Novel Water-Based Energy-Curable PU Dispersions

Investing in a sustainable future and building a coating resins portfolio on green core technologies, including waterborne, energy-curable and powder product ranges is a priority for our company. A focus is dedicated to the use of safer materials and renewable sourcing with low air emissions, energy efficiency and circular economy as other major cornerstones.
The introduction of energy-curable polyurethane dispersions (UV PUDs) to complement the traditional radiation curing technology profoundly changed the market landscape by bringing coating performance and sustainability to the next level of requirements. They re-combine in one single product the respective benefits of functionalized polyurethanes, waterborne dispersions and energy curing.
In order to emphasize the sustainable attributes of this fast-growing product range, we created a straightforward model inspired by Life Cycle Analysis, looking at three fundamental dimensions: the composition, the performance-in-use, and the lifetime and disposal (Figure 1).
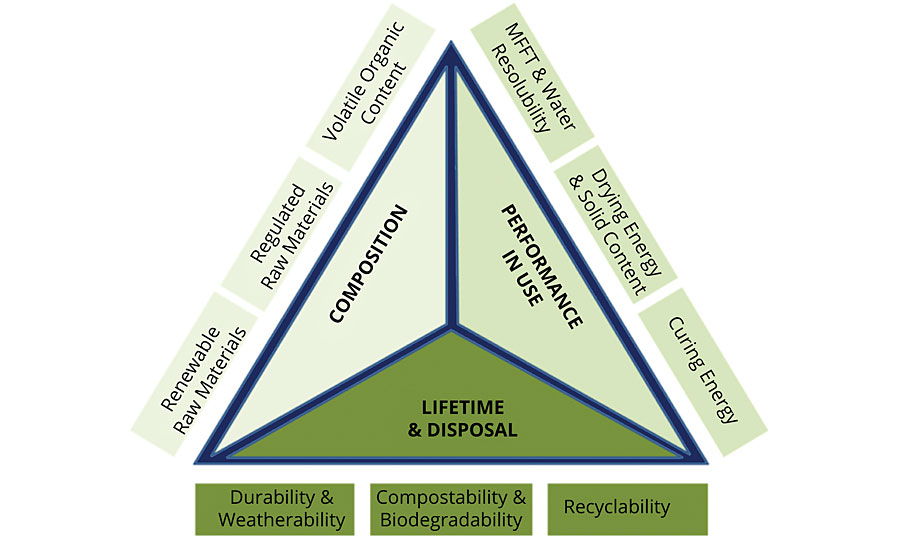
The Composition
Aqueous colloidal dispersions of acrylated polyurethane oligomers (UV PUDs) largely respond to the environmental regulations due to their waterborne nature and their low level of volatile organic compounds (VOCs). The use of raw materials of concern is restricted in our products, so that most are exempt from tin catalyst and alkyl phenol ethoxylate emulsifiers. It is also possible to introduce renewable raw materials coming from vegetable feedstock and certify the resulting bio-based carbon content (ASTM D6866) as a base for reduced material carbon footprint.
The Performance in Use
UV PUDs have good colloidal stability, and their low viscosity (sometimes associate to high solid content) makes them particularly suitable for application by spray, curtain or roller onto substrates like wood. They present the unique feature that the film formation (drying) and hardening (photo-curing) take place during two distinct steps. Their minimum film formation temperature (MFFT) is usually very low (below 10 °C) and does not require the use of additional coalescing agents that would contribute to increase VOC. The physically drying nature of many products (tack-free before cure) constitutes a distinct advantage for easy manipulation of the coated panels, surface embossing or field-applied operations. Moreover, some products can be made water-resoluble before cure, which allows easy cleaning of dried polymer without any solvent during the application. Finally, they encompass the high productivity of traditional radiation curing compositions by combining easy water evaporation and instantaneous ultraviolet or electron beam curing. New developments in the field of low-energy LED cure anticipate a future trend of the technology.
Lifetime and Disposal
The coatings obtained after curing are characterized by excellent resistance properties. The microstructure of the cured coating typically consists of soft and hard hydrogen-bonded segments entrapped within a dense crosslinking network, providing a particular ability to balance challenging properties such as flexibility and adhesion to various substrates on one side, mechanical and chemical resistance on the other side. These properties can be optimized for outdoor application where light fastness and weatherability become the essential elements for durable protection. Increasing attention is given to the disposal of the coated article where recyclability, compostability and ultimate biodegradability can reduce environmental impact.
Strong Value Propositions
Wood substrate is a natural, porous material consisting mainly of cellulosic fibers and lignin that requires per se sustainable coatings. It is not dimensionally stable and is very vulnerable to surface deterioration through fungal, microbial, moisture and light degradation – as well as to tannin staining. As such, the wood substrate continues to present a durability challenge requiring efficient coatings in terms of aesthetic and protective performance. A comprehensive range of products for primer, top-coat or self-sealing applications has been developed for wood construction, flooring, furniture, joinery or trims. In any case, an appropriate selection of products can be made within value-in-use and performance products (Figure 2).
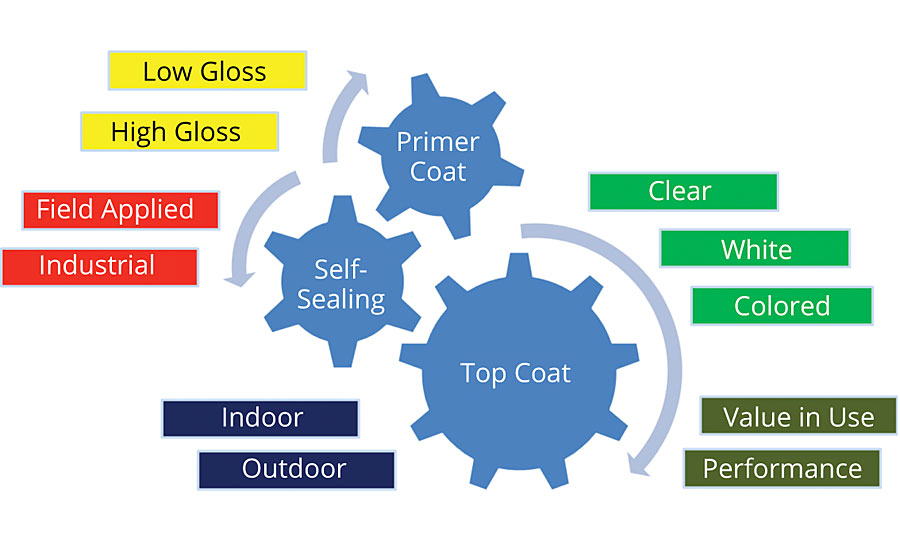
In the value-in-use product basket, the accent is given to product robustness during formulation and application together with an attractive price versus performance ratio. These products have good wood adhesion and Anfeuerung (for primers and stains), and offer a good overall resistance (for self-sealers or top coats). They constitute the foundation for effective wood protection for clear or white coatings.
In the performance product basket, the accent is made on a specific best-in-class feature that drives market innovation. These products are used for clear, white or any other colored coating applications and provide in each case a high protection with superior chemical and mechanical resistance. Other specific products cover low- to high-gloss demands (mirror effect), outdoor applications (good weatherability) as well as field-applied coating opportunities.
Our most recent development steps cover innovative products leading to a new value proposition in our product range. All these products (Table 1) have a good colloidal stability and present a low viscosity suitable for easy spray application. They benefit from a very low volatile organic content and a low MFFT requiring no additional co-solvents. The detailed formulations and application conditions used for testing the products in the following chapters are available upon request to the authors.
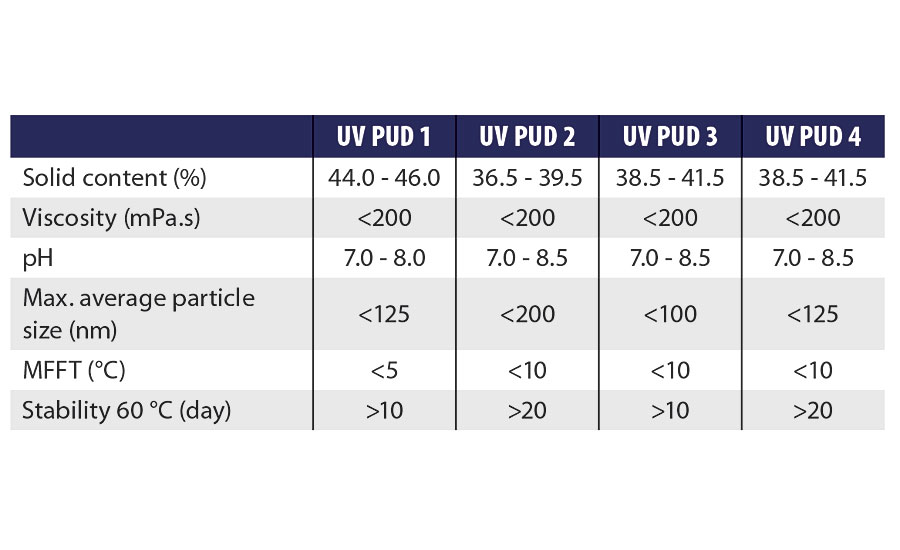
New Dispersion Morphology
Complex polymer dispersion morphologies1 are able to balance the coating properties for achieving optimized coating performance. Core and shell particles present some attractiveness for multiple-phase coatings with peculiar attributes, but they may be difficult to control so that their benefits over similar polymer blends are not always straightforward. We have shown that suitable polymer particles can serve as a reservoir for other constituents, like highly functional oligomeric polyacrylated molecules, to create a swollen particle with a very high acrylate content.
The tin-free UV PUD 1 (UCECOAT® 7230) is a new proprietary UV PUD strongly enhancing the coating performance of blends made therefrom. This product has a high solid content associated with good colloidal stability and is easy to formulate with other waterborne resins for boosting curing reactivity and performance towards desired mechanical and chemical resistance without compromising on flexibility. It is not recommended to be used alone for thick coating layers due to an extreme brittleness.
Figure 3 presents the comparative performance of UV PUD 1 alone and as a blend (6:4) with the alkyd emulsion ALKYD 1 (RESYDROL AZ 6191w/42WA). It is worth mentioning that the alkyd does not bear any acrylic functionality but that the blend can be cured efficiently under UV light to provide a decent and balanced performance level. As another advantageous consequence, the final product presents a renewable content of ~20% due to the natural oils present in the alkyd composition.
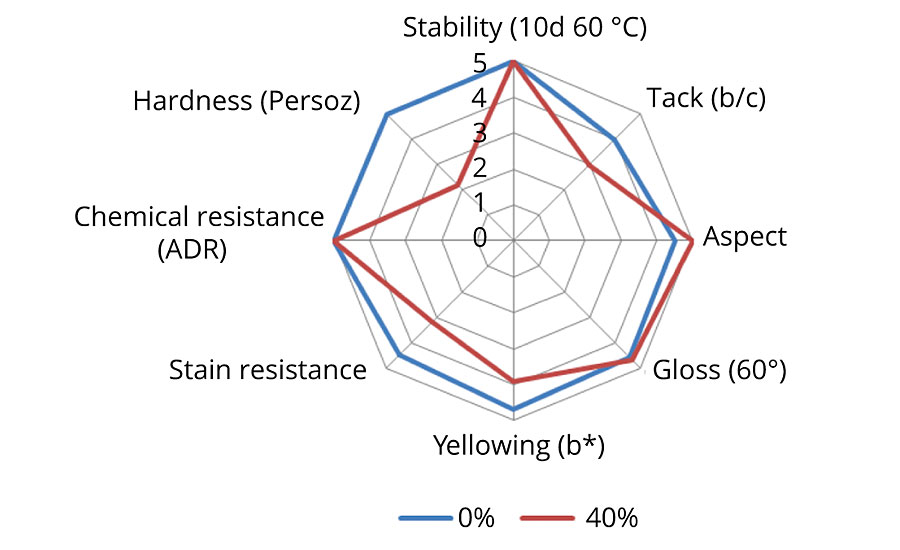
New Dispersion Stabilization
The stabilization of radiation-curable oligomers in aqueous systems is primarily dependent on their molecular weight, whether they are present as liquid-in-liquid (emulsion) or as solid-in-liquid (dispersion). Most of these heterogeneous systems are stabilized either by electrostatic or steric repulsion at the interphase of the droplets or particles, preventing their coalescence or flocculation. The electrostatic nature of the stabilization can be either anionic or cationic, while the steric nature of the stabilization is usually the result of nonionic poly-alkoxylated hydrophilic species. The chemical functionality necessary to ensure the stabilization can either be covalently incorporated into the polymer of the dispersed phase (internal stabilization) or be provided by an additional tensio-active component adsorbed at the interphases (external stabilization) – although these two cases can coexist.
The label-free and tin-free UV PUD 2 (UCECOAT 7738) is a new proprietary UV PUD binder for clear and white coatings with an optimum hardness balance. This product contains a mixed anionic and nonionic stabilization, and presents therefore an optimized colloidal stability with associated formulation robustness and pH stability. It shows effective drying with good water release during the coating process, and has a perfect balance between surface hardness and flexibility after cure, together with an excellent coin resistance. In particular for white pigmented formulations, we observed a high-gloss mirror effect, which is peculiar for a product that is physically drying before cure.
Figure 4 presents the comparative performance of UV PUD 2 with the label-free, fit-for-use benchmark UV PUD 5 (UCECOAT 7788). The new product outperforms for chemical and mechanical resistance, and demonstrates therefrom its strong value proposition.
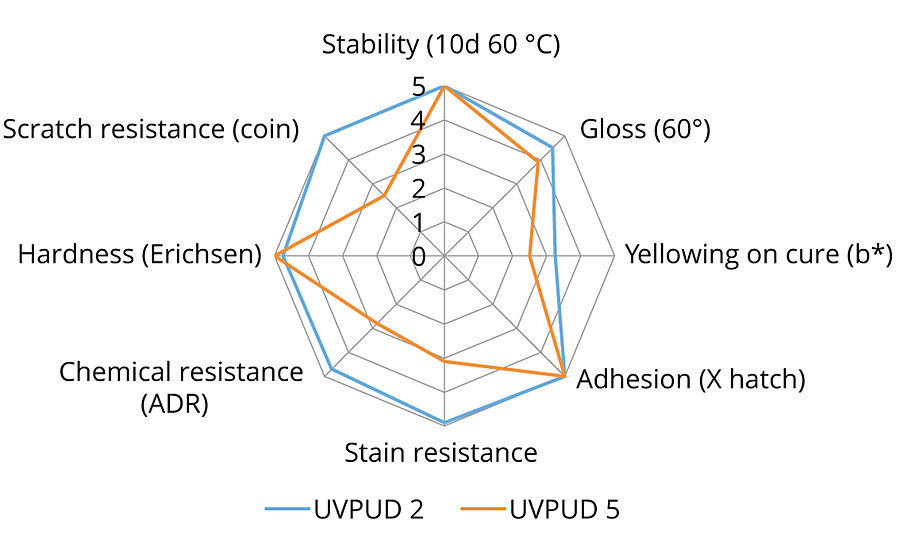
New Dispersion Functionalization
It is known that yellowing on cure may occur during the exposure of energy-curable compositions to energetic ultra-violet light or electron beam. Yellowing is typically decreasing after a few hours to the initial level. It is thus different from the long-term yellowing associated to polymer degradation during weathering. It can cause difficulties for online color matching in specific industrial lines. Root causes for yellowing on cure are not always clearly identified, but a reduction of photo-yellowing can be observed by the reaction of an aliphatic carboxylic hydrazide with aliphatic isocyanates present on the polyurethane backbone.
The tin-free UV PUD 3 (UCECOAT 7510) is a new proprietary UV PUD binder that has a good water release and effective drying during the coating process. It is optimized for low yellowing upon UV cure and is thus recommended for applications where color matching is essential (for instance on clear substrates). It shows good hardness with excellent mechanical, chemical and cold check resistance.
Figure 5 presents the comparative performance of UV PUD 3 with the benchmark UV PUD 5. The new product outperforms for yellowing on cure while bringing at the same time a higher hardness. It is also easier to matte.
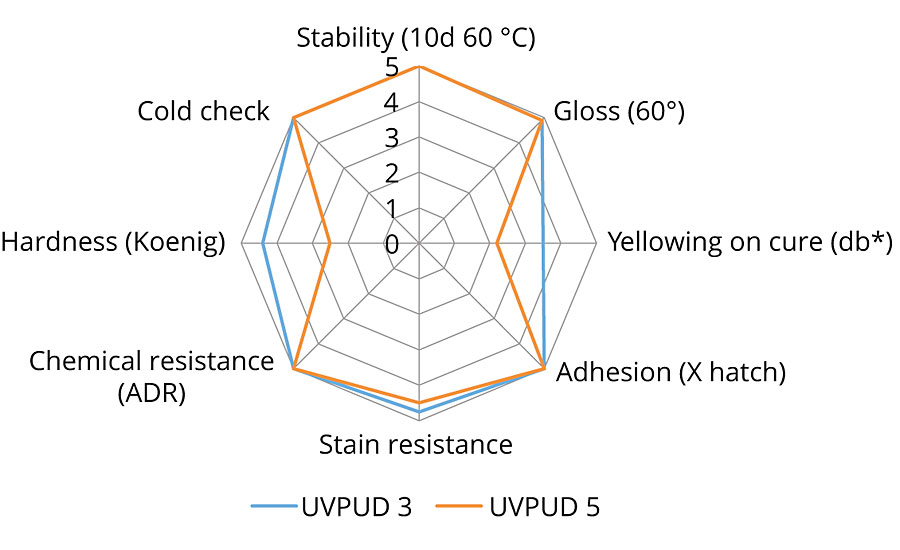
New Dispersion Composition
Typical ionomeric polyurethane structures encompass a very large range of polymer composition, molecular weight and architecture. They are composed from polyisocyanates and several other functional polyols, bringing for instance the acrylic functionality to the polymer. Dimethylol propionic acid (DMPA) is very often used as a monomer to provide the carboxylic acid functionality, resulting in an anionically stabilized polymer colloid in water. We developed a novel composition that advantageously uses polymeric carboxylated polyols instead of DMPA.
The tin-free UV PUD 4 (UCECOAT 2501) is a new proprietary UV PUD binder with optimized cost effectiveness and formulation robustness. This product offers optimized compatibility, in particular with conventional acrylic latexes, for tweaking performance and cost to the desired level. The coating dries with a good water release and becomes tack-free before UV cure. We can notice a good Anfeuerung and adhesion on wood in association with good stain resistance and reduced yellowing on aging – in clear or white coat applications. Last but not least, it offers a large magnitude of formulation with higher performance UV PUDs still at a competitive cost.
Figure 6 presents the comparative performance of UV PUD 4 alone and formulated as a blend (7:3) with much harder UV PUD 6 (UCECOAT 7655) and UV PUD 7 (UCECOAT 7734). It becomes very clear that, although the reference product alone presents an attractive overall performance, it is still possible to tailor coating hardness towards more demanding applications with good adhesion and at a reasonable cost increase.
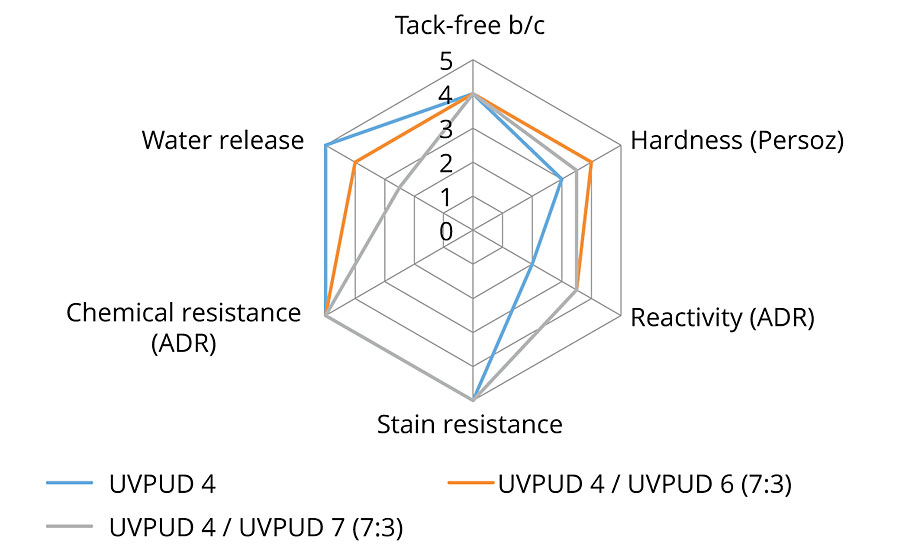
Conclusions and Perspectives
Through continuous innovation, allnex is building on its green core technologies to prepare the sustainable world for tomorrow. By merging the best attributes of waterborne polymers and radiation curing technology, it offers a unique and comprehensive range of WB UV products for wood, covering wide market needs and focusing on customer satisfaction. The wood coating portfolio is now extended with four novel fit-for-use products supported by clear innovative technological differentiation. The four products extend performance capabilities in the areas of mechanical and chemical resistance, stability and compatibility – as well as yellowing after cure.
Reference
1 Tielemans, M.; Roose, P.; Ngo, C.; Lazzaroni, R.; Leclère, P. Multiphase Coatings from Complex Radiation-Curable Polyurethane Dispersions, Progress in Organic Coatings 75 (2012) 560-568.
Looking for a reprint of this article?
From high-res PDFs to custom plaques, order your copy today!