Pigment Dispersion Procedures

In the last article we discussed high-speed dispersion. In this article we will continue the discussion on dispersion, this time using a quick screening method I developed using a dual axial centrifuge. This procedure saves time and allows significantly higher output. During the development of this process, I used a lab sandmill and high-speed disperser to make grinds, and compared the results to those made with the new method. The method was adjusted until results for several different dispersants coincided. Differences in tint strength and grinds were within error of the test.
Pigment dispersants are tested by adding standard or predicted amounts of dispersants to pigment/water or pigment/resin blends by varying the levels of dispersant with relation to the amount of pigment. Dispersant is added on a percent-actives basis with regard to the amount of pigment solids. These mixtures are subsequently dispersed using mechanical energy, with a high-speed blade for inorganic or extender pigments or a media mill for organic and carbon black pigments. The particle size of the mixture is then measured. When an optimal particle size is achieved, the viscosity of the grind is measured. The usage versus viscosity curve resulting from measurement of the viscosity of various levels of dispersant in a pigment identifies the potential of the molecule as a dispersant and the optimal level of dispersant.
Traditional lab procedures to screen dispersants have required minimum sample sizes of several hundred grams. This leads to increased consumption of raw materials, increased levels of waste produced, and more time to accomplish the dispersion. To increase efficiency, a new dispersion method was developed using a dual axial centrifuge. Sample sizes of 35 – 60 grams can repeatedly be dispersed with a tint strength variation of around +/- 2%. The procedure is also significantly quicker than traditional lab milling methods since you can do multiple dispersions concurrently. Since there is no mill or disperser to clean, there is a huge time raw and material savings.
There are several manufacturers of dual axial centrifuges, but the procedure is the same for most of them. Contrary to the name of this machine, it is a mixer and not a separator. In this method, “machine” will refer to a dual axial centrifuge.
Using traditional media mills, you can normally do two to four dispersions in a day. Using this procedure, 12 dispersions per day are possible including addition to paints and application of the paints.
Items needed:
- Coatings raw materials and a balance (0.001 g preferred);
- Dispersion media for organic pigments and carbon black (Zirconium beads);
- One small mix cup for each dispersion (up to three are done at a time);
- One medium mix cup for testing the tint strength of the dispersion in paint;
- Method of determining tint strength or color of the coating;
- Substrate and application apparatus.
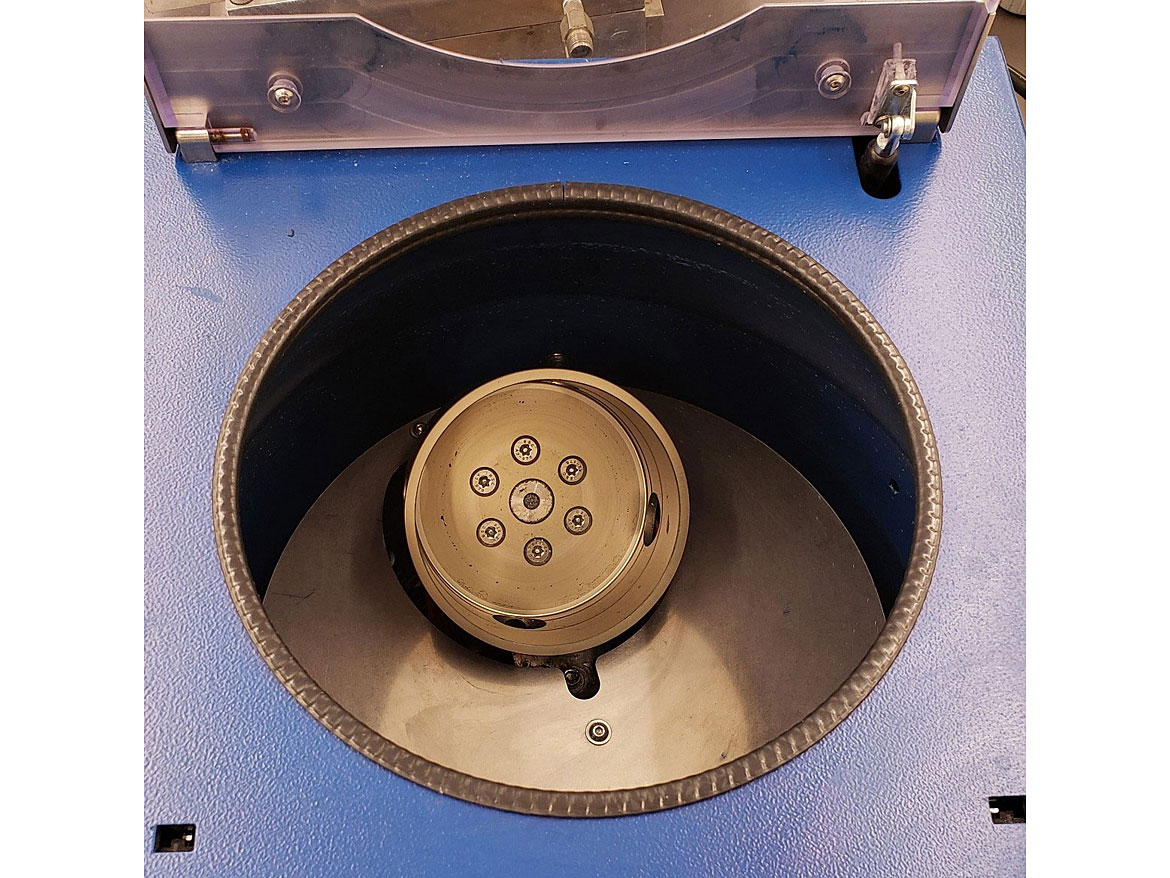
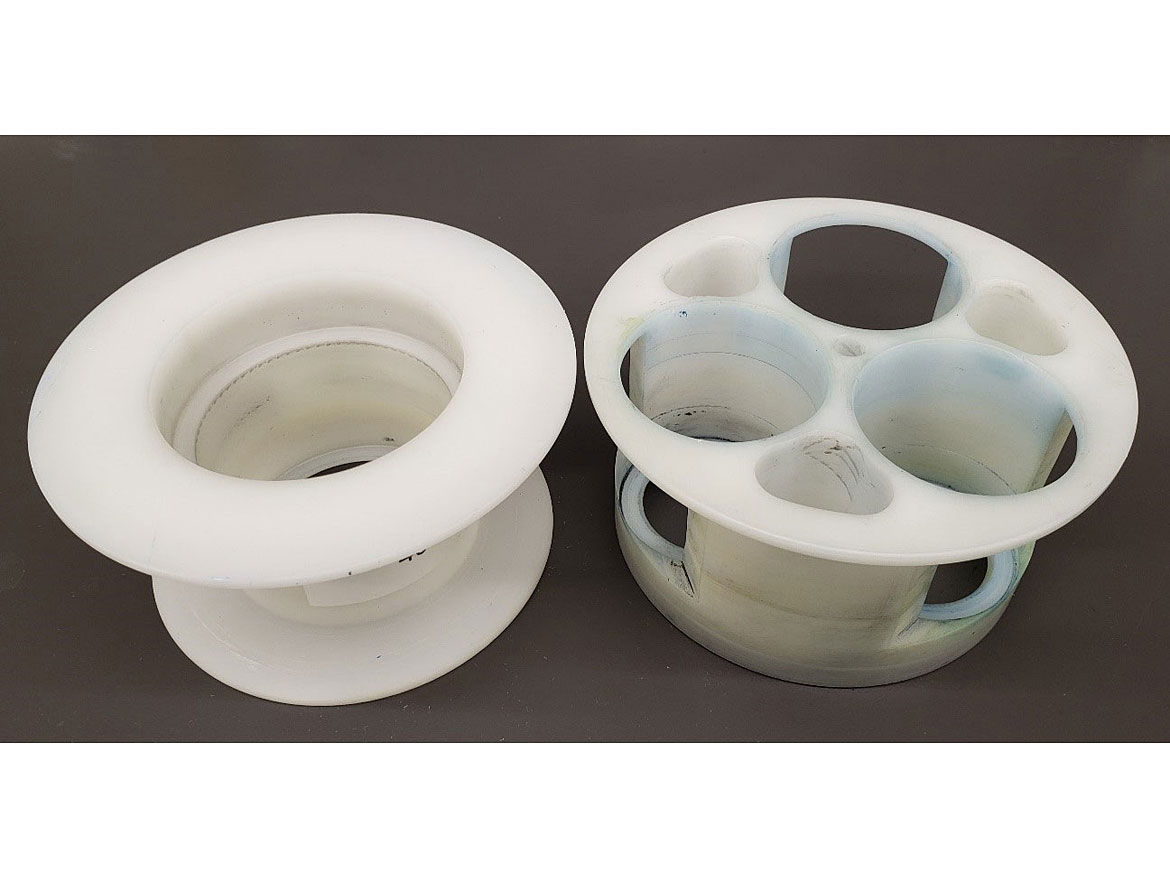
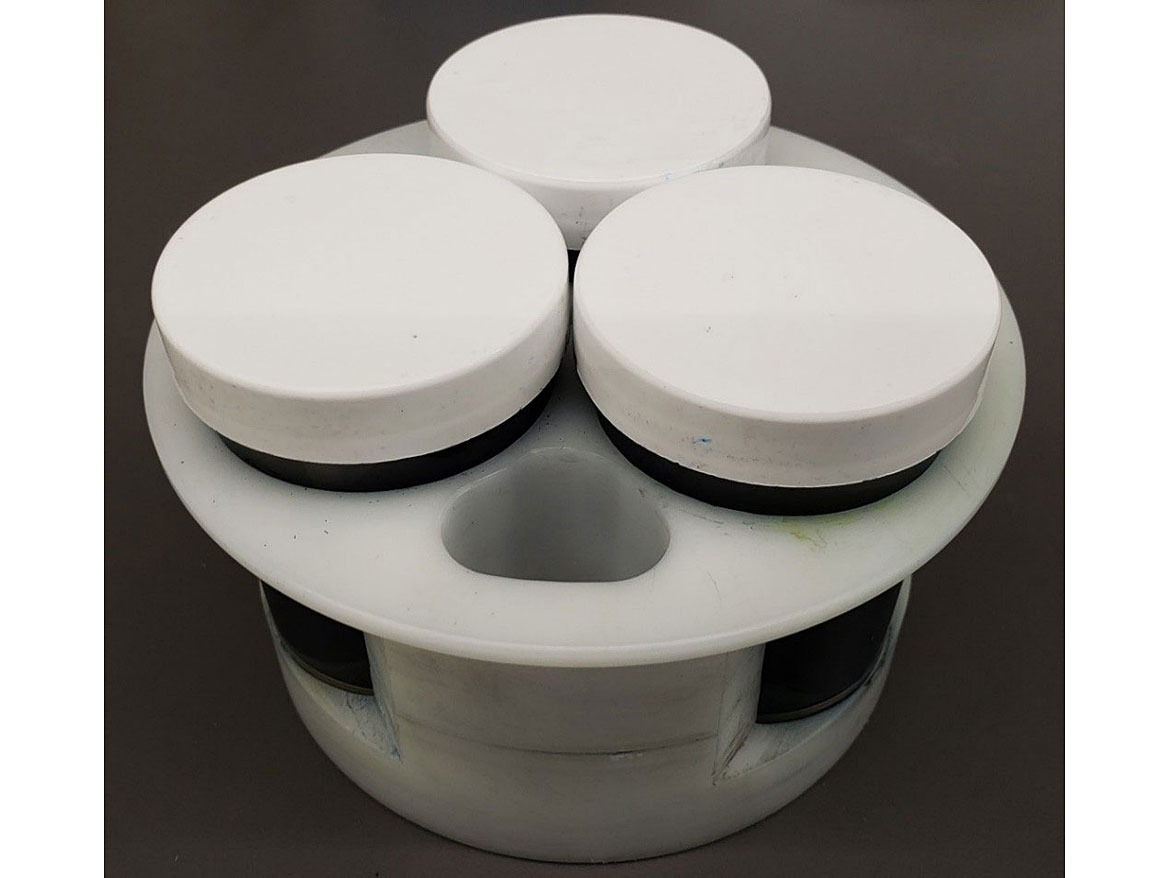
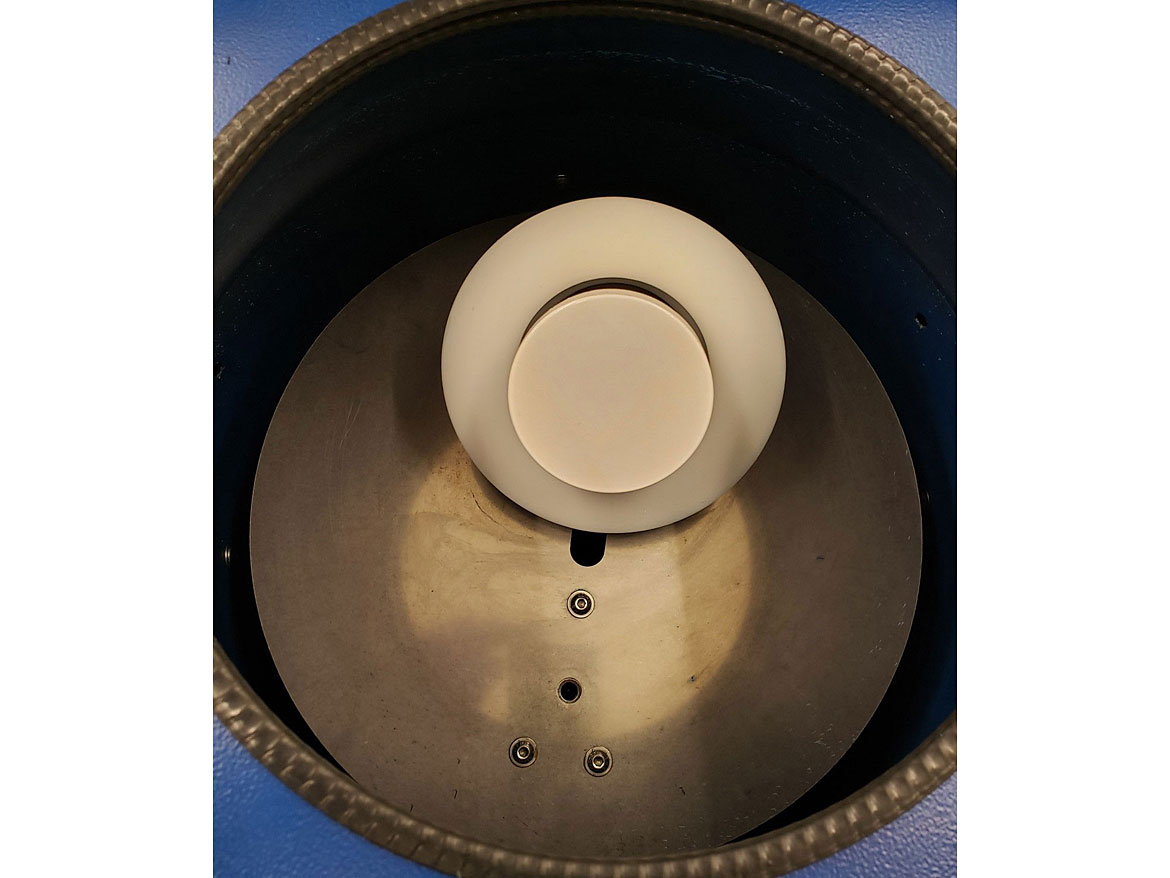
Method
Using the following formulas and dispersant actives on pigment solids for various pigments, these levels were found to work with most pigments and dispersants. For example, a carbon black dispersion in water works best at 30-60% dispersant actives on pigment solids. However, if the carbon black is a large particle size and is a surface treated pigment, lower levels will be necessary. The opposite is true for fine particle sized carbon black pigment. The following suggested levels were found to be a good starting point.
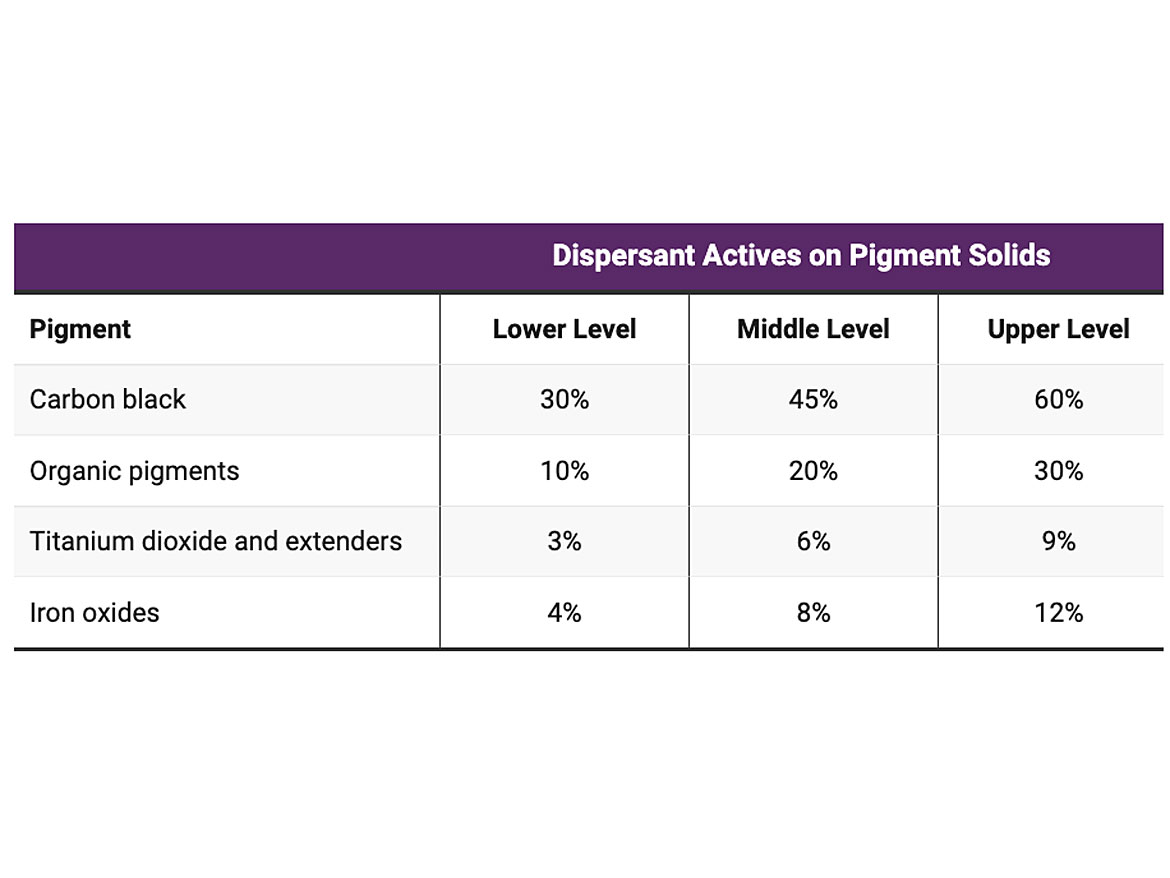
The formulation used will depend on the application, and the dispersion intensity and time is formulation specific.
This procedure is best used on low-viscosity dispersions. High viscosity inhibits the media kinetic energy, converts it to heat and rapidly increases the temperature of the system.
For the formulas listed below, this is the method:
- On a balance, add dispersant and water.
- Mix on the machine for one minute at 1,000 rpm.
- Add defoamer and mix for one minute at 2,000 rpm.
- Add pigment and mix for one minute at 2,000 rpm to wet the pigment.
- If media is required, add and then start the dispersion.
- Normally, three to four short dispersion steps are needed. This is to reduce heat buildup in the sample.
- Normally, five to 15 minutes between dispersion cycles is recommended for the samples to cool.
- After the last cycle, test the grind (Hegman Gage preferred).
Avoid rapidly cooling down the sample (for example in a water bath), as this can shock the system and cause a poor dispersion.
The machine normally has a vibration sensor. If vibrations are outside of the range, it shuts down. To avoid this:
- When using media, start mixing at a slow speed then increase speed to full speed.
- If using the three-hole holder, a sample must be in all holes.
- All samples mixing at the same time should have about the same weight. Use blank samples if only making one to two dispersions.
- Have blanks (water with/without beads) for each step if necessary.
It is difficult not to get material on the lid of the container due to the angle of the basket in the machine and handling the samples. If liquid gets on the lid before the first dispersion cycle, restart the sample. It is recommended to do a quick shake of the container between dispersion cycles to homogenize the contents with any potential material on the lid. Liquid on the cover poses other issues. As the material in the container heats up, the inside pressure of the container increases, forcing material out and quickly dirties the inside of the machine. It was found that wrapping the container with masking tape will minimize the mess. Since the label will be obscured, it is recommended to identify the top of the containers using a marker.

Sample Formulations
Below are some sample formulations for a simple water-based pigment dispersion. It was optimized to determine dispersant level in an architectural colorant system. It is not optimized for viscosity or stability. The goal was minimum raw materials to reduce the chance of raw material interactions.
Most organic pigments can use the phthalocyanine blue formula. For very high oil-absorbing reds and yellows, it is recommended dropping the pigment concentration in the grind to 20%, but keeping the dispersant actives on pigment solids the same. Extender pigments (with or without TiO2) pigments can use the TiO2 formula.
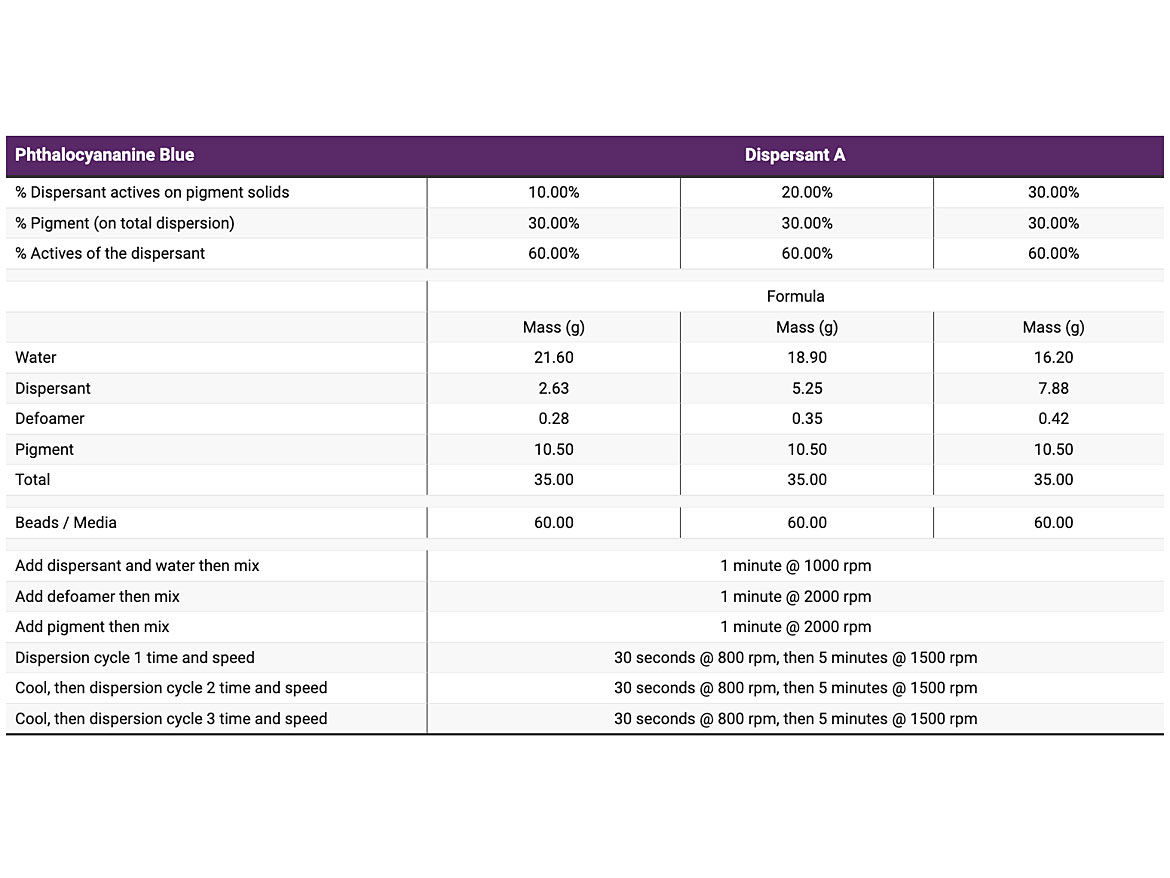
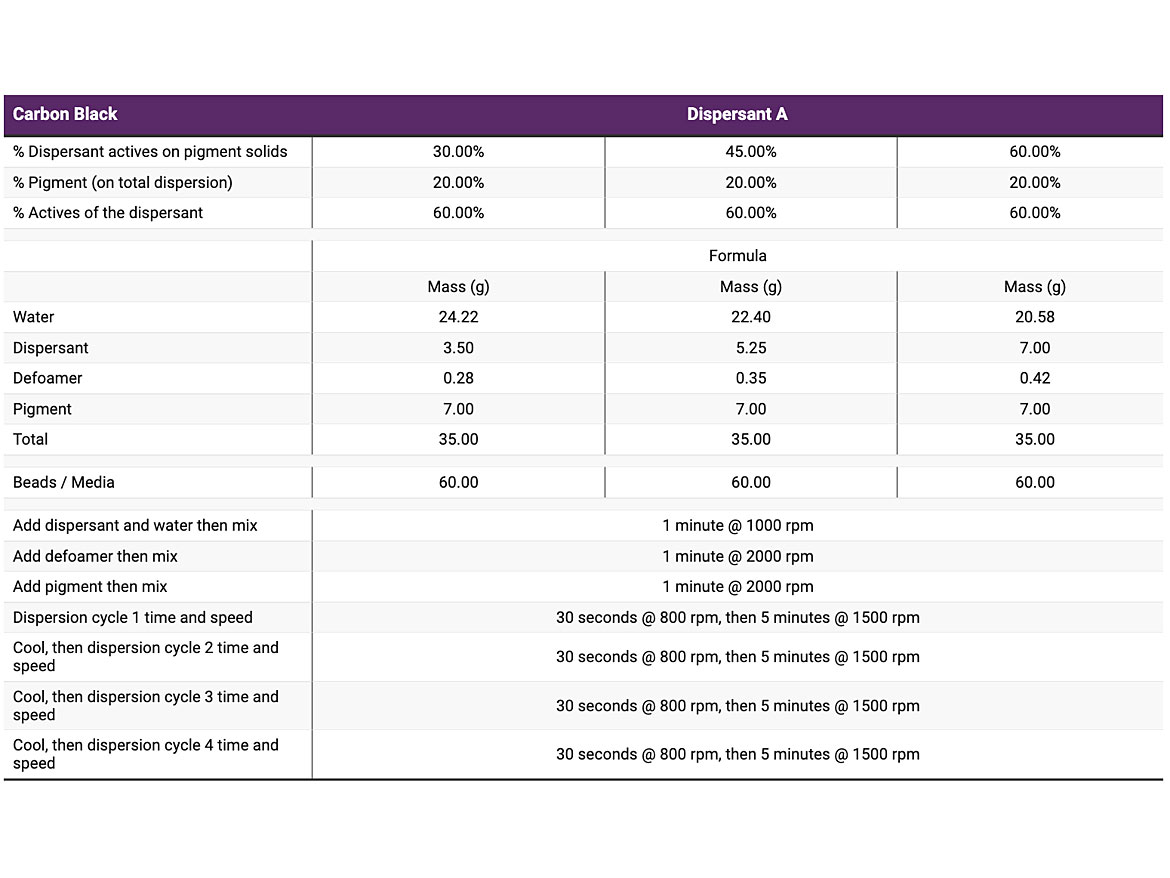
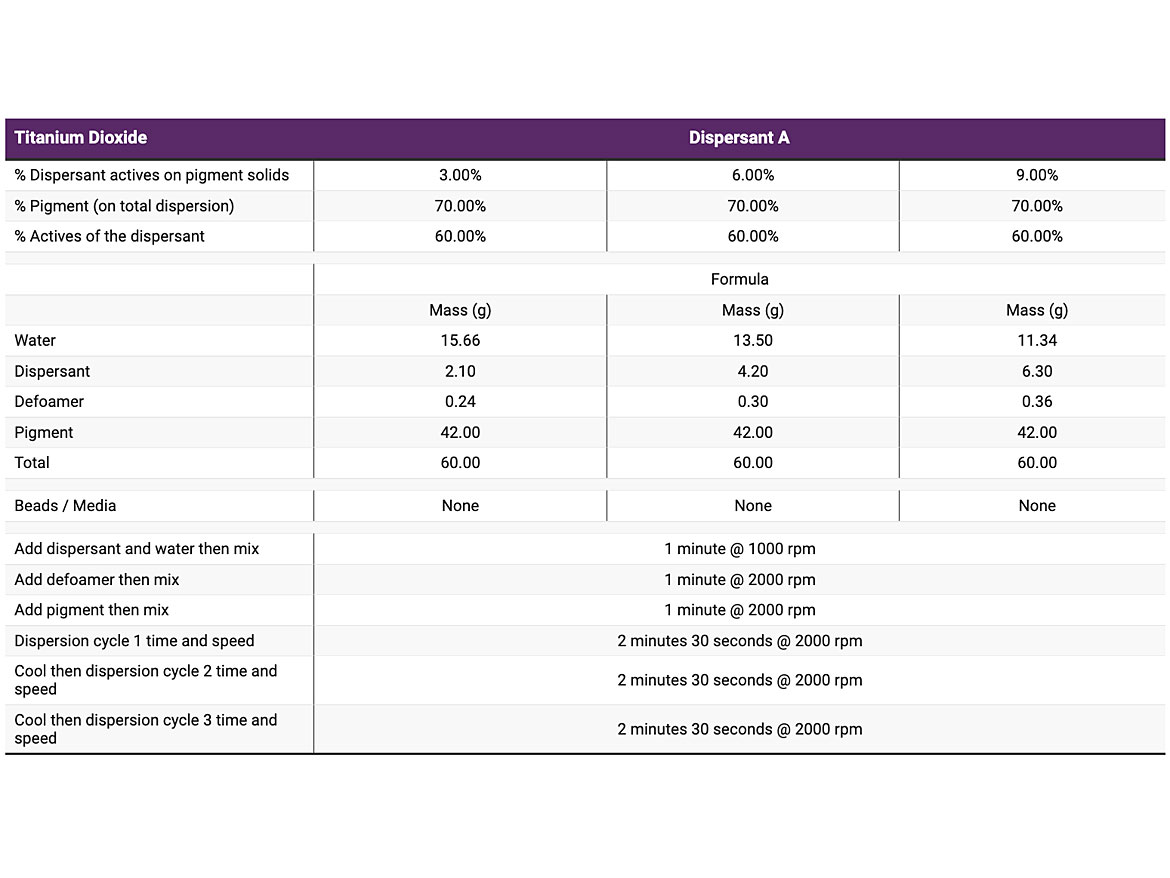
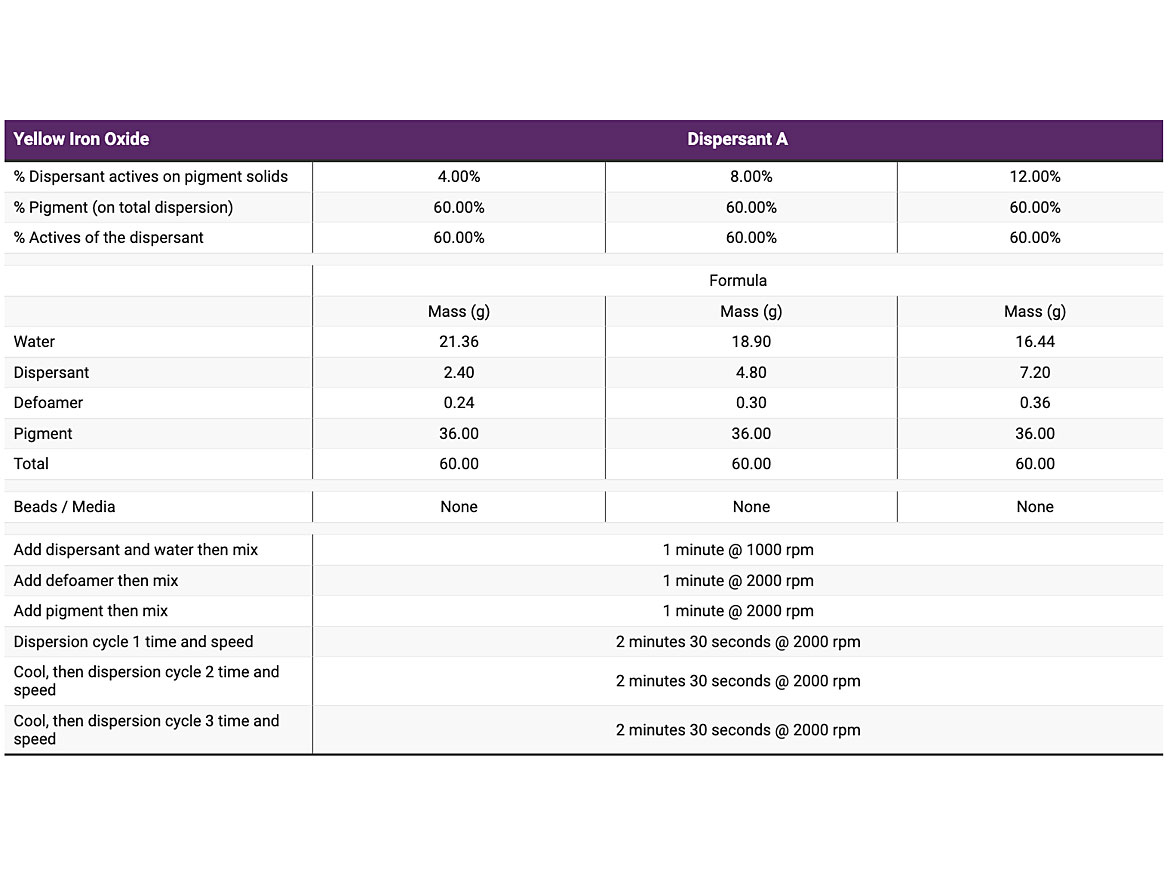
Let Down Procedure
Always let down the grinds or add them to paint immediately. Allowing them to stand, especially overnight, can lead to flocculation since the screening formulas may not be optimized for stability. Let the grinds cool if over 100 °F/38 °C.
For architectural paints, the dispersions were added to two different paints from two different companies. A white (high TiO2 level) semi-gloss and a deep-base flat. This allows significantly different levels of TiO2 and extender in the formulas as well as different formulating strategies from different companies. Two grams of dispersion were added to 98 grams of paint. Black color is added to the paints when dispersing TiO2.
Put the mixture in the machine for one minute at 1,000 rpm, scrape the sides and then one additional minute at 2,000 rpms. Then apply the coatings.
low iron oxide formula.
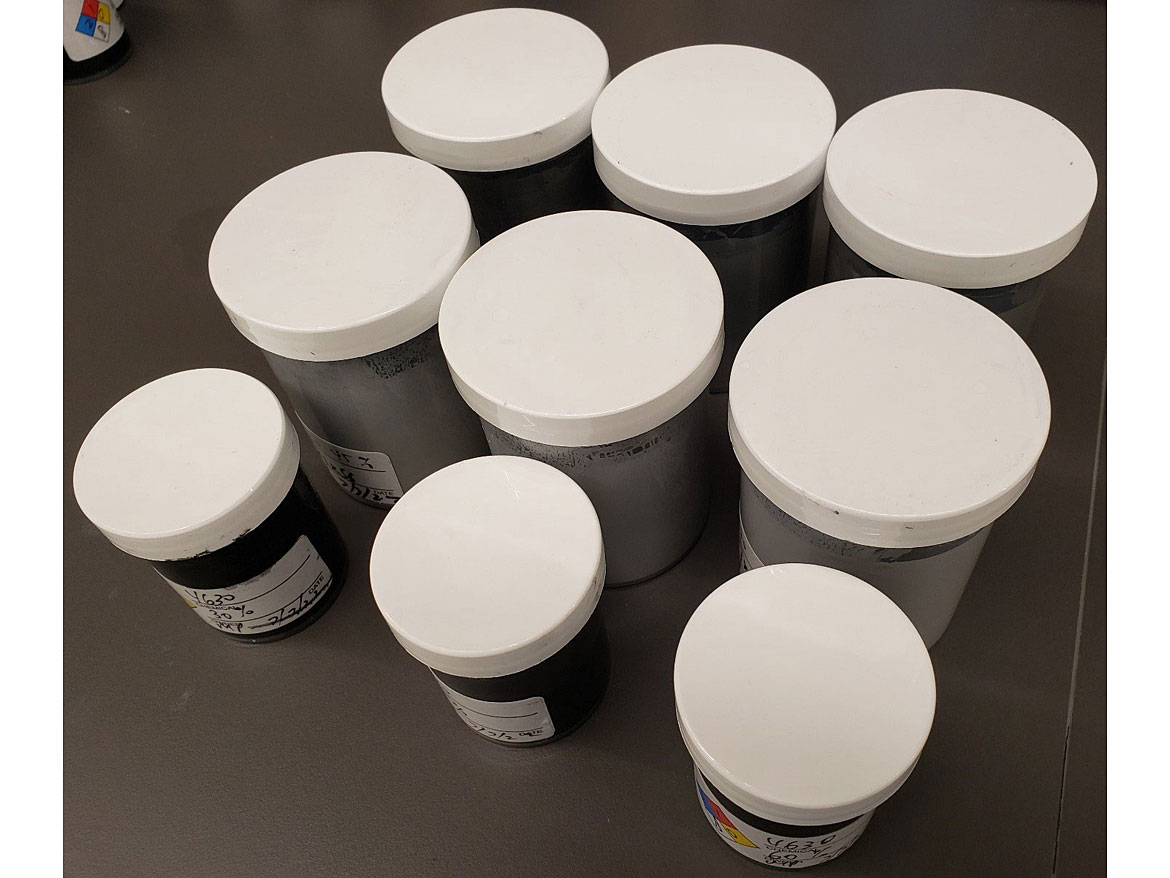
All information contained herein is provided "as is" without any warranties, express or implied, and under no circumstances shall the author or Indorama be liable for any damages of any nature whatsoever resulting from the use or reliance upon such information. Nothing contained in this publication should be construed as a license under any intellectual property right of any entity, or as a suggestion, recommendation, or authorization to take any action that would infringe any patent. The term "Indorama" is used herein for convenience only, and refers to Indorama Ventures Oxides LLC, its direct and indirect affiliates, and their Yellow iron oxide formula.employees, officers, and directors.
Looking for a reprint of this article?
From high-res PDFs to custom plaques, order your copy today!