Global TiO2 Pigment Industry Has Strongest Year in Two Decades
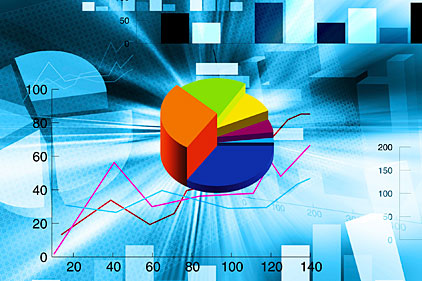
VICTORIA PARK, WA - The $17 billion global titanium dioxide (TiO2) pigment industry improved profitability in 2011, with figures that TZ Minerals International Pty. Ltd. (TZMI) believes are the strongest in two decades.
In the eighth edition of the Global TiO2 Pigment Producers Comparative Cost and Profitability Study 2012, TZMI reported that manufacturing cost is expected to increase dramatically in the next two to three years as legacy ore contracts roll off and are replaced by contracts that strongly favor feedstock producers.
In 2008, the TiO2 pigment industry operated in an environment of depressed profitability, with record-high raw material and energy costs resulting in an oversupply of TiO2 in western markets. With the onset of the global financial crisis, inventories were drawn down, and capacity idled, making it difficult to restart the supply chain when the market recovered.
The tight supply situation started in 2010 and continued through 2011, with price increases announced regularly during the two-year period. As a result, global pricing increased by 8 percent in 2010 and almost 40 percent in 2011. The EBITDA margin for the industry increased from a level of 11 percent entering 2010 to 32 percent exiting 2011 (based on reporting companies).
In 2011, production (pro forma basis) increased 3.5 percent after demand increased with the improved economy, consumers re-stocked their supply chains, and some producers – due to lack of available product – bought ahead of needs to de-risk availability in future months. Chinese producers led the production growth with a very bullish 14.5 percent year-on-year increase in output.
Growth during the last five years has been led by major emerging economies (most notably China), the emerging economies of Asia-Pacific (Indonesia, Thailand, Vietnam, Philippines, etc.), Brazil, Turkey, Russia and India. The mature economies of Western Europe and North America have remained flat or declined slightly in consumption.
Profitability gains in 2011 resulted from improved sales pricing due to strong demand, limited supply and low inventories. In 2011, all chloride plants were profitable according to TZMI’s independent analysis. DuPont held the lowest cost position with its 340,000 tpa plant in DeLisle, MS. Plants operated by all five of the major global producers (DuPont, Cristal Global, Huntsman Corp., Kronos Worldwide and Tronox Inc.) were among the 20 lowest-cost facilities. Half of the 20 lowest-cost plants were located in China.
For more information about the study, visit www.tzmi.com.
Looking for a reprint of this article?
From high-res PDFs to custom plaques, order your copy today!