Mineral Oil-Based Anti-Foaming Agents for Decorative Paint

Foam is a dispersion of gas bubbles in a liquid, which is formed by the presence of surfactants in the medium. In our everyday life we are accustomed to using products that foam up, such as shampoos or detergents, among others. Industrially, however, foaming is not always desirable, as it can cause a decrease in production yield and results in poor-quality finished products.
In the decorative paint industry, excess foam may cause an increase in production time, cause problems during packing and cause deficiencies in the final appearance of the coating. Thus, it is essential to use an anti-foaming agent that allows optimal control of foam formation during production stages and keeps its properties during storage. Thus, paint with a smooth finish that is free of craters and fisheyes can be obtained.
Choosing the appropriate defoamer for each formulation is imperative to ensure the quality of the paint. For this reason, it is necessary to study in detail the behavior of such additives by means of tests that allow us to predict their defoaming effectiveness, persistence and potential incompatibilities.
A range of anti-foaming agents called EMULTROL DFM OLM has been specifically formulated to achieve a persistent defoaming effect with the best cost effectiveness. One of the flagship products in the range of defoamers is EMULTROL DFM OLM-17, which is particularly suitable for controlling foam in decorative paints.
Study Methodology
For the evaluation of the properties of this defoamer we conducted tests of efficiency, stability and compatibility, using four kinds of polymer dispersions as a medium: acrylic, styrene-acrylic, vinyl-acrylic and vinyl-ester, which are the main bases for most decorative paints currently used.
To determine the defoaming effectiveness, 0.2% of EMULTROL DFM OLM-17 was added to 200 mL of polymer dispersion and then agitated at 1,300 rpm for 5 min. Afterwards, the percentage of air in the mixture was calculated by measuring changes in its density (Figure 1).
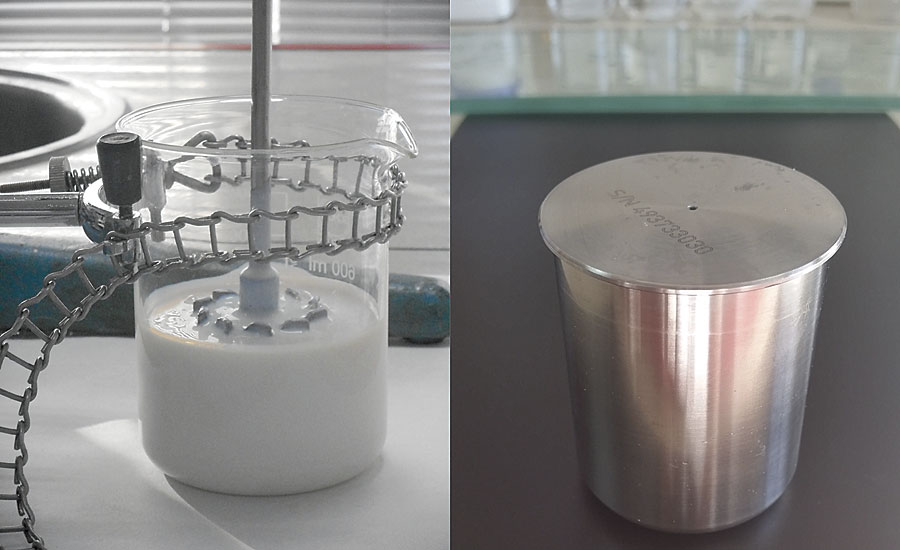
Another parameter to take into consideration is the formulation stability that a defoamer presents over time. For its study, a sample of polymer dispersion with 0.2% of defoamer was stored at 45 °C for one week. Subsequently, the defoaming effectiveness test was repeated.
Finally, to make sure that the tested defoamer does not present problems of compatibility with formulations, which would cause adverse effects such as fisheyes, craters or orange peel, a120-microns-thick layer was applied on a glass plate and visually assessed.
Results
Figures 2 and 3 show that EMULTROL DFM OLM-17 has a good defoaming effectiveness in the four polymers studied, which remain virtually unchanged over time. In addition, we note that this product does not cause any irregularity or defect in the final coating of the aforementioned polymers.
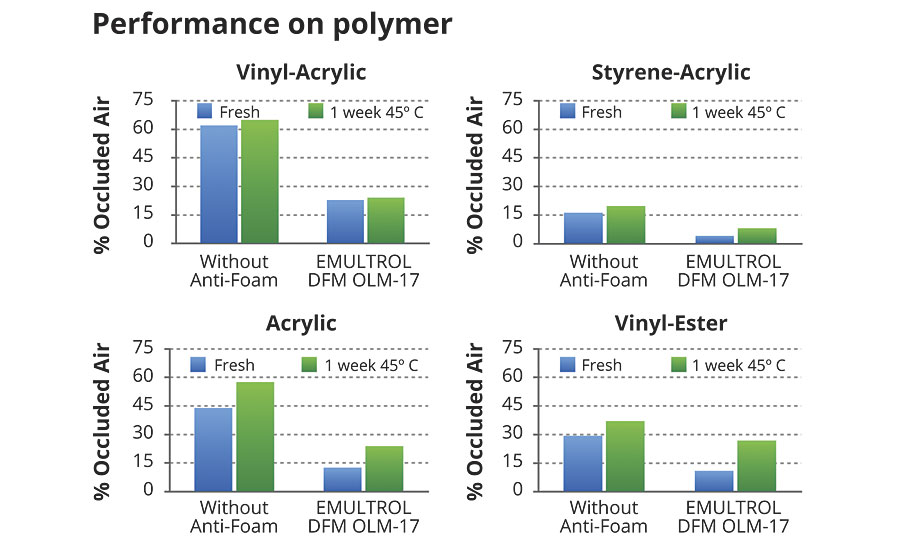
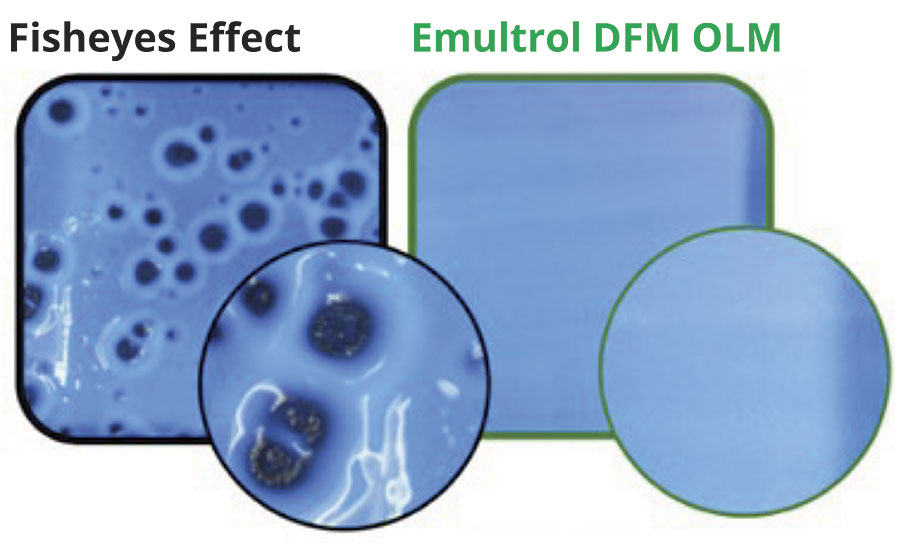
Therefore, we can conclude that EMULTROL DFM OLM-17 is a cost-effective defoamer that is suitable for the production of a wide variety of decorative paints, especially those based on polymeric dispersions such as acrylic, styrene-acrylic, vinyl-acrylic and vinyl-ester.
Conclusion
EMULTROL DFM OLM-17 is formulated from high-quality mineral oils and does not contain alkyl phenol ethoxylates. Properties include:
- Easy to handle;
- Stability during storage: no phase separation is observed;
- Excellent cost-effectiveness;
- Excellent defoaming efficiency;
- Good long-term performance;
- Appropriate compatibility: does not cause adverse effects on the paint such as orange peel, fisheyes, craters or wetting defects;
- Excellent foam reduction in paints based on polymer dispersions of acrylic, styrene-acrylic, vinyl-acrylic and vinyl-ester types.
Keep in mind that every formulation is unique and may require the use of specific defoamers to ensure optimal results.
Looking for a reprint of this article?
From high-res PDFs to custom plaques, order your copy today!