In today’s competitive manufacturing environment, pipe and tube manufacturing companies are continually challenged to manufacture superior products. End-use customers require a better product, more competitive pricing and improved lead times, year-over-year.
While each pipe and tube manufacturer has specific regional and market issues, it is critical they continue to drive process efficiencies to improve their existing manufacturing operations, thus helping them meet their customers’ needs. One other important customer requirement is that pipe and tube manufacturers improve their sustainability footprint, such as reducing volatile organic compounds (VOCs) and hazardous air pollutants (HAPs).
The pipe and tube market can be broken down into three distinct vertical markets: mechanical tube, safety/water suppression pipe, and OCTG/line pipe. All three market verticals have similar end-user customer requirements. This article focuses on the mechanical tube marketplace.
Mechanical Tube Marketplace
The mechanical tube marketplace provides products for fencing, carports, irrigation systems, security, structural and many other related areas.
Most manufacturers of these products incorporate some type of coating system into their tube manufacturing process. In most cases this involves a water-based coating system utilizing a flood and wipe or vacuum application, and some type of air flow and/or thermal drying system at end-of line, before tube cut-off.
This coating system provides an in-line coating that is applied to the mechanical tube, which delivers enhanced outdoor protection from humidity and temperature during transport, yard storage and end use.
In their quest to continue to reduce overall tube costs, mechanical tube manufacturers must continuously review their internal processes. One of the areas for review has been the type of coating applied to the tubes. Over the past decade, many mechanical tube manufacturers have reviewed their water-based coatings against UV coatings solutions.
UV Coatings vs. Water-Based Coatings
Water-Based Coatings
There are a significant number of mechanical tube manufacturers utilizing water-based coatings for their coating needs today. For manufacturing lines running less than 150 feet per minute, the investment cost for implementing a water-based coating line can be lower than a traditional arc lamp UV line. A simple flood and wipe with induction heating or heated air tubes will typically do the trick and provide a temporary rust inhibitor for the tube. Utilizing induction heating will greatly reduce the humidity and temperature issues that impact water-based coating applications.
Cost per gallon for water-based coatings is much lower than UV coatings, since percent solids for water-based coatings range from 18% to 30%; but you also get less coverage per gallon. This is where the ROI calculator in Table 3 will assist you in understanding coverage per gallon when comparing water-based coatings to UV coatings.
The UV Alternative
Ultraviolet coatings technology offers a unique opportunity to dramatically improve the manufacturing process, improve the sustainability footprint and deliver real ROI – less coating cost per linear foot of pipe or tube. Mechanical tube manufacturers are quick to embrace UV coatings once a detailed cost analysis is completed, as outlined below.
Customer Case Example
Industry: Mechanical Tube
Application: External Protective Coating
The top five specifications for mechanical tubes are listed in Table 1.
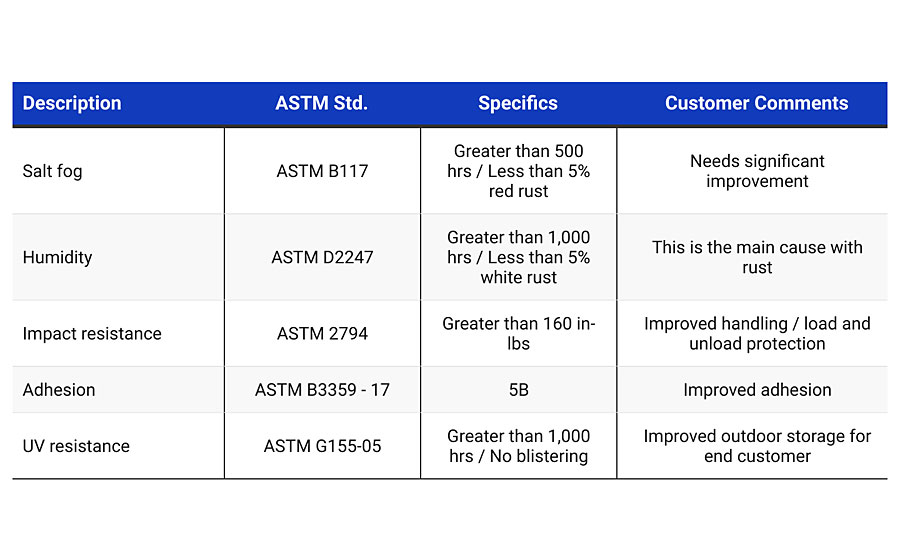
Goals:
- Reduce end-user complaints
- Improve aesthetic appearance
- Improve corrosion resistance – less than 5% red rust
- Increase line speed
- Eliminate VOCs and HAPs
- Minimize humidity and temperature impacts on the coating process
This Customer Case Example is broken into the following sections:
- Current WB Coating and New UV Coating
- Specification and Testing Results – Comparative Testing Results
- Process Improvements
- ROI – Return on Investment
- Process Solution/Equipment
Current WB Coating and New UV Coating
Current Solution:
Water-based coating/~11% co-solvent (flammable)
24.5% solids by volume – 393 square feet at 1.0 mil WFT (wet film thickness)
$18.55 per gallon
New Solution:
UV coating (no solvent, no water, no VOCs)
100% solids by volume – 1,604 square feet at 1.0 mil WFT
$69.40 per gallon
Specification and Testing Results
Table 2 shows the top five specification results between a water-based and a UV coating.
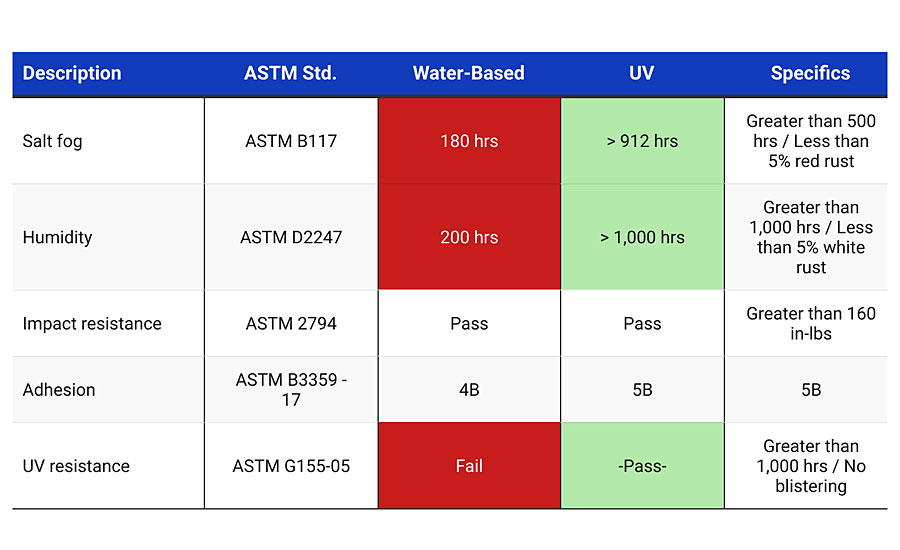
The real proof is in the pictures.
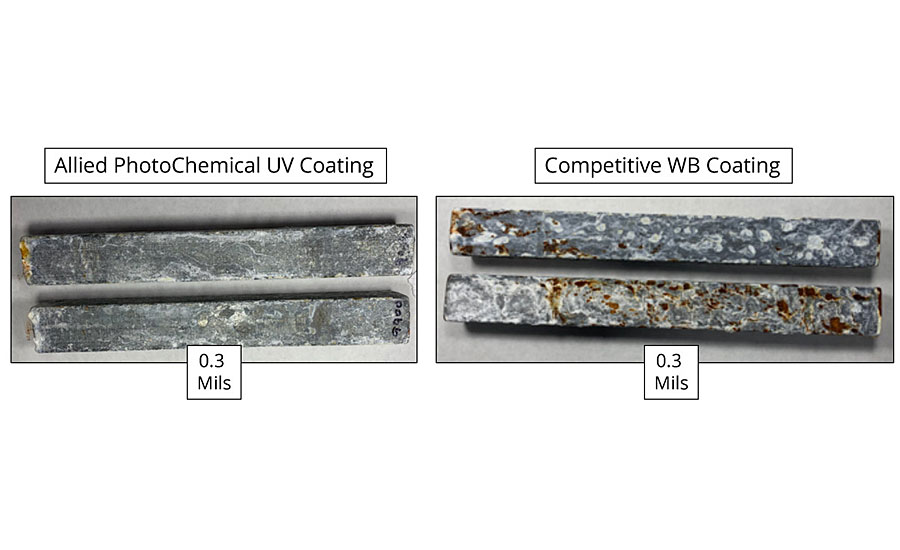
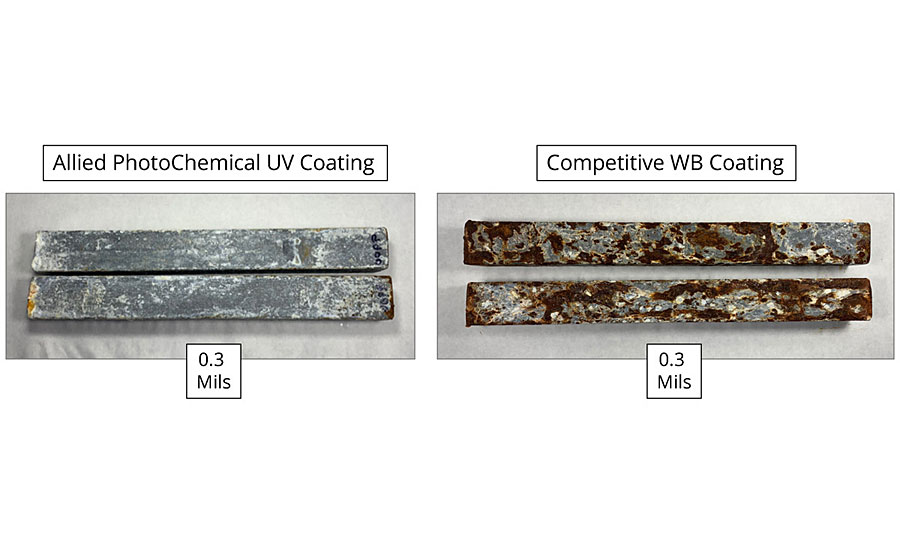
Process Improvements
Faster Production/Coating Cure: Overall, the UV coating process allowed the tube manufacturer to increase its lines speeds from 175 feet per minute to over 275 feet per minute, an increase of over 50%. UV coatings are not susceptible to humidity and temperature issues, like water-based coatings. Plus, the instant cure of UV eliminates any wet coating downstream, greatly reducing safety and quality issues with racking/packing of the mechanical tube.
Smaller Shipping, Quality and Energy Costs: UV coatings contain no water, solvent or fillers. The existing water-based coating contains nearly 60% water and 11% solvent, making up almost 70% of the WB coating. Transportation costs are reduced significantly when compared to UV coatings. Plus, UV coatings are not flammable. Overall, quality costs are reduced mainly due to the elimination of wet-coated mechanical tube reaching the cut-off and racking material handling system. Energy costs are less when comparing UV lights to thermal induction heating.
Cleaner: UV is inherently cleaner than water-based coatings – no VOCs or HAPs. Plus, eliminating the handling/exposure of flammable water-based coatings on the plant floor makes for a safer and cleaner overall coating operation.
ROI – Return on Investment
Table 3 shows a cost per linear foot comparison between water-based and UV coatings.
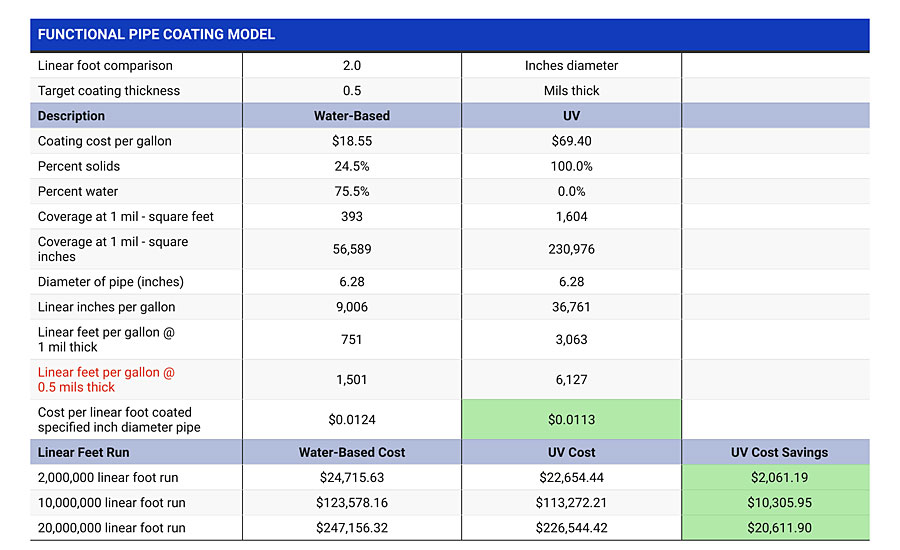
UV Process Solution/Equipment
Based on the results of the testing and cost analysis, the customer made the decision to implement a new UV coating system (Figure 3), which was being installed at the time this article was written.
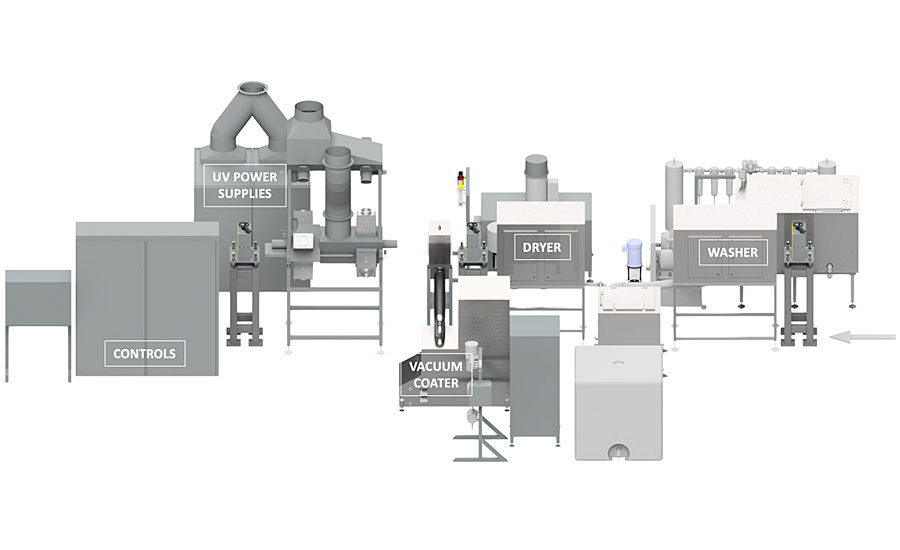
Conclusion
The mechanical tube marketplace has become increasingly competitive – driven mainly by the continued emphasis of customers for an improved product, along with more competitive pricing levels. Mechanical tube manufacturers must continue to innovate and challenge the status quo of their manufacturing processes to meet these demands.
Conversion to UV coatings allowed tube manufacturers to run faster production speeds, greatly reduce their shipping costs/handling of coatings and implement a much cleaner, green, sustainable process, while delivering an improved ROI to the bottom line.
For more information, visit www.alliedphotochemical.com.
Report Abusive Comment