RO Upgrade Improves Production, Quality at Texas Finisher
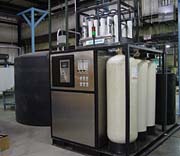
Rangaire produces range hoods with a class A finish at a rate of about 6,500 or more per shift. The cosmetic requirement of this product is high; excellent gloss and zero defects on appearance surfaces are mandatory. Pure water for rinsing is one of the keys to good gloss and adhesion, as well as final removal of particulate contamination after phosphating.
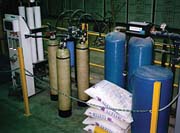
The problem was that the RO system was undersized by design when it was purchased almost 12 years earlier, the idea being that the holding tank would provide enough capacity so that the system could keep up during the day and catch up at night. When Rangaire added a second production shift, the RO immediately was a problem.
Another problem came up one day when suddenly the phosphate stage became impossible to control, cleaning began to suffer and the final rinse TDS (total dissolved solids) went to more than 1,000 parts per million (ppm). After several hours of head scratching and other troubleshooting techniques, it was discovered that the city had activated an old well to keep up with capacity. During the next several weeks, every time the city activated that specific well, the plant manager got complaints from the paint department and immediately called the city to request they turn it off. The RO system was removing some of the solids coming from that source, but the loading was so high (more than 3,800 ppm solids) that the system just could not handle it; water production would fall, and the product water quality became unacceptable.
Rinse water in all washers hits an equilibrium at which there is as much contamination coming into the tank as there is going out via overflow and dragout. The washer system also was modified to counterflow cleaner water upstream to earlier stages, thus saving the pure makeup water for the later stages where it is most important. It turns out that filling your washer with pure water only changes the starting point - the equilibrium is the same no matter where it starts.

R3 Technologies started by testing the entire system to be sure all the components were capable of running at the higher level, then built a strategy to upgrade the system by adding capacity where needed. A larger high-pressure pump, more membranes, new plumbing and changes to the pretreatment were necessary to accomplish the upgrade. The control system, one of the most expensive parts of the system, was sufficient without changes. A 480 V motor starter was added to run the larger pump motor instead of the relay that had been used to run the smaller motor before.
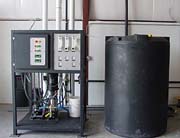
The work took place over a weekend and on Monday morning the rebuilt system was producing more than 12 gal/min of fresh RO water to replenish the halo and overflows. After a little adjustment, the system settled in to a 10 gal/min production, keeping up with the needs of the halo and overflows. This upgrade project cost less than a new system and made a smaller disturbance in the plant than installing a whole new system may have. The lead time was short, and because the controls were not changed there was very little learning curve or re-training after the rebuild was complete. Rangaire was able to upgrade its RO system at less than half the cost of installing a new system - a winning proposition in these days of doing more with fewer resources.
R3 Technologies can be reached at 817-313-6439, or visit www.R3Web.com.
Looking for a reprint of this article?
From high-res PDFs to custom plaques, order your copy today!