Water-Miscible Stabilizers for Wood Coatings: A Synergistic Approach


Prefer the magazine experience? Subscribe to our digital issue.


In line with its commitment to helping improve sustainability throughout the coatings value chain, SONGWON has applied Aristotle’s synergy concept, “The whole is greater than the sum of its parts,” and developed a range of water-miscible stabilizers for coatings that work together to produce enhanced effects. The new water-based additives and stabilization packages are designed to combine the efficiency of conventional products with the benefits of water miscibility and low to zero volatile organic compound (VOC) generation, as well as easy dosing and handling. The products lend themselves to a wide number of applications. This article describes their use in polyurethane wood coatings and the results of tests on wood with a number of different stabilizers.
Stabilization of Waterborne Polyurethane Wood Coatings
Waterborne coatings are increasing in importance generally, and in some applications they are one of the fastest growing markets in the coatings sector. Protective additives are essential components of wood coating formulations. While anti-oxidants guard against degradation through oxidation, UV absorbers protect both the coating binders and, in clearcoats, the underlying wood structures from UV degradation.
UV protective additives fall into two categories: UV absorbers and stabilizers. UV absorbers have chemical structures that allow them to absorb UV radiation and dissipate the energy in a less damaging form. Light stabilizers act as scavengers, reducing the reactivity of any free radicals formed within the coating.
The waterborne segment of the polyurethane (PU) coating industry provides a major opportunity in applications such as wood and furniture, as well as construction and others, because this type of binder meets environmental regulations, including minimal VOC generation, making it one of the most widely used coating materials. Another reason why polyurethane is a popular material for wood coatings is that it enhances the natural, warm effect of the wood.
The inherently advantageous properties of polyurethane can be further enhanced by using additives to manage temperature and light degradation, both of which can impact the appearance of wood elements, furniture, joinery, parquet and wood flooring, indoors as well as outdoors. Whether the color is preserved by protecting the pigment or the wood itself, our additives for temperature and light management, sold under the brand names SONGSORB® CS and SONGNOX® CS, can enhance the performance of polyurethane systems and ensure long-lasting resistance to damage caused by UV light and temperature variations.
A Synergistic Stabilization Package
The new range of light stabilizers and anti-oxidants combines the efficiency of conventional products with the benefits not only of water miscibility and low-to-zero VOC generation, but also of easy dosing and handling.
SONGSORB CS AQ01 is a fully water-miscible hindered amine light stabilizer (HALS) with a polymeric polyol structure that makes it the ideal solution for use in combination with polyurethane waterborne finishes. Thanks to its inherent properties, this product can be chemically incorporated in the polyurethane structure: it has high compatibility and is very easy to stir in, facilitating and accelerating integration in the system. Since it is fully mixed in, it offers the further benefit of very low, if any, VOC generation. The new HALS has been successfully tested, both in exterior wood stains and in the final polyurethane finish. It is not prone to the gelling that can be encountered with more traditional HALS systems. In addition, being a 100% active substance, it does not have the negative effects of systems containing chemicals that improve compatibility with water and of necessity have an impact on the final performance. Whether it is used for exterior wood stains or a polyurethane varnish, the product can be of great help to formulators and end users, thanks both to easy incorporation and to its prolonged protection effect. Several wood stains containing the HALS have already been launched.
The latest additions to the range include two water-miscible UV absorbers: SONGSORB CS 326 WB is a benzotriazole-based UV absorber for waterborne industrial, architectural, decorative and wood coating applications; SONGSORB CS 400 WB is a waterborne triazine-based UV absorber that is also suitable for more demanding applications such as automotive coatings. The water-compatible phenolic anti-oxidant, SONGNOX CS 2450 WB, designed for polyurethane-based coatings, helps to further stabilize the waterborne polyurethane during processing and curing, and once mixed with water, provides excellent compatibility as well. These new developments in water-miscible additives have been developed to provide customers with an excellent toolkit to increase the performance of their water-compatible coatings. Together with our water-compatible HALS, they provide a synergistic stabilization package for water-based coating systems.
Test Results with Anti-Oxidants and Light Stabilizers in Waterborne Wood Coatings
The efficacy of some of these as well other additives has been tested in waterborne exterior wood coating formulations based on three different types of binder chemistry: acrylic, alkyd and polyurethane.
Test Conditions
Four additives (Table 1) were compared with a competitive product, on their own and/or in combination with each other. The samples were exposed to 3,000 hrs of accelerated weathering in accordance with QUV method EN 927-6. The accelerated weathering study investigated the influence of these additive packages on changes over time to color and gloss of the coatings.
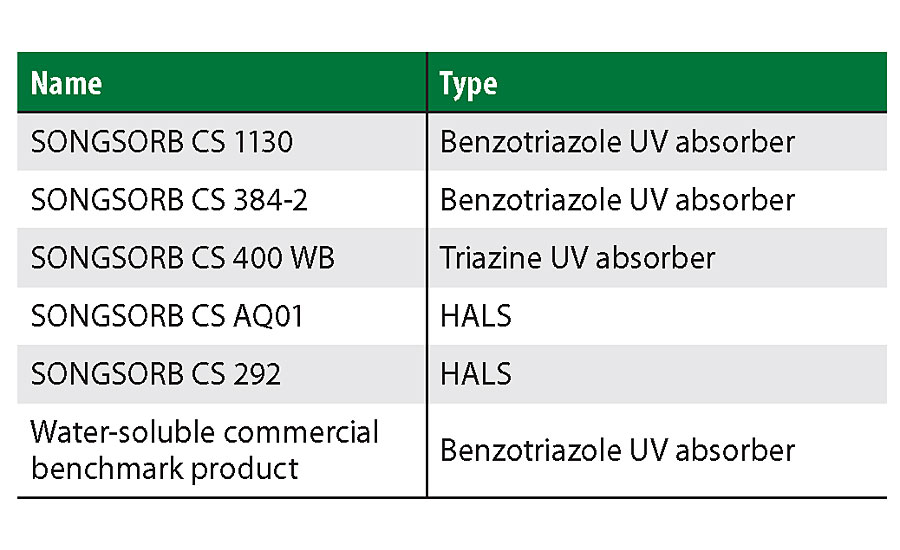
Table 2 provides a summary of the additives tested in the formulations investigated in this study. Formulations B-H were expected to perform better than Formulation A, which contained no stabilizers.
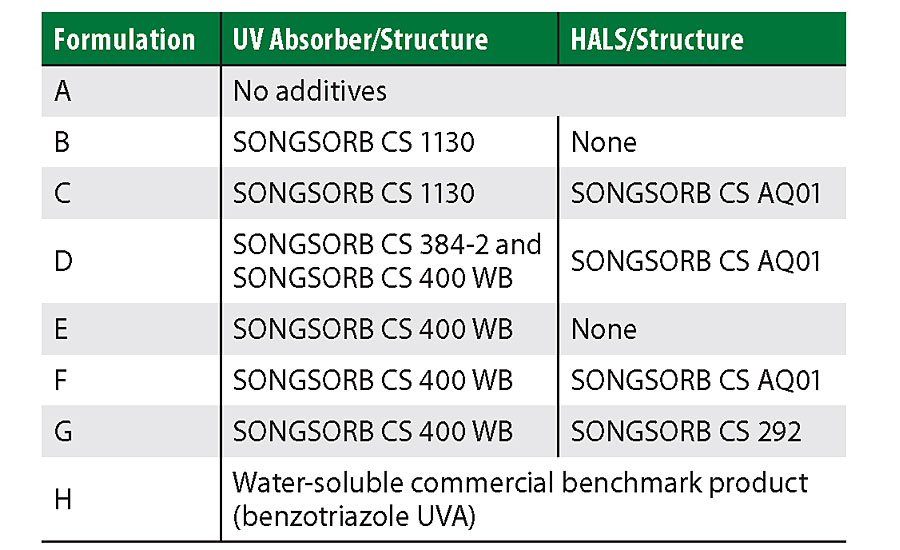
Results
QUV Weathering Test – Color Change
With the acrylic binder, color change and yellowness in most cases increased as a function of aging time. As expected, the formulation without UV absorbers or stabilizers (A) showed the fastest change in color and yellowness.
The alkyd-based group tended to perform better than both acrylic and polyurethane formulations. As with the acrylic binder, color change and yellowness increased as a function of aging time. The formulations containing UV absorbers and HALS performed better than those containing the UV absorbers alone.
The polyurethane formulations also exhibited changes in color and yellowness as a function of aging time. The formulation without UV absorbers or stabilizers showed the fastest change in color and a similar impact on whitening effects to that observed with the acrylic-based formulation.
QUV – Visual Assessment
Discoloration of the panels through weathering exposure was clearly observed with the acrylic binder, Formulation A (without UV stabilization additives) showing the greatest impairment, as expected. The best-performing additive packages in terms of visual appearance and resistance to development of defects contained SONGSORB CS 400 WB and a HALS. Formulations D and G were equivalent to the commercial benchmark in their performance. The waterborne additive SONGSORB CS 400 WB performed better than the 100% solids additive SONGSORB CS 1130 (Figure 1 and Figure 2).
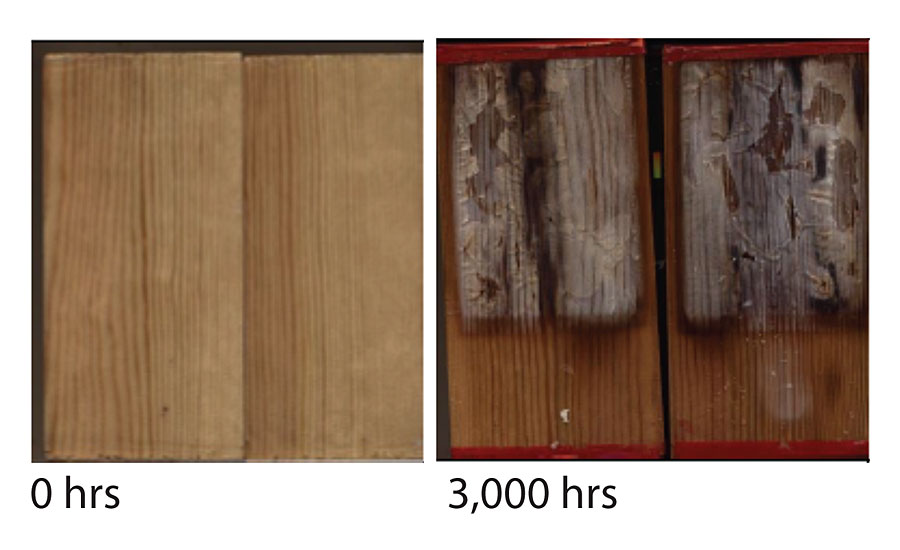
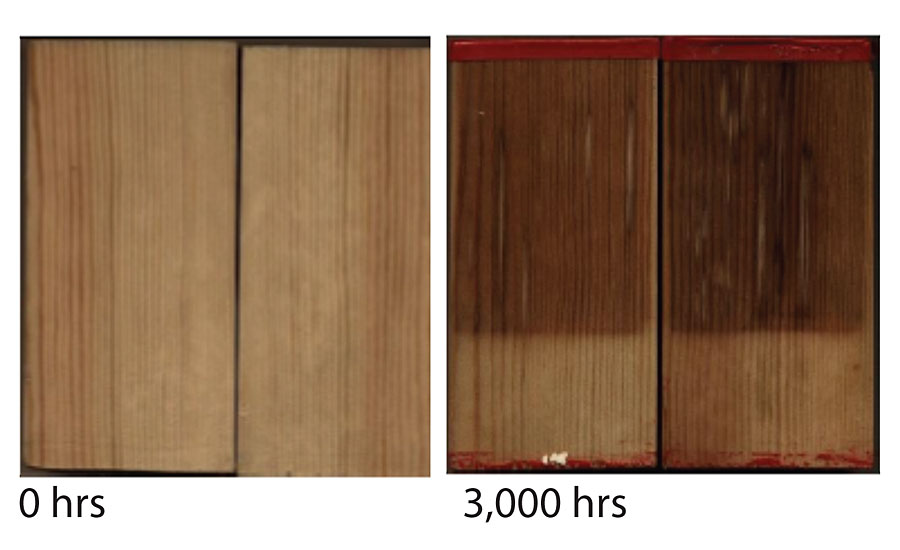
In the alkyd-based group, discoloration of the panels through weathering exposure was also clearly observed; Formulation A showing the greatest impairment, as expected, due to its lack of any UV stabilization additives. Significant yellowing of the coating occurred in sections of the panels exposed to heat but not UV: the color in areas exposed to UV was quite different from that of the masked parts of the panels. Formulation D performed best. All coatings except A (the formulation containing no stabilizers) performed well in the test. Most of the test formulations showed better performance as regards prevention of coating-defect formation than the commercial benchmark (H) (Figure 3 and Figure 4).
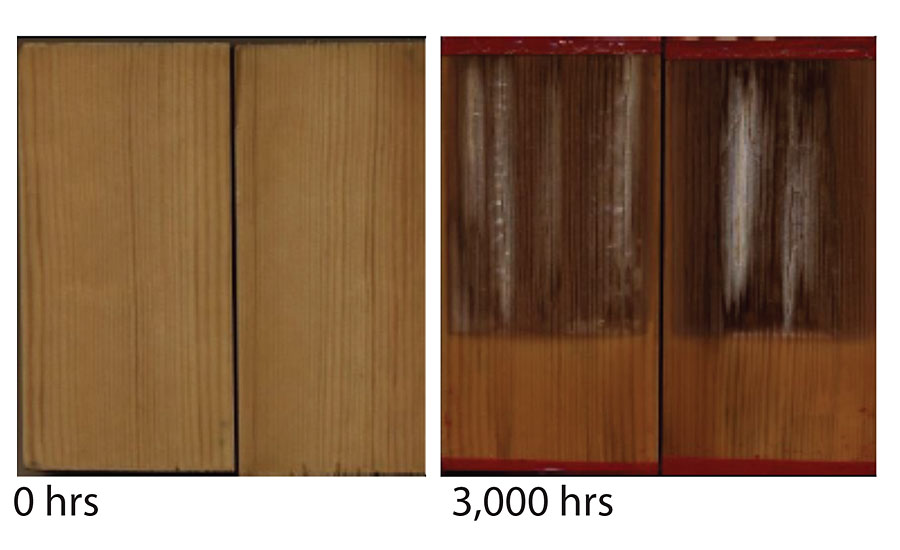
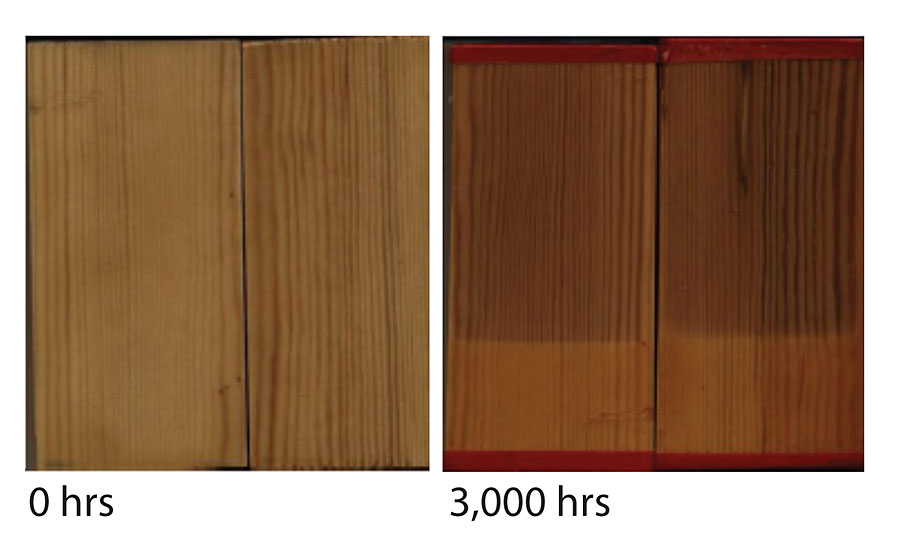
With the polyurethane binder, clear discoloration of the panels through weathering exposure was observed; Formulation A once again showing the greatest impairment, as expected, due to its lack of any UV stabilization additives. Formulations D and E were the best of the mixtures tested in this group. SONGSORB CS 400 WB performed better than SONGSORB CS 1130 as regards to prevention of coating-defect development (Figure 5 and Figure 6).
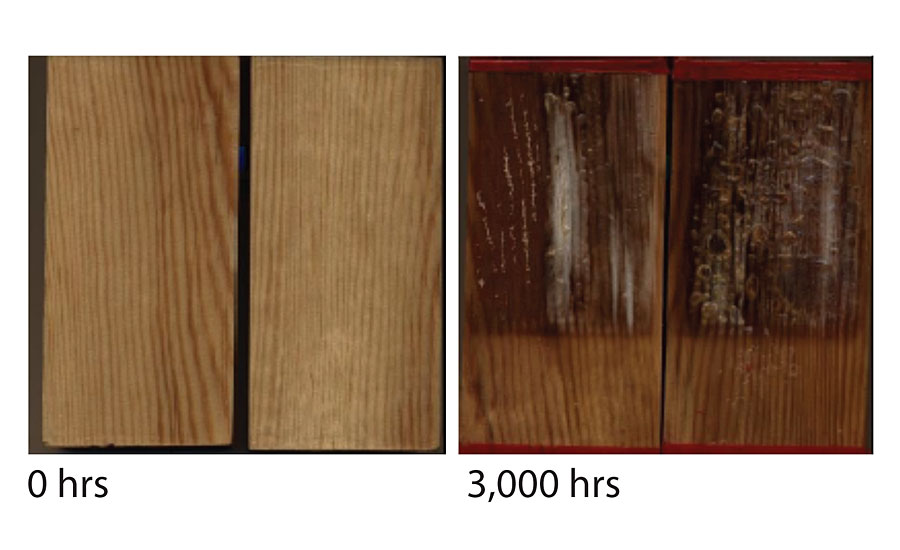
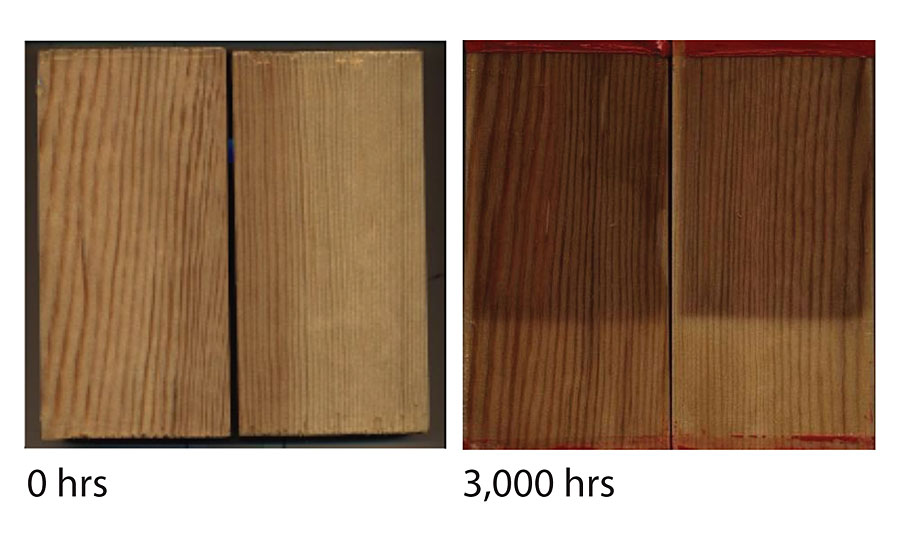
Summary of Test Results
As expected, the UV stabilizer/absorber-free baseline formulations underwent the greatest alteration during the exposure period. The changes included increased yellowness and color modification, as well as gloss reduction and the development of defects such as whitening, blistering, cracking and flaking on all tested panels.
The best-performing formulation depended both on the base coating formulation and on the parameter being tested. Generally, but not in all cases, the best-performing formulations contained a combination of UV absorber and HALS. Formulations containing SONGSORB CS 400 WB performed better than those with SONGSORB CS 1130.
Ongoing Developments
The initial assessments of standard and basic formulations described above are being supplemented by further tests with improved formulations and optimized ratios of our additives, which are being carried out in our Coating Laboratory in Maeam, South Korea.
Our team of specialty chemicals experts is currently working to expand the newly introduced WB range still further. These, together with the recently launched products, will make up a comprehensive portfolio of water-compatible solutions for the coating industry.
Looking for a reprint of this article?
From high-res PDFs to custom plaques, order your copy today!