Cleaning Lenses with Plasma
A new automatic lens cleaning machine based on room-temperature plasma technology can minimize processing errors and dramatically reduce cleaning costs.
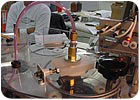
No longer an exotic technology limited to use in expensive manufacturing processes, plasma technology is experiencing rapid growth in new applications, enabled by the availability of new, more user-friendly plasma sources. As a cleaning step before a coating is applied to a surface, the microscopic etching that plasma causes can improve the surface adhesion qualities of materials such as polymers, composites and glass. In the past, however, a drawback to the use of plasma is that the plasma etching process needed to take place at high temperatures in a vacuum. Recently, the development of room-atmosphere plasma sources is enabling plasma cleaning to be accomplished more flexibly while dramatically reducing system costs.
One application that stands to benefit from this advance is eyeglass cleaning and coating. A new machine incorporating a room-atmosphere plasma source was recently developed for this field by Quantum Innovations, Central Point, OR. Called AtomiClean, the machine removes surface contamination in the pores of eyeglass lenses and microscopically etches the lenses in preparation for applying a layered antireflective coating (which is done by another machine). The machine uses plasma etching as an alternative to ultrasonic cleaning.
Ultrasonic cleaning involves submerging the lenses in a series of baths, followed by drying in an oven over a period of one to two hours. Using plasma, a stream of high-temperature ionized gas combines the etching and drying functions to allow for quick turnaround. Since a separate drying step is not required, a lens can be cleaned in less than 40 seconds - a decrease in processing time of over 99% compared to ultrasonic cleaning, which requires a separate lens drying step.
The mechanical workings behind the new machine were designed by Concept Systems Inc., an industrial systems integrator based in Albany, OR. Before Concept Systems got involved, Quantum had already developed a rough prototype for the lens cleaning system, but it did not include a programmable logic controller (PLC), human machine interface (HMI), and other standard automated controls. In addition to designing the lens transport control system and electrical layout, Concept’s team was tasked with developing an automated solution for scanning the plasma source across the lens surface.

At the start of the process, the operator goes to the HMI and selects the kind of lens he or she will be etching (i.e., the correct recipe number for that specific lens). Then, the operator grabs the ring holding that particular lens, puts it on the loading tray, and pushes the ring into the cleaning machine in a manner that is similar to loading a CD into a player. The machine rotates the internal receiver table to the first station, where both the top and bottom of the lens are washed under high pressure as the ring is spun.
The machine incorporates a pumping system and waste disposal system for the cleaning and drying station. (Quantum supplies the lens cleaning solution to its customers.) Concept Systems added sensors to tell when the cleaning solution is low. There are also proximity sensors to tell distances and a through-beam sensor to keep operators’ hands away. The machine uses a siphon effect generated by compressed air to cause the spray to atomize the cleaning solution into a high-velocity mist.
The second station is the drying station, where compressed air is used to dry the still spinning lens and ring. The system supports different lengths of drying times for different lenses (lenses with different amounts of curvature dry differently). After this stage is complete, any lint and dirt have been removed from the glass.
The third station is the plasma etching station, where the lens is rotated more slowly as microscopic impurities are eliminated from the lenses. The cleaning machine uses an atmospheric plasma system called Atomflo™, supplied by Surfx Technologies, Culver City, CA.
Gases are sprayed through a radio frequency (RF) grid, creating a plasma about ¼ in. off of each of two plasma heads, one for the top and one for the bottom of the lens. As the lens is spinning, the plasma heads are positioned approximately ¼ in. from the lens and moved in an arcing motion, conforming to the contour of the lens. The amount of time the head spends above different points on the lens is programmable and is directly related to the specific recipe the machine operator chooses.
The plasma applicator can be directed to follow uneven surfaces with exceptional uniformity, microscopically “roughing up” the lens surface to clean it at the atomic level, similar to the way that sandpaper is used in preparing a surface to be painted. The stream of oxygen atoms produced by the plasma head quickly strips organic films from the surfaces, producing carbon dioxide and water as reaction byproducts. In addition to the adhesion-enhancing benefits of plasma usage, the speed of cleaning can also greatly exceed the speed of other washing techniques; the plasma system can remove several microns of organic material per second.
At the end of the cleaning cycle, as the table carrying the lens through the various process stages reaches the front of the machine, the ring carrying the lens comes into contact with a “kicker” arm that knocks it into a chute that guides it into a tray, ready for the operator to collect.
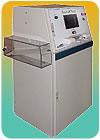
Another challenge was completely drying every type of lens that the operator might want to use. Due to changing aerodynamics with differing lens curvatures, this was a very difficult problem to overcome. Furthermore, the air velocity and pressure had to be completely equal and opposite on the top and bottom of the lens, or the lens would work itself right out of the ring and be blown off of the receiver table. Heat could not be introduced to the process, because this method left water marks on the lens. After many hours of testing, brainstorming, and calculating, the perfect pressure, velocity, and nozzle angle combination was found, and from then on, every lens was completely dried.
A third challenge related to issues with the plasma unit. The unit used by the cleaning machine was initially designed to work on a strictly manual basis, meaning it was not equipped with auto alarming or the ability to relax gas mixture tolerances. Quantum worked with the machine manufacturer to provide a customized unit that would be much more lenient with its gas mixture ratios and give error indications if certain conditions occurred. Concept Systems was then able to take the new “auto” version and integrate it into the automated cleaning process.
To ensure a reliable, high-performance lens processing system, the Concept Systems team chose to completely redesign the mechanical system instead of going the “safe” route of using the existing mechanical design. The result was a system that is easier for the operator to load, with automatic unloading, and an increased level of control and repeatability of the lens cleaning process, which minimizes processing errors and ensures a consistent high-quality output.
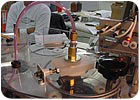
No longer an exotic technology limited to use in expensive manufacturing processes, plasma technology is experiencing rapid growth in new applications, enabled by the availability of new, more user-friendly plasma sources. As a cleaning step before a coating is applied to a surface, the microscopic etching that plasma causes can improve the surface adhesion qualities of materials such as polymers, composites and glass. In the past, however, a drawback to the use of plasma is that the plasma etching process needed to take place at high temperatures in a vacuum. Recently, the development of room-atmosphere plasma sources is enabling plasma cleaning to be accomplished more flexibly while dramatically reducing system costs.
One application that stands to benefit from this advance is eyeglass cleaning and coating. A new machine incorporating a room-atmosphere plasma source was recently developed for this field by Quantum Innovations, Central Point, OR. Called AtomiClean, the machine removes surface contamination in the pores of eyeglass lenses and microscopically etches the lenses in preparation for applying a layered antireflective coating (which is done by another machine). The machine uses plasma etching as an alternative to ultrasonic cleaning.
Ultrasonic cleaning involves submerging the lenses in a series of baths, followed by drying in an oven over a period of one to two hours. Using plasma, a stream of high-temperature ionized gas combines the etching and drying functions to allow for quick turnaround. Since a separate drying step is not required, a lens can be cleaned in less than 40 seconds - a decrease in processing time of over 99% compared to ultrasonic cleaning, which requires a separate lens drying step.
The mechanical workings behind the new machine were designed by Concept Systems Inc., an industrial systems integrator based in Albany, OR. Before Concept Systems got involved, Quantum had already developed a rough prototype for the lens cleaning system, but it did not include a programmable logic controller (PLC), human machine interface (HMI), and other standard automated controls. In addition to designing the lens transport control system and electrical layout, Concept’s team was tasked with developing an automated solution for scanning the plasma source across the lens surface.

The operator interface has been designed for flexibility and ease of use. Below the screen is the slot through which a lens is fed to initiate the cleaning process.
How the New Machine Works
The lens cleaning is done on the lens blank before it is cut to fit the desired eyeglass frame. At this stage, the blank is round, about 70 to 80 mm in diameter, and already has the desired curvature to match the customer’s prescription. The lens blank is held through the cleaning process in spring-loaded, ring-shaped holders. At the core of the machine is a receiver table that rotates the rings and moves them from station to station.At the start of the process, the operator goes to the HMI and selects the kind of lens he or she will be etching (i.e., the correct recipe number for that specific lens). Then, the operator grabs the ring holding that particular lens, puts it on the loading tray, and pushes the ring into the cleaning machine in a manner that is similar to loading a CD into a player. The machine rotates the internal receiver table to the first station, where both the top and bottom of the lens are washed under high pressure as the ring is spun.
The machine incorporates a pumping system and waste disposal system for the cleaning and drying station. (Quantum supplies the lens cleaning solution to its customers.) Concept Systems added sensors to tell when the cleaning solution is low. There are also proximity sensors to tell distances and a through-beam sensor to keep operators’ hands away. The machine uses a siphon effect generated by compressed air to cause the spray to atomize the cleaning solution into a high-velocity mist.
The second station is the drying station, where compressed air is used to dry the still spinning lens and ring. The system supports different lengths of drying times for different lenses (lenses with different amounts of curvature dry differently). After this stage is complete, any lint and dirt have been removed from the glass.
The third station is the plasma etching station, where the lens is rotated more slowly as microscopic impurities are eliminated from the lenses. The cleaning machine uses an atmospheric plasma system called Atomflo™, supplied by Surfx Technologies, Culver City, CA.
Gases are sprayed through a radio frequency (RF) grid, creating a plasma about ¼ in. off of each of two plasma heads, one for the top and one for the bottom of the lens. As the lens is spinning, the plasma heads are positioned approximately ¼ in. from the lens and moved in an arcing motion, conforming to the contour of the lens. The amount of time the head spends above different points on the lens is programmable and is directly related to the specific recipe the machine operator chooses.
The plasma applicator can be directed to follow uneven surfaces with exceptional uniformity, microscopically “roughing up” the lens surface to clean it at the atomic level, similar to the way that sandpaper is used in preparing a surface to be painted. The stream of oxygen atoms produced by the plasma head quickly strips organic films from the surfaces, producing carbon dioxide and water as reaction byproducts. In addition to the adhesion-enhancing benefits of plasma usage, the speed of cleaning can also greatly exceed the speed of other washing techniques; the plasma system can remove several microns of organic material per second.
At the end of the cleaning cycle, as the table carrying the lens through the various process stages reaches the front of the machine, the ring carrying the lens comes into contact with a “kicker” arm that knocks it into a chute that guides it into a tray, ready for the operator to collect.
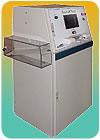
The machine accepts lenses to be cleaned through the slot on the right and deposits cleaned lenses down the chute on the left.
Overcoming Design Challenges
One key design challenge was getting proper control of the rings. It was difficult to rotate the rings while washing them under high pressure, without the main drive wheel slipping due to friction loss from the cleaning fluid. Concept solved this problem by creating more surface area that the main drive wheel would contact with the ring in the washing station.Another challenge was completely drying every type of lens that the operator might want to use. Due to changing aerodynamics with differing lens curvatures, this was a very difficult problem to overcome. Furthermore, the air velocity and pressure had to be completely equal and opposite on the top and bottom of the lens, or the lens would work itself right out of the ring and be blown off of the receiver table. Heat could not be introduced to the process, because this method left water marks on the lens. After many hours of testing, brainstorming, and calculating, the perfect pressure, velocity, and nozzle angle combination was found, and from then on, every lens was completely dried.
A third challenge related to issues with the plasma unit. The unit used by the cleaning machine was initially designed to work on a strictly manual basis, meaning it was not equipped with auto alarming or the ability to relax gas mixture tolerances. Quantum worked with the machine manufacturer to provide a customized unit that would be much more lenient with its gas mixture ratios and give error indications if certain conditions occurred. Concept Systems was then able to take the new “auto” version and integrate it into the automated cleaning process.
User-Friendly Operator Interface
The system uses a touch-screen HMI with a graphic display that shows the processing status of different lenses at different stages in the cycle, and to exactly what recipe they are being processed. The system was designed with a high degree of programmability. For example, the operator can program and choose the different recipes to enable lenses with varying curvatures to spend varying amounts of time at the different stations. In addition, safeguards are provided, including detailed alarms to alert the operator if the cleaning solution is low, system air pressure is low, waste fluid is high, plasma unit malfunctioning, unloading tray full, etc.To ensure a reliable, high-performance lens processing system, the Concept Systems team chose to completely redesign the mechanical system instead of going the “safe” route of using the existing mechanical design. The result was a system that is easier for the operator to load, with automatic unloading, and an increased level of control and repeatability of the lens cleaning process, which minimizes processing errors and ensures a consistent high-quality output.
Looking for a reprint of this article?
From high-res PDFs to custom plaques, order your copy today!