Corrosion Protection for Space and Beyond
NASA’s Corrosion Technology Lab at the Kennedy Space Center is evolving to provide a better understanding of the corrosion processes affecting NASA’s redesigned launch sites, structures, facilities and launch vehicles. Such knowledge will undoubtedly help benefit the future finishing industry as a whole.
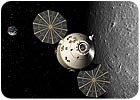
Florida is home to NASA’s Launch Operations Center. Since its establishment in July 1962, the spaceport has served as the departure gate for every American manned mission and hundreds of advanced scientific spacecraft under the Launch Services Program. The center was renamed the John F. Kennedy Space Center in late 1963 to honor the president who put America on the path to the moon. Today, NASA is on the edge of a bold new challenge: the Constellation Program. Constellation is a NASA program to create a new generation of spacecraft for human spaceflight, consisting primarily of the Ares I and Ares V launch vehicles, the Orion crew capsule, the Earth Departure stage and the Lunar access module. These spacecraft will be capable of performing a variety of missions, from Space Station resupply to lunar landings. The ambitious new endeavor calls for NASA to return human explorers to the moon and then venture even farther, to Mars and beyond.
As the nation’s premier spaceport, Kennedy Space Center (KSC) will play a critical role in this new chapter in exploration, particularly in the conversion of the launch facilities to accommodate the new launch vehicles. To prepare for this endeavor, the launch site and facilities for the next generation of crew and cargo vehicles must be redesigned, assembled and tested. One critical factor that is being carefully considered during the renovation is protecting the new facilities and structures from corrosion and deterioration.
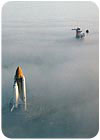
To combat the harsh environment, NASA established the Corrosion Technology Laboratory at KSC. This facility has complete capabilities for corrosion research and testing. Scientists and engineers at Kennedy’s Corrosion Technology Laboratory are working to reduce the impact of corrosion and even develop new corrosion-prevention technologies as NASA prepares KSC for the Constellation Program.
The facilities of NASA’s Corrosion Technology Laboratory include a beachside atmospheric exposure site, an electrochemistry and coating development laboratory, an accelerated corrosion laboratory, a coatings application facility, and a photo documentation laboratory. The beachside atmospheric exposure site includes a full weather data station, a cathodic protection compatibility tank, seawater immersion tanks, and an on-site laboratory, in addition to the numerous racks for atmospheric exposure. This site has been actively maintained for more than 40 years and has generated a historical database for evaluation of new materials. The site has remote access network connectivity for data acquisition and real time video by the Internet. These facilities are available to companies and individuals outside of NASA, and can provide a way for the finishing industry to advance corrosion resistant technologies.
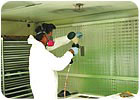
NASA uses different types of coatings to protect flight hardware, launch pad structures and ground support equipment. Barrier coatings, such as epoxies and urethanes, are used to isolate the surface of a metal structure from the corrosive environment. Conversion coatings, such as the Super Koropon primer used for corrosion protection of areas throughout the Orbiter, convert the surface into a hard, durable, corrosion-resistant layer. And sacrificial coatings, such as the zinc-rich primers used at the launch pads, offer corrosion protection by corroding in preference to the carbon steel.
Smart coatings, a more recent development, represent the state-of-the-art of coating technology. These coatings sense the environment and provide an appropriate response. The Corrosion Technology Laboratory is currently developing “smart coatings” for corrosion detection and control at an early stage to prevent further corrosion. The lab is also involved in the development of self cleaning photocatalytic coatings that remove contamination without human intervention.
Kennedy Space Center corrosion experts use test equipment such as acidic and standard salt spray chambers, weatherometers, AC and DC electrochemical corrosion instrumentation, adhesion testers, data loggers, and other instrumentation to conduct research on the corrosion behavior of materials in various environments, including the interiors of the processing facilities and on transport equipment. The Vehicle Assembly Building is currently undergoing modifications to accommodate the simultaneous assembly and checkout operations for both the shuttle and for the Ares I. Eventually, the building will allow for the assembly of both an Ares I and Ares V when lunar missions commence after 2018. NASA will also build two new mobile launch platforms designed to handle the Ares I with the current crawler-transporters and will eventually replace the Apollo-era machines with new units when the Ares V comes on-line. Corrosion resistant materials are vital to sustain the operability and life of these structures.
Current projects in the Corrosion Technology Laboratory also support the future development of space vehicles by examining technology that will prevent corrosion of materials in the space environment. These projects include the testing of stainless steel in oxygen-deficient environment and the fracture of high-strength, low-alloy steels. Results of these projects will help protect vehicles launching from a third launch complex NASA is considering - 39C - which will be used primarily to accommodate future Mars missions when more than one Ares V would be required to launch the Mars-bound spacecraft into low-earth orbit.
As NASA prepares to move forward, the Corrosion Technology Lab at KSC will evolve to provide a better understanding of the corrosion processes affecting NASA’s redesigned launch sites, structures, facilities and launch vehicles. Such knowledge will undoubtedly help benefit the future finishing industry as a whole.
For more information about NASA’s Corrosion Technology Lab, visit http://corrosion.ksc.nasa.gov/.
Author’s Acknowledgment: Jeffrey A. Kohler, ASRC Aerospace Technology Programs and Partnerships, contributed to this article.
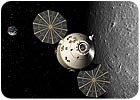
An artist’s rendering of the Orion crew capsule orbiting the moon. Image courtesy of Lockheed Martin Corp.
Florida is home to NASA’s Launch Operations Center. Since its establishment in July 1962, the spaceport has served as the departure gate for every American manned mission and hundreds of advanced scientific spacecraft under the Launch Services Program. The center was renamed the John F. Kennedy Space Center in late 1963 to honor the president who put America on the path to the moon. Today, NASA is on the edge of a bold new challenge: the Constellation Program. Constellation is a NASA program to create a new generation of spacecraft for human spaceflight, consisting primarily of the Ares I and Ares V launch vehicles, the Orion crew capsule, the Earth Departure stage and the Lunar access module. These spacecraft will be capable of performing a variety of missions, from Space Station resupply to lunar landings. The ambitious new endeavor calls for NASA to return human explorers to the moon and then venture even farther, to Mars and beyond.
As the nation’s premier spaceport, Kennedy Space Center (KSC) will play a critical role in this new chapter in exploration, particularly in the conversion of the launch facilities to accommodate the new launch vehicles. To prepare for this endeavor, the launch site and facilities for the next generation of crew and cargo vehicles must be redesigned, assembled and tested. One critical factor that is being carefully considered during the renovation is protecting the new facilities and structures from corrosion and deterioration.
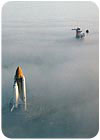
The accelerated corrosion lab includes traditional salt spray testing techniques, as well as advanced cyclic and acidic methods.
A Resource for Corrosion Research
NASA began corrosion studies at the KSC in 1966 during the Gemini/Apollo Programs with the evaluation of long-term protective coatings for the corrosion protection of carbon steel. The KSC environment near the launch pads has been documented by the American Society of Materials (ASM) as one of the most corrosive, naturally occurring, environments in the world.1 With the introduction of the space shuttle in 1981, the already highly corrosive conditions at the launch pads were rendered even more severe by the acidic exhaust from the solid rocket boosters. In the years that followed, numerous studies have identified materials, coatings and maintenance procedures for launch hardware and equipment exposed to the highly corrosive environment at the launch pads. Research and development of technologies that offer corrosion protection and prevention at the launch facilities is high on NASA’s priority needs list.To combat the harsh environment, NASA established the Corrosion Technology Laboratory at KSC. This facility has complete capabilities for corrosion research and testing. Scientists and engineers at Kennedy’s Corrosion Technology Laboratory are working to reduce the impact of corrosion and even develop new corrosion-prevention technologies as NASA prepares KSC for the Constellation Program.
The facilities of NASA’s Corrosion Technology Laboratory include a beachside atmospheric exposure site, an electrochemistry and coating development laboratory, an accelerated corrosion laboratory, a coatings application facility, and a photo documentation laboratory. The beachside atmospheric exposure site includes a full weather data station, a cathodic protection compatibility tank, seawater immersion tanks, and an on-site laboratory, in addition to the numerous racks for atmospheric exposure. This site has been actively maintained for more than 40 years and has generated a historical database for evaluation of new materials. The site has remote access network connectivity for data acquisition and real time video by the Internet. These facilities are available to companies and individuals outside of NASA, and can provide a way for the finishing industry to advance corrosion resistant technologies.
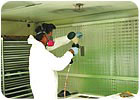
The coatings application lab is equipped with conventional, airless and plural component spray capabilities.
Corrosion-Resistant Coating Advances
Corrosion in concrete is a major concern in areas with marine environments like the space center. The Corrosion Technology Laboratory has developed technology to protect both concrete and steel rebar in concrete. KSC’s two shuttle launch sites each consist of 68,000 yd3 of concrete weighing 1.3 million lb. As these two launch pads are being refurbished to accommodate the manned Ares I (Crew Launch Vehicle) and the unmanned Ares V (Cargo Launch Vehicle) in support of the Constellation Program, the lab will continue developing technology to protect these structures. Recently, a sacrificial galvanic coating was developed to prevent the corrosion of steel rebar in concrete. NASA licensed the patented technology to two companies. The coating is currently being reformulated and tested on structures throughout the world.NASA uses different types of coatings to protect flight hardware, launch pad structures and ground support equipment. Barrier coatings, such as epoxies and urethanes, are used to isolate the surface of a metal structure from the corrosive environment. Conversion coatings, such as the Super Koropon primer used for corrosion protection of areas throughout the Orbiter, convert the surface into a hard, durable, corrosion-resistant layer. And sacrificial coatings, such as the zinc-rich primers used at the launch pads, offer corrosion protection by corroding in preference to the carbon steel.
Smart coatings, a more recent development, represent the state-of-the-art of coating technology. These coatings sense the environment and provide an appropriate response. The Corrosion Technology Laboratory is currently developing “smart coatings” for corrosion detection and control at an early stage to prevent further corrosion. The lab is also involved in the development of self cleaning photocatalytic coatings that remove contamination without human intervention.
A Better Understanding
The Corrosion Technology Lab and its work are considered unique within NASA. New procedures have been developed for rapidly evaluating corrosion-resistant alloys, protective coatings and other materials, thereby enhancing the safety and reliability of the nation’s launch infrastructure and flight hardware. Results of this research will benefit the new structures for launch. For example, Launch Complex 39B will undergo the beginnings of its conversion to the Ares I facility with the building of three to four new tall lightning masts, followed by a stripping of the pad’s fixed and rotating service structures currently used to access the shuttle and insert payloads into the Orbiter. The Launch Complex will resemble the Apollo-like “clean pad” design for the first time since 1977. Two new moveable launch platforms and a launch tower will be constructed to accommodate the Ares I, and a new “roller coaster” escape system, replacing the existing slide wire system, will connect the launch tower with a new fortified bunker located 1000 meters from the pad. Fortifying the new platforms, tower and escape system with alloys and protective coatings will greatly enhance the safety and reliability of this equipment.Kennedy Space Center corrosion experts use test equipment such as acidic and standard salt spray chambers, weatherometers, AC and DC electrochemical corrosion instrumentation, adhesion testers, data loggers, and other instrumentation to conduct research on the corrosion behavior of materials in various environments, including the interiors of the processing facilities and on transport equipment. The Vehicle Assembly Building is currently undergoing modifications to accommodate the simultaneous assembly and checkout operations for both the shuttle and for the Ares I. Eventually, the building will allow for the assembly of both an Ares I and Ares V when lunar missions commence after 2018. NASA will also build two new mobile launch platforms designed to handle the Ares I with the current crawler-transporters and will eventually replace the Apollo-era machines with new units when the Ares V comes on-line. Corrosion resistant materials are vital to sustain the operability and life of these structures.
Current projects in the Corrosion Technology Laboratory also support the future development of space vehicles by examining technology that will prevent corrosion of materials in the space environment. These projects include the testing of stainless steel in oxygen-deficient environment and the fracture of high-strength, low-alloy steels. Results of these projects will help protect vehicles launching from a third launch complex NASA is considering - 39C - which will be used primarily to accommodate future Mars missions when more than one Ares V would be required to launch the Mars-bound spacecraft into low-earth orbit.
As NASA prepares to move forward, the Corrosion Technology Lab at KSC will evolve to provide a better understanding of the corrosion processes affecting NASA’s redesigned launch sites, structures, facilities and launch vehicles. Such knowledge will undoubtedly help benefit the future finishing industry as a whole.
For more information about NASA’s Corrosion Technology Lab, visit http://corrosion.ksc.nasa.gov/.
Author’s Acknowledgment: Jeffrey A. Kohler, ASRC Aerospace Technology Programs and Partnerships, contributed to this article.
Looking for a reprint of this article?
From high-res PDFs to custom plaques, order your copy today!