A New Technical Solution to Cover the Orange Color Space

One of the main tasks of coatings manufacturers is to cover the full color space, offering a wide variety of high-quality coatings in a large range of applications. An important part of their know-how is focused on pigment selection. They have at their disposal inorganic pigments, rather known for their opacity, outdoor durability and thermal stability, and organic pigments offering highly chromatic colors at the expense of lower durability. Depending on the resins used and the targeted markets, the right pigment combinations must be determined to achieve the required properties, avoiding challenges such as pigment settling, floating, high viscosity, metamerism and so on.
In the last decades, a worldwide, regulation-driven evolution in inorganic pigment offerings has been observed, with the progressive withdrawal of the lead-containing pigments Chrome Yellow (PY34) and Molybdate Orange (PR104) from the market. These two pigments are well known for their bright shade, high opacity, high gloss and good durability, but unfortunately their toxicity leads authorities throughout the world to ban their use today and in the near future. Ever since, it has been a challenge for the coatings industry to replace these pigments, and in some cases, technical improvements are still needed.
For the greenish yellow spectrum, Nickel Titanate (PY53) and Bismuth Vanadate (PY184) are widely used.1 Bismuth vanadate is characterized by a very greenish, highly chromatic shade, whereas nickel titanate offers more thermal stability at the expense of lack of chroma and color strength. The recently developed pigment Niobium Tin Pyrochlore NTP (PY227) covers the mid yellow shades, offering thermal stability advantages against certain bismuth vanadates. For the more reddish yellow to orange shades, inorganic pigments available are CICPs (complex inorganic colored pigments) Chromium Titanate (PBr24) and Rutile Tin Zinc Orange (RTZ, PY216 and PO82). Even though the aforementioned RTZ chemistry offers a higher chroma than the buff-colored chromium titanate, none of these pigments can achieve the chroma obtainable with the bismuth vanadate chemistry, and there is consequently a gap in the orange color space.
The missing link of bright orange shades with high chroma and tinting strength can be achieved with bismuth oxyhalide solid solutions of general formula BiOBr(1-x)Ix, as described in the 1980s by Du Pont de Nemours (Figure 1).2 A solid solution is a technical term of the solid-state chemistry describing a homogeneous solid phase capable of existing throughout a range of chemical composition with a single crystal structure, in this case a tetragonal PBFCl-type structure (Figure 2). With this chemistry and technology, a broad color spectrum from bright reddish yellow to reddish orange is obtainable by increasing iodine amount. Conversely, the physical mixture of colorless Bismuth Oxy Bromide (BiOBr) with the brick red Bismuth Oxy Iodide (BiOI) leads to duller brick red colored powders with unchanged hue of the color compared to BiOI. The morphology of the pigments is plates of size 0.2-0.5 µm and thickness from a couple of nanometers.
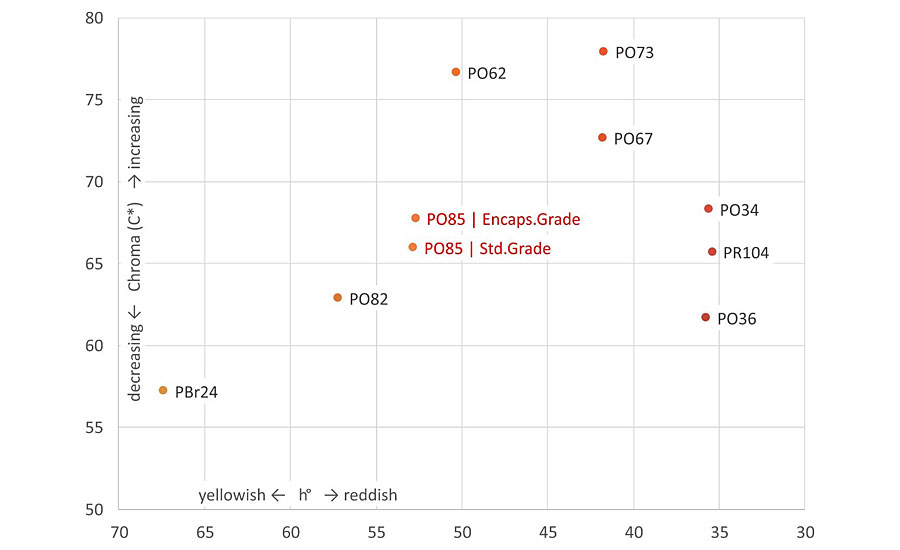
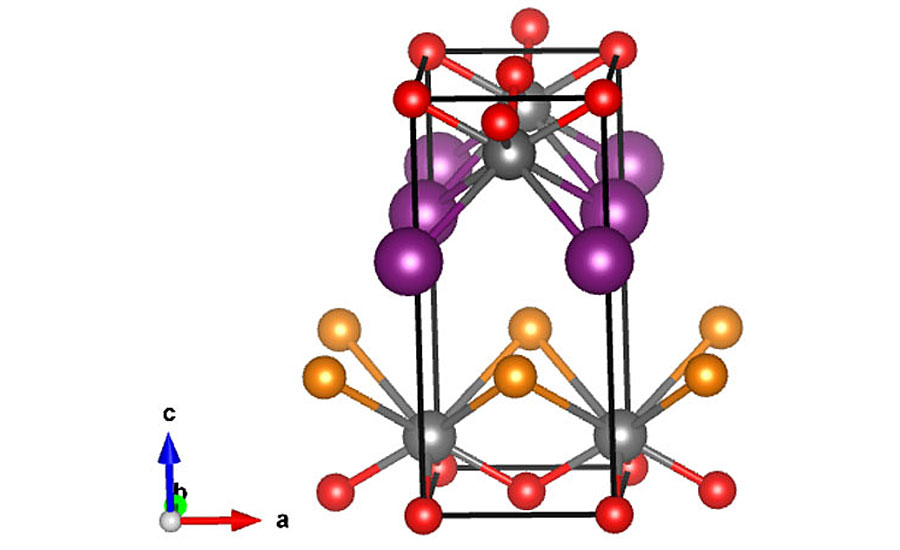
Despite their vibrant color, the BiOBr(1-x)Ix pigments obtained by wet precipitation process were not commercially viable due to their low chemical stability. As the inherent properties of BiOBr(1-x)Ix, including its chemical stability and outdoor durability, depend on the chemical composition, it is however possible to radically improve these properties by playing with doping agents or by stabilizing the pigment with several layers of metal oxide(s). Another methodology to improve pigment properties is to encapsulate the core pigment. Ferro has continuously dedicated R&D resources to improve the properties of BiOBr(1-x)Ix for targeted applications, combining aforementioned technologies with its historical know-how of the bismuth vanadate chemistry. As a result, Ferro has been the pioneer to develop, register and commercialize a range of innovative, durable and patented pigments, for which color index PO85 has been assigned (Figure 3).3 Application-optimized commercial grades include Lysopac Orange 6820B for general purpose industrial coatings, Lysopac Orange 6821B for waterborne coatings and soon-to-be-launched Lysopac Orange 6823B with improved outdoor durability.
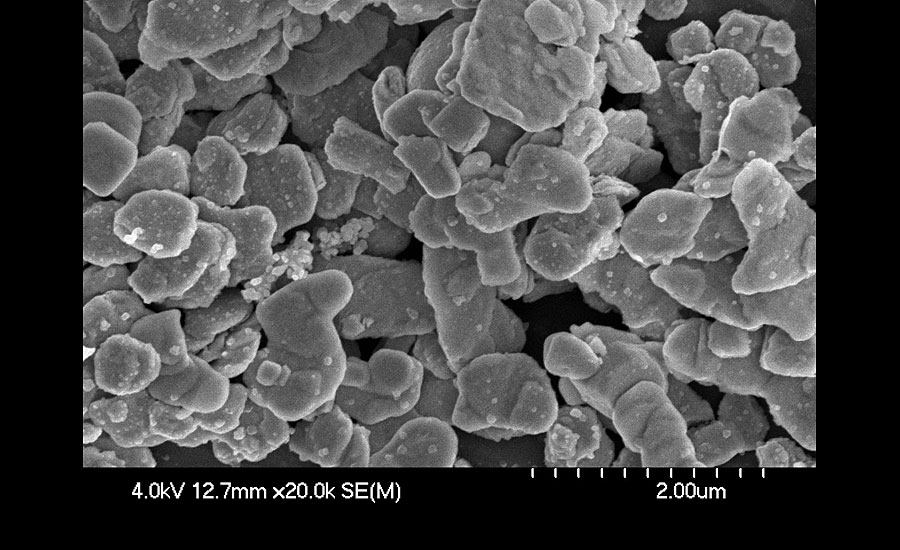
Technical Performance: Solvent-Based Alkyd/Melamine
The pigment performance of Lysopac Orange 6820B and 6821B, respectively core pigment PO85 and an encapsulated version, are summarized in Table 1 with the comparative values of commercially available inorganic orange pigments. PO85 shows excellent coloristic performance, achieving high-gloss finishes in full shade applications, outperforming chromium titanate (PBr24) and RTZ Orange. In white reduction, its tinting strength is much stronger, with up to 180% relative tinting strength compared to PBr24 and up to 130% compared to RTZ Orange. Its excellent opacity is similar to RTZ Orange and PBr24, while showing outstanding dispersibility and viscosity. PO85 is also fit for purpose for outdoor durability, heat fastness and overspray fastness, with properties approaching the CICPs PBr24 and RTZ Orange, which are well known for their stability.
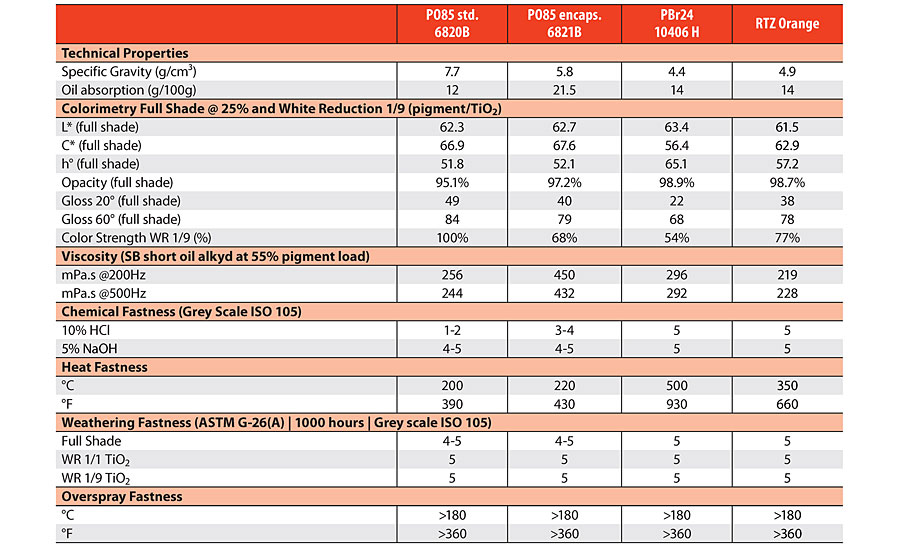
Another added benefit is its high Total Solar Reflection (TSR) of 55% (Figure 4), outperforming PBr24 in the visible spectrum, and outperforming RTZ Orange both in the visible and NIR range. With the ever-increasing concerns on global warming, PO85 can act as “Cool Color” solution to decrease the solar heat build-up in real estate or other applications.
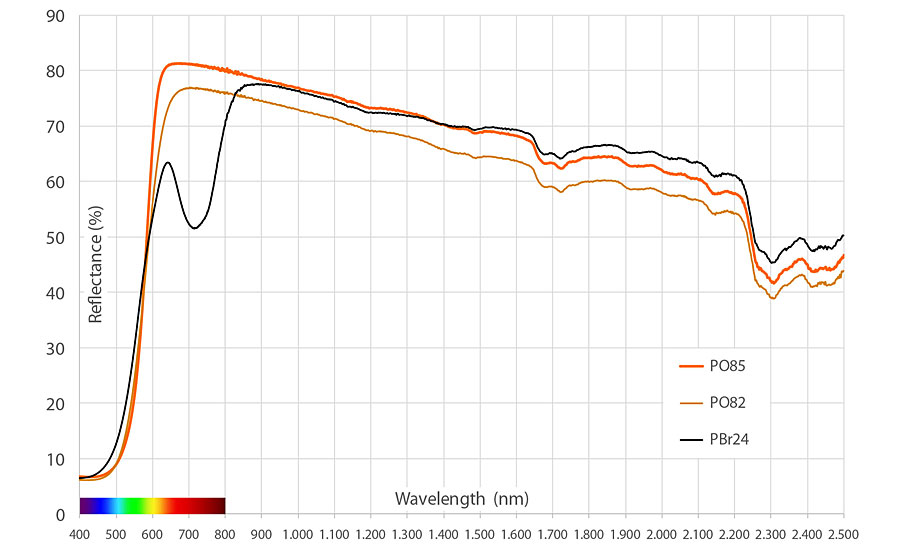
These overall properties fit to the expectation for an inorganic pigment and make PO85 an excellent candidate as a colorant for coatings, giving the possibility to prepare high-performance coatings and concentrates at high pigment loading. PO85 is also highly suitable for powder coatings (such as Polyester/Primid XL552 95:5) with outstanding durability performance, creating again new possibilities to cover the orange spectrum for this application. Furthermore, its high heat fastness makes it recommendable for coil coatings applications.
Increasing the Color Envelope
Thanks to its distinctive color and shade, PO85 is an ideal pigment to combine with Bismuth Vanadate (PY184) as color range extender from greenish yellow to orange (Figure 5). The most noticeable added value of PO85 is its vibrancy, brightness and cleanliness of the shade, with DC* values up to 5 and 12 compared to RTZ Orange and chromium titanate (respectively) at equal hue. Consequently, it achieves a broader color palette and covers parts of the orange spectrum that were difficult to reach using RTZ Orange or PBr24 (Figure 6).
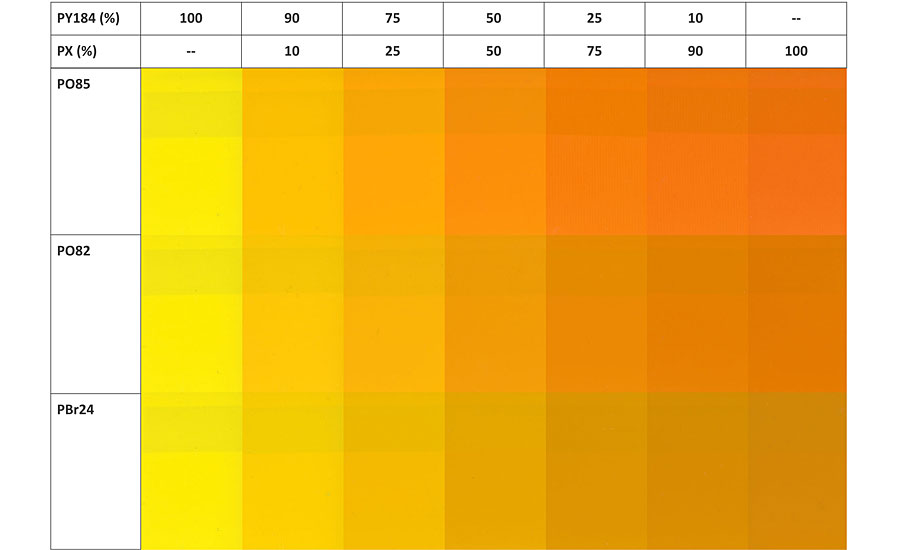
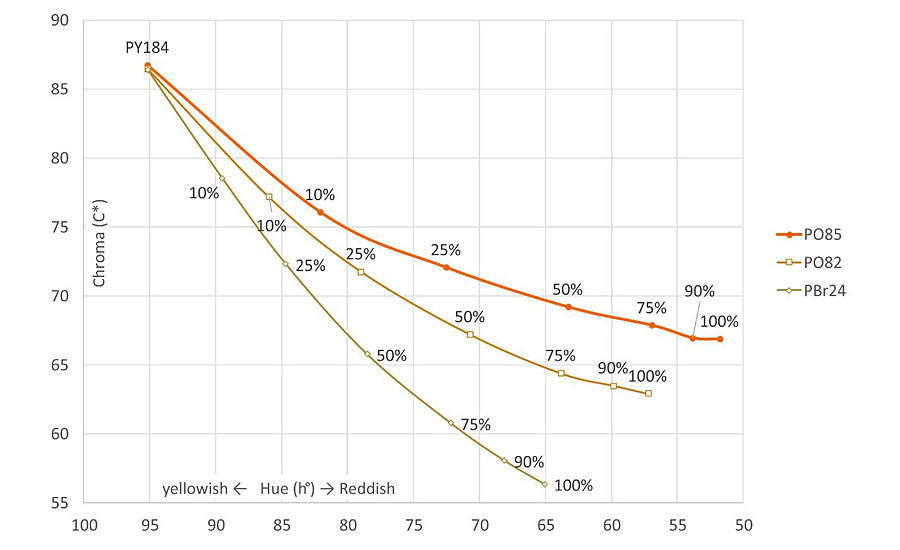
Drawbacks and Pitfalls
PO85 is a bismuth-based pigment, and as such the core pigment shows an inherent weakness in terms of resistance towards acid and alkaline agents. In solventborne coatings this weakness is majorly compensated by the protective barrier from the binder system. Waterborne coatings with high pigment volume concentration for outdoor architectural applications are, however, limited in their protective role, having an open pore structure. It is therefore advised to use encapsulated versions of PO85 for waterborne coatings, such as Lysopac Orange 6821B, as they have been specifically developed for these applications. Even though encapsulated versions of PO85 are characterized by a decreased tinting strength, their relative strength is still similar to RTZ Orange. Moreover, the bright, clean shade in full shade applications remains unaffected, and are therefore still the better performer.
Another specificity of this color index is the flake morphology of its primary particles. As with all the flake particles, it may suffer from over-milling, as primary particles are large enough to be broken or eroded by the shear forces applied during the milling. It is thus important to carefully control the milling parameters such as time, speed and temperature, as this is usually the case for all the pigment dispersions.
Summary
Bismuth oxy iodide/bromide chemistry (PO85), obtained by wet precipitation process, results in vivid orange colors, but stability issues limited the use of this chemistry on the market. Ferro has developed a series of durable products during the last years and has demonstrated their possible uses in a wide range of applications, offering to the coatings industry a new possibility to produce heat-stable, weatherable, bright and clean shades from the orange yellow to the reddish orange. The pigments can be used alone, but thanks to their good dispersibility and opacity, are also excellent shading components to expand the color envelope by mixing with other high-performance inorganic or organic pigments.
Applications are liquid coatings, both solventborne and waterborne systems, but the pigment shows also excellent properties in powder coatings. The high total solar reflectance makes this product range highly suitable for cool coatings applications.
Experimental Notes
-
Pigments were evaluated in a solventborne short-oil alkyd/melamine baking enamel (Allnex Setal 84 XX-70/Allnex Setamine US 136), with the mill base prepared at 55% pigment load in short-oil alkyd. Drawdowns were prepared at 25% pigment load at respectively 100 µm WFT full shade and 75 µm WFT white reduction 1/9, and were cured at 120 °C for 30 min. Coloristic values were measured according to CIE1976 at 10°/D65, with color strength calculated according to ISO 787-26 (weighted K/S).
-
The mill base viscosity was measured using an Anton-Paar Rheolab MC1 equipped with a spindle Z3DIN.
-
The acid and alkaline stability were evaluated by addition of droplets of 10% HCl and 5% NaOH on a cured full shade coating, and visual assessment after 24 hrs using the grey scale (ISO 105 A02).
-
The heat fastness of the full shade and white reduction 1/9 was assessed by curing at stepwise increasing temperature and is defined as the maximum temperature at which there is no observable visual degradation vs. the default curing temperature.
-
The overspray fastness was evaluated by applying a white paint (alkyd/melamine) on top of a cured full shade or white reduction 1/9, and the recoated panels were cured at stepwise increasing temperature. The overspray fastness is defined as the maximum temperature at which the degree of bleeding into the white paint is negligible according to the grey scale.
-
The weather resistance was determined by exposing coated steel panels (full shade or white reduction 1/9) for 1,000 hrs in a Weather-Ometer (Atlas) according to standard ASTM G-26(A).
References
¹ Faulkner, E. B.; Schwartz, R. J. High Performance Pigments, 2nd Edition. Wiley-VCH, 2009.
² Shannon, R. D. Bismuth oxyhalide solid solution. U.S., Patent No. 4252570A, 1979.
³ Verspaille, G. ; D'haeveloose, J. ; Devreux, V. ; Clabaux, E. A Coated Bismuth Oxy Halide-Based Pigment. W.O., Patent No. WO/2017/102735, 2017.
Looking for a reprint of this article?
From high-res PDFs to custom plaques, order your copy today!