Advancing Sustainable Water-Based Coatings
With Heavy-Metal-Free Corrosion Inhibitors

Alexandr Pristavko, Creatas Video+ / Getty Images Plus, via Getty Images.
Sustainability has become a focused effort across the globe. The United Nations has developed 17 Sustainable Development Goals (SDG) to focus society on finding better ways to function that do not negatively affect human health and the planet. The 2030 Agenda for Sustainable Development was adopted in 2015 to identify specific targets for growth in areas such as educational access, elimination of poverty and hunger, clean energy and water, and the pursuit of global peace.1 As we relate these SDGs to the coatings industry, it is clear that we can impact the success of these global initiatives. The coatings industry can address sustainability by focusing on environmental preservation, responsible consumption and production of materials, and the reduction of negative impacts our products can have on human health. High-performance coatings are an essential tool to extend the life of metal assets in many industries including transportation, utilities, manufacturing, and national defense. Corrosion protection is achieved by utilizing a high-performance, multi-layer coatings system, which predominantly includes a primer containing heavy-metal corrosion inhibitors. Direct-to-metal mono-coat systems are also becoming popular to achieve multiple performance attributes in one coat, including corrosion resistance.
Congruently, the annual cost of corrosion is estimated to be $2.5 trillion, which equates to 3.4% of the global GDP, according to the 2013 NACE economic impact study.2 This fact exemplifies protective coatings as an essential need in the global migration to sustainable living. Metal protective coatings vary in performance requirements and regulatory restrictions and are dominated by solventborne technology. Pressure to reduce dependence on solventborne systems is growing, however. Likewise, historical use of corrosion inhibitors based on chromium, lead, and zinc chemistries has brought great benefit to coating performance, but at a detriment to the environment and human health. Advances in technology have produced alternatives containing no heavy metals that maintain coating performance.
Corrosion-preventative chemistries based on lead and chromium are being phased out of formulations because of the negative long-term health effects, long after they became heavily relied upon for coatings performance. Lead-based chemicals were banned in the United States in 1978 due to their impacts on the cardiovascular, reproductive, and cognition systems, which can lead to death. Despite this, many countries continue to allow lead use today. The United Nations has developed the Lead Paint Alliance to reduce the annual deaths attributed to lead exposure, which still stands at 900,000. Currently, 87 countries have lead regulations, but the UN Alliance is targeting 100 more to add to that list.3
Hexavalent chromium compounds, such as strontium or zinc chromate, provide excellent corrosion protection at a modest cost. Hexavalent chrome has been a known carcinogen since the 1920s, but it wasn’t until 1980 that the U.S. Department of Health and Human Services documented it as such.4 Chromium has reached its 2019 sunset date in the European Union and must be registered for special authorization to continue use, which is limited to aerospace and high-performance applications.5
Zinc is another heavy metal that has long been relied upon as a replacement for lead and chromium-based corrosion inhibitors. Increased regulatory scrutiny towards zinc compounds is driving corrosion-inhibitor choices to heavy-metal free (HMF) options. Zinc is defined as a chronic aquatic toxin and is on the candidate list of Substances of Very High Concern for Authorization. Zinc use is still allowed globally, but GHS hazard labeling is required for any formulation consisting of more than 0.25%.6
These few examples of lead, chromium, and zinc regulations are just a snapshot of the complex global regulatory environment that coatings manufacturers must consider when designing, producing, and selling products. The complexity of regulatory compliance continues to grow as each region or country determines its own regulatory constraints for each of these compounds. To achieve optimal corrosion inhibition, the move to heavy-metal-free (HMF) inhibitors in water-based systems will ease the navigation of complex regulatory scrutiny. These HMF solutions are currently found in ICL’s HALOX® product line, along with technical expertise to guide selection and successful formulation. Demonstration of HMF, water-based applications can drive the migration to sustainable solutions.
Background
Corrosion is the naturally occurring oxidation of metal, which can cause structural damage to an object and shorten its lifespan. An electrochemical reaction takes place in the presence of moisture and oxygen, converting a refined metal alloy back to its lower energy state, metal oxide. Figure 1 depicts the standard corrosion cell diagram. Protective coatings are designed to prevent the formation of rust on metal surfaces and extend the life of metal. The resin system is the key contributor to providing the necessary service life of the coating. Corrosion-inhibitive additives further enhance the corrosion resistance by providing chemical interference of the oxidation-reduction reaction of corrosion formation.
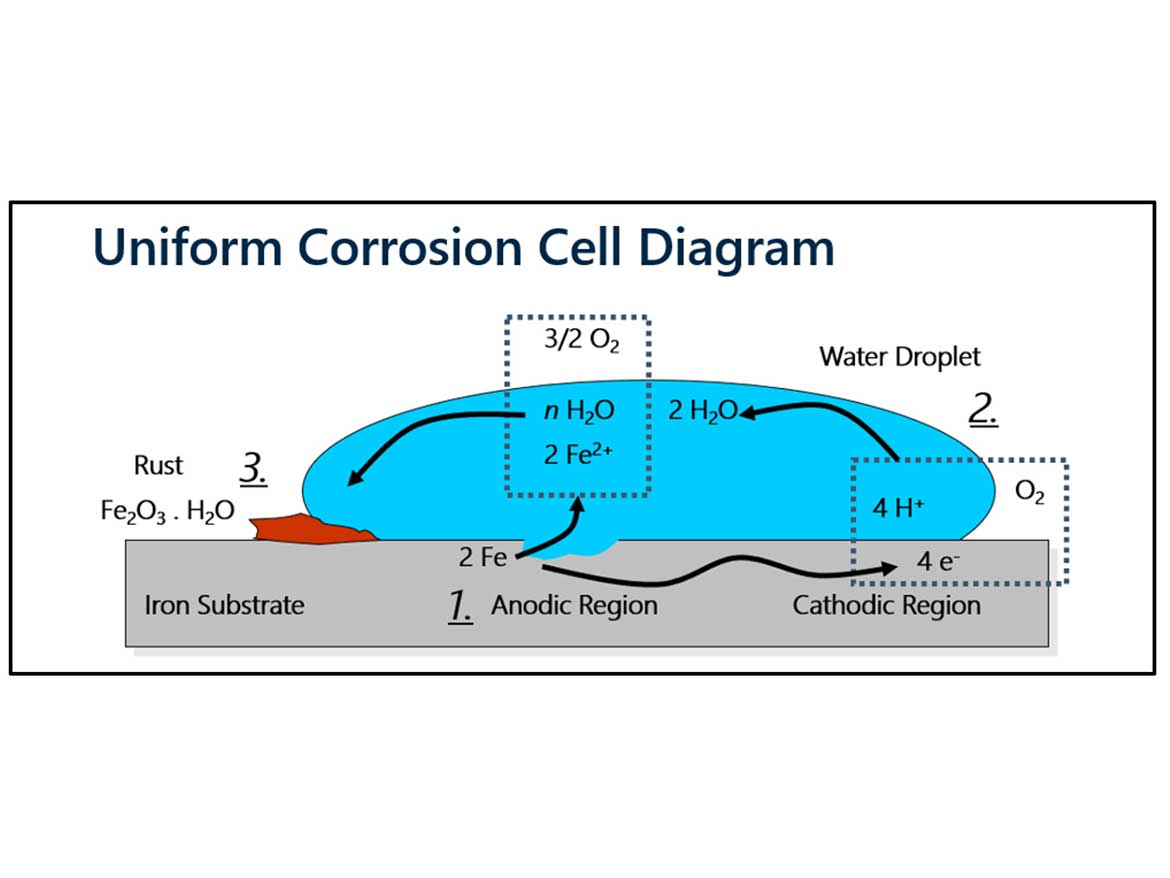
Corrosion inhibition can be achieved by both inorganic and organic compounds. Inorganic materials are commonly relied upon in protective coatings to provide passivation at the anodic site, preventing the formation of a metal oxide. Heavy metal compounds provide passivation and have been relied upon for robust protection. Hexavalent chromium provides unique advantages as it can provide both anodic and cathodic inhibition. This function, along with the versatility in many environments, makes it a difficult compound to replace.4
Other inorganic corrosion inhibitors include metallic salts that solubilize to prevent the oxidation of metal at the anode. Commonly used chemistries include salts of phosphates, molybdates, and borates. The performance level of these materials is dependent on the concentration and compatibility with other components in the coating’s formulation.
A key property that determines performance level is the solubility of the metallic salt. Inorganic inhibitors are insoluble in water. Their very low Ksp values demonstrate the maximum number of ions that will be solubilized in a water solution at a given time. Table 1 depicts the Ksp values for various phosphate salts. Zinc phosphate is known to provide excellent corrosion protection, which correlates to having the lowest solubility. The passivation mechanism will be available for longer-term protection because of the slow solubility.
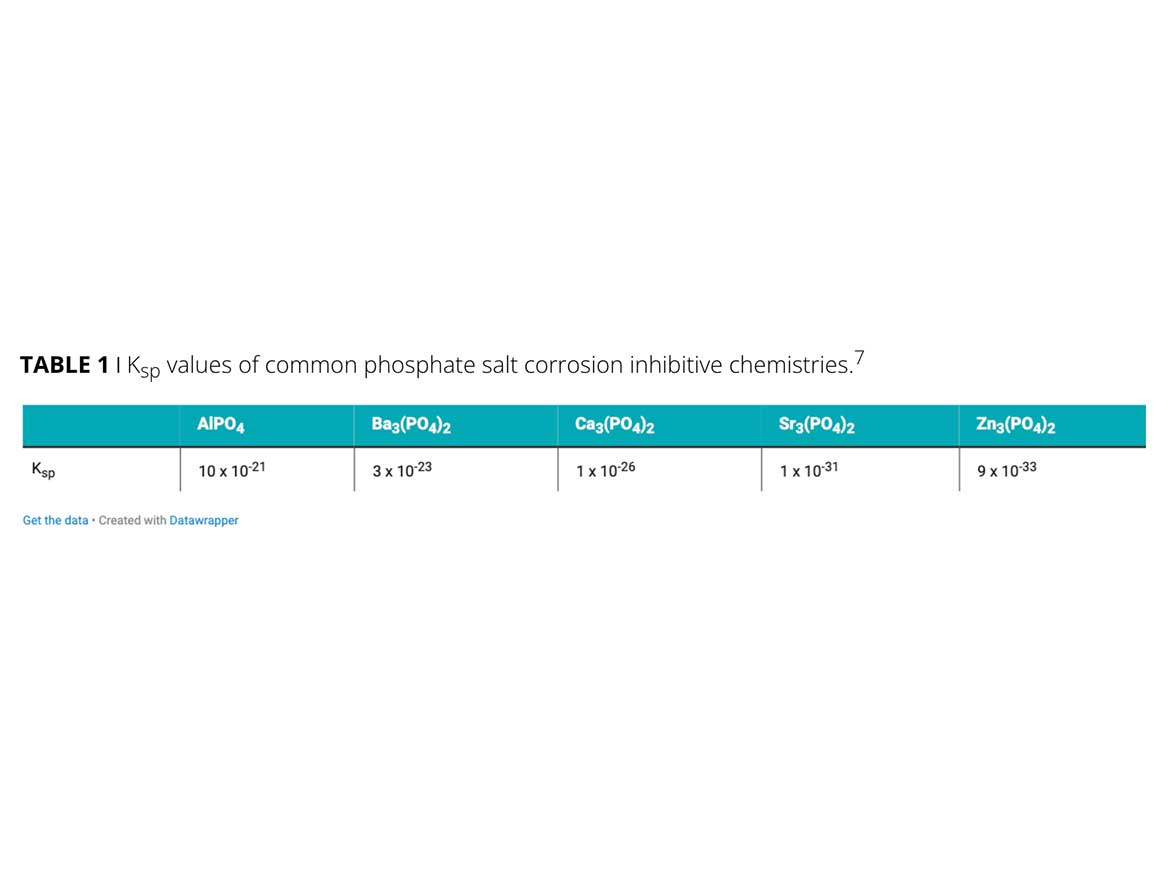
Organic corrosion inhibitors can also be a valuable addition to protective coatings by providing a different mechanism that complements inorganic passivation. The functional groups of organic corrosion inhibitors have a strong affinity to metal and adsorb onto the surface. This provides a stronger interface with the metallic substrate. A hydrophobic protective layer is formed that displaces water at the metal surface, preventing corrosive reactions. The association to the metal substrate can be by physisorption or chemisorption, depending on the chemical structure or surface charge of the metal.8 These properties lead to higher hydrophobicity at the substrate-coating interface, increasing adhesion, which reduces corrosion formation. Organic corrosion inhibitors are generally heavy-metal free and more environmentally friendly, which has generated increased interest and use in protective coatings.
Experiment
Several water-based resin technologies were selected to demonstrate the performance of heavy-metal-free corrosion inhibitors versus their zinc-containing counterparts. Gloss, cross hatch adhesion, field blistering, scribe creep, and field corrosion were assessed during the evaluation. Analysis of these products is predominantly focused on the scribe creep measurements at failure in salt fog as specified by ASTM B-117. At the end of the salt spray exposure, adhesion at the scribe was measured according to ASTM D-1654, Procedure A, Method 2. The panel is scraped perpendicular to the scribe mark with a metal spatula, and a measurement of total scribe width, divided in half, is reported. Measurements of the scraped scribe were taken at five positions along the scribe and averaged over two panels. For this study, scribe creep values are measured in millimeters and expressed as a percentage improvement versus the control.
Coatings systems were evaluated by screening various corrosion-inhibitor chemistries versus a benchmarking standard. In place of the corrosion-inhibitive pigment, the control formula contains equal volume of calcium carbonate to maintain the PVC of the system. Various chemistries of corrosion inhibitors were tested in each system to demonstrate a wide range of products. Cold-rolled steel panels were coated with trial coatings using a bird bar. Dry film thickness for each experiment varies depending on the application parameters.
In the first example, a light-duty water-based 1K-polyurethane formulation was used to screen zinc versus zinc-free inorganic powders. Strontium zinc phosphosilicate (SZP), and calcium phosphate (CAP2), were tested versus a calcium carbonate control. After 144 hours of ASTM B-117, the scribe creep results for the zinc-containing product (SZP) did not show an improvement over the blank. Both levels of the CAP2 sample improved the scribe creep significantly. The 4% calcium phosphate sample demonstrated half the amount of scribe creep versus the zinc and blank samples (Figure 2). Cross-hatch adhesion also improved with the addition of the calcium phosphate. This formula demonstrates the gloss impact corrosion-inhibitive pigments can have in high-gloss coatings (Table 2). As the calcium phosphate loading level increases, the gloss level is reduced while the scribe creep improves. A balance of the performance requirements must be found to achieve formula constraints.
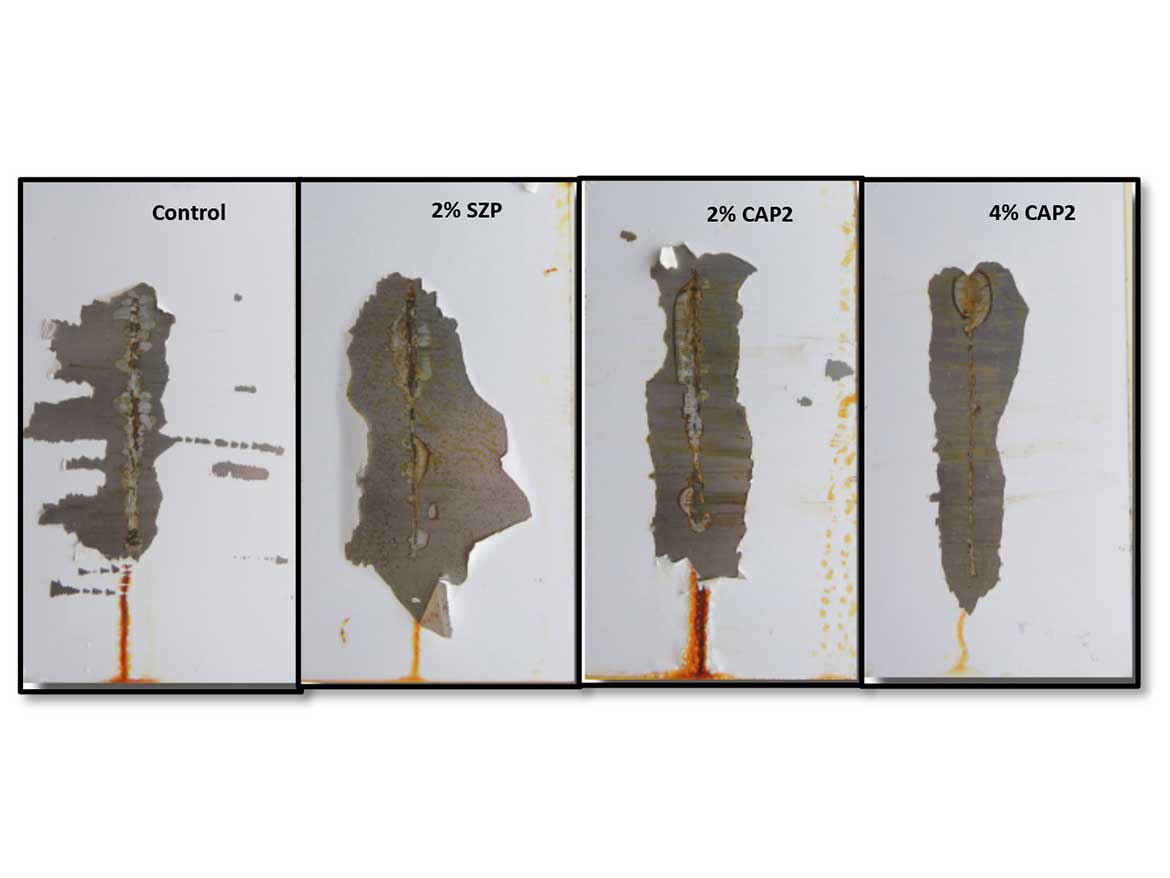

In the second case study, HMF options strontium phosphosilicate (SRP) and two calcium phosphates (CAP1 and CAP2) were evaluated versus zinc-containing products, strontium zinc phosphosilicate (SZP), and zinc phosphate (ZP). They were formulated into a 2K water-based epoxy system at a 5% loading level. In this case, the zinc-containing products provided a four times scribe creep advantage over the blank control. Two of the three HMF counterparts further improved creep measurements to nine times and seven times versus the control. The third HMF product, CAP2, provided equal performance to the zinc-containing options (Figure 3).
Historically, zinc-containing corrosion inhibitors have the widest breadth of use and compatibility in many resin systems, while providing excellent performance benefits. This can be seen in this formulation, but this test set also demonstrates further advancements can be achieved when optimizing corrosion-inhibitor packages to find the most compatible chemistry. HALOX heavy-metal-free options are achieving good results in low- and medium-duty applications. There are options to not only match the zinc chemistries, but also exceed their performance, while moving to a HMF option.
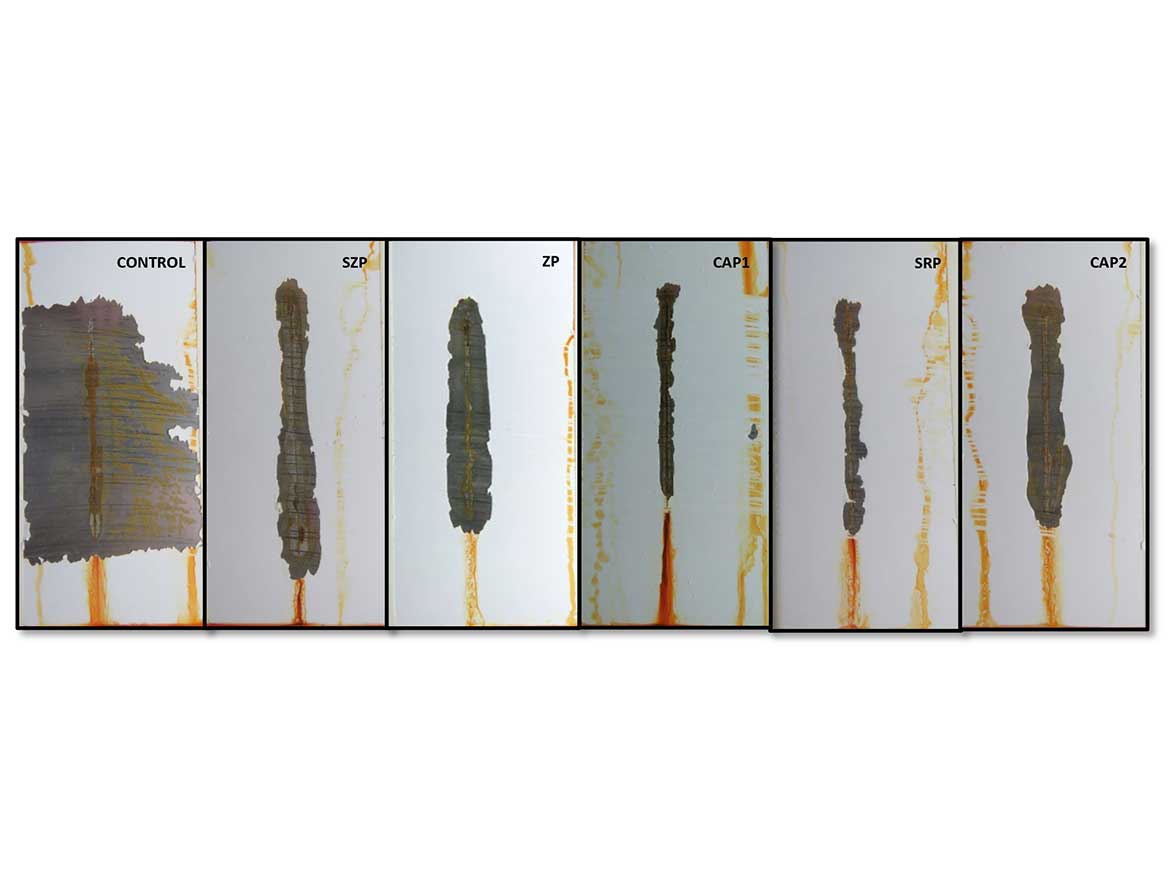
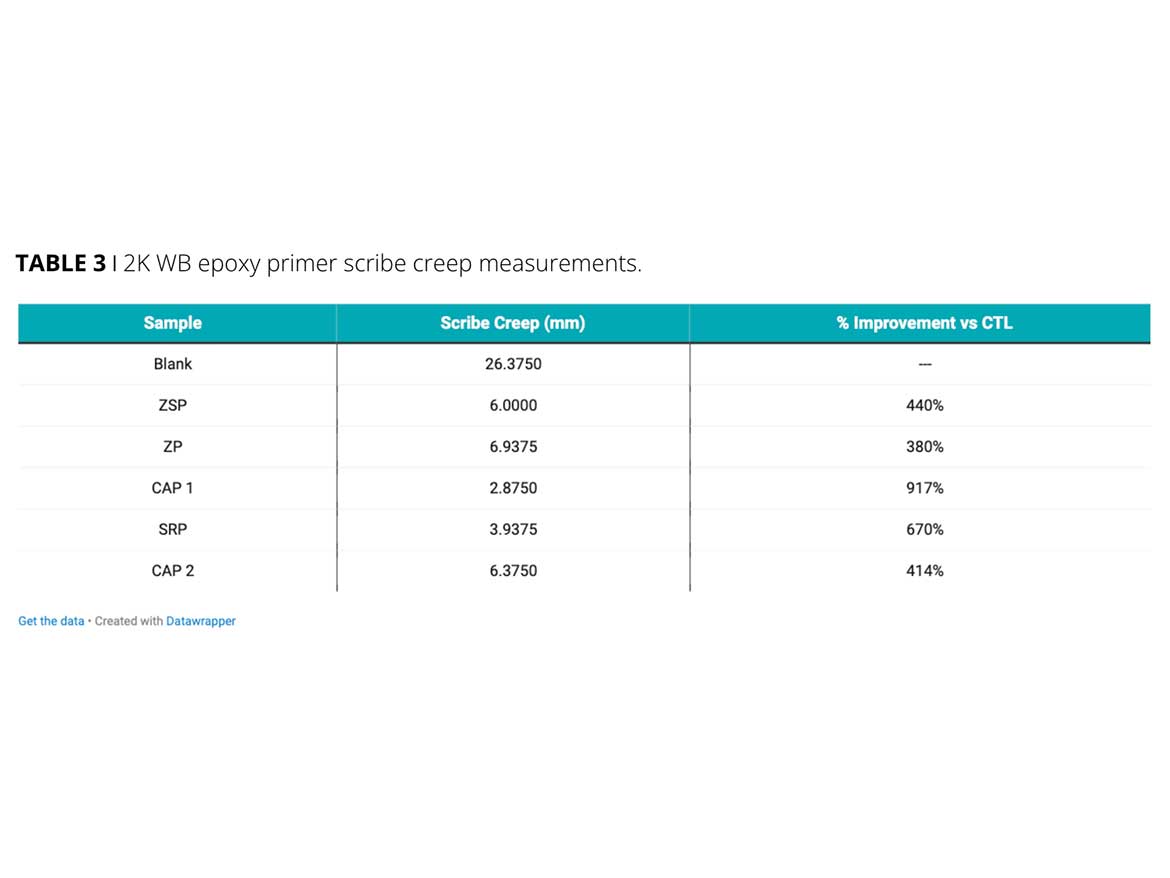
Organic chemistries can also provide corrosion benefits in applications where inorganic pigments are not tolerated. These situations are common when developing a high-gloss product, or when the application requires a low dry-film thickness. In the case of this water-reducible alkyd system, an organofunctional silane (OFS) addition provides a blistering reduction at the scribe at 96 hours of salt spray testing. The adhesive benefit of the silane reduces delamination at the scribe, as seen in Figure 4. When the loading level is optimized, the functional groups of the molecule can also act as a wetting agent and offer improved gloss levels (Table 4).
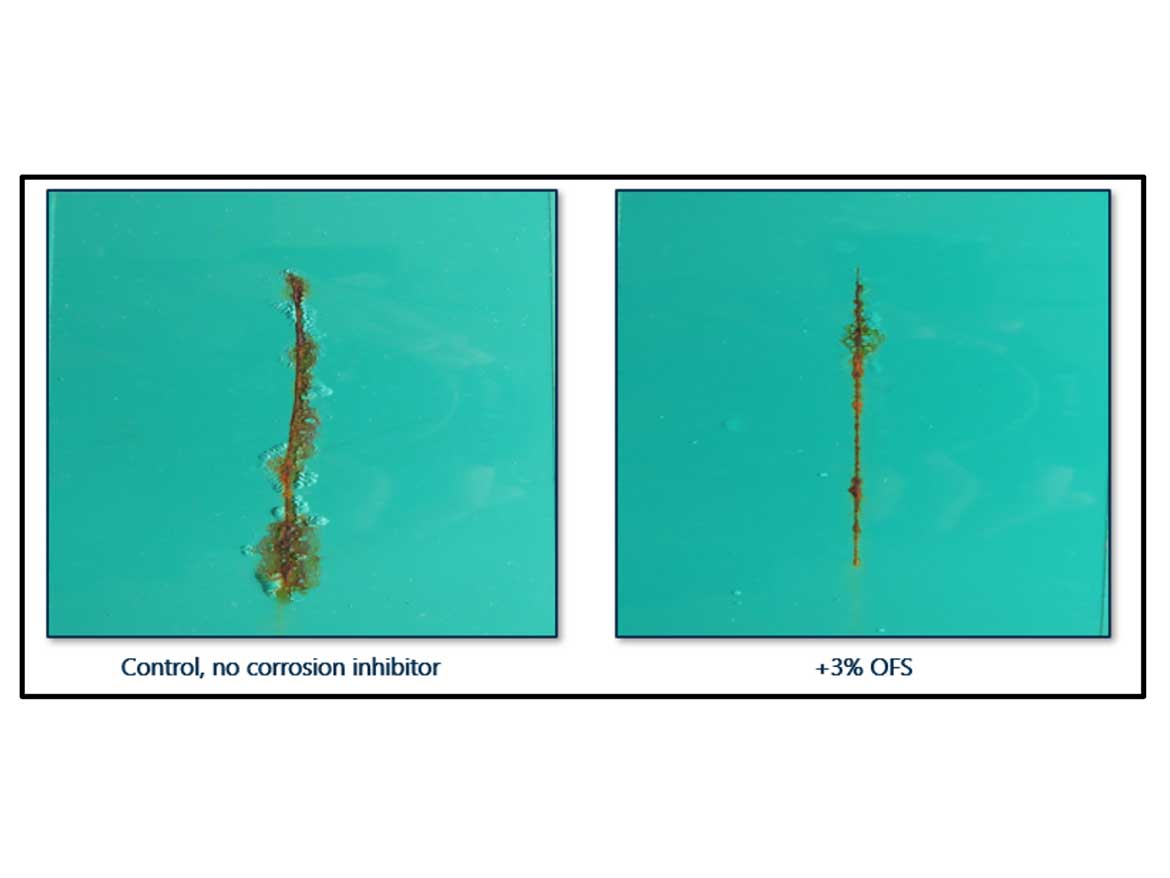
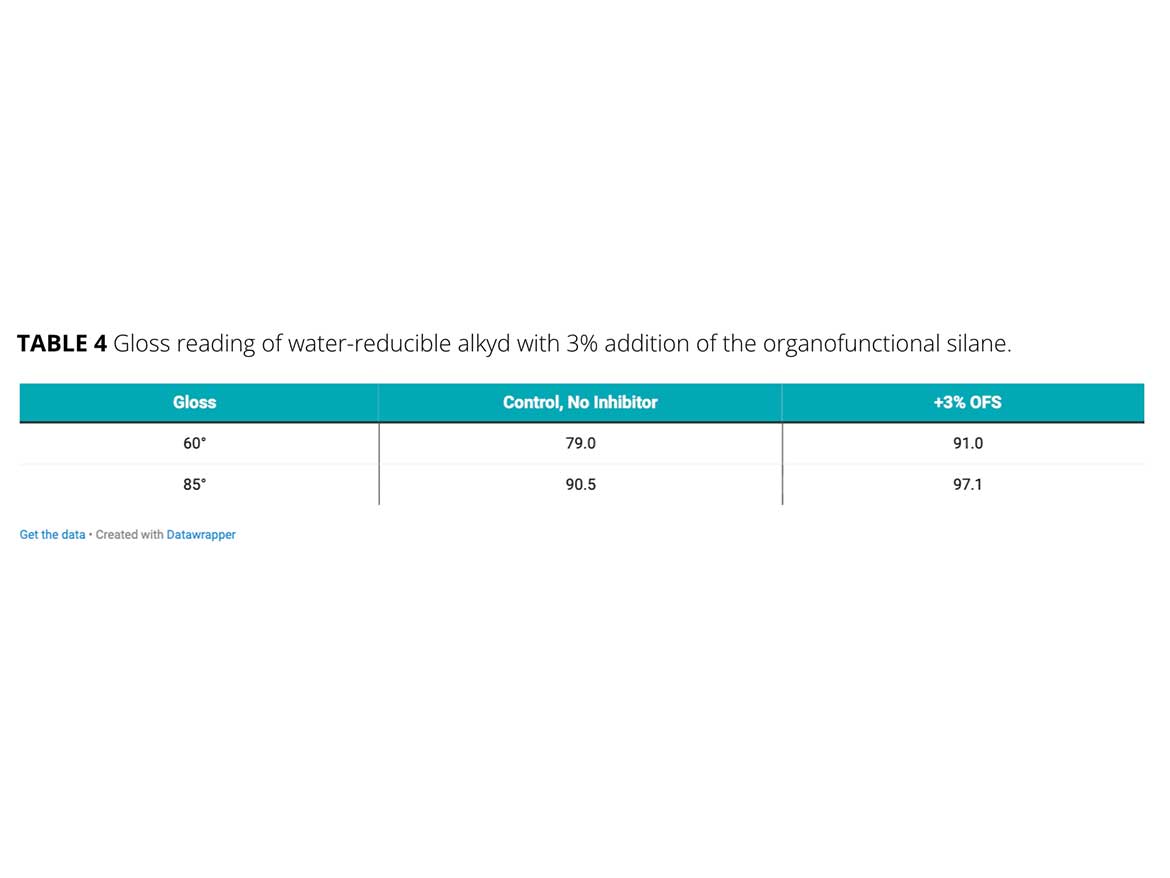
The addition of an organofunctional silane has also demonstrated benefits in a water-based acrylic-epoxy hybrid system. The scribe creep width was greatly reduced with just 0.5% addition, based on total formula weight. Further enhancement of the corrosion performance was achieved by adding a complimentary acid-amine complex (AAC) and an inorganic powder, strontium phosphosilicate (SRP). The combination of these three products provides superior performance versus the blank control, all while providing solutions that are HMF. The corrosion-inhibitor combination achieved 336 hours of salt spray exposure, while the blank failed at just 24 hours (Figure 5). The addition of the SRP doubled the salt spray performance beyond the organic products on their own. Combining multiple products allows the formulator to fine tune the performance of the coating based on the performance requirements for each application.
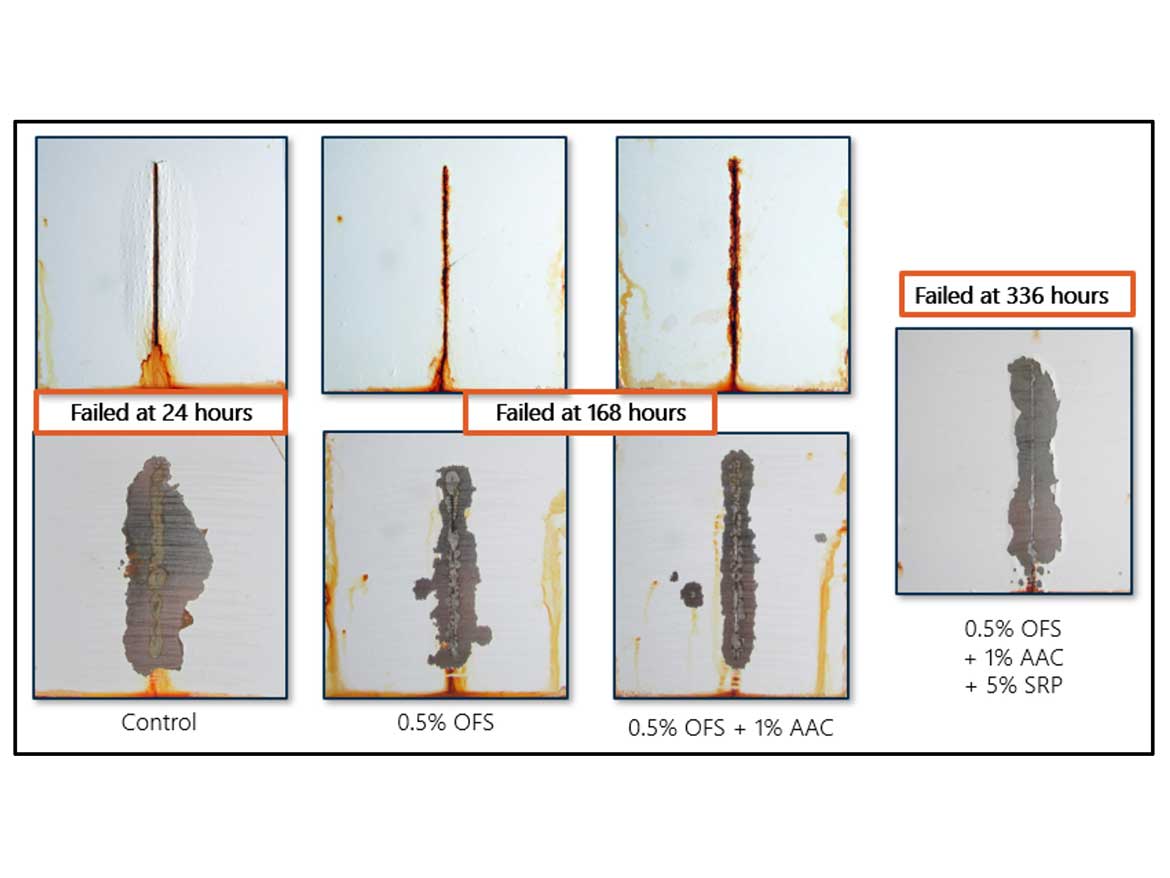
Conclusion
Metal asset protection is an essential component of the global economy. Protective coating performance will continue to be a demanding application that requires superior protection and environmentally friendly solutions. The migration to heavy-metal-free options is already in progress, along with the shift to water-based coatings. Combining these technologies provides performance achievements that meet the demanding regulatory landscape the industry is facing.
As the global focus towards sustainable practices takes hold, we must re-evaluate the use of all materials in our coatings to provide safe and effective solutions. Successful demonstration of utilizing sustainable corrosion inhibitors in water-based systems will lead the industry to regulatory compliance. These “green” products can match the performance of previous technology, maintaining service life and the cost expectation for reapplication.
Contributors
The author would like to acknowledge the contributions of the ICL Paints and Coatings R&D team members: Candace Bonner, Dr. Anthony Gichuhi, Yvette Gomez, and Tanya Hunter.
References
1 Transforming our world: the 2030 Agenda for Sustainable Development, A/RES/70/1, UN General Assembly. (2015).
2 Koch, G.; Varney, J.; Thompson, N. et al. International Measures of Prevention, Application, and Economics of Corrosion Technologies Study, NACE International, 2016.
3 (2022). Inside the push to eliminate lead from paint. UNEP.https://www.unep.org/news-and-stories/story/inside-push-eliminate-lead-paint.
4 Gharbi, O.; Thomas, S.; Smith, C. et al. Chromate replacement: what does the future hold? npj Materials Degradation 2, 12, 2018.
5 REACH Authorisation and Hexavalent Chrome. International Aerospace Environmental Group. https://iaeg.com/wg5-chromate-authorization-communication.pdf.
6 Zinc oxide Brief Profile. ECHA. https://echa.europa.eu/brief-profile/-/briefprofile/100.013.839.
7 Haynes, W. G. (2014). CRC Handbook of Chemistry and Physics. In CRC Press eBooks. https://doi.org/10.1201/b17118
8 Chandra Sahu, B. Organic Corrosion Inhibitors. IntechOpen, 2023.
Looking for a reprint of this article?
From high-res PDFs to custom plaques, order your copy today!