Gloss Control Powder Coating Resin
for Robust Manufacturing and Processing Efficiency

Since the introduction of powder coatings in North America in the 1960s, it has been growing as a popular environmental compliance alternative for metal surface finishing. By 2024, the global powder coatings market is expected to reach USD 16.55 billion. Powder coatings are used as decorative and protective coatings on many products we use daily, representing about 15% of the total industrial finishing market in the North America, with the estimated value of more than USD 1.79 billion. Powder coating producers and end users continue to specify powder coatings because of their excellent corrosion protection and outdoor durability to meet the rising demand of high quality and high film build. Powder coatings are also specified for their ease of achieving a wide range of color and texture finishes.
There are multiple resin technologies behind these coating systems, and they vary in their properties and performance characteristics. These resin types include epoxy, epoxy-polyester hybrid and epoxy-acrylic hybrids used for indoor applications. Polyester and acrylic technologies are used for outdoor applications. Acrylic technology is used for special applications. Polyester with acid functionality can be crosslinked with triglycidyl isocyanurate (TGIC) or hydroxyalkylamide (HAA), while polyester with hydroxyl functionality can be crosslinked with either blocked or unblocked isocyanate. Polyester resins are available in a standard and super-durable technology.
The matting of powder coatings for exterior durable application remains an ongoing challenge. Over the past few decades, this area has witnessed numerous innovative developments involving different techniques to achieve matting effects. Such approaches range from the polyester urethane and GMA acrylics to the dry-blend of two polyester resin systems. There is also the latest development through a one-shot matte technology using two carboxyl functional polyester resins with high and low acid values. All of these innovative approaches come with unique limitations such as manufacturing efficiency and reproducibility, additional manufacturing overhead due to the cost of dry-blend operations, use of two resins system, cross-contamination, poor mechanical properties, gloss stability after multiple reclaim cycles, high cost of isocyanate, batch-to-batch inconsistency, sensitivity to processing conditions, and sparkling effects.
It is in the light of these limitations that a new and novel technology using HAA coating is presented in this article for robust manufacturing and processing efficiency using a single resin system.
The Need for Matte Finish
Matte finish powder coating application has gained wide acceptance due to its physical and aesthetic properties. It is used to hide surface imperfections and impart a considerable amount of value to consumer products. It reflects less sunlight, thereby making the coating surface less visible. It provides a warm, softer appearance and is easy to touch-up. Matte finish powder coatings have a wide range of applications such as lighting fixtures, automotive trim parts, lawn furniture, architectural extrusion, office furniture, military application, glass bottles and sporting goods.
Market analysis suggest that these applications represent about 25-30% of total powder coating usage, which signifies roughly 500,000 MT globally. The key critical requirements for matte finish applications center around exterior durability, flow and mar resistance. There has also been an increasing obligation to meet global regulatory requirements. This necessity is the key, driving future developments toward TGIC-free, super-durable technology.
A Novel, Single-Resin, One-Shot Technology
The new generation of the novel gloss control outdoor polyesters for powder coatings is designed to advance manufacturing efficiency and reduce processing time. The technology is based on a single-resin β-hydroxyalkylamide hardened binder, which delivers outdoor-durable, low-gloss powder coatings that are reproducible and trouble-free. This single-resin, innovative approach comes with scores of benefits such as elimination of multiple steps and simplification of the paint-making process (Table 1), reducing batch time and increasing plant capacity, and a significant reduction in inventory and rework. This ease-of-use is bringing cost effectiveness and reduction in manufacturing cycle time for the coating producer.
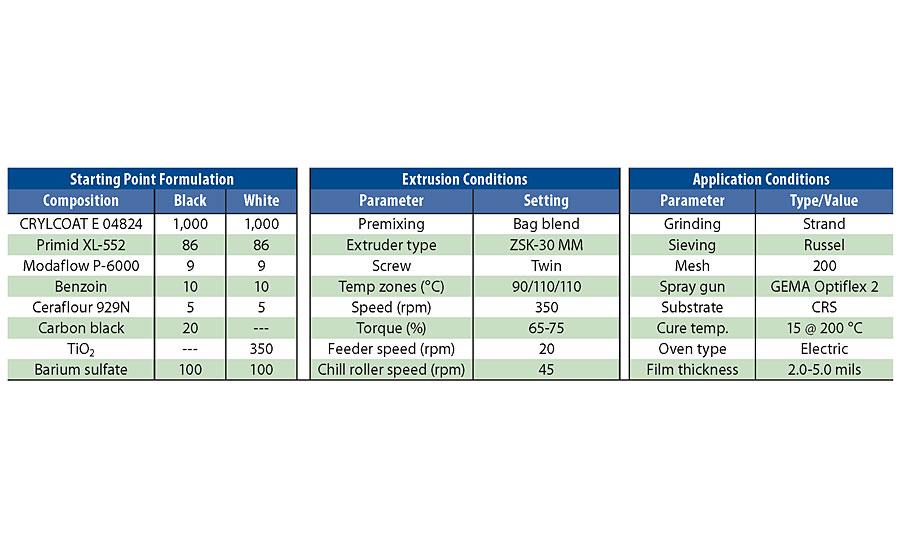
Dull-Matte (2-7 Units), One-Shot HAA Technology
The new technology requires conventional processing to achieve a consistent and reproducible gloss range. The amount of filler and the particle size distribution of the finished powder does not have drastic effects on the gloss. The gloss reduction capability is driven by the innovative engineering of the backbone of the polyester resin and its interaction with the β-hydroxyalkylamide hardener. This technology can be processed using both single and twin screw extruders, although we noticed more dispersion efficiency and gloss development with the twin screw extruder. Table 2 shows paint performance properties.
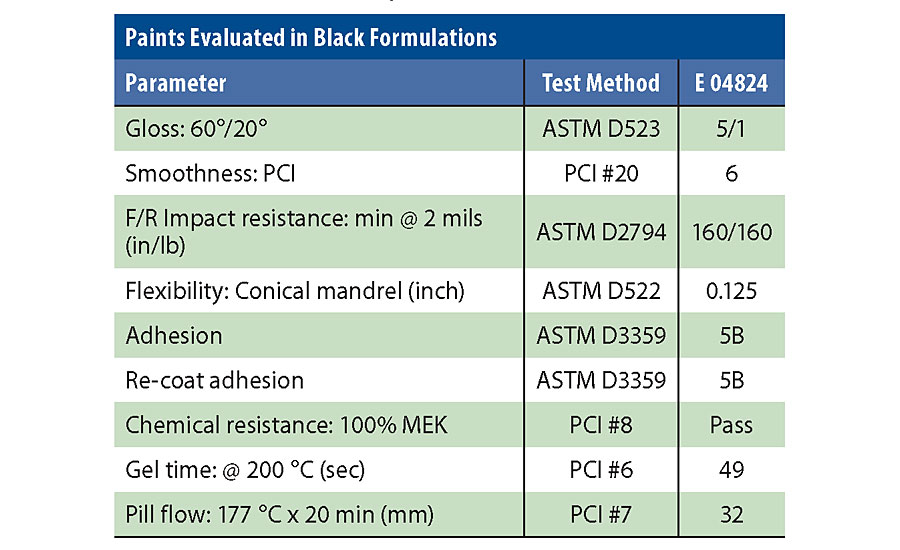
Robust Technology
Coatings based on this new technology give highly consistent gloss levels irrespective of extruder setting. The gloss levels are very stable when torque levels are varied at both low and high RPM. Similarly, the gloss levels are very stable when torque levels are fixed and RPM is varied (Figure 1).
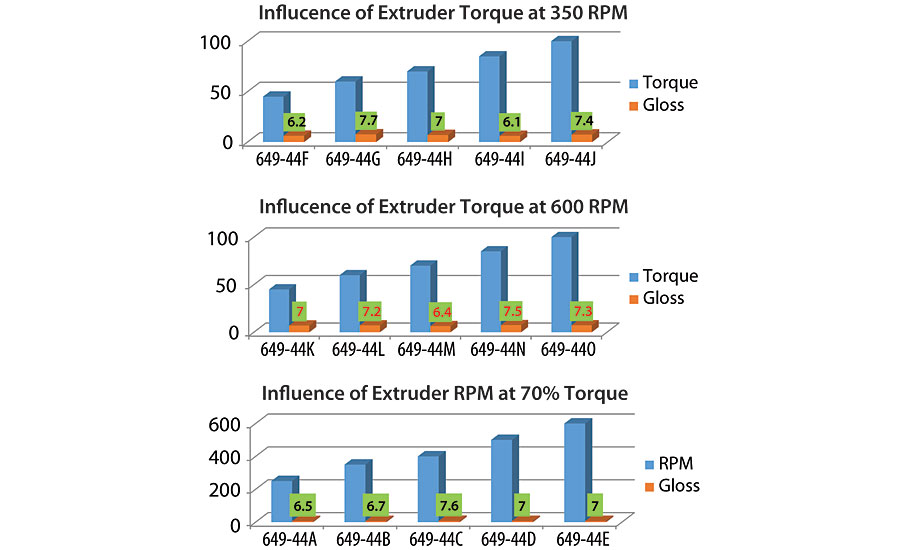
Furthermore, the gloss is equally stable when cured at temperature ranges of 180 C to 220 C for 10 min and 20 min (Figure 2). One of the industrial issues with matte finishes is the gloss variability after multiple extrusions (Figure 3). This novel technology has demonstrated greater stability in gloss and performance properties after triple extrusions.
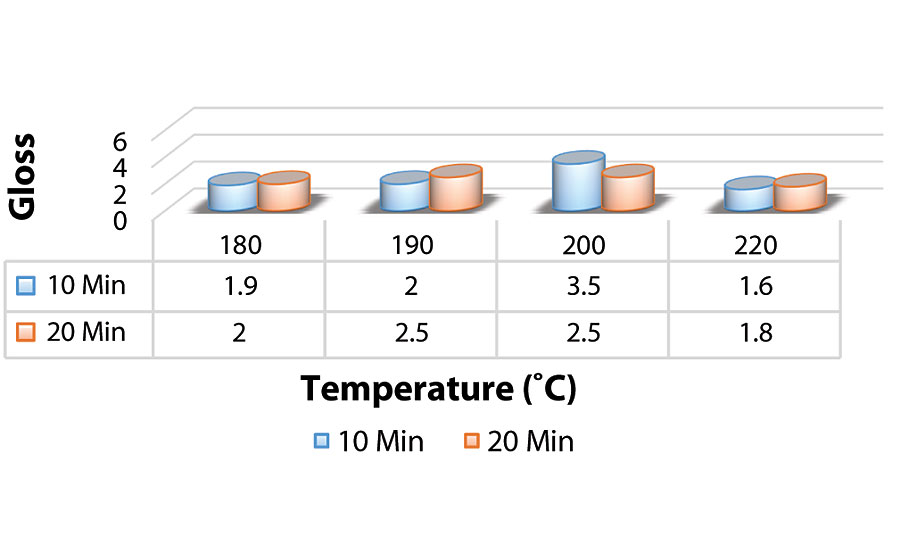
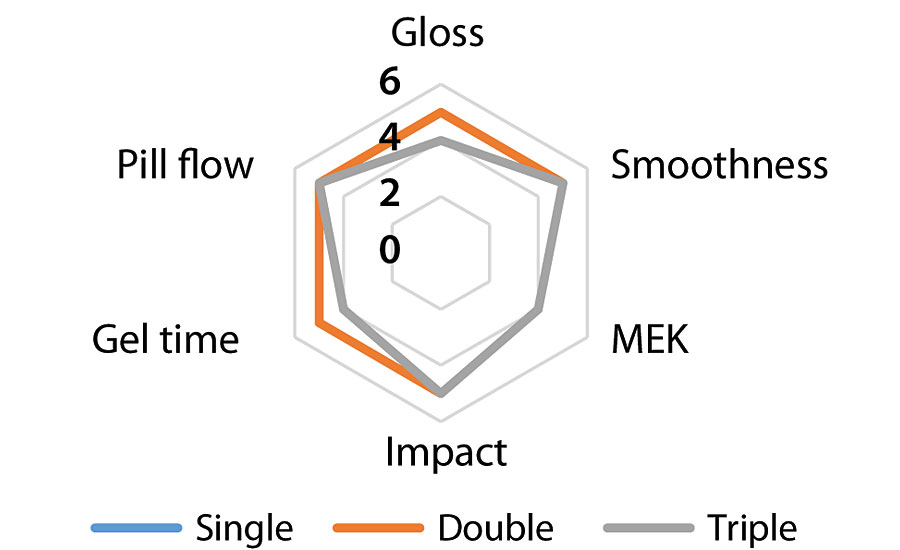
Gloss Adjustment Guidelines
The technology is designed to achieve gloss as low as 2 units. This gloss level can be modified to achieve up to 10 gloss units by following the gloss adjustment guideline (Figure 4). We recommend to limit adjustment under 10% using the novel resin CRYLCOAT E 04884. Our studies show that 10% adjustment will raise gloss by 4 GU. In order to balance the stoichiometric ratio of the system, we recommend adding the required corresponding ratio of the hardener.
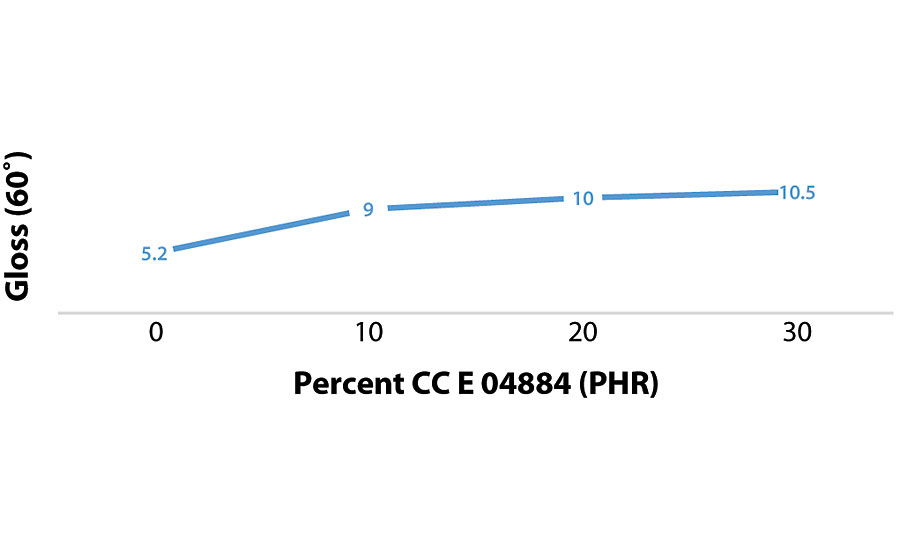
Storage Stability
Powder stability at room temperature after 49 days is good (Figure 5). Similar exposure at 35 C showed stable gloss over time, especially with the addition of a micronized polyethylene wax at the range of 0.2 to 0.5 percent of the total formulation.
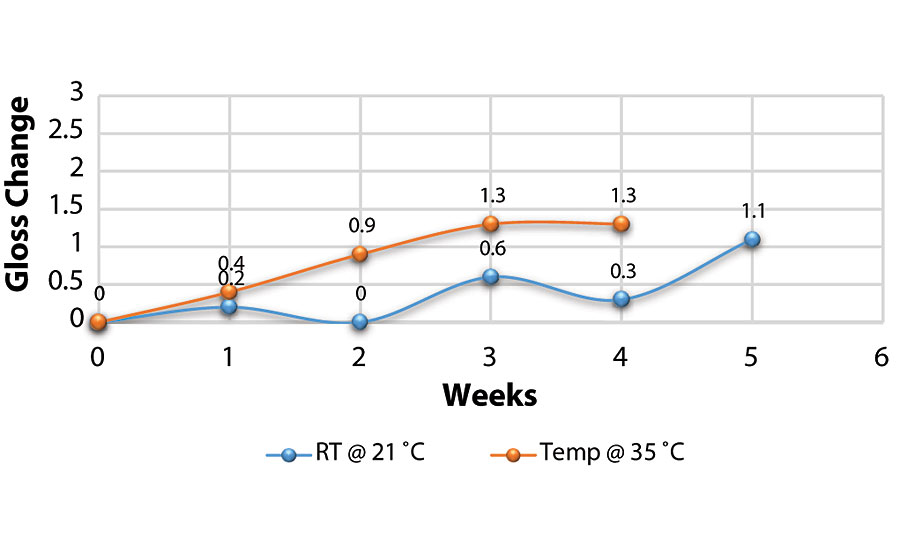
Weathering
The accelerated weathering test using the novel resin CRYLCOAT E 04824 showed that the coating has equal or better gloss retention than the traditional one-shot matte super-durable system (Figure 6). Florida natural weathering data of three primary colors are ongoing, but the historical data derived from the mother chemistry gives a high degree of confidence in the expected weathering performance of the new technology (Figure 7).
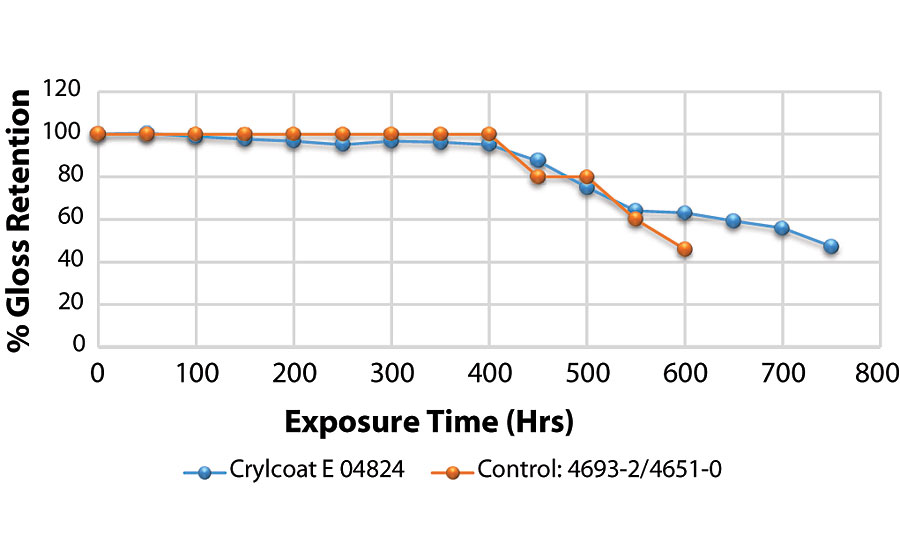
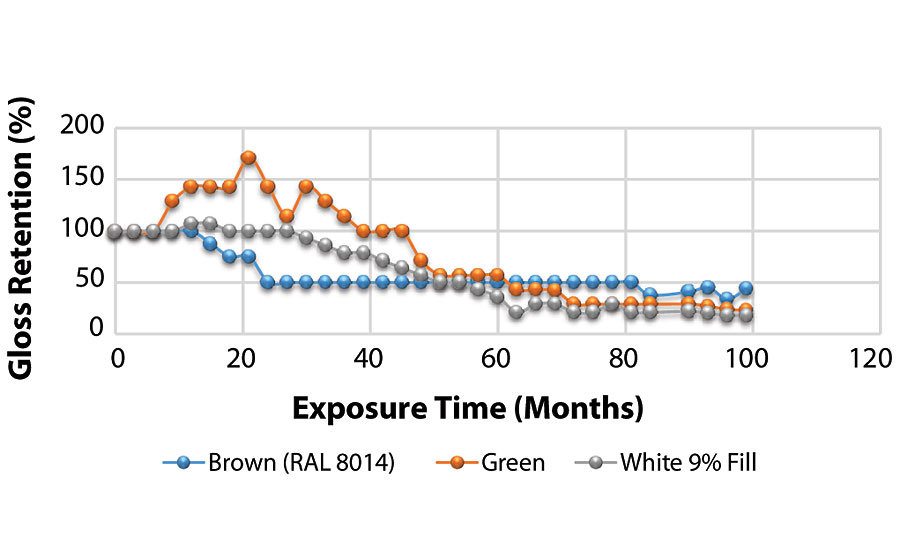
Further Development
Matte finish continues to be an ongoing development for allnex. We believe that the knowledge acquired in the development of this novel technology is transferable to the development of other difficult-to-achieve gloss ranges with improved flow properties that have consistently proven to be problematic to manufacture and reproduce. The goal is to meet flow properties equal or greater than PCI smoothness of 7. The area we will be focusing for our next development are the gloss ranges of:
- 10-20 units: CRYLCOAT E 04814
- 20-30 units: CRYLCOAT E 04884
For more information, visit https://allnex.com or https://lowglosspowdercoatingresins.com.
References
1. Powder coatings market size to reach $16.55 Billion by 2024, Grand View Research, 2017-03-07. {Online} Available: https://www.grandviewresearch.com/press-release/global-powder-coatings-market.
2. What is Powder Coating, Powder Coating Institute (PCI) 2016. {Online} Available: https://www.powdercoating.org/page/WhatIsPC.
3. Matting without mixing, European Coatings Journal 12/2009. {Online} Available: www.european-coatings.com/content/download/59461/669262/version/1/file.
4. Burnish Resistant, Ultra-Durable Matte Powder Coatings, Powder Coatings Institute (PCI), October 2, 2000. {Online} Available: https://www.pcimag.com/articles/83052-burnish-resistant-ultra-durable-matte-powder-coatings.
Looking for a reprint of this article?
From high-res PDFs to custom plaques, order your copy today!