Custom Oven Solution Divides to Conquer Aerospace Manufacturer's Increased Capacity Challenge
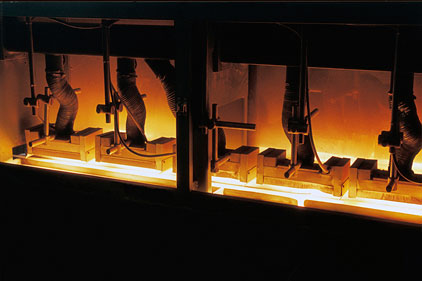
Carbolite was able to modify its standard design to precisely meet an aerospace manufacturer’s requirements.

When a large, blue chip aerospace manufacturer’s coatings plant based at Filton in Bristol, UK, faced the need to expand capacity to handle increasing demand, the organization soon realized that the Carbolite ovens it was using were simply no longer large enough to satisfy the new production output requirement.
The need to expand capacity at the aerospace manufacturer’s combustion and castings operation called for a new, much larger paint stoving and curing oven that would meet the need for a strict internal performance specification or ‘Statement of Requirement’ (SOR) as well as conform to the specifications of the aerospace heat treatment regime of NADCAP/AMS 2750D Class 2.
An initial assessment of the challenge suggested that one of the heavy-duty industrial ovens from Carbolite’s LGP (large general purpose) range looked to be the ideal solution to the increased capacity headache. Carbolite’s LGP6 2700 provides a durable, stainless steel interior with 2,700 litre capacity and a maximum operating temperature of 600°C. The system’s powerful horizontal airflow offers excellent uniformity.
On further review of the requirements, it quickly became clear there was a key, compelling obstacle to installing a standard LGP6 2700 oven. Put simply, the size of the oven required would not fit through the aerospace manufacturer’s workshop doors. Ultimately the tight space requirements did not prove insurmountable because all Carbolite ovens are designed and built to order in the company’s own UK factory, which means that design modifications can be made simply and precisely.
By applying the principle that the simplest solutions are frequently the best, Carbolite simply cut the oven design in half. Once built, the two modules were re-assembled in order to enable the customer to view, test and approve the oven’s performance at Carbolite’s factory. On approval the oven was then re-split into separate halves for delivery and installation. At the Filton site Carbolite’s engineering team then reunited the two halves in their final working location.
Carbolite also supplied a range of custom options, which included a 12 channel chart recorder, independent over temperature protection, a tower light to signal the process cycle and over temperature status, explosion relief panels, forced cooling, exhaust dampers as well as a reinforced base for additional load carrying. An internal panic switch was also fitted to prevent entrapment. Once activated, the switch shuts down the oven and sounds an alarm.
Commenting on the application, Carbolite’s Chief Engineer, Noel Wilson, said, “It is the ability to modify our standard designs to precisely meet customers’ requirements that sets Carbolite apart from other manufacturers”.
Carbolite’s systems feature chamber sizes up to 10,000 litres and maximum operating temperatures to 1800°C.
For sales and technical information, e-mail info@carbolite.com or visit www.carbolite.com.

When a large, blue chip aerospace manufacturer’s coatings plant based at Filton in Bristol, UK, faced the need to expand capacity to handle increasing demand, the organization soon realized that the Carbolite ovens it was using were simply no longer large enough to satisfy the new production output requirement.
The need to expand capacity at the aerospace manufacturer’s combustion and castings operation called for a new, much larger paint stoving and curing oven that would meet the need for a strict internal performance specification or ‘Statement of Requirement’ (SOR) as well as conform to the specifications of the aerospace heat treatment regime of NADCAP/AMS 2750D Class 2.
An initial assessment of the challenge suggested that one of the heavy-duty industrial ovens from Carbolite’s LGP (large general purpose) range looked to be the ideal solution to the increased capacity headache. Carbolite’s LGP6 2700 provides a durable, stainless steel interior with 2,700 litre capacity and a maximum operating temperature of 600°C. The system’s powerful horizontal airflow offers excellent uniformity.
On further review of the requirements, it quickly became clear there was a key, compelling obstacle to installing a standard LGP6 2700 oven. Put simply, the size of the oven required would not fit through the aerospace manufacturer’s workshop doors. Ultimately the tight space requirements did not prove insurmountable because all Carbolite ovens are designed and built to order in the company’s own UK factory, which means that design modifications can be made simply and precisely.
By applying the principle that the simplest solutions are frequently the best, Carbolite simply cut the oven design in half. Once built, the two modules were re-assembled in order to enable the customer to view, test and approve the oven’s performance at Carbolite’s factory. On approval the oven was then re-split into separate halves for delivery and installation. At the Filton site Carbolite’s engineering team then reunited the two halves in their final working location.
Carbolite also supplied a range of custom options, which included a 12 channel chart recorder, independent over temperature protection, a tower light to signal the process cycle and over temperature status, explosion relief panels, forced cooling, exhaust dampers as well as a reinforced base for additional load carrying. An internal panic switch was also fitted to prevent entrapment. Once activated, the switch shuts down the oven and sounds an alarm.
Commenting on the application, Carbolite’s Chief Engineer, Noel Wilson, said, “It is the ability to modify our standard designs to precisely meet customers’ requirements that sets Carbolite apart from other manufacturers”.
Carbolite’s systems feature chamber sizes up to 10,000 litres and maximum operating temperatures to 1800°C.
For sales and technical information, e-mail info@carbolite.com or visit www.carbolite.com.
Looking for a reprint of this article?
From high-res PDFs to custom plaques, order your copy today!