The Value of Operator Training
Perhaps the greatest challenge facing manufacturers in their attempts to maintain efficient finishing is finding and keeping good employees. From an economic and continuity standpoint, it’s important to focus on keeping good spray operators rather than on training new ones. The finish that operators apply to a product is likely the first thing a customer notices, and efficient finishing can save a lot of time and money.
Though spray operators have the greatest impact on application efficiency, most receive little, if any, formal training on the equipment they use. As a result, application equipment is often used inefficiently and an excessive amount of coating material is sprayed.
Variables such as equipment setup and maintenance also have significant effects on finish quality, transfer efficiency and film-build efficiency. Application improvements will help a business reduce its VOC emissions, hazardous and nonhazardous waste generation rates, regulatory burden and production costs.
Often, a few, simple changes can produce significant results. Following are two case studies that exemplify the potential that exists with operator training and process changes.
Significant solvent reduction
Process Training personnel from the Iowa Waste Reduction Center (Cedar Falls, IA) visited a northern Wisconsin manufacturing facility that was attempting to improve its painting process. The facility had just switched from conventional to HVLP air spray guns. However, after the change, production personnel reported an increase in paint consumption.The coatings sprayed at the facility included a fast-dry gray oxide primer and a urethane alkyd gloss enamel topcoat. Out of the can, the solids content of the primer and topcoat (by volume) were 38% and 42%, respectively. However, for sprayability, the coatings were reduced before application. Although no standard operating procedure was in place for coating reduction, the primer was typically reduced by a ratio of 1:1, while topcoat reduction was approximately three parts topcoat to two parts reducer. Measurements collected by the training staff indicated a viscosity of 18 seconds on a #2 Zahn cup (at 70?F) for both the primer and topcoat as applied.
Pressure-feed HVLP spray guns operating off pressure pots were used for the facility’s finishing work. Both the primer and topcoat spray guns were equipped with a 0.055-inch fluid needle/nozzle/aircap combination. The fluid-pressure settings were 10 psi for the primer and approximately 8 psi for the topcoat. Atomizing air pressures were set at approximately 35 psi at the pressure pots. In general, the operating parameters and equipment were in relatively good shape.
Process modifications
After reviewing the company’s painting operation, a few simple modifications were made. First, a standard procedure for primer and topcoat reduction was developed. Using the degree of reduction recommended by the coating manufacturer, the primer was reduced at a ratio of one part solvent to five parts paint.At this reduction, the viscosity of the primer was 43 seconds on a #2 Zahn cup. Because of the primer’s higher viscosity (and higher solids content), the fluid needle/nozzle size of the HVLP gun was increased from 0.055 inch to 0.086 inch. This made it possible to spray the material with the same make of spray gun at a fluid pressure of 12 to 13 psi and an atomizing air pressure of 35 psi (at the pot).
The topcoat was reduced by a 10% (by volume) solvent addition, which produced a viscosity of approximately 34 seconds on a #2 Zahn cup. Again, to handle the higher viscosity material and maintain an adequate fluid delivery rate, the HVLP gun was equipped with a 0.086-inch needle/nozzle/aircap combination. The topcoat material was also sprayed at a fluid pressure of approximately 13 psi and an atomizing air pressure of 35 psi.
During the system changes, training staff informed facility personnel about the modifications and why they were made. Finish quality requirements were considered when making adjustments to the system.
After modifying the facility’s painting process, paint line personnel and production staff were told why the modifications were made and what benefits were anticipated. Spray operators and supervisory personnel were also given some instruction in spray technique, both in the classroom and in the spray booth.
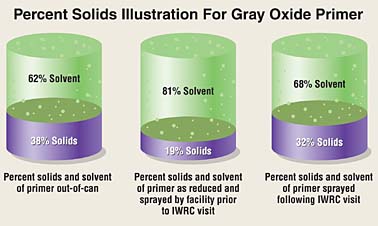
Results and benefits
The site visit’s most notable achievement was a decrease in the amount of solvent necessary for coating reduction and the increased solids content of the material sprayed. The 1:1 reduction ratio used for the primer prior to the visit meant one gallon of solvent was mixed with one gallon of primer to obtain a sprayable coating. Following the visit, the sprayable primer was prepared by mixing 0.2 gallon of solvent to one gallon of primer, representing an 80% decrease in the amount of solvent used to obtain a sprayable primer.Figure 1 illustrates the solids content for the primer out of the can, reduced at a 1:1 ratio and at a 1:5 ratio. As shown, the primer sprayed at the facility prior to the IWRC site visit consisted of 19% solids and 81% solvent (by volume) after reduction. By limiting the solvent addition to the manufacturer’s recommended 1:5 reduction ratio, the percent of solids climbed to 32% while the solvent content dropped to 68%.
Similar results were obtained for the topcoat. Instead of mixing 0.67 gallon of solvent with one gallon of topcoat, the facility began to mix 0.10 gallon of solvent with one gallon of topcoat. This represents an 85% decrease in solvent usage.
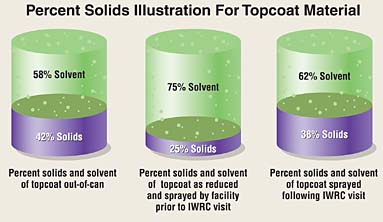
In a follow-up of the facility’s progress, the manufacturing engineer for the Wisconsin facility reported a decrease in paint consumption and VOC emissions after the training visit. It was determined that 25% less paint, with comparable production rates, was then being used at the facility.
VOC emissions were 27% less for the month following the training staff’s visit, even though the facility’s production rate was higher.
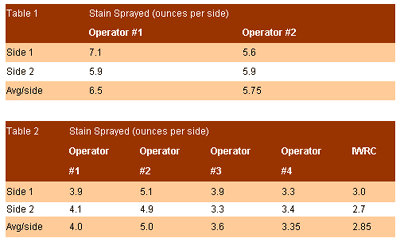
Greater control, less waste
The training staff visited an Iowa wood-finishing facility to help improve the application efficiency of its staining process. The finishing material sprayed at the facility consisted of a water-reducible wiping stain with a viscosity of approximately 34 seconds on a #2 Zahn cup (at 71?F). A conventional air spray gun operating off a pressure pot was used to apply the stain. A cloth rag was then used to wipe down the stain and work it into the wood grain to achieve the desired finish.During the site visit, the following information was noted about the facility’s operating parameters:
- The spray gun was equipped with a 0.046-inch fluid nozzle.
- Fluid pressure supplied to the gun was set at 90 psi.
- The atomizing air pressure to the spray gun was unknown. Air to the gun was fed off the main compressed air line without the use of a regulator or pressure gauge.
- The fluid needle adjustment valve on the gun was nearly closed off in an apparent effort to gain some control over fluid delivery.
Spray operators then used the existing setup to stain hollow-core wood doors. Table 1 indicates the volume of material used to finish a door under the facility’s previous operating parameters.
After staining the doors using the existing equipment and setup parameters, the following modifications were made to the finishing process:
- Fluid pressure from the pressure pot was reduced to 15 psi.
- The conventional air spray gun was replaced with an HVLP air spray gun with a 0.087-inch fluid nozzle/needle/aircap combination.
- The atomizing air to the gun was plumbed so that it could now be controlled (i.e., regulated and monitored). The atomizing air pressure was set at 40 psi (at the wall).
Spray technique, degree of atomization and a “plan-of-attack” were discussed. Facility employees were encouraged to practice triggering the gun, maintain good gun orientation and orient the spray pattern to better fit the part. Additional spraying tips included partial triggering of the spray gun (a feature not available with the conventional spray gun because its fluid-needle adjustment valve was nearly closed off), target orientation and banding of the part.
Unlike most other finishing processes, coarser atomization was better for this application. It helped keep the stain workable for subsequent wiping and required a low atomizing air pressure (a favorable condition for higher transfer efficiency). The importance of overlap and good gun orientation were evaluated based on the staining procedure and finish quality objectives. Although a 50% overlap of each spray pass was not required because the stain was wiped down, a uniform application of stain made the finishing process less work for employees. A streaked stain application (from poor gun orientation or poor overlap) creates more work during the wiping stage of the process since more effort is required to work the stain and obtain a uniform look.
Operators then finished additional doors using the newly prescribed equipment, settings and suggestions. Table 2 shows the results from one of the finished doors and also includes data collected for a training staff person who finished a door to better demonstrate the benefits of good spray technique.
Results
As indicated in Table 2, gaining control over the process and using good spray technique results in significant materials savings. Depending on the skill of the operator, the material usage numbers of Tables 1 and 2 indicate the amount of stain sprayed could be reduced by anywhere from 13 to 56%.
As the preceding examples show, operators’ performance also has a direct impact on paint/powder consumption, waste generation rates, air emissions and product quality. Ultimately, they have a significant effect on customer satisfaction, production costs and the degree of burden experienced by management in complying with environmental regulations. Whenever possible, the performance of capable spray operators should be acknowledged by work-environment improvements, financial rewards or other incentives.
Iowa Waste Reduction Center’s Process Training Program
The IWRC’s Process Training program focuses on improving efficiency, pollution prevention and environmental compliance at businesses with spray-finishing operations. It is a multifaceted approach based on education, demonstration and research. Components of the program include process training sessions, on-site training and technical assistance, equipment resource availability and outreach efforts. Services are free of charge, confidential and nonregulatory. Equipment resources include:- Two-inch, variable-speed monorail system
- Five-stage recirculating spray washer
- Spray wand pretreatment equipment
- Cross-draft liquid spray booth
- Walk-in powder coating booth
- Batch powder coating booth
- Combination convection/IR oven
- Chemical paint-stripping system
- Assortment of liquid and powder coating application equipment
IWRC’s address is 1005 Technology Parkway, Cedar Falls, IA 50613; phone: 800-422-3109; Web: www.iwrc.org.
Looking for a reprint of this article?
From high-res PDFs to custom plaques, order your copy today!