The Promise of Plasma Pretreatment
It’s no surprise that the auto industry is seeking to replace some of its existing processes with more environmentally benign operations. But in today’s tough economic climate, “environmentally friendly” technologies have to do more than just benefit the environment; they also must have a positive impact on a company’s bottom line. At Ford Motor Co.’s Research and Innovation Center (RIC) in Dearborn, MI, researchers have been testing a new atmospheric plasma pretreatment technology that promises to achieve both goals.
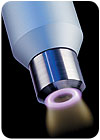
A typical automotive paint shop confronts significant environmental challenges. Chemical solvents and adhesion promoters, water and material waste, air emissions, high energy consumption - for an industry facing increasing public and legislative pressure to “green” its operations, the list is daunting. It’s no surprise that the auto industry is seeking to replace some of its existing processes with more environmentally benign operations. But in today’s tough economic climate, “environmentally friendly” technologies have to do more than just benefit the environment; they also must have a positive impact on a company’s bottom line.
At Ford Motor Co.’s Research and Innovation Center (RIC) in Dearborn, MI, researchers have been testing a new technology that promises to achieve both goals. Known as atmospheric plasma, the technology uses a stepped, high-frequency, pulsed current to convert compressed air into a relatively low-temperature, voltage-free beam of plasma. In finishing applications, the plasma can be directed onto the material surface to remove static electricity and dust, as well as to vaporize contaminants, including waxes and silicone residues. The plasma also increases surface wettability and the adhesion of coatings to the substrate being treated.
The technology has been used successfully in production to pretreat small plastic components used in automotive and other applications. However, transferring the technology to large parts has been difficult, primarily due to the lack of suitable large-scale processing equipment. Fortunately, this hurdle didn’t stop Ford. Seeing the promise of the technology, the company’s Dearborn laboratory designed and engineered a robotic workcell capable of delivering atmospheric plasma surface treatments precisely and accurately to large, flexible, three-dimensional plastic parts. The results of the lab’s surface engineering program could change the way the entire automotive industry approaches the paint operation - and could have far-reaching benefits for the environment.
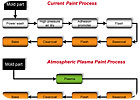
According to Larry Haack, technical expert – surface engineering, Ford’s research team has been investigating surface treatment technologies for more than 10 years. The team first became interested in the atmospheric plasma technology in February 2002, after hearing a presentation at an Adhesion Society meeting by Plasmatreat, developer of the Openair® atmospheric plasma surface treatment technology.
“One of the major benefits we saw with the Openair plasma was the simplicity of the technology, as well as the fact that it is environmentally friendly,” Haack says.
From that point on, the Ford team began developing ideas on how to improve cost and quality by integrating atmospheric plasma solutions into automotive applications. Initially, they evaluated the technology with analytical techniques to measure how the atmospheric plasma changed the surface of plastics. They also worked with Plasmatreat to evaluate different plasma jet configurations for manufacturing applications. These efforts eventually progressed from the laboratory to production. In 2006, the Ford team developed a prototype workcell that would be used to demonstrate the feasibility of using the technology on TPO bumper fascias to replace primers. The workcell uses two gantry robots, working in concert with two rotating trunnions, to ensure that the treatment distance to the bumper fascia is maintained precisely to achieve reliable paint adhesion. (In previous applications, this constraint restricted the size and complexity of components that could be treated by atmospheric plasma). The fascias are attached with high positional precision to the workcell using vacuum cups on structured aluminum fixtures.
The Ford research team discovered that the atmospheric plasma technology both cleans and activates the surface in a one-step process. The physical cleaning imparted by the technology removes mold-release agents and accumulated dust from storage as effectively as a power wash. At the same, it adds oxygen to the surface to provide the needed functional groups for subsequent bonding. These benefits allow the technology to replace both the power wash and adhesion promoter for painting TPO bumper fascias, without requiring reformulation of any of the subsequent paint layers (see Figure 1). The result is a much more environmentally friendly process.
“On average, eliminating the adhesion promoter layer can result in a material reduction of around 30%, depending on transfer efficiencies in the paint process, targeted film build and production volume,” says Ann Straccia, research scientist, Surface Science and Engineering team at Ford RIC. “There also are substantial reductions in the amount of water, solvents and other chemicals, emissions, waste, and energy associated with the powerwash and paint operations.”

Ford’s research team also discovered that using the atmospheric plasma technology actually improves paint appearance compared to the existing process. The applied adhesion promoter does not wet out effectively on low-surface-energy TPO and often results in an “orange peel” texture that is transmitted through to the final paint surface. The atmospheric plasma treatment increases the surface energy of the TPO to an amount that is greater than that of the applied paint layers, thereby allowing the sprayed paint to wet out properly with uniform flow. With the plasma treatment, the measured appearance numbers can increase up to 20% compared to conventional adhesion-promoter painted fascias.
For Ford, while the cost savings and quality improvements are important, the true promise of the technology lies in the environmental benefits.
“Ford has taken a very proactive stance in finding solutions to environmental issues. The atmospheric plasma pretreatment is one of the best technologies we’ve seen so far that address these issues in terms of painting processes,” says Joe Holubka, technical leader, Surface Science and Engineering team at Ford RIC.
The process has proven itself on both a laboratory and prototype scale. The next step is to implement the technology in manufacturing and perform reliability testing associated with the full production system. According to Straccia, the robotic workcell developed by the Ford team could be used to produce bumper fascias for low-volume vehicles (under 40,000 per year), and the technology can be scaled up easily to handle larger production volumes.
With all of the benefits offered by atmospheric plasma pretreatment, broad-scale acceptance of the technology likely isn’t a matter of if, but when.
For more information about Ford RIC, call 313.323.9803 or visit www.ford.com. More information about the atmospheric plasma pretreatment technology can be found at www.plasmatreat.com.
For an in-depth explanation of the atmospheric plasma pretreatment technology, see the related article from March 2007 Finishing Today, "A Brilliant Finish"
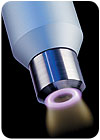
A rendering of the Openair plasma jet. Image courtesy of Plasmatreat.
A typical automotive paint shop confronts significant environmental challenges. Chemical solvents and adhesion promoters, water and material waste, air emissions, high energy consumption - for an industry facing increasing public and legislative pressure to “green” its operations, the list is daunting. It’s no surprise that the auto industry is seeking to replace some of its existing processes with more environmentally benign operations. But in today’s tough economic climate, “environmentally friendly” technologies have to do more than just benefit the environment; they also must have a positive impact on a company’s bottom line.
At Ford Motor Co.’s Research and Innovation Center (RIC) in Dearborn, MI, researchers have been testing a new technology that promises to achieve both goals. Known as atmospheric plasma, the technology uses a stepped, high-frequency, pulsed current to convert compressed air into a relatively low-temperature, voltage-free beam of plasma. In finishing applications, the plasma can be directed onto the material surface to remove static electricity and dust, as well as to vaporize contaminants, including waxes and silicone residues. The plasma also increases surface wettability and the adhesion of coatings to the substrate being treated.
The technology has been used successfully in production to pretreat small plastic components used in automotive and other applications. However, transferring the technology to large parts has been difficult, primarily due to the lack of suitable large-scale processing equipment. Fortunately, this hurdle didn’t stop Ford. Seeing the promise of the technology, the company’s Dearborn laboratory designed and engineered a robotic workcell capable of delivering atmospheric plasma surface treatments precisely and accurately to large, flexible, three-dimensional plastic parts. The results of the lab’s surface engineering program could change the way the entire automotive industry approaches the paint operation - and could have far-reaching benefits for the environment.
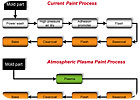
Figure 1. The atmospheric plasma pretreatment technology simplifies the paint process for TPO bumper fascias.
An Environmental Solution
The adhesion of an automotive finish is crucial to ensuring high quality and consumer appeal. To achieve a good bond between the coating and underlying substrate, automotive components made of thermoplastic polyolefin (TPO), such as bumper fascias, are cleaned with a power wash solution, dried in an oven, and then primed with a solventborne chlorinated adhesion promoter. All of these steps carry a substantial environmental impact in the form of high energy consumption, wastewater, air emissions containing volatile organic compounds (VOCs), and sludge waste that can end up in landfills.According to Larry Haack, technical expert – surface engineering, Ford’s research team has been investigating surface treatment technologies for more than 10 years. The team first became interested in the atmospheric plasma technology in February 2002, after hearing a presentation at an Adhesion Society meeting by Plasmatreat, developer of the Openair® atmospheric plasma surface treatment technology.
“One of the major benefits we saw with the Openair plasma was the simplicity of the technology, as well as the fact that it is environmentally friendly,” Haack says.
From that point on, the Ford team began developing ideas on how to improve cost and quality by integrating atmospheric plasma solutions into automotive applications. Initially, they evaluated the technology with analytical techniques to measure how the atmospheric plasma changed the surface of plastics. They also worked with Plasmatreat to evaluate different plasma jet configurations for manufacturing applications. These efforts eventually progressed from the laboratory to production. In 2006, the Ford team developed a prototype workcell that would be used to demonstrate the feasibility of using the technology on TPO bumper fascias to replace primers. The workcell uses two gantry robots, working in concert with two rotating trunnions, to ensure that the treatment distance to the bumper fascia is maintained precisely to achieve reliable paint adhesion. (In previous applications, this constraint restricted the size and complexity of components that could be treated by atmospheric plasma). The fascias are attached with high positional precision to the workcell using vacuum cups on structured aluminum fixtures.
The Ford research team discovered that the atmospheric plasma technology both cleans and activates the surface in a one-step process. The physical cleaning imparted by the technology removes mold-release agents and accumulated dust from storage as effectively as a power wash. At the same, it adds oxygen to the surface to provide the needed functional groups for subsequent bonding. These benefits allow the technology to replace both the power wash and adhesion promoter for painting TPO bumper fascias, without requiring reformulation of any of the subsequent paint layers (see Figure 1). The result is a much more environmentally friendly process.
“On average, eliminating the adhesion promoter layer can result in a material reduction of around 30%, depending on transfer efficiencies in the paint process, targeted film build and production volume,” says Ann Straccia, research scientist, Surface Science and Engineering team at Ford RIC. “There also are substantial reductions in the amount of water, solvents and other chemicals, emissions, waste, and energy associated with the powerwash and paint operations.”

A prototype workcell developed at Ford RIC demonstrates the feasibility of using the technology on TPO bumper fascias to replace primers.
A Solid Business Case
In this case, what’s good for the environment is also good for the bottom line. The adhesion promoter can account for up to 20% of the overall paint material cost, so eliminating this paint layer provides a significant cost savings for an automotive paint shop. Replacing the power wash and adhesion promoter steps also can reduce processing time by as much as 30%, thereby increasing productivity and throughput capacity. The reductions in energy and water consumption provide additional savings, especially as costs for these resources continue to rise.Ford’s research team also discovered that using the atmospheric plasma technology actually improves paint appearance compared to the existing process. The applied adhesion promoter does not wet out effectively on low-surface-energy TPO and often results in an “orange peel” texture that is transmitted through to the final paint surface. The atmospheric plasma treatment increases the surface energy of the TPO to an amount that is greater than that of the applied paint layers, thereby allowing the sprayed paint to wet out properly with uniform flow. With the plasma treatment, the measured appearance numbers can increase up to 20% compared to conventional adhesion-promoter painted fascias.
For Ford, while the cost savings and quality improvements are important, the true promise of the technology lies in the environmental benefits.
“Ford has taken a very proactive stance in finding solutions to environmental issues. The atmospheric plasma pretreatment is one of the best technologies we’ve seen so far that address these issues in terms of painting processes,” says Joe Holubka, technical leader, Surface Science and Engineering team at Ford RIC.
The process has proven itself on both a laboratory and prototype scale. The next step is to implement the technology in manufacturing and perform reliability testing associated with the full production system. According to Straccia, the robotic workcell developed by the Ford team could be used to produce bumper fascias for low-volume vehicles (under 40,000 per year), and the technology can be scaled up easily to handle larger production volumes.
With all of the benefits offered by atmospheric plasma pretreatment, broad-scale acceptance of the technology likely isn’t a matter of if, but when.
For more information about Ford RIC, call 313.323.9803 or visit www.ford.com. More information about the atmospheric plasma pretreatment technology can be found at www.plasmatreat.com.
For an in-depth explanation of the atmospheric plasma pretreatment technology, see the related article from March 2007 Finishing Today, "A Brilliant Finish"
Looking for a reprint of this article?
From high-res PDFs to custom plaques, order your copy today!