Exploring the Use of Bio-Derived, Isosorbide-Based Polyols in the Synthesis of High-Performance Polyurethanes

LightStock, iStock / Getty Images Plus, via Getty Images
Polyurethanes (PUs) are an extremely flexible and widely used class of industrial polymers. U.S. production rates were close to three million tons in 2016,1 and globally the polyurethane market is expected to be worth approximately $95 billion by 2028.2
PUs are made by reacting polyols with diisocyanates or polyisocyanates. This chemistry has inherent versatility with a wide range of both types of monomers available for use. Over decades, polymer scientists have learned how to control and manipulate PU chemistry to deliver plastics optimized for applications ranging from insulation for buildings and fridges/freezers, to furniture and underlay, footwear and coatings. However, as with most polymers, PUs are traditionally made from fossil fuel-based building blocks.
Those working at the forefront of PU chemistry are now transitioning to a palette of bio-derived alternatives to enable society’s continuing use of these valuable materials and, simultaneously, access new performance profiles.
Danimer Scientific (Bainbridge, Georgia), a pioneer in the development of sustainable polymers, has recently developed a portfolio of 100% bio-derived polyols (Avio™) for PU synthesis, using isosorbide.
Isosorbide is a plant-derived, renewable feedstock made at an industrial scale to very high purity (POLYSORB®) by Roquette (Lestrem, France), a global leader in plant-based ingredients. The new polyols have been shown to deliver enhanced PU performance as well as fulfilling requirements for renewable/sustainable feedstocks.
This article introduces the multiple potential uses of isosorbide in PU chemistry and provides experimental data demonstrating how the new monomers compare with conventional alternatives in two-component coating, aqueous dispersion (PUD), and casting applications.
Creating New Polyols for PU Synthesis
Isosorbide is routinely referenced as a sustainable monomer with significant potential for the manufacture of plastics. The schematic in Figure 1 illustrates its manufacture from renewable, plant-based feedstocks. The hydrolysis of plant starches produces glucose that is converted to sorbitol and isosorbide via sequential reduction and dehydration.
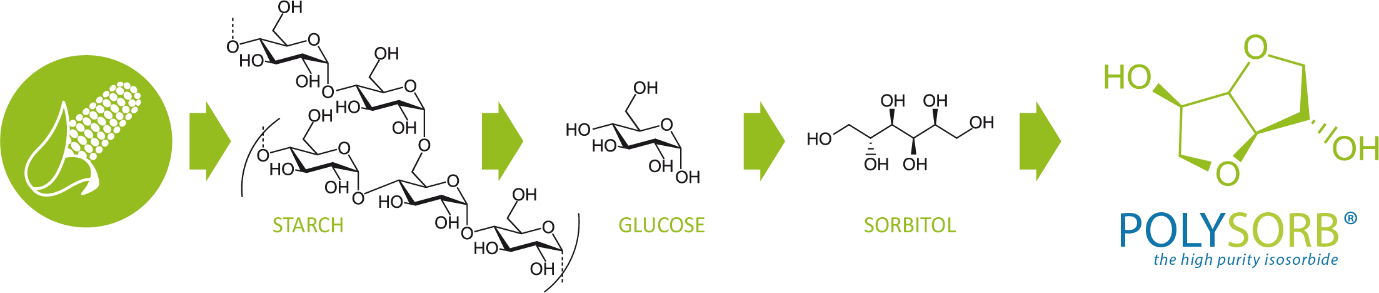
This process has been progressively refined and optimized to produce highly consistent, high-purity isosorbide on an industrial scale. The resulting monomer is sustainable. The carbon footprint has been reduced to just 0.09 kg CO2/kg of product* – non-toxic and available in multiple grades to meet the requirements of different polymer producers.
It has application in the production of PET and polycarbonates, and can play a range of roles in PU chemistry (Figure 2).
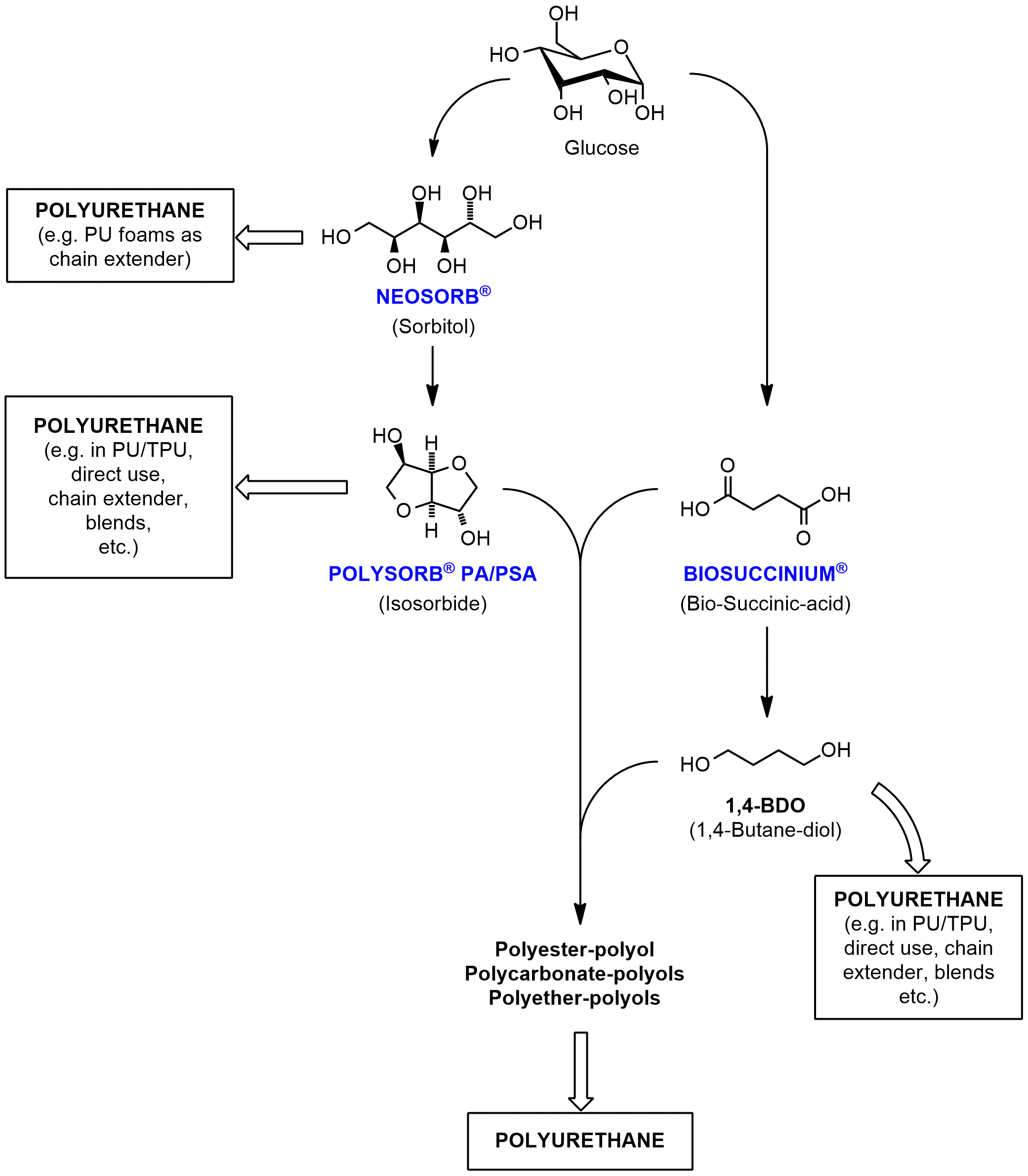
Making a customized PU with properties tailored to a specific application relies on developing an appropriate formulation. Polyols form the bulk of the formulation that includes the selected di- or polyisocyanate and may additionally incorporate chain extenders, catalysts, surfactants, pigments, flame retardants, adhesion promoters, and blowing agents.
The PU is formed by exothermic reaction between the isocyanate and polyol, a reaction that proceeds readily at room temperature but can be accelerated via catalysis. Unlike many other polymers, PUs are made at the point of use/application.
Isosorbide is a diol, as is its precursor sorbitol. Both can be used directly as chain extenders to build molecular weight. Isosorbide can also be used as an additive to improve PU properties or directly as the reactive polyol, alone as part of a blend. Diols such as isosorbide produce linear polymers while higher numbers of reactive hydroxyl groups increase crosslinking, producing a PU of greater rigidity. In fact, polyol choice is one of the main ways in which chemists control rigidity and the hardness of the finished PU.
Lastly, isosorbide can be used to synthesize other polyols such as polyester-polyols, polycarbonate-polyols, polyether-polyols, and/or polycarbonate polyester polyols, via reaction with other diols such as 1,4-butane-diol, as shown.
Danimer Scientific has harnessed this latter capability to create the Avio family of 100% bio-derived, hydroxy-terminated oligomers, specifically for PU synthesis. These have broad, beneficial applications across all types of PU systems including UV-cure systems and thermoplastic PUs (TPUs). Advantageous performance is attributable to the cycloaliphatic nature of the isosorbide, but these innovative polyols have been synthesized to deliver high levels of primary hydroxyls in order to enhance reactivity.
Primary hydroxyls are in the region of three times more reactive than secondary hydroxyls, as found on unreacted isosorbide. Avio 2426 and Avio 2962 have already been approved for use while two further polyols are awaiting TSCA registration. The following studies illustrate what can be achieved with Avio 2426 and Avio 2962 in three different types of PU systems.
Case Study One
Improving the Abrasion Resistance, Impact Resistance, and Adhesion of Two-Component PU Coatings
Two-component (2K) PU systems are the benchmark for coating applications, delivering high-performance finishes that are used to protect products ranging from structural steel and architecture to furniture and internal features such as paneling and balusters.
Since the polyol (resin) and isocyanate (hardener) are stored separately, 2K PU systems offer the additional benefit of high stability/long shelf life. 2K PU coatings can be formulated to deliver UV stability and weatherability, a good mechanical property profile (hardness, toughness, and flexibility) and sound chemical resistance.
Table 1 shows data for 2K solvent coating systems based on Avio 2426 and Avio 2962. Baseline data were also measured using a commercially available polyester diol (1,6 hexane diol (HDO)/neopentyl glycol (NPG) adipate) of comparable molecular weight.
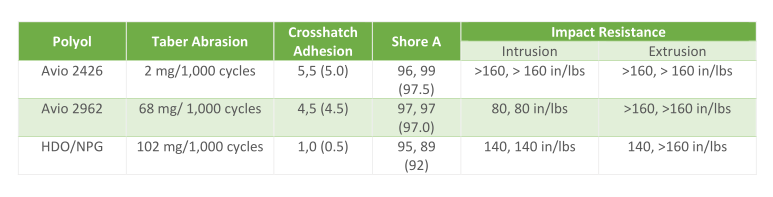
Test methods: ASTM D4060, 3359, 22402794.
All the coatings were formulated with an aliphatic polyisocyanate at an isocyanate index of 1.05 and to a solids loading of 70% in ethyl acetate (solvent). Dibutyltin dilaurate (DBTDL) was incorporated as a catalyst at a concentration of 100 ppm.
Coatings were drawn down on to steel Q panels and Taber panels to a thickness of 0.3 mm using a Bird bar. The resulting samples were then cured at room temperature for 24 hours and then at 70 °C for 8 hours, prior to characterization with respect to abrasion resistance (Taber Abrasion), adhesion (Crosshatch Adhesion), hardness (Shore A), flexibility (Mandrel bend test, ASTM D552), and impact resistance.
All the panels exhibited comparable flexibility, passing the Mandrel bend test up to 180 °C. However, significant differences were observed with respect to abrasion resistance and adhesion.
The bio-based polyols delivered superior performance in these areas relative to the control, notably the Avio 2426, which produced a coating with significantly better abrasion resistance and higher adhesion.
This system also scored highly in terms of hardness and impact resistance. Avio 2962 also performed well relative to the control with respect to hardness; impact resistance was somewhat lower.
Coatings formulated with Avio 2426 also exhibited superior chemical resistance relative to the control, especially to caustic and Skydrol, a fire-resistant aviation fluid (Figure 3). In summary, in this demanding application, the new bio-derived polyols delivered PU coatings with a range of substantially enhanced and valuable properties relative to a commercial control.
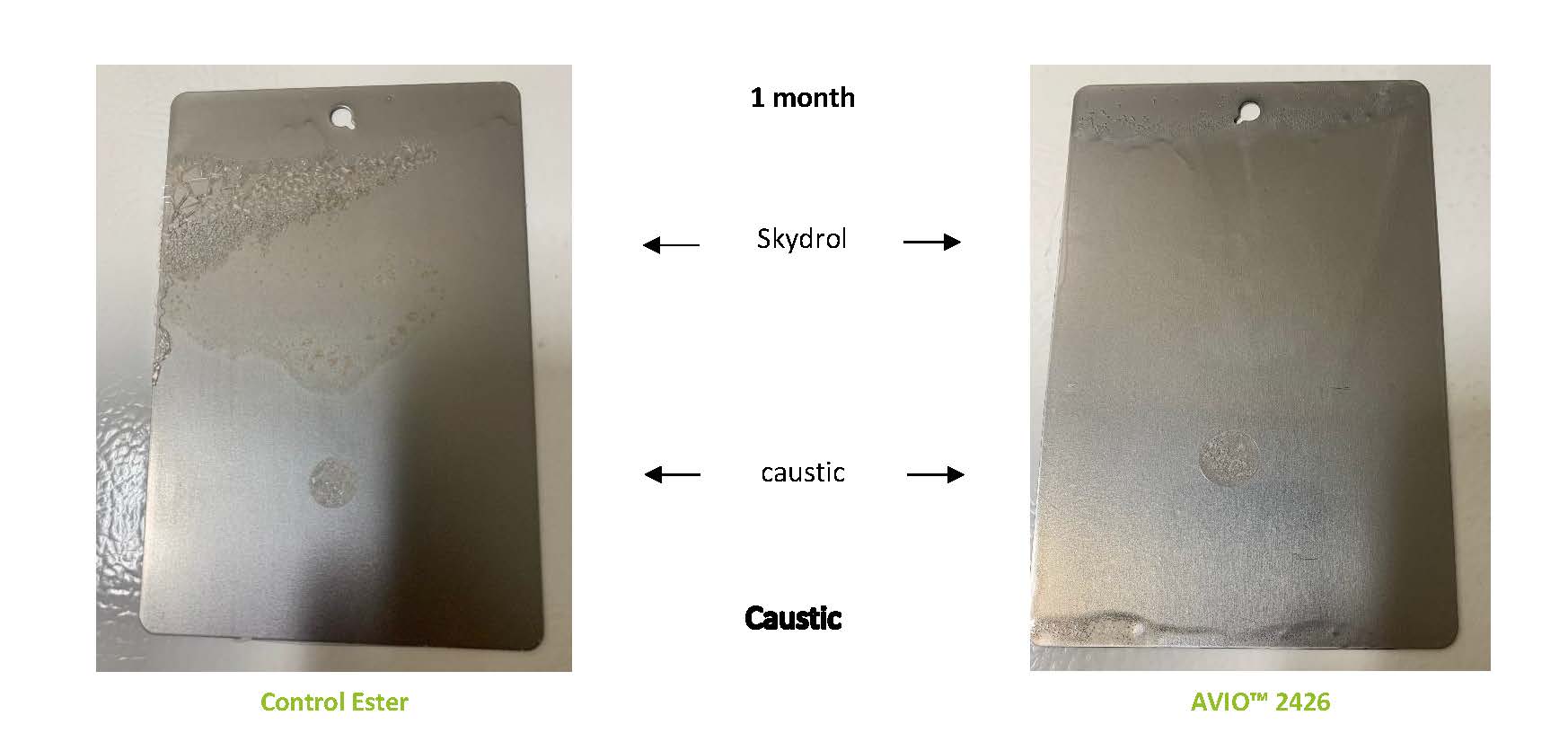
Case Study Two
Improving the Hardness of PU Dispersions
The use of water-based PU dispersions (PUDs) is growing, primary attractions being ease of use and a reduction in levels of volatile organic compounds (VOCs). Performance is also improving. PUDs are now widely used as coatings for leather, in textiles and flooring, as inks, and as adhesives.
Polycarbonate-based PUDs tend to be associated with exceptional performance but can be highly viscous, making application more difficult; polyester-based systems are a less-expensive alternative. Polyether-based PUDs are the lowest cost option, but performance limitations mean that they are often only suitable for less demanding applications.
Table 2 shows data for PUD systems based on Avio 2426 and Avio 2962. Baseline data were also measured using commercially available polyester (HDO/NPG adipate) and polycarbonate (1,4 BDO initiated system) diols of comparable molecular weight.
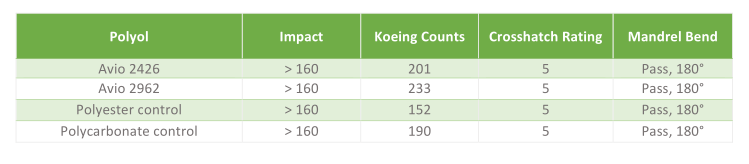
All the coatings were formulated as standard, anionically stabilized aliphatic PUDs using H12MDI (methylenediphenyl diisocyanate) and NMP (N-methylpyrrolidone) as a co-solvent. Additional formula ingredients included dimethylol propionic acid (DMPA, as a stabilizer); triethyl amine (TEA, as a counter-ion) and hydrazine (as a chain extender). Coatings were drawn down on to substrates, as in the preceding case study, to a thickness of 0.3 mm and then cured for 24 hours at room temperature and subsequently 8 hours at 70 °C.
The resulting samples were characterized with respect to impact resistance, hardness (Koenig counts, ASTM D4366), adhesion (crosshatch rating), and flexibility (mandrel bend). In this application, the bio-derived polyols exhibited comparable performance on all metrics, excepting hardness where superior characteristics were observed, notably with Avio 2962, which delivered the hardest coating of all the PUDs. Solvent resistance was also assessed and here too closely similar results were observed (Table 3) though the Avio systems delivered some marginal gains.
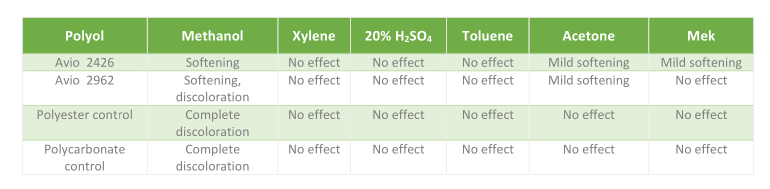
In summary, for PUDs, the bio-derived polyols deliver largely comparable performance across the property slate, with the notable exception of improved hardness. It is worth noting that this improvement is relative to polycarbonate diol PUDs, which tend to be associated with particularly high performance.
Case Study Three
Improving the Mechanical Properties of PU Castings
The casting of PUs, into soft silicone molds, is a simple, low-cost process used routinely to make items ranging from wheels, rollers, shock absorbers, and other automotive components to shoe insoles and electronic casings. Prototyping and product design is also an important application, with casting particularly well-suited to low-to-medium production volumes.
Casting formulations are typically optimized to control the mechanical properties of the resulting component and afford considerable versatility to tailor performance with respect to hardness, abrasion, and impact resistance and strength.
Table 4 shows data for cast PU samples produced using Avio 2426 and 2962. Baseline data were also measured using a commercially available polyester polyol (HDO/NPG adipate) of comparable molecular weight. Cast PUs were synthesized with each of the polyols using an hexamethylene-diisocyanate (HDI) trimer and an isocyanate index of 1.05. Other ingredients in the formulation included silicone (as a surfactant); defoamer; a moisture scavenger, to reduce bubbles and imperfections; and carbodiimides (crosslinkers, as required).

Samples were cast at 85 °C-90 °C in a heated mold, and then allowed to cure overnight. Sample strips were cut from the resulting sheets and used for tensile testing (Instron) of the castings.
In this application, both bio-derived polyols exhibit substantially better tensile properties than the polyester control, although the control does offer high stiffness (Modulus values). The strength of the Avio 2426 casting is extremely high; the Avio 2962 is also markedly better than the polyester control. Once more, the data illustrate the potential to improve mechanical properties while at the same time reducing the environmental footprint of the PU casting.
Conclusion
Moving to more environmentally benign monomers is essential for the continuation of a highly beneficial relationship with polymers. This shift creates an opportunity to, simultaneously, access new property profiles.
New polyols from Danimer Scientific, synthesized using POLYSORB, a high-purity isosorbide from Roquette, illustrate what is possible. In experimental studies, these new monomers proved beneficial in all types of PU systems, 2K coatings, PUDs, and castings, delivering a better mechanical property profile in each case. Furthermore, there was also evidence of industrially useful improvement in chemical resistance.
The results demonstrate the potential to simultaneously access greater sustainability and improved performance, a win-win opportunity for polyurethane chemists and manufacturers.
*Internal comparative study based on life cycle analysis methodology, peer-reviewed by an external auditor.
References
1 C. Liang et al ‘Material Flows of Polyurethane in the United States,’ Environ. Sci. Technol 2021, 55, 14215-14224.
2 Grandview Research Press Release ‘Polyurethane Market Size Worth $94.59 Billion By 2028 | CAGR: 3.8%’ Available to view at: https://www.grandviewresearch.com/press-release/global-polyurethane-pu-market.
Looking for a reprint of this article?
From high-res PDFs to custom plaques, order your copy today!