Pigment Dispersants for Improving Color Development in Waterborne Acrylic and Styrene/Acrylic Paints

In order to achieve high-quality coatings, a pigment dispersion must be liquid, have an optimal particle size and be stable over long periods of time. Surfactants can offer dispersion and stabilization of the pigment particles. During the grinding process, dispersing agents distribute and stabilize the smaller pigment particles, restricting re-agglomeration. These same dispersing agents help prevent flocculation of the pigment particles during storage and when mixed in a white-base, latex paint. This study looked at improvement of the shelf life of the pigment dispersion, as well as enhancement of the compatibility of the pigment dispersion with a waterborne, white-base, latex paint.
Experimental
Raw Materials
The dispersing agents (DAs) used as standards were a nonyl-phenol with 9-10 mol EO (STD NP) and a high-molecular-weight block copolymer with pigment affinic groups (STD BCP). The comparative nonionic surfactants were E-Sperse® 326 (326), E-Sperse 343 (343) and E-Sperse 345 (345). Comparative anionic surfactants were E-Sperse 713 (713), E-Sperse 1202 (1202), E-Sperse 1203 (1203) and E-Sperse 1204 (1204). 713 and 1202 are sulfates, while 1203 and 1204 are phosphates. Phthalo green (PG7) was the organic pigment that was dispersed in a water-based system for the study. The wetting agent, defoamer and biocide were the same in all formulations.
Dispersing Agents Prescreening
50% by weight of PG7 was added to 50% by weight of demineralized water (DMW). Using a syringe, STD NP was added in a dropwise fashion until the pigment went into solution. The volume of STD NP needed was noted and converted to mass of 100% active product. STD BCP and other surfactants were evaluated in a similar manner. Any product that required equal to or less than the mass of the STD NP was tested in the Dispersant Demand test.
Dispersant Demand
50% by weight of PG7 was added to 50% by weight of DMW. Incremental volumetric additions of the dispersant were calculated, taking into account density, percent activity and grams of pigment to be used. Aliquots of dispersant to wet out the pigment and defoamer may have been required before the implementation of a high-speed grind. After the grind, a viscosity measurement was taken. An aliquot of dispersant was added, stirred and measured for viscosity. This was repeated until the viscosity leveled out or continued to rise. Any dispersant that had a lower viscosity or required a lower dosage to get to a low viscosity when compared to the standards’ viscosity or dosage was considered for the pigment dispersion preparation.
Pigment Dispersion Preparation
The general formula for the organic pigment dispersion formulation is shown in Table 1. All materials, except the pigment, were charged to a stainless steel double wall container, which was then placed on a disperser with a Teflon milling impeller. After stirring at low rpm for 5-10 min to homogenize, the pigment was slowly added over 20 to 30 min. Once the pigment was incorporated, Zircoa® beads were added and the mill speed was increased. The grind was checked after a minimum of 30 min milling. Once the grind met 7+ Hegman, the dispersion was complete.

Water-based, interior satin paints were purchased at local hardware and paint stores. The resin system of these paints was either acrylic or styrene acrylic. The pigment dispersions were added to the latex paints at approximately 8 oz/gallon. The paint was placed in a paint shaker for approximately 4 min, or until homogenous.
Viscosity
The initial viscosity, based on ASTM D 2196, of the pigment dispersion and the tinted paint was determined at 25 °C using a calibrated, rotational viscometer after the dispersion or paint was allowed to sit overnight. The pigment dispersions and tinted paints were placed in a 54 °C oven. Viscosity was retested after 1 week and 2 weeks in the oven to determine storage stability.
Color Difference
ASTM D 2244, E 308 and E 1164 are references in the calculation of color differences, the use of the CIELab, and the use of a spectrophotometer for object color evaluation. The color differences between the tinted paints employing the standard surfactants and the other surfactants were measured using an X-Rite spectrophotometer. The tinted paint was drawn down on a Leneta 3B opacity chart using an automatic drawdown machine and a #40 drawdown rod, which is equivalent to a 4-mil wet film thickness. The film was allowed to dry in a vertical position in a wall chart hanger. When dry, three points on the white background were measured using the CIELab color system. The average of these measurements was taken and compared to the average measurement of the tinted paint using the standard surfactants. Color difference can be expressed in a single numerical value called DEcmc, which is based on variables of lightness, chroma and hue. The DEcmc results were used as a comparison of STD NP and STD BCP to the other DAs.
Color Acceptance
“Rub-ups” were made on drawdowns of the tinted paint to determine the compatibility of the pigment dispersion with the paint. Paints were tinted immediately after the pigment dispersion was complete and then again after the pigment dispersion was kept in a 54 °C oven for two weeks. The tinted paint was drawn down on a Leneta 3B opacity chart using an automatic drawdown machine and a #40 drawdown rod, which is equivalent to a 4-mil wet film thickness. A rub-up was immediately applied to the film using slight pressure and a circular motion of a gloved finger. The film was allowed to dry in a vertical position in a wall chart hanger. When dry, the swirls were examined, noting any differences in color in the swirl and at the contact point of the non-disturbed film. A good rub-up showed no color differences to the naked eye, while a poor rub-up showed extreme differences in color. To gain a quantitative reference, three points of the undisturbed paint were measured using CIELab color system with an X-Rite spectrophotometer, then three points were measured in the disturbed surface, or “swirls.” The color difference was calculated between the disturbed and undisturbed surfaces. If the DEcmc of the standard was greater than the DEcmc of the tested dispersing agent, then the pigment dispersion made with that dispersing agent was considered more compatible with the paint than the pigment dispersion made with the standard.
Syneresis
The tinted paints were measured for syneresis, or the degree of separation, after one week and two weeks in a 54 °C oven. Using a dental ruler, the measurement of the layer of semi-clear liquid, which had formed on the top of the paint, was taken in the 4-oz jar in which the tinted paint was stored. These measurements were compared with the untinted paint and against the tinted paint which incorporated the standards used in this study.
Gloss
20° and 60° gloss, based on ASTM D 523, were measured using micro-TRI-gloss glossmeter. The tinted paint was drawn down on a Leneta 3B opacity chart using an automatic drawdown machine and a #40 drawdown rod, which is equivalent to a 4-mil wet film thickness. The film was allowed to dry in a vertical position in a wall chart hanger. When dry, three points on the white background were measured. The average of these measurements was taken and compared to the average measurement of the tinted paint using the standard surfactants.
Results
Viscosity of Pigment Dispersion
Initially, all of the pigment dispersions had viscosities ranging from 432 to 6,265 cps (Table 2). All of the comparative DAs, except 1204, had an initial viscosity lower than the standards.
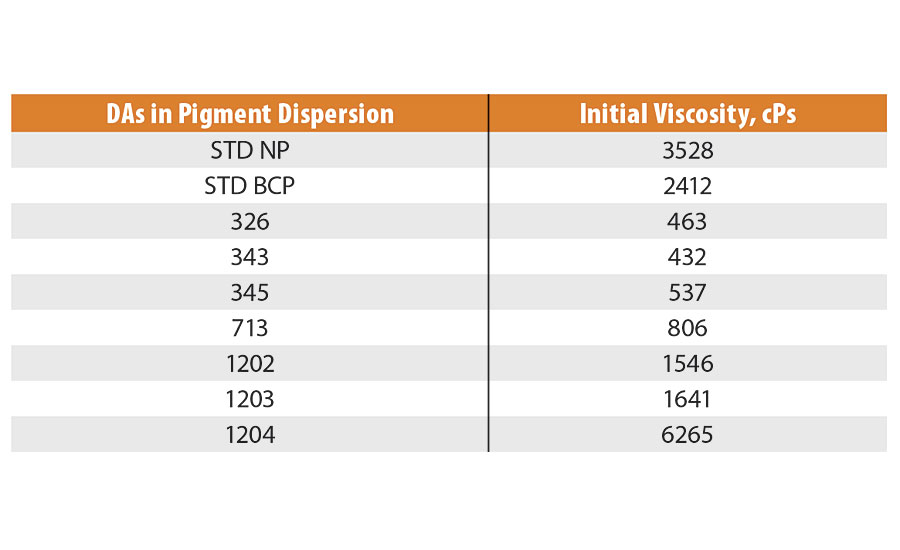
Figure 1 shows the results of viscosity testing of the pigment dispersion measured initially, after one week and after two weeks in an oven set at 54 °C. After being in the oven, the standards and 1204 increased in viscosity significantly. After the initial measurement, STD BCP had too high of a viscosity to be measured by the rotational viscometer. STD BCP was a clumpy paste that did not thin when stirred. After being in the oven for one week, STD NP jumped to a viscosity of 166,000 cPs and then to 775,000 cps. STD NP was an air-entrained paste that was thixotropic, but not fluid. All of the pigment dispersions containing the comparative DAs were thixotropic after being in the oven, but once thinned, viscosities could be measured. With the exception of 1204, all comparative dispersions remained below 40,000 cPs with the anionics - 713 and 1202 - keeping the lowest viscosities at one week and 343, 345, 1202, and 1203 below 20,000 cPs after two weeks. Overall, 1202 performed the best, with the highest viscosity recorded at 5,155 cPs after two weeks in the oven.
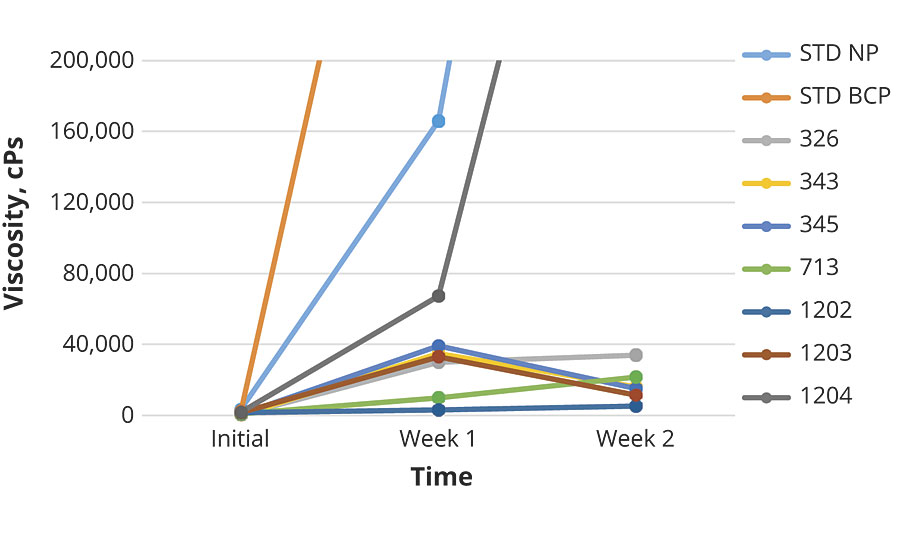
Viscosity of Paint
Figures 2-4 show the results of viscosity testing of the pigment dispersions mixed into three commercially available, white acrylic bases measured initially, after one week and after two weeks in an oven set at 54 °C.
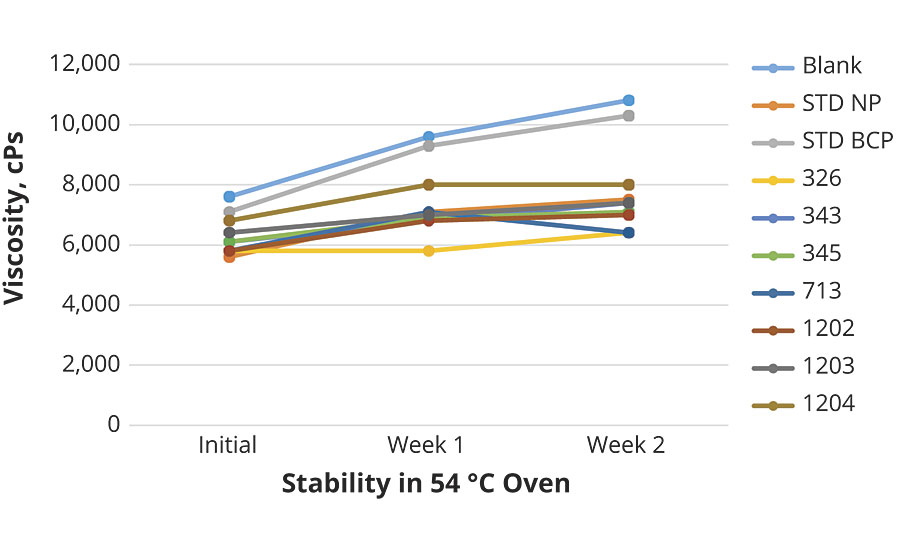
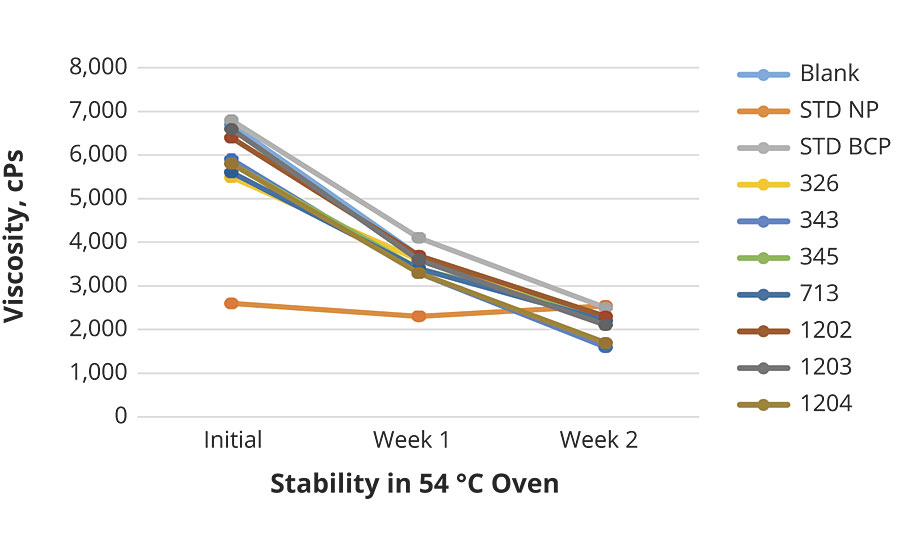
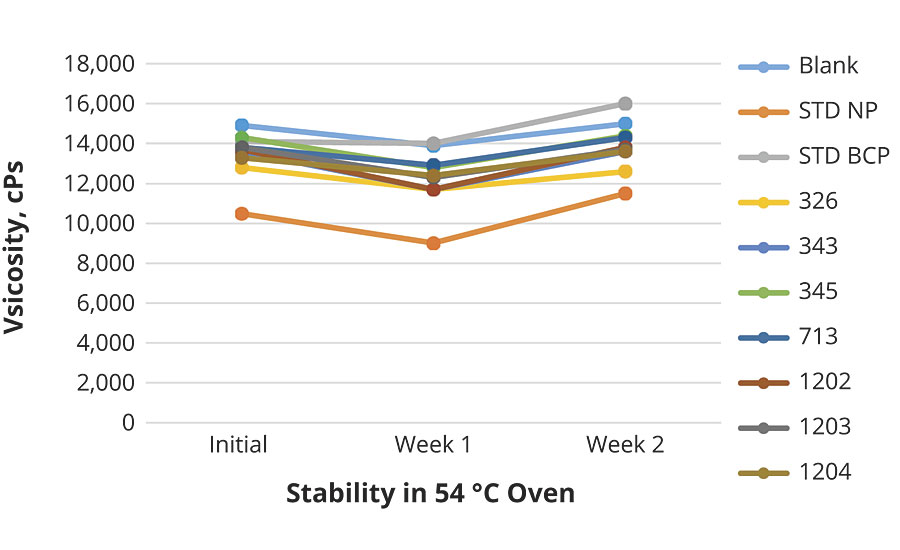
In Acrylic Paint 1, 326, 343, 345, 1202 and 1203 had lower viscosities than STD NP and STD BCP for the whole two week storage in the oven. In Acrylic Paint 2 all of the pigment dispersions with the comparative DAs incorporated into the paint had lower viscosities than the two standards after two weeks in heated storage. The STD NP had the lowest viscosity in Acrylic Paint 2 initially and after one week in storage. In Acrylic Paint 3 STD NP had the lowest viscosity overall, but the comparative DAs outperformed STD BCP.
The viscosity results of the pigment dispersions mixed into a styrene acrylic, white base paint, measured in the same fashion as in the acrylic paints, are shown in Figure 5. STD NP had the lowest viscosity overall, but the STD BCP had a significantly higher viscosity than the comparative DAs during the two week storage.
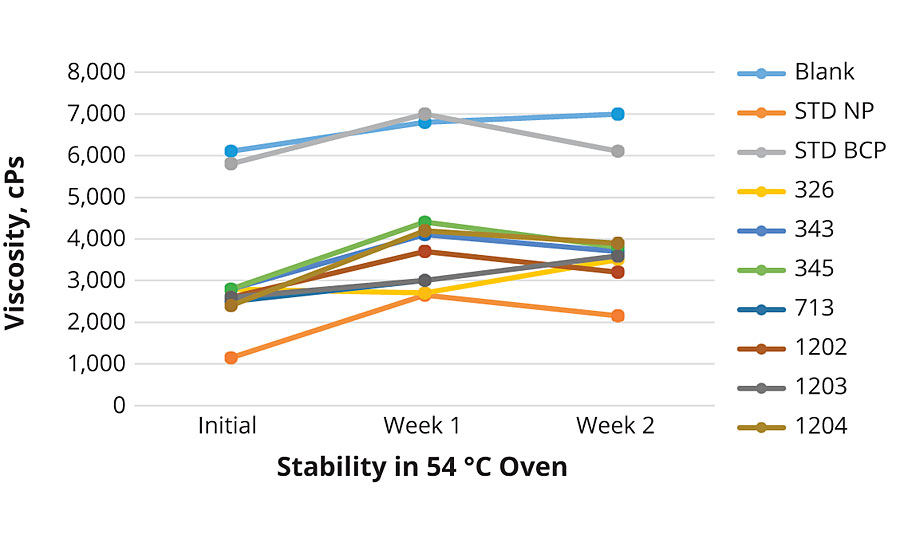
Color Difference
All tinted paints were measured against the corresponding tinted paint that contains STD NP and STD BCP. L*a*b*and L*C*h results were evaluated for each pigment. Figure 6 shows CIELab results of PG7 pigment dispersions in an acrylic paint in relation to STD BCP. Most of the results fell near to the standard (the intersection of the axes), but more toward the yellow/red. The outlier was the STD NP9 that was deep into the green area, which was marked as marginally acceptable by being just within the oval depicting that which is still considered comparable to STD BCP.
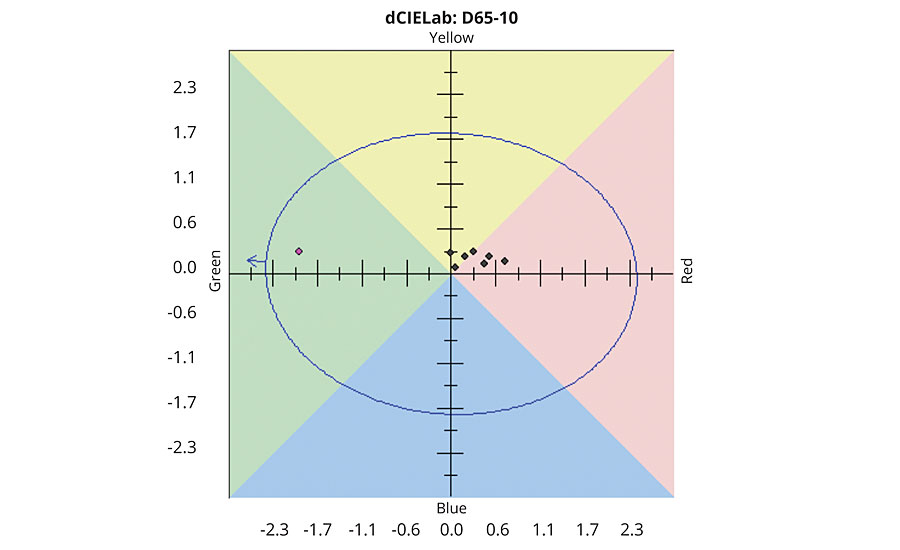
Figure 7 shows CIELab results of PG7 pigment dispersions in a styrene acrylic paint in relation to STD BCP. Most of the results fell toward the yellow/green, with over half depicted in red, indicating marginally acceptable. The STD NP9 was also in the green area, but higher toward the yellow. The other two acrylic paints followed the same pattern of results as in Acrylic Paint 1.
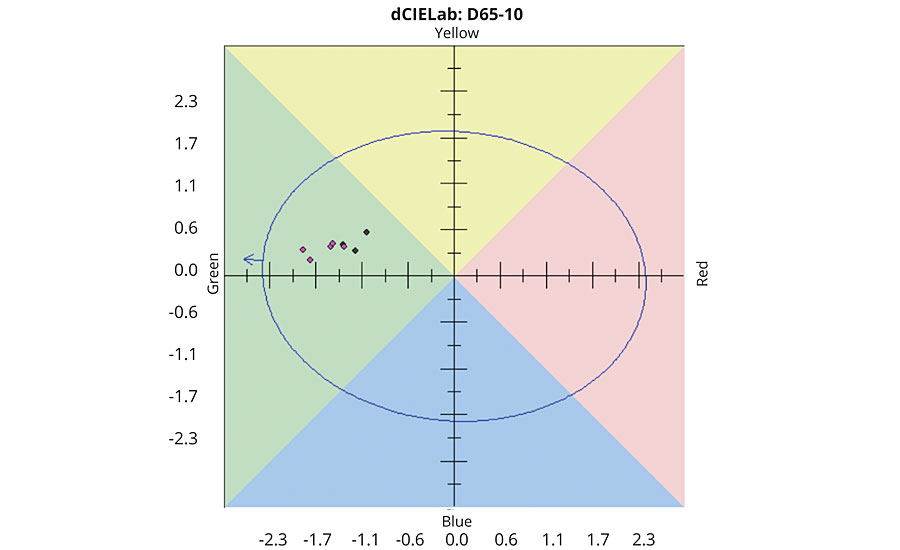
As a general rule, if DEcmc is less than 1.0, the surfactant is comparable with that of the standard used in the pigment dispersion. Table 3 lists the DEcmc of the tinted paints when using STD BCP as the standard surfactant. All of the dispersing agents had a DEcmc less than 1.0 in the acrylic paints. The dispersing agents that tested with DEcmc less than 1.0 in the styrene acrylic paint were 326, 343 and 1204.
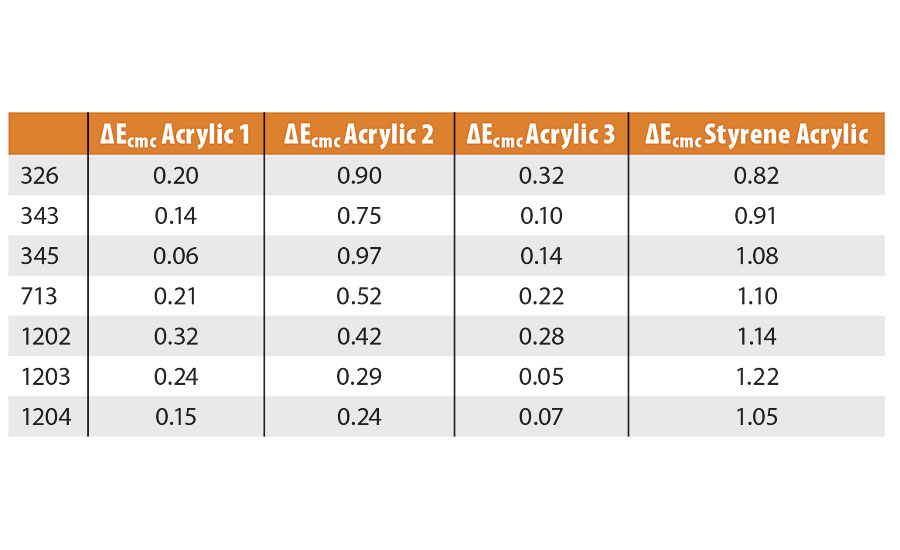
Table 4 lists the DEcmc of the tinted paints when using STD NP as the standard surfactant. All of the dispersing agents had a DEcmc of less than 1.0 in the styrene acrylic paint and in Acrylic Paint 3. The dispersing agents that tested with DEcmc of less than 1.0 in the Acrylic Paint 2 were the anionics – 713, 1202, 1203 and 1204. None of the DAs tested below 1.0 in DEcmc in Acrylic Paint 1.

Color Acceptance
Rub-up results in the Acrylic Paint 1 (Figure 8) demonstrated none of the pigment dispersions initially offered as good of color acceptance as the STD NP, while the dispersions made with 343, 345, 1202, 1203 and 1204 showed better color acceptance than STD BCP. Paints tinted with pigment dispersions that have been heat-aged for two weeks presented greater differences in compatibility. 343, 345 and 1203 had lower DEcmc than either of the standards. 326 and 1202 performed better than STD BCP after heat-aging.
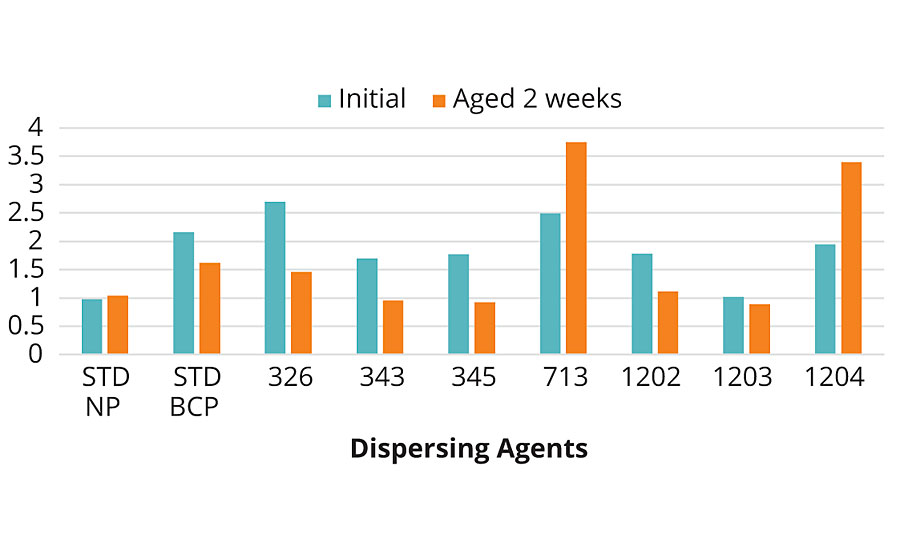
Rub-up results in the Acrylic Paint 2 (Figure 9) showed none of the pigment dispersions initially offered as good of color acceptance as the STD NP, while all of the dispersions had better color acceptance than STD BCP. In the tinted paint with pigment dispersions that have been heat-aged for 2 weeks, 326, 343, 345 and 1203 had lower DEcmc than either of the standards. 1204 performed better than STD BCP after heat-aging.
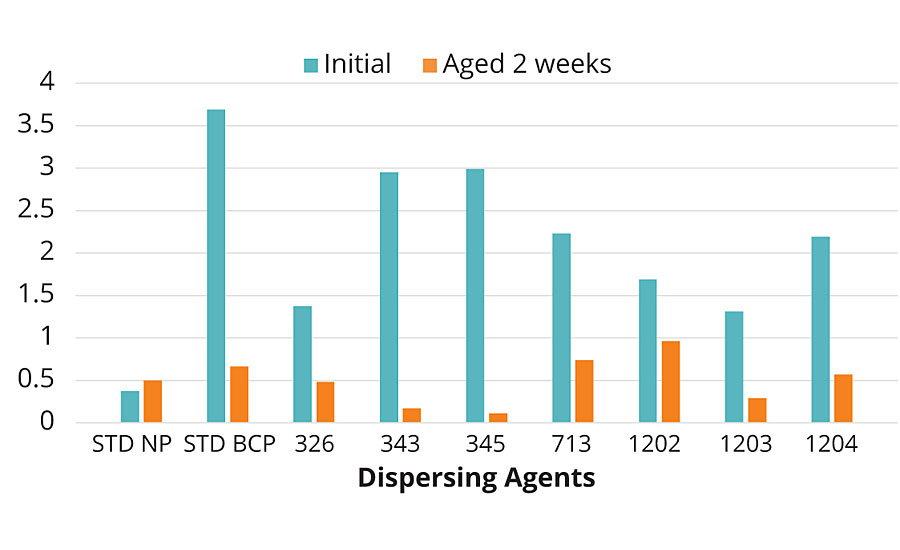
Rub-up results in the Acrylic Paint 3 (Figure 10) revealed that all of the pigment dispersions initially offered better color acceptance than the STD NP, while none of the dispersions showed better color acceptance than STD BCP. In the tinted paint with pigment dispersions that have been heat-aged for 2 weeks, 343 and 1203 had lower DEcmc than either of the standards. 1202 and 1204 performed better than STD NP after heat-aging.
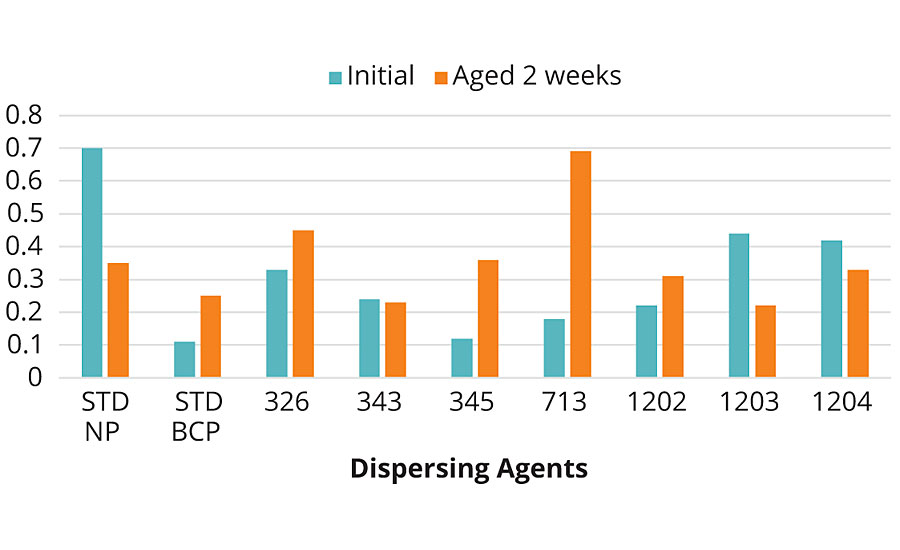
Rub-up results in the Styrene Acrylic Paint (Figure 11) showed the pigment dispersions made with 326, 1203 and 1204 initially offer better color acceptance than the STD NP, while all of the dispersions, except 345, had better color acceptance than STD BCP. In the tinted paint with pigment dispersions that have been heat-aged for 2 weeks, 343 and 1203 had lower DEcmc than either of the standards. 326 performed better than STD NP after heat-aging.
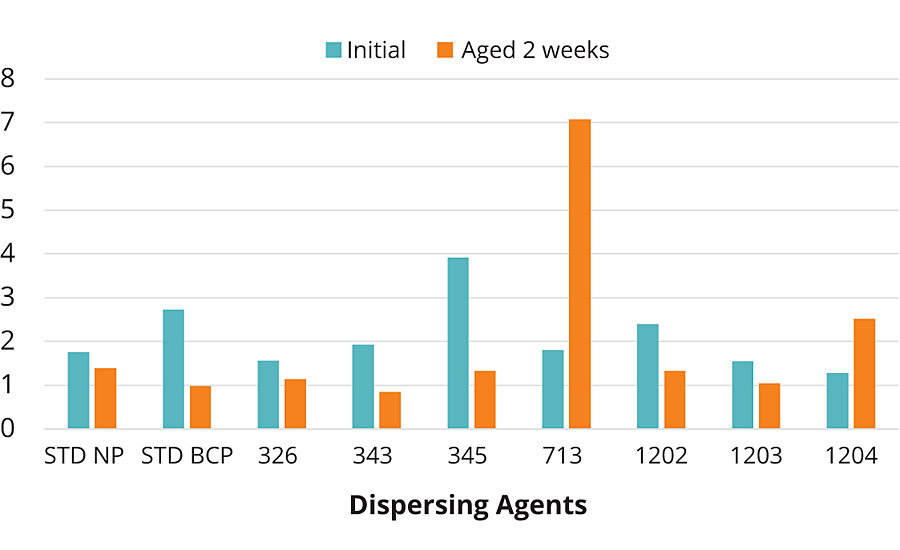
Syneresis
No significant differences in syneresis between the untinted paint and the paint tinted with pigment dispersions containing the standard dispersing agents in the acrylic paints was noted. There was some syneresis in the styrene acrylic paint, not only a clear layer, but also a white layer. This happened in the tinted paints with the comparative DAs, as well as the standard DAs. The clear layer tended to be 1.0-1.5 mm, while the white layer ranged from 8-13 mm. When shaken, the paint easily homogenized.
Gloss
A perceivable difference to the trained observer would be a difference of five gloss units or greater. The gloss readings showed no significant differences between the initial readings and the readings after three and seven days. There was, also, no significant differences between the comparative DA tinted paints and the standard tinted paints. The three- and seven-day samples were compared to the initial standard readings, as well, with no noted differences.
Conclusion
This study does not reveal any dispersing agent, including the standards, that works in all of the pigment dispersions and paints. The anionic dispersing agents, such as E-Sperse 1202 and 1203, show better application characteristics than the standards overall. E-Sperse 1202 especially has demonstrated maintaining a lower viscosity in the pigment dispersion. E-Sperse 1203 has proven to help with color acceptance in all of the paints tested, acrylic and styrene acrylic. The nonionics – E-Sperse 326, 343 and 345 – have displayed results better than the standards in most of the application testing, but they have notably presented improved color development and dispersion quality to the tinted paints, both acrylic and styrene acrylic. To summarize, for improved compatibility of the pigment dispersion with acrylic or styrene acrylic paints E-Sperse 326, 343, 345 and 1203 have shown performance better than the standards. And stability of the pigment dispersion would benefit from formulating with E-Sperse 1202. n
References
1. Van de Mark, M.R.; Collier, H.L.; Shuman, Thomas. Basic Composition of Coatings, UMR Coatings Institute, University of Missouri-Rolla, Rolla, Missouri, March 14-18, 2005.
2. Jackson, M. Overview of Polymer Types and Coating Formulation, Specialty Coating Services, Inc., Louisville, Kentucky, July 19, 2006.
3. ASTM Standard D 523-14, Standard Test Method for Specular Gloss, ASTM International, West Conshohocken, PA, 2014, www.astm.org.
4. ASTM Standard D 2196-15, Standard Test Methods for Rheological Properties of Non-Newtonian Materials by Rotational Viscometer, ASTM International, West Conshohocken, PA, 2015, www.astm.org.
5. ASTM Standard D 2244-16, Standard Practice for Calculation of Color Tolerances and Color Differences from Instrumentally Measured Color Coordinates, ASTM International, West Conshohocken, PA, 2016, www.astm.org.
6. ASTM Standard E 1164-12(2017)e1, Standard Practice for Obtaining Spectrometric Data for Object-Color Evaluation, ASTM International, West Conshohocken, PA, 2017, www.astm.org.
For more information, e-mail blowe@ethox.com.
Looking for a reprint of this article?
From high-res PDFs to custom plaques, order your copy today!