A New Generation of REACH-Compliant Ketamine Epoxy Curing Agents

A new generation of ketamine epoxy hardeners are technically outperforming their analogous predecessors both during and after cure. This article examines why their unique combination of long pot-life, reduced hazard and fast thin-film cure speeds make them the ideal curing agents for the paint and coatings industry.
Traditionally, ethylene amines have been used as epoxy curing agents and can cross-link epoxy resins to form an infusible mass. However, their poor compatibility with conventional aromatic epoxy, inherent toxicological properties and low active hydrogen equivalent weights with subsequent low stoichiometric loading levels negates their use in modern formulated systems.
Many modification techniques are employed to enhance their performance, including reaction with carboxylic acids to generate amido-amine and polyamides, mannich bases, association salts, adduction, and for applications requiring high latency and fast thin film cure, ketamines.
Reversible Reaction
Ketamines are formed through the dehydration of a primary amine group with a ketone, as depicted in Figure 1. The process employed in the manufacture of this particular ketamine involves the reaction of 2 moles of MIBK with 1 mole of EDA.
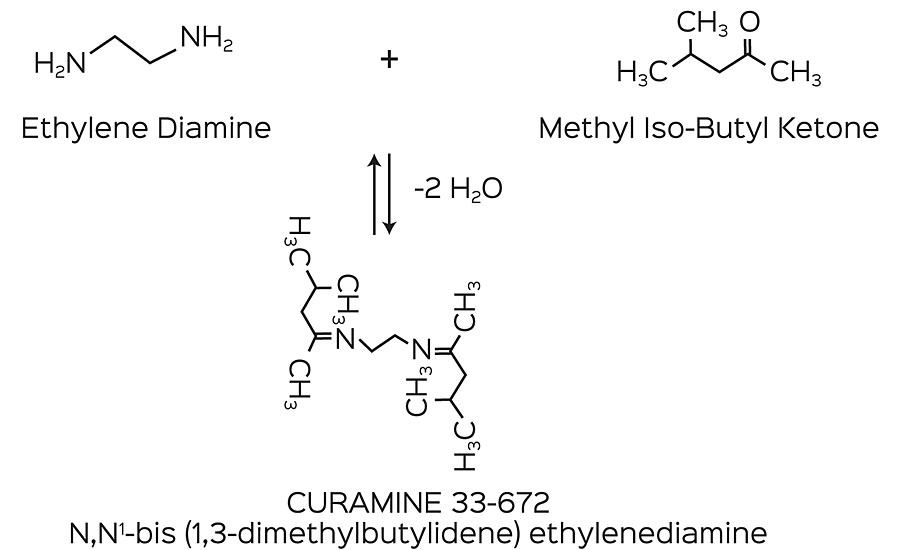
– Ethylene Diamine (EDA)
CAS 107-15-3
– Methyl Iso Butyl Ketone (MIBK)
CAS 108-10-1
Liberating 2 moles of water to form the reaction product:
– N,N’-bis(1,3-dimethylbutylidene)ethylenediamine
CAS 25707-70-4
The above ketamine is a former industry standard, but was withdrawn due to REACH (Registration, Evaluation, Authorization and Restriction of Chemicals) restrictions. This grade was one of a small series of ketamines employed in the formulation of high-stability, two-pack epoxy systems. These ketamines demonstrate stability, if not exposed to atmospheric moisture. As the reaction is reversible, when combined with the epoxy component and applied, the ketamine is hydrolyzed, liberating the functional amine and ketone components. The regenerated ketone is a volatile released from the film, and the original amine has active hydrogen groups that can react with the epoxy component in a conventional manner.
The product above is hydrolyzed to liberate ethylene diamine, which then in turn reacts with the epoxy. EDA is a relatively fast curing agent, but by generating the ketamine the reaction is retarded, requiring the hydrolyzation to occur before the epoxy-amine reaction proceeds. Ketamines provide excellent pot-life while also retaining fast thin-film cure speeds, making them quite unique.
The homologous series of ethylene amines with terminal primary amine groups, of which EDA is the basic member, allows a series of ketamines to be produced. These products have offered some desirable performance properties, but the liberated amines are generally of a low molecular weight with high vapor pressures. Concern over their toxicity and the costs attributed to REACH registration of each new ketamine species essentially led to the withdrawal of these conventional ketamines from circulation in Europe.
This withdrawal and the resultant void in the marketplace led to Bitrez recently developing a new range of REACH-compliant ketamines to satisfy the market demand. In addition to generating REACH-compliant products, it was opportune to rectify some of the other less-favorable characteristics and refine the products while maintaining the desirable pot-life/reactivity features associated with this class of curing agent. The new series of ketamines are offered as solvent cut or solvent-free materials, although all of them liberate some solvent during the hydrolysis process.
New Ketamine Grades
First and foremost, the new series of ketamine grades was developed to be REACH compliant and available for use in Europe. Additionally, improvements in the following properties were targeted;
- Reduced free amine in supply product,
- Reduced free amine during application (when hydrolyzed),
- Improved compatibility,
- Improved surface appearance,
- Maintain pot-life and cure properties.
Looking at these target requirements, and using conventional grades and regulatory standards as benchmarks we can demonstrate the improvements made.
Reduced Free Amine
The conventional grades are processed from EDA and DETA (Di Ethylene Tri Amine), the next grade in the aforementioned homologous series.
Following the introduction of GHS, the threshold limits and reporting requirements for free monomer levels have been adjusted, and the escalating hazard rating for free DETA is as follows:
Conventional ketamine requirements (context of amine)
- H302 (Harmful if swallowed)
- H330 (Fatal if inhaled)
- H314 (Causes severe skin burns and eye damage)
- H317 (May cause an allergic skin reaction)
- H335 (May cause respiratory irritation)
In the case of the conventional DETA-derived ketamine, the free monomeric DETA on supply generally falls within the 2-5% range, varying slightly based on the specific supplier and their specification, and the subsequent storage conditions.
One version of the new ketamine epoxy curing agent range has been formulated so that the initial free DETA level is <0.2% as supplied. The label requirements based on free monomers on supply is detailed in Table 1.
New Ketamine label requirements [context of amine] EUH 208: contains 2,2 iminodiethylamine. May produce an allergic reaction.
Reduced Free Amine During Application (when Hydrolyzed)
With exposure to moisture, the reaction liberates further DETA for reaction purposes. The conventional ketamine reversal reaction liberates approximately 35% monomeric DETA. The same grade mentioned above formulated with an initial free amine level <0.2% as supplied when hydrolyzed still liberates <2% monomeric DETA compared with 35% from the conventional grade. The associated hazard rating is detailed in Table 1 below.
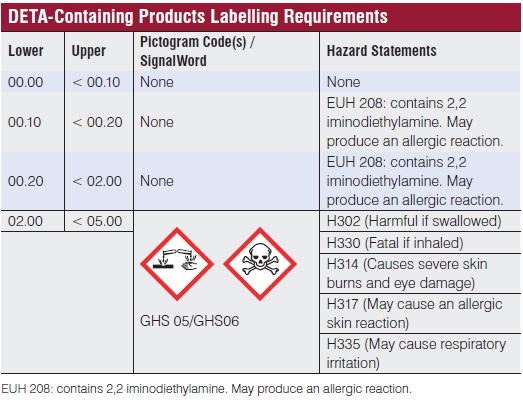
The fact that the amine is formed during the reversal reaction means consumers and formulators may be left with technical and moral dilemmas regarding label requirements/advisory information, as clearly the product supply label for a conventional ketamine is based on the free amine as supplied. However, knowing that on application the product hazard increases (albeit only until such time as crosslinking occurs/completes), the label may warrant explanatory discussions with applicators who may become exposed to a product listed as potentially being fatal on inhalation.
The new ketamine curing agents have low-supply free amine levels and low free amine levels following hydration, so they remain more consistent in terms of the hazards associated with corrosive amines. Of course, in either case the products liberate the solvent as a volatile component.
Improved Compatibility and Improved Surface Appearance
Through reaction with atmospheric humidity, this new generation of ketamine curing agents is less prone to the problems associated with humidity during cure. Whereas conventional ketamines, when hydrolyzing, liberate ethylene amines that are prone to compatibility issues with conventional epoxy resins; this can lead to surface migration or exudation of free amine to the coating surface. Surface migration of amines can cause at best reduced gloss or in some cases tacky/greasy surfaces, which in turn result in “amine blush” or “amine bloom”. These two phenomena are well documented, but essentially consist of moisture condensing or water-soluble compounds migrating to the surface of the coating. The moisture can react with CO2 and subsequently form ammonium carbamate by-products. Aside from the negative impact that this has on the aesthetic appearance of the film, these side reactions can alter the formulated stoichiometry, resulting in an imbalance of the desired reaction. This in turn potentially reduces the mechanical properties and chemical resistance.
However, the new generation of ketamine grades offers enhanced epoxy compatibility. An added benefit is that some grades have been modified to enhance thin-film cure rate to further protect against the above problems.
It is evident that poor compatibility, exudation and surface migration of free amine can result in blushing and blooming issues, which offer aesthetic concerns, but the cosmetic defect is more an illustration of the fact that the intended or desired reaction hasn’t fully occurred. These problems can also influence overcoatability and subsequent inter-coat adhesion, which in turn can alter mechanical properties and chemical resistance.
Comments regarding the surface films following the reactivity evaluation above are detailed in Table 2.
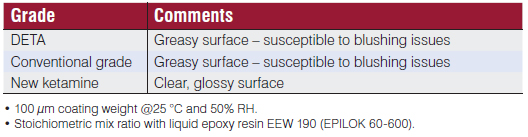
The new generation of ketamine grades offer enhanced compatibility and vary in terms of their surface appearance from a moderate improvement to the surface film to a significant advance based on selected grades from within the range. The new ketamine grades are offered in several supply forms with some high solid-content grades diluted with ketone and/or aromatic solvents, or supplied free from any supplementary solvent – meaning they are supplied solvent free but acknowledging the solvent inherently generated following hydration.
Maintain Pot-Life and Cure Properties
From a technical perspective, the new generation of ketamine grades offers significant improvement in performance while maintaining desirable reactivity characteristics. Again, for illustrative purposes the relative reactivity of small mass cure and thin-film cure rates are detailed in Figure 2 using DETA and conventional ketamine as benchmark values against one of the new generation grades.
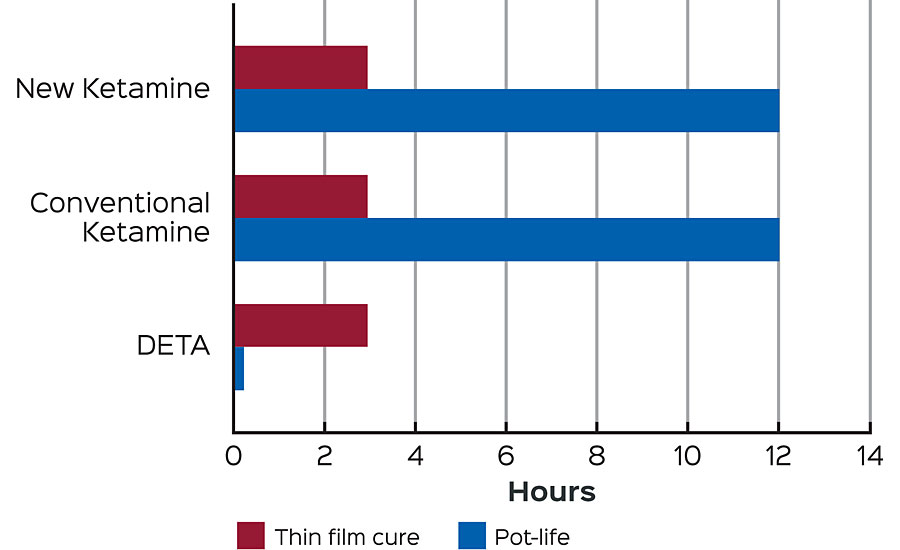
Figure 2 illustrates that the new generation of ketamine curing agents offers significant improvement of working time/pot-life while maintaining desirable high thin-film reactivity. Alteration and extension to pot-life is the main design driver for this generic product group, and the new ketamines satisfy that particular aspect as expected. While they work just as well in this respect and in addition to the regulatory improvements outlined above, it is their technical performance, both during and after cure, that really sets them further apart from their analogous predecessors.
These grades can be used as curing agents in their own right or combined with other grades to formulate systems with bespoke reactivity and other process or cured performance attributes.
Conclusion
In summary, as the laboratory tests prove, the new generation of ketamines are unique - not only are they REACH compliant, but technically they also outperform their conventional counterparts both during and after cure, as well as offering both long pot-life and reduced hazard, making them the ideal curing agents for the paint and coatings industry.
Looking for a reprint of this article?
From high-res PDFs to custom plaques, order your copy today!