Gloss Control of Powder Coatings
by Engineered Mineral Fillers

The success of powder coatings over the last decades can be attributed to several advantages that this technology offers in comparison with traditional solventborne systems and the newer technologies such as high solids and water-based formulations, including no VOC emissions, minimal loss of material (recycle of overspray possible) and no waste water.
Powder coatings are used in both indoor and outdoor applications and in a very broad range of gloss levels (from high gloss, through silk or egg-shell gloss, to dead-matte). Generally, amongst other things, the gloss level depends on the coating thickness and the loading level of the filler(s). Apart from the loading level, the level of gloss is strongly affected by particle shape, particle size and the particle size distribution (PSD) of the filler(s). The topcut (D97) and the average particle size (D50) in cumulative PSD are normally used to characterize the PSD of the filler.
In outdoor applications, precipitated barium sulphate, natural barium sulphate (barite) and aluminum trihydroxide (ATH) are used as chemically inert functional fillers. Fillers with very small sized particles are used to achieve high gloss levels. With increasing particle size, the gloss level will drop. When the target is to achieve dead-matte finishes, the role of fillers becomes smaller, yet still important. Dead-matte finishes can be achieved by combining incompatible binders, but the fine-tuning of the gloss level is still done by using fillers (such as barium sulphate and ATH) and waxes.
The use of waxes, however, has disadvantages. Besides the high cost of waxes, problems in processing and application may arise from the use of such additives, such as excessive slip, bad overcoatability and bad adhesion of sealants (in case of window frames). Gloss control and matting without such problems is achieved in a technically and economically more attractive way by using barite (combinations) and/or ATH (combinations) with specially designed PSD.
Under the trade names Portaryte B and Portafill A, Sibelco offers very pure, natural white barites and synthetic aluminum trihydroxide with engineered PSD to suit different customer requirements. Table 1 shows the basic properties of each product.
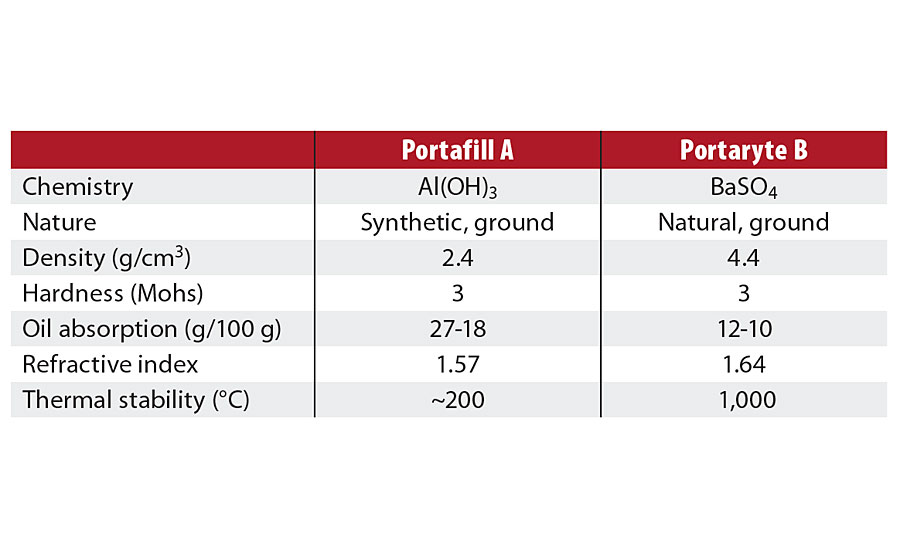
The Basics
The main advantage of barium sulphate is its excellent chemical inertness and the very low binder demand, resulting in highly durable coatings with good flow and levelling properties. When the end product is sold by weight, the high density of barium sulphate (4.4 g/cm3) compared to other fillers is also a clear advantage. However, sometimes it is a disadvantage in terms of covered surface area per kg powder. In such cases, aluminum trihydroxide (ATH) with density of 2.4 g/cm3 is used. In addition, ATH performs significantly better in terms of water spotting or blanching reduction as compared to barium sulphate.
The density is also an important parameter when replacing barium sulphate by ATH, or vice versa. It is worth keeping in mind that it has a clear impact, not only on the density of the paint, but also on the relative volume of the filler in the formulation. Because of the change in volume of the fillers, the Pigment Volume Concentration (PVC) of the paint changes when the replacement of barium sulphate by ATH is done by weight. Depending on the size of this change, the PVC can come close to the Critical Pigment Volume Concentration (CPVC), or even become higher than the CPVC. The result in the latter case is a clear deterioration in the properties of the coating when cured (i.e. corrosion resistance, gloss level. Therefore, replacement of barium sulphate by ATH should always be done by volume instead of by weight.).
Particle Size Distribution
As mentioned previously, PSD of the filler can be used to control the gloss level of the coating. When comparing fillers with the same chemistry and produced using the same production process, the following statements are valid:
- The finer the product (the lower D97 and D50), the higher the gloss level that can be achieved.
- The coarser the product (i.e. the higher D97 and D50), the lower the gloss level that can be achieved.
Table 2 shows the different grades of Portaryte B and Portafill A currently available. Both Portaryte B40/10 and the newly developed Portafill A25/10 are produced using a different processing technique, resulting in an optimized PSD. With both these grades, one can achieve significantly lower gloss levels than one would expect based on the PSD data. Compared to our regular grades, Portaryte B40/10 and Portafill A25/10 allow formulators to: achieve lower gloss levels, or achieve similar gloss levels at lower loading levels; or reduce the wax content and still achieve the same low gloss level, avoiding the disadvantages of waxes, which include excessive slip, bad overcoatability, bad adhesion of sealants (in case of window frames) and high costs.
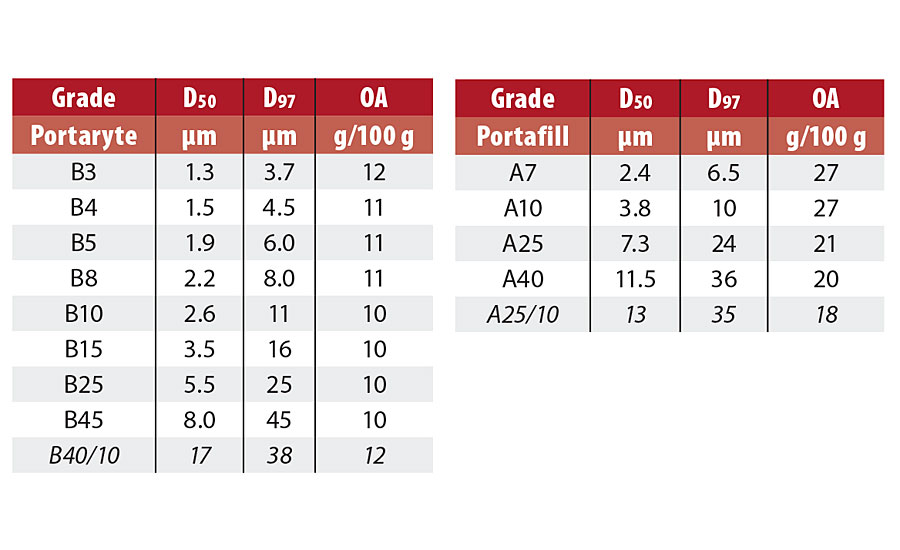
On top of the advantages mentioned above, Portafill A25/10 will enable formulators to: increase extruder throughput, because A25/10 has improved flow properties resulting in faster discharge from the loading hopper; and optimize the residence time inside the extruder, reducing the risk of pre-polymerization and associated formation of bits inside the extruder.
Testing
Two investigations were carried out with polyester-based powder coatings to demonstrate the versatility of the particle size distribution concept in the control of gloss.
Comparison of Portaryte B Grades in a Polyester Topcoat
The formulations shown in Table 3 were prepared and evaluated externally. After application and curing, the gloss was measured at 60°. The results in Figure 1 show that Portaryte B3 provides the highest gloss level, comparable to the performance of precipitated grades (Blanc Fixe). The coarser the grades (i.e. the higher D97), the lower the gloss. Portaryte B40/10 provides an additional step in gloss reduction. This is caused by the optimized PSD of this grade.
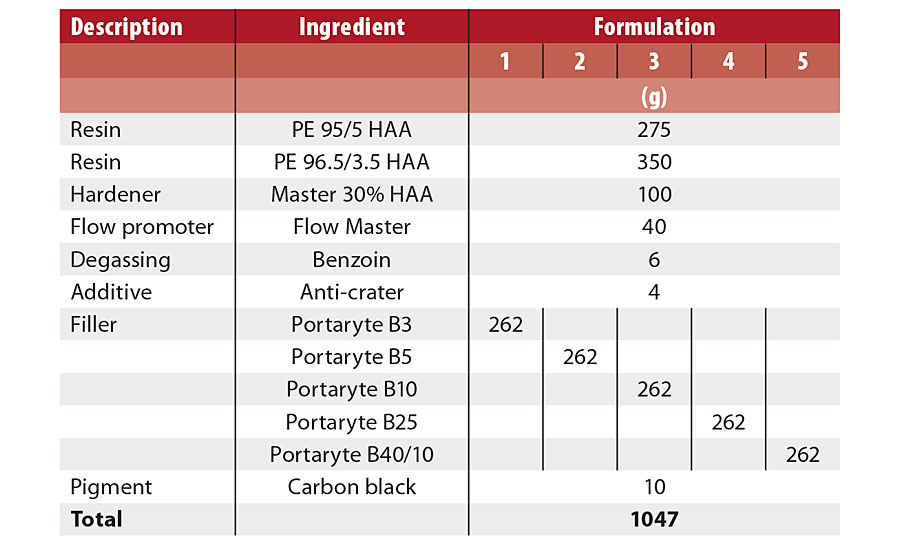
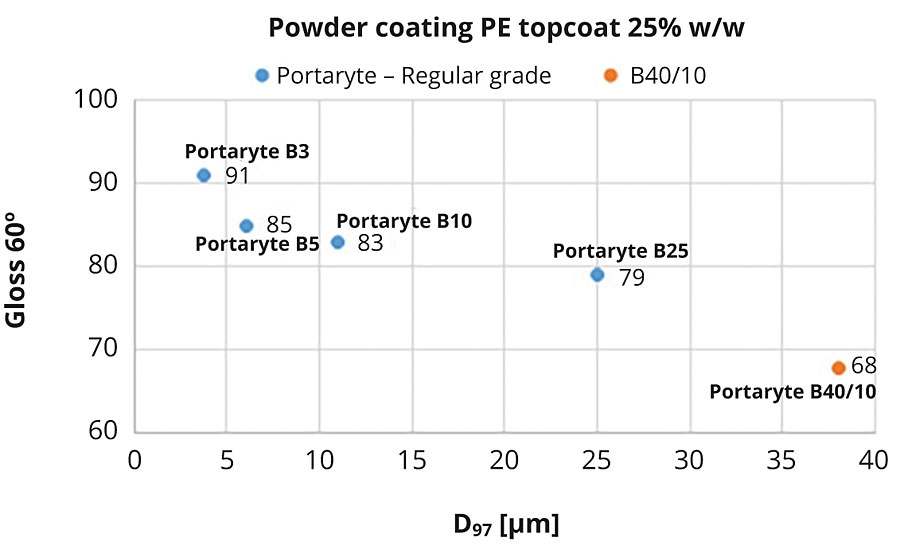
Comparison of Portafill A Grades in a Polyester Topcoat
A similar experiment was done with Portafill A, using the same volume of Portafill A versus Portaryte B compared to the previous experiment. Table 4 shows the formulations that were prepared and evaluated externally.
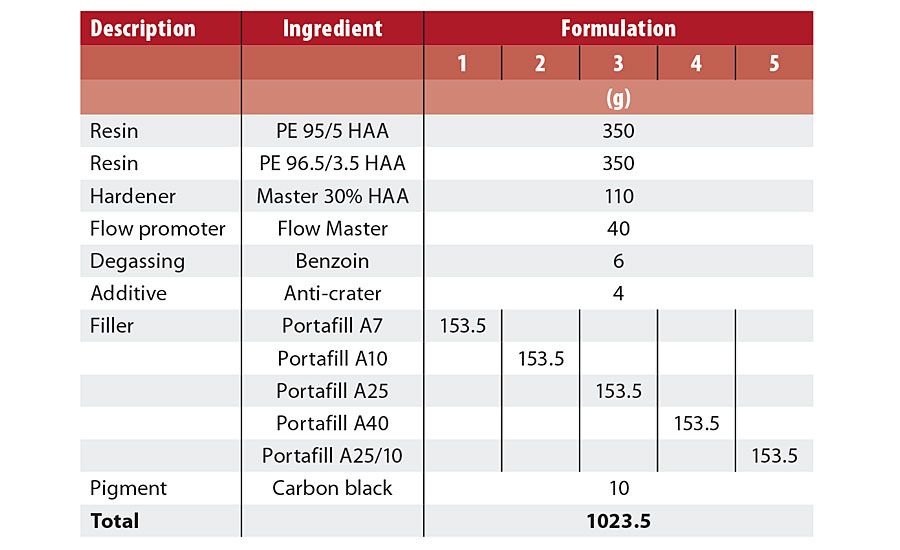
After application and curing, the gloss was measured at 60°. The results in Figure 2 show that Portafill A7 allows Sibelco’s ATH to be used in applications with high gloss requirements. Its gloss level approaches the gloss level obtained with the finest barite, Portaryte B3.
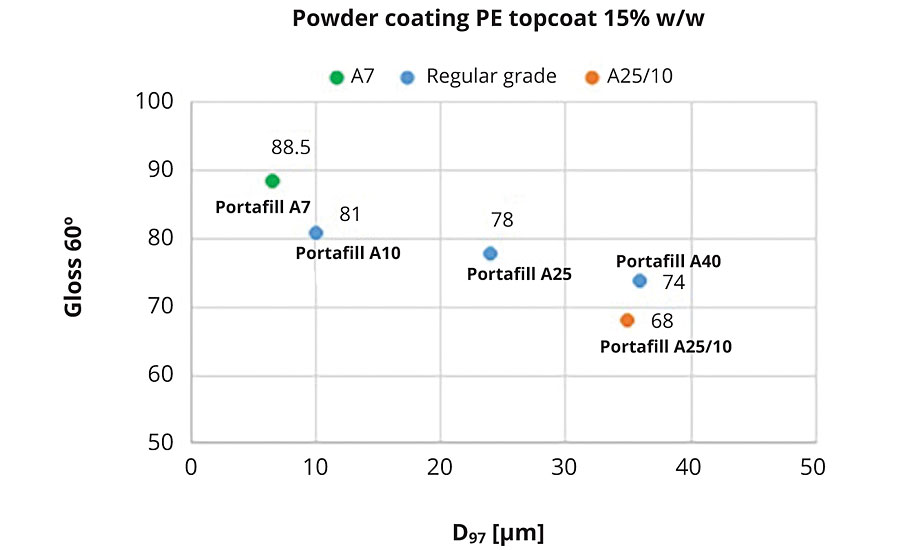
On the other end of the spectrum, Portafill A25/10 allows a reduction of 6 gloss units (-8%) when compared to Portafill A40, despite the slightly lower D97. Also in this case, similar to Portaryte B40/10, the specially optimized PSD is crucial to achieve this improved performance.
Conclusions
The use of barites is a proven method for accurate control of gloss in the high- to medium-gloss range. Portaryte B40/10 results in the best combination of matting and overall performance. The low gloss level is achieved without the use of matting waxes and avoids its disadvantages, e.g. greasy and slippery surface, irregular gloss, poor adhesion and overcoatability problems. Portaryte B3 is currently the most efficient barite grade in case high gloss levels are required.
ATH is the product of choice for gloss control when the relatively high density of barite is undesired, or in applications where improved resistance to water spotting is an issue. Portafill A7 is the finest grade available in Sibelco’s ATH product portfolio, and as a result offers the highest gloss levels. Portafill A25/10 is the product of choice for the best matting requirements. It allows formulators to:
- achieve lower gloss levels, or
- achieve similar gloss levels at lower loading levels, and/or
- reduce the wax content and still achieve the same low gloss level, avoiding the disadvantages of waxes, which include excessive slip, bad overcoatability, bad adhesion of sealants in case of window frames, and high costs.
- increase extruder throughput, because A25/10 has improved flow properties resulting in faster discharge from the loading hopper, and
- optimize the residence time inside the extruder, reducing the risk of pre-polymerization and associated formation of hard bits inside the extruder.
For more information, e-mail info@sibelco.com or visit www.sibelco.com.
Looking for a reprint of this article?
From high-res PDFs to custom plaques, order your copy today!