New Range of Ecological Anti-Foaming Agents

Credit: phongphan5922, iStock / Getty Images Plus, via Getty Images
Anti-foam products allow controlling the presence of unwanted foam in different processes, including the manufacture and application of paints.
One of the most critical foaming steps in paints is the grinding phase. During the grinding of paints, equipment that generates high-shear forces is used in order to obtain a homogeneous distribution of the particle size of the fillers. Although the equipment is usually designed to reduce foaming, some entrapped air is unavoidable. Another phase where foam tends to cause deviations in the production system is during packaging, where the decrease in the density of the paint, meaning the relationship between its volume and its weight, causes that the weight specifications cannot be reached due to excessive air content. During the application of paints, high-shear applicators such as spray guns or foam rollers promote the incorporation of entrapped air in the paint that can cause surface defects in the coating, such as craters, pinholes, or reduced gloss.
The usual approach to solving foam problems generally involves selecting the appropriate anti-foaming agent. The optimal anti-foam is usually established based on the characteristics of the process, the formulation and the type of foam generated in the paint, and whether it is macro- or micro-foam.
Traditionally, mineral oil-based anti-foams with hydrophobic foam-destroying particles have been used in the paint industry1. This class of anti-foams are generally the ones that offer the best ratio between anti-foaming effectiveness and cost, these two criteria being the ones that often turn out to be the most important when choosing the anti-foam. However, there is a growing tendency to consider ecological criteria as a fundamental requirement in the selection of raw materials.
In 2004, the European Union passed the 2004/42/EC paint directive2, limiting the presence of volatile substances in paints, varnishes and vehicle finishes. In 2014, it established the criteria for obtaining the ECOLABEL3, with which the final consumer is guaranteed that paints and varnishes with this label will have a minimum content of toxic substances, a minimum content of volatile and semi-volatile organic compounds (VOC and SVOC), and an assurance of paints and varnishes efficacy when used indoors and/or outdoors.
For this reason, at CONCENTROL we have designed a new range of mineral oil-free anti-foams, which are not harmful to humans or the environment due to their low or no toxicity, and the enhanced bio-degradability of the raw materials. They have been designed with a zero content of VOC and SVOC (volatile and semi-volatile organic compounds) emission gases that can pollute air quality and be harmful to the atmosphere. From the point of view of efficacy, they improve anti-foaming effectiveness compared to traditional anti-foams based on mineral oils. The new range of anti-foam agents comply with the European Union regulation 10/20114 that lists the allowed raw materials to be used in materials and plastics for food contact applications, making them a suitable and compliant option for applications such as coatings intended for food packaging.
In short, they are antifoams designed to be the best in terms of quality/cost/ecology ratio.
Presentation
The new range of environmentally friendly anti-foams EMULTROL DFM is made up of the following references, which are compared in the following table with two traditional anti-foams based on mineral oils.
The new formulated anti-foams EMULTROL DFM OLV-24 and EMULTROL DFM AFO-24 are based on vegetable oils, and the newest EMULTROL DFM OLV-25 and EMULTROL DFM AFO-25 are based on ecological oils. In the experimental part, further performance tests will be shown to verify how these new formulations perform in efficiency as anti-foam and compatibility in test paint applications. High quality raw materials have been chosen to ensure that the formulation, as a whole, can be used in the most sensitive applications such as the formulation of paints and coatings suitable for food contact. In addition, its composition is optimal to be used in paints and coatings that seek to comply with the most demanding ecological certifications such as ECOLABEL or Nordic Swan5.
Comparative Study
To evaluate the anti-foam efficacy of these new products, effectiveness, stability, and compatibility tests have been carried out in Concentrol's application laboratories, using as test medium, standard water based polymeric dispersions of the paints and coatings industry, such as styrene-acrylic polymer, acrylic, vinyl-veova, and ethylvinylacetate.
Anti-Foam Performance Test
To evaluate the anti-foam performance, a 200 ml sample of polymeric dispersion is taken in a beaker, 0.2% of the anti-foam to be tested is added, and a stirring process is undertaken at 1300 rpm for 5 minutes. The percentage of entrained air is obtained by calculating the difference in the measured density between the initial density of the dispersion and its final density after the test. The preparation is aged in an oven at 45 °C for one week, afterwards the test is repeated to determine the performance stability of the anti-foam during the aging. This last process allows us to evaluate the stability of the anti-foam effect throughout the shelf life of the paint.
Results and Discussion
Further results of the anti-foaming performance tests in the different test media are shown. A lower % of entrained air indicates a greater anti-foam effectiveness.
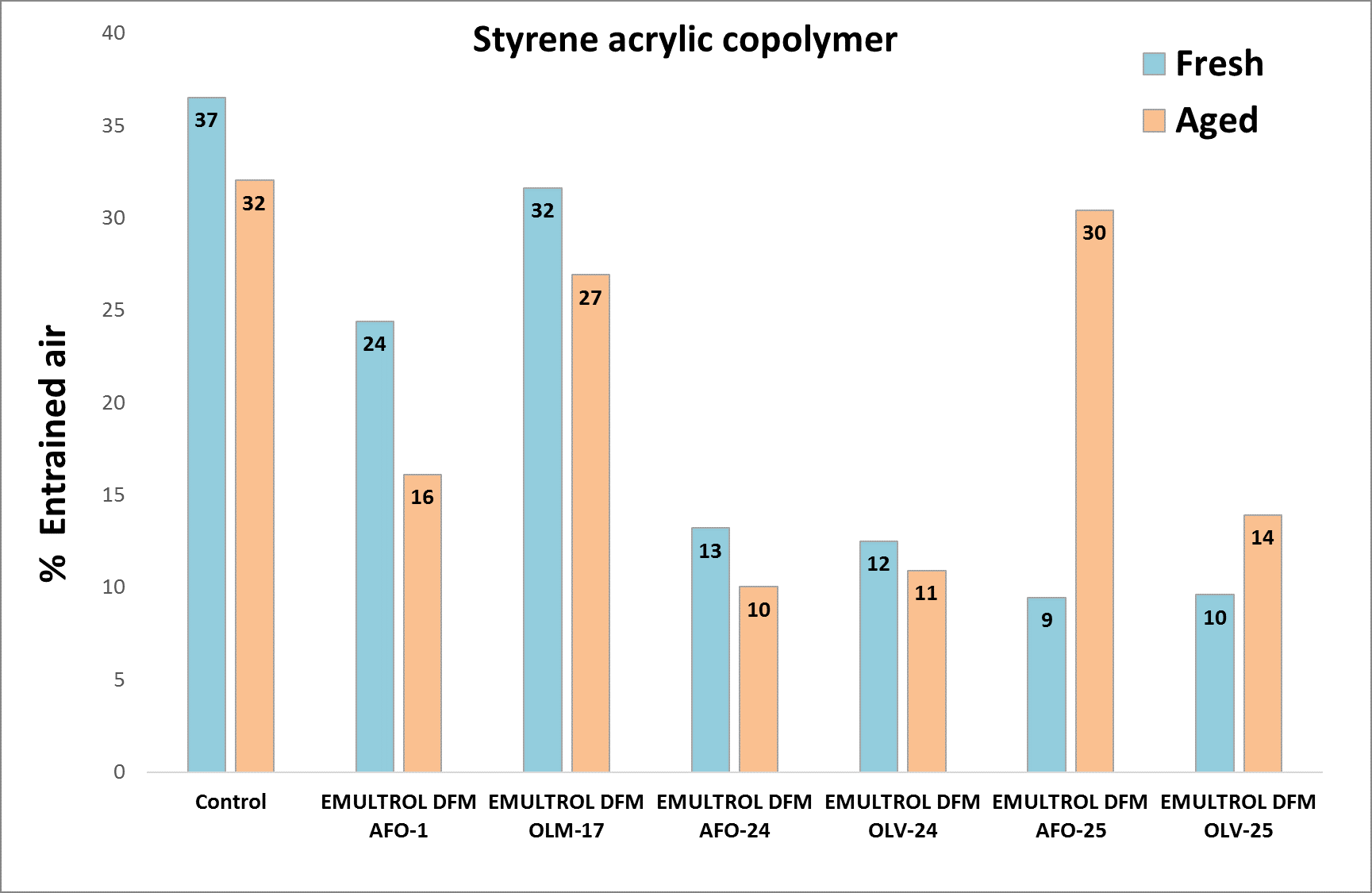
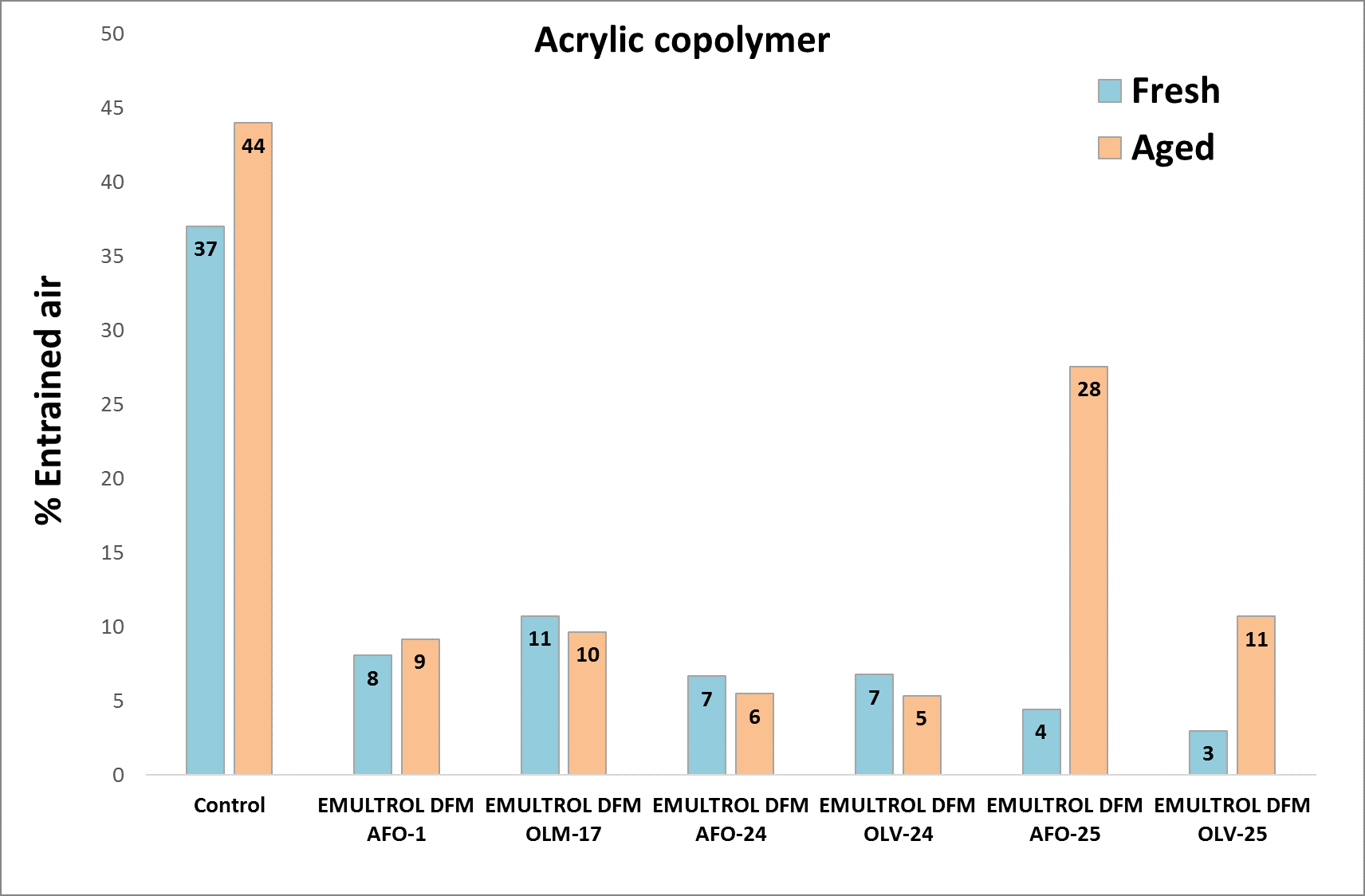
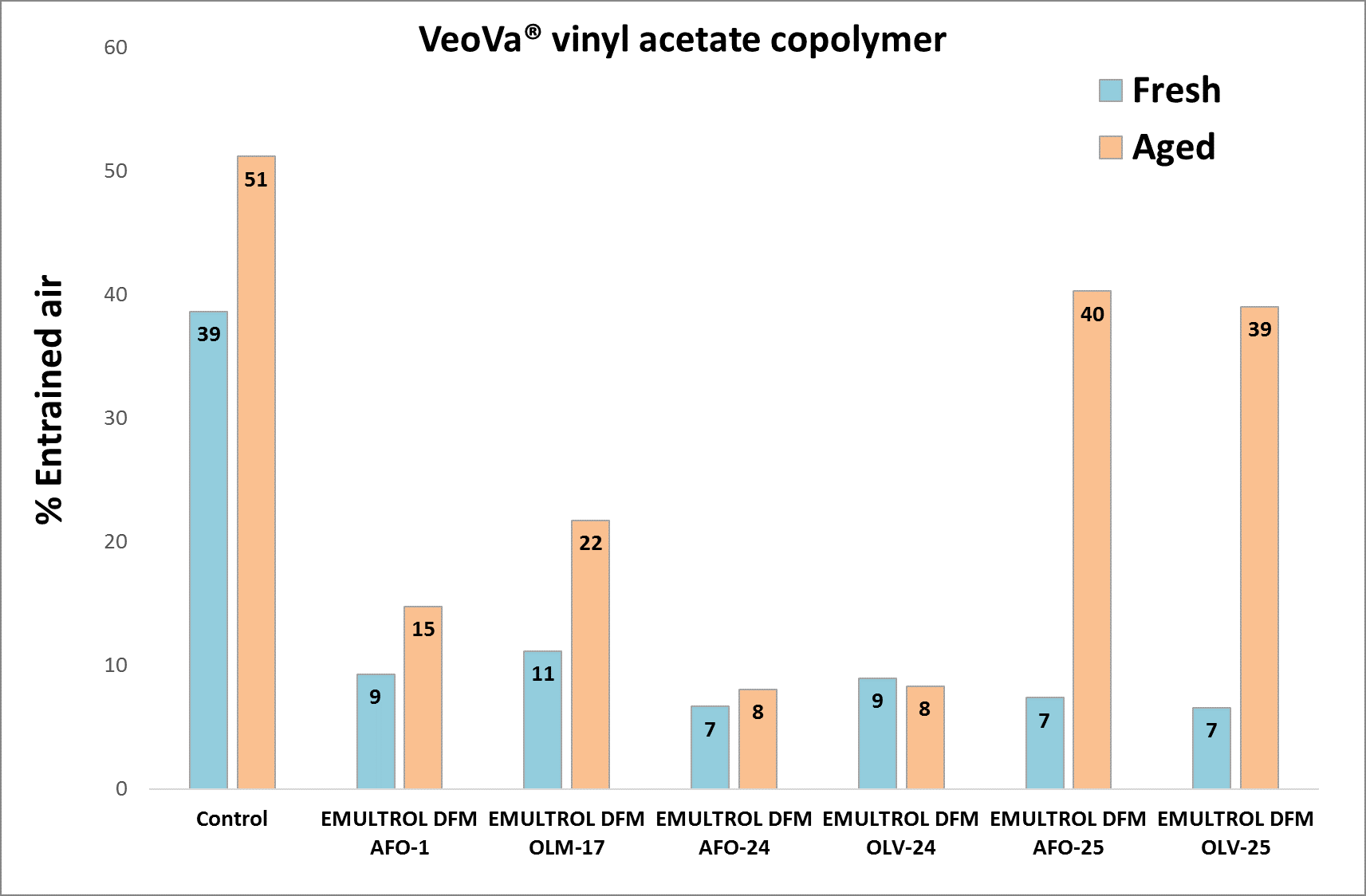
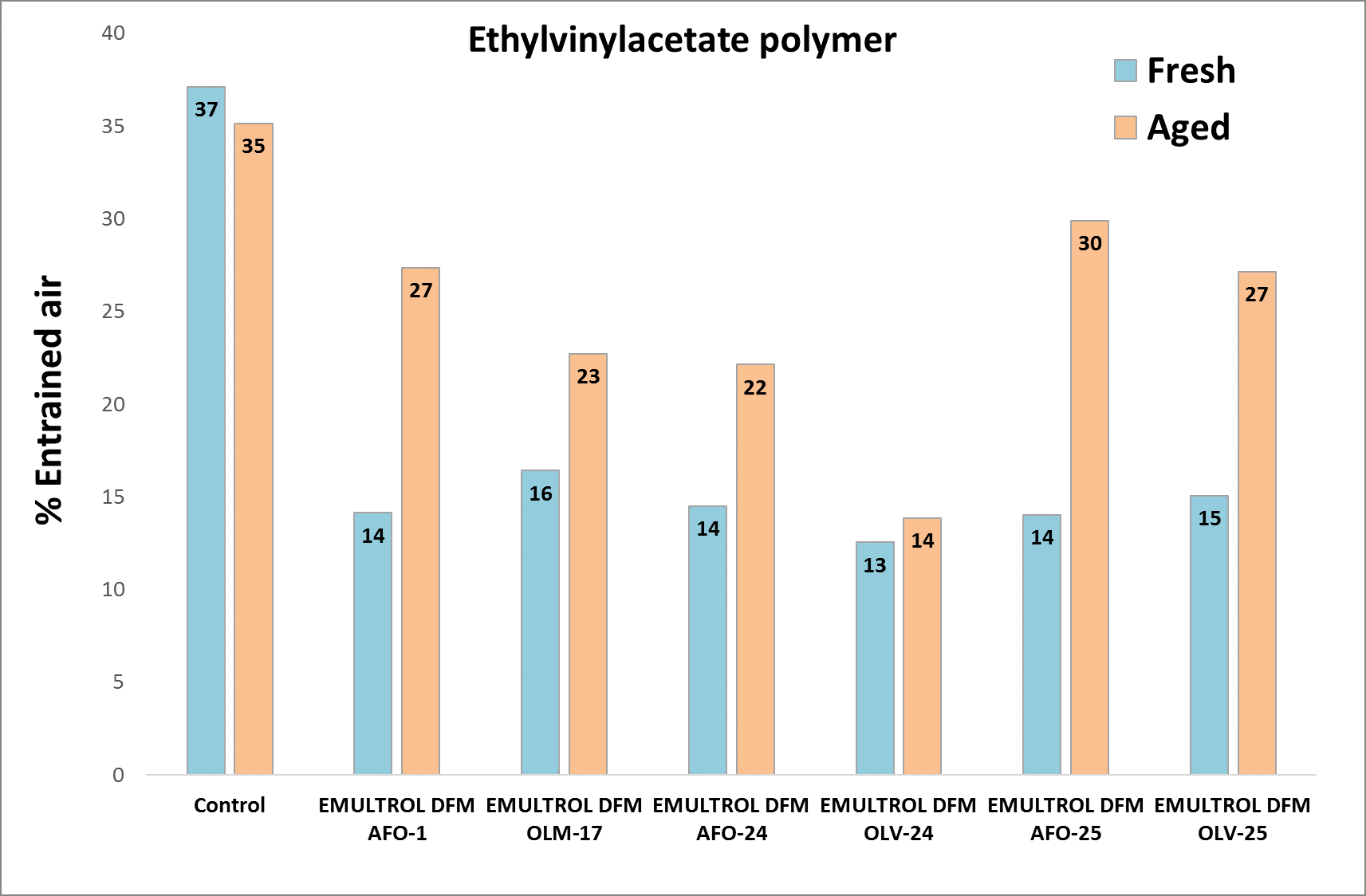
It can be seen that ecological anti-foams show a better performance in terms of anti-foam effectiveness than traditional anti-foams. In polymeric dispersions such as styrene acrylic, they can de-aerate between twice and three times as much entrained air as traditional anti-foams. It is observed that the references EMULTROL DFM OLV-24 and EMULTROL DFM AFO-24 present an increased persistency of the anti-foam effect against aging. While the EMULTROL DFM OLV-25 and EMULTROL DFM AFO-25 references show a slightly better immediate anti-foam performance, their aged performance is comparatively worse.
Anti-Foam Compatibility Test
The compatibility of the studied anti-foam preparations with the different polymer dispersions is evaluated in order to verify that the anti-foam does not cause quality problems such as fish eyes, craters, or orange peel in paint application. For this purpose, an application of the preparations of polymer dispersions, with a Mayer-type spiral bar, of 25 micrometers depth, on a LENETA® cardboard support, has been tested.
Figures 2, 3, 4, and 5 show the compatibility tests of the polymer dispersions, showing examples of each of the new references in comparison with their traditional anti-foam equivalent. It can be seen that the finished coatings containing anti-foams are generally better or similar to the finish of the control test. A trend is observed where preparations with less entrained air % show a better coating and levelling, resulting in a more homogeneous finish.
Conclusions
A new range of ecological anti-foams has been developed as an alternative to mineral oil based anti-foams, showing an equal or better anti-foaming performance for applications in architectural paint formulations. In addition, they have an excellent compatibility with most of the standard paints on the market. And last but not least, they are designed for the most sensitive applications, fulfilling the most demanding ecological and food standards in the paint and coatings sector.
References
1. Maurice R. Porter. (1992). Antifoams for Paints. In P. Garret (Ed.), Defoaming: Theory and industrial applications (p. 269-297). Boca Raton: Taylor & Francis Group.
2. DIRECTIVE 2004/42/CE OF THE EUROPEAN PARLIAMENT AND OF THE COUNCIL of 21 April 2004 on the limitation of emissions of volatile organic compounds due to the use of organic solvents in certain paints and varnishes and vehicle refinishing products and amending Directive 1999/13/EC. https://eur-lex.europa.eu/legal-content/EN/ALL/?uri=CELEX%3A32004L0042
3. 2014/312/EU: Commission Decision of 28 May 2014 establishing the ecological criteria for the award of the EU Ecolabel for indoor and outdoor paints and varnishes. https://eur-lex.europa.eu/legal-content/EN/TXT/?uri=CELEX:32014D0312
4. Commission Regulation (EU) No 10/2011 of 14 January 2011 on plastic materials and articles intended to come into contact with food. https://eur-lex.europa.eu/legal-content/en/TXT/?uri=CELEX%3A32011R0010https://www.nordic-ecolabel.org/product-groups/group/?productGroupCode=096
6. No other additives have been used, except of the antifoam agent, in order to improve the levelling, the wetting or other quality aspects of the coatings shown in the compatibility test of figures 2-5.
Looking for a reprint of this article?
From high-res PDFs to custom plaques, order your copy today!