Alkyd Resins, Part Three: The Emulsification Process

Davizro / iStock / Getty Images Plus, via Getty Images.
In last month’s column, we covered alkyd resins, the move to waterborne alkyds, and alkyd emulsions. In this issue we will cover the emulsification process and then some test data of alkyd emulsions. I would like to thank Bruno Dario, Juliane Pereira, Silmar Barrios, Fabio Rosa, and Kip Sharp of Indorama Ventures for the test data.
The Emulsification Process
The emulsification of liquid phases with low viscosity – lower than 500 cP – typically is performed through direct emulsification. Direct emulsification consists of simply adding the dispersed phase into the continuous phase. The indirect emulsification, also known as phase inversion methodology, goes the other way around. It consists in adding the liquid of the continuous phase, usually water, into the liquid of the dispersed phase. It is typically applied when the dispersed phase is viscous. The emulsification of resins to generate oil-in-water emulsions is usually prepared through the phase inversion methodology, due to the high viscosity of the resins. The phase inversion methodology for an alkyd resin is schematically represented in Figure 1.
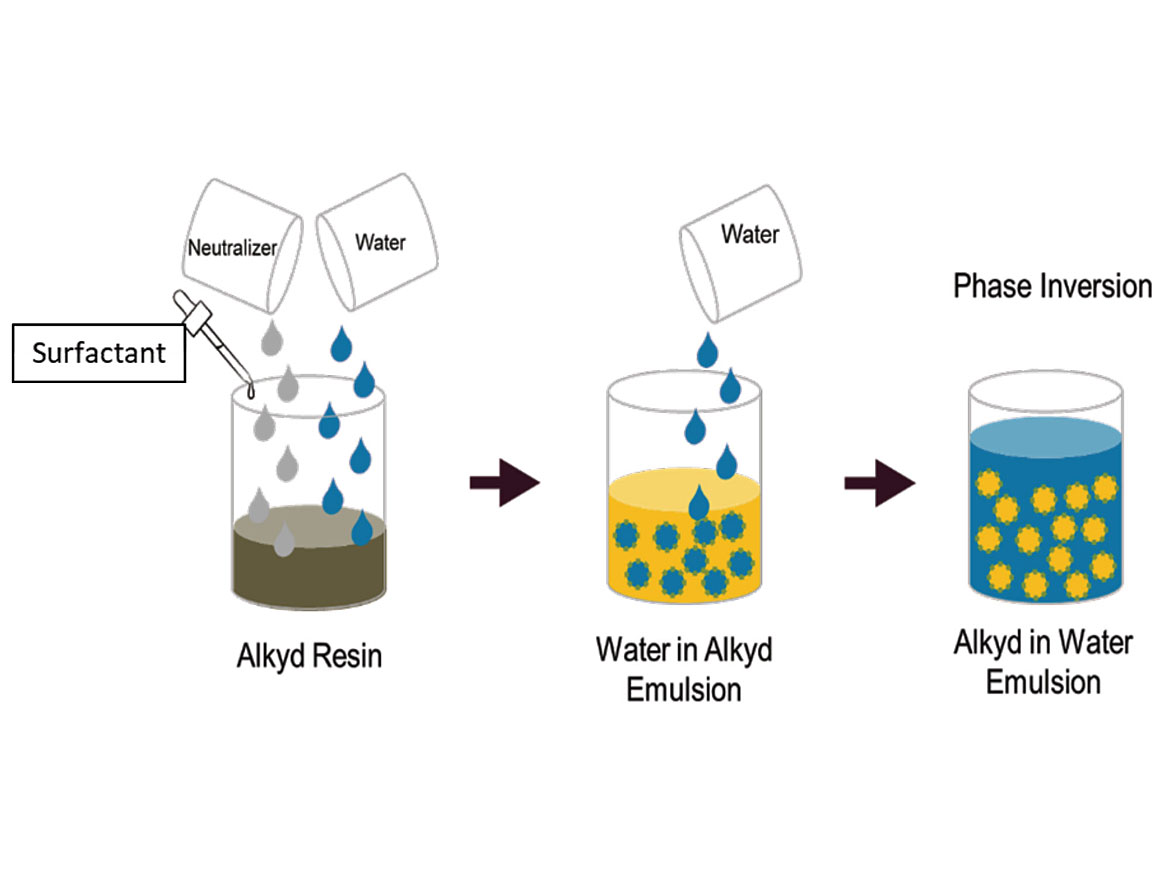
The emulsification of alkyd resins by the phase inversion takes place after the polymerization of the resin, normally below 100 °C, and under atmospheric pressure conditions. It is essential to evaluate the resin’s viscosity as a function of the temperature because the emulsification process must be carried out at a temperature in which the resin’s viscosity is between 500-15,000 cP.
After the reactor achieves the desired temperature, the emulsifiers are added and homogenized, using mechanical agitation. The neutralization of acidic groups within the resins is very important for improving the electrostatic stability of the final oil-in-water emulsion. In the case of alkyds, resins with acid content ranging from 5-10 mg KOH/g are more appropriate for emulsification. Therefore, a base is added to neutralize the acidic groups of the resin and the anionic emulsifier, if supplied not already neutralized. Potassium hydroxide can be used in the neutralization step, but it is essential to evaluate the hydrolysis resistance of the resin at the emulsification temperature. Weaker bases, such as amine derivatives, are recommended as neutralizers, and lessen the chance of hydrolysis of the alkyd, especially when the emulsification process is carried out at higher temperature. The percentage of neutralization of the acidic groups can vary from 50-100%. Usually, in starting formulations, the practice is to neutralize 100% of the acid groups.
After the neutralization step, a slow addition of water, at the same temperature of the resin, is carried out. In this step of the process you see an increase of the viscosity of the water-in-oil emulsion, as the water volume fraction increases. The slow addition of water goes on until the volume fraction of water achieves a critical point in which there is a spontaneous change in the interfacial curvature of the liquid-liquid interface, caused by the rearrangement of the surfactant molecules, resulting in the phase inversion from water in oil to oil in water. A sudden drop in the emulsion viscosity characterizes phase inversion. Depending on the actual formulation of the emulsion, the material may gel before the inversion, and lead to a necessary reformulation. After the phase inversion, normally you have to increase the water flow rate to hit the desired solid content. The phase inversion at low water volume helps to increase the process productivity, since the slow initial addition of water before phase inversion is the time-consuming step. This also allows process flexibility to generate oil-in-water emulsions with higher solids content.
The emulsification process normally needs a high-shear disperser, due to the high interfacial tension between the two immiscible liquid phases. During the dispersion of the liquids, the surface area increases, as well, due to the energy added to the system, which is the reason why it is so unstable. The emulsifiers (surfactants) are added to adsorb at the interface between the two liquid phases and decrease their interfacial tension and the energy the system required for emulsification. That is why we need the emulsifiers. Nevertheless, the higher the emulsifier’s efficiency for decreasing the interfacial tension between the liquid phases, the lower is the amount of surfactant needed, and the lower the dispersion energy required to generate emulsions containing small droplets of the dispersed liquid phase in the continuous liquid phase. Lower levels of emulsifiers within the oil-in-water emulsions are important to minimize water sensitivity of the final waterborne coatings.
Objectives
- Evaluate surfactants for the emulsification of alkyd resins and characterize the emulsion prepared thereof.
- Study the optimization of the emulsion properties through a design of experiment (DOE).
Materials and Methods
The main properties of the alkyd resin are described in Table 1. The viscosity as a function of the temperature is shown in Figure 2. The main properties of the surfactants are described in Table 2. The temperature chosen for the emulsification was 80 °C.
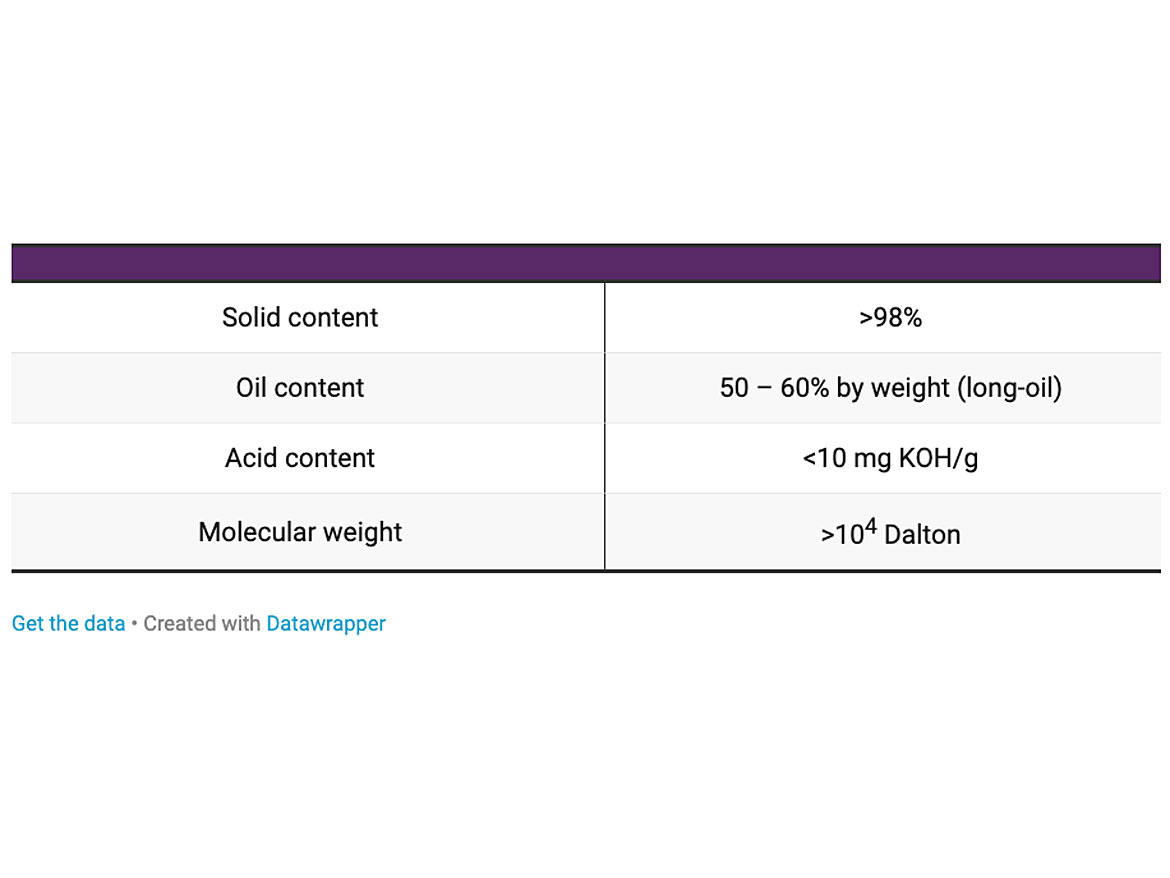
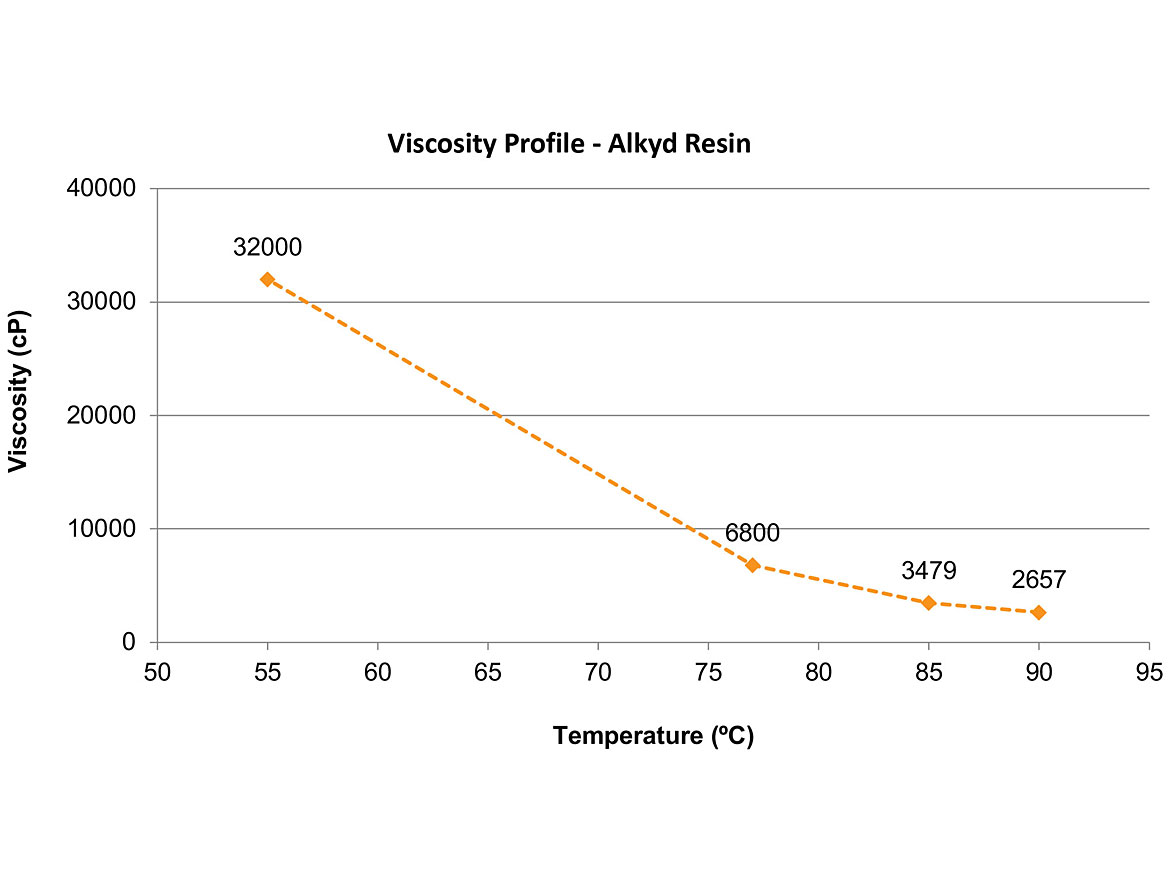
The main properties of the surfactants are described in Table 2.
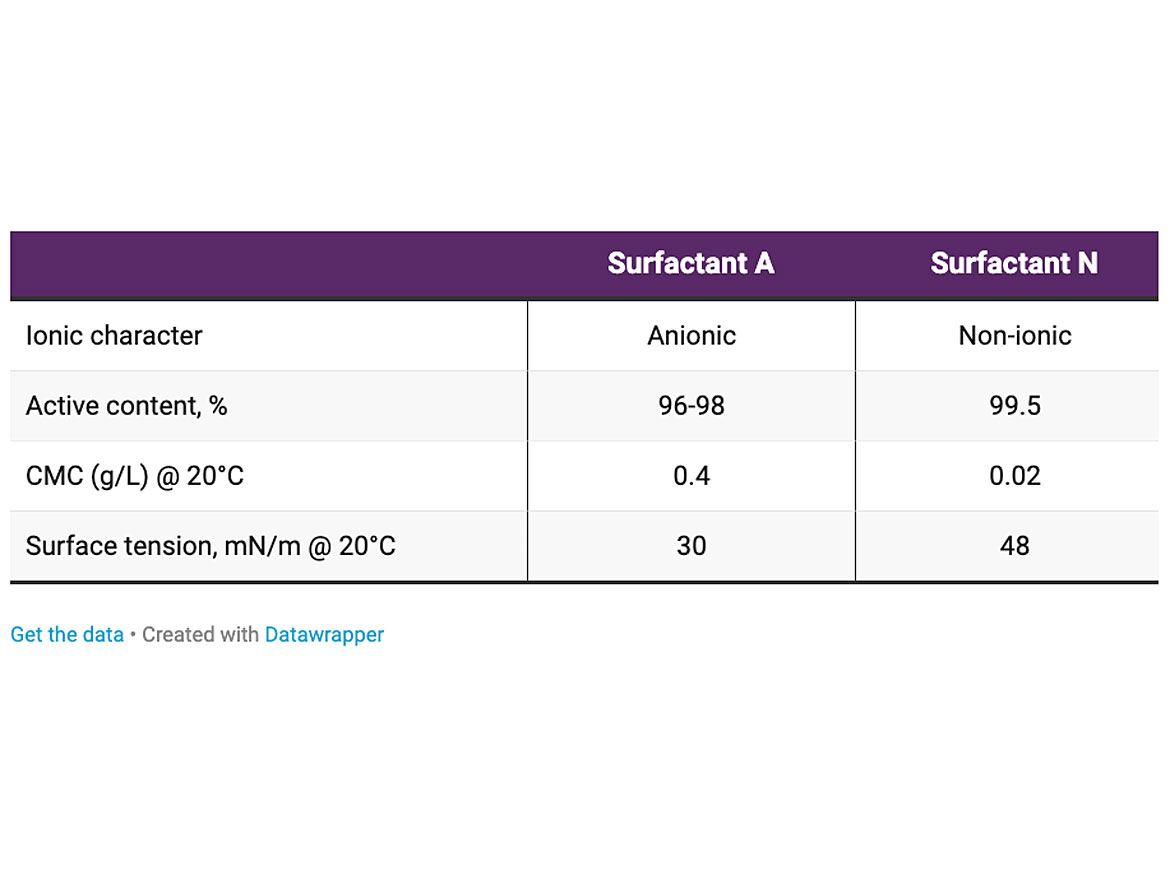
Emulsification Apparatus
The emulsification process was carried out according to the flowchart presented in Figure 3. The alkyd resin was placed in a three-neck round-bottom flask under constant stirring with an overhead stirrer, and kept at 80 °C in a bath. Water was added using a pump.
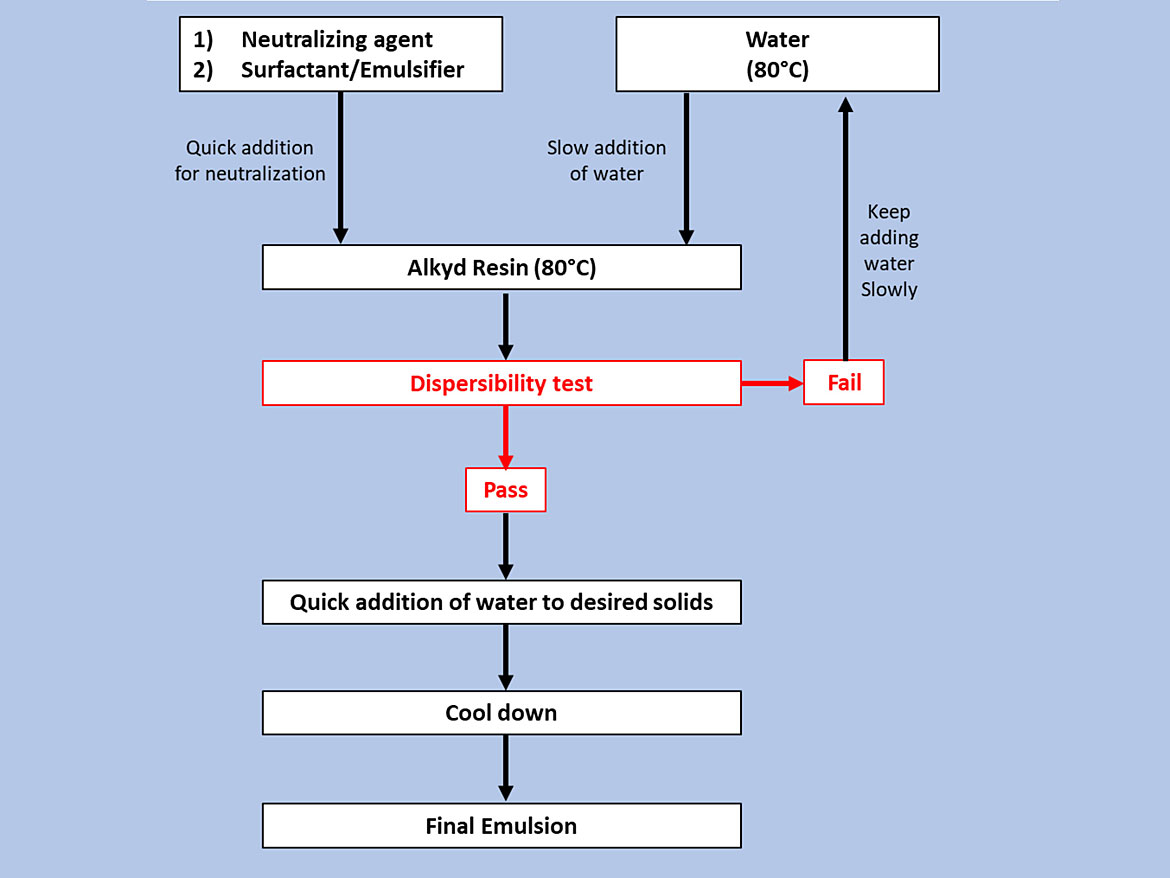
Solid Content
The solid content was measured by weight difference (in oven at 100 °C for 2 hours).
Particle Size
The particle size of the emulsions was measured via static light scattering.
Viscosity
The viscosity of the alkyd resin and the emulsion was measured using a spindle viscometer.
Results and Discussions
Emulsification
The starting formulations used in the emulsifications are described in the Table 3. The total surfactant content evaluated was 7.5% based on resin, or 7.5 parts per hundred parts resin (php). The ratio of nonionic to anionic surfactants used was ranged from 65:35 to 95:5, to evaluate its effect on the main properties of the emulsion.
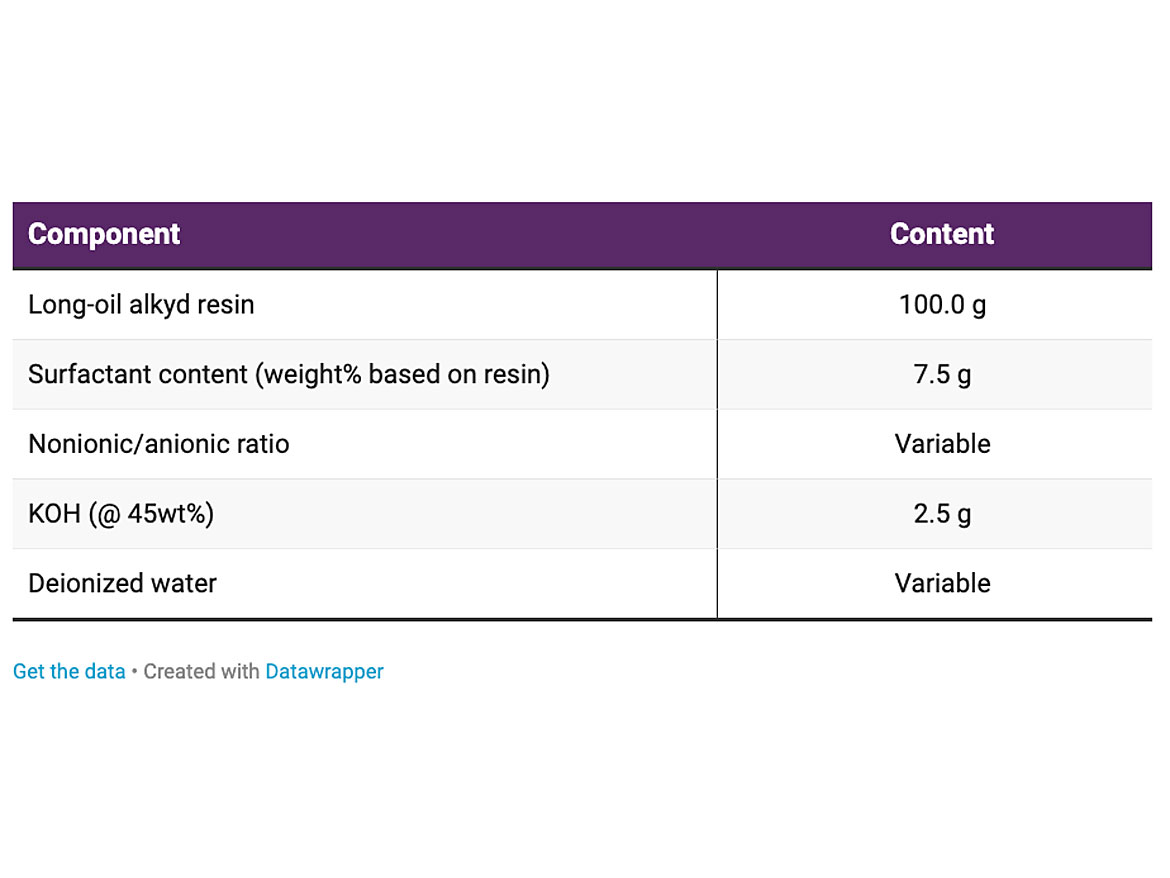
The results for the first set of emulsification reactions are described in the Table 4. For each emulsion we tested solids content, particle size, and viscosity.
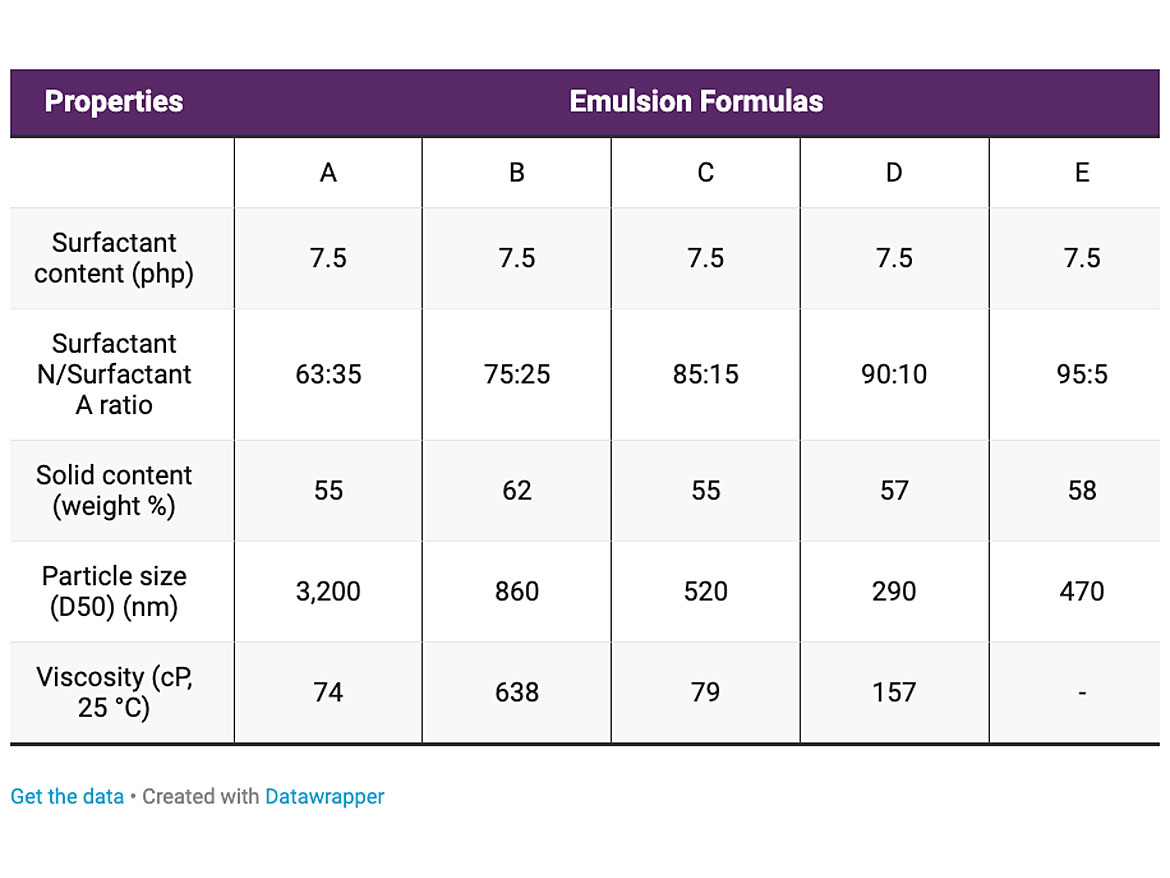
All five emulsions were inverted from water in oil to oil in water and had solids higher than 50% by weight. It is important to note that the emulsification process was carried out at 260 rpm, which is very low shear. This is possible because the structure of the nonionic surfactant has multiple adsorption sites which results in significant reduction in the interfacial tension between the alkyd phase and the water phase. This allows us to generate emulsions with low particle size at low surfactant content.
It is possible to correlate how that the ratio of nonionic/anionic surfactant ratio can determine the particle size of the final emulsion. Figure 4 shows the graph of the particle size for emulsions B, C, D, and E. Usually, emulsions with particle size lower than 500 nm have higher colloidal stability because the Brownian motion suppresses the gravity effect, preventing sedimentation. These results demonstrate the importance of optimizing the surfactant composition for each resin type to generate emulsions with particle sizes lower than 500 nm.
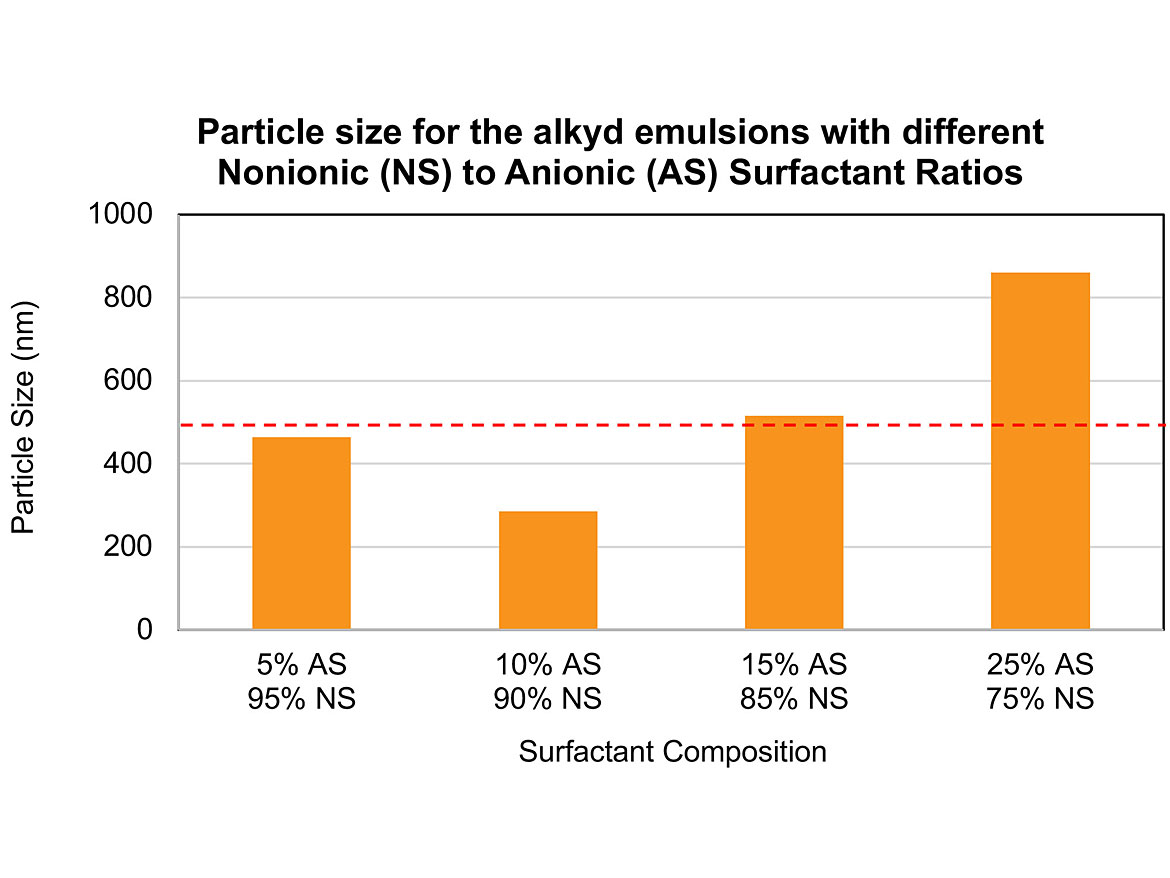
Design of Experiments
Based on these emulsions, it was possible to determine a region in which a low particle size and stable emulsion can be prepared. The second step was the optimization of the emulsion’s properties via DOE. Solid content and particle size were the response factors. The most important parameters that control the emulsification process and the properties of an emulsion are described below. Table 5 describes the factors and levels determined for the experiments.
- Energy input: The type of stirring and stirring rate has an important influence on the creation of the droplets of the dispersed phase.
- Temperature: The temperature controls the viscosity of the liquid phases as well as the solubility and the distribution of emulsifiers in both liquid phases, especially their distribution at interfaces, therefore influencing the interfacial tension.
- Surfactant composition: This influences the pattern of the emulsifier’s adsorption at the interface and the resulting interfacial tension between the liquid phases, as well as the stability of the emulsion.
- Surfactant content: This affects the resulting interfacial tension between the liquid phases, the size of droplet of dispersed liquid, and the stability of emulsions.
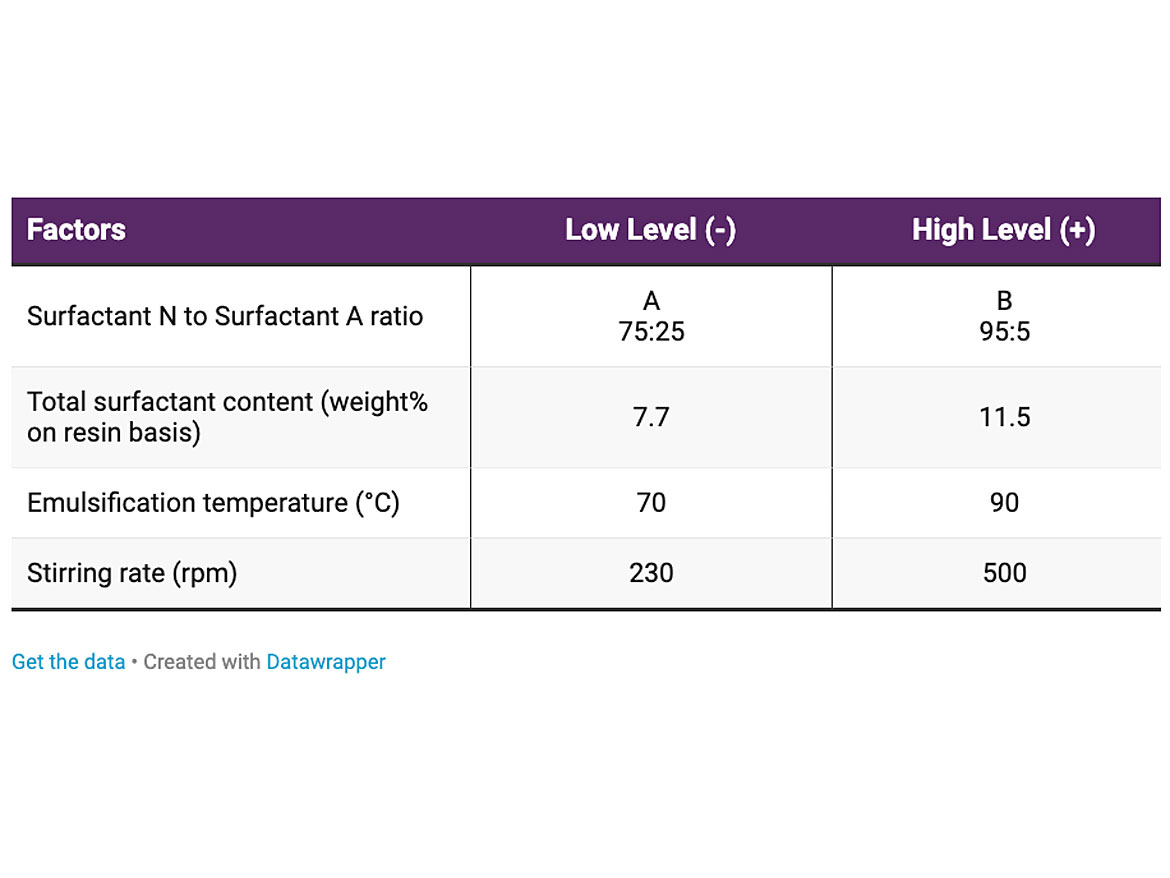
Figure 5 shows the effect of the factors evaluated on particle size. Stirring rate, temperature, and surfactant ratio had minor effect on particle size. The difference is lower than the error of the measurement. As expected, the surfactant content had a significant effect on particle size, and the higher the surfactant content, the lower the particle size of the emulsion.
It is important to remark that within the space in which the DOE was performed, the overall particle size was very low, in fact, lower than 300 nm, for all cases. This trend is interesting because it indicates that for all surfactant contents and compositions evaluated, the low shear rate is more than adequate.
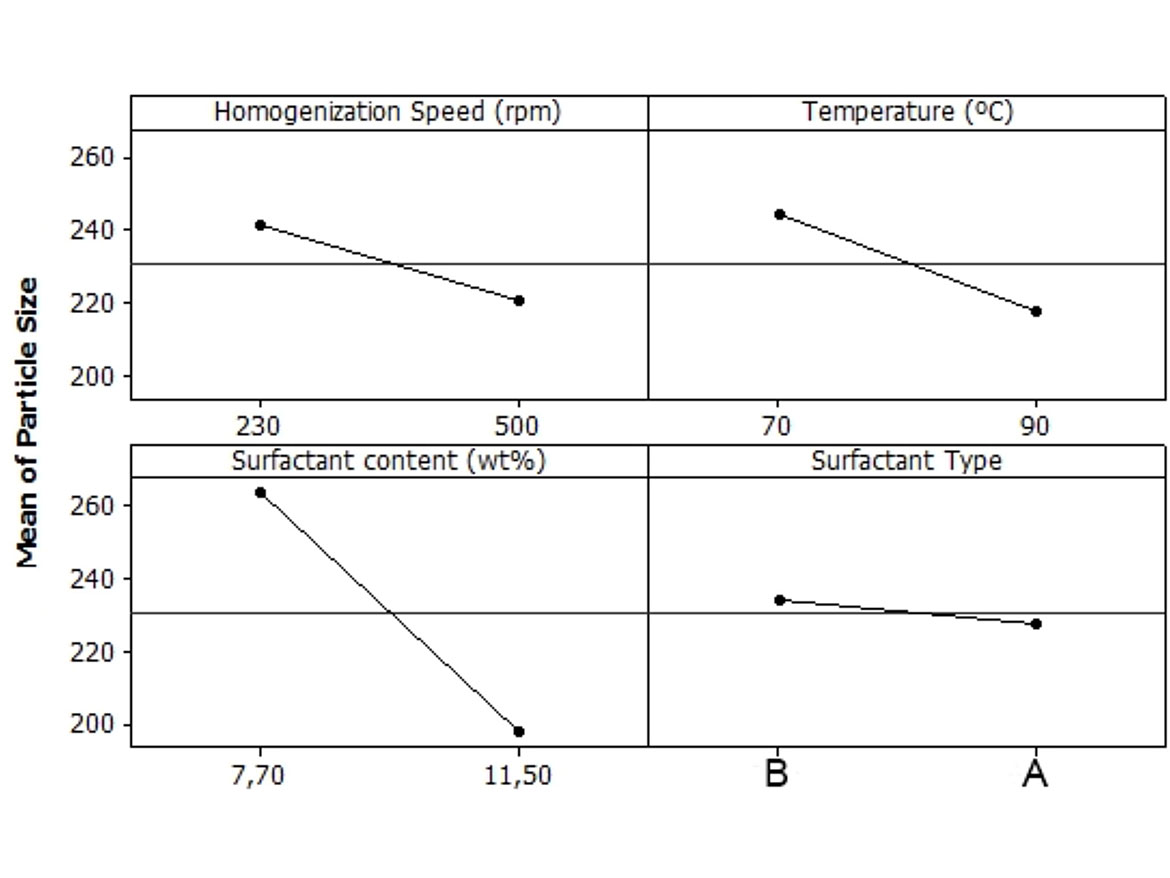
This behavior is unusual for emulsification and it is only possible because the surfactants selected can expressively reduce the interfacial energy between the two phases and stabilize the small droplets. To confirm this trend, a new set of experiments was carried out at a lower total surfactant content. The other factors and levels studied in the DOE were kept as described in Table 5. Models designed using ANOVA are shown in Figure 6 for the experiments conducted at 5.0 php and 6.6 php of total surfactant content.
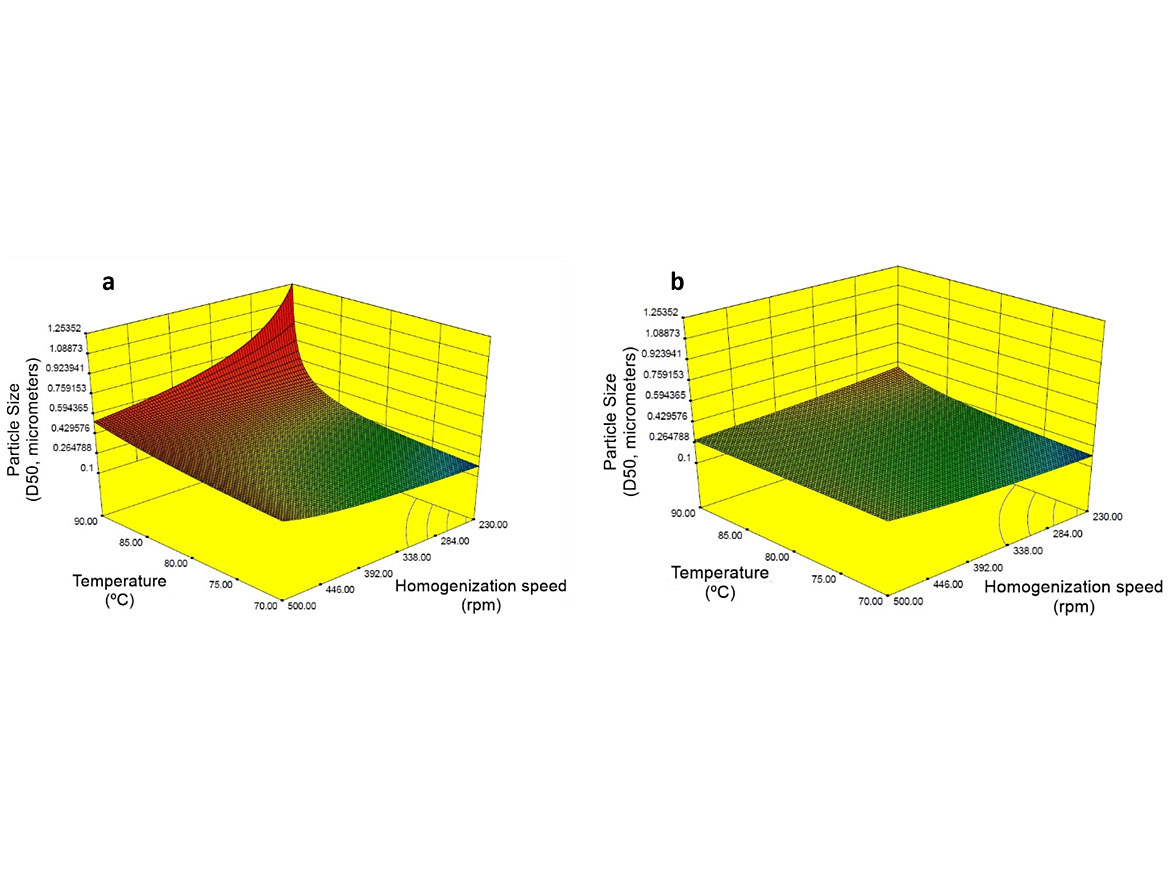
The surface response for particle size presented in Figure 6a shows that at 5.0 php of total surfactant content, the stirring rate becomes a significant factor, and particle size higher than 1,000 nm is obtained at low stirring speed. This experiment shows that it is possible to use a very low dosage of surfactant, but it requires special stirring equipment capable of transferring more energy to the system to generate small droplets. However, the selected surfactants were efficient enough to generate small particles at 6.6 php of total surfactant content. This is not usual for alkyd emulsification that typically requires surfactant content around 10 php.
Figure 7 shows the effect of the factors evaluated on solid content. The stirring rate and the total surfactant content had minor effect on the solid content. The difference is lower than the error of the measurement. The temperature and the ratio of nonionic/anionic surfactant had a great impact on this property. The lower temperature and compositions richer in anionic surfactant allowed the phase inversion to occur more rapidly, hence the solid contents of these emulsions were higher.
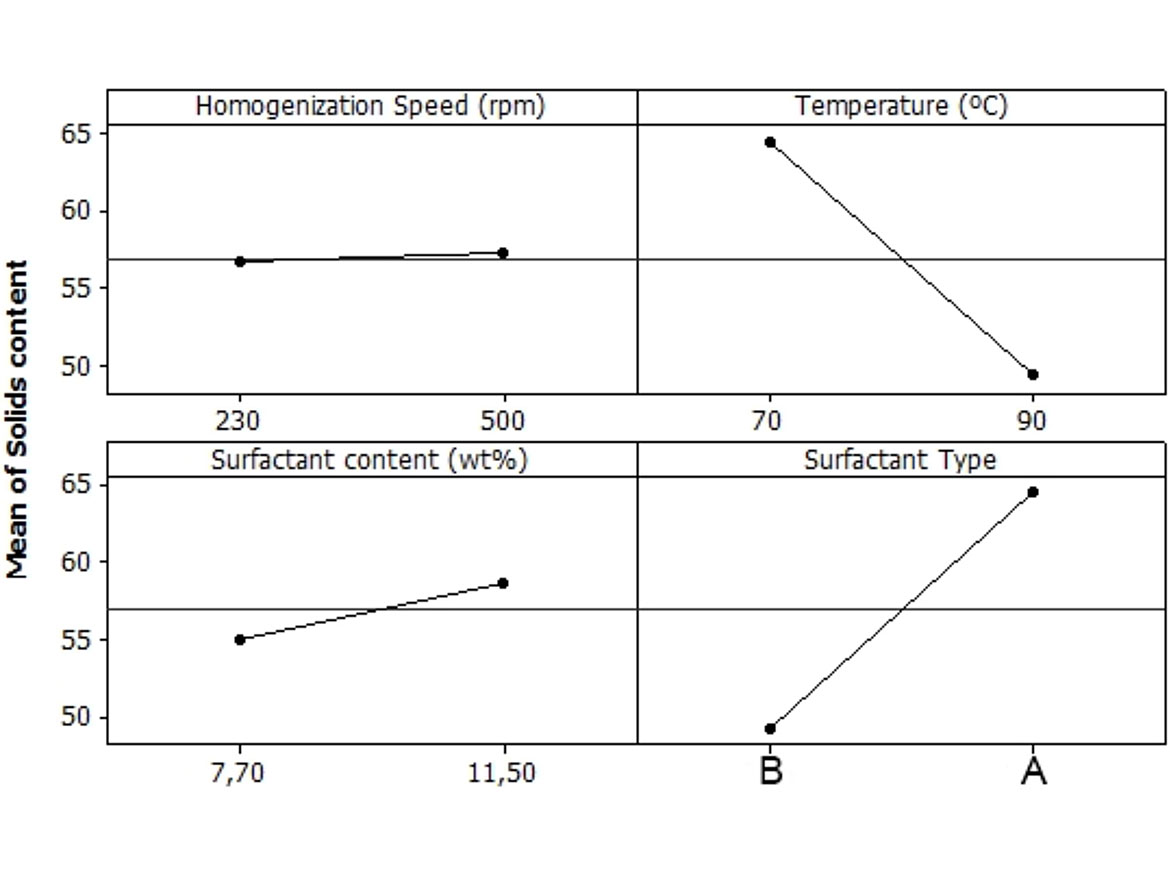
Based on the DOE proposed, it is possible to conclude that for alkyd emulsification through phase inversion methodology using a combination of anionic and nonionic surfactants the key factors are the emulsifier content, the ratio of nonionic to anionic, and the temperature of the process. These three key factors define the inversion point, solid content, particle size, and therefore, the shelf-life stability of the emulsions. Moreover, surfactant content and composition are essential because they can affect hardness evolution, gloss, and water resistance of the final coating.
Based on these studies, the high efficiency of these emulsifiers to adsorb at the water-alkyd interface, decrease the interfacial tension, and stabilize the oil-in-water emulsions are the main reasons for generating a stable oil-in-water alkyd emulsion with small particle size and high solids, while using low energy input from conventional stirring equipment.
In the next article we will cover the life cycle assessment of alkyd emulsions versus alkyd resins and conclusions that were reached.
All information contained herein is provided "as is" without any warranties, express or implied, and under no circumstances shall the author or Indorama be liable for any damages of any nature whatsoever resulting from the use or reliance upon such information. Nothing contained in this publication should be construed as a license under any intellectual property right of any entity, or as a suggestion, recommendation, or authorization to take any action that would infringe any patent. The term "Indorama" is used herein for convenience only, and refers to Indorama Ventures Oxides LLC, its direct and indirect affiliates, and their employees, officers, and directors.
Looking for a reprint of this article?
From high-res PDFs to custom plaques, order your copy today!