High-Performance Heat Protection
Nickel aluminide diffusion coatings help gas turbine components withstand extremely high temperatures. However, defects such as craters, drips, sags, bare spots and mudcracks can compromise performance and lead to high levels of rejects in the finishing operation. Following the coating supplier’s recommended surface preparation, application and diffusion procedures can eliminate coating defects and ensure high-quality components.
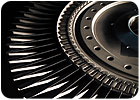
Gas turbines for aerospace and power generation applications are constantly being pushed to the limits of operation. Frequently, these limits are constricted by the component materials. For example, the combustors and other components farther aft in the engine (blades and vanes) often are exposed to temperatures in excess of 1600°F (871°C) under operation, depending on their location in the engine, the type of engine, the operating parameters and other factors. The high temperatures provide increased power and efficiency for the turbine. Stainless steel components with a high nickel content typically are used in these applications because they possess excellent strength at high temperatures. However, these materials are subject to high-temperature oxidation and hot corrosion attack.
Nickel aluminide coatings, which are hard and corrosion-resistant, have been used for decades to protect components that operate in temperatures from 1200 to 1800°F (649 to 982°C). Packed cementation is a method of applying nickel aluminide coatings in which the part is packed in a container with aluminum, an activator (usually a fluoride) and a thermal ballast such as aluminum oxide, and the entire container is heated to about 1350°F (732°C). Following this treatment, the parts are removed and further heat treated at about 1900°F (1038°C) for several hours to diffuse the aluminum into the surface of the part, creating a nickel aluminide. For certain applications, this process can be costly and time-consuming.
The invention of spray-applied diffusion coatings has streamlined the process of applying nickel aluminide coatings significantly. There are three key steps to achieving a high-performance spray-applied nickel aluminide finish: surface preparation, spray application of the slurry, and diffusion heat treatment. Although the spray-applied method seems to be straightforward, many potential pitfalls await the inexperienced applicator.
In grit blasting, the surface of the part typically is abraded with a 120- to 240-mesh aluminum oxide. The grit blast provides a roughened surface for the spray-applied coating to adhere prior to diffusion.
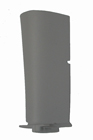
It is during this stage that inadequate surface preparation often becomes a problem. Any organic contaminants on the part - even just a fingerprint from handling - will cause the coating to crater or crawl. The finishing operator’s initial reaction might be to apply the coating heavier to cover the defect, but this response usually exacerbates the situation.
Most spray-applied diffusion coatings are best applied using a conventional air atomizing touchup spray gun. When spraying larger parts, the tendency is to switch to a larger industrial or automotive spray gun. However, the larger gun can cause problems because of the increased spray droplet size, which can lead to difficulty in wetting the surface with the coating.
When using a touchup gun at about 40 psi, it is best to apply a light “mist coat” that is barely noticeable on the surface. After allowing the “mist coat” to air dry to a dull gray, a wet coat should be applied so that the surface has a uniform glossy appearance that is free of runs or sags.
Following spray application of the coating, the parts need to air dry to a dull gray finish. They should then be cured at 650°F (343°C) for 30 minutes to adhere the coating firmly to the surface and drive out any remaining water in the coating prior to diffusion. If this step is bypassed, it will create an uneven diffusion. Several coats might be needed to achieve the necessary dry film thickness, which is usually about 3 to 5 mils. Inspection of the thickness is best performed with an eddy current gauge.
Figure 1 shows an example of a turbine blade after the 650°F cure but prior to diffusion. At this stage, the coating sometimes is referred to as the “green coat.”
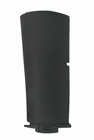
The equipment required to perform the diffusion varies greatly, depending on the size of the parts. Parts from large power generation units require large furnaces for diffusion; however, a certain degree of the aluminum will be released in the form of a vapor, which will then adhere to the inside of the furnace. For this reason, most applicators perform diffusion in a retort, which is essentially a chamber that holds the parts to be diffused and that can be sealed to draw a vacuum or be filled with an inert gas such as argon.
The retort typically is manufactured from Inconel or another high-temperature alloy. Recently, however, the cost of these metals has been climbing quickly. Many applicators have begun to research means of using lower-grade steels for the retort by coating the steels with a material that will protect the outside from oxidation while running the diffusion cycle.
In a typical diffusion process for gas turbine blades, the green coated blades or parts are placed inside the retort, usually with as many other blades or parts as will fit, and then the retort is placed in the diffusion furnace and purged with argon. The furnace is next raised to about 1650°F and held for about four hours. The parts are allowed to cool and are then removed. The parts will exhibit a friable white layer on the surface, sometimes referred to as the bisque. Applicators who are not familiar with this type of coating might think that the diffusion went poorly after seeing the bisque. The bisque is just remnants of the binder that held the green coat together before the parts entered diffusion. It should be removed by glass bead burnishing in a standard blast cabinet. The resultant nickel aluminide should be a uniform dark gray, as shown in Figure 2.
It is at this time that problems with the coating application will become evident. Any imperceptible craters or surface defects that were present in the green coat will show up as an unacceptable bare spot in the nickel aluminide. Another problem seen only after diffusion is the appearance of mudcracks on the surface of the nickel aluminide layer, which often are caused by applying too much material prior to the 650°F green coat cure. Since it is difficult to fix these problems once the parts have gone through diffusion, great care should be taken to inspect the parts for defects prior to the diffusion cycle.
A scrap part or sample panel should be included with each batch of parts. After diffusion, the scrap part should be cross-sectioned and mounted for metallographic analysis to determine the depth of diffusion and, if necessary, the ratio of the nickel aluminide. Figure 3 shows a cross-section of a part after the diffusion process was complete. The bottom layer is the raw substrate, followed by an interdiffusion zone and then the nickel aluminide layer.
For more information, visit www.coatingsforindustry.com.
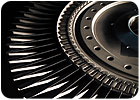
Gas turbines for aerospace and power generation applications are constantly being pushed to the limits of operation. Frequently, these limits are constricted by the component materials. For example, the combustors and other components farther aft in the engine (blades and vanes) often are exposed to temperatures in excess of 1600°F (871°C) under operation, depending on their location in the engine, the type of engine, the operating parameters and other factors. The high temperatures provide increased power and efficiency for the turbine. Stainless steel components with a high nickel content typically are used in these applications because they possess excellent strength at high temperatures. However, these materials are subject to high-temperature oxidation and hot corrosion attack.
Nickel aluminide coatings, which are hard and corrosion-resistant, have been used for decades to protect components that operate in temperatures from 1200 to 1800°F (649 to 982°C). Packed cementation is a method of applying nickel aluminide coatings in which the part is packed in a container with aluminum, an activator (usually a fluoride) and a thermal ballast such as aluminum oxide, and the entire container is heated to about 1350°F (732°C). Following this treatment, the parts are removed and further heat treated at about 1900°F (1038°C) for several hours to diffuse the aluminum into the surface of the part, creating a nickel aluminide. For certain applications, this process can be costly and time-consuming.
The invention of spray-applied diffusion coatings has streamlined the process of applying nickel aluminide coatings significantly. There are three key steps to achieving a high-performance spray-applied nickel aluminide finish: surface preparation, spray application of the slurry, and diffusion heat treatment. Although the spray-applied method seems to be straightforward, many potential pitfalls await the inexperienced applicator.
Surface Preparation
As with the application of most coating systems, proper surface preparation is paramount to creating an acceptable coating. For turbine blades, the first surface preparation step is chemical or thermal degreasing. All organic contaminants (oils and dirt) must be completely removed during this stage so that they are not impinged in the surface of the part during the next step of grit blasting.In grit blasting, the surface of the part typically is abraded with a 120- to 240-mesh aluminum oxide. The grit blast provides a roughened surface for the spray-applied coating to adhere prior to diffusion.
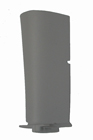
Figure 1. A turbine blade after the 650°F cure but prior to diffusion.
Spray Application
The spray-applied liquid coating is composed of a water-based inorganic phosphate binder with dispersed aluminum powder and a small percentage of silicon metal powder. The material has a low viscosity, about 200 centipoise (cp), so the applicator must control the application rate tightly to prevent sagging and running.It is during this stage that inadequate surface preparation often becomes a problem. Any organic contaminants on the part - even just a fingerprint from handling - will cause the coating to crater or crawl. The finishing operator’s initial reaction might be to apply the coating heavier to cover the defect, but this response usually exacerbates the situation.
Most spray-applied diffusion coatings are best applied using a conventional air atomizing touchup spray gun. When spraying larger parts, the tendency is to switch to a larger industrial or automotive spray gun. However, the larger gun can cause problems because of the increased spray droplet size, which can lead to difficulty in wetting the surface with the coating.
When using a touchup gun at about 40 psi, it is best to apply a light “mist coat” that is barely noticeable on the surface. After allowing the “mist coat” to air dry to a dull gray, a wet coat should be applied so that the surface has a uniform glossy appearance that is free of runs or sags.
Following spray application of the coating, the parts need to air dry to a dull gray finish. They should then be cured at 650°F (343°C) for 30 minutes to adhere the coating firmly to the surface and drive out any remaining water in the coating prior to diffusion. If this step is bypassed, it will create an uneven diffusion. Several coats might be needed to achieve the necessary dry film thickness, which is usually about 3 to 5 mils. Inspection of the thickness is best performed with an eddy current gauge.
Figure 1 shows an example of a turbine blade after the 650°F cure but prior to diffusion. At this stage, the coating sometimes is referred to as the “green coat.”
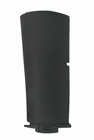
Figure 2. Following diffusion, the nickel aluminide should be a uniform dark gray.
Diffusion
The diffusion process is performed at high temperatures (1650 to 1950°F [899 to 1066°C]) either in a vacuum or an inert gas atmosphere. The inert gas or vacuum prevents oxidation at the high diffusion temperatures and allows the aluminum in the green coat to migrate into the substrate, where it bonds with the nickel to become nickel aluminide.The equipment required to perform the diffusion varies greatly, depending on the size of the parts. Parts from large power generation units require large furnaces for diffusion; however, a certain degree of the aluminum will be released in the form of a vapor, which will then adhere to the inside of the furnace. For this reason, most applicators perform diffusion in a retort, which is essentially a chamber that holds the parts to be diffused and that can be sealed to draw a vacuum or be filled with an inert gas such as argon.
The retort typically is manufactured from Inconel or another high-temperature alloy. Recently, however, the cost of these metals has been climbing quickly. Many applicators have begun to research means of using lower-grade steels for the retort by coating the steels with a material that will protect the outside from oxidation while running the diffusion cycle.
In a typical diffusion process for gas turbine blades, the green coated blades or parts are placed inside the retort, usually with as many other blades or parts as will fit, and then the retort is placed in the diffusion furnace and purged with argon. The furnace is next raised to about 1650°F and held for about four hours. The parts are allowed to cool and are then removed. The parts will exhibit a friable white layer on the surface, sometimes referred to as the bisque. Applicators who are not familiar with this type of coating might think that the diffusion went poorly after seeing the bisque. The bisque is just remnants of the binder that held the green coat together before the parts entered diffusion. It should be removed by glass bead burnishing in a standard blast cabinet. The resultant nickel aluminide should be a uniform dark gray, as shown in Figure 2.
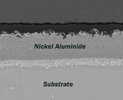
Figure 3. A cross-section of a part after the completed diffusion process. The bottom layer is the raw substrate, followed by an interdiffusion zone and then the nickel aluminide layer.
A scrap part or sample panel should be included with each batch of parts. After diffusion, the scrap part should be cross-sectioned and mounted for metallographic analysis to determine the depth of diffusion and, if necessary, the ratio of the nickel aluminide. Figure 3 shows a cross-section of a part after the diffusion process was complete. The bottom layer is the raw substrate, followed by an interdiffusion zone and then the nickel aluminide layer.
Defect-Free Protection
Nickel aluminide coatings are allowing turbines to operate in temperature ranges not otherwise reachable. They are finding use as a platform to apply thermal barrier coatings and are continually being modified to offer protection at even higher temperatures. Following the supplier’s recommended preparation, application and diffusion steps can help ensure a high-performance, defect-free coating.For more information, visit www.coatingsforindustry.com.
Looking for a reprint of this article?
From high-res PDFs to custom plaques, order your copy today!