Alkyd Resins, Part Four: The Life Cycle Assessment of Alkyd Emulsions

Davizro / iStock / Getty Images Plus, via Getty Images.
This is the last article on water-based alkyds. In previous editions of “Formulating with Mike” we have covered alkyd chemistry, emulsifying alkyds, and some testing results of alkyd emulsions using a design of Experiment (DOE) to determine which inputs are the most important. In this issue we will look at the life cycle assessment of alkyd emulsions. Normally a life cycle assessment should have been done in the last two years, but the data I will be providing is a bit older than that, about five years old. Please note the life cycle assessment was done using inputs for production in Brazil, but will be similar to other regions. As usual, I wish to thank the following people for providing the information used in this article: Bruno Dario, Juliane Pereira, Silmar Barrios, Fabio Rosa, and Kip Sharp of Indorama Ventures. We will also be discussing conclusions drawn from the four articles in this series on alkyd emulsification, as well as tips/learnings from the work in this study.
Life Cycle Assessment
A life cycle assessment (LCA) quantitatively evaluates the environmental impacts of various areas. These areas are associated with the consumption of matter and energy, as well as the generation of waste – in the form of air emissions, wastewater, solid waste, and energy loss that occur throughout the life cycle of a product. LCA was developed in the early 1970s, and since then it has been refined and supported with inventory databases and impact-assessment methodologies. Today, LCA can be applied to very complex issues aiming to compare the eco friendliness of products and processes, allowing us to design process and products for continuous improvement in the environmental dimension of sustainability. LCA is essentially a comparative method, where different systems serving the same purpose are compared. The basis of comparison is a functional unit, for instance, a specific painted area in the case of paint and coatings.
The scope of this study is to compare the environmental impacts related to the conventional solventborne and waterborne alkyd enamels considering the systems depicted in Figure 1 and Figure 2. These systems are made up of an alkyd dilution or emulsion, and the preparation and application of alkyd paints. In this study, the functional unit is to coat an area of 1m2 (~10 ft2) using 0.133 L (~4 oz) of each paint. This represents the reference flow.
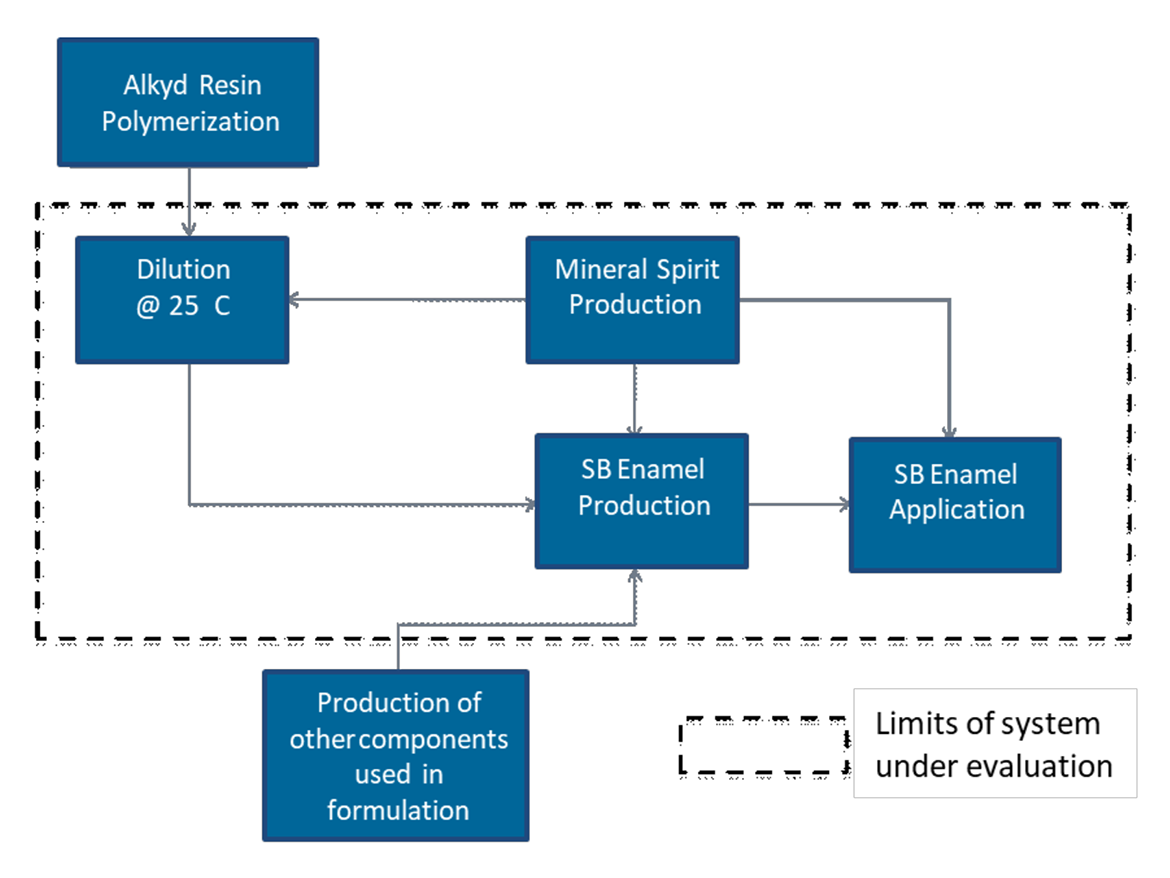
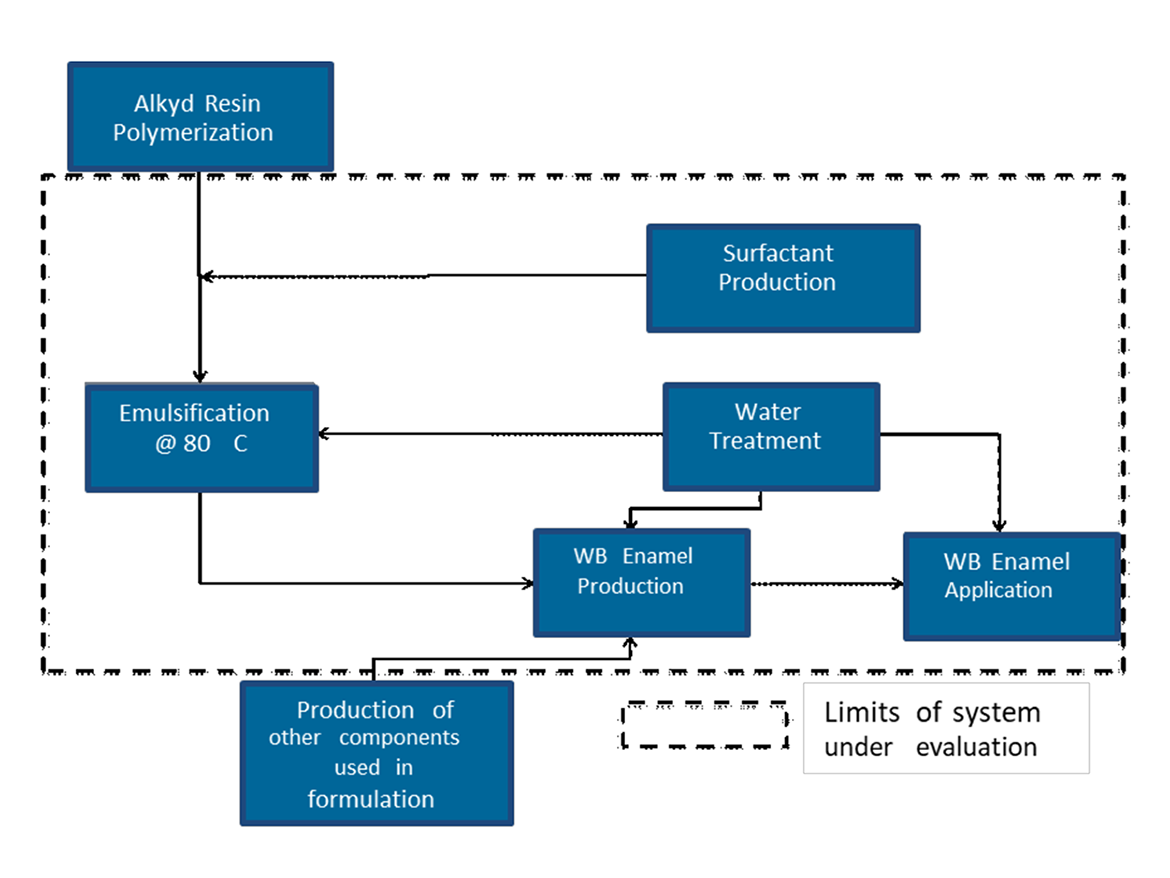
The basic waterborne and solventborne formulations evaluated in this article are shown in Table 1.
The following environmental impact categories were evaluated: climate change (CC), terrestrial acidification (TA), human toxicity (HT), photochemical oxidant formation (POF), terrestrial eco-toxicity (TET), water eco-toxicity (WET), water depletion (WD), and fossil fuel depletion (FD). These environmental impact categories were chosen based on their relevancy for paint and coatings applications.
The results obtained in the environmental impact categories are summarized in Table 2. For the solventborne enamel, the environmental impacted categories most affected by alkyd dilution and paint production and application were WD, FD, CC, POF, and HT. The main results for WD are a result of water consumption in petroleum extraction and naphtha production. FD is associated with the use of petroleum for producing the naphtha used in the production of mineral spirits. CC is mainly due to CO2 and CH4 emissions coming from naphtha and mineral spirits production. The emission of mineral spirits due to evaporation during the application of the solventborne enamel is the main reason for POF. Mineral spirits are responsible for the HT results observed for the solventborne enamel. The main category for water-based alkyds was WD, which is the water used in the formulation. All these results show that the main environmental problems related to the solventborne enamels come from the use of mineral spirits as a solvent.
In Figure 3, the data of Table 2 is shown as percentages to facilitate the comparison between the impacts of solventborne and waterborne enamels. The highest value for each category was set to 100%, and the lower result is shown as a percentage of that. The waterborne enamel has better environmental performance than the solventborne in seven of the eight impact categories evaluated in the LCA. The waterborne enamel is slightly worse than the solventborne in the WD category, due to water consumption in the alkyd emulsification process and enamel production. Although not expected, the water consumption in the solventborne enamel is also high. This is due to the high water consumption in all processes involved in the production of mineral spirits.
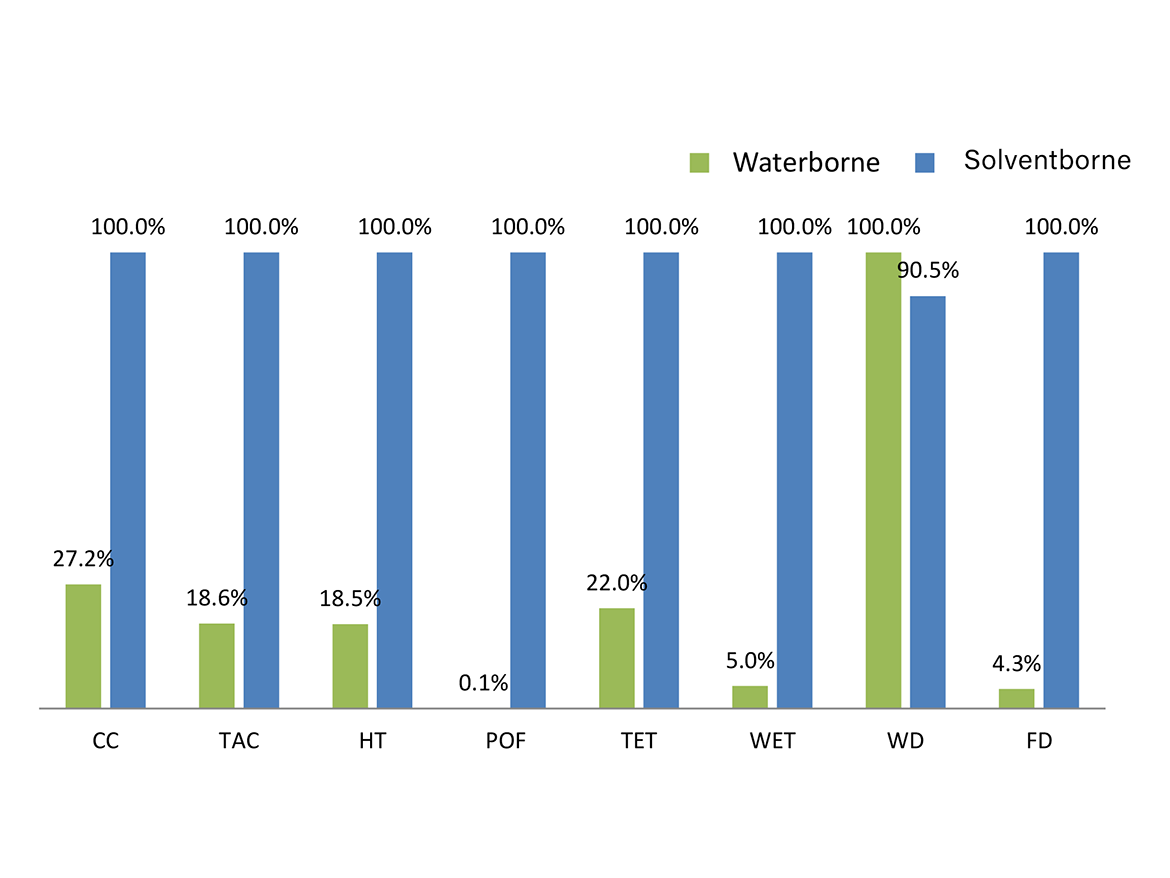
Conclusions
The surfactants used in this study generated stable alkyd-in-water emulsions with a small particle size and high solid content. This was done via phase-inversion emulsification with low energy input using conventional mixing equipment. The efficiency of these surfactants and the optimization of the emulsification was evaluated via a design of experiments (DOE). The results of the DOE showed that within the levels studied, the energy input is not a significant factor to generate emulsions with small particle size and high solid content. Further studies showed that low surfactant content (6.6 php) could also generate small particle size emulsion with low energy input. The DOE also showed that non-ionic/anionic ratio and temperature are significant inputs for the emulsification and, if optimized, can improve the final emulsion. This will affect shelf life stability and coating properties.
Life Cycle Assessment results of solventborne alkyd enamels confirmed that this technology has several environmental limitations. These are water depletion, fossil fuel depletion, climate change, photochemical oxidant formation, and human toxicity. Most of these impacts are due to mineral spirits production and evaporation during paint application. In terms of environmental impact, the only limitation of waterborne enamels in comparison to solventborne is that they consume slightly more water due to the emulsification of the alkyd and paint production. The LCA study reinforced that waterborne alkyd coatings have a better environmental performance profile than solventborne coatings, and are environmentally friendlier.
Lessons Learned/Tips
- Viscous alkyds (viscosity higher than 15,000 cP at high temperature) can be emulsified if small amounts of organic solvents are added to lower viscosity below 15,000 cP.
- Neutralization can be done with a strong or weak base, but hydrolysis of the alkyd resin is the limitation. If hydrolysis occurs with a strong base, like KOH, change it to a weak base, like ethanolamine. If hydrolysis still occurs after that, a small change in the alkyd can be studied. Replacing a small part of the glycerin by pentaerythritol and slightly increasing the molecular weight is recommended.
- Drying time needs to be studied for the formulation for this property to be optimized in the waterborne enamel. Usual cobalt driers can precipitate as hydroxides during storage of the waterborne paint, therefore different drying agents optimized for water-based coatings should be used.
All information contained herein is provided "as is" without any warranties, express or implied, and under no circumstances shall the author or Indorama be liable for any damages of any nature whatsoever resulting from the use or reliance upon such information. Nothing contained in this publication should be construed as a license under any intellectual property right of any entity, or as a suggestion, recommendation, or authorization to take any action that would infringe any patent. The term "Indorama" is used herein for convenience only, and refers to Indorama Ventures Oxides LLC, its direct and indirect affiliates, and their employees, officers, and directors.
Looking for a reprint of this article?
From high-res PDFs to custom plaques, order your copy today!