Peelable Anti-Corrosion Coatings

Most bare metal will corrode if exposed to moisture and other environmental factors. That’s a given. Traditional paints for metal are designed for corrosion prevention to preserve the appearance and integrity of the surface. These paints adhere strongly to the metal, and this adhesion is vital to the corrosion protection they provide. Typical paints are designed to be difficult to remove, and to last.
But bare metal parts that are temporarily stored or transported during processing often require a coating that will protect against corrosion and be easily removed just prior to final assembly. Considering strict specifications of many OEMs and suppliers, corrosion is not an option.
But is it possible to provide the corrosion protection and durability of a paint with the limited adhesion of a temporary, peelable coating?
The Dirt on Grease
Oily, greasy or waxy materials are commonly used to provide a basic level of corrosion protection and can effectively form a barrier between bare metal and the environment. However, they can be difficult and messy to remove, and could require special disposal if environmentally hazardous. Grease may also require re-application every two to six months if exposed to rain or other conditions that can wash away the protective layer.
A further issue with greases is that painted areas can stain and require retouching. While they provide corrosion resistance, they are often ineffective at providing protection against the caustic chemicals common around machine shops and OEM facilities.
Altogether, greases may prevent corrosion, but the maintenance they require can slow production, consume resources and cause inefficiencies that impact the bottom line.
Traditional Peelable Coatings
Peelable coatings have long been available for uses such as protecting paint on new vehicles, window protection and to prevent scratches during shipping. While these traditional peelable coatings are easy to remove, they only provide general protection, with very little corrosion protection or chemical resistance.
Lubrizol set out to discover whether a peelable coating technology could also deliver outstanding corrosion protection. Tapping into extensive experience in specialty corrosion inhibitors and acrylic polymer technology, Lubrizol innovated a resin capable of delivering the corrosion protection, scratch protection and chemical resistance of a paint, but that is also easily peelable.
A Peelable Pioneer
Carboset® PL 3127 combines proven performance in coating durability, ease of application, quick drying, and outstanding corrosion and weather resistance that protects bare and painted metal products, without leaving residue behind.
It can be brushed, sprayed or dipped, making application faster and easier than grease or oil. When the part or surface is needed, the coating simply peels off and can be disposed of in general waste streams. If desired, the coating can also be left in place, and will naturally wear off over time. To help as a visual indicator in end-use applications, coatings with Carboset PL 3127 can be tinted with virtually any color.
Carboset PL 3127 is a waterborne polymer with ultra-low VOC content (unlike oil and grease), and can easily be incorporated into formulations with VOCs less than 50 g/L. In addition to VOC compliance, the polymer does not contain APEOs or NPEs. It is designed to be used in both interior and exterior environments.
Corrosion Testing
Using ASTM B117 salt spray corrosion testing, the new resin was analyzed against three commonly available peelable resins. The results of the testing demonstrate the polymer’s ability to greatly extend corrosion resistance. Figure 1 shows the results of salt spray testing after 336 hrs, clearly demonstrating the outstanding corrosion protection delivered by Carboset PL 3127.
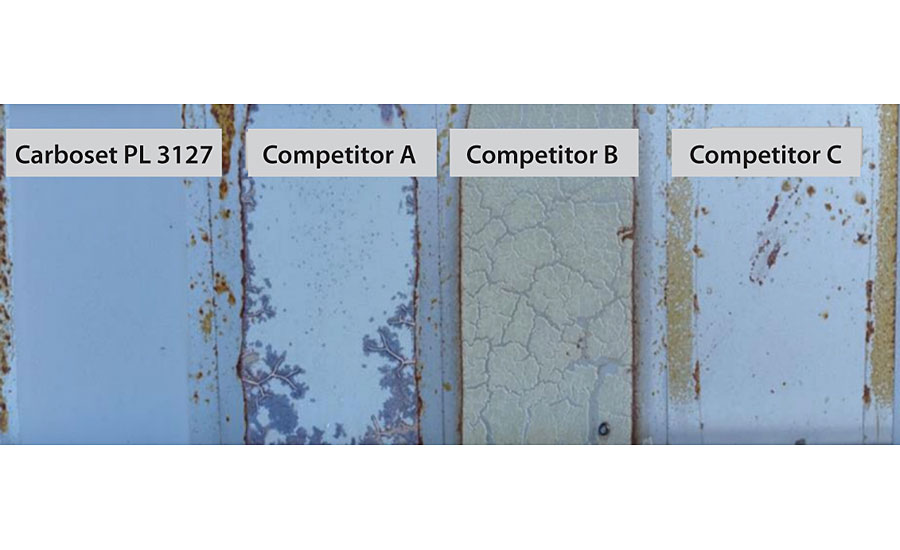
In addition to providing corrosion protection, coatings formulated with Carboset PL 3127 maintained peelability throughout a rigorous testing process. Figure 2 shows that after 1,000 hrs of salt spray exposure, the peel release was outstanding, and film continuity was strong during peeling.
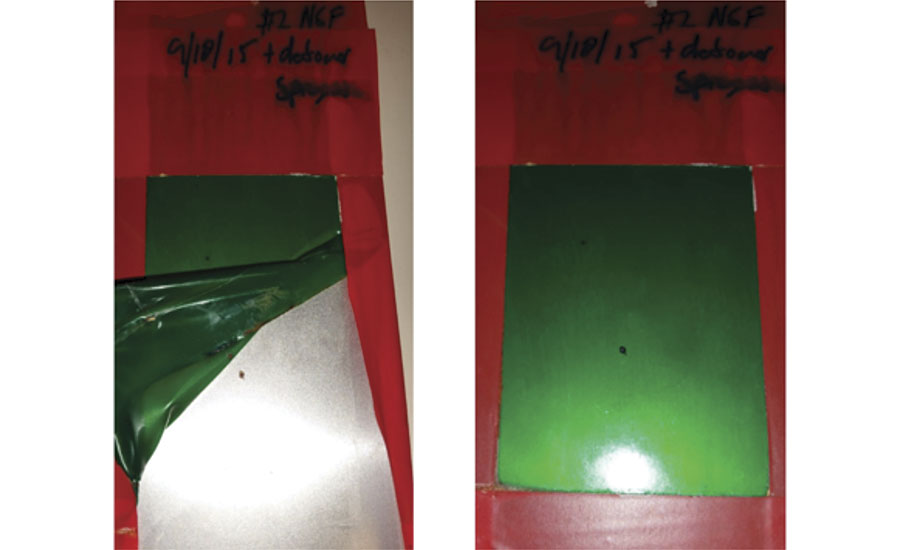
Outdoor Exposure – Northern Climate
Using ASTM D1014-09 test standards on cold rolled steel panels against other peelable coatings through extended exposure to harsh Ohio weather, the new resin demonstrated excellent durability and longevity (Table 1).
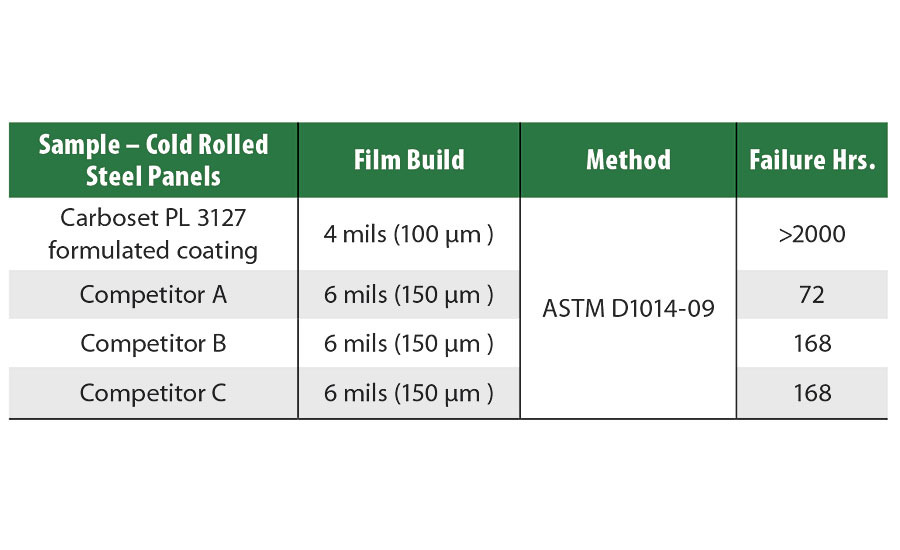
A Differentiated Resin Technology
New resin technologies offer the promise to bring specialty, value-added solutions to the marketplace. Carboset PL 3127 holds tremendous potential as a replacement for grease, oil and other temporary anti-corrosion materials. As a peelable resin for metal protection, the resin proves that it is possible to deliver a coating that provides the corrosion protection, scratch protection and chemical resistance of a paint, but with the easy removal of a peelable coating.
Do you have an opportunity where you think peelables could solve an anticorrosion challenge? Please contact your Lubrizol rep or visit www.lubrizol.com/coatings for additional information.
Looking for a reprint of this article?
From high-res PDFs to custom plaques, order your copy today!