Faster E-Coating with Advanced Ultrafiltration
Ames True Temper needed to increase its ultrafiltration capacity significantly, but additional floor space was not available. Complicating matters was the need for all new UF equipment to quickly accommodate changes in paint color. The company asked three membrane companies to submit proposals for systems and provide price quotations.
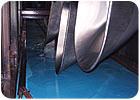
Over the past decade, production has grown rapidly at the Harrisburg, PA, manufacturing plant of Ames True Temper. Ames is the oldest and one of the largest producers of non-powered lawn and garden tools in North America. the plant increased its production of wheelbarrows, shovels, striking tools, hand tools and hundreds of other products by 200% from the units produced a few years ago.
Ames True Temper uses anodic acrylic electrocoat (e-coat) paint to provide corrosion and abrasion resistance to its products. The e-coat system was originally installed in 1977 with a 10-gallon-per-minute (gpm) ultrafiltration (UF) membrane system that employed ABCOR® tubular membrane modules from Koch Membrane Systems (KMS), located in Wilmington, MA. In 1996, the systems were expanded, and the UF capacity was doubled to 20 gpm.
By 2005, Ames once again needed to increase its ultrafiltration capacity significantly, but additional floor space was not available. Complicating matters was the need for all new UF equipment to quickly accommodate changes in paint color.
“We needed to increase the capacity of our electrocoat process,” said Wayne Wright, manufacturing manager at the Harrisburg plant. “Not only did we need to keep up with the higher production levels, but we were applying six different paint colors (up from the single color used in the past) in response to market demand. We currently change the paint color in our e-coat process two or three times each day during our two nine-hour shifts.”
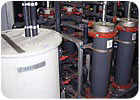
Ames’ original specifications called for use of 8-in.-diameter UF spiral modules. Fortunately, KMS had recently introduced a new 10-in.-diameter module, with 462 ft2 (42.9 m2) of membrane. Using the larger-capacity modules, UF equipment occupying the same floor space can provide nearly twice the UF capacity. Because fewer modules are required, piping, hardware and installation costs are reduced significantly.
The Harrisburg plant commissioned two of the UF systems in October 2005. Each system uses four 10-in. modules to provide a total UF permeate production rate of 80 gpm.
“The decision was not difficult, because no other membrane vendor offered a 10-in. solution,” said Wright. “The 10-in. membranes gave us the capacity we needed with far fewer membranes and much less equipment compared to systems with 8-in. modules. Our two new KPAK systems now sit on the same footprint as the ones they replaced, and yet the new systems provide four times the UF capacity.”
In order to change colors processed by the membrane unit, deionized water is cycled through the UF modules in a simple reverse flushing operation, a process that takes less than 1.5 hours.
“We now have a cleaner paint, which yields a better quality product,” said Wright. “We have been able to increase our production speed by over 10%, and we are now painting at 17 feet per minute, up from 15 feet per minute. Moreover, the higher-capacity ultrafiltration system has significantly reduced the time for conversion from one color to another, as our post rinses can now be filled faster.”
When compared to other spiral membranes, the virtually zero-bypass design of the new UF modules results in higher permeate output relative to paint feed. Maximum energy efficiency is achieved because practically all of the paint circulation flow passes over the membrane surface. The lower paint feed flow requirements means that smaller pumps can be employed to satisfy a given duty. In fact, the new system uses the same pumps as the original system. Since the UF capacity has quadrupled, energy efficiency has improved by 300%.
“We took a bit of a risk as an early adopter of the 10-in. diameter module, but I had confidence in KMS because of our nearly 30-year relationship and because of their expertise and leadership in the electrocoat industry,” said Wright. “We have no regrets and no doubts that the high capacity module will become commonplace for large-scale e-coat operations.”
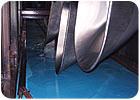
Ames True Temper wheelbarrows enter the e-coat dip tank. The new 10-in. modules have allowed the company to increase production speed by more than 10%.
Over the past decade, production has grown rapidly at the Harrisburg, PA, manufacturing plant of Ames True Temper. Ames is the oldest and one of the largest producers of non-powered lawn and garden tools in North America. the plant increased its production of wheelbarrows, shovels, striking tools, hand tools and hundreds of other products by 200% from the units produced a few years ago.
Ames True Temper uses anodic acrylic electrocoat (e-coat) paint to provide corrosion and abrasion resistance to its products. The e-coat system was originally installed in 1977 with a 10-gallon-per-minute (gpm) ultrafiltration (UF) membrane system that employed ABCOR® tubular membrane modules from Koch Membrane Systems (KMS), located in Wilmington, MA. In 1996, the systems were expanded, and the UF capacity was doubled to 20 gpm.
By 2005, Ames once again needed to increase its ultrafiltration capacity significantly, but additional floor space was not available. Complicating matters was the need for all new UF equipment to quickly accommodate changes in paint color.
“We needed to increase the capacity of our electrocoat process,” said Wayne Wright, manufacturing manager at the Harrisburg plant. “Not only did we need to keep up with the higher production levels, but we were applying six different paint colors (up from the single color used in the past) in response to market demand. We currently change the paint color in our e-coat process two or three times each day during our two nine-hour shifts.”
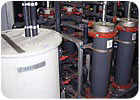
The 10-in. diameter ultrafiltration modules allowed Ames True Temper to achieve twice the capacity available with 8-in. modules.
A High-Capacity Module
Ames True Temper asked KMS and two other membrane companies to submit proposals for systems and provide price quotations. After a thorough evaluation process, Ames chose the KPAK™ ultrafiltration modules from KMS. “We selected the KPAK UF modules because they were lower in capital cost, more user-friendly and practically maintenance-free,” said Wright.Ames’ original specifications called for use of 8-in.-diameter UF spiral modules. Fortunately, KMS had recently introduced a new 10-in.-diameter module, with 462 ft2 (42.9 m2) of membrane. Using the larger-capacity modules, UF equipment occupying the same floor space can provide nearly twice the UF capacity. Because fewer modules are required, piping, hardware and installation costs are reduced significantly.
The Harrisburg plant commissioned two of the UF systems in October 2005. Each system uses four 10-in. modules to provide a total UF permeate production rate of 80 gpm.
“The decision was not difficult, because no other membrane vendor offered a 10-in. solution,” said Wright. “The 10-in. membranes gave us the capacity we needed with far fewer membranes and much less equipment compared to systems with 8-in. modules. Our two new KPAK systems now sit on the same footprint as the ones they replaced, and yet the new systems provide four times the UF capacity.”
Lower Maintenance and Better Quality
“The KPAK system has far exceeded our expectations,” said Wright. “Some of our employees were initially skeptical about our being one of the first companies to utilize the new 10-in. diameter module. But now they say that we should have installed the KPAK spiral membranes long ago. The new systems have dramatically reduced our maintenance effort. Since installing the system eight months ago, the membranes have performed flawlessly, and we have not had to clean them even once.”In order to change colors processed by the membrane unit, deionized water is cycled through the UF modules in a simple reverse flushing operation, a process that takes less than 1.5 hours.
“We now have a cleaner paint, which yields a better quality product,” said Wright. “We have been able to increase our production speed by over 10%, and we are now painting at 17 feet per minute, up from 15 feet per minute. Moreover, the higher-capacity ultrafiltration system has significantly reduced the time for conversion from one color to another, as our post rinses can now be filled faster.”
When compared to other spiral membranes, the virtually zero-bypass design of the new UF modules results in higher permeate output relative to paint feed. Maximum energy efficiency is achieved because practically all of the paint circulation flow passes over the membrane surface. The lower paint feed flow requirements means that smaller pumps can be employed to satisfy a given duty. In fact, the new system uses the same pumps as the original system. Since the UF capacity has quadrupled, energy efficiency has improved by 300%.
“We took a bit of a risk as an early adopter of the 10-in. diameter module, but I had confidence in KMS because of our nearly 30-year relationship and because of their expertise and leadership in the electrocoat industry,” said Wright. “We have no regrets and no doubts that the high capacity module will become commonplace for large-scale e-coat operations.”
Looking for a reprint of this article?
From high-res PDFs to custom plaques, order your copy today!