Making High-Performance Green Coatings More Sustainable

The coatings industry continues to make significant strides in addressing the three pillars of sustainability. This includes maintaining and growing its economic contribution to society, fostering the well-being of our communities, and utilizing sustainable manufacturing practices and procurement measures that protect the environment and ensure resources will be available for future generations. Legislation to address customer demand for more sustainable coatings has resulted in a heavy focus on biorenewable ingredients, which provide greener feedstock options. However, recycled content has remained relatively unexplored for high-performance applications.
Resinate has developed technology to create recycled-content-based polyols that impart critical performance properties such as hardness, flexibility and chemical/stain resistance in waterborne systems. This enables formulators to make green coatings even more sustainable, by incorporating polyols with up to 75% recycled content for polyurethane dispersions and other high-performance coating applications. Key applications include flooring, furniture and cabinetry, plus other challenging ambient- and energy-cure industrial coating applications.
The Business Case for Recycled Content Use
Cradle to Cradle® is a design framework that goes beyond ‘cradle to grave’ for designing sustainable products with materials that are in abundance in a circular economy.1 Due to robust performance properties, one material with a substantial opportunity for Cradle to Cradle use is polyethylene terephthalate (PET) plastic. Plastic use has increased 20 times over the past half century, and is expected to double over the next 20 years.2 Yet millions of tons of valuable plastic molecules are deposited in landfills every year, ending the material lifecycle and filling landfills at an alarming rate. Those materials have significant energy and environmental footprint paid to that point, considering the resources used to mine, transport and process them. Through novel technology, Resinate has developed the capability to harvest still-valuable molecules from those intended waste streams, to create affordable, high-performance polyols for polyurethane dispersions (PUDs) for coatings.
More Than Recycling
It is important to distinguish the difference in Resinate’s view of recycling methods: downcycling, which degrades material performance and longevity; and upcycling, which builds performance and extends the material’s lifecycle. For example, when a PET bottle is reclaimed, it goes through many processing steps to become a flake or pellet material. In the case of a downcycling method, that flake or pellet material is then melted down and remolded into new plastic consumer goods. However, the melting process results in a loss of performance properties that existed in the virgin material - things like toughness, flexibility and chemical resistance. To correct that degradation of material, virgin material has to be blended into the recycled content. Each time the material is recycled thereafter, more of those performance properties are lost, meaning even more virgin material has to be added. This cycle can only be repeated four or five times, on average, before performance properties of the original material begin to decline. Although commonly referred to as recycling, this process is actually downcycling, as it results in the degradation of performance, value and ultimate longevity of the material.
The upcycling method, on the other hand, involves improving both the quality and longevity of a reclaimed material. Using proprietary technology, Resinate can upcycle PET to create high-performance polyols, incorporating biorenewable intermediates as well, to customize performance for specific applications. That is the work described in this article.
Science and Innovation
Resinate has developed proprietary digestion/functionalization process technology, which allows the inherent properties of recycled PET, poly(bisphenol A carbonate) (PBAC) and other recycled raw material streams to be harvested and reassembled into polyols made with up to 100% recycled and renewable content (Figure 1). This patented technology includes a hierarchy of components in molecular design, which are selected for integration with oligomeric intermediates. This hierarchy refers to methods and direction for raw material selection. The first choice is always post-industrial and post-consumer recycled material streams, with a second choice of biorenewable components. However, the process is robust enough to incorporate appropriate intermediates from petroleum sources as a final choice, if necessary, to achieve customer performance and cost requirements.
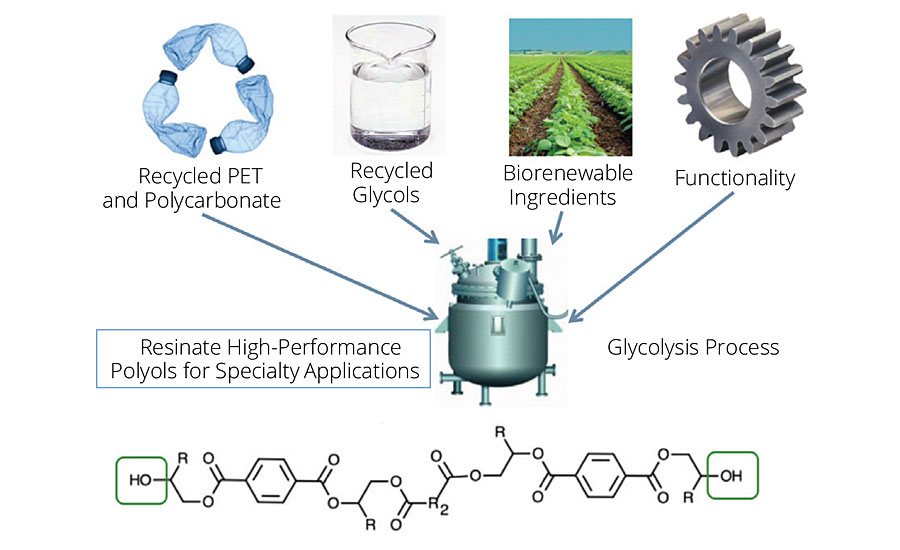
FIGURE 1 » The inherent properties of recycled PET, PBAC and other raw material streams to be harvested and reassembled into polyols made with up to 100% recycled and renewable content.
Robust Feedstock Capabilities
Resinate’s patented Recycolysis™ process allows the digestion of multiple PET waste streams. Each feedstock is selected to meet the specific needs of respective applications, such as recycled water bottle plastic for high-performance coatings. Alternative recycled PET feedstocks, such as carpet, automotive components and medical packaging, can also be used for no-show applications, such as urethane foams. Regardless of feedstock source, the Recycolysis process allows Resinate to produce polyols with similar, or in some cases, identical performance to those made from recycled water bottles.
Using Upcycled-Content Polyols to Manufacture PUDs for High-Performance Coatings
The coatings industry has various definitions of ‘green’ coatings. This encompasses a variety of criteria including environmental impact, such as smaller carbon footprint, low VOC, high recycled or renewable content, and ‘safer’ products. Waterborne resins have become one of the fastest growing technologies in this green space. Our company combines all of these key, green coatings criteria into our high-performance polyols to enable a new class of highly sustainable water-based polyurethane dispersions. As a side note, recent work3 comparing a variety of linear aliphatic or cycloaliphatic polyols (14) along with aromatic acid/aliphatic diol polyols (12) indicated that the rate of hydrolysis was the slowest for the phthalic and terephthalic-based polyols. This certainly helps the overall profile for terephthalate-based polyols along with the performance properties mentioned, when making comparisons for PUD design.
We further define polyol green content as the summation of the recycled + biorenewable content. We developed three polyester polyols based on rPET and other recycled/biorenewable content, with up to 84% total green content. These polyols can be used alone or as blends to achieve the desired balance of properties, including excellent stain resistance, hardness and flexibility (Table 1).
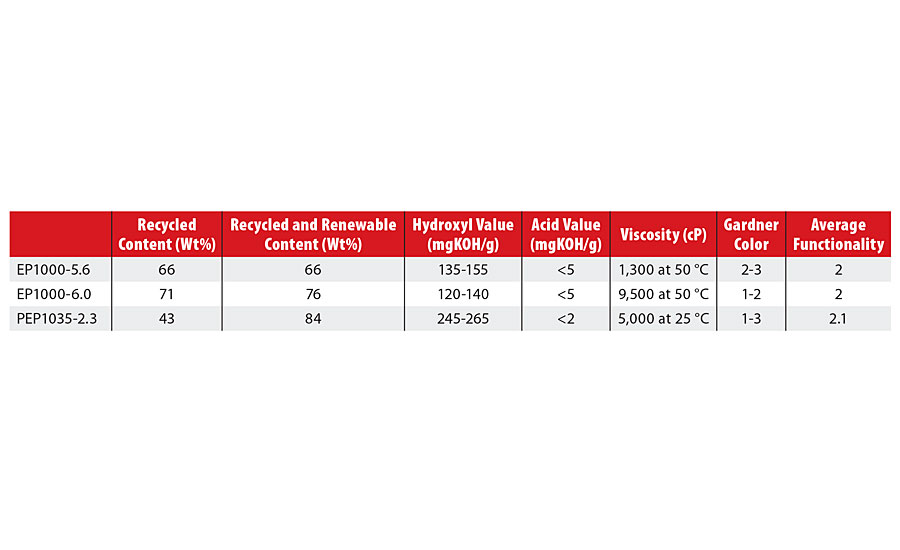
TABLE 1 » Polyester polyols based on rPET and other recycled/biorenewable content that can be used alone or as blends to achieve the desired balance of properties.
General Procedure for Making Polyurethane Dispersions
The information in Table 2 describes a stepwise overview of the PUD process defined in our labs, working with the EP and PEP polyol series. The process is quite similar to many published methods using NMP as a process solvent. The typical amount of NMP used for these PUDs was 4% on polyol solids, to achieve a workable viscosity of the prepolymer and enable small particle formation during inversion. This process does not transfer the prepolymer into water, but instead inverts the prepolymer in the same reactor, minimizing the total loss of solids during transfer. A high-shear Cowles-type mixing blade was used for the entire process. The polyols that were used in this recent work are listed in Table 1, along with their respective properties. All materials shown were derived from recycle content and are highly sustainable coatings resins.
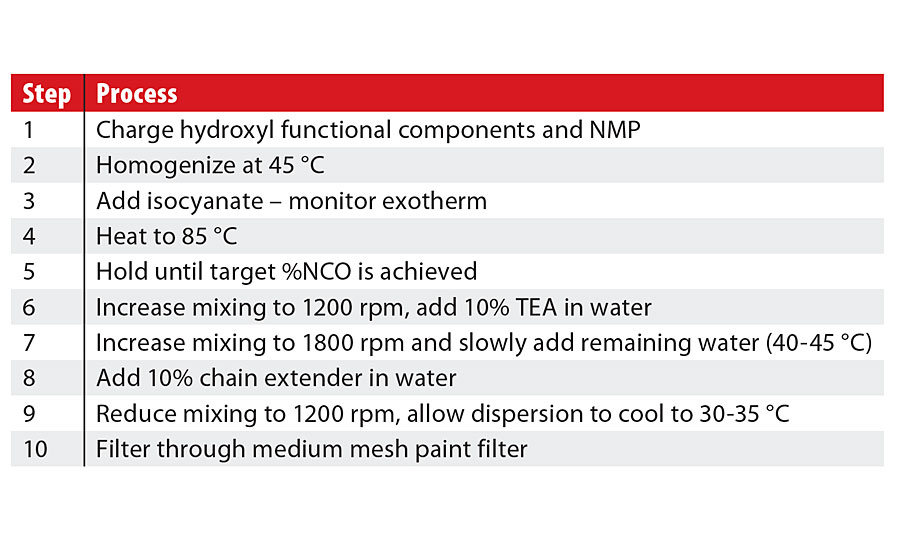
TABLE 2 » PUD manufacturing process.
Once the PUDs had full chain extension completed, were cooled to 30 °C and filtered, samples were then stored in a 50 °C oven for accelerated storage stability data. We performed film property testing of 7-day ambient-dry 1-mil dry films over aluminum panels, as illustrated in Table 3. We also included some blended PUDs that were made from the fully formed dispersions post-blended at the ratios indicated. Since the EP1000-5.6 was the softest of the group, we blended it with the hardest of the group, the PEP1035-2.3. There was also a commercial control PUD included, which is available currently, in the same class of materials since it also contains NMP. According to the safety data sheet, this commercial control has a higher level of NMP used than any of the Resinate materials. The EP1000-6.0 blended with the PEP1035-2.3 produced a very nice blend, having the same flexibility, chemical resistance and impact resistance as the well-known commercial control, however, it also had much harder Konig and pencil measurements.

TABLE 3 » Ambient-dry film properties of PUDs prepared and their blends.
As potential components for OEM wood applications, especially focusing on the areas of importance to the Kitchen Cabinet Manufacturers Association, the household chemical stain data is shown graphically in Figure 2. Resistance to ethanol is a common challenge to waterborne systems that are not crosslinked. Except for the softest EP polyol (EP1000-5.6), all results were either a 4 or a 5 rating across the entire test array, which indicates favorable performance for finished wood applications for kitchen use. Depending on the level of residual NMP, penetration of the ethanol can vary, indicating that total removal of the NMP from the process may ultimately improve resistance to this household chemical.
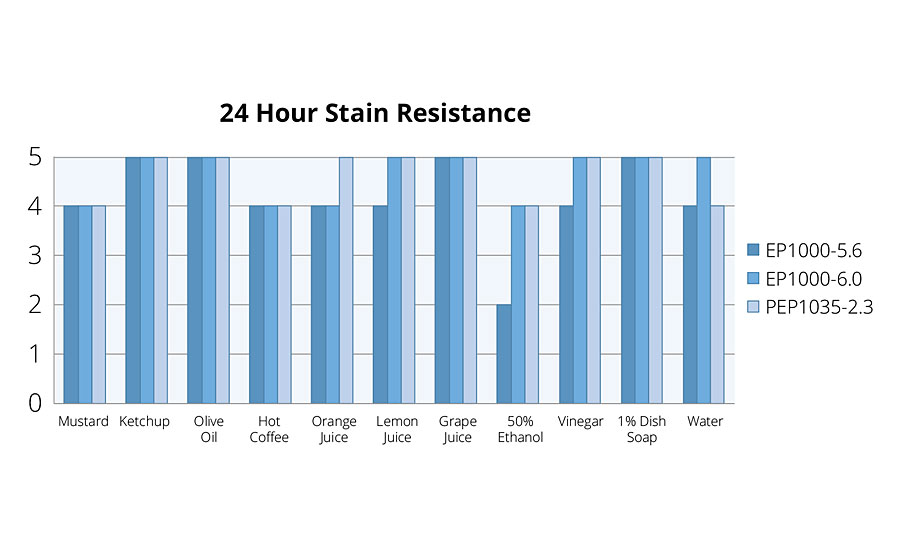
FIGURE 2 » Household stain data for ambient-dry PUDs, maximum rating 5.
Based on the proprietary chemistry of the new Resinate polyols for PUDs, there is an option to further process thin films using UV-cure technology. For this purpose, photoinitiator is added to the dispersion, the film is applied to the substrate, flashed, and finally cured under UV lamps for a short exposure. There are many wood applications that benefit from this technology, including wood flooring, where fast cure allows a faster turnaround for restoring foot traffic. Some of the OEM wood manufacturers have also gone to this cure technology, mostly due to speed and throughput. Obviously if parts do not have to air-dry or bake, they can be processed to their final destination much quicker. Table 4 shows the comparative properties of two of the PUDs made from EP polyols. In this case, the softer one (EP1000-5.6) has more residual flexibility as it starts out softer, however, after UV cure has obtained a much higher Konig hardness as well as having great chemical resistance. The EP1000-6.0 becomes a bit more brittle, passing 1” mandrel bend flexibility, but has only lost 1% of its mass after 200 MEK double rubs.
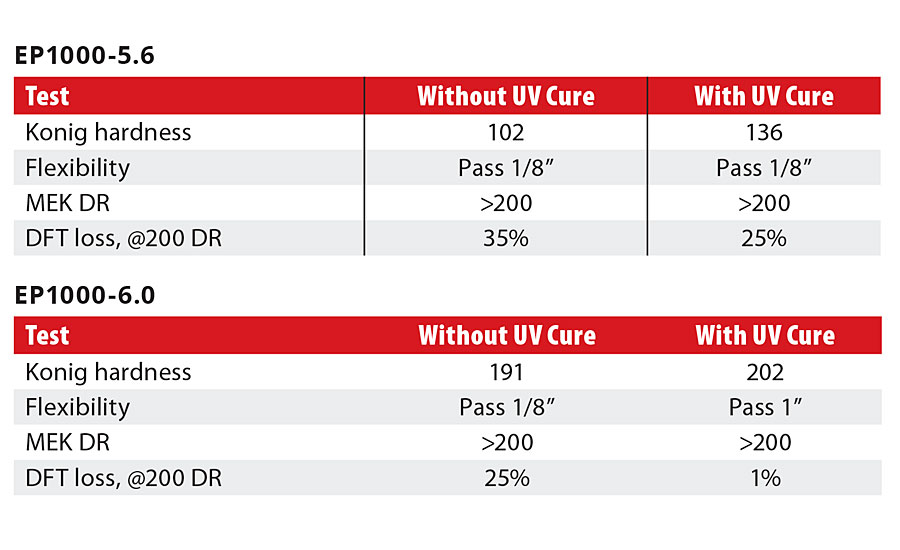
TABLE 4 » UV-cure properties for selected EP polyols.
Conclusion
Resinate Materials Group, Inc. has developed technology that drives higher sustainability options for waterborne, ambient and UV-curable polyurethane dispersion-based coatings. This allows the formulator to achieve very high performance such as hardness, chemical resistance and flexibility, while simultaneously taking advantage of alternative feedstocks from recycle streams. The customizable performance options and increased sustainability provide a very optimistic path for the future of high-performance coatings.
Acknowledgements
The authors wish to acknowledge the entire Resinate Materials Group technical team, especially David Paul, Josh Cupp, Austin Ardanowski, Simone Marshall, Adam Emerson and Rick Tabor. Assistance with preparation of this paper, and the materials and testing required to develop the technology, were due to their efforts.
References
1 McDonough, W.; Braungart, M. Cradle to Cradle: Remaking the Way We Make Things. Farrar, Straus and Giroux. 2002.
2 World Economic Forum. The New Plastics Economy; Rethinking the future of plastics. January, 2016.
3 Ramirez-Huerta, M.; Zvonkina, I.J.; Soucek, M.D. J. Coat Technol. Res., 13 2016, 781-793.
Looking for a reprint of this article?
From high-res PDFs to custom plaques, order your copy today!