New Engineered Polysaccharides as Sustainable Performance Additives in 1K Water-Based Polyurethane Dispersions

Polyurethanes today represent one of the most diverse class of polymers, finding uses in a broad range of applications across multiple industries. Numerous raw materials are being utilized today in this diverse material category to enhance and modify product performance. Innovation continues to not only target further product performance improvements but also increasingly focuses on the overall material sustainability with regard to environmental aspects driven by a circular economy framework.
In the protective coatings market, the major initiative has focused on improving the emissions by replacing organic solvents as the carrier material with water. As a result, solvent-free, water-based polyurethane dispersions (PUDs) have been developed for a broad range of applications including wood coatings, leather and textile coatings, and metal coatings. To meet the sustainability objectives, PUDs have also been synthesized from renewable-based PO3G polyether polyols. In addition, PUDs with high renewable content have been produced from polyester polyols based on succinic, azelaic, sebacic and octadecanedioic acids.
More recently, enzymatic polymerization has been under development to convert sucrose to engineered alpha-1,3-polyglucose (glucan) materials with properties tailored for use in water-based PUD coatings. Alpha-1,3-polyglucose can be produced from sucrose using a biocatalyst from the general class of glucosyltransferases (GTF), for example isolated from Streptococcus salivarius. These alpha-1,3-polyglucose systems are found in nature (for example from mushrooms) but are isolated here directly from a scalable bioprocess.
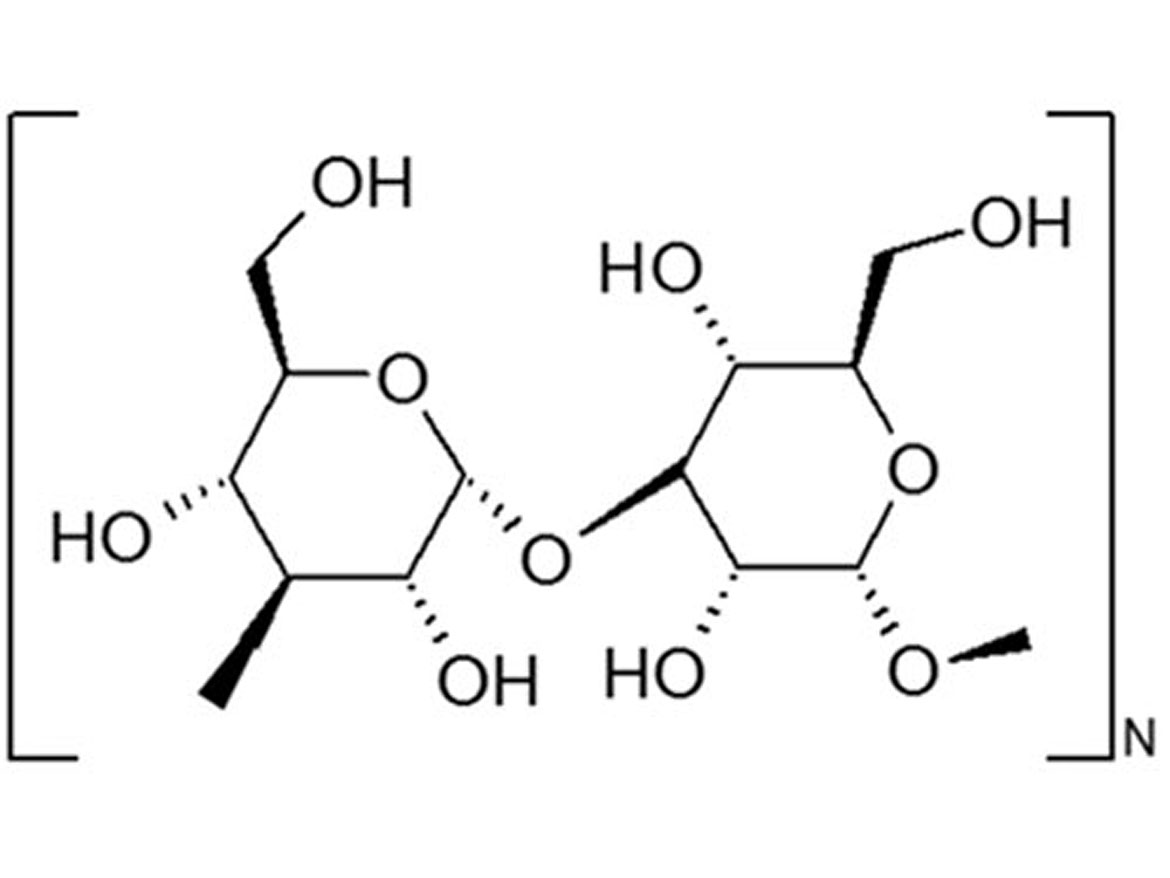
This enzymatic polymerization process yields a polymer with high selectivity containing >99% alpha-1,3 linkages and with high compositional consistency (Figure 1). Using this technology, the alpha-1,3-polyglucose (glucan) structure can be controlled, with different levels of crystallinity (Figure 2), resulting in controlled spherical aggregates similar to fumed silica or submicron platelet-like particles (microcrystalline glucan, MCG).
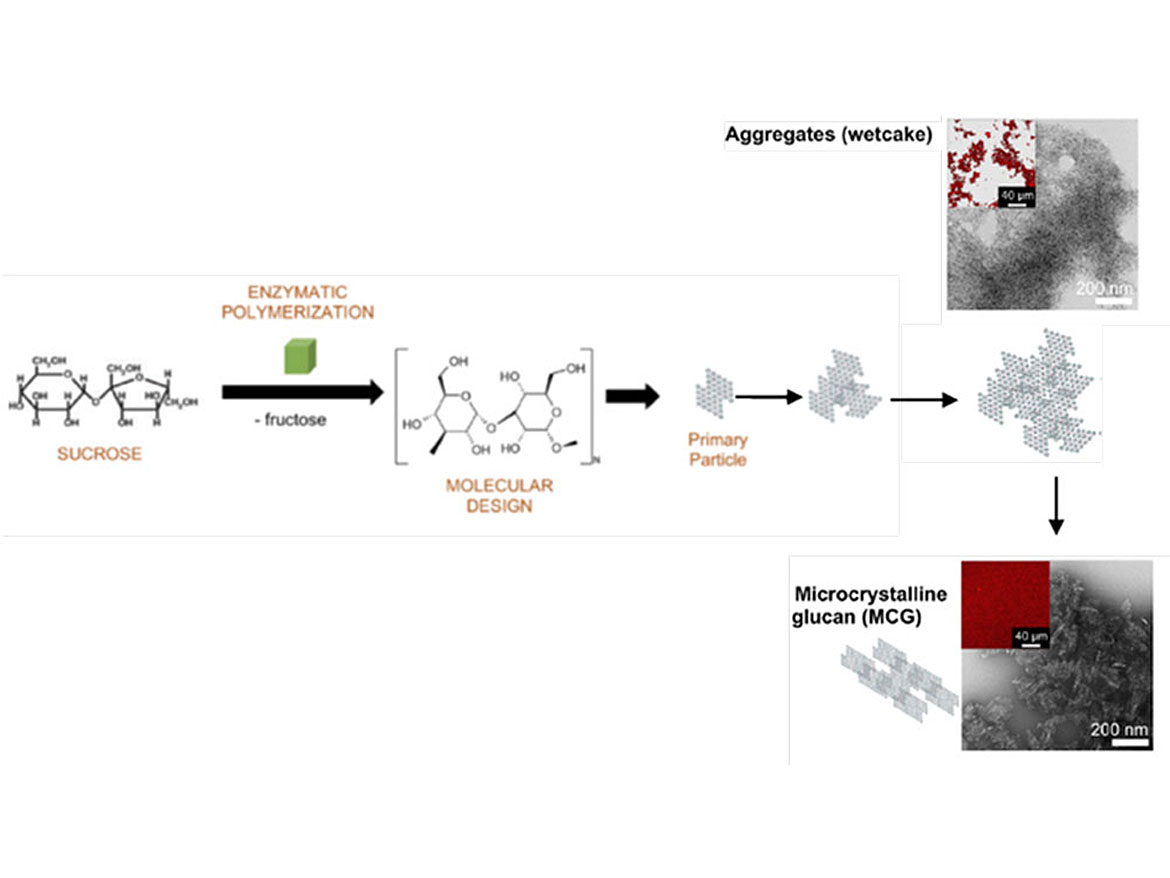
The resulting polysaccharides have repeat units that contain primary and secondary hydroxyl groups, which have been shown to be reactive with isocyanates, making them a potentially viable reactive additive in syntheses of polyurethanes, including water-based PUDs. In a model thermoplastic urethane system it has been shown that glucan impacts the polyurethane matrix morphology by forming a new covalent and hydrogen-bonded hard segment that strongly improves the solvent resistance of TPUs. Similarly, isocyanate-reactive glucan was shown to enhance the load-bearing properties of visco-elastic polyurethane foams.
Unlike water-soluble starch and water-insoluble cellulose, the glucan is also water-insoluble powder with sufficient affinity to water to produce stable water dispersions. As a result, the glucan morphologies are readily suited for incorporation into water-based PUDs. In water-based PUDs, the glucan can be utilized as an isocyanate reactive component in the synthesis of the polyurethane matrix. However, due to its water dispersability, glucan can also be added to a finished water-based PUD system, where these glucans are expected to impact the properties of the resulting films and coatings. Therefore, the aim of this study it to quantify the impact of enzymatically produced alpha-1,3 polyglucose of different morphologies on the performance of water-based PUDs, and to establish the impact of the glucan morphology and performance of the resulting polyurethane matrix.
Experimental
Materials
The discussed morphologies of glucan used in this study are prepared and supplied by IFF.
The glucan wet cake is the basic form of the alpha-1,3-polyglucose materials derived from the enzymatic polymerization of sugars, and typically contains about 35 wt.% solids, with the balance comprised of water. Prior to use for this study, glucan wet cake powder was dispersed in water, creating a 10 wt.% polysaccharide dispersion.
MCG is a highly crystalline form of alpha-1,3-polyglucose and was received as 8% dispersion in water.
1K water-based dispersions were supplied by Troy Polymers. The dispersions are based on high-renewable-content, sebacate-based polyester polyols.
Glucan/PUD Blends Preparation
Glucan was added to 1K-PUD at varying ratios. The mixture was first blended in a closed cup via multi-axial speed mixer for 1 minute, followed by wet milling for 1 minute via IKA mill.
The glucan/PUD mixtures were used to produce stand-alone films and coatings on aluminum. Using a Dr. Blade at 30 mils thickness, stand-alone films were prepared by coating the dispersion blend mixtures onto a polypropylene substrate. Similarly, glucan/PUD mixtures were coated onto aluminum substrates.
The films and coatings were allowed to dry for 24 hours at room temperature, followed by 24 hours at 50 °C. The films and coatings were conditioned for at least two additional days prior to testing.
Glucan/PUD Blends Testing
Glucan/PUD Films Testing
Tensile strength and elongation at break were determined using Instron equipped with heating chamber (5500R, Model 1122) following ASTM D2370. Stress-strain properties of PUD-based films were also measured upon hydrolytic aging in a moisture chamber at 95% relative humidity, 50 °C for 3 days.
Thermal properties of films were measured using differential scanning calorimetry (DSC) (Q10, TA Instruments). DSC analysis of TPU was carried out over the temperature range of -100 to 200 °C at the heating rate of 10 °C/min. In the first run, the TPU sample was heated from room temperature to 150 °C. The sample was then cooled down to -100 °C and heated to 200 °C (second run). The results from the second DSC run were reported.
FTIR spectra of TPUs were recorded on a Perkin Elmer Spectrum 100 equipped with Universal ATR Attachment, recording the spectra over a wavenumber range of 650 to 4,000 cm-1. The average value of 16 scans with 4 cm-1 resolution was collected for each sample.
Glucan/PUD Coatings on Aluminum Testing
Gloss was determined at 60° angle using a gloss meter (ETB-0686 from M&A Instruments). Hardness was determined via pencil hardness method per ASTM D3363. Impact resistance was measured according to ASTM D2794. Adhesion was assessed via tape test per ASTM D3359. The hardness and adhesion of coatings cast on metal substrate was measured after hydrolytic aging in a moisture chamber for 3 days, 38 °C and 95% relative humidity ASTM D 2247.
Results
PUD with MCG Dispersion and Derived Films
MCG is the highly crystalline form of the polysaccharide materials and was received as 8% dispersion in water. MCG was added directly to PUDs, forming stable dispersions. Subsequently, PUD/MCG blends were cast on aluminum plates or cast onto polypropylene to form stand-alone films.
Interestingly, fully transparent and flexible films were obtained with up to 50% MCG content on dry film bases (Figures 3 and 6). Tensile properties of these films plotted as the concentration of MCG on dry film bases are shown in Figures 4 and 5. As expected, tensile modulus of the films increased with the addition of MCG. However, interestingly, tensile elasticity of the films essentially remained unaffected with the addition of up to 10% of MCG on dry film bases. Even with the addition of up to 40% MCG the films were quite elastic, with about 290% elongation at break.
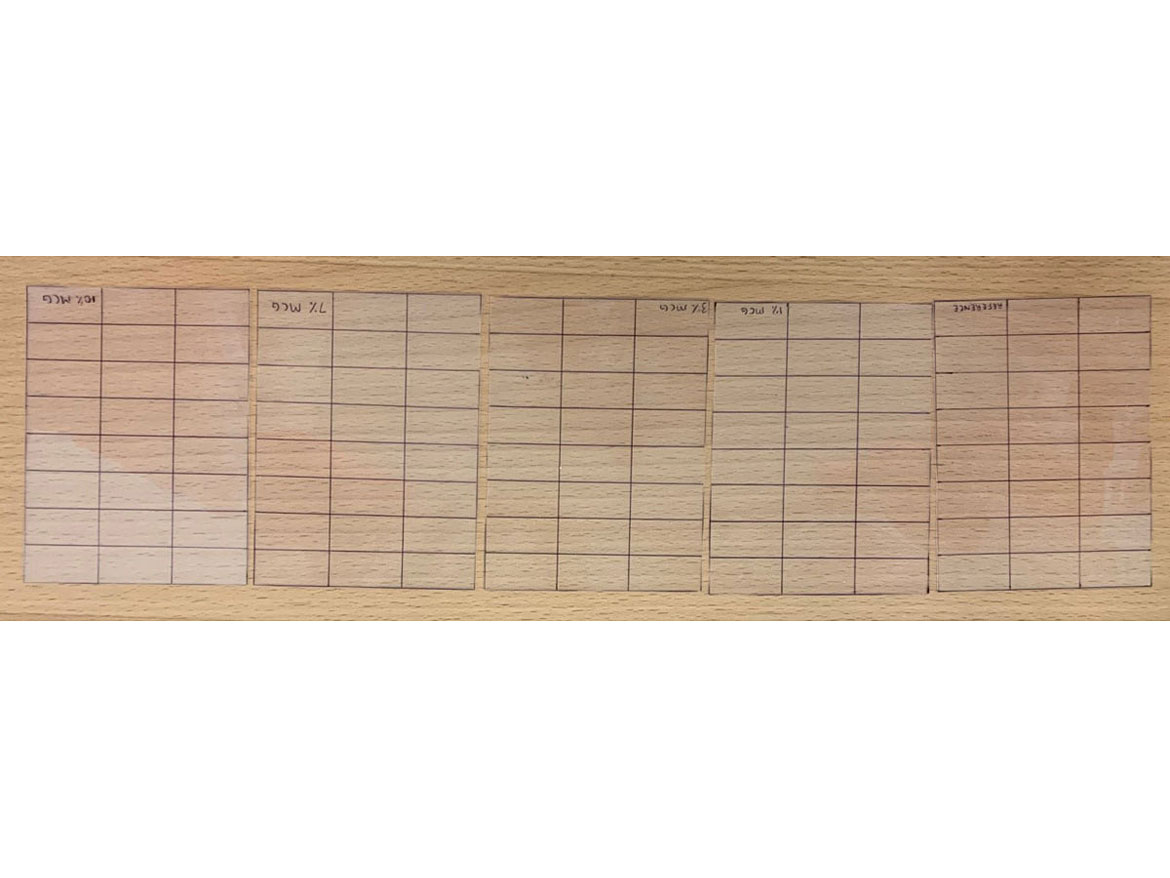
After hydrolytic age, modulus and elasticity of the referent film and films containing MCG decreased somewhat. However, elasticity of films improved, especially with the films containing higher levels of MCG. As a result, films containing 50% MCG became highly flexible, with elongation at break of about 290% (Figures 5 and 6).
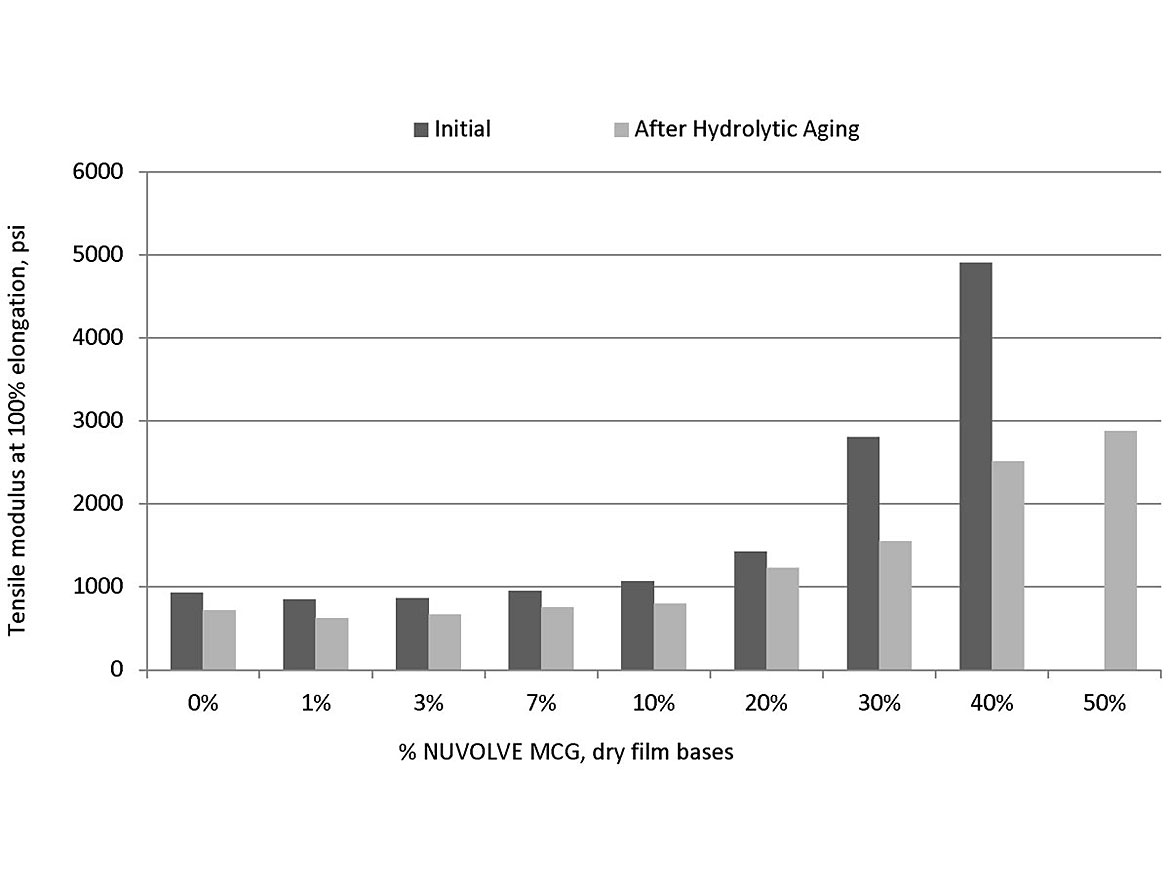
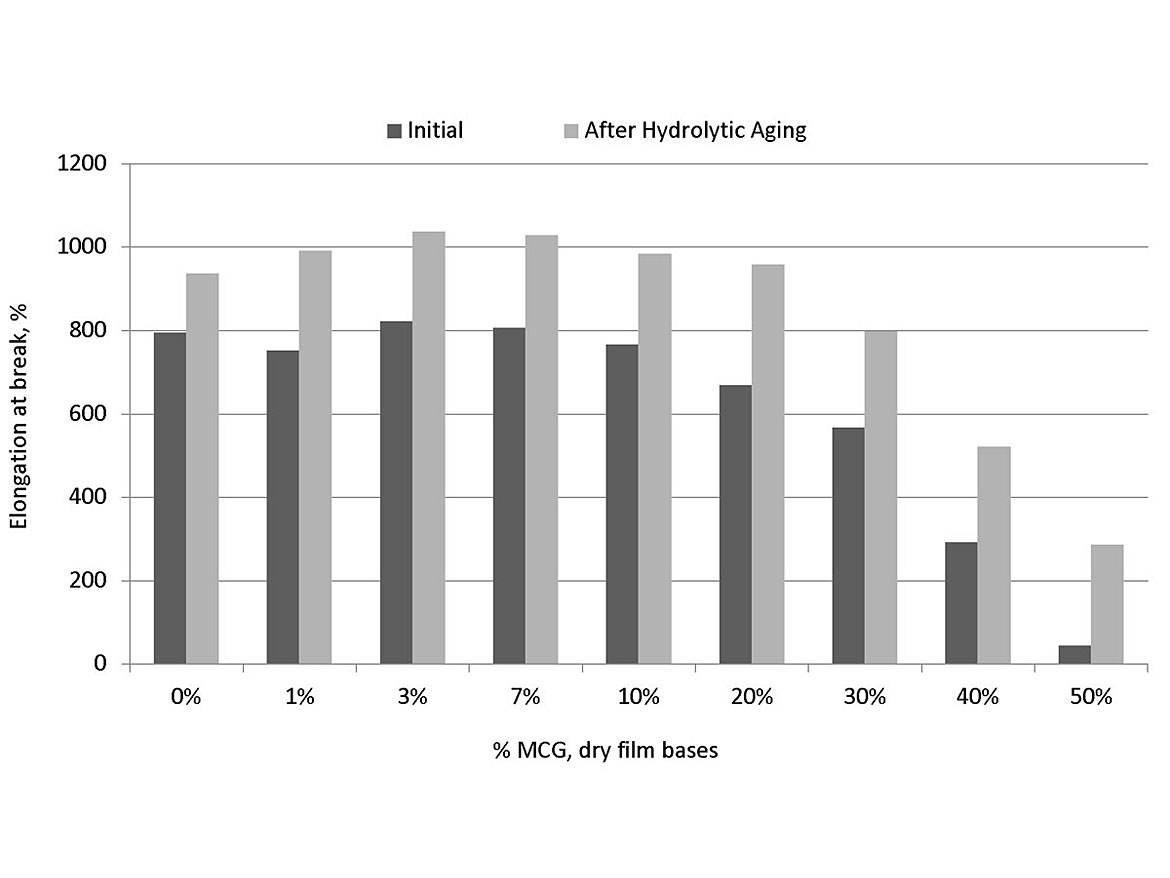
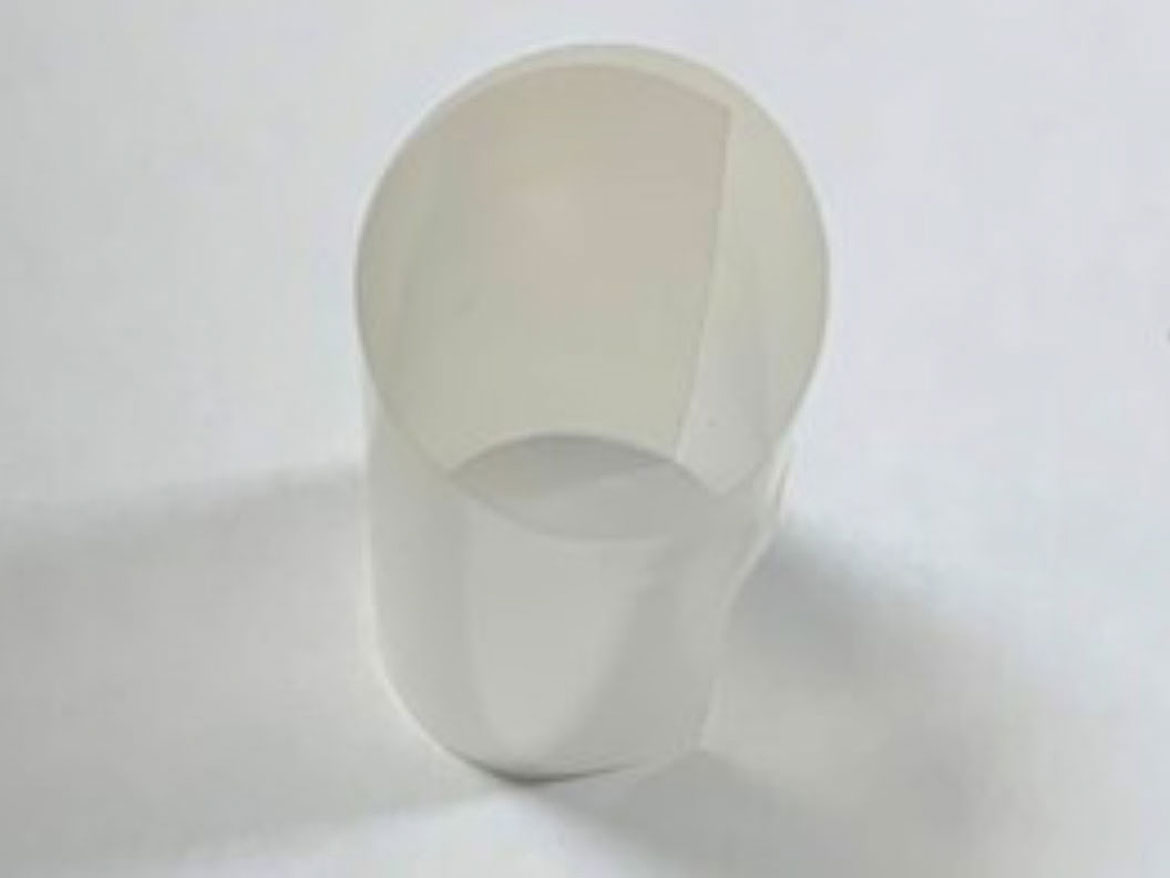
PUD with Wet Cake Dispersions and Derived Films
The alpha-1,3-polyglucose wet cake is the high surface area spherical morphology produced via the enzymatic polymerization of sugars. 10% glucan wet cake dispersion was added directly to PUDs, forming stable dispersions with a slow rate of settling (essentially stable). Subsequently, PUD films containing various levels of glucan wet cake were coated onto aluminum plates or cast onto polypropylene to form stand-alone films.
The addition of 10% glucan wet cake to PUDs resulted in an increase in viscosity (Figure 7). Due to this, the largest content evaluated was 15% glucan wet cake on dry film comparison base.
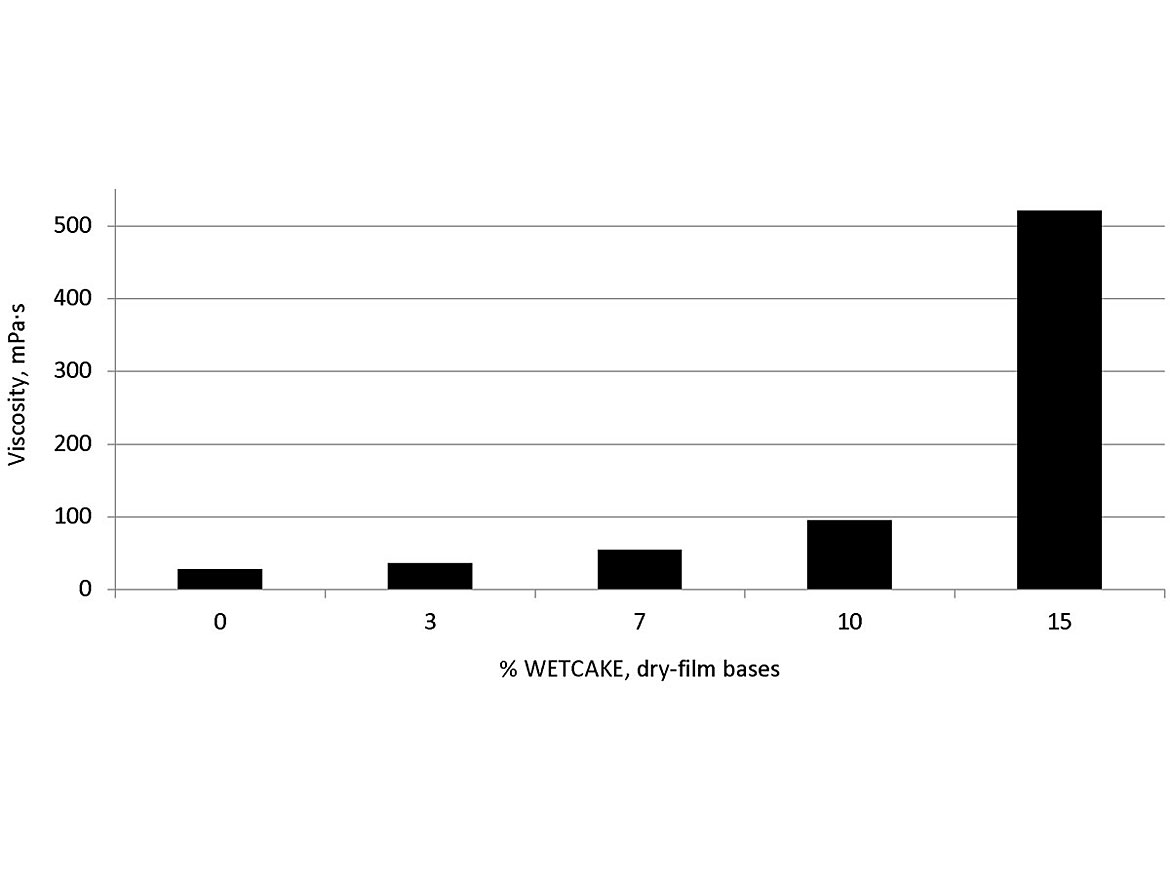
As expected, the tensile modulus of the films increased with the addition of glucan wet cake. However, interestingly, tensile elasticity of the films was minimally affected with the addition of glucan wet cake, with films containing 15% of glucan wet cake having 600% elongation at break.
After hydrolytic age, modulus and elasticity of the referent film decreased somewhat. However, in general, both modulus and elasticity of films improved with increased content of glucan wet cake. Detailed analyses of tensile properties after hydrolytically aging of films shows that with increased content of glucan wet cake, tensile strength, modulus and elasticity increase, resulting in significant increase in film toughness (measured by area under stress-stain curves) (Figures 8 and 9, and Table 1).
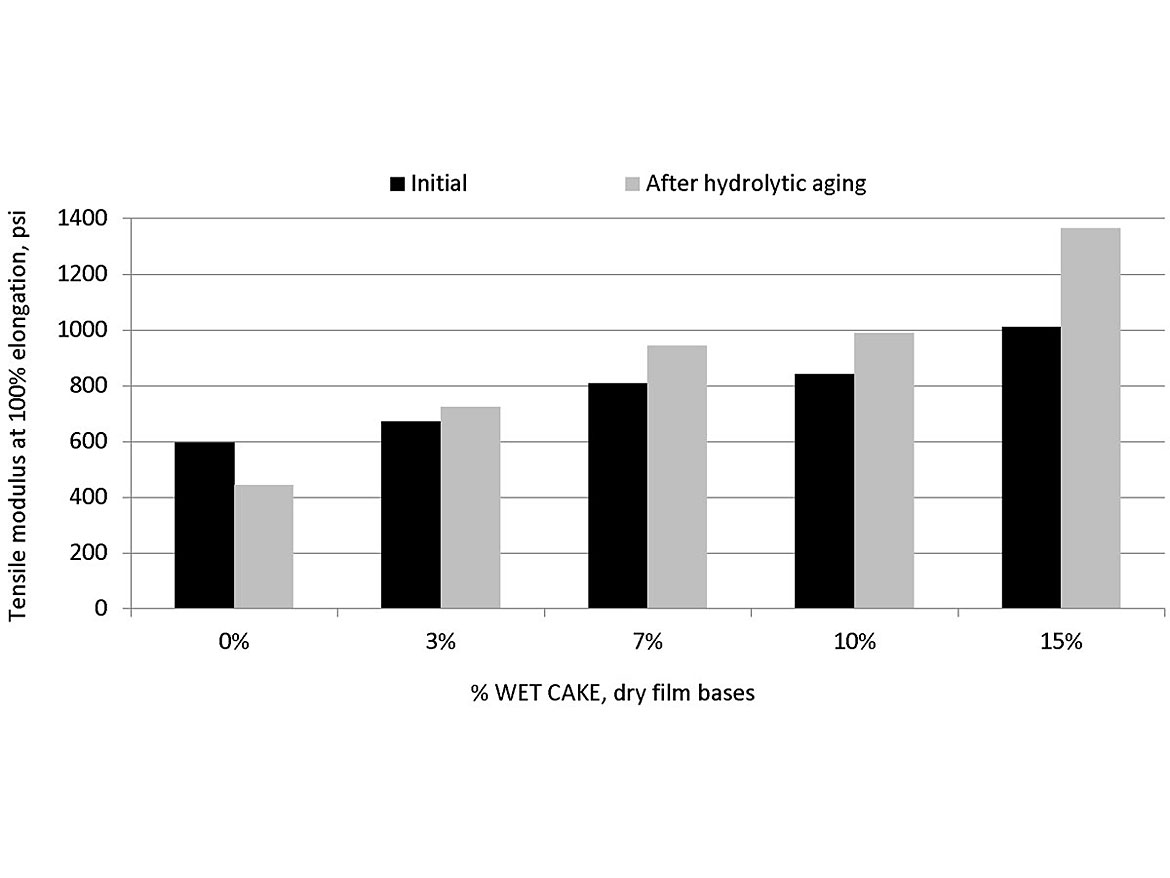
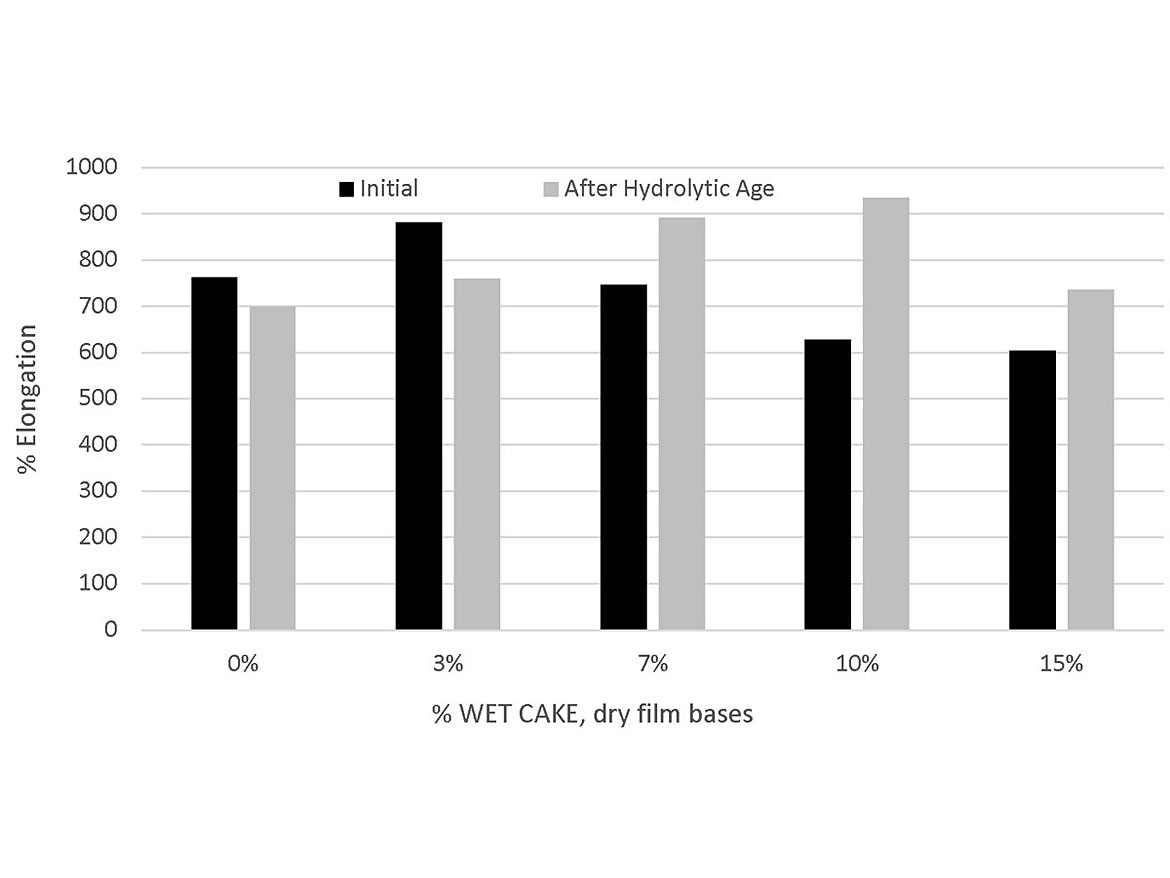
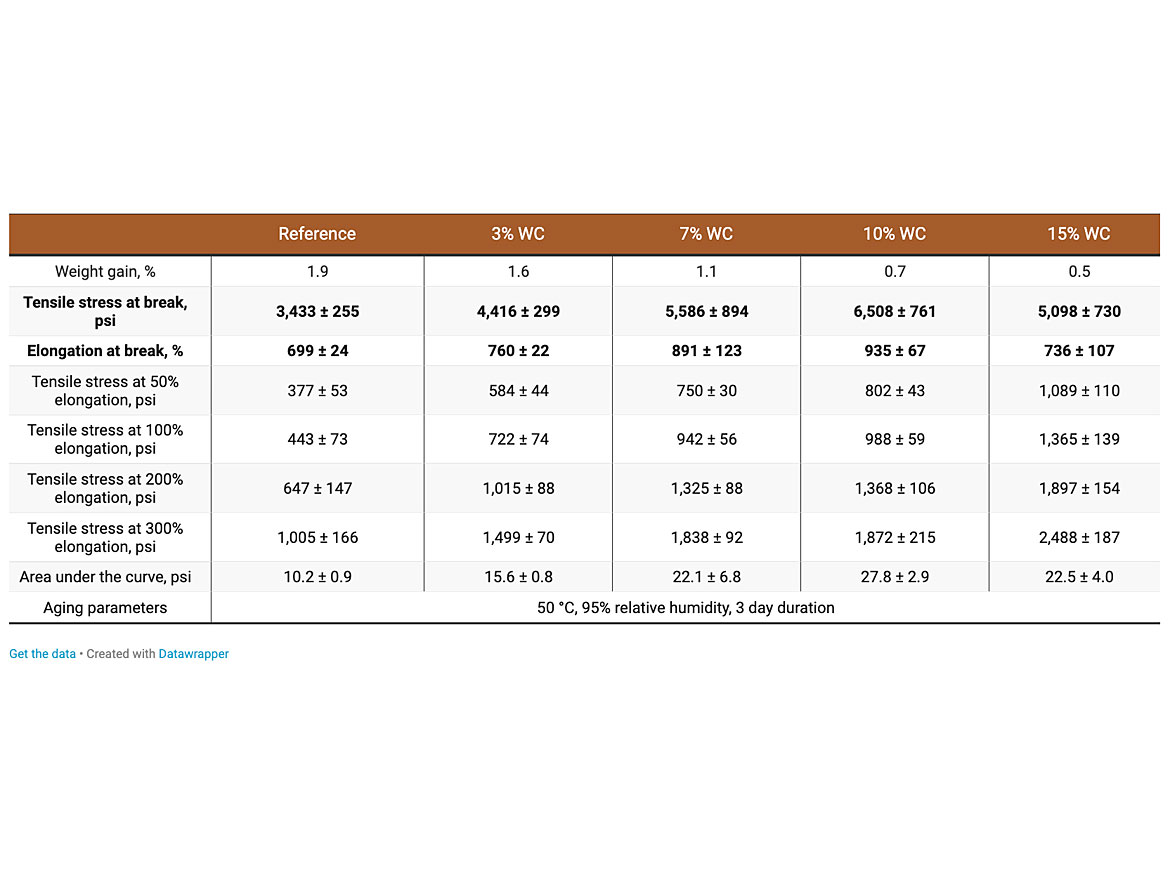
PUD with MCG Coatings
PUDs with various levels of MCG were coated onto aluminum and steel plates, and evaluated for key properties. The addition of MCG had no measurable impact on the impact resistance of the coatings. Also, the addition of MCG had no significant impact on the hardness of the coatings. Adhesion strength of PUDs on steel, as measured by tape test, was slightly improved with the addition of MCG. Adhesive strength to aluminum was slightly reduced with the addition of 20% MCG, however, cohesive mode of failure was maintained. Tables 2 and 3 show these results.
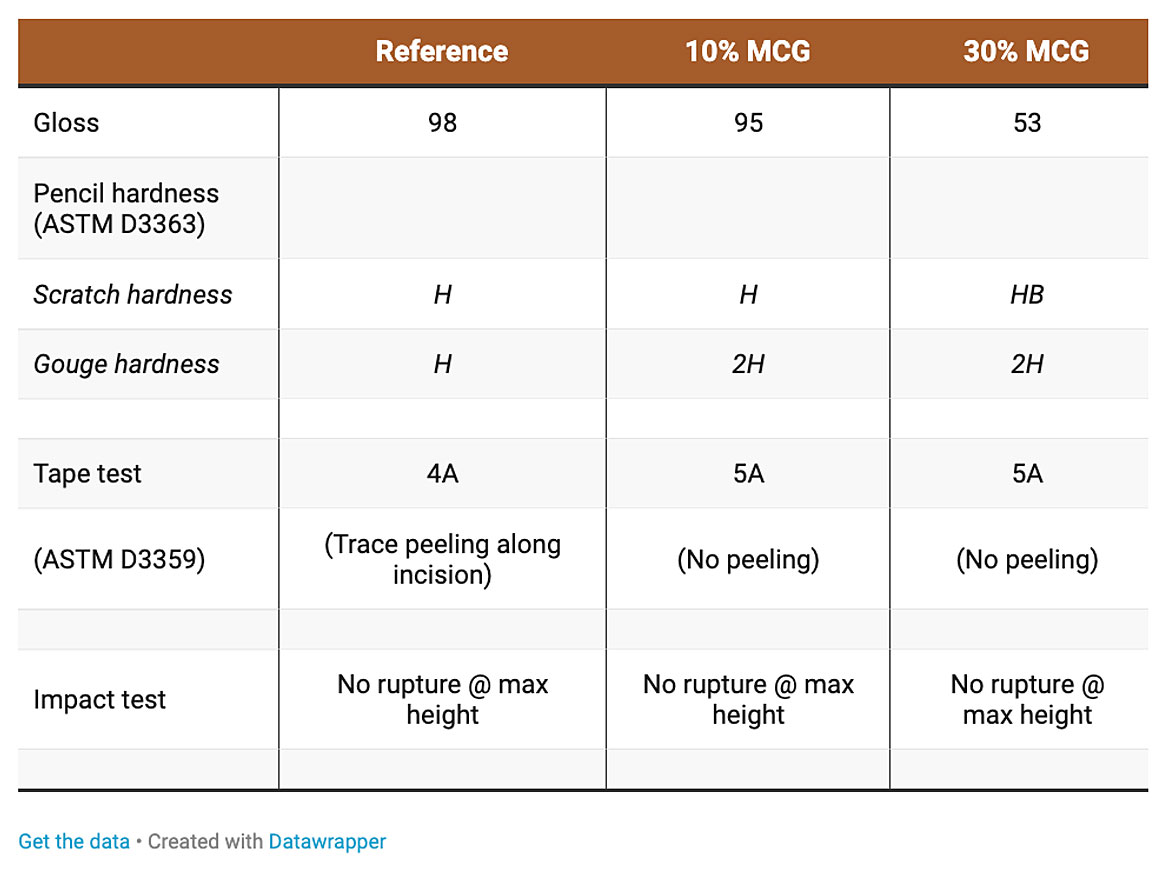
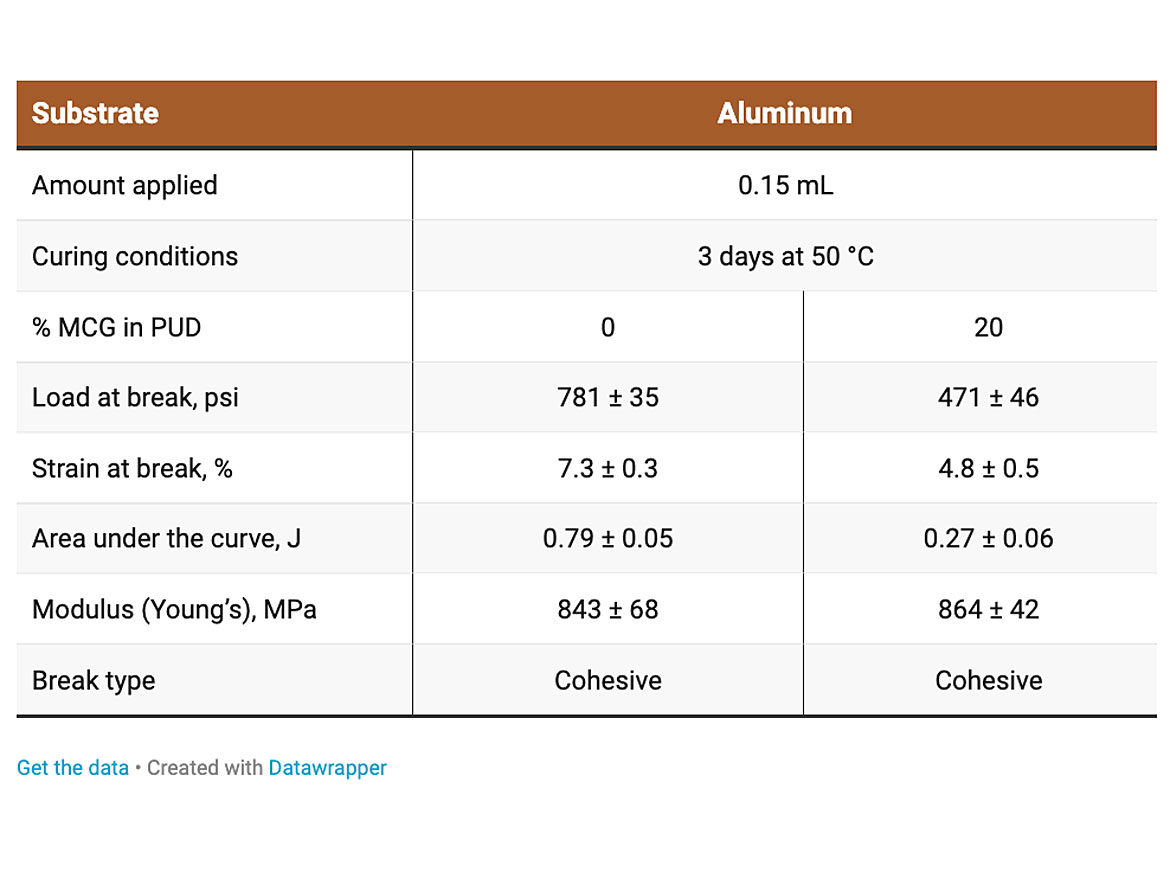
PUD with Wet Cake Coatings
PUDs with various levels of glucan wet cake were coated onto aluminum plates and evaluated for key properties. As shown in Table 4, the adhesive strength to aluminum as measured by load at failure was not affected. However, the mode of adhesive failure was improved. Whereas reference films experienced adhesive failure, films with glucan wet cake experienced cohesive failure.
The addition of glucan wet cake had no measurable impact on the impact resistance of the coatings. Also, the addition of glucan wet cake had no significant impact on the hardness of the coatings. Only at 15% glucan wet cake incorporation on dry film base was a slight reduction in hardness of coatings applied on aluminum observed. It should be noted that the hardness of coatings actually increased with the addition of glucan wet cake on the various substrates, such as for example wood.
Chemical resistance of the coatings was evaluated via rub-test with IPA and toluene. The addition of glucan wet cake was found to have essentially no negative impact on the chemical resistance to IPA and only slight decrease in resistance to toluene (Table 5).
Analysis of the coatings indicates that the addition of glucan wet cake decreases the gloss of the coatings (Figure 10). Therefore, it is possible that glucan wet cake can be utilized as a matting agent if that is desired in addition to the observed other property benefits. Having a matting agent that also enhances mechanical properties of films would be beneficial in a broad range of applications, including wood, textile and leather coatings.
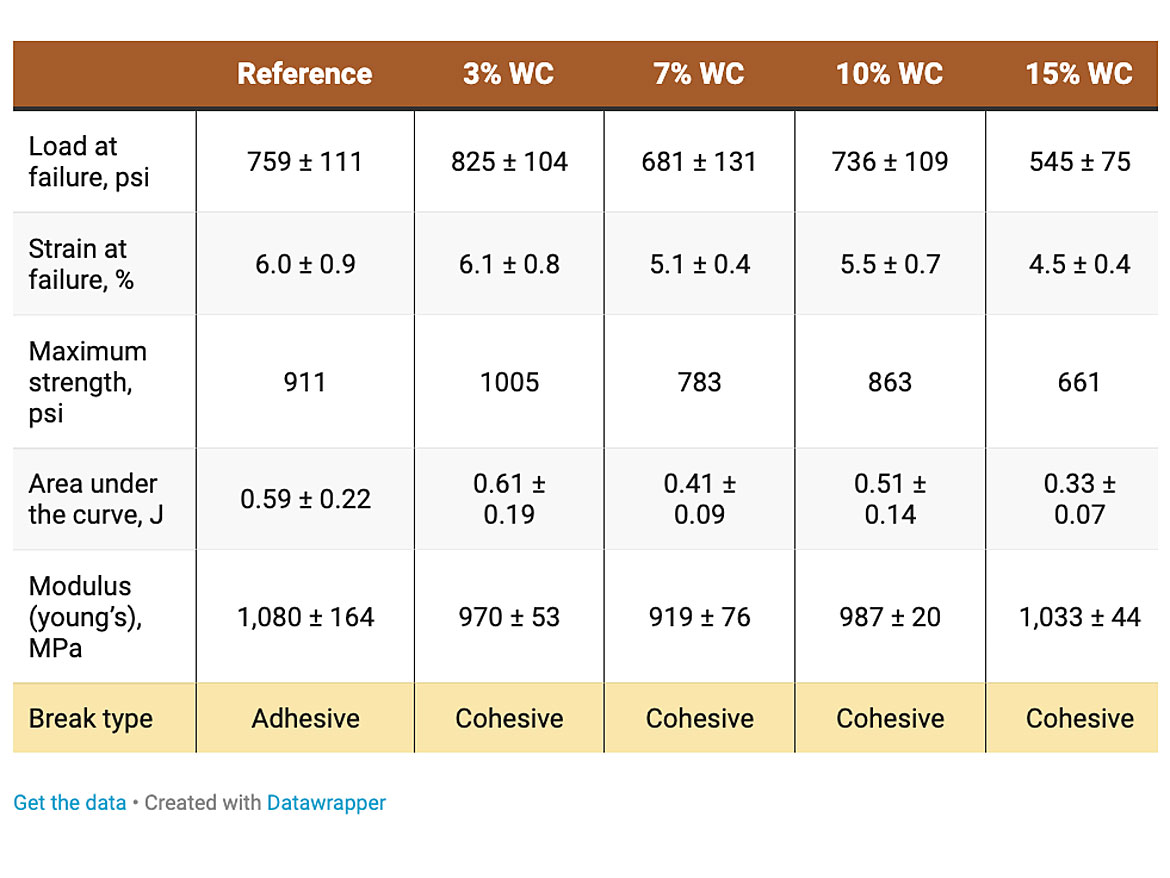
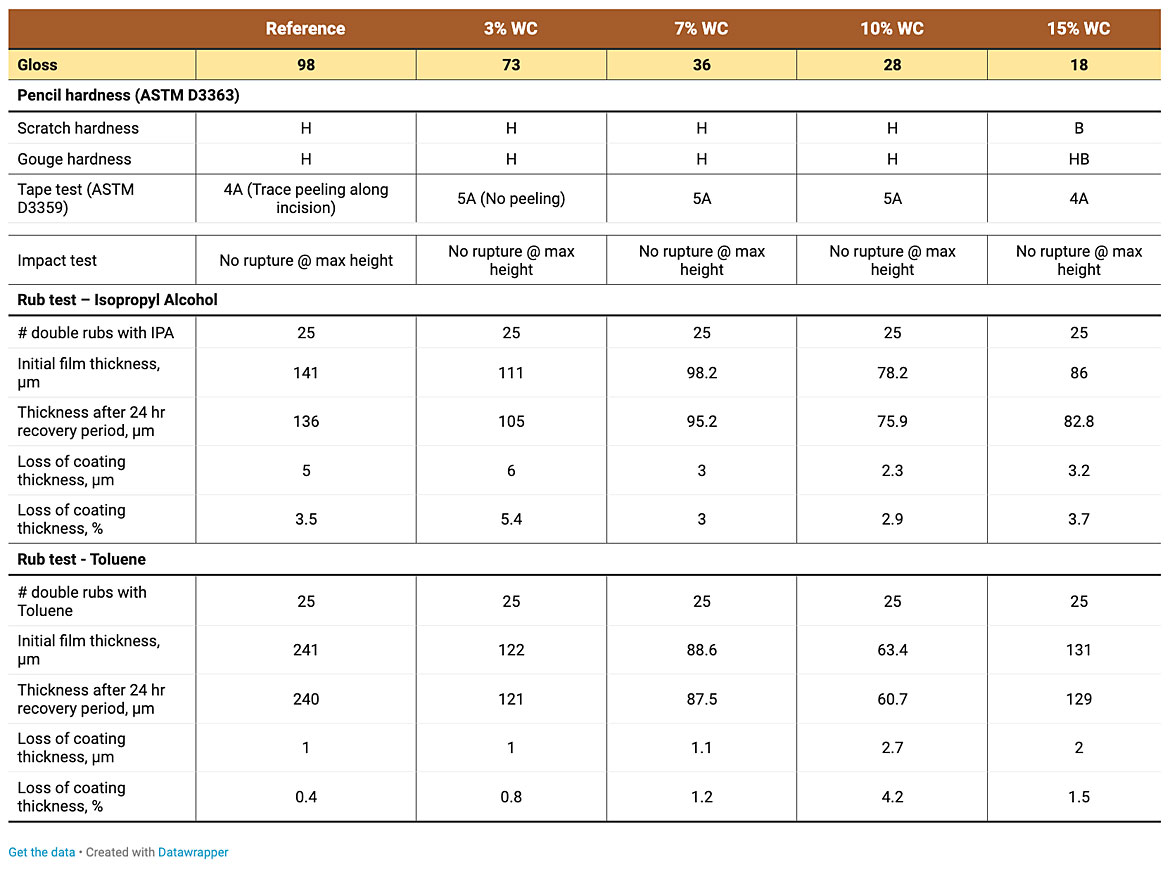
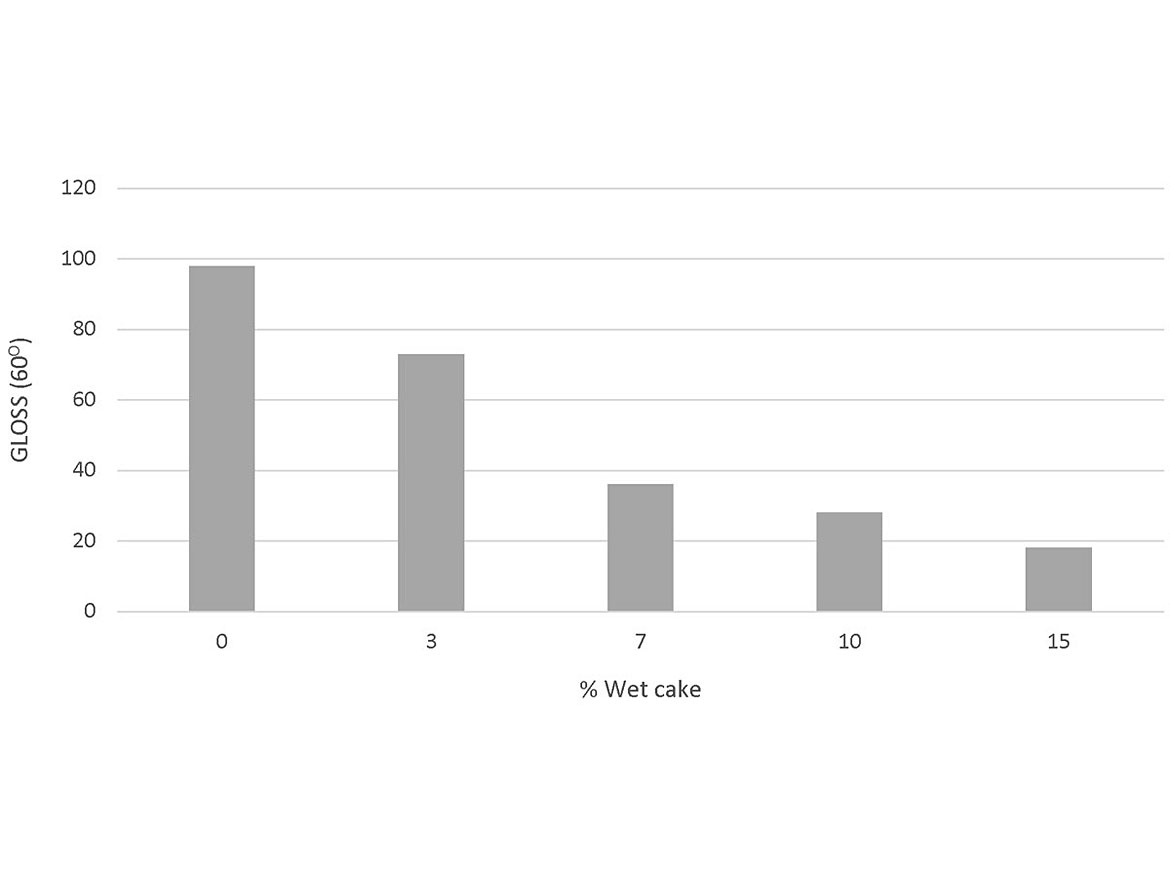
Wood Coating Evaluation
PUDs with various levels of glucan wet cake and MCG were coated onto oak and evaluated for key properties. The addition of glucan wet cake and MCG to the base PUD reduced the tackiness of the coating, providing a hand feel comparable to commercial wood coating. The addition of glucan wet cake reduced the gloss of coatings measured on wood, while the addition of MCG had no impact on gloss. Therefore, when matt finish is required, glucan wet cake can be used. When higher gloss finishes are required, MCG offers a better choice (Figure 11).
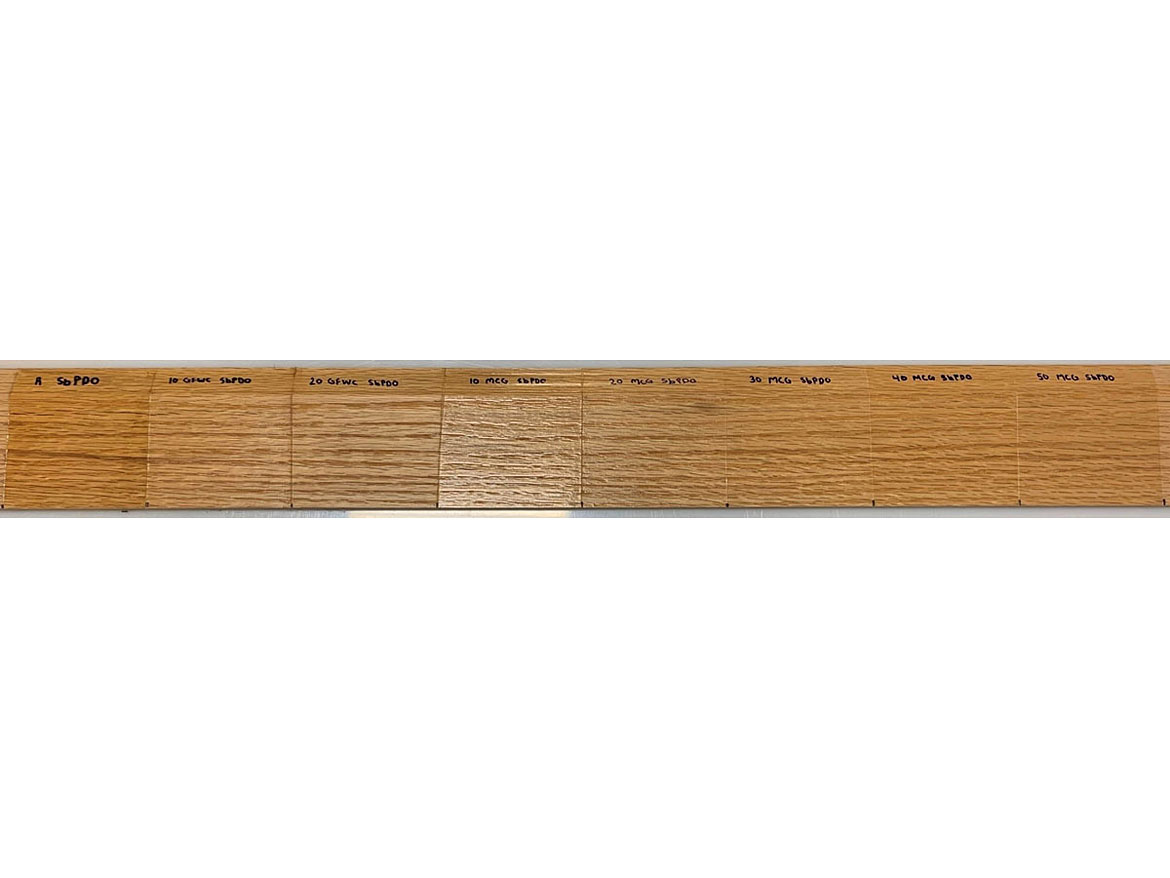
Scratch resistance of the PUD coatings on wood was not affected with the addition of glucan wet cake and MCG. Coatings with up to 60% MCG and 30% glucan wet cake maintained scratch hardness of 7H-8H, which is significantly higher than 1H scratch resistance hardness measured for commercial water-based PUD wood coating (Tables 6a and 6b).
Additionally, rub test indicates that the addition of glucan wet cake and MCG improved the resistance of PUDs to IPA and water. It was found that the addition of either form of glucan resulted in reduced weight loss resulting from rub test to IPA. Coatings with up to 60% MCG and 30% glucan wet cake maintained lower weight loss during the rub test with IPA than commercial water-based PUD protective wood coating. Water drop test also indicates that wood coatings containing glucan wet cake and MCG offer potentially better protection than the reference commercial wood coating (Tables 6a and 6b).
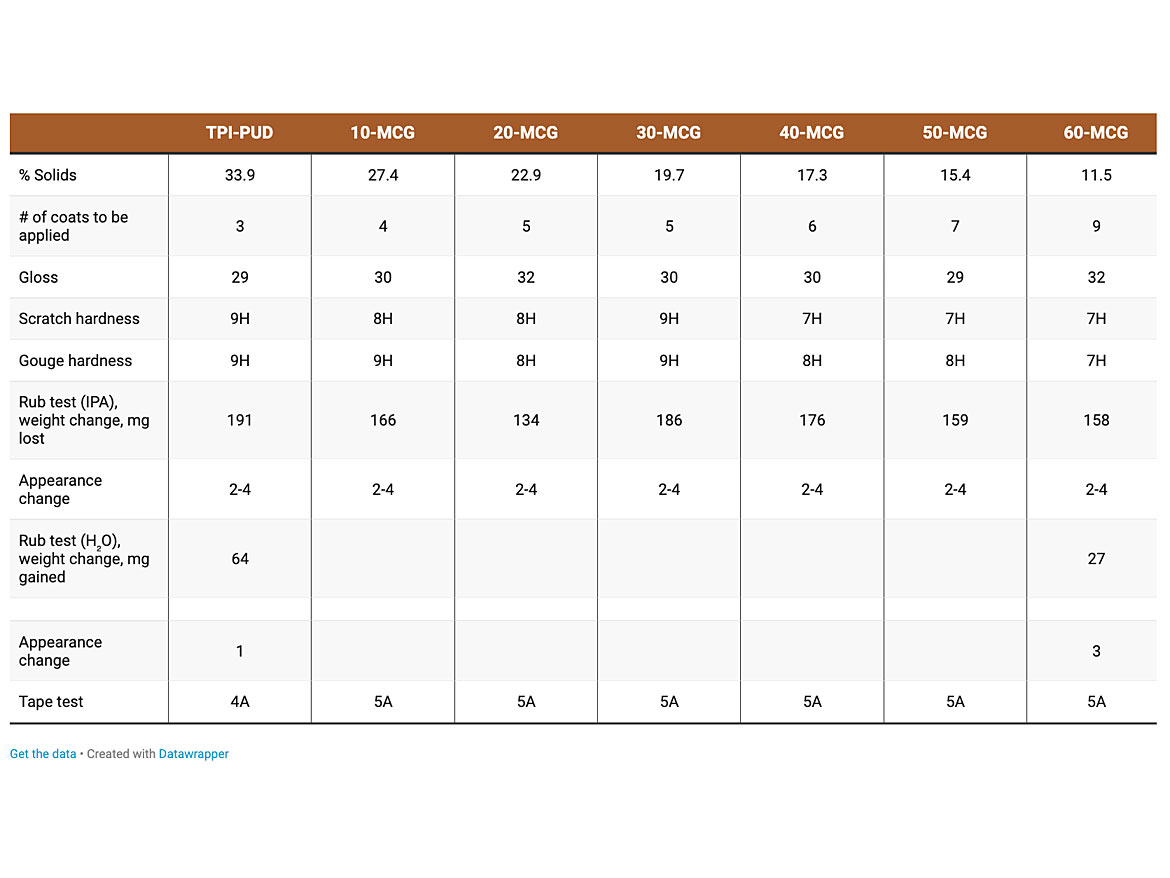

Summary
Alpha-1,3-polyglucose glucan wet cake and MCG were evaluated as additives to 1K-PUDs. It was demonstrated that the addition of high levels of glucan wet cake and MCG to PUDs resulted in increased modulus of films while maintaining high levels of elasticity. Although hygroscopic, both glucan wet cake and MCG improved the hydrolytic resistance of PUD films, resulting in increase elasticity while maintaining higher tensile modulus and toughness compared to the reference PUD. As a result, after humid age films containing 50% MCG had almost 300% elongation at break.
It was demonstrated that the addition of high levels of glucan wet cake and MCG on PUDs had negligible impact on the properties of coatings on metal substrates. It was demonstrated that glucan wet cake and MCG had no significant impact on hardness, adhesion strength, impact resistance, or resistance to polar or non-polar solvents. However, PUDs with high levels of glucan wet cake or MCG showed promising performance on wood coatings, outperforming the commercial water-based 1K-PUDs in both the scratch resistance and water-resistance tests.
*This paper was presented at the 2021 Polyurethanes Technical Conference.
Looking for a reprint of this article?
From high-res PDFs to custom plaques, order your copy today!