Additives for Powder Coatings

In the world of resins and related paints, which is not an exact science, the role of additives and other special products is extremely important to obtain characteristics that often are a fundamental requirement for meeting pre-defined technical specifications or to meet the needs of end users. In fact, paints that normally play an aesthetic role in improving a product’s appearance also provide mechanical or chemical resistance. As an example we can mention paints for household appliances or those for aluminum frames, two cases where the satisfaction of technical specifications is a necessary requirement for approval in the end market.
By definition, additives are added in small quantities, often less than one point percent, to re-inforce selected chemical or physical properties of the finished paint. The powder coatings sector is no exception, and has some limitations that are intrinsic to the technology itself, which are linked to the physical state of the paint before application on the piece to be painted. Powder paint particles must melt first (melting), then aggregate to form a homogeneous liquid film (flow) and finally crosslink to form the final coating film (crosslinking) (Figure 1). Sometimes the “orange peel” effect is created, which sometimes distinguishes the final appearance of powder coatings compared to more conventional liquid coatings.
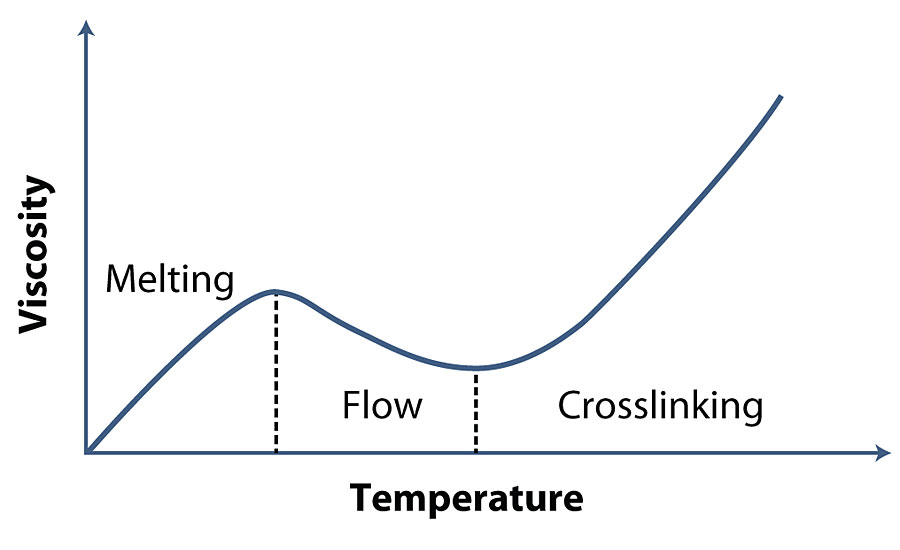
Therefore, additives used as flow promoters play an important role in powder coating technology. Flow promoters are additives that allow the paint film to wet the substrate homogeneously during the melting phase of the powder paint and then reduce the orange peel effect during the crosslinking phase.
Surface tension is the parameter that regulates the wettability of the substrate; a low surface tension implies high wettability of the substrate (Figure 2). Without going into details with the complex Orchard’s equation, the flow of the film (F) is regulated by some key parameters such as surface tension, paint viscosity of the fluid phase before crosslinking and film thickness. Intuitively let’s try to connect those parameters through a simple mathematical formula that explains their direct or inverse dependence.
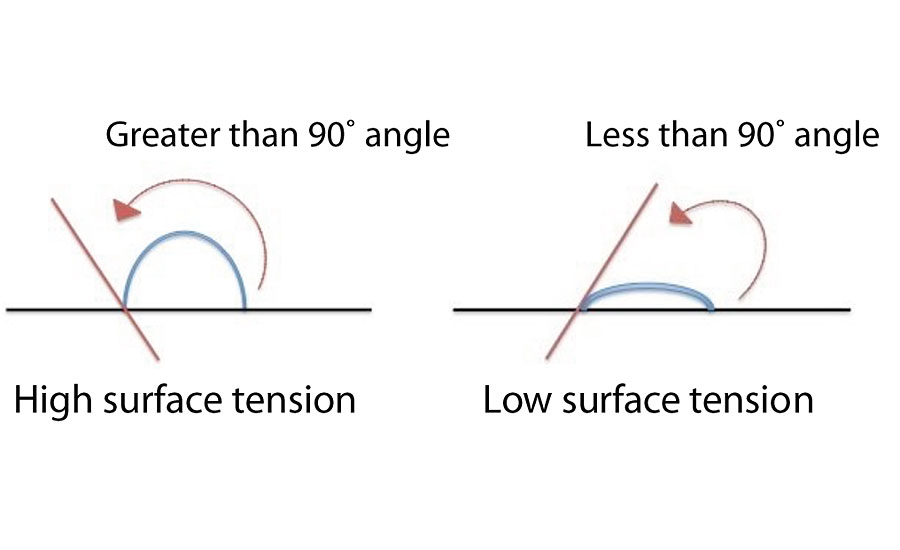
F α h x Ts/Vx
where h = thickness, Ts = surface tension and Vx = viscosity.
With high film thickness, high surface tension and lower viscosity, the flow of the coating film will be better. Regarding the formation of a homogeneous film without superficial defects (craters, holes in the film), the ideal situation is with high viscosity and surface tension as homogeneous as possible. In this case, some theories add that a good wettability of the substrate surface (low surface tension) is also important to avoid these surface defects.
As far as pigmented powder coatings are concerned, it should also be considered that good flow is related to good dispersion of the pigment in the powder paint matrix when this is still fluid, which can also be defined as good wettability of the paint while fluid on the solid pigment particles. Also in this case we can intuitively understand how the wettability of the pigment improves when the fluid-pigment interaction forces exceed those of pigment agglomeration. The wettability (p) of agglomerated pigment particles is regulated also in this case by relatively complex mathematical equations (Washburn and Blake-Kozeny formulas for instance), usually similar to the penetration of a fluid on a capillary.
P α Ts/Vx
where Ts = surface tension and Vx = viscosity.
According with this reasoning, low viscosity and high surface tension have a positive impact on the wettability of the solid pigment particles. On the other hand, too low of a viscosity can generate problems of poor edge coverage and even sagging with vertical surfaces.
In summary, for both viscosity and surface tension, a compromise is essential to facilitate wettability of the substrate, absence of surface defects and pigment dispersion.
In the powder coatings sector, flow promoters are divided into two main categories depending on the solid carrier used for dispersing the liquid active substance, the additives dispersed on silica and those dispersed on polyester resin (so called masterbatch). Both consist of a liquid acrylic additive, which is the active substance dispersed on a solid matrix that can be either silica powder or polyester resins. These two alternative technologies present certain differences linked to the process conditions for the industrial production of powder coatings and to the final characteristics of the coating film (Table 1).
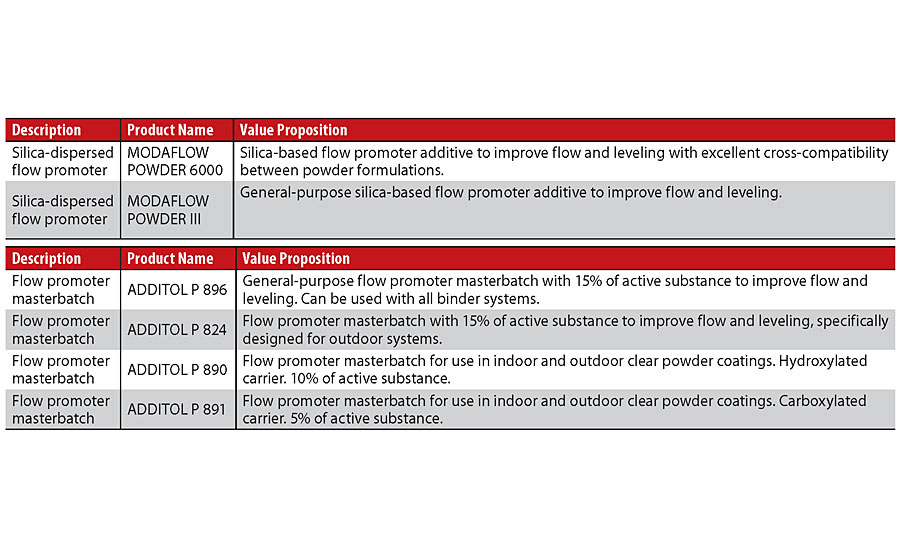
The choice between the two classes of products is not always unambiguous, and both technologies have advantages and disadvantages. For example, if we want to limit the content of the non-active carrier, we can focus on silica-dispersed spreaders that are more concentrated as a quantity of active ingredient. On the contrary, if perhaps we have process limitations with regard to paint dispersion during preliminary mixing and extrusion, then we can focus on masterbatches that, being less concentrated, require a greater quantity of product. When you choose products dispersed on polyester resins there is also the possibility to choose between products with carboxylated or hydroxylated resin functionality. This allows, if necessary, the carrier of the additive to react with the hardener used in the reaction of the binder.
The crosslinking reaction of some of the main binders in the world of powder coatings involves the addition reaction of a glycidyl group with an acid group:
R-COOH + R1-CH(O)CH 2 + R-COOCH 2 CH(OH)-R1 (addition reaction)
Without going into details with the study of complex mathematical equations that regulate the kinetics of chemical reactions, it is well known that the speed of this chemical reaction can be accelerated by some families of chemical compounds such as acids and bases. Often these types of products are not added, as they are in the paint premix but, to facilitate dispersion, they are once again dispersed onto a polyester matrix (Table 2).
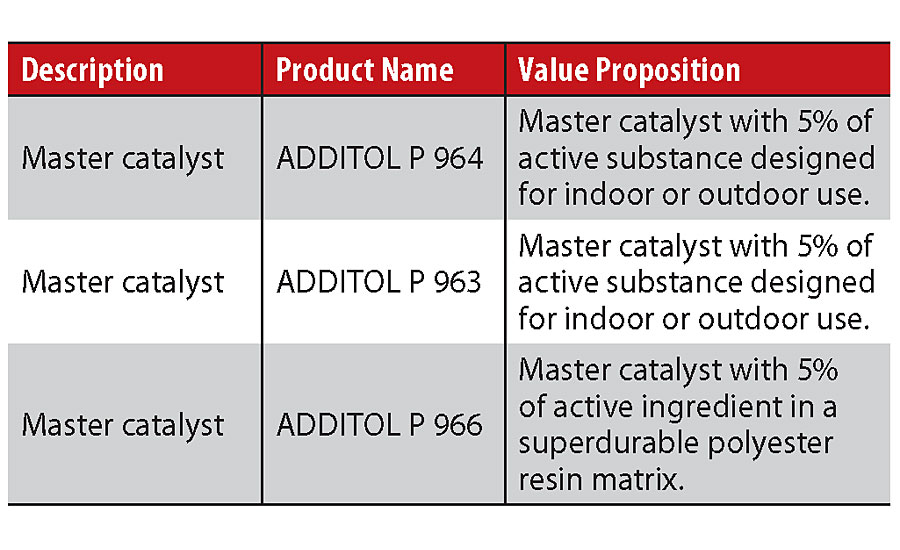
Obviously, by choosing the right type of polyester carrier you can also moderately influence some of the final characteristics of the powder paint, a good example is the durability of the paint with regard to outdoor resistance.
Catalysis therefore plays an important role in reducing the crosslinking temperature of paints or in reducing the curing time at the same temperature, in essence to reduce energy consumption during the curing phase without compromising the final result. Once again, a reasonable compromise is welcome in order to avoid too much catalyst, which may adversely affect the final appearance of the paint and perhaps also the storage stability of the powder paint, or even cause a premature reaction in the extrusion phase (key step in the production process of powder coatings). We could say that the ideal catalyst should therefore accelerate the reaction of the paint at a selected curing temperature without affecting the paint properties during the process preparation and the storage phases.
The process of applying powder coatings requires electrostatically charging the particles of solid paint that have to adhere to the metal object discharged to the ground. Obviously in this phase it is important that the powder paint remains graphed to the metal object to be coated in its path from the exit of the application area until it arrives to the curing oven.
A couple of options are possible for this step: either apply an electric field that charges the paint particles or induce charging of the paint particles via friction with an insulating material (tribocharging). Special additives can facilitate this second option, and considering almost all of them are solid, they can be dispersed once again using polyester resins as a carrier. Table 3 shows an example of tribo chargeability measurement using the Kleber laboratory test. The higher the amount of charge, the more effective the application and permanence of the powder coating on the substrate will be.
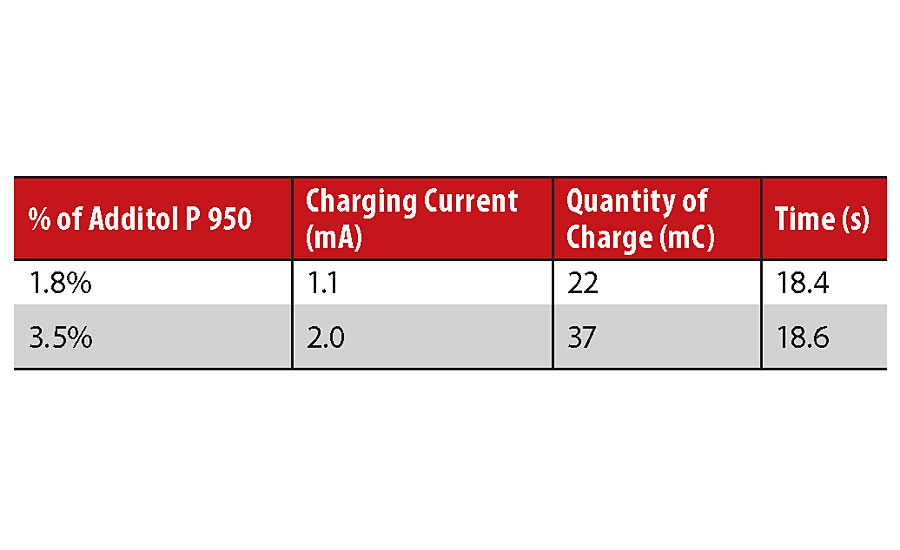
Other Special Products for Powder Coatings
Other special products are usually components of the paint formulation that help obtain special finishes such as a matte finish, textured finish or wrinkle effect (Figure 3).

In order to obtain these types of finish effects it is often necessary to formulate the paints using alternative products that are not necessary when formulating conventional glossy paints. An example is high-viscosity glycidyl acrylics, which can react with carboxylated polyesters to obtain a matte coating without the need to use the more conventional and complex process of physically mixing two paints (commonly dry-blend) with different reactivity and functionality. In this specific case the matte film has very interesting aesthetic characteristics considering that the light is only reflected to a limited degree, drastically reducing the gloss of the surface.
Another example is the wrinkled finish that is normally obtained through the use of a special catalyst for the reaction between a hydroxylated polyester and a glycoluril hardener. This is quite a complex chemistry where, among other things, related alcohol is released as a secondary product.
The chemistry of those products is often different when compared with more conventional binders used in powder coating technology. Particular mention should be made with polyanhydrides, which can be aromatic or aliphatic, a factor that affects the outdoor resistance of the final paint. These polyanhydrides can react with hydroxylated polyesters to obtain paint films with excellent thermal resistance or with glycidyl groups such as epoxy resins or glycidyl acrylics (Table 4).
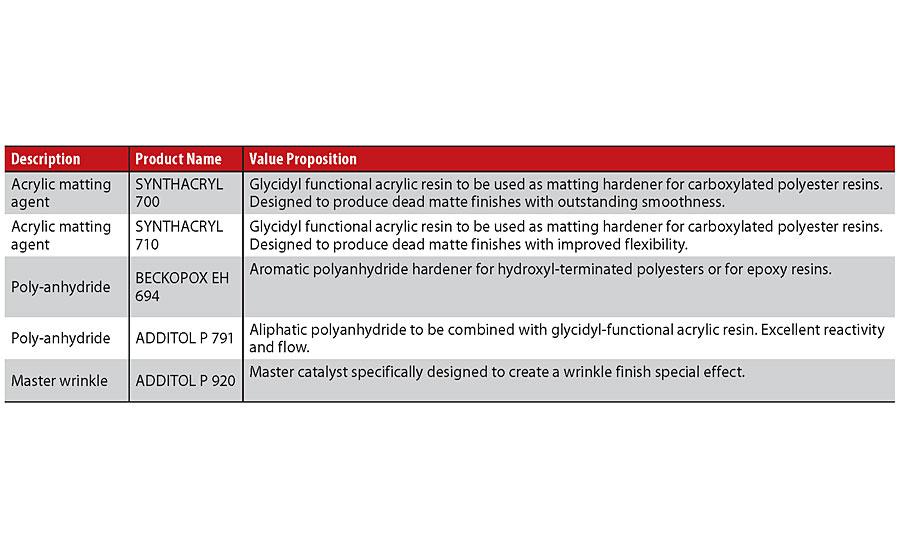
Interesting is the case of anhydride of dodecane-dicarboxylic acid, which melts at a lower temperature than the corresponding acid. This leads to a different flow of the paint when acid or anhydride react with the same glycidyl acrylic resin. In fact, during the fluidization phase of the paint, a lower viscosity is reached with the polyanhydride, which has a positive impact on the flow of the acrylic cured film (Figure 4).
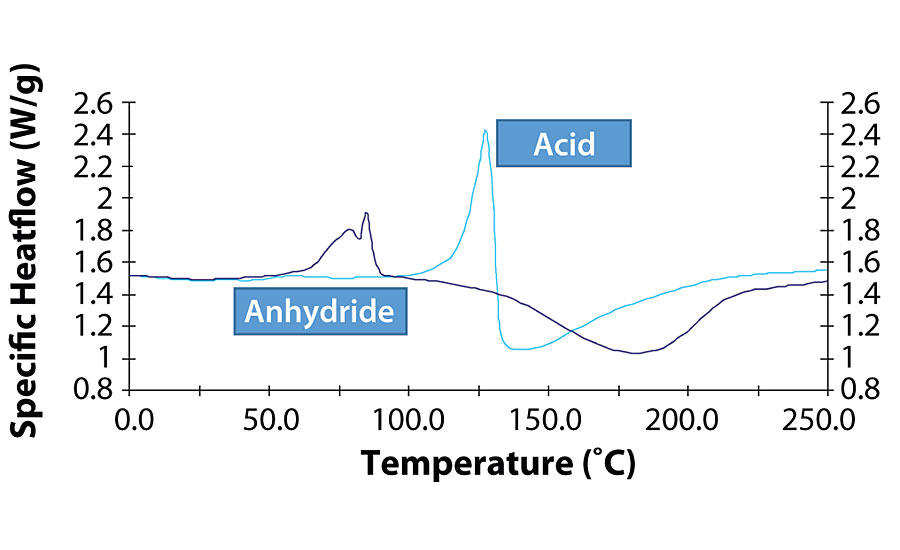
Conclusion
In this journey through the world of additives and other special products, we can certainly say that all of them play an important role in the field of resins and paints in powder coatings. We can therefore agree with Arthur Conan Doyle when he said that “small things are by far the most important.”
References
1. Winkler, J. Dispersing Pigments and Fillers, European Coatings Tech, 2012.
2. Duivenvoorde, F. Pigment Dispersing in Powder Coatings: Synthesis and Use of Block Copolymer Dispersing Agents, TU/E, 2000.
3. Spyrou, E. Powder Coatings Chemistry and Technology, European Coatings Tech, 2012.
4. Misev, T.A. Powder Coatings Chemistry and Technology, Wiley & Sons, 1991.
5. Muller, B.; Poth, U. Coatings Compendia – Coatings Formulation, 2006.
6. Adler, J. Film Formation and Surface Tension Studies of Powder Coatings, KTH, 2005.
Looking for a reprint of this article?
From high-res PDFs to custom plaques, order your copy today!