Small Particles, Big Changes
Cost-Effective Improvement of Corrosion Protection for DTM Coatings

Direct to Metal (DTM) coatings are, as the name suggests, coatings that are applied to a metal substrate without the use of a primer. The resin chemistry is normally acrylic or polyurethane depending on whether it is a water-based, waterborne or solvent-based coating. DTMs are applied on surfaces that require little to no pre-treatment. They are commonly used in the non-professional market, when basic corrosion protection is required and/or when a surface aesthetic is not as important (no specific requirement for a high-gloss topcoat or decorative coat). 1
In coatings, the use of traditional corrosion-inhibiting pigments gives a matte or reduced gloss finish to the paint. For gloss finishes with better corrosion protection capability, a two-coat system is required (i.e. a primer and a topcoat). The primer coating offers corrosion protection through the use of a corrosion-inhibiting pigment, and the topcoat provides the required aesthetic finish (high gloss). In DTM coatings, the formulator balances the optical properties with the corrosion protection. Standard corrosion inhibitors are usually pigmented materials, and their irregular shape and large size have a significant effect on the optical properties of a gloss coating. Thus, a compromise is usually made between these two features of the coating, as obtaining high gloss and robust corrosion protection in a single coat is not usually possible. This tends to limit the applications of DTM coatings to either protection of assets in less demanding environments (e.g. indoor) or where high gloss is not a key requirement. The challenge for the innovative formulator is how to produce a single-coat DTM system with durable corrosion protection and decorative aesthetic properties similar to a topcoat.
To solve this issue, a corrosion-inhibiting product with no effect on optical properties of the coating (gloss) and that is easy to incorporate into a coating, is required. The inhibitor needs to be as efficient as or better than current traditional anti-corrosive pigments used in one- or two-coat systems. The optical properties of the coating must not be compromised by the addition of the inhibitor. These requirements that are normally in balance in a DTM can be achieved using Inhibispheres ® (IS) due to their size, shape, refractive index and the sustained release of their unique corrosion inhibitors. 2,3
Inhibispheres are a range of corrosion-inhibiting pigments designed for use in paints and coatings. These materials are porous silicas with organic or organometallic corrosion inhibitors uniformly dispersed inside a solid silica matrix. They offer the paint formulator a wide range of corrosion prevention options with six different products for the protection of both steel and aluminum. Organic inhibitors are very efficient in preventing corrosion on metal surfaces, but their use in coatings is limited by their incompatibility with paint resin chemistry. Inhibispheres allow the use of organic and organometallic inhibitors in coatings through entrapment within the pores of the silica matrix. They are mechanically resistant and can be used in a mill base without premature release of the inhibitor inside the particle. Being made primarily of silica, the Inhibispheres can easily replace other paint fillers in a coating, thus minimizing the impact on the Pigment Volume Concentration.
Inhibispheres are made via an emulsion polymerization process using carefully selected precursors and a highly effective organic or organometallic corrosion inhibitor. Meticulous control of the synthetic conditions allows for the tailoring of particle size and distribution. This results in a spherical product that is perfectly uniform and monodisperse (Figure 1). The practical advantage this gives is that the particles have a low refractive index due to the small particle size with D 50 = ~0.5 µm.
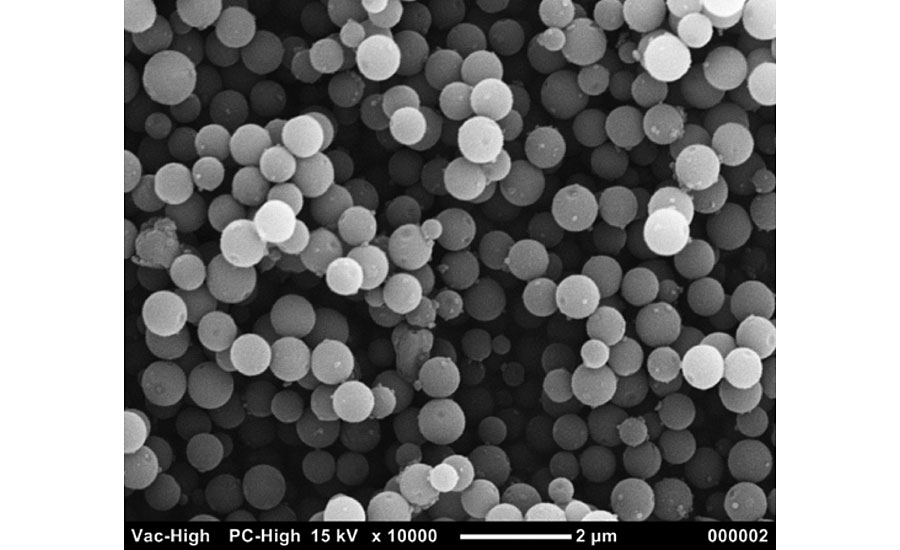
Results
The Inhibispheres are essentially made of a porous silica with a sponge-like morphology where the pores are filled with the chosen inhibitor. The inhibitors are specially selected to work with specific substrates (aluminum and/or steel) and are capable of working synergistically with traditional corrosion-inhibiting pigments.
To demonstrate their use in DTM coatings, the performance of Inhibispheres has been investigated in a selection of commercial coatings (Table 1). A high-gloss polyurethane topcoat (1) with no corrosion inhibitor was compared against an analogous DTM (2) product from the same product range and manufacturer. Both have the same resin chemistry, but the DTM contains a commonly used traditional pigmented corrosion inhibitor. The addition of the traditional pigmented corrosion inhibitor gives the commercial DTM a C1-C3 corrosion rating while sacrificing on gloss (Figure 2). As a comparison, the topcoat was used with Inhibispheres (3) to show how their addition into a coating can significantly improve the capability to inhibit corrosion while maintaining a high-gloss finish on the coat. A second comparison was made with Inhibispheres in the PU gloss topcoat (3) against a two-coat system using a primer with a traditional anti-corrosive pigment and the same PU gloss topcoat (4).
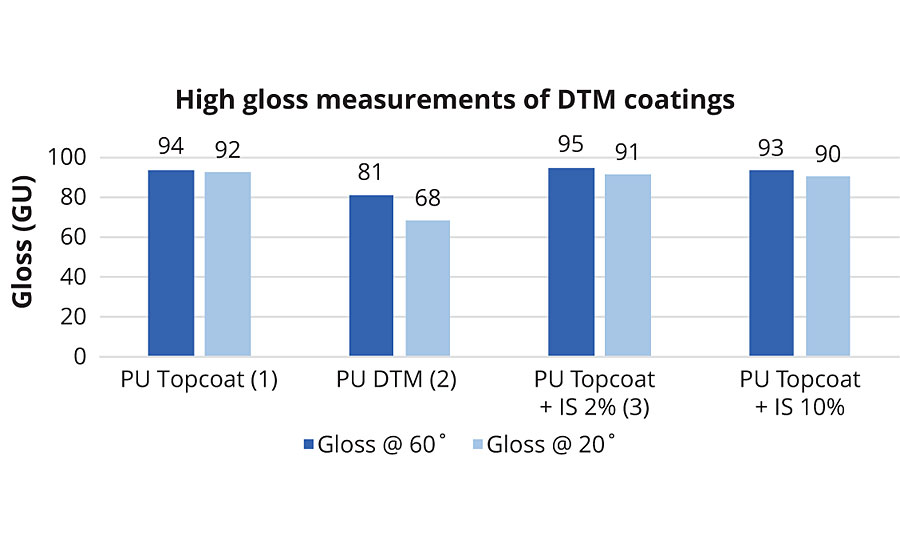
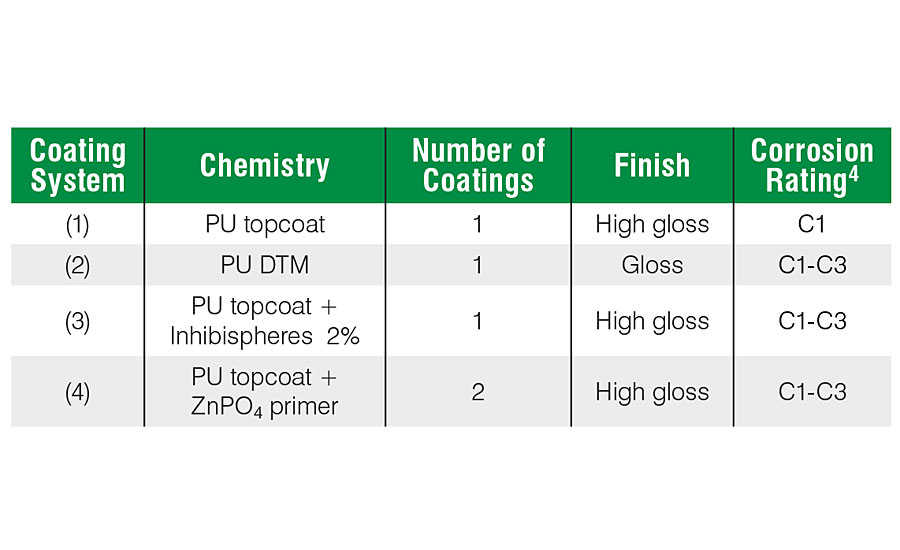
The gloss of the coatings was measured (Fig. 2) at both 60 (normal gloss) and 20 (high gloss) degrees. It is clear that the addition of Inhibispheres at 2% had little to no effect on the gloss of the coatings. Even at a loading as high as 10% the Inhibispheres materials had minimal effect on the gloss of the coating. Cold rolled mild steel panels (EN10130) were coated. The panels were then added to a NSST for 250 hrs for accelerated testing. The corroded panels were scanned, and the coating removed around the scribe to visualize the corrosion.
The corrosion performance of the different coating and inhibitor systems was tested using ASTM B117. 5 The panels were exposed for 250 hrs to a corrosive environment (Table 2). There was some staining from rust on all the samples. If a comparison is done by looking at the staining on the coating, there appears to be minimal difference between any of the paint systems. However, when comparing the samples with the coating around the scribe removed, the story regarding corrosion inhibition is completely different and much more revealing. It is clear that sample 3 (Inhibispheres) performed far better at corrosion prevention when compared to the other systems with the coating removed. The worst performing system was clearly sample 1, which had the most creep from the scribe underneath the blistering in the coating caused by the corrosive environment. It is also clear that sample 2 was better than 1, and better even than 4 (2-coat system) but underwent some blistering that 4 did not. However, sample 3 (Inhibispheres) clearly had no blistering and by far the least amount of creep from the scribe of all the paints tested.
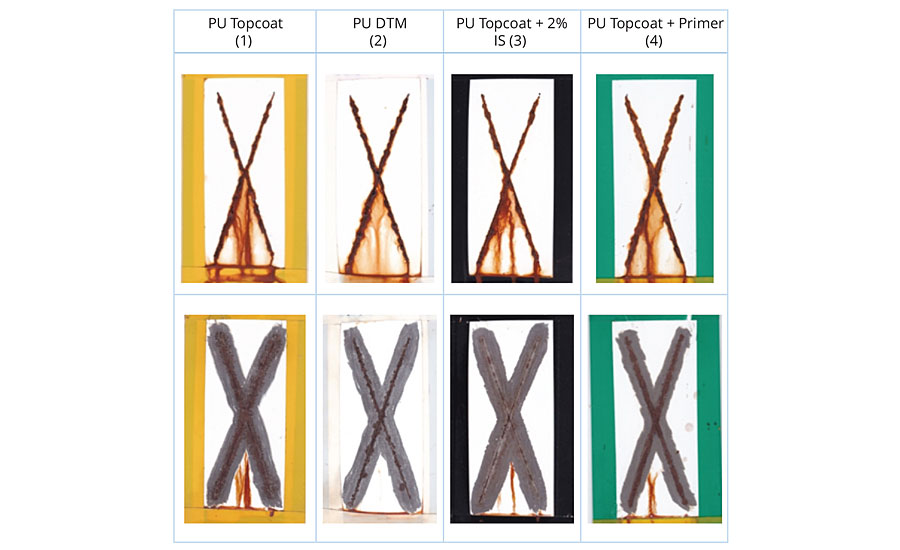
In addition to the visual assessment, the corrosion creep from the scribe for each of the samples was recorded and graphed in Figure 3 as an average of four measurements taken at the widest point on each of the four parts of the scribed X. The measurements make clear what is seen in the images in Tab. 2. The best performing system for corrosion inhibition was the topcoat with the Inhibispheres inside. A significant reduction in the length of the corrosion creep was recorded. Average creep in 3 was seven times lower than 4, and three and half times lower than 2. (Both comparison systems being the commercially available paint systems.)
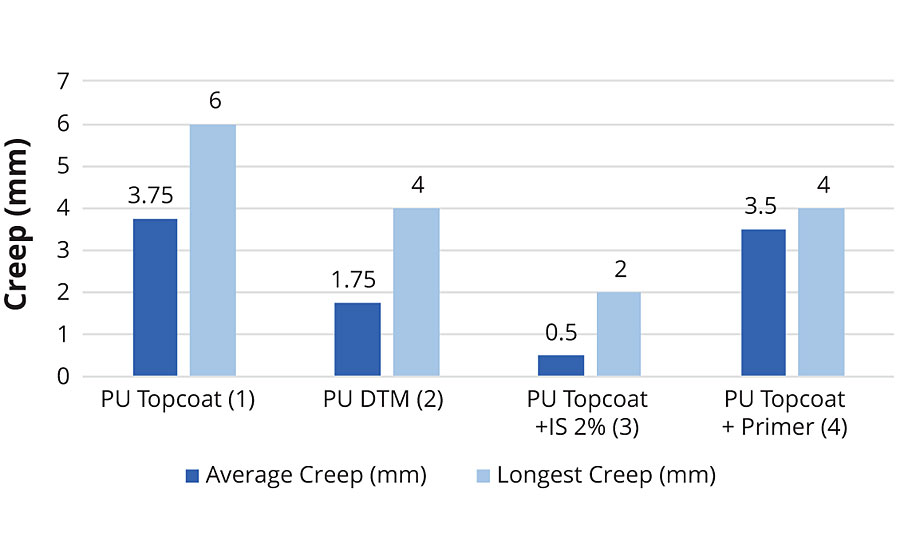
Conclusions
A summary is given in Table 3 of the results of the different coatings systems tested. A DTM coating with better gloss and anti-corrosive functionality can be easily achieved utilizing Inhibispheres. A small increase in the formulation cost (of the topcoat) can yield a product with a significantly greater ability to withstand corrosive environments. It is possible to take a C1 corrosion class coating and create a C3 or better coating.
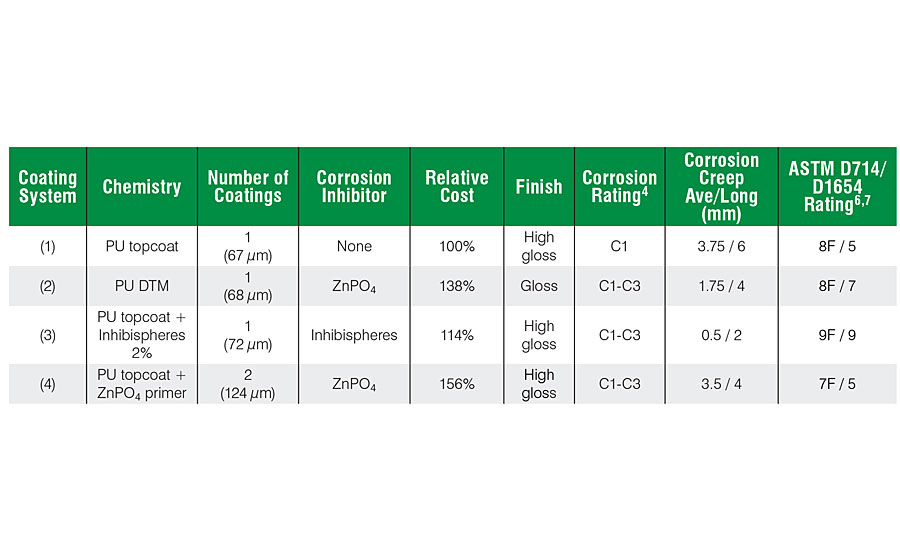
It is obvious that sample 1 was at best a C1 coating. With the addition of the Inhibispheres the coating was capable of showing better corrosion prevention than coatings with a C3 corrosion environment rating (both 2 and 4) while maintaining a high-gloss finish. The cost of coating system 3 (Tab. 2) per liter increases by 14%. However, the cost of the commercial DTM is 38% more than the topcoat formulation. Thus, for a 14% increase versus 38% increase (a saving of 24%) in cost, the resulting product, which offers better performance than a commercial DTM, could translate into a significantly higher selling price for the manufacturer. For the end users, the benefit of using a high-performing DTM coating remains substantial. The labor requirement for putting a single coat down compared with a two-coat system represent a significant gain in time and money. In summary, the use of Inhibispheres in DTM formulations makes a compelling business case for both the paint manufacturer and the end user.
References
1 Boggs, L. Paint and Coatings Industry Magazine, Oct 2016 , pg. 28-30.
2 Noble-Judge, A.; Barbé, C. Paint and Coatings Industry Magazine, Oct 2016 , pg. 22-26
3 Noble-Judge, A.; Barbé, C. Paint and Coatings Industry Magazine, Feb 2019 , pg 26-31
4 BS EN ISO 12944 Paints and varnishes corrosion protection of steel structures by protective paint systems.
5 ASTM B117 Standard Practice for Operating Salt Spray (Fog) Apparatus.
6 ASTM D714 – Standard Test Method for Evaluating Degree of Blistering of Paints.
7 ASTM D1654 Standard Test Method for Evaluation of Painted or Coated Specimens Subjected to Corrosive Environments.
Looking for a reprint of this article?
From high-res PDFs to custom plaques, order your copy today!