Perfect Paint Preparation of Agricultural Equipment Components

Agricultural equipment is constantly exposed to tough climate and weather. For this reason, optimal paint preparation is essential for the equipment to hold up under such tough conditions. A custom-engineered continuous-feed spinner hanger blast machine RHBD-K 22/27-HD, installed in a new factory of a globally active manufacturer, is making a significant contribution towards this goal. The shot blast machine is integrated into a fully automated manufacturing line. It allows the blast cleaning of a variety of complex weldments, weighing up to two tons, prior to painting.
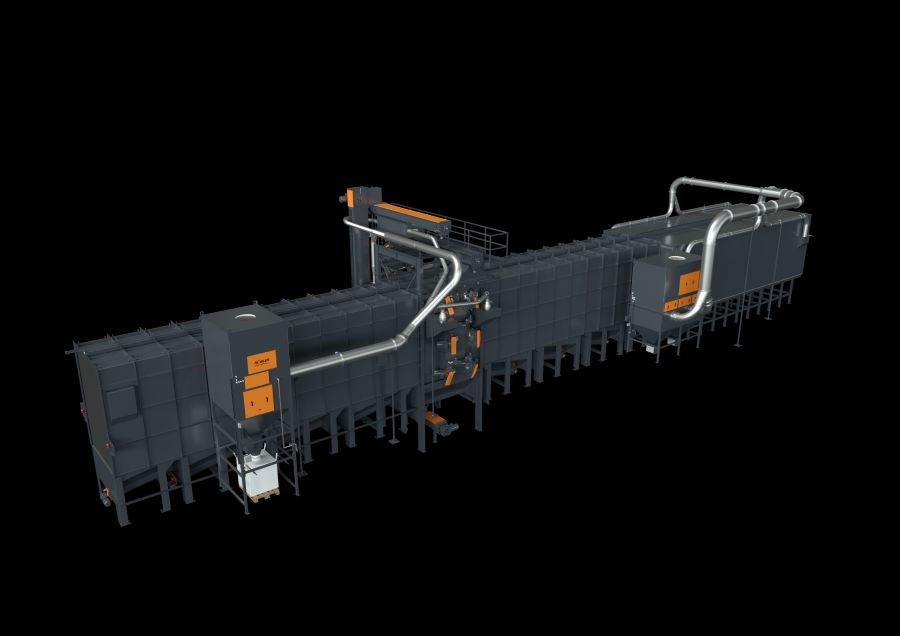
This Brazilian manufacturer supplies innovative agricultural machinery for a wide range of applications. For example, it is used for harvesting coffee beans and sugar cane, as well as for seeding and cultivating all kinds of agricultural crops. The company is active in more than 100 countries. Reasons for this success are the excellent productivity and quality of the equipment as well as the continuous improvement of the manufacturing operation. It is not surprising that the new factory in Brazil is equipped with a fully automated, digitized manufacturing line. There, steel plates and profiles are cut, welded into complex constructions, shot blasted, and painted in continuous-flow operation. Based on the tailor-made equipment concept, the technical implementation and the high equipment quality, the company had decided to purchase the continuous feed spinner hanger blast machine RHBD-K 22/27-HD made by Rösler. The work pieces are transported through the shot blast machine by the power and free-conveyor system of the manufacturing line. This required optimal coordination of the various interfaces in the manufacturing line. But thanks to the help by the colleagues at Rösler Brazil, the whole project went very smoothly.
Energy-Saving Shot Blast Operation Integrated into the Overall Manufacturing Process
After the welding operation, the components are transported through an inlet chamber into the actual blast chamber equipped with 12 gamma 400G turbines, each with a drive power of 11 kW. These innovative Rösler high-performance turbines contain curved throwing blades in the “Y” design. Compared to conventional turbines, the special blade design with optimal curvature increases the throwing speed significantly. This results not only in an up to 20% higher blasting performance, but also in significantly shorter cycle times.
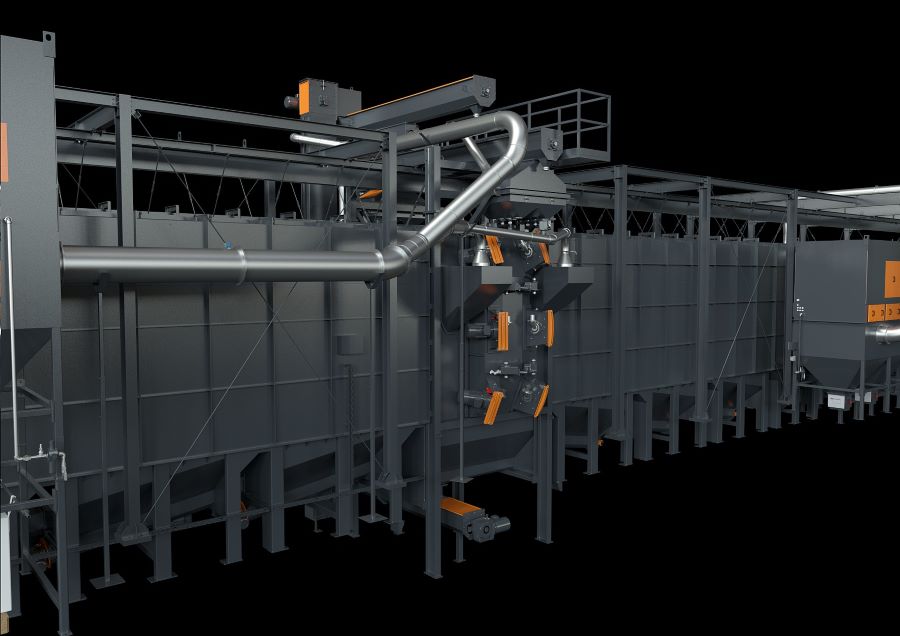
The 12 Gamma 400G turbines are arranged in a circle around the blast chamber. Because of the curved design of the throwing blades, the shot blast process is particularly productive and energy efficient. The turbine RPM is controlled by frequency inverters. The variable turbine speed and the automatic control of the media flow allows the precise adaptation of the blast-cleaning process to the different welding assemblies. This ensures optimal paint adhesion and prevents warping of thin-walled components.
Sophisticated Equipment Design Allows More Flexible Shot-Blasting Operation
Due to the enormous work piece diversity, the shot blast machine was designed to handle welding assemblies with dimensions of up 10,000 x 2,000 x 2,500 mm (L x W x H) and weights of maximum 2,000 kg. Some of the weldments have thick walls and are very sturdy, whereas others have thin walls and are delicate. To account for these differences and to consistently achieve the required preparation grade of Sa 2.5 as well as the specified surface roughness values, the turbine RPM is controlled by frequency inverters. This ensures optimal paint adhesion and prevents warping of the thin-walled components. The variable turbine speed and the automatic control of the media flow allows precise adaptation of the blast-cleaning process to the different welding assemblies. Selection of the workpiece-specific shot blast programs is done at the master computer of the manufacturing line.
Behind the outlet chamber of the shot blast machine is a blast room that allows the manual touchup blasting of geometrically complex assemblies with undercuts and internal passages. Augers below the blast room floor transport the thrown blast media to the central media cleaning system. This eliminates the need for a separate media transport and cleaning system for the blast room.
Wear-Resistant Design Ensures High Equipment Availability
The customer was also impressed by the wear-resistant design of the Rösler equipment. For example, the blast chamber is made from manganese steel and is protected by easily replaceable 10 mm thick wear liners, also made from manganese steel. Another plus is the fact that both sides of the throwing blades can be used, which practically doubles their usable life. The throwing blades can be replaced with a quick-change system without having to take the turbine apart.
For more information visit www.rosler.com.
*Images courtesy of Rösler Oberflächentechnik GmbH
Looking for a reprint of this article?
From high-res PDFs to custom plaques, order your copy today!