on the gloss, tint strength and opacity needed in the pigment. Low alumina levels yield better gloss and lower tint strength than higher levels. A good starting point would be a balance of these properties. A polyol would be the best starting point for the organic treatment on a coating-grade pigment.
As a first step, one or more pigments would be treated in the laboratory to determine if the starting point was close enough to the desired pigment for optimization. After the general treatment scheme was chosen, design of experiments would be used to fully optimize the treatment. The optimized treatment would then be taken to the plant for a test. If the resulting pigment met the targets and exhibited no processing problems, the pigment would be commercialized.
Links
Looking for a reprint of this article?
From high-res PDFs to custom plaques, order your copy today!