Evaluation of 1,3-Propanediol-Based Polyester and Polyether Polyols in Polyurethane Water Dispersions
for Direct-to-Metal Applications
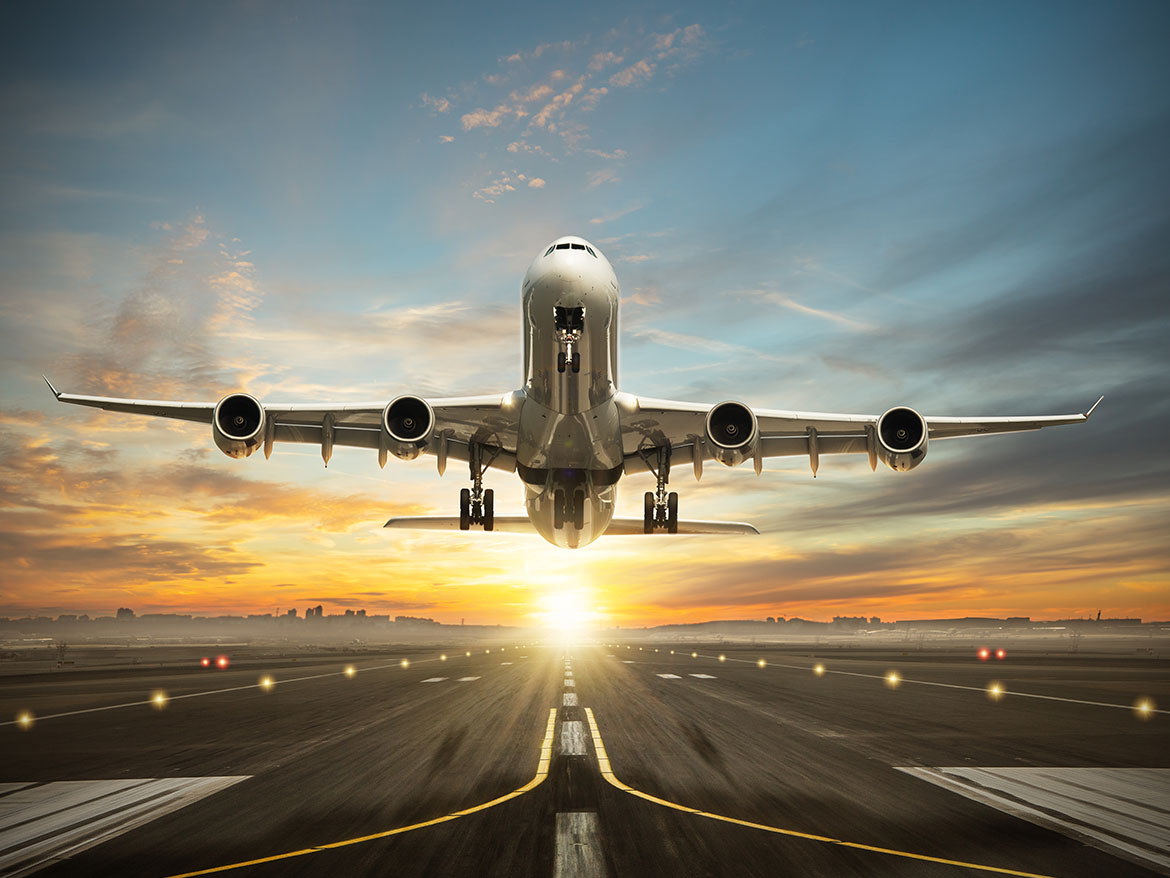
The use of solvent-free, waterborne polyurethane dispersions (PUDs) is widely discussed in the literature and has grown commercially across various industries due to several environmental factors. The introduction of 1,3-Propanediol (1,3-PDO) has been found to be useful in polyurethanes as a building block component of polyester and polyether polyols, and as a chain extender. Furthermore, the use of 1,3-Propanediold has been increasingly accepted based on its use on the commercial scale for producing polyester and polyether polyols. PUDs are a desirable coating for various applications including direct-to-metal (DTM) applications since they provide very good tensile strength, wear resistance, and have good adhesion to various metal substrates.
In a previous study, 2K-PUDs were prepared using the following PDO-based polyols: PDO-Adipate 2000 polyester polyol, PDO-Sebacate 2000 polyester polyol, PO3G 2000 polyether polyols, and for reference, BDO-Adipate 2000 polyester polyol, and PTMG 2000 (Evaluation of 1,3-Propanediol-Based Polyester and Polyether Polyols in Polyurethane Water Dispersions (PUDs) for Textile Coating Applications, CPI 2018). These 2K-PUDs were evaluated as coatings on textile substrates. 2K-PUDs were based on hydroxyl-functional oligomer dispersed in water, which was crosslinked with multi-functional hydrophilic aliphatic isocyanate. Due to the crosslinking, all 2K-PUD films exhibited significantly higher tensile modulus, and improved hydrolytic and solvent resistance compared to a 1K-PUD based on PDO-Adipate 2000.
PUDs are used also as coatings and adhesives for DTM applications. PUDs are a desirable coating for various DTM adhesive and coating applications since they provide a good combination of tensile strength and wear resistance, while providing excellent adhesion to various substrates, and can be formulated to be moisture resistant, offering potential resistance to corrosion. To obtain PUDs with good performance, the effects of varying the building block components (soft and hard segments) needs to be understood. The introduction of dimethyl propionic acid (DMPA) pendant ionic groups into hard segment blocks facilitates the formation of stable PUDs of acceptable solids loading by increasing hydrogen bond interactions. 2K-PUDs utilized in DTM applications are typically harder with higher modulus compared to 1K-PUDs. In many applications, these coatings are exposed to an exterior environment, low and elevated temperatures, oil and solvents, high humidity, UV radiation, and precipitation, among other conditions. Under these conditions, metals are susceptible to rusting and malfunctioning. As a result, metals are typically protected with coatings that include a corrosion-resistant additive of various chemical compositions. In this study, 2K-PUDs based on PDO-derived polyester and polyether polyols were evaluated as adhesives and coatings for DTM applications. The results of this study show that PDO-derived polyester polyols, while sustainable, also provide an interesting combination of performance in 2K-PUDs that could benefit DTM application as coatings and adhesives.
Experimental
Materials
The chemicals and materials used in this study are listed in Table 1. Aliphatic isocyanates IPDI and BAYHIDUR XP2655 were used as received from the supplier. The polyols used in 2K-PUD preparation were obtained from various sources (Table 1). PDO-Dodecanedioate (C12) 2000 MW polyester polyol was synthetized at Troy Polymers, Inc. The water content for the polyols used in the PUD synthesis was all less than 0.06% and measured using a Karl Fisher method, ASTM D 4672. As needed, the polyols were de-moisturized under vacuum at ~3 mm Hg and 70 °C – 80 °C prior to use.
The list of metals used in various 2K-PUD testing is also included in Table 1.
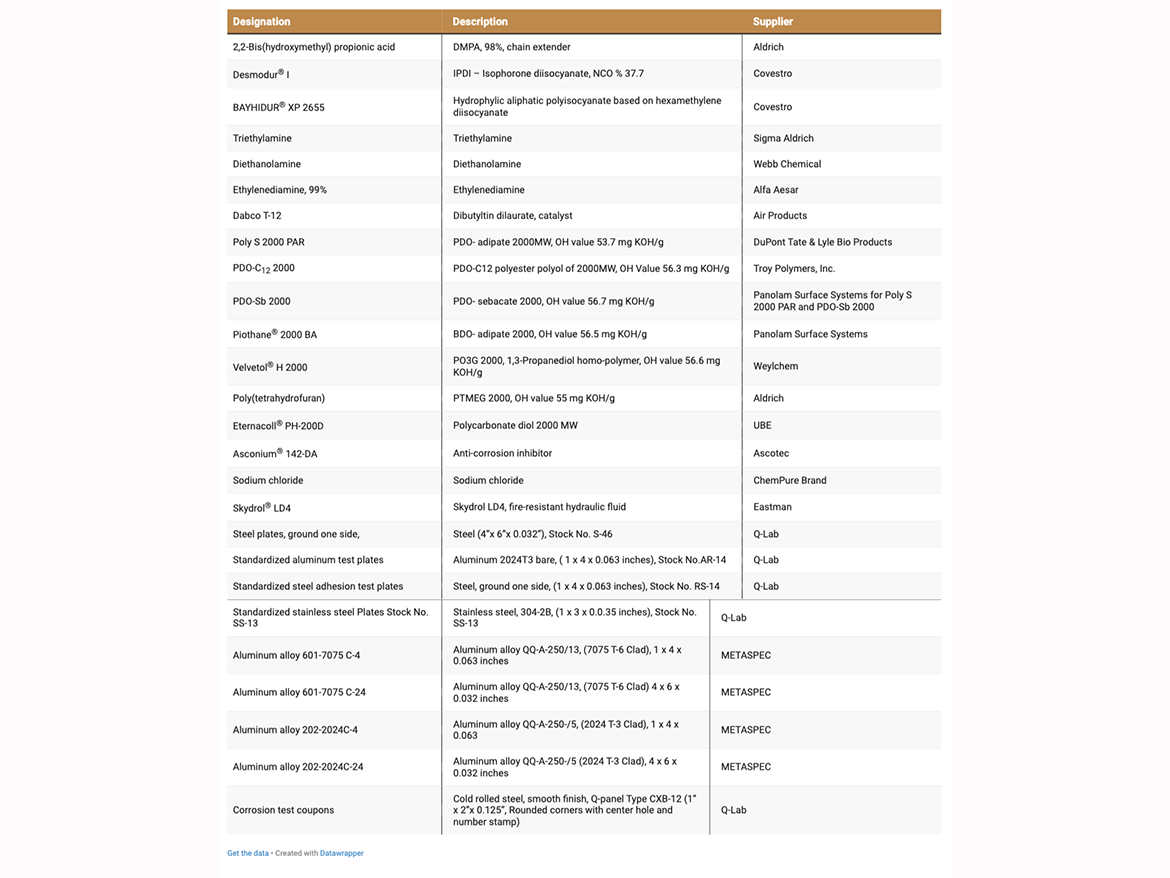
Preparation of 2K-PUDs
Seven types of 2K-PUDs were prepared and evaluated as direct-to-metal adhesives and coatings (Table 2). Two-component crosslinked PUDs (2K-PUDs) were based on (A) hydroxyl functional ionomer oligomers dispersed in water (HFO-4) that was reacted with (B) water-dispersible multi-functional aliphatic isocyanate (BAYHIDUR XP2655).
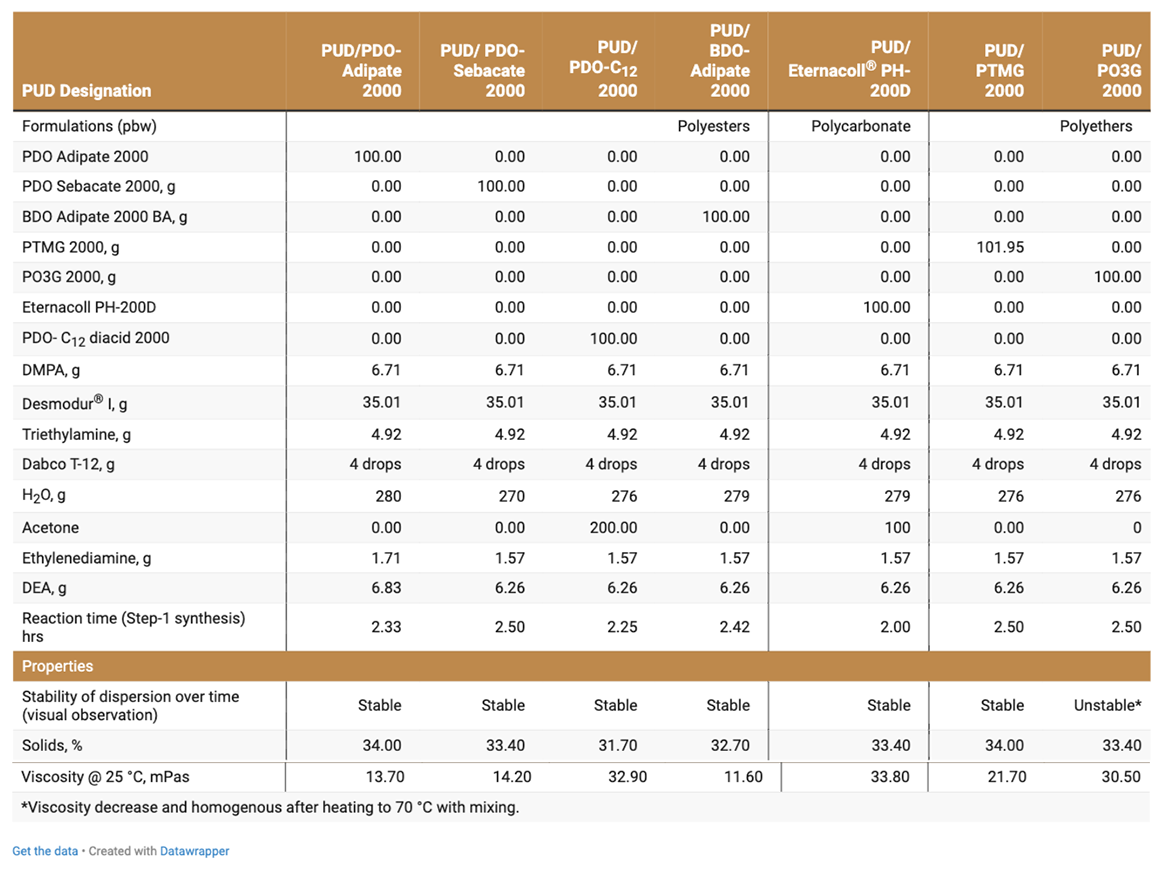
Hydroxyl functional ionomers were prepared in several steps, as follows:
The synthesis of hydroxyl functional ionomers (HFO-4) consists of the following steps (see Scheme 1):
- Step 1: NCO-terminated prepolymer was prepared by reacting aliphatic diisocyanate IPDI with a blend of polyol and chain extender DMPA (2,2-dimethylolpropionic acid) to introduce pendant carboxylic group into prepolymer backbone at the molar ratio of isocyanate: polyol: DMPA of 3.05:1:1.
- Step 2: The carboxylic group was neutralized with triethylamine (TEA), forming an ionomer group that enables dispersion of NCO-prepolymers in water.
- Step 3: The NCO-prepolymer was dispersed in water.
- Step 4: The NCO-prepolymer was reacted with the blend of diethanolamine (DEA) and ethylene diamine (EDA) at isocyanate index 1.05 (an end-capping reaction).
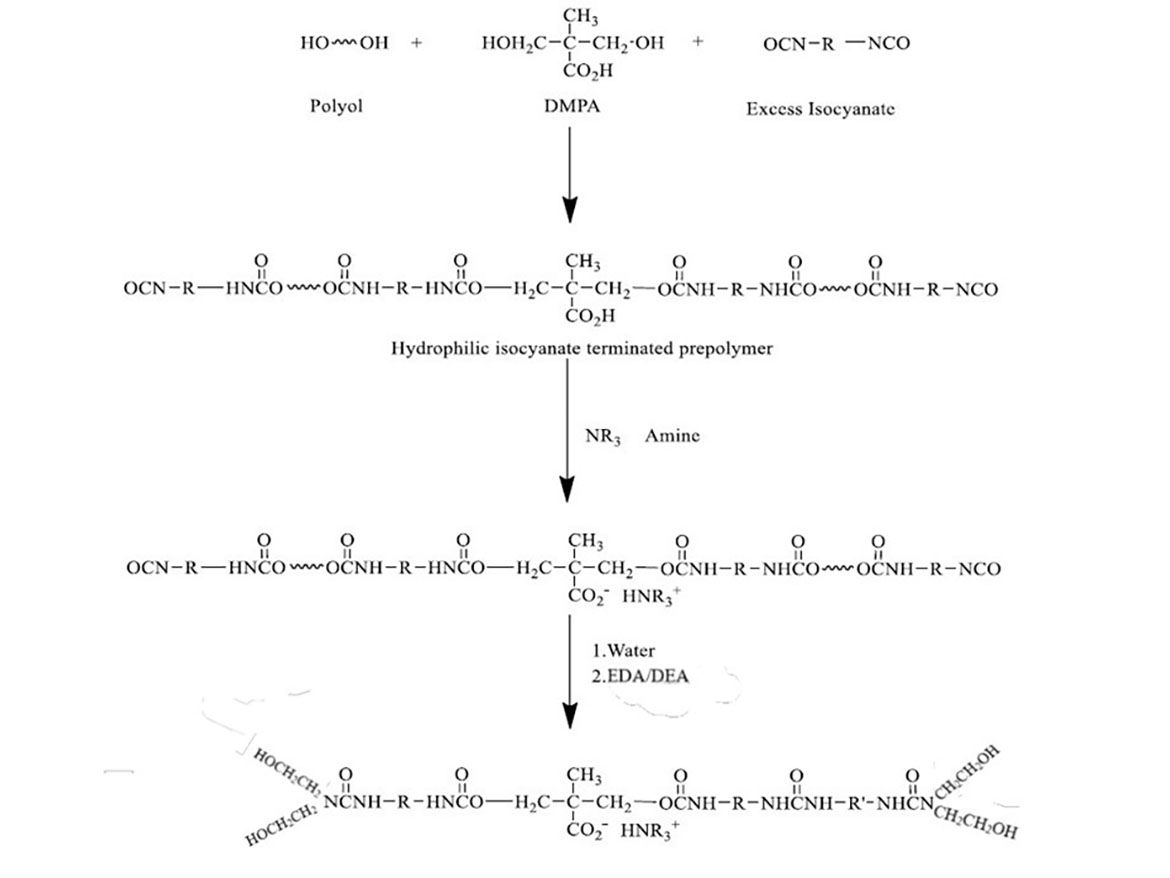
The synthesis of PUDs was carried out in a 1000 mL reactor equipped with nitrogen flow, heating mantle with temperature controller, and mechanical mixing. Liquid polyol (0.1 equivalent) and DMPA (0.1 equivalent) were charged into reactor and heated under mixing to 135 °C (Table 3). At that temperature, DMPA was melted and homogenized with polyols for 10 minutes. The mixture was cooled gradually under mixing to 80 °C. Dabco T-12 catalyst was added to the reactor, followed by the addition of IPDI (0.305 equivalents). NCO-prepolymer synthesis was monitored via NCO% determination (ASTM D 5155). The synthesis of NCO-prepolymer was completed within 2-3 hours, however, was somewhat dependent on the polyol. After the NCO-prepolymer was formed, it was cooled to 50 °C. Triethylamine (TEA) was added to react with the carboxylic group at equimolar ratio, followed by mixing for 20 minutes. Subsequently, distilled water was added to the ionomer NCO-prepolymer under vigorous mixing to form a milky, stable dispersion. A calculated amount of diethanolamine (DEA) in 30 mL of water was added to the NCO-prepolymer water dispersion under stirring for 20 minutes. Subsequently, ethylene diamine (EDA) in 30 mL of water was added to the prepolymer water dispersion and mixed for an additional 20 minutes to complete the reaction, with remaining isocyanate groups thus forming a hydroxyl-functional ionomer oligomer water dispersion (HFO-4). The resulting HFO-4 water dispersions contained 30-35% solid content.
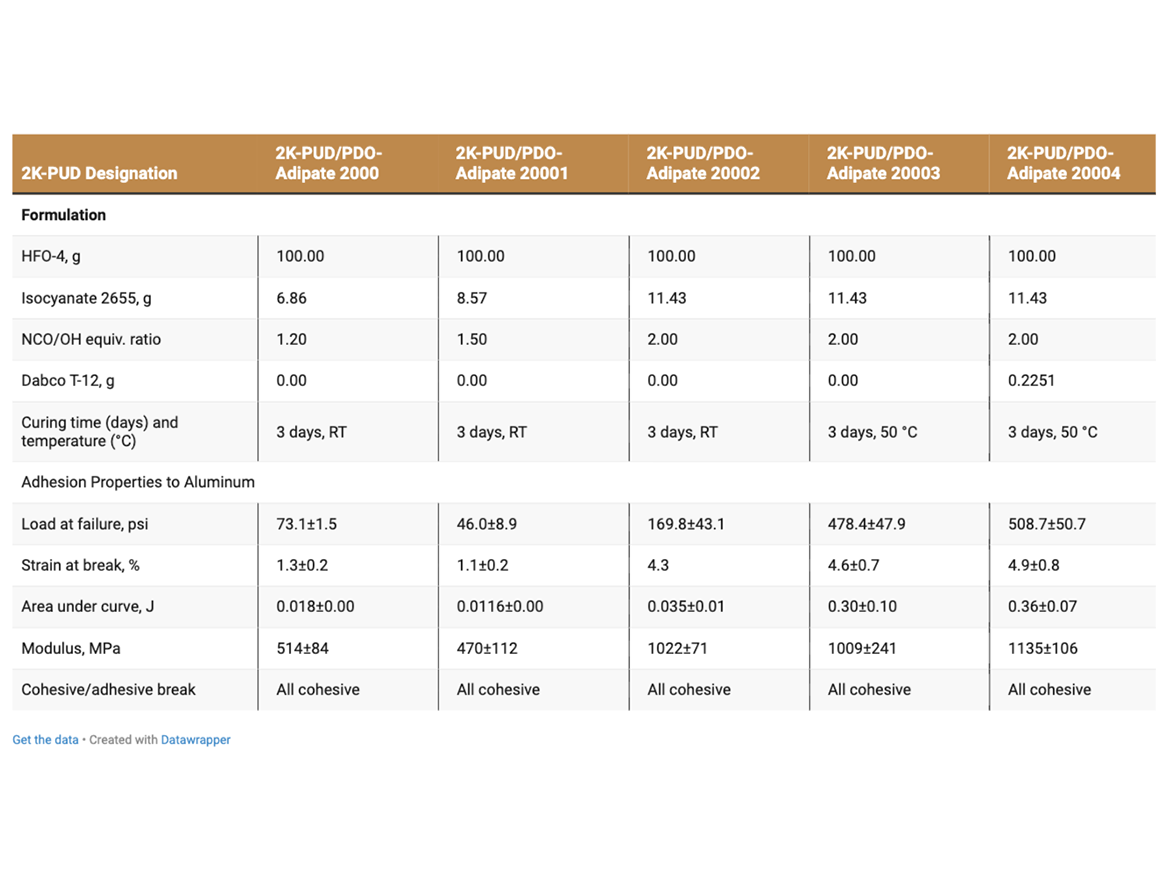
HFO-4 based on polycarbonate polyol and PDO-C12 diacid 2000 MW polyol were prepared using the acetone process and presented with the remainder of the materials being evaluated in this study (Table 4). For the acetone process, the product of Step 2 of synthesis was dissolved in acetone. Acetone was removed from the final HFO-4 via vacuum distillation using a rotary evaporator.
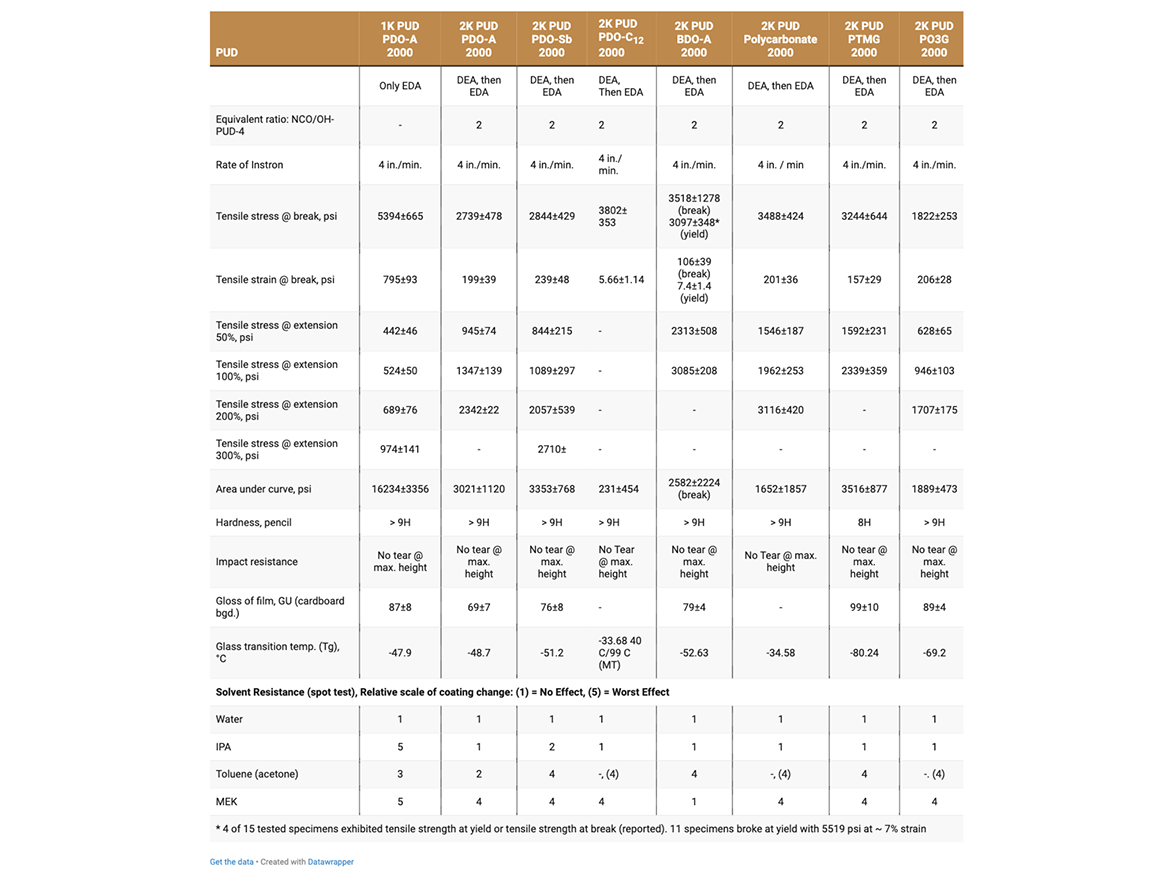
Properties of HFO-4 PUDs are reported in Table 2. HFO-4 PUDs were subsequently evaluated for:
- Viscosity (25 °C, ASTM D 4878, Brookfield Viscometer (Spindle No. 6));
- Solid content, %;
- Stability over time, RT.
2K-PUD Films, Adhesives, and Coatings Testing
HFO-4 water dispersions were mixed at room temperature with 100% sufficiency of multi-functional aliphatic isocyanate BAYHIDUR XP 2655.
Films (only on PUD based on polycarbonate polyols and PDO-Dodecanedioate polyester polyol) were prepared by casting PUDs onto polyethylene substrate using Dr. Blade at 30 - 40 mils thickness followed by curing for 3 days at room temperature. The following film properties were tested according to the following:
- Hardness, pencil hardness, ASTM D3363;
- Tensile strength and elongation (flexibility), ASTM D2370;
- Humidity resistance (change of tensile properties prior and after humid aging at 95% relative humidity at 50 °C for 3 days);
- Chemical characterization, FTIR (Appendix E);
- Glass transition temperature (Tg), Differential Scanning Calorimeter (DSC).
The adhesive strength of 2K-PUDs in bonding to various metal substrates (aluminum, steel, stainless steel, aluminum alloy 601-7075 and aluminum alloy 202-2024C) was measured according to Lap Shear test ASTM D1002. Hydroxyl-functional water dispersions (HFO-4) were mixed with a calculated amount of water-dispersible aliphatic isocyanate at room temperature. This blend (2K-PUD) was stirred at room temperature for 10 minutes. After 1 hour, samples were applied on metal substrates to create an adhesive test sample. 0.2 g of the 2K-PUD blend was spread over a ½ x 1-inch bond area of standardized adhesion test plate. Two plates were clamped together over the bond area and allowed to cure and dry at 50 °C for 3 days before testing. Ten samples for each type of 2K-PUD on each metal substrate were tested using Lab Shear test ASTM D1002. The initial adhesion lap shear strength data are presented in Tables 5a, 5b, and Figure 1.
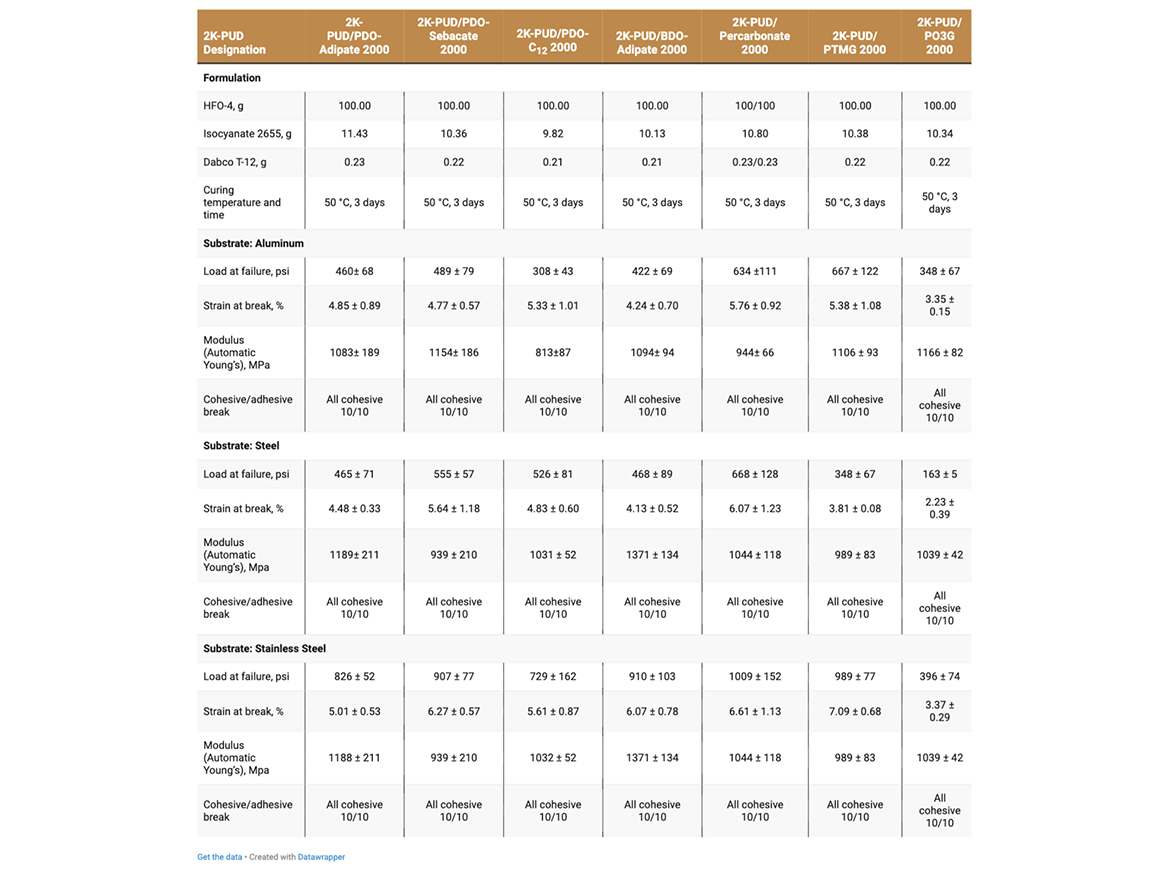
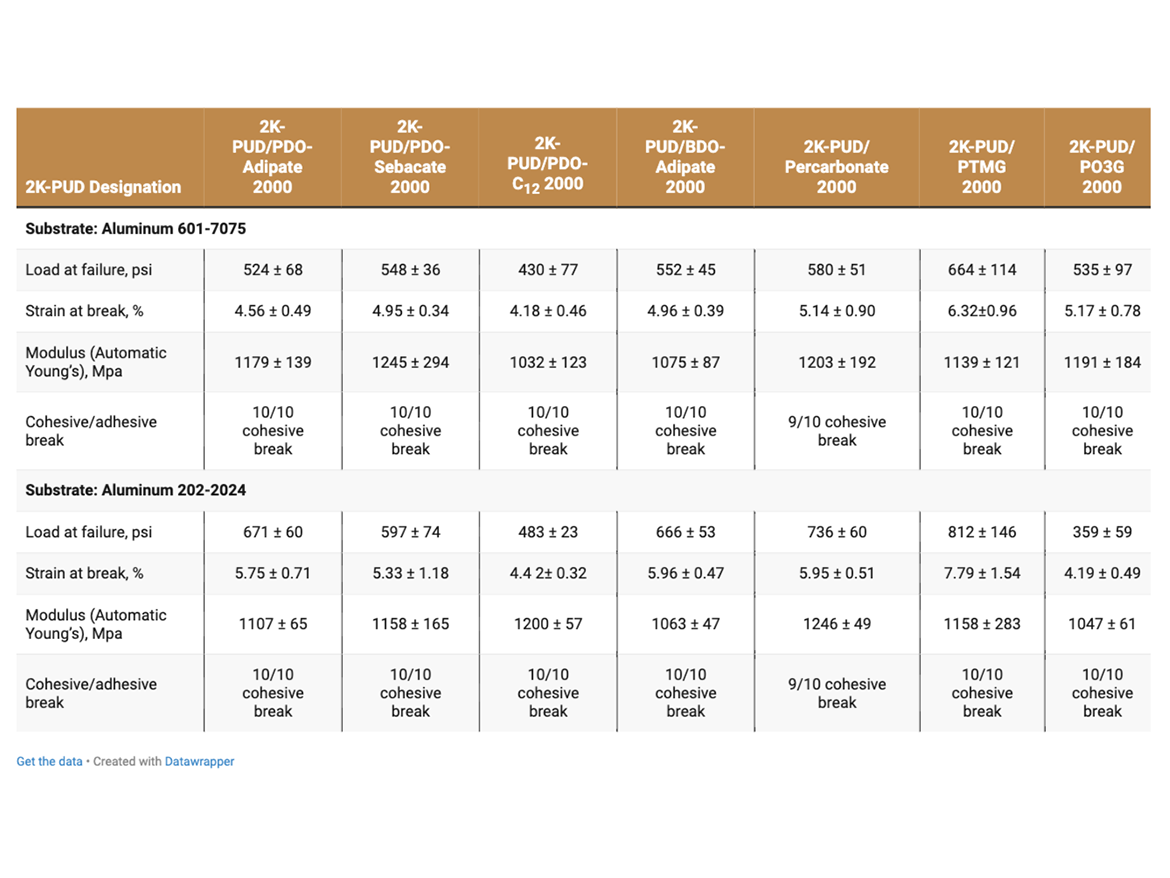
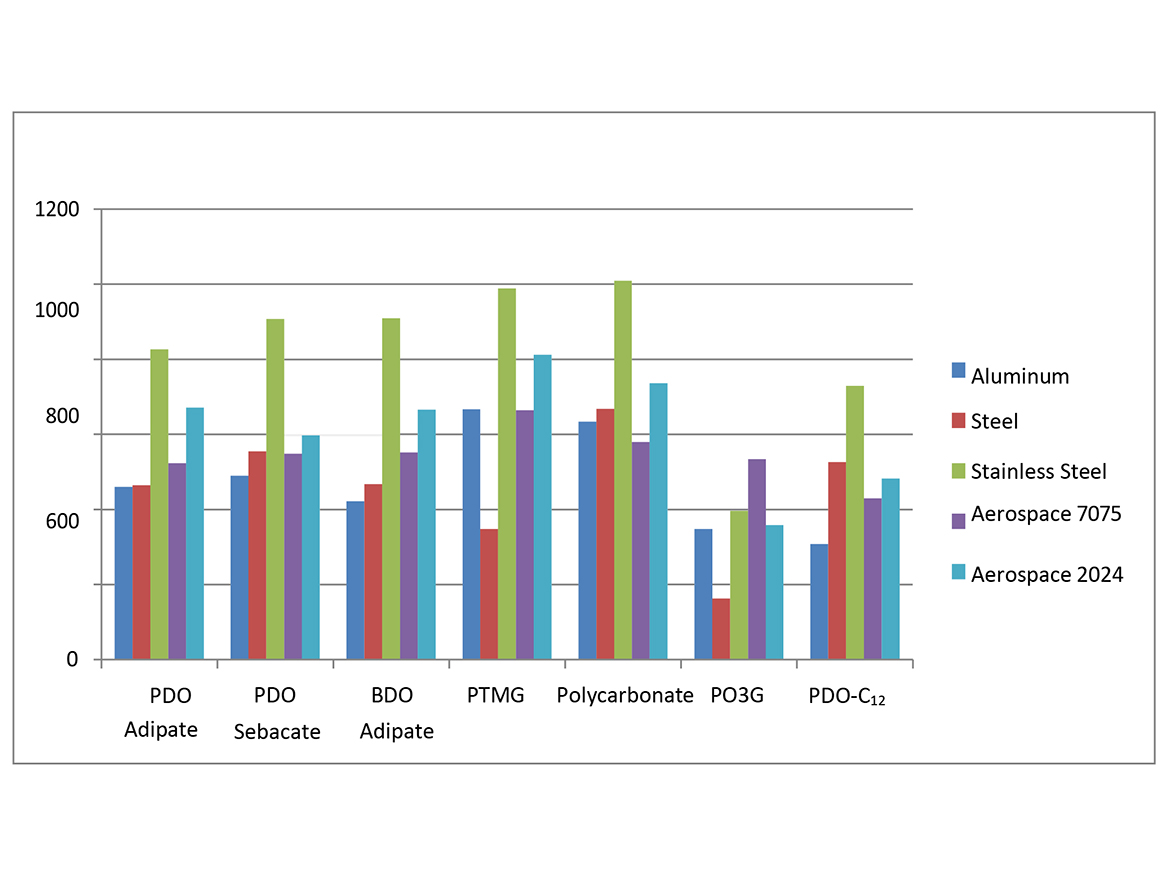
Adhesive samples were aged in a humidity chamber at 38 °C and 95% relative humidity for 7 days. The adhesion properties for the aged adhesion samples were measured according to Lab Shear test ASTM D1002 and are presented on Tables 6a and 6b.
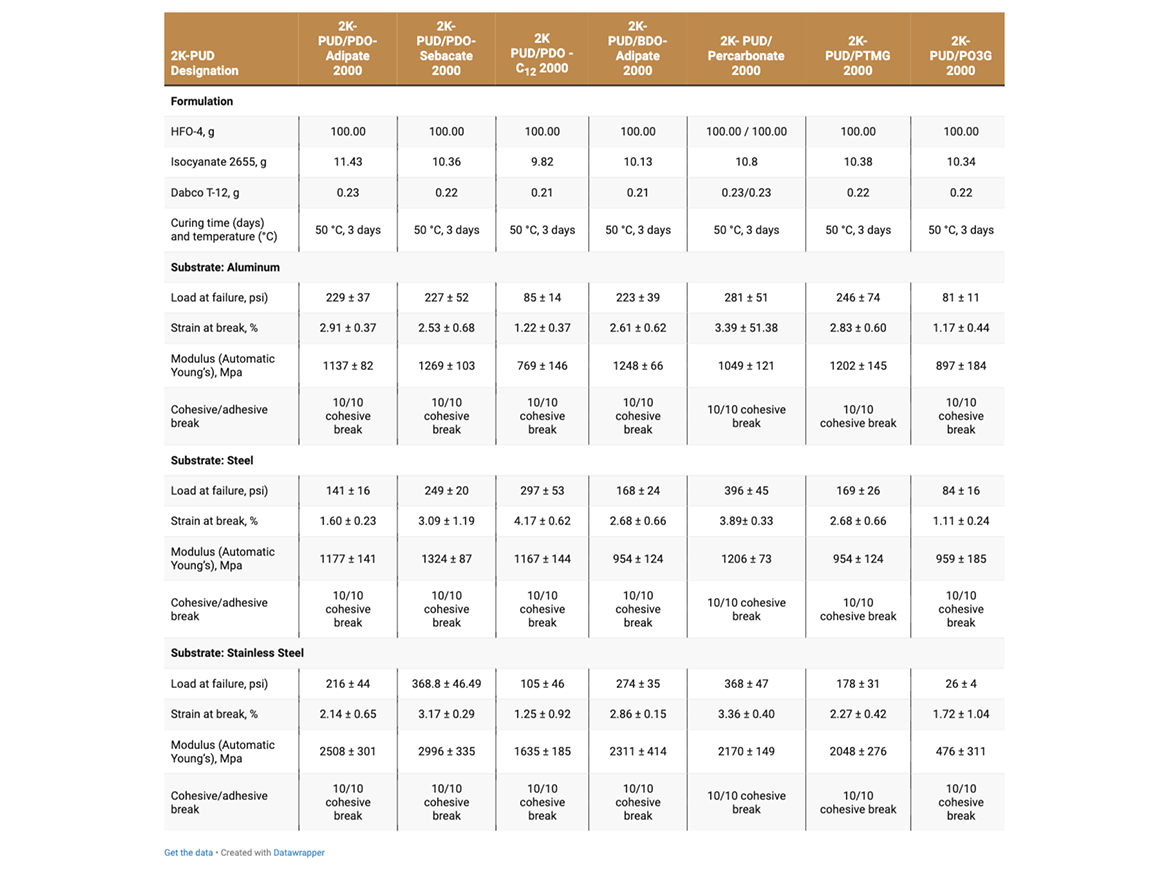

Coatings on metal substrate were prepared by casting 2K-PUDs onto standardized stainless-steel test coupons (S-46, Q-Panel) using Dr. Blade at ~30 mils thickness and cured at RT for 3 days. The following properties measured:
- Impact resistance, ASTM D2794;
- Adhesion – peel test, ASTM D3359;
- Solvent resistance – Rub test, ASTM D5402
- Change of film thickness of coatings on metal substrate after 200 double rubs;
- 10 drops of solvent were applied on coating, covered with a watch glass for 10 minutes, and afterwards scratched with metal spatula. The changes were visually observed and graded on a relative scale: (1) = No effect, (5) = worst effect.
2K-PUDs were coated onto various substrates (aluminum, steel, stainless steel, aluminum alloy 601-7075 and aluminum alloy 202-2024C) and exposed to humid conditions 38 °C, 7 days and 95% relative humidity to determine the effects of hydrolytic aging (Table 7). The following properties for the hydrolytically aged samples were evaluated:
- Impact resistance, ASTM D2794;
- Adhesion – peel test, ASTM D3359;
- Blistering;
- Rusting.

Corrosion steel test coupons (cold rolled steel, smooth finish, Q-panel Type CXB-12) were coated on both sides by dipping into 2K-PUDs containing an anti-corrosion additive (corrosion inhibitor), Asconium® 142-DA. Note: The corrosion additive was added and blended into the HFO-4 dispersion prior to blending with isocyanate. Coated metal specimens were cured for 2 days at RT and 1 day at 50 °C. Cured specimens were immersed into a 3% aqueous sodium chloride solution (Table 8a). Control 2K-PUD samples of PDO-Adipate and BDO-Adipate were prepared without the addition of a corrosion inhibitor for reference (Table 8b). Coated steel coupons were observed periodically for changes in corrosion coverage and graded.
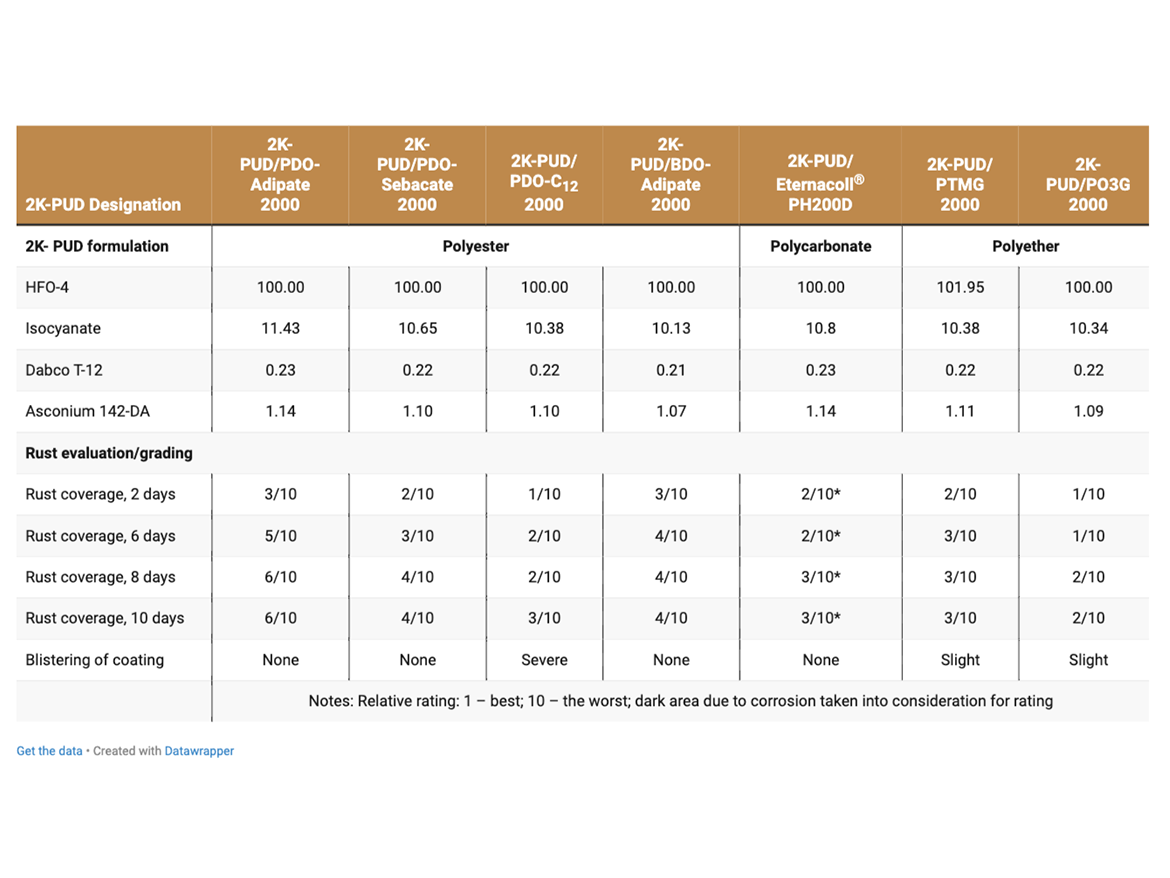
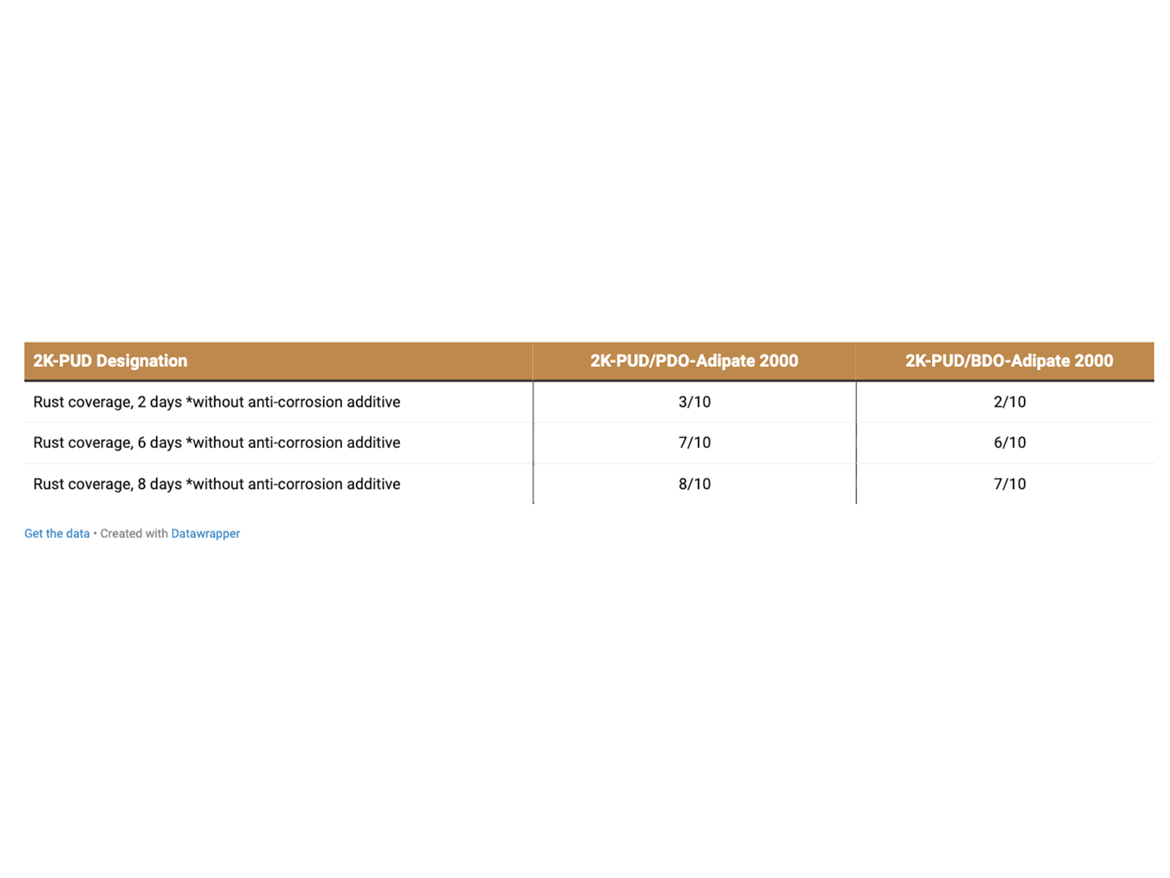
The effect of Skydrol® LD4 fire-resistant hydraulic fluid (spot test) on all 2K-PUDs coated on aluminum alloy 601-7075 and aluminum alloy 202-2024C was evaluated (Table 9).
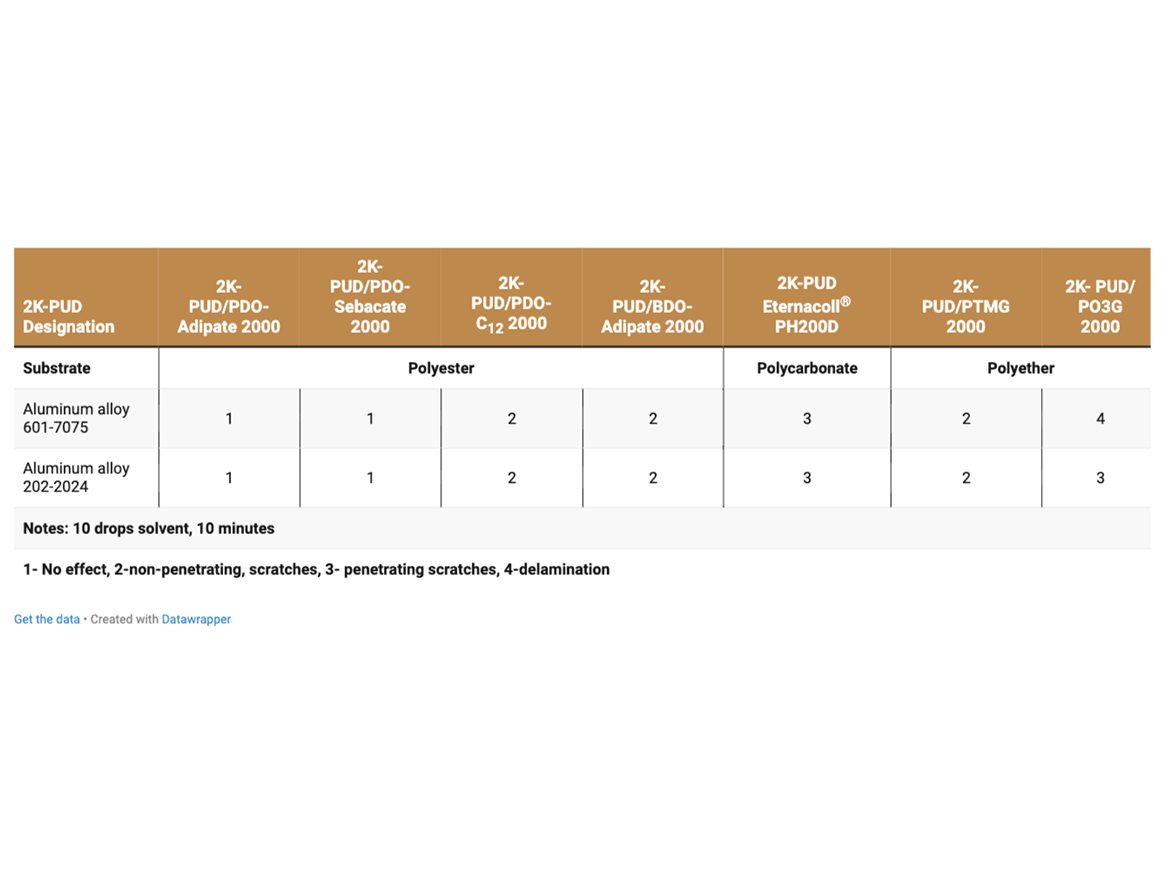
Results and Discussion
2K-PUD Dispersions
Seven types of 2K-PUDs were prepared and evaluated as DTM coatings and adhesives. 2K-PUDs were prepared with 1,3-PDO-based polyols included: PDO-Adipate 2000, PDO-Sebacate 2000, PDO-Dodecanedioate (C12) 2000 and PO3G 2000 (Polytrimethylene ether polyol 2000). BDO-Adipate 2000 was used as the reference polyester polyol, and PTMG 2000 was used as the reference polyether polyol. Polycarbonate 2000 performance polyol in various PUD applications was used as an additional reference. Formulation details are presented in Table 2.
2K-PUDs were based on (A) hydroxyl-functional oligomer dispersed in water (HFO-4) that was crosslinked with (B) multi-functional water-dispersible aliphatic isocyanate and the addition of tin-catalyst. HFO-4 water dispersions were prepared in a four-step procedure. In this procedure, an NCO-prepolymer, based on a polyol, an aliphatic isocyanate, DMPA and triethylamine was dispersed in water and reacted with chain stoppers, DEA and EDA, to introduce four hydroxyl groups for the HFO-4 oligomer (Schematic 1). HFO-4 oligomers based on PDO-Dodecanedioate (C12) 2000 and polycarbonate 2000 MW polyol were prepared using acetone as co-solvent. The solid content of HFO-4 dispersions were determined to be 32%-34%, and their viscosities were relatively low (Table 4). HFO-4 water dispersions were stable over time, except for PO3G 2000 polyols. PO3G 2000-based PUD dispersion was stable for 3 days and then stratified; however, the dispersion was re-dispersed by heating at 70 °C with mixing.
The effect of formulation parameters and curing conditions on Lap-shear adhesion strength of 2K-PUD based on PDO Adipate 2000 was evaluated (Table 3). The highest adhesion strength of 2K-PUD was obtained when formulated at NCO/OH equivalent ratio of 2/1 of isocyanate cross-linker/HFO-4, added a tin-catalyst and the adhesive was cured for 3 days at 50 °C (Table 3). These conditions were applied in the preparation and testing of all 2K-PUD adhesives and films in this study.
2K-PUDs Films
In this study, the basic structural properties of films from 2K-PUDs based on polycarbonate 2000 and PDO-Dodecanedioate (C12) 2000 polyester polyols were evaluated (Table 4). The properties of five other 2K-PUDs were reported in an earlier study.8 2K-PUDs based on Eternacoll PH-200D and PDO-Dodecanedioate (C12) 2000 exhibited good tensile strength. However, the elasticity of film based on PDO-Dodecanedioate (C12) 2000 was low at 5%, compared to the elasticity of the 2K-PUD polycarbonate film of 200%. The films based on 2K-PUD based on the remaining polyols also had tensile elasticities greater than 100%. Low elasticity of 2K-PUD films based on PDO-Dodecanedioate (C12) 2000 is most probably due to a high degree of crystallinity.
Polycarbonate 2K-PUD film performed very well in hydrolytic aging testing, retained 97% of their original tensile strength and 77% elongation at break, while the elasticity of PDO-Dodecanedioate (C12) 2000 polyol increased 10 times and tensile strength reduced to ~40%. These two 2K-PUDs exhibited similar solvent resistance properties. PDO-Dodecanedioate (C12) 2000 was synthetized at Troy Polymers using in-house protocol for synthesis of polyester polyols, as described in the Experimental section of this report. The polyol of targeted hydroxyl value and low acidity was obtained (Table 1). The polyol was crystalline, having a melting point of 62 °C.
2K-PUDs Adhesive Strength to Metal Substrates
The adhesive strength of 2K-PUDs was studied using five different metal substrates, including aluminum 2024T3 (Q-Lab), aluminum alloy 601-7075 C-4 (Metaspec), aluminum alloy 202-2024C-4 (Metaspec), stainless steel 304-2B (Q-Lab) and steel (Stock No RS-14, Q-Lab). Details on metals are presented in Table 1.
The adhesive strength was found to depend on both the type of 2K-PUD and type of substrate (Tables 5a and 5b, Figure 1). Overall, the polycarbonate polyol-based 2K-PUD appears to provide the highest initial adhesion strength as measured by load at failure. However, 2K-PUDs based on PDO-Adipate 2000, BDO-Adipate 2000, and PDO-Sebacate 2000 also provide excellent adhesion strengths while the adhesive strengths to all tested metals, resulting in cohesive breaks. 2K-PUDs based on PDO-C12 2000 polyester polyol was somewhat lower compared to 2K-PUDs based on the other polyester polyols, but still yielded cohesive breaks. Among polyester polyols, PDO-Sebacate yielded 2K-PUDs with the best combination of adhesion to metal substrates. The adhesion strength of 2K-PUD PO3G 2000 was lower than PTMEG-based 2K-PUDs, however, they both resulted in cohesive failures. 2K-PUD PTMG 2000 based performed comparable to the polycarbonate 2000 polyol, except on the steel substrate. Stainless steel appears to have better adhesion properties than other substrates for most 2K-PUDs; in some cases, relatively high adhesion strength of approximately 1000 psi was obtained (Figure 1).
The adhesive strength and strain at break of all 2K-PUDs on all substrates in general decreased upon hydrolytic aging, while the modulus increased (Tables 6a and 6b). This indicates the possibility of some additional crosslinking taking place during the hydrolytic age. It should be noted that overall, 2K-PUD based on PDO-Sebacate 2000 MW polyol performed comparable in adhesion to various metals after hydrolytic age to 2K-PUD based on polycarbonate polyol. Overall, 2K-PUDs based on PTMEG outperformed 2K-PUDs based on PO3G in adhesion test to metals after the hydrolytic age.
2K-PUDs Coatings Performance on Metal Substrates after Hydrolytic Aging
2K-PUD coatings on aluminum, steel, stainless steel, aluminum 601-7075, and aluminum 202-2024, were exposed to hydrolytic aging (38 °C, 95% relative humidity, 7 days) and their properties evaluated (Table 7). The coatings based on PDO-Adipate 2000 and BDO-Adipate 2000retained excellent adhesion (peel test) properties on all tested substrates. The coatings based on polycarbonate 2000 exhibited tearing during the adhesion peel test on all substrates. Most of other coatings exhibited tearing just on one substrate (Table 7).
The coatings retained good impact strength, and there were no signs of blistering. All coatings (with no anti-corrosion additive) on steel substrate exhibited signs of rusting after the hydrolytic age. It appears that coatings based on PDO-Sebacate 2000, polycarbonate 2000, and PTMG 2000 offered higher resistance to rusting.
2K-PUDs Corrosion of 2K-PUD Coatings on Steel Substrate
The corrosion resistance of 2K-PUDs coated on steel coupons (Q-panel Type CXB- 12) immersed in a 3% aqueous sodium chloride solution was tested (Tables 8a and 8b). An anti-corrosion additive (Asconium, 142-DA) was added to PUD coatings.
The area of the coated plate covered by rust spots as well as blistering was used to grade performance of coatings with respect to corrosion resistance. It is noted that corrosion developed with all 2K-PUD-coated steel substrates. It is proposed that the corrosion of 2K-PUDs could be also linked due to hydrophilic ionomer site in the polymer network.
As presented in Table 8a, coatings based on PO3G 2000 polyether polyol performed the best in this test (relative scale). 2K-PUD based on PDO-Dodecanedioate (C12) polyester polyol performed comparable to coatings based on PTMG and polycarbonate polyols. 2K-PUDs based on PDO-Sebacate was also very close in performance.
The corrosion of 2K-PUDs coatings, without anti-corrosion additive, was more severe than that with anticorrosion additive (Tables 8a and 8b).
2K-PUD Coating Resistance to Skydrol LD4
Resistance to Skydrol LD4, a fire-resistant hydraulic fluid, is of importance for coatings in the aviation industry. Coatings based on PDO-Adipate 2000 and PDO-Sebacate 2000 polyester polyols exhibited excellent chemical resistance to Skydrol LD4 using a spot test when tested on both plain aluminum, aluminum 601-7075, and aluminum 202-2024, used commonly in the aviation industry (Table 9). On the other hand, 2K-PUDs based on polycarbonate polyols and polyether polyols did not perform as well.
Conclusions
The objective of this project is to evaluate two-component polyurethane water dispersions (2K-PUDs) based on 1,3-PDO polyester polyols (PDO-Adipate 2000 and PDO-Sebacate 2000, and PDO-Dodecanedioate (C12) 2000), and PO3G polyether polyols as coatings and adhesives for direct-to-metal applications. Reference 2K-PUDs based on BDO-Adipate 2000, PTMG 2000, and polycarbonate 2000 MW polyols were used as controls for comparison. The following conclusions can be made based on the work in this study.
- Seven types of waterborne PUDs were successfully synthesized from a range of different polyol chemistries by using DMPA (dimethylolpropionic acid) neutralized with triethylamine (TEA) as the ionic hydrophilic segment incorporated in the polymer backbone.
- The effects of different soft segments on the stability of waterborne PUDs, as well as the physical, mechanical, thermal and chemical resistance properties of the resultant PUDs as films and coatings for DTM applications were investigated.
- DSC results indicated that films based on polyether PUDs were softer and had better cold resistance than polyester-based films from PA, BA and PDd, and PSb-based polyol.
- Mechanical testing showed that PUD films based on PDO were typically lower in tensile strength, higher in flexibility (elongation), and lower in tensile stress modulus versus the standard BDO, Polycarbonate, and PTMG.
- Chemical and corrosion resistance was evaluated where PDO-Sebacate performed exceptionally well.
- PUD films based on PDO-Adipate and PDO-Sebacate showed exceptional solvent resistance to Skydrol LD4, a fire-resistant hydraulic fluid and is of importance for coatings in the aviation industry.
- Overall, the testing demonstrated that PDO-based polyols performed very well as DTM coatings, especially PDO-Sebacate when compared to Polycarbonate.
- Adhesive Lap Shear strength was performed on the polyester and polyether based 2K-PUDs including load to failure, stress at break, modulus (Young’s), and mode of adhesive break (adhesive vs cohesive) for both prior (unaged) and after (aged) hydrolytic aging. Polycarbonate had the best lap shear adhesive strength properties across all metal substrates; however, PDO-Sebecate performed very well in comparison.
- 2K-PUD based on PDO-Dodecanedioate (C12) might be a good candidate as a hot melt adhesive based on its crystallinity.
It can be concluded that 2K-PUDs performance depends on the metal substrate. Optimization of the formulation, knowledge of the environmental conditions, and the specific metal substrate will be keys to developing a successful material for protecting or adhering to metal surfaces. However, overall, it appears that 2K-PUDs based on PDO-Sebacate 2000 polyol are the best candidate for adhesives and coatings for DTM applications, with overall performance approaching 2K-PUDs based on polycarbonate polyol.
Acknowledgements
CovationBio™ LLC would like to thank Aisa Sendijarevic and Ibrahim Sendijarevic from Troy Polymers, Inc., for their dedication to and guidance on this project, including the ultimate preparation, syntheses comparative analyses, and interpretation of results.
References
1.Xiao, H.X.; Frisch, K.C. ed.: Advances in Urethane Ionomers., Inc. Technomic Publishing Company Inc., Lancaster, Pennsylvania, USA; 1995.
2. Dietrich, D. Progress in Organic Coatings. Vol. 9 (1981) 298.
3. Wicks, Jr., Z.W.; Wicks, D.A.; Rosthauser, J.W. Progress in Organic Coatings, Vol.44 (2002) 161-183.
4. Kim, B.K.; Lee., J.C. J. Polymer. Sci., Polym. Chem. Ed, Vol. 34 (1996), 1095-1104.
5. Rosthauser, J.W.; Nachtkamp, K. Adv. Urethane Sci. Technol., Vol. 10 (1987) 121.
6. Miller, R. (DuPont Tate & Lyle Bio Products); Janssen, R.; Theunissen, L. (Reverdia). “Evaluating the Properties and Performance of Susterra 1,3-Propanediol and Biosuccinium Sustainable Succinic Acid in TPU Application”, CPI Polyurethanes 2012 Technical Conference, September 2012, Atlanta, Georgia.
7. Hurff, S.J., and Shen, M. (DuPont Tate and Lyle Bio Products); Sendijarevic, I., and Sendijarevic, A. (Troy Polymers). “Advances in the Use of Bio-based Components in Aqueous Polyurethane Dispersions for Coating and Adhesive Applications”, CPI Polyurethanes 2018 Technical Conference, October 2018, Atlanta, Georgia.
8. Gahan, S.L., and Shen, M. (DuPont Tate and Lyle Bio Products); Sendijarevic, I., and Sendijarevic, A. (Troy Polymers). “Evaluation of 1,3-Propanediol Based Polyester and Polyether Polyols in Polyurethane Water Dispersions (PUDs) for Textile Coating Applications”, CPI Polyurethanes 2019 Technical Conference, October 2019, Orlando, Florida.
Looking for a reprint of this article?
From high-res PDFs to custom plaques, order your copy today!