Breakthrough in Furniture Coating with UV LED Curing



SC Freda, Lithuania’s oldest furniture company founded in 1880, has started production on its new high-speed furniture coating line. The company specializes in manufacturing flat pack furniture from chipboard, MDF and cellular lightweight construction panels. The surfaces range from decorated paper surfaces with clear UV varnish, to highly pigmented UV coating systems. The company is a major supplier for IKEA, manufacturing multiple product series.
As a measure to increase its manufacturing capacity, SC Freda expanded with a new production facility, featuring a high-speed production line with UV curing. This new line must comply with the high IKEA quality and process control standards. In addition, sustainability and energy efficiency were important topics that were taken into consideration to ensure a strategic, long-term investment, and to stay in the forefront of sustainable manufacturing.
EFSEN UV & EB TECHNOLOGY, founded in 1986, focuses on radiation curing technology, with extensive experience in measuring and integrating UV-curing equipment for a wide range of applications and industries. Due to the strong heritage of furniture production in Denmark and its neighboring countries, it has been natural for EFSEN to develop a unique understanding for optimizing curing solutions for the wood and furniture industries.
EFSEN and Freda have been working on optimizing UV for many years, and the discussions about the super-efficient and intelligent UV line started between the two companies in 2017. There were many things for Freda to consider, with cost efficiency, superior product quality and maximized production capacity being some of them. Their intention to implement a modern, effective and environmentally friendly production process were key directives from the start of the project.
For EFSEN, it was clear that the only reasonable way to supply a highly efficient and future-proof production line would be with UV-LED curing. While UV-LED curing in the wood industry is nothing unique anymore, the current UV-LED curing production lines are only using a fraction of the capability the technology can offer. EFSEN wanted to go one step further, not limiting the use of UV-LEDs to gelling positions, which is how UV-LEDs are used in most lines. The intention was to change the whole process to UV-LED curing on all positions except the final top coat cure. The price/performance of conventional Mercury lamps can’t be matched yet for the final layer, due to the challenges of formulating price-competitive UV-LED curing top coatings that meet the high resistance and color accuracy requirements of a top coat.
Curing the sanding sealer with LED only is an industry first, and such a challenging task goes beyond what an equipment supplier can accomplish alone. With the high-power output of LEDs today, the primary limiting factor of the technology, and also the main cost driver, is the coating itself. Therefore, it was a benefit that AkzoNobel was the designated coating supplier for this project. This leading manufacturer of wood coatings is known as an innovative company with extensive R&D capabilities. From the first discussions AkzoNobel agreed to cooperate to develop a UV-LED-curable process with as much UV-LED as possible, without a negative impact in coating price or properties. EFSEN worked closely with AkzoNobel, sharing not only the technical expertise, but also utilizing the chemical expertise of David Ivarsson, the EFSEN chemist highly specialized in UV-LED formulations. In direct contact with AkzoNobel, it was possible to develop a new curing process, replacing all conventional UV systems with the exception of Mercury lamps at the end of the production line. A key decision to make this a reality was the choice of 365 nm LED for the sanding position.
From Conventional to LED
Going through the normal coating process, starting with sealing of the surface with two clear coats, following up with sanding the surface, and then proceeding to build the color with multiple layers of base coats, to finally finish it off with a top coat, the challenge was to find a process solution with only one LED unit in each position, replacing multiple conventional UV lamps on each station.
The conventional line setup that was the starting point at SC Freda is as follows, with 50 m/min as the target speed (Figure 1):
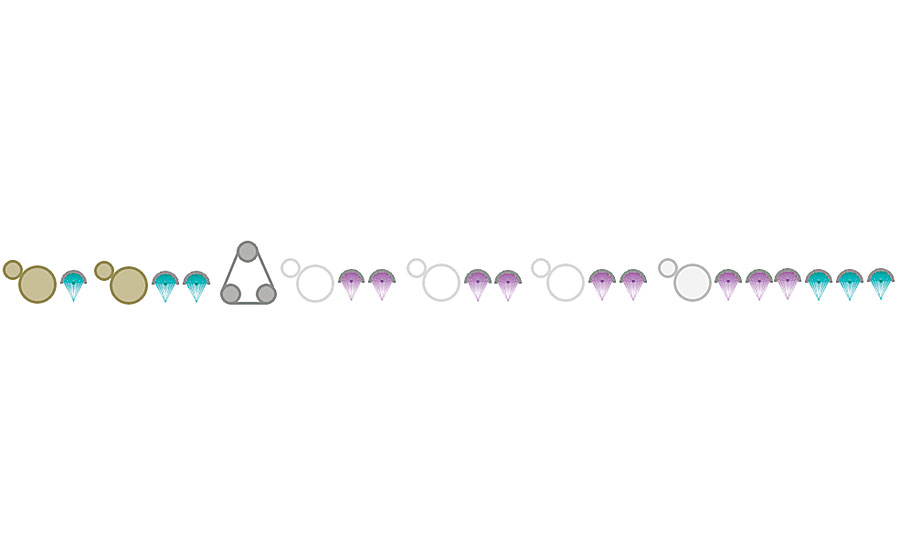
Step 1:
Sanding primer, gelled with 1x
120 W/cm Hg-lamp
Step 2:
Sanding primer, cured with 2x
120 W/cm Hg-lamps
Step 3:
Base coat layer 1, gelled with 2x
120 W/cm Ga-lamps
Step 4:
Base coat layer 2, gelled with 2x
120 W/cm Ga-lamps
Step 5:
Base coat layer 3, cured with 2x
120 W/cm Ga-lamps
Step 6: Top coat, cured with 3x 120 W/cm Ga-lamps and 3x 120 W/cm Hg-lamps
The biggest difficulties to be considered for the new line were the surface cure in front of the sanding station. It is critical that the coating cures well enough not to clog the sanding. Furthermore, both white and dark grey base coats will run, which include titanium dioxide pigment that absorbs a lot of the UV irradiation up to 400 nm.
EFSEN solved these challenges together with AkzoNobel by defining the optimal LED wavelength on each station, ensuring a perfect match with the chemistry for optimal curing. The final setup also uses height-adjustable LEDs to adjust the gloss level of the top coat (Figure 2). With the low temperature of an LED-cured process in combination with the full control of the UV uniformity with EFSENs proprietary ICAD ® Technology, the process runs with very high gloss stability. Furthermore, the low running temperature prevents issues with edge band glue melting, which can otherwise be a problem.
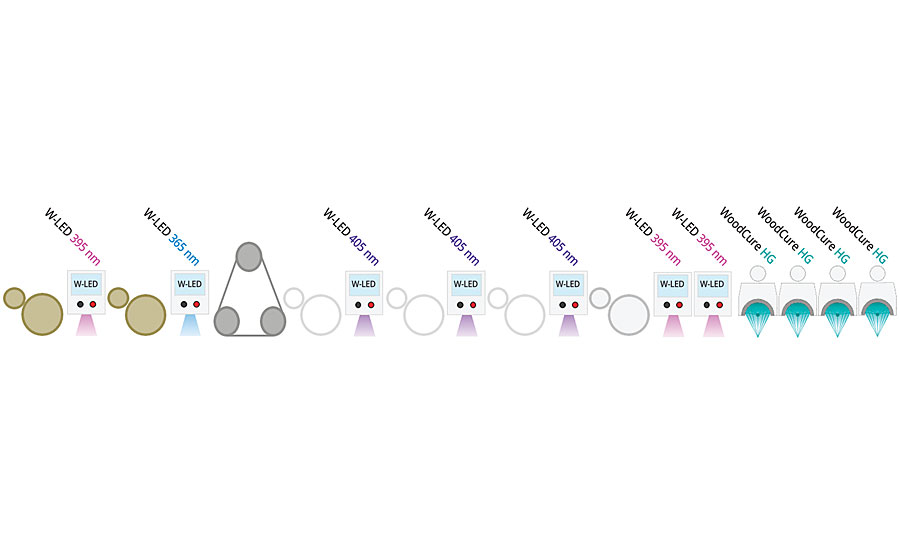
Energy efficiency is a major requirement for any modern installation. Figure 3 shows that 55% energy saving could be realized by selecting UV-LED systems rather than conventional mercury-based systems. In addition, the long lifetime and reduced maintenance required with UV-LED systems helps to maximize the uptime of the production line. The standby power consumption of conventional UV lamps (which has not been taken into account in the calculations in the figure) is eliminated when choosing UV-LED, increasing the actual efficiency further.

In addition to the LED systems, EFSEN’s conventional UV lamp system, the WoodCure, provides some nice benefits. Due to guided cooling and superior temperature control, in combination with state-of-the-art reflectors and power supplies, the system provies an exceptionally high intensity and a maximized lifetime. The system utilizes reflector cassettes, which allow for a very quick and convenient cleaning and bulb change. With only 25% stand-by power level, it features some of the market’s lowest stand-by power consumption (Figure 4).
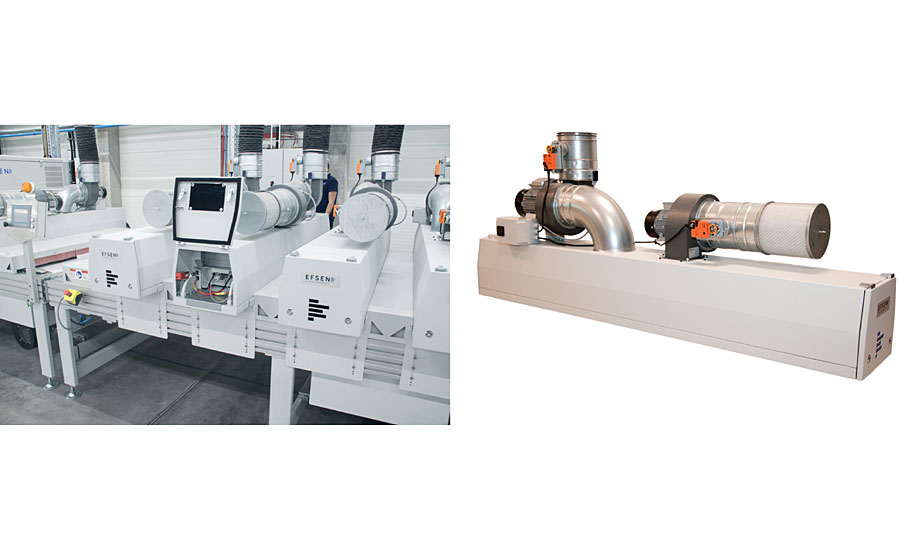
Long-Term Process Stability
But even after ensuring that the chemistry and the light sources work in synergy, fulfilling the application requirement, LED curing presents a unique obstacle to overcome in order to ensure long-term process stability. UV-LEDs, in difference to conventional UV systems, consist of thousands of individual light sources, and each of them are slightly different. Measuring the light source at a few defined positions, as it is being done at conventional light sources, will not give the required process security. During the lifetime of the LED, a deviation will occur, such as a defect segment, damaged optics or dirt on the lens that would have a negative impact on the output, hence the cure. If this would happen in a position away from the measuring point, it would not be recognized in a normal measurement.
But defect segments, damage or dirt are not the only reason why an in-line process control would be a huge benefit for UV-LED systems. Even if UV-LEDs last much longer than mercury-based UV lamps, they still age. This means they lose power over their lifetime. This aging is very temperature sensitive, requiring a perfect balance of the cooling within the UV-LED system. The aging might also be different from chip to chip, something resulting in deviations within the UV-LED system that become bigger over the lifetime. Furthermore, any replacement LED-modules would have a higher power output compared to remaining modules.
EFSEN solved this process stability issue with the proprietary ICAD inline process control, which is integral part of all EFSENs UV-LED products. ICAD is an inline control that continuously measures the UV output of the lamp across the width of the whole line (Figure 5). It recognizes deviations of the emitted UV power and automatically adjusts the individual UV-LED arrays to produce a homogeneous UV-distribution over the whole width of the UV-LED system. Deviations of <5% can easily be reached using this technology, which is capable of measuring inline during production, something that has been confirmed by countless hours of production testing.
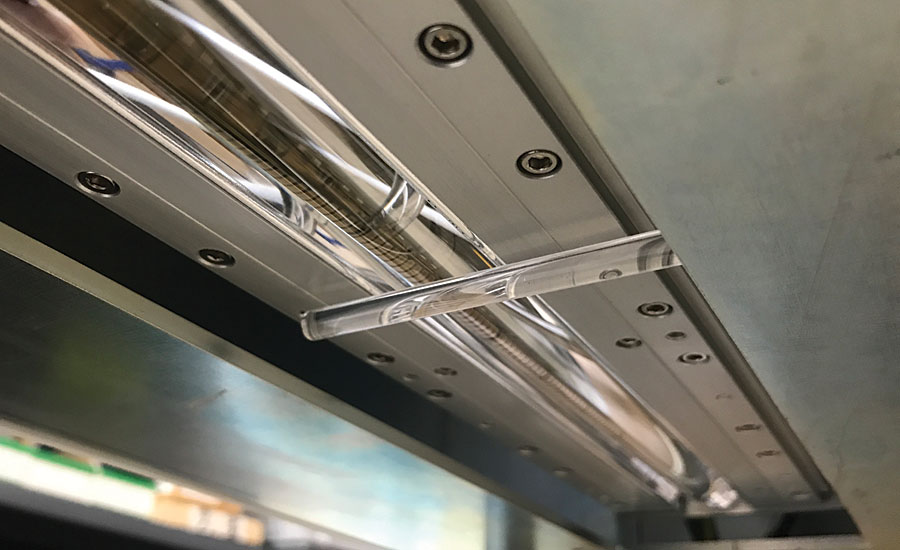
By utilizing the ICAD technology, SC Freda is able to have continuous control of the UV output being applied during actual production (Figure 6). All this information generated by ICAD can be extracted to provide a complete history of UV output, which can be used for quality documentation of the production batch. If required, the documentation can be made for each piece of product individually, showinag the actual UV energy being applied to each individual product.
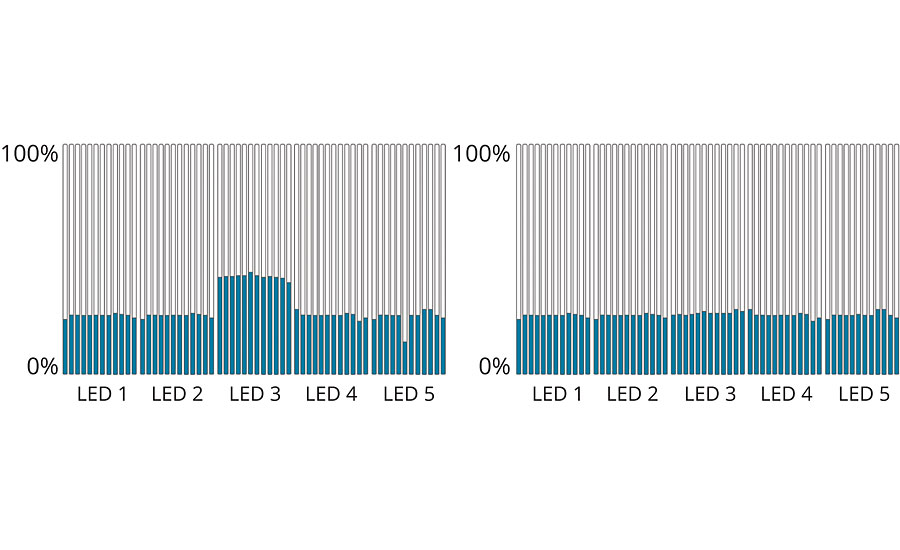
SC Freda decided to choose EFSEN’s W-LED systems incorporating ICAD. The W-LED is an “all in one” unit, where power supplies, PLC control and cooling air supply are all included into an easy-to-maintain housing. This saves space around the line, as no external electrical cabinets are required. W-LED is made with the user in mind. It is easy to install and use, only requiring a power and PLC connection. The integrated cooling air blowers forward filtered cooling air to the LED modules, taking care that the LED modules are not getting dirty to guarantee optimal cooling of the LED modules, increasing the lifetime further. This filtered cooling is very important under the normal condition inside a wood processing plant. Exchanging the air filters of a W-LED can be done without tools, for a fast and easy filter replacement utilizing standard filter cassettes.
The W-LED comes with optional electrical height adjustment, sensors that activate the W-LED when a product arrives, safety sensors to deactivate the conveyor in case a bended part is getting stuck, and customized light shields that are designed to fit onto the conveying system.
Conclusion
With the help of EFSEN and AkzoNobel, furniture maker SC Freda was able to transform the majority of its coating line to a UV-LED system, maintaining a stable, robust production method that ensures a high-quality end product that meets the target requirements. The W-LED, with integrated UV-LED modules, and the ICAD measuring system provide a novel solution that is unique in the market, providing complete UV control, all the time.
For more information, visit www.efsen.dk.
Looking for a reprint of this article?
From high-res PDFs to custom plaques, order your copy today!