Development of More-Sustainable Water-Based DTM Coatings
Part 1, Latex Paints

Soy is a highly abundant, sustainable, cost-effective renewable material, offering a viable alternative to petroleum-derived products. For over seven decades, soybean oil has served as a drying oil in solventborne alkyd coating resins. As the demand for sustainable, domestically sourced renewable feedstocks grows, coatings manufacturers face the challenge of finding bio-based materials that are environmentally friendly and excel in demanding applications. The United States leads in producing high-quality soybeans and their resulting oil. Compared to other oilseeds, U.S. soy boasts superior consistency, lower color, odor, and impurities. While soy is a global commodity, the United States, Brazil, and Argentina stand among the largest soybean producers.
The United States Soybean Export Council (USSEC) engaged Blonk Consultants, an international leader in environmental and sustainability, to conduct a study on the carbon footprint of soy from various regions. It was determined that U.S. soy has higher yields, minimal fertilizer use, and efficient machinery, all of which help minimize its carbon footprint. In addition, cultivation significantly contributes to carbon footprint and Land Use Change (LUC), which sets U.S. soy apart as a highly sustainable raw material (Figure 1).
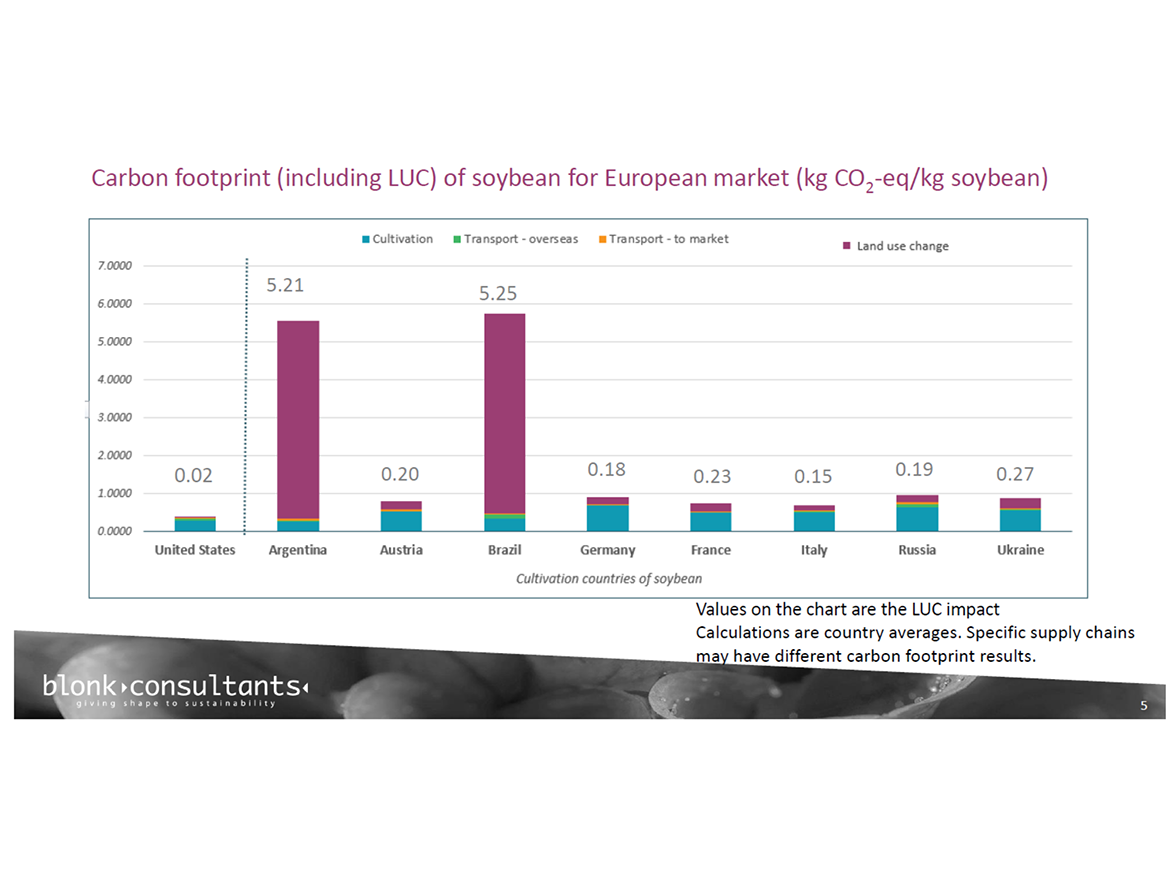
The projected 2023 soy harvest in the United States is estimated at 4.5 million bushels, yielding approximately 25 billion pounds of soybean oil.1 Crushing capacity is anticipated to grow by 30% over the next three years in the United States, significantly increasing the availability of soybean oil domestically.
The U.S. Soy Sustainability Assurance Protocol outlines regulations, processes, and management practices to ensure sustainable soybean production. Over 95% of U.S. soy farmers participate in this third-party verification, focusing on four sustainability directives: bio-diversity, conservation, public labor, health and welfare, and continuous improvement in technology and cultural practices.1 Between 1980 and 2020, U.S. farmers have increased soy production by 130%, while improving energy use efficiency by 46%, and greenhouse gas emissions efficiency by 43%.2 United States soy farmers continue to target aggressive goals to further reduce land use, soil erosion, energy use, and greenhouse gas emissions by 2025.
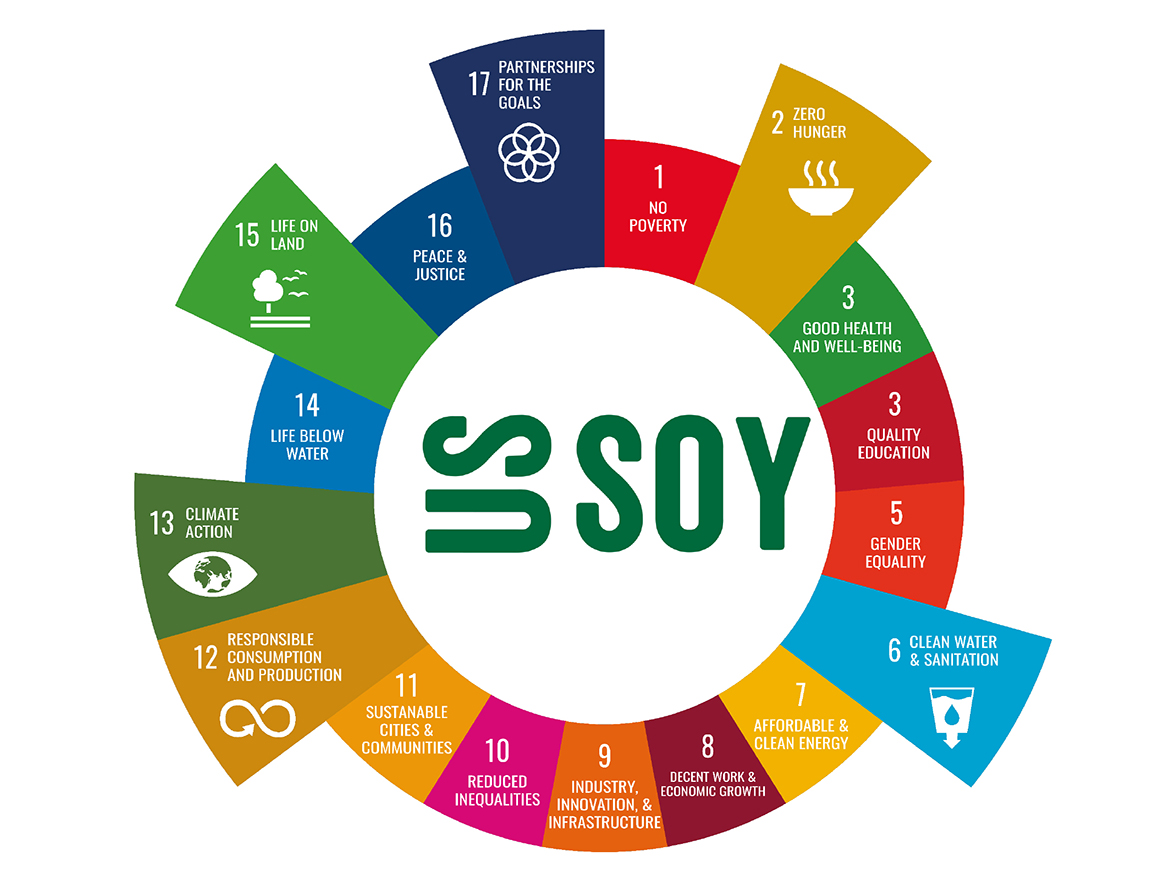
Furthermore, U.S. soy strategically maps to the United Nations' sustainability goals. By enhancing crop yield, promoting sustainable farming techniques, and ensuring equitable access to resources, U.S. soy contributes significantly to addressing goal number two – zero hunger. Moreover, this initiative intersects with five other sustainable development goals, leveraging resilient agricultural practices to influence broader environmental and societal objectives for U.S. farmers positively (Figure 2).
Soy in the Coatings Industry
In response to environmental regulations, the coatings industry has been compelled to develop eco-friendly formulations, including low-VOC solventborne alkyd coatings, waterborne, high-solids, and powder variations. To meet these demands, coating scientists are revisiting key attributes of soybean oil – hydrophobicity, unsaturation, and carbon chain length.
Commercially available in unrefined or refined/bleached/deodorized grades, soybean oil's hydrophobic nature and C18 carbon chains contribute to performance improvements in coatings, enhancing hydrophobicity and flexibility in the coating film. The unsaturated fatty acids provide reactive sites, forming the foundation for chemical intermediates. Even after transformation, soybean oil's unique properties result in coatings with outstanding water repellency, impact resistance, strength, toughness, corrosion resistance, and adhesion to substrates (Figure 3).
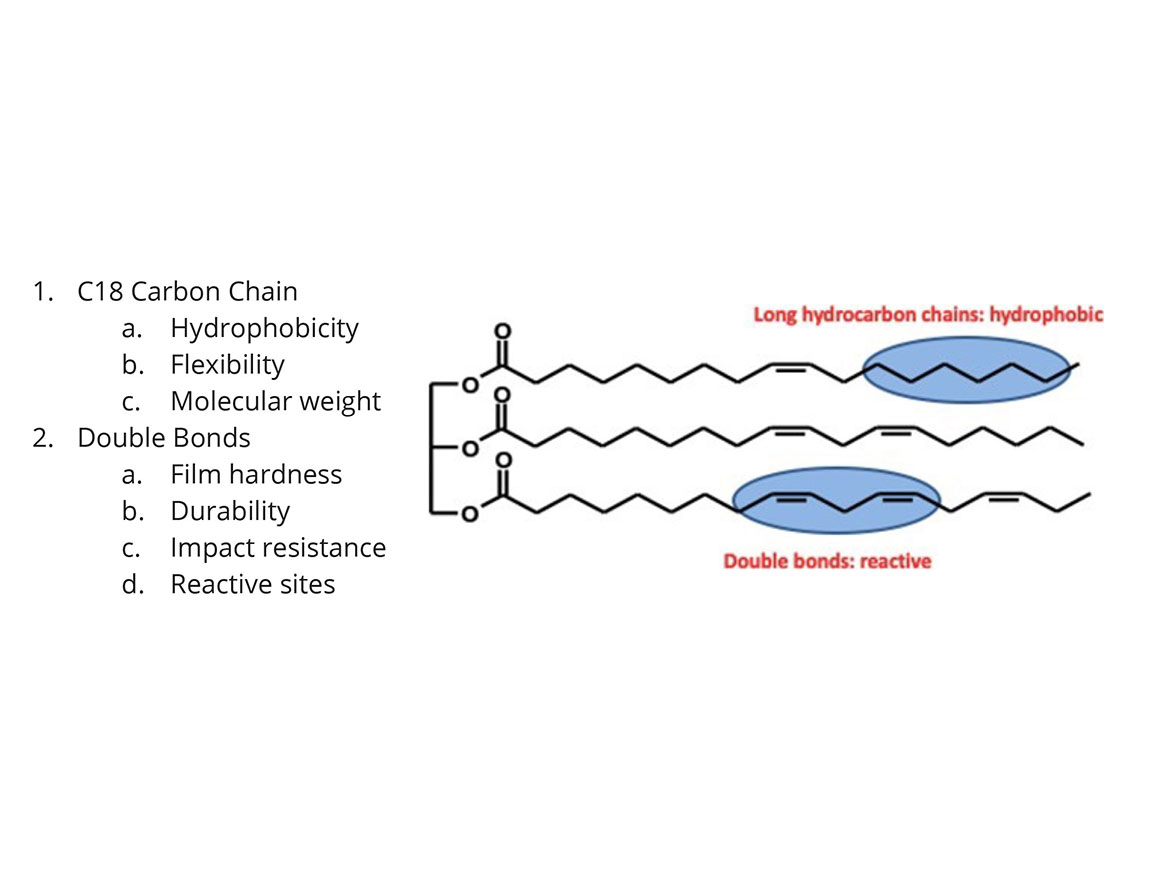
Soybean oil also serves as the building block for various intermediates, including methyl soyate, epoxidized soybean oil (ESO), and epoxidized methyl soyate (EMS) (Figure 4).
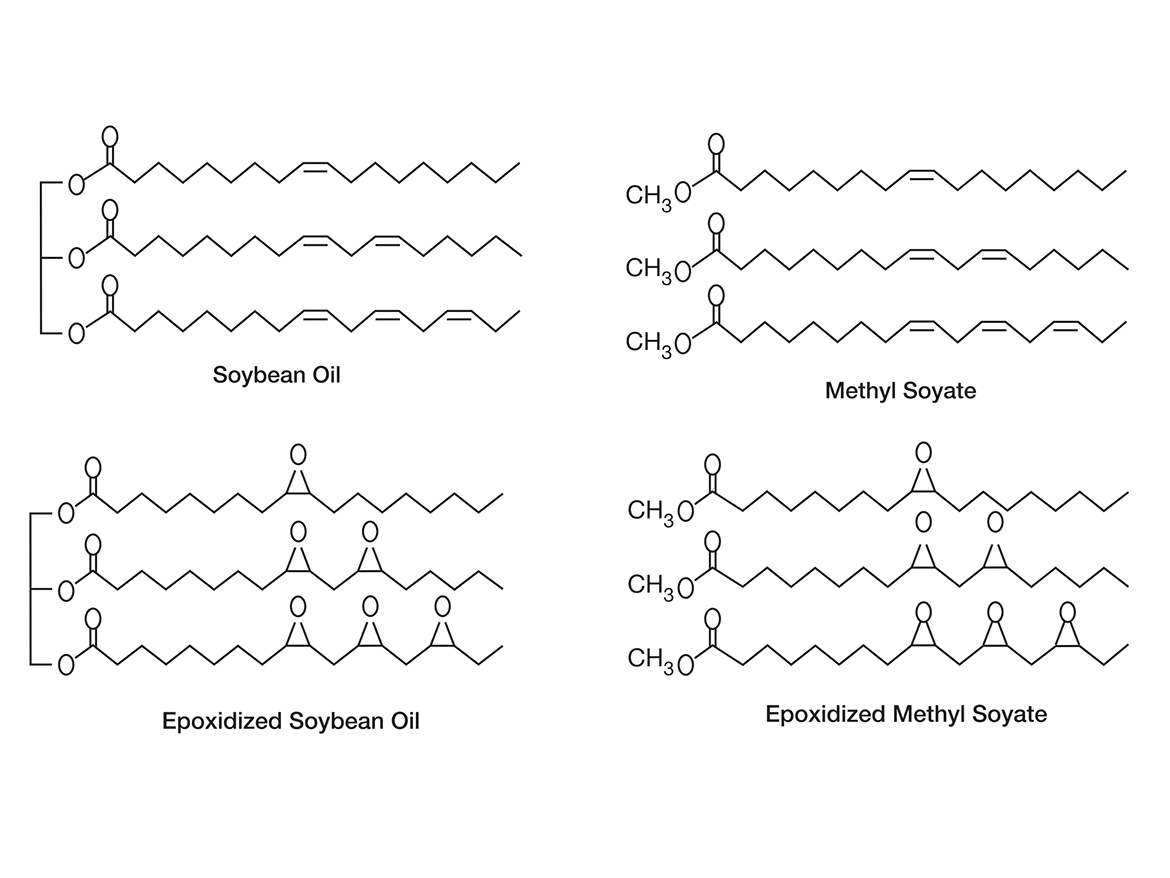
Epoxidized soybean oil (ESO) offers higher chemical reactivity, presenting opportunities for diverse chemistries in resin development. It is produced by the oxidation of soybean oil with a peroxide or a peracid to convert the double bonds into epoxy groups. ESO offers a higher chemical reactivity. For many years, it was used as a green plasticizer for PVC. However, chemists have discovered that the reactive epoxy groups lend themselves to great opportunities for a multitude of chemistries.
Building up this highly sustainable raw material's unique chemical structure with multiple unsaturation sites enables it to undergo various chemical transformations, producing polymeric materials with versatile applications in paint and coatings, while retaining the inherent hydrophobicity property.
Soybean oil opens many opportunities for cross-linkable resin technology, contributing to coating hardness, durability, and impact resistance. In addition to alkyd-based resins, soy is a key material in other raw materials for paint and coatings, including coalescents, solvents, and dispersants.
United Soybean Board Funded Research
Because of the potential for bio-based products to create new markets for soybeans, U.S. soybean farmers have invested millions of dollars to research, test, and promote bio-based products. Much of this work was done through the United Soybean Board (USB), composed of 77 U.S. soybean farmers appointed by the United States Secretary of Agriculture to invest in soybean checkoff funds.
Throughout the years, research funded by the USB has focused on many soybean derivatives ranging from waterborne architectural wood coatings to high-performance, low-VOC industrial direct-to-metal coating applications.
In the last two years, the USB has extended its research efforts in collaboration with Stonebridge Coatings Labs. The objective is to showcase the performance of sustainable, soy-based coating materials in real-world formulations, comparing them to benchmarks derived from petroleum-based counterparts.
Development of More-Sustainable Water-Based DTM Coatings
Throughout the years, the coatings industry transitioned from solvent-based paint to water-based paint for the architectural coatings market, with industrial coatings following suit years later. Today, this is accomplished primarily using latex polymer resins. These resins result from emulsion polymerization, where tiny liquid particle droplets of organic resin are suspended in water.
The resins are made from various monomers combined to create more extensive polymeric materials that give paints their protective performance properties, such as abrasion, water, and corrosion resistance. Several factors affect performance, including monomer types, molecular weight, and ionic stabilization. Typically, harder latexes with higher molecular weights provide better performance.
All latex polymers dry through a process called coalescence. These tiny polymeric particles fuse as the water evaporates to create a continuous, protective film. Very-soft polymers fuse readily, but harder, more-durable polymers require coalescing agents to temporarily soften the particles to essentially stick them together. The most common measurement of a latex's coalescing capability is minimum film forming temperature (MFFT). This is the minimum temperature at which the latex polymer forms a continuous film after the water evaporates. Below this temperature, the resulting film is brittle and non-continuous. Figure 5 illustrates an MFFT test strip where the liquid latex is cast onto a platen surface with cold temperatures at one end (left) and increasingly warmer temperatures at the other (right). The measured MFFT is where the cast film goes from cracked or crazed to a transparent, continuous film.
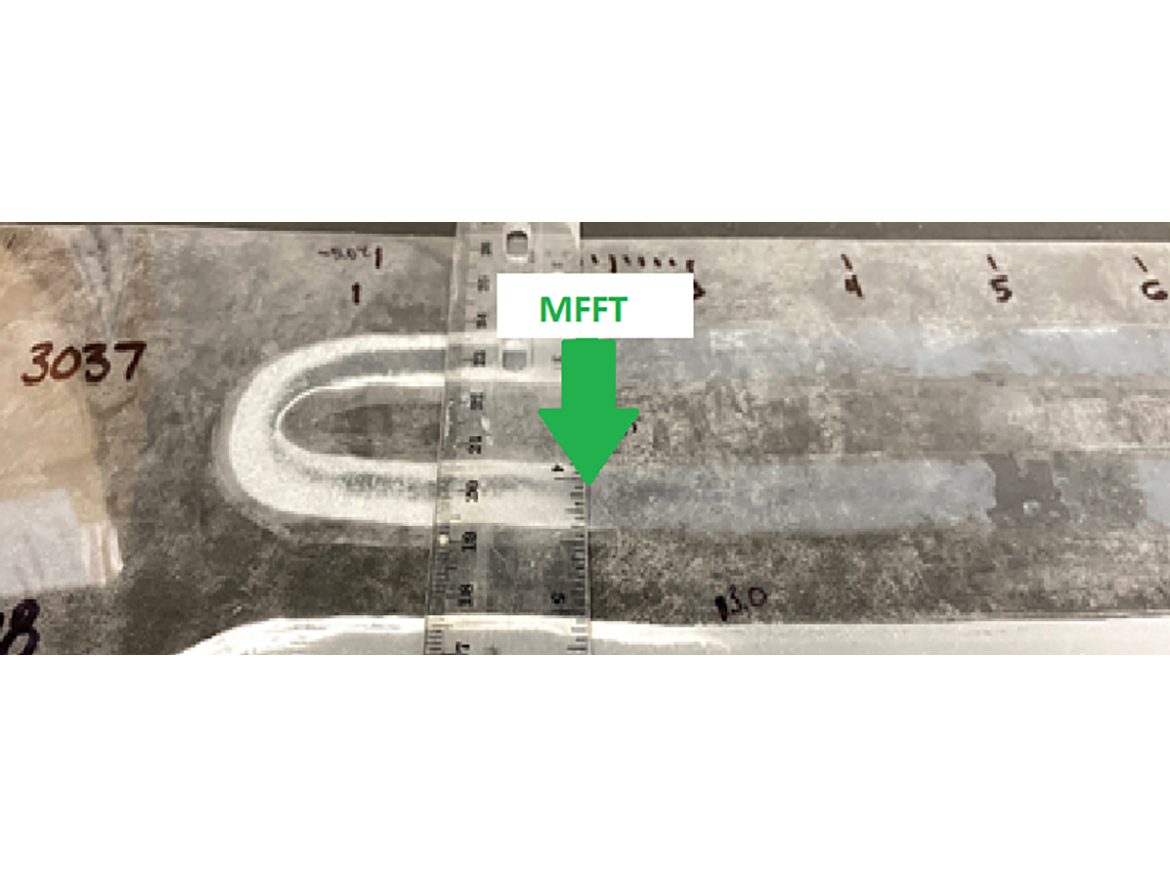
Most latex resins used in the market today require coalescing agents. These are typically petroleum-based, higher-molecular-weight solvents that evaporate over time from the paint film and contribute to coating VOCs. This study looked at the use of near-zero-VOC bio-renewable coalescing agents made from soy derivatives for the industrial direct-to-metal (DTM) coatings market and was conducted in three parts:
- Effectiveness on MFFT reduction of industrial latex polymers compared to petroleum-based coalescing agents.
- Effectiveness in starting-point paint formulation compared to petroleum counterparts.
- Optimization for DTM applications and comparison with commercial DTM paints.
Two soy coalescing solvents were compared to four petroleum-based coalescing solvents for industrial coatings in two different latex resins. They were tested for their ability to reduce the latex MFFT. The percent concentration necessary to lower the MFFT to 0 oC was selected and used with Latex 1 to formulate a white semi-gloss paint for general use to assess effectiveness (Study B). The soy coalescing agents were then used in optimized DTM paint formulations and compared to commercial water-based DTM paints (Study C).
Study A – MFFT Reduction
Two industrial latex resins were blended with four petroleum-based and two soy-based coalescing agents at multiple concentrations and measured for reductions in MFFT (Table 1).
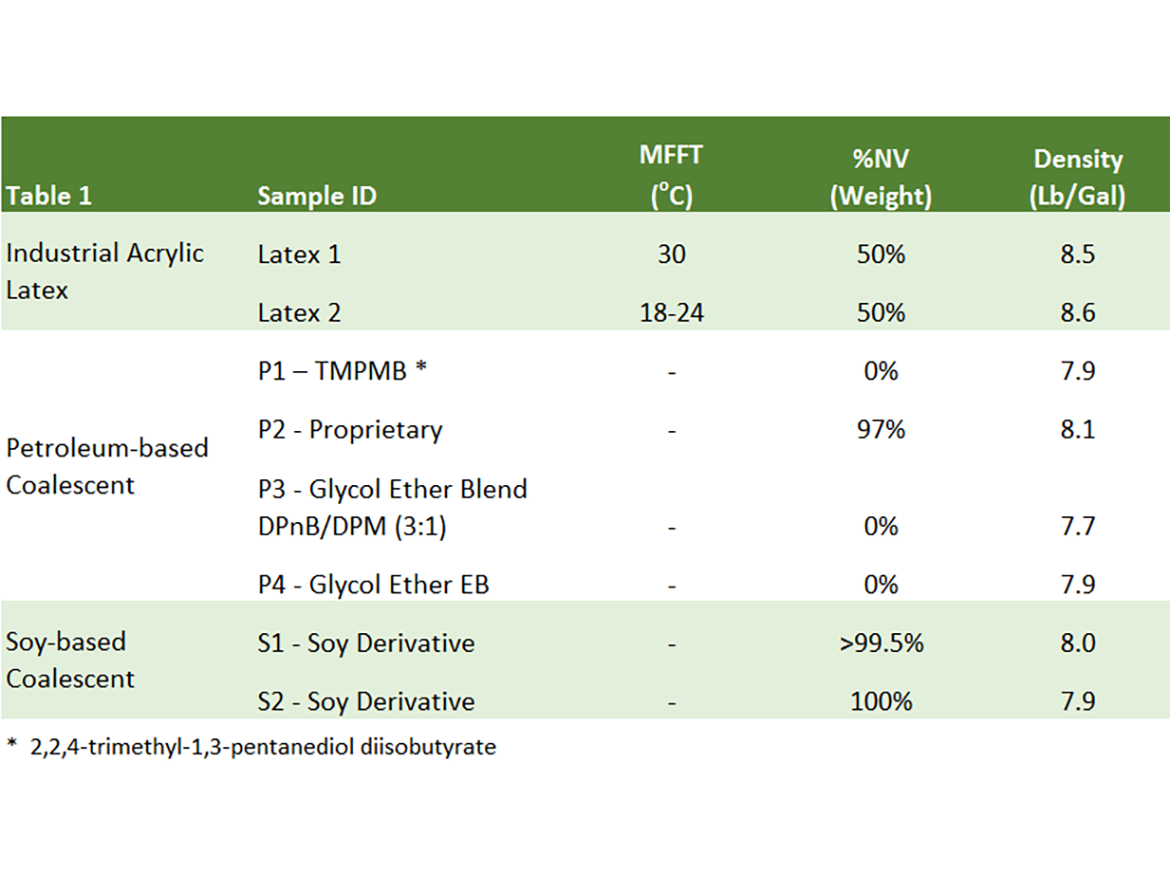
Based on the manufacturers' recommendations, the six coalescing solvents were blended with the latex resins at multiple levels and optimized to achieve an MFFT near 0 °C. The selection of petroleum-based coalescing solvent was based on the resin manufacturers' recommendations for compatibility. The two soy products were used in both latexes.
All levels were reported as % coalescent on total resin solids (TRS), and testing for MFFT was conducted per ASTM D2354. Figures 6 and 7 illustrate the results of this study.
The soy coalescing solvents were as effective as the petroleum counterparts at the same concentrations for MFFT reduction.
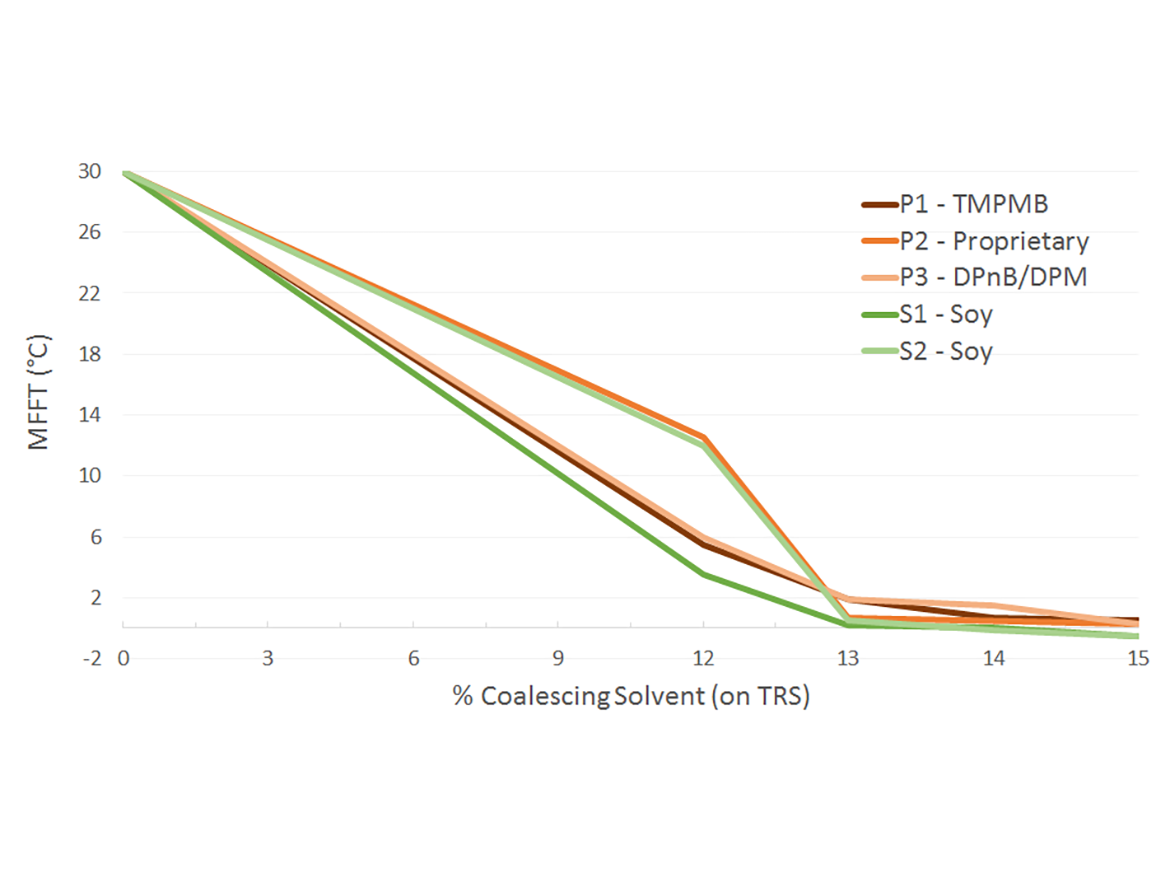
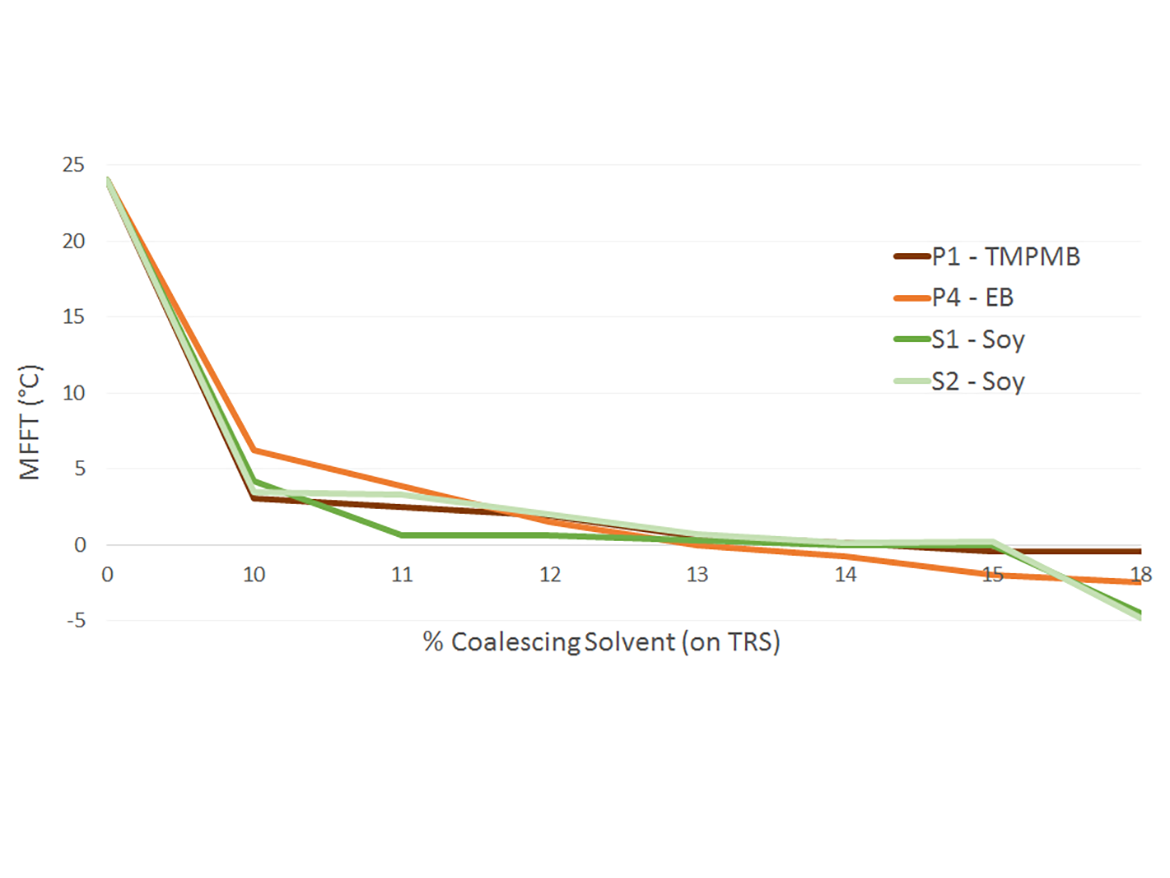
The soy-based coalescing agents effectively reduced the MFFT of the two latex resin systems at the same level of incorporation as the petroleum counterparts.
Study B – Starting-Point Formulation Assessment
The two soy coalescing solvents were compared to three petroleum-based coalescing solvents in a white semi-gloss latex paint using Industrial Latex 1 for DTM applications. They were tested for appearance, hardness, adhesion to steel, flexibility, impact resistance, corrosion, and UV resistance.
The five coalescing solvents were formulated into a standard white semi-gloss paint at 15% of TRS. The formulation contained titanium dioxide as the sole pigment at 16% pigment volume concentration (PVC). All paints were adjusted to pH 9.4-9.6 and 79-91 KU. Table 2 illustrates a representative formulation used for all paints.
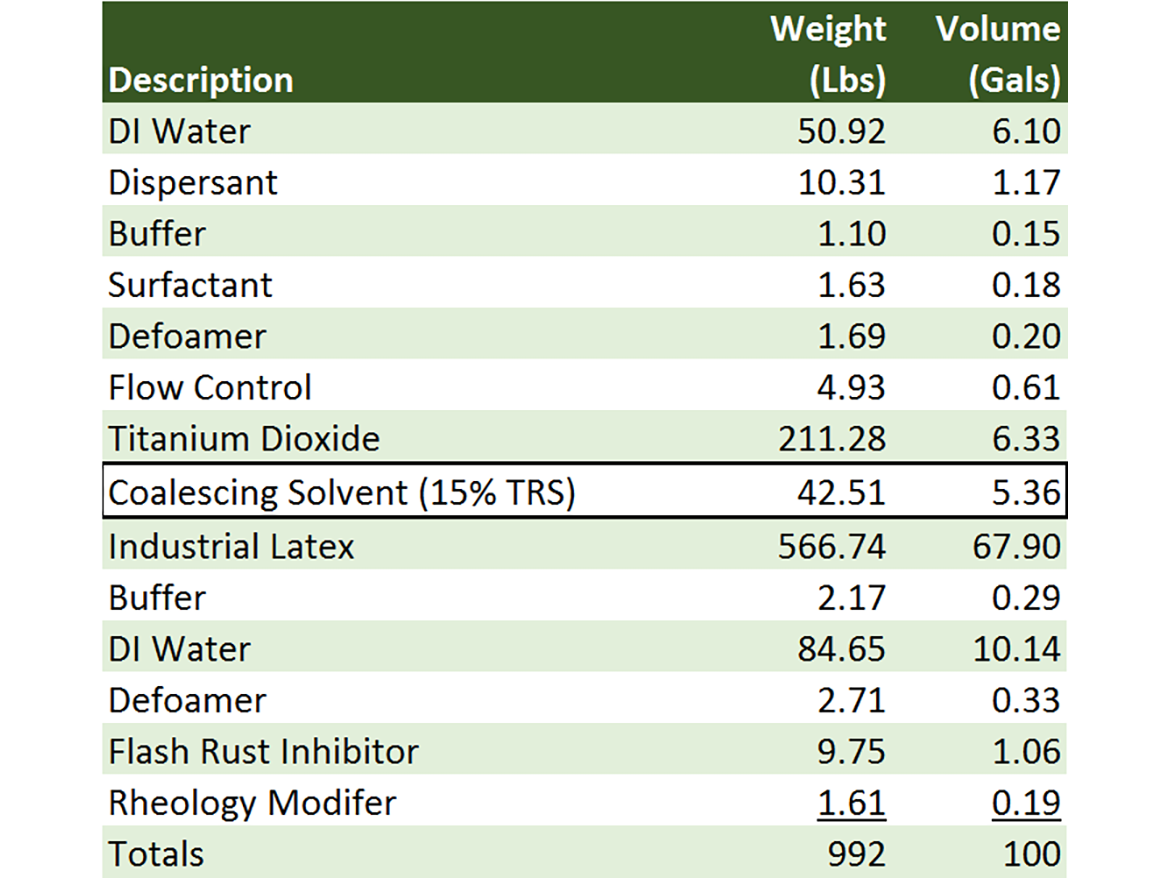
Appearance Properties
All the coalescing agents produced gloss levels in the semi-gloss range, although they varied somewhat. With P2, the proprietary coalescent was significantly higher than the rest. Opacity was suitable for all paints, with S2 soy product slightly lower than the others. All experienced some viscosity drop after heat-age exposure, but dried paint films showed a good appearance.
Physical Properties
All paints showed excellent flexibility, impact resistance, and good adhesion to cold-rolled steel (CRS). Samples varied in pencil hardness, with the DPnB/DPM blend producing the hardest films of 2B, and the proprietary petroleum and soy coalescents the softest with < 6B. These same three coalescing solvents were > 97% non-volatile, thus remaining in the ambient-dried paint films, likely contributing to the softness.
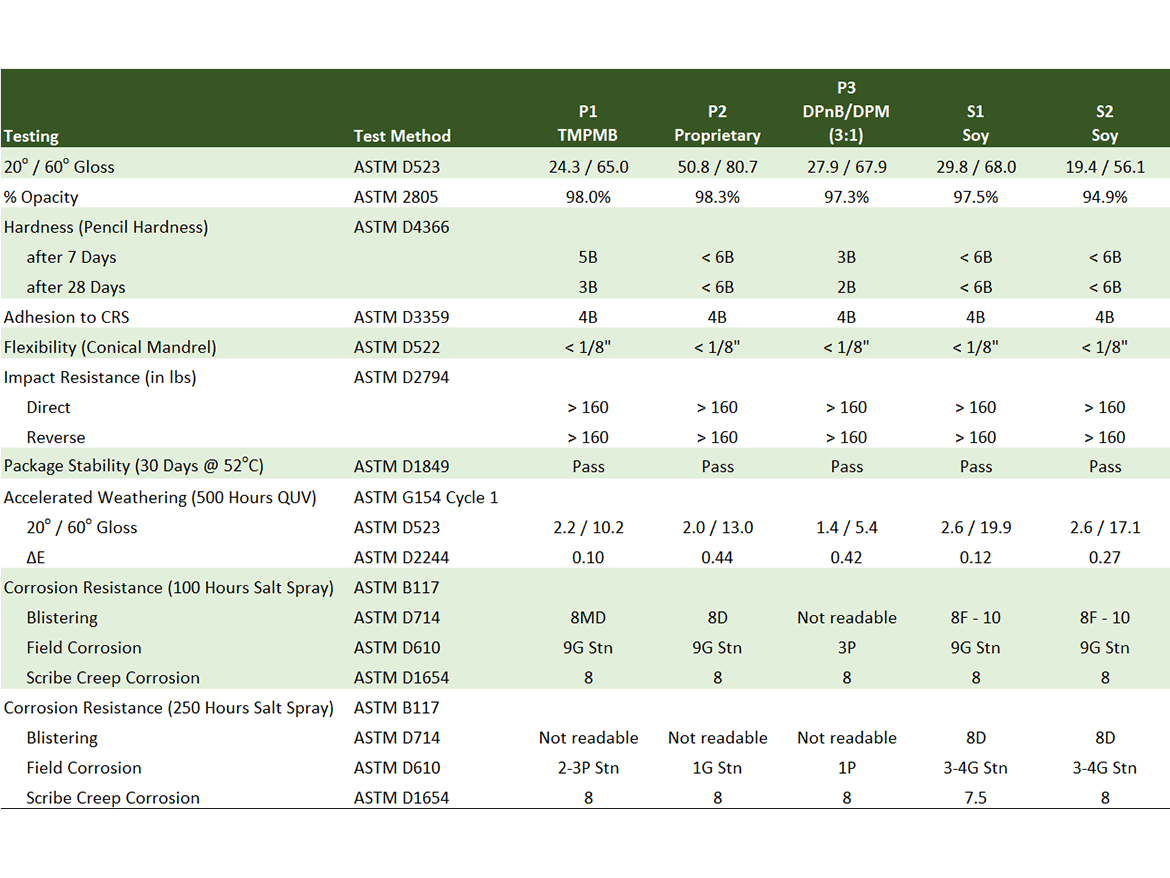
UV Resistance
All the samples showed gloss loss upon exposure to 500 hours of QUV weathering. The soy coalescing agents produced slightly better gloss retention, while the proprietary product lost the most gloss after exposure. All showed acceptable color change with their ∆E values less than 0.50.
Corrosion Resistance
Interestingly, the softer soy-containing paints improved corrosion resistance with less blistering after 100 and 250 hours of salt spray and improved field corrosion. Figures 8 and 9 illustrate photos of the corrosion panels after 100 and 250 hours of salt spray.
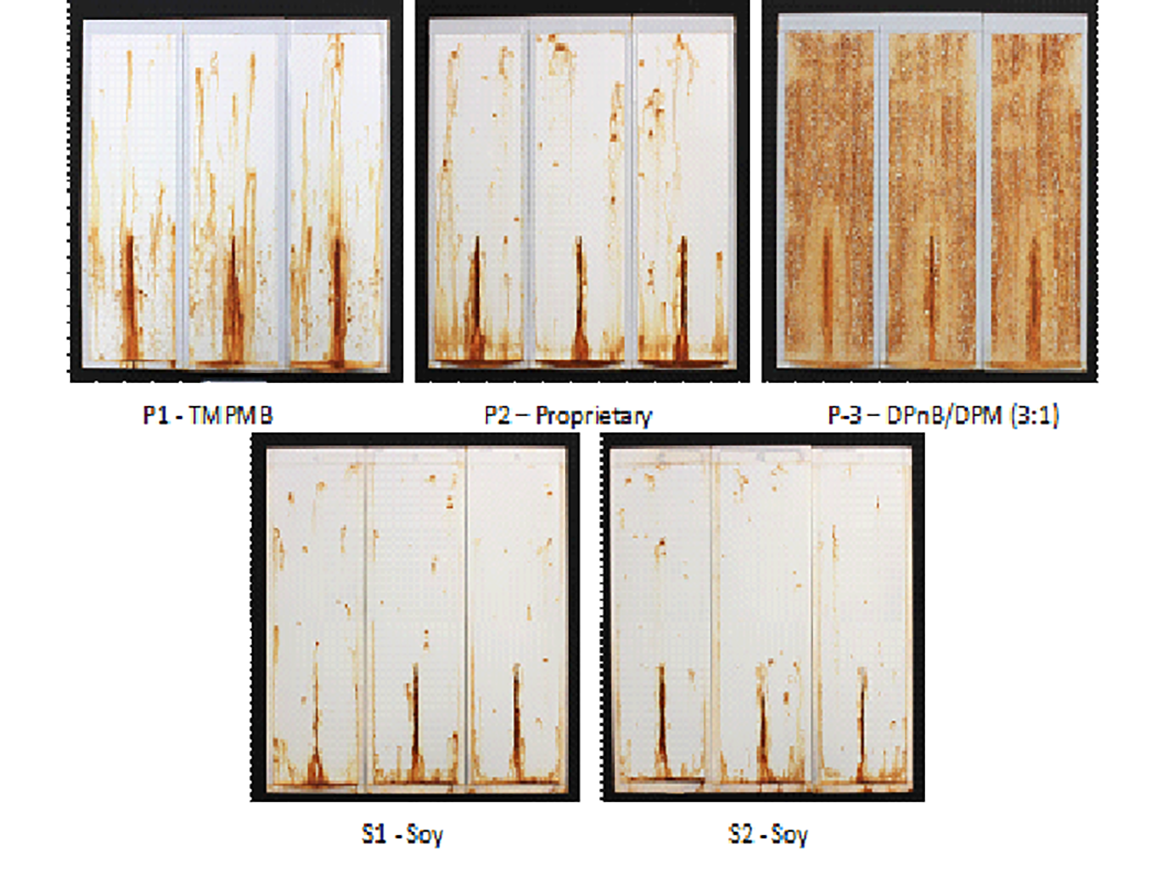
The test data was normalized and used to create total scores for comparisons. Figure 10 illustrates the balance of properties and highlights how the coalescing solvents are compared.
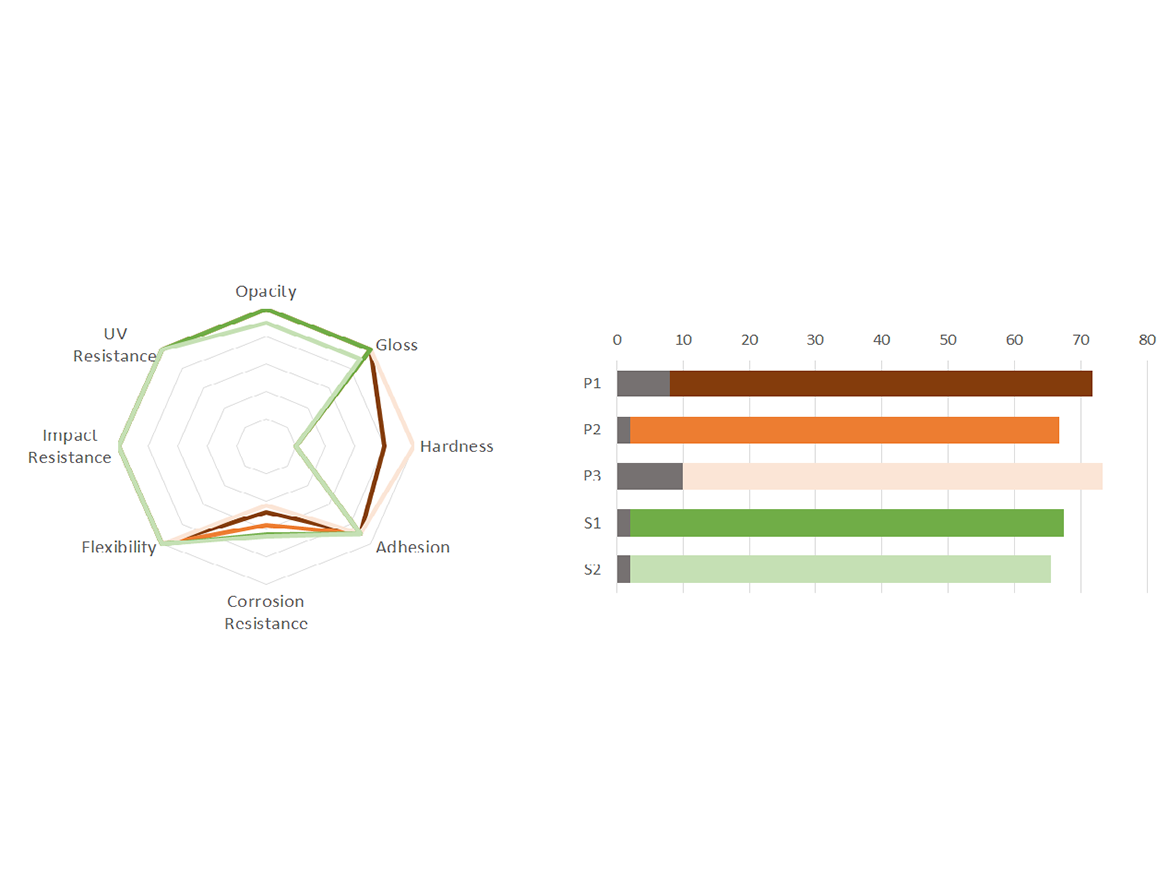
Overall, the soy coalescing solvents demonstrated viability in latex industrial coatings. They were formulated into optimized DTM paints and benchmarked against commercially available water-based DTM paints (Study C).
Study C – Optimized DTM Paint Formulations
The paint formulation in Study B was optimized using a higher-performing industrial acrylic latex (Latex 2) with the incorporation of a corrosion-inhibiting pigment. The two soy coalescing solvents were added, and the resulting paints were compared to two commercial benchmark DTM paints for appearance, hardness, adhesion to steel, flexibility, impact resistance, corrosion, and UV resistance. A total of four paints were tested.
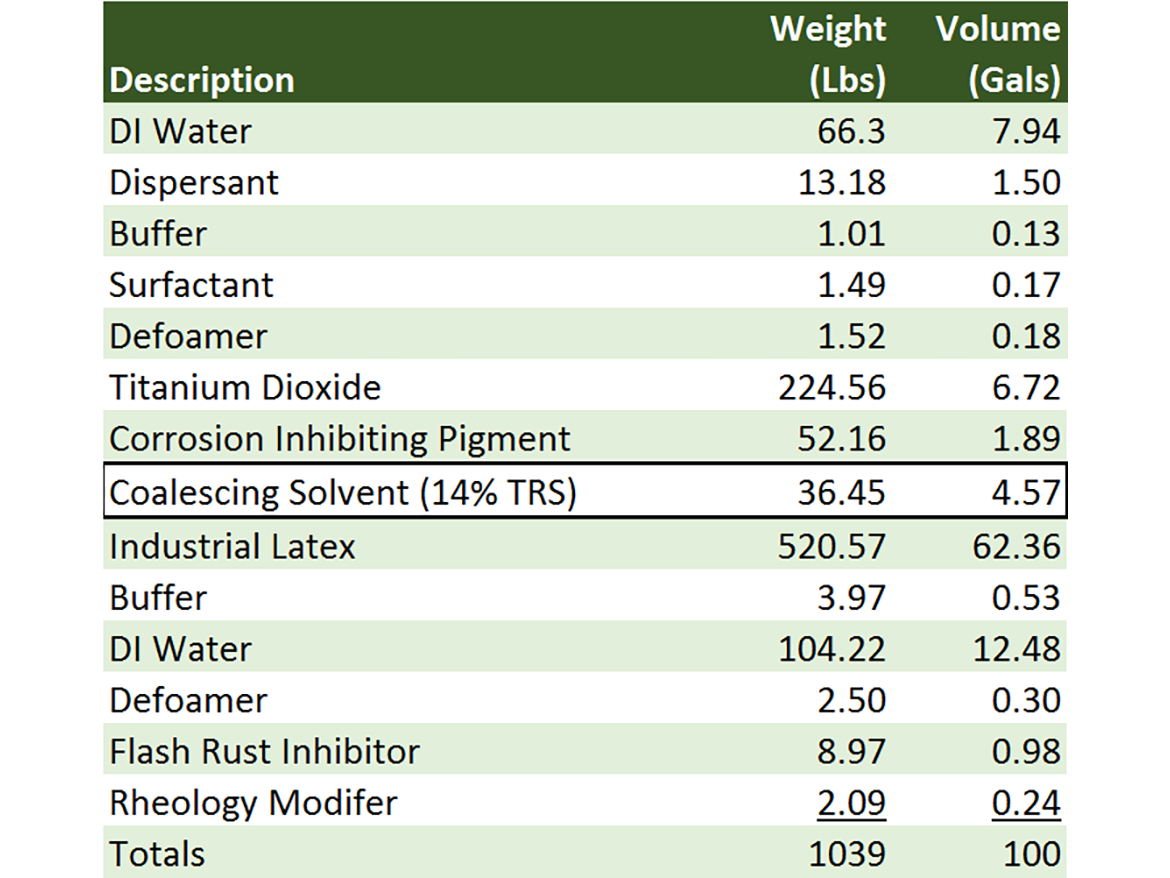
The two soy coalescing solvents were incorporated at 14% of total resin solids (TRS). The formulation contained 20% corrosion-inhibiting pigment on TRS and titanium dioxide for a total pigment volume concentration (PVC) of 40%. Paints were adjusted to pH 8-9 and viscosity to 100-105 KU. Table 4 illustrates the formulation used for the two soy-containing paints.
The paints were applied to sealed opacity charts at three mils wet and measured for appearance properties. The test panels were applied via wire round applicators in single and double coats, 2.5 and 5 mils dry-film thickness. Note that the commercial benchmark product data sheets specified two coats.
All charts and panels were allowed to age under ambient conditions for 7 days before testing. The dried films were tested for gloss, opacity, hardness, adhesion, block resistance, flexibility, impact resistance, UV, and corrosion resistance. Testing was conducted by ASTM standards. Table 5 illustrates the four paints' test methods and detailed test results.
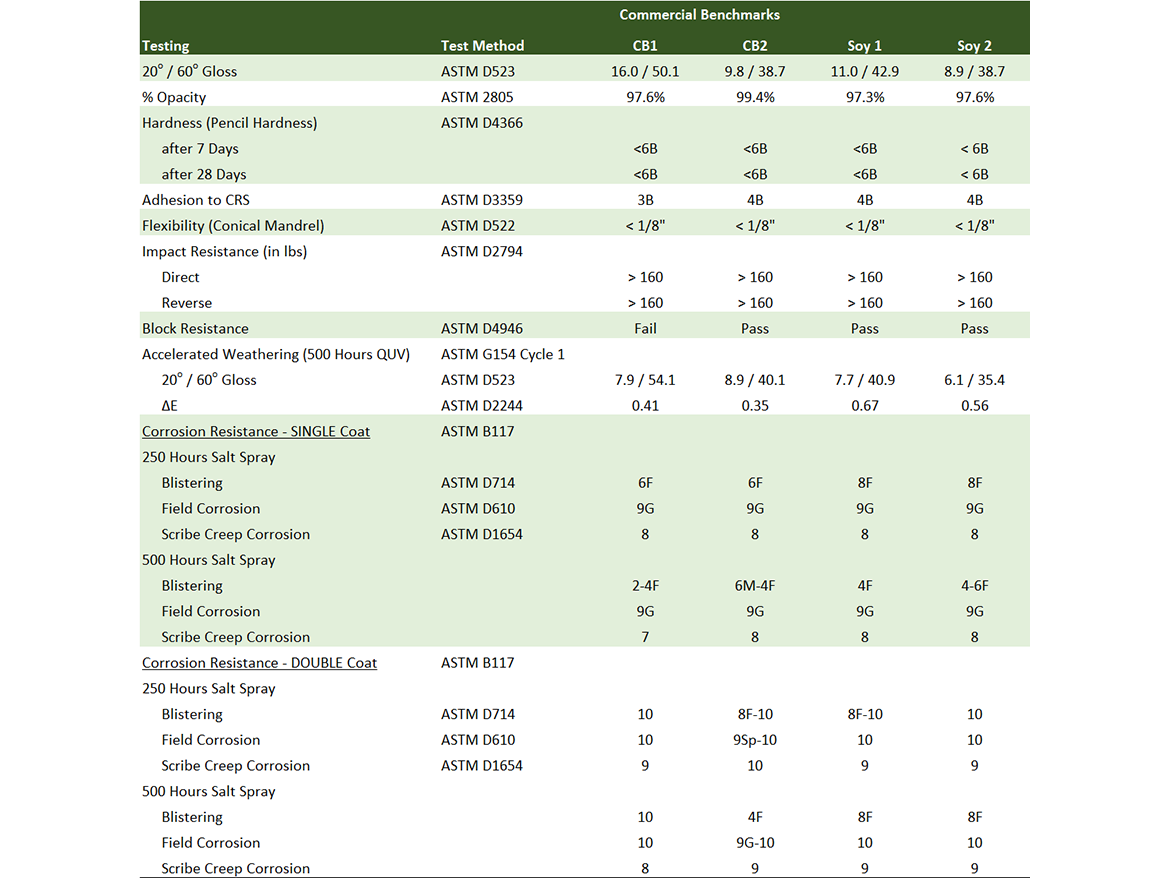
Appearance and Physical Properties
All paints showed good opacity and gloss in the semi-gloss range and were softer than 6B pencil hardness after 28 days of ambient age. Adhesion was fair to good over cold rolled steel (CRS), with excellent flexibility and impact resistance. The soy paints and Commercial Benchmark 2 passed block resistance, while Commercial Benchmark 1 failed with slight tackiness.
UV Resistance
The soy paints were comparable to the commercial benchmarks, with good gloss retention and little color change after 500 hours of QUV exposure.
Corrosion Resistance
The soy paints performed similarly to Commercial Benchmark 1 and superior to Commercial Benchmark 2 in single and double coats after 250 and 500 hours of salt spray exposure. Figures 11 and 12 illustrate photos of the salt-spray-exposed panels.
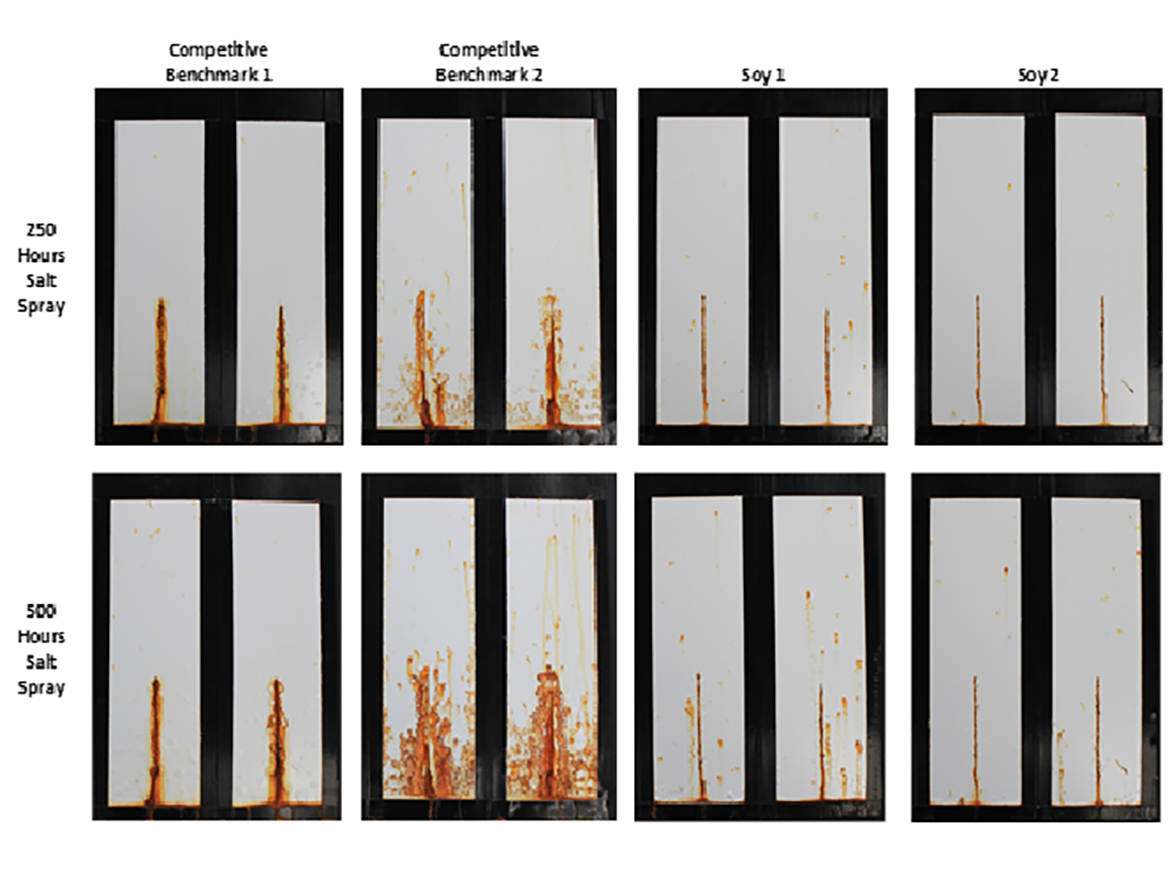
The test data was normalized and used to create total scores for comparisons. Figure 13 illustrates the balance of properties and highlights how the soy coalescent-containing paints performed to the two commercial benchmark DTM paints. Overall, the soy paints proved comparable and, in some cases, superior to the commercial DTM paints today.
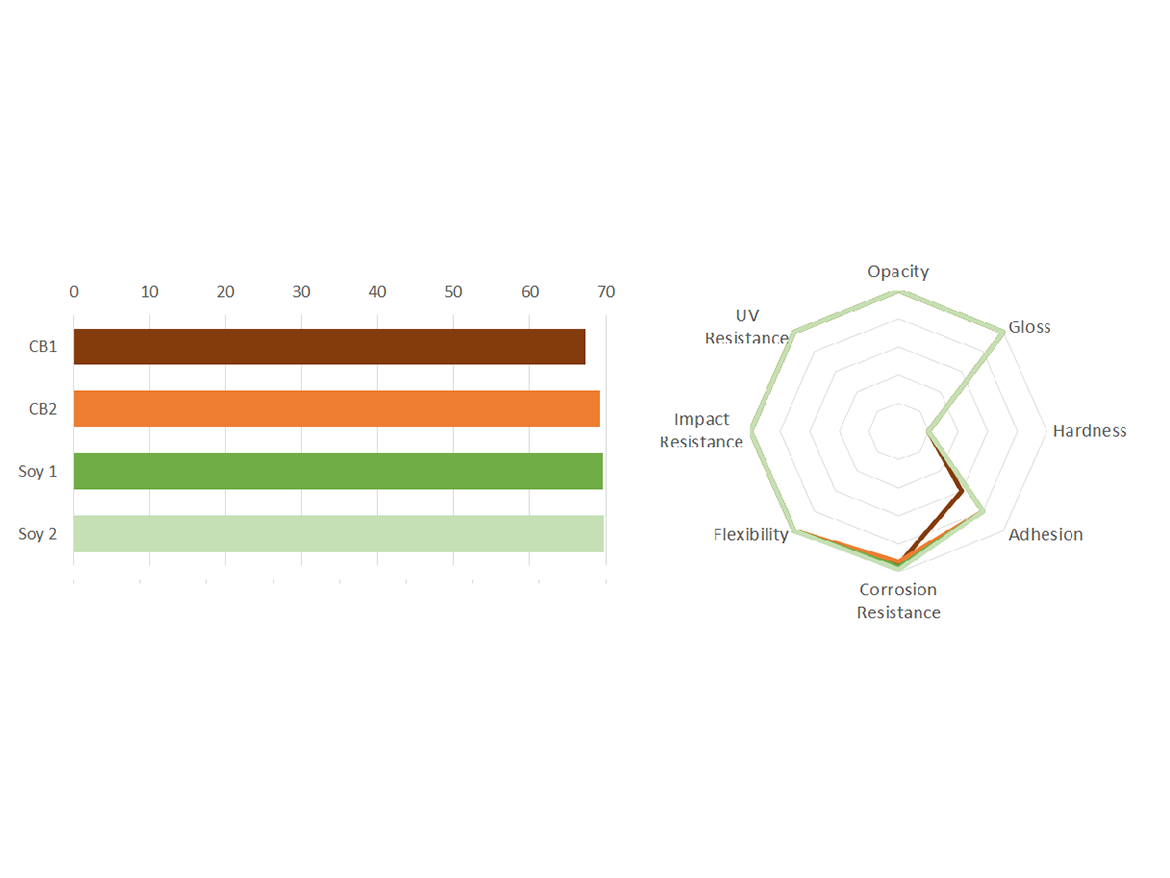
Summary
In conclusion, soybean oil, derived from sustainably grown soybeans in the United States, emerges as an economical and widely available renewable raw material. Its hydrophobic nature and double bonds allow novel chemistries that enhance film hardness and resistance, offering outstanding durability against water, polar solvents, and corrosion to replace petro-based materials in various coating applications.
Ongoing Work – Part 2 – Soy Alkyd Dispersions
Current work is underway to develop sustainable water-based DTM coatings using soy alkyd dispersions. Whereas latex DTM paints containing soy coalescing agents contain 7-10% bio-renewable content, these new paints will include 40-50% bio-renewable content on total paint solids.
Acknowledgments
The authors would like to acknowledge the assistance of our colleagues Brandie Bennett, Jane MacDonell, and Jessica Lake, and express gratitude for funding from the United Soybean Board (Projects 23-106-D-A-1-A and 24-106-D-A-1-A).
For more information, e-mail Kris Weigal at kweigal@omnitechintl.com; or Debora Hense at dhense@stonebridgelabs.us.
References
1 USDA Agricultural Projections to 2032. USDA Economic Research Service. 2023. https://www.ers.usda.gov/publications/pub-details/?pubid=105852
2 United Soybean Board Releases 2023 Sustainability Overview Report. US Soy. 2024. https://ussoy.org/united-soybean-board-releases-2023-sustainability-overview-report/
Looking for a reprint of this article?
From high-res PDFs to custom plaques, order your copy today!