Cost-Effective Cleaning with Vapor Degreasing
Aqueous cleaning systems tend to have large footprints, require a significant capital investment, guzzle electricity at a prodigious rate, are maintenance intensive, and require processed water and wastewater treatment systems. Most young engineers feel these constraints are locked in stone, but there is another cleaning option, one from the history books. If you’re willing to go “back to the future,” it’s time to revisit vapor degreasing.
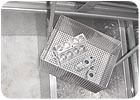
For decades, vapor degreasing was the cleaning technology of choice in the finishing industry. This ended in the 1990s, when the ozone issue forced the phase-out of the most popular vapor degreasing solvents, and water-based systems filled the void. Today, most precision cleaning is performed using aqueous technology. But aqueous cleaning systems tend to have large footprints, require a significant capital investment, guzzle electricity at a prodigious rate, are maintenance intensive, and require processed water and wastewater treatment systems. Most young engineers feel these constraints are locked in stone, but there is another cleaning option, one from the history books. If you’re willing to go “back to the future,” it’s time to revisit vapor degreasing.

The concept behind vapor degreasing is simple. Figure 1 illustrates the design of a modern, efficient, two-sump degreaser. A vapor degreaser boils a liquid into a vapor, contains the vapors, cools the vapors back into a liquid, and collects this purified liquid for continuous use. A vapor degreaser therefore is not only a parts cleaning system but also a tight, fast, energy-efficient recycling system that captures and refreshes the solvent with little waste.
The solvent is placed in the “boil” sump (lower left chamber in Figure 1) and is heated to its boiling point, usually 100-170°F (38-77°C), depending on the solvent. The heat can be provided with electric heating elements, hot water coils, steam coils or the heat from a “heat pump” refrigeration unit.
It’s noteworthy that even a small water-cleaning system will consume considerably more energy in heating the cleaning solution than a vapor degreaser of comparable capacity. The higher energy consumption occurs because water has a much higher specific heat and a much higher latent heat of vaporization than vapor degreasing solvents. This fundamental characteristic of water also explains why it takes so many BTUs to dry the parts after they have been cleaned in an aqueous system. In contrast, some small vapor degreasers operate on 120 V power supplies.
Once boiling, the solvent produces a clear, dense vapor that rises through the machine, displacing the air in the degreaser. Eventually the vapors rise up and reach the lower set of cold coils, called the “primary condensing coils.” These coils chill the solvent vapors and condense the solvent back into its liquid state. This liquid drips into a condensate trough that is under the primary condensing coils and around the interior circumference of the machine. There it is routed through a water separator, decanting any water that may have condensed on the condensing coils and removing it from the solvent.*
At this point, the distilled solvent is directed back into the rinse sump from the water separator (lower right chamber in Figure 1). Since the rinse sump already is filled with clean solvent, the addition of clean, newly distilled solvent will cause the sump to overflow into the boil sump, completing the distillation cycle. The addition of this fresh, pure solvent maintains a consistently clean rinse sump and also allows contamination and particulate to be washed back into the boil sump and concentrated there.
Another important feature of modern vapor degreasers is a second set of cooling coils, located above the primary condensing coils (also shown in Figure 1). Called “freeboard chillers,” these coils are always colder than the primary condensers, usually around -20°F (-29°C). Their purpose is to lower the temperature and humidity of the air above the vapor blanket to minimize solvent diffusion from the saturated vapor blanket into the air, thereby minimizing solvent losses. In addition, since the freeboard chillers dehumidify the area above the vapor blanket, minimal water will be condensed on the primary condensing coils, which helps maintain solvent integrity.
(Note that the freeboard chiller coils are not used to contain the solvent blanket in the degreaser. That’s the job of the primary condensing coils. If the vapor blanket ever rises above the primary condensing coils into the area of the freeboard chiller coils, there is something wrong with the primary condensing coils and a refrigeration technician needs to be consulted.)
Lastly, another option in the degreaser is the installation of “superheated” coils. These coils superheat the vapor blanket above the “normal” boiling point of the solvent. This superheated vapor quickly heats the freshly cleaned parts and ensures that all the condensed solvent on the parts is vaporized and recovered under the vapor blanket. This process guarantees that the parts are dry before being removed from the system, which minimizes solvent drag-out and solvent consumption.
There are more than a dozen manufacturers of vapor degreasers in the U.S., and several dozen more worldwide. Depending on the cleaning application and process requirements, the technology exists to handle the largest parts and highest volumes. These large machines, when properly designed, operated and maintained, can be extremely efficient with minimal solvent consumption.
The best way to evaluate the operating costs of different types of cleaning systems is to compare them on a cost-per-part-cleaned basis. This approach provides an apples-to-apples comparison that can illuminate the hidden costs of water cleaning.
First, the acquisition and installation costs are tabulated. Included among these are the direct capital costs of the cleaning system (the hardware itself, plus the support systems, wastewater treatment systems, and so on), as well as the indirect capital costs (the floor space, upgrades to the facility’s electrical system, plumbing costs, etc.).
The next step is to estimate the direct operating costs for both systems. This estimate includes the solvent and water costs, energy costs, labor costs, waste disposal costs, inventory costs that change due to faster or slower cleaning cycles, and any other direct expense that touches the cleaning system. Engineers also will need to take into account the personnel time needed to operate and maintain the cleaning equipment. Vapor degreasers typically are almost maintenance-free; aqueous systems can be much more complex and time-consuming.
Then there is the solvent cost. While the solvent selection process is beyond the scope of this article, evaluating the cost of the solvent is simple. The proper way to estimate solvent costs is not to compare the cost per pound, but to compare the cost per part cleaned. For example, a modern vapor degreaser will use approximately 0.062 lb of solvent/hr/ft2 of solvent/air interface when in use. A typical 10-gallon degreaser has about 2.5 ft of solvent/air interface, so it will lose about 1.25 lb of solvent (less than one cup) in an eight-hour work day. If the solvent is priced at roughly $3/lb, the solvent cost for a day of cleaning is under $4, and the cost-per-part, assuming 1,000 parts were cleaned that day, is $0.00372 per part.
When these costs are tabulated and then divided by the total number of parts cleaned by the system, the true cost of cleaning becomes apparent.
To obtain the desired results in the most economical and environmentally acceptable manner, it is imperative that the degreaser system be properly configured, operated and maintained. In addition to the hardware issues, the proper solvent selection requires careful analysis, and that selection depends on the contamination being removed. When analyzing the application, always define the impurities first, then select the chemistry that removes those impurities, as well as the equipment that uses the chosen solvent properly.
It is clear that the vapor degreasing concept is being revitalized. In today’s world, where quality, reliability and energy efficiency are paramount, the old process of vapor degreasing deserves another look as a modern, planet-friendly and cost-effective cleaning process.
*Water and solvents are easily separated in these systems since they generally are not miscible in each other. The lighter water floats on top of the heavier solvent, and the water is easily separated and discharged from the system.
A less-damaging group of cleaners, called the “Class II Ozone-Depleting Substances,” was recommended to users as an interim cleaning option. The most popular of these was a solvent called HCFC-141b. However, the manufacture of HCFC-141b ended on January 1, 2003, and the use of this material in solvent cleaning applications was banned in 1997.
Fortunately, suppliers have developed more environmentally acceptable alternatives. Newer hydrofluorocarbon-based fluids and solvents based on n-propyl bromide (nPB) have zero or minimal ozone depletion and low global warming potential, while providing consistent, affordable, high-quality cleaning. Additionally, advanced product stewardship programs can help ensure the safest, most efficient use of these chemicals in vapor degreaser applications.
For more information about vapor degreasing, visit www.microcare.com.
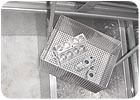
This look inside a vapor degreaser shows the boil sump on the left and the condensate rinse sump on the right. The boil sump has an aggressive boil. Note the clean solvent in the right sump. The basket of parts is first submerged in the boil sump and then moved manually or by automatic hoist (not shown) into the rinse sump.
For decades, vapor degreasing was the cleaning technology of choice in the finishing industry. This ended in the 1990s, when the ozone issue forced the phase-out of the most popular vapor degreasing solvents, and water-based systems filled the void. Today, most precision cleaning is performed using aqueous technology. But aqueous cleaning systems tend to have large footprints, require a significant capital investment, guzzle electricity at a prodigious rate, are maintenance intensive, and require processed water and wastewater treatment systems. Most young engineers feel these constraints are locked in stone, but there is another cleaning option, one from the history books. If you’re willing to go “back to the future,” it’s time to revisit vapor degreasing.

Figure 1. The internal workings of vapor degreasers tend to be remarkably simple, which is one characteristic that makes them so highly cost-effective. Crucial to the process is the selection of a nonflammable “low-boiling” solvent (as opposed to a high-boiling liquid, such as a hydrocarbon solvent or water), which makes the liquid-vapor-liquid cycle fast and reliable.
Vapor Degreasing Concepts
To a certain degree, the term “vapor degreasing” is a misnomer. Certainly it is possible to clean in the solvent “blanket” of vapors, with the solvent vapors condensing to liquid on the part. But for faster, more reliable cleaning in the vapor degreaser, the parts normally are immersed into the liquid solvent. There, liquid surrounds the part and enters all of the nooks and crannies to maximize solvent contact and cleanliness.The concept behind vapor degreasing is simple. Figure 1 illustrates the design of a modern, efficient, two-sump degreaser. A vapor degreaser boils a liquid into a vapor, contains the vapors, cools the vapors back into a liquid, and collects this purified liquid for continuous use. A vapor degreaser therefore is not only a parts cleaning system but also a tight, fast, energy-efficient recycling system that captures and refreshes the solvent with little waste.
The solvent is placed in the “boil” sump (lower left chamber in Figure 1) and is heated to its boiling point, usually 100-170°F (38-77°C), depending on the solvent. The heat can be provided with electric heating elements, hot water coils, steam coils or the heat from a “heat pump” refrigeration unit.
It’s noteworthy that even a small water-cleaning system will consume considerably more energy in heating the cleaning solution than a vapor degreaser of comparable capacity. The higher energy consumption occurs because water has a much higher specific heat and a much higher latent heat of vaporization than vapor degreasing solvents. This fundamental characteristic of water also explains why it takes so many BTUs to dry the parts after they have been cleaned in an aqueous system. In contrast, some small vapor degreasers operate on 120 V power supplies.
Once boiling, the solvent produces a clear, dense vapor that rises through the machine, displacing the air in the degreaser. Eventually the vapors rise up and reach the lower set of cold coils, called the “primary condensing coils.” These coils chill the solvent vapors and condense the solvent back into its liquid state. This liquid drips into a condensate trough that is under the primary condensing coils and around the interior circumference of the machine. There it is routed through a water separator, decanting any water that may have condensed on the condensing coils and removing it from the solvent.*
At this point, the distilled solvent is directed back into the rinse sump from the water separator (lower right chamber in Figure 1). Since the rinse sump already is filled with clean solvent, the addition of clean, newly distilled solvent will cause the sump to overflow into the boil sump, completing the distillation cycle. The addition of this fresh, pure solvent maintains a consistently clean rinse sump and also allows contamination and particulate to be washed back into the boil sump and concentrated there.
Equipment Considerations
Numerous options are available that make the vapor degreasing process even simpler, cleaner and faster, some of which are shown in Figure 1. The rinse sump is usually fitted with a circulating filtration system to remove insoluble contamination (particulate). Another common option is for the rinse sump to be fitted with ultrasonic transducers to enhance cleaning. Automated hoists can free up technicians from lifting parts in and out of the system while also ensuring that the proper cycle time and part movement takes place, which can lead to reduced solvent use and more consistent cleaning.Another important feature of modern vapor degreasers is a second set of cooling coils, located above the primary condensing coils (also shown in Figure 1). Called “freeboard chillers,” these coils are always colder than the primary condensers, usually around -20°F (-29°C). Their purpose is to lower the temperature and humidity of the air above the vapor blanket to minimize solvent diffusion from the saturated vapor blanket into the air, thereby minimizing solvent losses. In addition, since the freeboard chillers dehumidify the area above the vapor blanket, minimal water will be condensed on the primary condensing coils, which helps maintain solvent integrity.
(Note that the freeboard chiller coils are not used to contain the solvent blanket in the degreaser. That’s the job of the primary condensing coils. If the vapor blanket ever rises above the primary condensing coils into the area of the freeboard chiller coils, there is something wrong with the primary condensing coils and a refrigeration technician needs to be consulted.)
Lastly, another option in the degreaser is the installation of “superheated” coils. These coils superheat the vapor blanket above the “normal” boiling point of the solvent. This superheated vapor quickly heats the freshly cleaned parts and ensures that all the condensed solvent on the parts is vaporized and recovered under the vapor blanket. This process guarantees that the parts are dry before being removed from the system, which minimizes solvent drag-out and solvent consumption.
There are more than a dozen manufacturers of vapor degreasers in the U.S., and several dozen more worldwide. Depending on the cleaning application and process requirements, the technology exists to handle the largest parts and highest volumes. These large machines, when properly designed, operated and maintained, can be extremely efficient with minimal solvent consumption.
Cost Comparison
Despite the historically proven performance advantages of vapor degreasers, many engineers worry about the operating costs of these systems. After all, water is basically free, while ozone-safe solvents cost $1,500-$10,000 per drum. Can vapor degreasers truly be cheaper to run than water cleaning systems?The best way to evaluate the operating costs of different types of cleaning systems is to compare them on a cost-per-part-cleaned basis. This approach provides an apples-to-apples comparison that can illuminate the hidden costs of water cleaning.
First, the acquisition and installation costs are tabulated. Included among these are the direct capital costs of the cleaning system (the hardware itself, plus the support systems, wastewater treatment systems, and so on), as well as the indirect capital costs (the floor space, upgrades to the facility’s electrical system, plumbing costs, etc.).
The next step is to estimate the direct operating costs for both systems. This estimate includes the solvent and water costs, energy costs, labor costs, waste disposal costs, inventory costs that change due to faster or slower cleaning cycles, and any other direct expense that touches the cleaning system. Engineers also will need to take into account the personnel time needed to operate and maintain the cleaning equipment. Vapor degreasers typically are almost maintenance-free; aqueous systems can be much more complex and time-consuming.
Then there is the solvent cost. While the solvent selection process is beyond the scope of this article, evaluating the cost of the solvent is simple. The proper way to estimate solvent costs is not to compare the cost per pound, but to compare the cost per part cleaned. For example, a modern vapor degreaser will use approximately 0.062 lb of solvent/hr/ft2 of solvent/air interface when in use. A typical 10-gallon degreaser has about 2.5 ft of solvent/air interface, so it will lose about 1.25 lb of solvent (less than one cup) in an eight-hour work day. If the solvent is priced at roughly $3/lb, the solvent cost for a day of cleaning is under $4, and the cost-per-part, assuming 1,000 parts were cleaned that day, is $0.00372 per part.
When these costs are tabulated and then divided by the total number of parts cleaned by the system, the true cost of cleaning becomes apparent.
Economical, Environmentally Acceptable Cleaning
For decades, the vapor degreasing process has proven to be the most consistent and “headache-free” cleaning process for manufacturing engineers. Vapor degreasing has come full cycle, and many engineers have realized that it is a safe, economical and environmentally acceptable cleaning method. Energy demands and new environmental concerns are generating an increased interest in the vapor degreasing process. If a current aqueous cleaning system is reaching the end of its life cycle, now is the time to explore vapor degreasing as an alternative in your manufacturing plant.To obtain the desired results in the most economical and environmentally acceptable manner, it is imperative that the degreaser system be properly configured, operated and maintained. In addition to the hardware issues, the proper solvent selection requires careful analysis, and that selection depends on the contamination being removed. When analyzing the application, always define the impurities first, then select the chemistry that removes those impurities, as well as the equipment that uses the chosen solvent properly.
It is clear that the vapor degreasing concept is being revitalized. In today’s world, where quality, reliability and energy efficiency are paramount, the old process of vapor degreasing deserves another look as a modern, planet-friendly and cost-effective cleaning process.
*Water and solvents are easily separated in these systems since they generally are not miscible in each other. The lighter water floats on top of the heavier solvent, and the water is easily separated and discharged from the system.
SIDEBAR: Why Consider Vapor Degreasing?
A properly designed, operated and maintained vapor degreasing process offers many advantages versus aqueous cleaners and other choices. Vapor degreasers and solvents:- Use minimal floor space
- Minimize energy consumption
- Minimize solvent consumption
- Distill and recycle the solvent for continued use
- Minimize waste disposal
- Minimize chemical exposure
- Provide consistent, reproducible cleanliness performance
- Can be completely automated
- Are easy to maintain
- Do not require a chemist to run
- Can easily clean complex configurations
- Have the lowest cost per part cleaned
SIDEBAR: Solvent Solutions
Prior to the 1990s, the two most common vapor degreasing solvents were CFC-113 and 1-1-1-trichloroethane. The production of these “Class I Ozone-Depleting Substances,” as defined under the Clean Air Act, was terminated on January 1, 1996, and industry has been living off stockpiles ever since. Scarcity has driven up prices, making these cleaners impractical as precision cleaners except in the most exotic uses.A less-damaging group of cleaners, called the “Class II Ozone-Depleting Substances,” was recommended to users as an interim cleaning option. The most popular of these was a solvent called HCFC-141b. However, the manufacture of HCFC-141b ended on January 1, 2003, and the use of this material in solvent cleaning applications was banned in 1997.
Fortunately, suppliers have developed more environmentally acceptable alternatives. Newer hydrofluorocarbon-based fluids and solvents based on n-propyl bromide (nPB) have zero or minimal ozone depletion and low global warming potential, while providing consistent, affordable, high-quality cleaning. Additionally, advanced product stewardship programs can help ensure the safest, most efficient use of these chemicals in vapor degreaser applications.
For more information about vapor degreasing, visit www.microcare.com.
Looking for a reprint of this article?
From high-res PDFs to custom plaques, order your copy today!