Significance of Coal Tar Tape in Underground Pipelines

As we are about to cross two decades into the 21st century, it may sound regressive talking about coal tar-based coating technologies for protection of underground pipelines. However, looking around, it is apparent that in the Indian (as well as African) subcontinent there is a maze of water transportation pipelines being laid that faithfully relies on the proven track record of coal tar products (commonly referred as wrapping coating) for underground installations. Thus, let us look upon various coal tar-based anti-corrosive systems used for UG piping and their relevance in today’s industry, especially the widely used torch-applied coal tar tapes.
An underground pipeline can be conceptualized as one integrated structure that passes through a variety of phases – across its length and in the changing surroundings in the same location over time. In India, all UG pipelines have to pass through different types of soil. It can be sandy, clay or a mix of both in varied proportions. A clay-type soil is more expansive and exerts higher stress on the buried pipeline than a sandier soil. This happens when the soil is subjected to top-down water ingress during the rainy season or due to bottom-up capillary rise of moisture while in a geography having a higher water table.
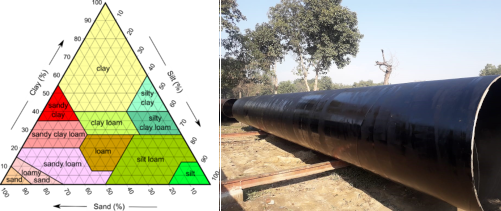
Similarly, a sandier soil has higher thermal conductivity than a clay soil, resulting in higher temperature at the soil crust surrounding the pipeline, and in turn resulting in acceleration of chemical reactions in the vicinity. Most of the topography in India is agricultural land, and years of farming activity results in the soil holding large traces of chemical fertilizers along with natural mineral salts. These turn aggressive while in contact with water, causing gradual dissolution of the pipe coating material. Soil also contains microbes, which initiate biodegradation of all materials buried in it. Further, tree and plant roots expand their way into the soil at a snail’s pace, but have the capability of piercing through very hard substrates. These are some of the challenges that an underground pipeline is subjected to.
Coal tar, by virtue of its two inherent properties, became the first choice of formulators for developing an anti-corrosive system to protect buried structures. It possesses high resistance against degradation through soil bacteria as well as repellency towards root infiltration.
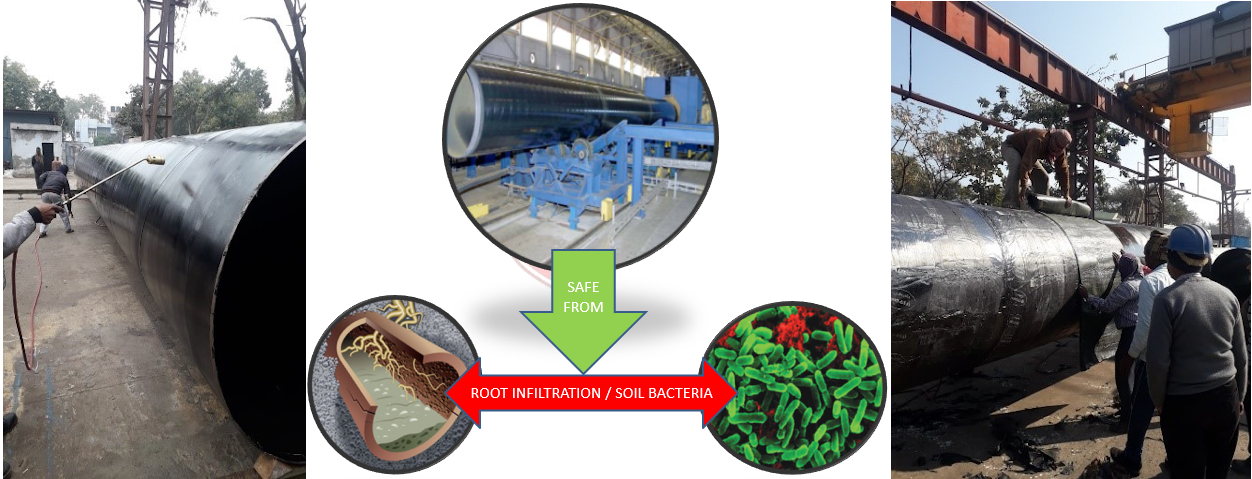
During the initial years, coal tar was utilized to develop anti-corrosive paints in low-build and eventually high-build mastic forms. It is still widely being used in small structures like UG fuel tanks in petrol pumps as an anti-corrosive outer coating. But pipelines require more than just a barrier protection, and needed a system that has enough mechanical strength to sustain soil stresses and possible physical damages that may occur during laying and filling activities. A five-step enamel coating system was adopted for coating pipes with a 4- to 4.5-mm thick protective layer.
Coal Tar Enamel Wrapping Coating System
- Primer – chlorinated rubber and synthetic plasticized primer.
- Coal tar enamel – hot-pour coal tar enamel modified by inert mineral filler.
- Inner wrap – reinforced glass fiber mat.
- Coal tar enamel – hot-pour coal tar enamel modified by inter mineral filler.
- Outer wrap – impregnated and coal tar enamel coated reinforced glass fiber mat.
The above system has been covered by British Standards under BS-4164 for Grade 105/8 (-25 °C to +65 °C) and Grade 120/5 (-5 °C to +80 °C) of coal tar enamel. The American Water Works Association has also covered it under AWWA C-203, Type 1.
With time, the enamel system is gradually becoming obsolete, largely due to unavailability of trained contractors for carrying out such a cumbersome application process, and mainly after high-tensile fiber-reinforced tapes were developed to substitute the old format. The new taping product not only matches the strength and bonding characteristics of the older system, but also exhibits better electric resistivity and has high resistance against dissolution.
Today’s coal tar tape is an integrated, factory-made product that is easy to apply, either inside a pipe manufacturing facility or at a project site where pipes are being commissioned. It comprises a five-layer anatomy where a high-tensile glass fiber fabric is sandwiched with high-quality coal tar modulate, designed with a thicker overlay towards the pipe substrate side for heat fusing on primed steel substrate.
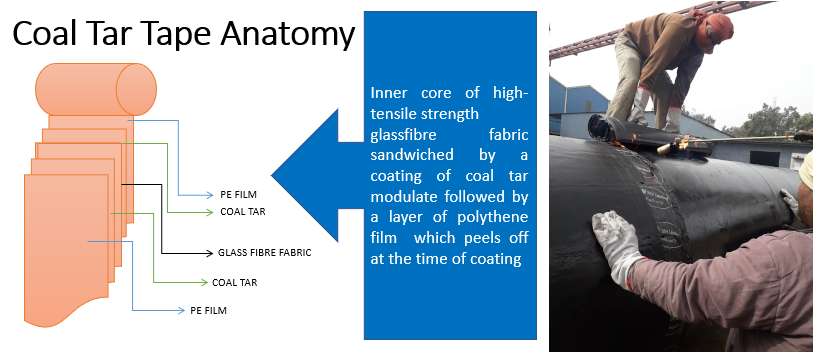
While hot-applied coal tar tape is a widely accepted technology for UG pipes; especially for raw water intake pipeline in power plants, fire hydrant water pipeline loops within process plants and similar circulating water handling piping across the industry, it is important to understand the quality parameters based on how its long-term dependability is designed.
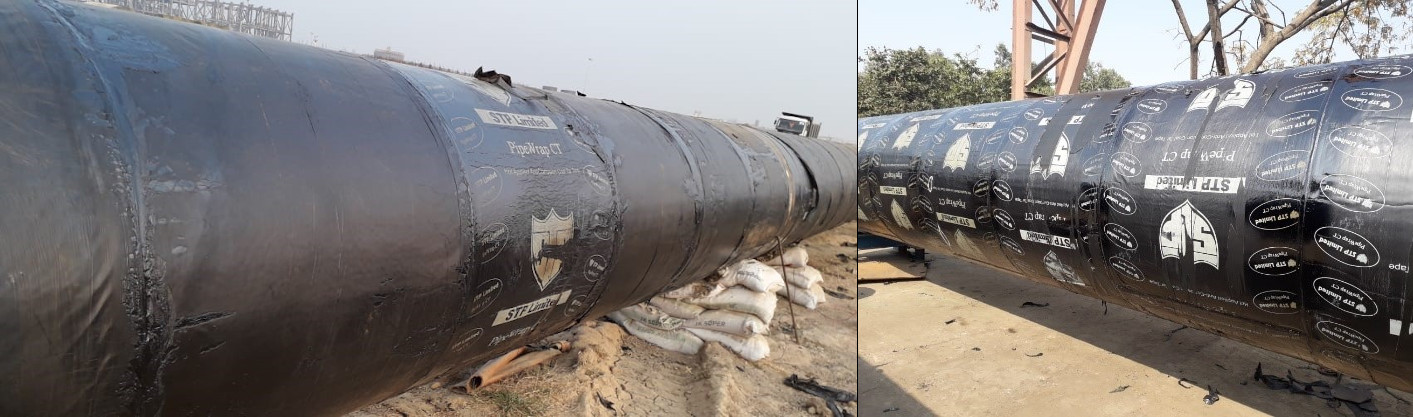
Quality Aspects of a Coal Tar Tape
The Bureau of Indian Standards has detailed the requirements for coal tar tapes. Their initial release in 1982 under IS:10221 titled, “Code of Practice for Coating and Wrapping of Underground Mild Steel Pipelines” included guidelines for both enamel and tape application. Eventually an IS Standard was released in 2003 exclusively for coal tar tapes under IS:15337 titled, “Coal Tar-Based Anticorrosion Tape for Protection of Underground Mild Steel Pipelines – Specification”. A revision of IS:10221 in 2008 indicated that older requirements of coating wrapping materials has been withdrawn and IS:15337 be considered as the required specification for CT Tapes. Thus, in the present scenario, IS:15337-2003 is the sole exclusive guideline for coal tar-based anti-corrosion tapes for protection of underground mild steel pipelines.
Check Points for Coal Tar Tapes
It has been a perennial problem of project engineers to identify high-quality coal tar tapes from mere “black tapes”. These may be considered as the checkpoints from a QC perspective.
Pre-Application Tests
- Density – Coal tar tapes are manufactured in 2-mm, 3-mm and 4-mm thicknesses, and the density of a tape is at the rate of 1.5 kg per mm per square meter with an allowable tolerance of 10%. This should be checked by weighing any supplied roll randomly.
- Thickness – While the density has an allowable tolerance of 10% it is not to be misconstrued as tolerance for thickness. Thickness of the supplied tape must be randomly measured for QC clearance in order to see if it meets the specified thickness.
- Flexibility – A high-quality coal tar tape will not be too flexible, particularly at lower ambient temperatures. Before unwinding a roll for application, it becomes conducive to place it under the sun in order to make it more pliable for application. As compared to this, a bitumen tape is extremely flexible by nature.
- Odor – Coal tar has a distinctive pungent odor in all coal tar-based products. Any other tape made out of black bitumen will not have this odor.
- Petrol dissolution – IS:15337-2003 lays down a stringent quality criterion in order to attach high resistance of the tape against dissolution. For effective testing, it requires immersing a specified section of the tape in petrol. After 24 hours the loss of weight should be maximum 5% (EIL specification no. 6-79-0011 Rev.2 exempts it up to 7%).
Post-Application Tests
- Destructive testing – In line with IS:15337-2003 guidelines, adhesion and impact tests are carried out to ascertain bonding strength of the tape after 72 hours of application.
- Non-destructive testing – Based on thickness of the tape, a spark test at suitable voltage, as per IS recommendation, should be carried out in order to spot and repair holidays.
These tests can be easily carried out at the project site (for petrol insolubility, random samples may be sent to a NABL-certified lab to check conformance).
Other than mastic, enamel and tapes, coal tar hybrid formulations blended into epoxy has evidently shown excellent resistance in saline environments and have become a preferred choice for coastal infrastructure. The latest enhancements of single-coat high-build coal tar epoxies have reduced considerable labor costs by eliminating the need to apply multiple coats.
New chemistries in protective coating are emerging with time, however, it is well understood that every project is a marriage between technology and affordability. While we still have a long time to spend with coal tar-based anti-corrosive technologies, it is important to remain in congruence with the required technical understanding of these products in order to get the best out of them.
Looking for a reprint of this article?
From high-res PDFs to custom plaques, order your copy today!