UV Protection Put to the Test
The Triple Combination
As in many other areas, the natural look of wood has become trendy. It requires colorless coatings which, until now, have not been recognized as sufficiently equipped to protect wood from the elements because they failed prematurely to fulfill their function.1 However, the latest research in this field shows that the correct combination of light stabilizers makes it possible to produce transparent, colorless clearcoats with extraordinary brilliance and very good long-term UV protection.Some Wood Basics
As a naturally grown material, wood reacts to temperature and especially to differences in ambient humidity by shrinking, expanding, warping, cracking or winding. In short, wood is alive, and its movements in the three different directions vary in strength. However, wood does follow certain regularities and, if these are taken into due consideration, its tendency to “move” can be successfully controlled. The most important factor is the proper drying of wood, a process that takes place in large kilns during which moisture is removed from the wood until its moisture level is equal to the average temperature of rooms with average heating (20 ºC room temperature and 45 - 55% humidity). The proper balance is achieved when the wood has moisture content of 8 - 10%. Only after the completion of this step, may wood be processed.The availability of a large variety of wood types with a wide range of properties and color shades offers a suitable material for almost every application. The possible applications of wood are determined by two factors: its mechanical properties and the composition of ingredients. Wood contains 25 to 30% lignin, which fills the cell walls between cellulose components and bonds them together. While lignin itself is insoluble in water, UV radiation separates it into water-soluble components that can be washed out when the wood moisture content changes. This makes the upper layers of cellulose fiber lose their cohesion, so they can no longer provide a suitable substrate for coatings. As a result, large pieces of varnish and coating are detached. As air penetrates the cracks between the cellulose fibers, the reflection of light at the borders makes the damaged coating appear cloudy and milky.
Completely weathered wood surfaces look silver-gray, which is the original color of cellulose. Depending on the type of wood, UV radiation can penetrate up to 2 mm into the wood surface.2
In order to permanently protect wood from damage in outdoor applications, effective protection is necessary. Usually special coatings are applied onto wood. The hydrophobic coating film repels water and environmental influences from the wood surface. The addition of biocides protects the wood against insects and microbial attacks. Two groups of stabilizers have been specially developed for the light protection of coatings, which are suitable for protecting both the substrate and the coatings. These two groups are sterically hindered amines (also referred to in the following text as HALS = Hindered Amine Light Stabilizers) and UV absorbers.
HALS Provide Surface Chemical Protection
Light stabilizers of the sterically hindered amine type are, with few exceptions, derived from tetramethyl piperidine. Under photo-oxidative conditions, HALS compounds generate stable nitroxyl radicals that can serve as a trap for carbon-centered radicals of the alkyl-type evolving from resin degradation. According to Denisov, these hydroxylamine ethers react further with (polymer)peroxyl radicals to form relatively stable (polymer)peroxides, or a ketone and an alcohol, while releasing the effective nitroxyl radical again so that one nitroxyl radical can neutralize up to several hundred radicals. Stabilization with HALS is a chemical process.The optimal distribution of the HALS in the binder is crucial for its effective use. When sunlight hits the coating, the radiation density is highest right at the surface. Consequently, this is where the formation of protective nitroxyl radicals for light stabilization is most needed. The deeper the sunlight penetrates the coating, the weaker the radiation density, because it is being absorbed by the binder, and, in some cases, by an additional UV absorber. In the deeper layers the likelihood of light-induced decomposition decreases continuously, and so the role of the sterically hindered amines in these areas loses importance. The radical scavengers prevent the photolytic decomposition of the binder, indirectly shielding the wood below. The coating lasts longer, and the substrate is also protected for a longer time.
All of the tested radical scavengers are sterically hindered amines. HALS 1 is a liquid, 100%-active compound; a second product consists of an 80%-solution HALS 2 in N-methyl-2-pyrrolidone (NMP). The third of the tested radical scavengers, HALS 3, is photo-reactive and is added as an aqueous dispersion. This product, based on a malonic acid derivative, has not only the typical functional groups of a sterically hindered amine, but it also has an UV absorbing system of conjugated double bonds.
Physical Absorption Provides Deep Layer Protection
The function of UV absorbers is based on the physical absorption of light, which protects both the substrate and the coating from the high-energy radiation of the sunlight. According to the Lambert-Beer Law:- E = e* c*d
E = extinction,
e = extinction coefficient [l/Mol cm],
c = concentration [Mol/l], and
d = film-thickness [cm].
The light absorption of a medium depends, among other factors, on the concentration of the UV absorber and the distance that light rays pass through the medium. The concentration of the light absorber and the thickness of the coating (or their multiplication product, for that matter) should not fall below a certain minimum in order to provide safe protection of the substrate by way of absorption. The deeper the UV radiation penetrates the coating, the more absorption is taking place, or the stronger the effect of the UV absorbers. Conversely, the protective effect of the UV absorber is the lowest at the surface of the coating.
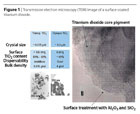
Inorganic UV Absorbers
Titanium dioxide white pigments are designed by their particle size for optimum light scattering in the visible region. For high light refraction, a maximum refractive index is a prerequisite. However, this is not sufficient - the particle size has to be fine-tuned as well. Unlike standard-sized titanium dioxide pigments, ultra-fine titanium dioxides, which were initially developed for transparent UV protection, ideally do not scatter visible light.However, standard-size and ultra-fine titanium dioxides have the same refractive index, so it is the finest particle size that is responsible for the transparency of the coating. The finer the dispersed particles the more transparent the coating. Thus, for transparent UV absorption the finest grades in optimum dispersion are applied. It has to be noted as well, that certain ultra-fine titanium dioxides grades with selected “intermediate” primary particle size do scatter blue light. This is why these nanosized TiO2 particles are used in metallic coatings and other pigmented systems in which sophisticated color effects are desired.
Titanium dioxide absorbs UV radiation and serves as a “photo-semiconductor.” This property is practically independent from the particle size. Energy absorption leads to the transfer of an electron from the valence band to the conduction band. This process creates two mobile, charged particles: the negatively charged electron in the conduction band and the positive charge (hole) in the valence band. The formation of this pair of charges is summarized under the term “excitons.” As described above for the organic UV absorbers, UV radiation is absorbed and transformed into thermal energy. However, unlike organic substances, the chemically inert titanium dioxide does not decompose, so that the long-term stability of the entire system is increased.
In order to “tame” the UV radiation and prevent it from causing damage by forming radicals, foreign ions such as trivalent aluminum (Al+3) are incorporated into the inner crystal lattice of TiO2. In the crystal, these ions tend to take the lattice positions of the titanium ions, acting as traps in which the excitons tend to recombine.3 In addition, the surface of the pigment is encapsulated with an inorganic coating consisting of aluminum oxide (Al2O3) and/or silica (SiO2). Figure 1 shows the transmission electron microscopic image (TEM) of a surface-coated pigment. In addition to the interplanar spacing of the crystalline TiO2, the amorphous surface coating is visible. This stabilizing technology is generally used for photo-resistant and weather-resistant white pigments and inorganic UV absorbers. Typical white pigments have a crystallite size of 200 to 350 nm. They are available as anatase or rutile pigments. The inorganic TiO2-based UV absorbers have a primary particle size of 10 to 50 nm and are usually offered as rutiles with a high-surface coating.
These surface coatings make it possible to modify not only the photoactivity but also the optical and colloidal properties of the white pigment. It is also a must to achieve good dispersibility of the ultra-fine titanium dioxides. For this reason, the pigments are treated with an additional organic substance.
The two types of products used in this case are ultra-fine titanium dioxides in the rutile modification (both containing > 99% rutile) and mainly differ in their primary crystal size and doping. The type that was specially developed for transparent wood coatings has a primary crystal size of ~10 nm and a specific surface of ~110 m2/g (hereafter called “Mikrorutile 10 nm”). The second product has a primary crystal size of 15 nm and accordingly a smaller specific surface area of ~70 m2/g (Mikrorutile 15 nm).

Organic UV Absorbers
The most common UV absorbers for coatings are 2-hydroxyphenyl benzotriazoles, 2-hydroxy-benzophenones, 2-hydroxy-phenyltriazines and oxalanilides. Salicylates, formamidines and cyanacrylates may also be used on an individual basis.The photoprotection mechanism resides in the ability to form reversible intramolecular hydrogen bonds between an o-hydroxyl group and a heteroatom such as nitrogen. Upon absorption of UV-light, a p-electron is promoted to an excited singlet state and via intersystem crossing, to an excited triplet state followed by ESIPT (Excited-State Intramolecular Proton Transfer) or “enolization” with proton transfer taking place along the intramolecular hydrogen bond. The quinonoid intermediate tautomerizes through a rapid non-radiative relaxation process (heat) and return proton transfer, thus regenerating the original ketone. This process, called the keto-enol tautomerism mechanism, is nothing but a continuously repetitive proton transfer.
Due to their bathochromic shift of the absorption maximum toward the long-wavelength spectrum, halogenated benzotriazoles are particularly suited for the protection of photo-sensitive wood. The halogen substituent modifies the electron density and expands the delocalized electron system. As a result, less energy is required to bring the electrons into the excited state - the absorption of radiation is shifted towards lower frequencies. In this case, the absorption maximum reaches the areas of the visible sunlight, thus more efficiently protecting the lignin from the damaging effect of this type of radiation.
In this study o-hydroxyphenyl benzotriazole was tested in two variants: non-substituted in liquid form and a Cl-substituted crystalline type, which was applied in its preparation as an aqueous dispersion. Figure 2 shows the UV transmission of all applied UV absorbers in concentrations of 1.0%. The concentrations always relate to active UV stabilizer on solid resin. The addition of liquid organic UV absorbers did not lead to opacity, but the addition of powder additives does do so. In the case of the halogenated benzotriazole this opacity disappeared almost completely as soon as the dispersed organic UV absorber had been completely diluted in the binder.
UV C radiation is not present on the ground, since it is filtered off by the ozone layer in the upper atmosphere. UV B, and to some extent also UV A radiation, is absorbed by the binder and destroys the polymer of the coating. Wood, especially lignin as one of its major components, is degraded by UV B, UV A and wide parts of the visible radiation.

Formulas, Possible Combinations and Testing Methods
To determine the optimal light stabilization formula, a waterborne clearcoat based on a styrene-free acrylic emulsion was used in testing, into which different light stabilizers were dispersed. The coating ingredients included commonly available commercial solvents, biocides, antifoaming agents and wetting agents from different manufacturers (Table 1). For light stabilization, proven light stabilizer types from various manufacturers were used. Inorganic and organic UV absorbers and HALS were tested individually, and in double and triple combinations. The only exception was made for HALS compounds, as experience has shown that these products do not yield sufficient results if they are not combined with an UV absorber. The stabilizer concentration in the coating mixture ranged from 0.5 to 2% by wt. of the total formula, with the entire amount of stabilizers never exceeding 4%.
For the weathering tests, 7x28-cm pieces of North European pine were treated with wet coats that had been stabilized with different stabilizer additives. After drying, the coated panels (dry coat thickness around 40 µm) were exposed to natural weathering. The exposure at a location 50 km north of Düsseldorf, Germany, consisted of a 9-month and a 15-month test series. The testing parameters included gloss (20°, 60°), transparency, yellowing (Delta b*), decrease of brightness (Delta L*) and reddish shade (Delta a*), as well as an evaluation of the general stability and fouling of the coatings. These parameters were measured every six weeks.

The Perfect Mix
By far the best results were achieved by the triple combination of all colorless light stabilizers: 0.5% ultra-fine titanium dioxide (Mikrorutile 10 nm), 1% dispersed HALS with 1% organic UV absorber using the halogenated type in dispersed form (wt% of the total formula and 40 µm dry coating thickness). Clearcoats containing this combination offer good long-term UV protection while featuring excellent transparency and colorlessness. Figure 3 illustrates the permanent stability of the coating, which did not show any weathering even after 15 months of outdoor exposure and remained colorless and transparent.This outstanding protection provided by this triple combination can be explained by a close look at the different light stabilizer types. Each light stabilizer, when studied by itself, works differently. The test results described in this article have illustrated that every light stabilizer has different properties. Using the right mixture creates a synergetic effect with optimal results.
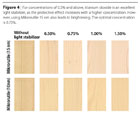
Organic UV absorbers also have a very positive effect on transparency. Coatings with organic stabilizers show exceptionally good transparency, both the liquid and the dispersed variants, although the dispersed types initially showed some cloudiness that disappeared when the stabilizer was completely dissolved in the binder. Even in long-term exposure to radiation, the transparency is not affected. However, organic UV absorbers tend to yellow, a drawback that can be significantly improved by adding a HALS. Adding radical scavengers also substantially improves the resistance of coatings. This is clearly illustrated by the samples in Figure 5. The coating containing this combination did not show any weathering neither after artificial nor after outdoor weathering. For this reason, organic UV absorbers should never be used alone, but always in combination with HALS.
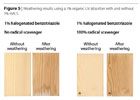
Summary
The outstanding effect of the triple combination is a result of the positive properties of the different light stabilizers. UV absorbers offer the necessary protection deep inside the coating. Here, ultra-fine TiO2 provides especially long-term and good UV protection. The optimal choice is ultra-fine titanium dioxides with a particle size of 10 nm and in a concentration of 0.75% (of the total formula).Organic UV absorbers support their inorganic counterpart, which work in the deeper layers of the coating. They also make it possible to produce transparent clearcoats. The variant of choice is halogenated benzotriazole, which is added to the coating mix in dispersion form.
Sterically hindered amines provide additional stabilization by transforming destructive UV radiation into harmless heat already at the surface. They also minimize the yellowing tendency of organic UV absorbers, thereby making a significant contribution to the brilliant visual effect of the clearcoat.
Based on these results, new possibilities are opening up for the wood industry. For the first time, it is possible to provide woods, even those in tough outdoor exposure, with permanent UV protection without affecting their color. Depending on the application, several options are available. Inorganic UV absorbers can be viewed as “specialists” for exterior applications because they offer the most effective and easiest long-term UV protection and do not decompose even under continuous weathering. On the other hand, organic UV absorbers in combination with HALS are the first choice for applications that require utmost transparency and brilliance, for example in the furniture industry. Clearcoats with the triple combination feature the highest transparency and brilliance while providing long-term light stabilization, so they are a primary solution for sophisticated applications.
Looking for a reprint of this article?
From high-res PDFs to custom plaques, order your copy today!