Turning on a Dime
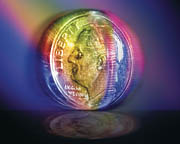
It's 10 a.m. and an unannounced truck has just pulled up. Inside are 50 metal computer cabinets that need to be powder coated in less than 24 hours. What could be next? It might be later that day when 50,000 small, wire-formed parts for the telecommunications industry are delivered for coating. For Teknicote (Cumberland, RI), a powder coating job shop with more than 100 employees, consistent production scheduling often takes a back seat to meeting its customers' just-in-time manufacturing requirements.
"Typically about half of what comes in from our customers is without notice," says Ken Barthelemy, vice president of engineering for Teknicote. "We might not know what or how much is coming, but we do know that we have to turn it around quickly."
Lean manufacturing schedules cause order sizes to decrease while order frequency increases. The majority of Teknicote's competitors consist of much smaller shops that can quickly react in such an environment.
"We have to be as nimble as our smaller competitors to keep up with our customers and keep our costs and our customers' costs down," says Steve Dolan, Teknicote's president. "In a slower economy, flexibility and being cost competitive become even more critical to maintaining our business."
Teknicote also tries to differentiate itself from smaller shops through its engineering expertise-taking on jobs with tight requirements, many specifications and difficult-to-coat parts.
With its largest automated powder coating line relying on aging equipment, Teknicote found it increasingly difficult to meet customers' lean schedules. Rather than just replacing equipment, the company set out to transform its entire operation. It consolidated three facilities into one 100,000-square-foot building, reorganized its operating structure and began the ISO approval process.
The move to upgrade technology began with the powder coating system. Teknicote wanted a system that would increase productivity by reducing color-change time for faster turns on smaller lots, while providing the capability to increase throughput on larger batches and increase transfer efficiency.
Its existing system required one hour for color changes. With four to five color changes per shift, Teknicote was running parts as little as 50% of the time. Further, powder contamination was a weekly occurrence, leading to further downtime and hundreds of pounds of wasted powder.
"Those are scary numbers when you really start looking at them," says Dolan. "We had to decrease time for color changes and improve powder usage."

The solution
Teknicote evaluated the latest powder coating system technology, ultimately choosing Nordson's (Westlake, OH) ColorMax powder spray system for its quick color change and powder usage capabilities. Teknicote and Nordson moved quickly to install the new system, having it fully operational and in production in only 11 days.
Teknicote has more than 400 customers and may coat materials for as many as 50 customers on any given day. The company stocks 200 colors and typically runs 20 colors on its line routinely, with DuPont (Houston), Morton Powder Coatings (Reading, PA), Protech (Canada) and Sherwin-Williams (Cleveland) supplying the majority of the powder. Coated materials include steel, zinc, aluminum and brass.
Parts enter the powder coating operation after a three-stage pretreatment process. After parts exit the dry-off section of the oven, they are conveyed past part-identification sensors that signal preselected parameters for gun triggering, gun positioning and parts-recognition system controls. Once inside the ColorMax booth, 12 automatic Nordson powder guns apply powder at a customer-specified thickness.
Manual post-touchup is performed primarily with the ColorMax booth when reclaiming. The Nordson Versa-Coat booth is used for very short runs or for very difficult parts that need either pre- or post-touchup. Parts then enter a gas-fired convection oven for curing, typically around 400°F. Because of the variety of parts coated, curing times can range from 6 to 18 fpm.

Color-change time cut two-thirds
Color changes that used to take an hour now take 15 to 20 minutes. That means Teknicote can quickly shift gears when unannounced parts arrive or short batches need to be coated to meet a deadline, Barthelemy says.
"Our booth and guns used to be the bottleneck," he says. "Now they're ready in 10 minutes, with parts being coated within 15 or 20 minutes. "We've gone from 30 to 50% downtime with our old system to only 15 to 20% downtime. That's critical when we're scrambling to meet customers' needs."
Barthelemy adds that downtime could be further reduced if line speed were consistent, but with the variety of parts coated and the vast differences in sizes, the line may run at 8 fpm for one job and 14 fpm on another.
A typical week is anything but typical, which is why the newly found versatility and increased throughput have become such a boon. Teknicote may coat hundreds of thousands of parts in a week, running 10,000 pieces per hour or 100 pieces per hour on the same line, depending on the size of the part and the job.
In addition, jobs might run for 30 minutes or for eight hours.
Quick color changes are made possible through a number of features, including dual cyclones with hinged sections that open for easy inspection and cleaning, and the absence of conventional ductwork between the booth and cyclones.
"Without ductwork, there's one less area to be inspected and cleaned," Barthelemy says. "And we have full access to the cyclones, so we can see inside to blow it out quickly. Overall, it's very easy to clean."
Automatic gun setup and positioning have also proven to be big benefits because Teknicote can run the same color on multiple parts, regardless of their complexity, without manual intervention to change gun settings. That, along with the size of the line and the versatility of the equipment, gives the company the ability to run a wide mix of parts to keep the line filled-whether it's small wire-formed parts, large computer cabinets or metal tubes for car-rack-accessory systems.
Teknicote has also greatly reduced the amount of powder wasted. Oversprayed powder is recovered inside the booth and then recycled through the cyclones for 98% efficiency of powder usage without cross contamination of colors. Due to the efficient performance of the cyclones and a decreased amount of powder in process, Teknicote now achieves system efficiencies above 95%.

Exceeding expectations
Teknicote was affected by the same economic slowdown that most companies experienced in 2001, just as its new system was about to come on-line. The company was forced to drop its second shift as customers cut back. After a few months with the new system up and running, Teknicote now sees the benefits paying off through more work.
Customers are still receiving the consistent quality they expect from powder, while Teknicote has become more competitive in its pricing and turnaround times, especially on smaller jobs.
"We used to have difficulty being competitive on smaller jobs because we had to build in downtime," says Alan Nathan, Teknicote's chairman. "By maximizing our line speed through faster color changes and higher densities, we can compete even on small lots. And small jobs often lead to bigger ones."
Teknicote brought back its second shift in the spring of 2002, even as other job shops in New England continued to be slow. The ability to better meet the lean schedules of its customers, combined with its engineering capabilities and recent ISO certification, have Teknicote poised for the future after 30 years in the powder coating business.
"We can consistently and quickly react to any size and type of job, which really sets us apart," says Nathan. "It doesn't matter if it's a small batch or a trailer load, we now have the flexibility and capacity to coat a tremendous variety of parts with consistent quality and fast turnaround."
Ken Kreeger is director, North American Powder Sales, and an Industrial Paint & Powder Editorial Advisory Board member.
Looking for a reprint of this article?
From high-res PDFs to custom plaques, order your copy today!