Daylight Fluorescent Pigments
A Technology that Delivers a Luminously Enhanced Universe of Color to Products and Applications

Objects and surfaces compounded or treated with certain dyes and then captured within specially designed polymer systems have extraordinary luminous properties. Unlike conventional colorants, these materials are able to absorb shorter wavelengths of sunlight and then re-emit that light at longer wavelengths, producing a visual experience of color intensity above and beyond anything we expect to see from light reflected from a "passive" colored surface. This phenomenon is termed ‘daylight fluorescence’.
Daylight fluorescent pigments emit as much as four times the light reflected from surfaces colored with conventional pigments and invariably attract more attention. The intense visibility of fluorescent pigments makes them ideal in safety applications such as traffic cones, barriers, safety vests, helmets, and signage in roadwork, construction, and marine applications. In addition to the intense visual appearance of daylight fluorescent objects and coatings, there's an almost magical impression experienced as a result of the unexpected "glow" given that adds a special attraction when used as an attention-capturing element in the coloring and design of sporting gear, textiles and clothing, children's toys, product packaging, and even for adding a special extra “pop” to conventional paint colors. The applications of daylight fluorescent colorants are so diverse that an entire industry has developed to prepare and tailor these materials to be compatible with and to maximize their luminous performance across a range of product categories.
Consistent Performance Under Diverse Manufacturing Conditions
Creating formulations capable of liberating the brilliant daylight fluorescent properties from dyes with inherent fluorescent capacity such as Rhodamine B (shown in Figure 1 in its powdered form), in a daylight fluorescent pigment application, and as a representation of its molecular structure) is the result of decades of R&D. Daylight fluorescent colorants are tailored for incorporation in inks, plastics, paint, textile dyes, and pigments that are applied to all manner of printed and coated surfaces, as well as being incorporated in formed objects and films. Liquid "vehicles" come in a variety of compositions and properties, and the colorants must be designed both for compatibility and maximized performance in each type. A mismatch in physical compatibility with an ink or paint vehicle will result in failure to properly disperse the pigment. Having solved that problem, one is still faced with ensuring that the dispersion of the daylight fluorescent pigment remains stable, and maximizes its luminance when applied to a specific surface. Beyond that, there is the matter of extending the daylight fluorescent lifetime of the coating whether on a printed, painted, or dyed surface. Here, additional additives are incorporated to achieve that objective.
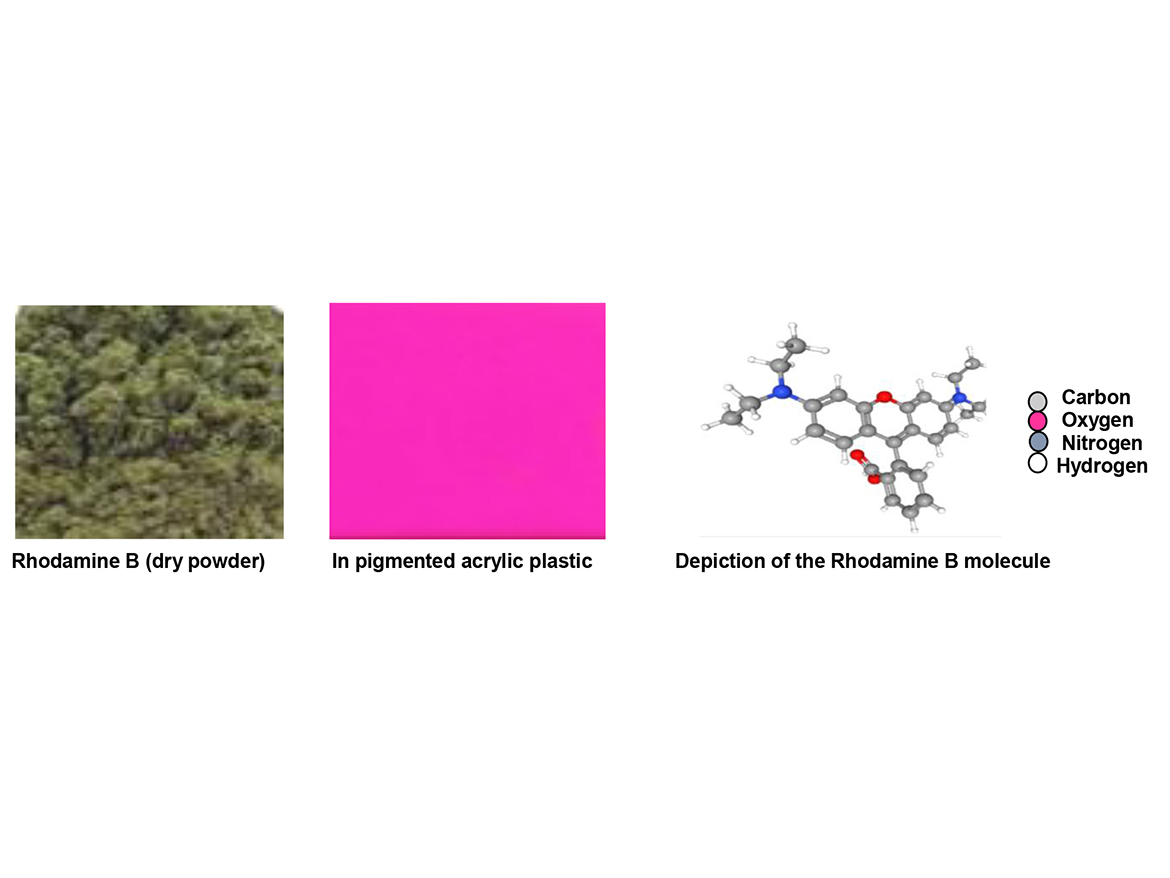
Incorporation of daylight fluorescent pigments in plastics presents an entirely different range of application problems. Pigments designed for different methods of manufacture such as injection molding, blow molding, and extrusion must be able to "stand up" to elevated temperatures as high as 500 °F for various lengths of time. They must also survive the extreme shearing forces applied to incorporate the pigment into the master batch prior to "let down" for subsequent stages of processing. Moreover, polymer-composed plastics have very different chemical entities with different physical and optical properties, and require different methods of pigmentation and pigmenting entities. There is a world of difference in processing to achieve a luminous color effect in the crystal clarity of an acrylic sheet, depicted above, and the diffuse opacity of different polyethylene films and objects. Clearly, this is a case of “one size does not fit all.” For that reason, daylight fluorescent colorants for plastics are tailored for physical and chemical compatibility with the plastic and its follow-on processing. Similar to daylight fluorescent applications in liquid media, plastic pigment formulations are compounded with a variety of special additives to maximize product color and luminance, and minimize loss of fluorescent color over time and under different conditions of exposure and use.
Much chemical technology must be implemented to transform not one, but a multiplicity of dyes and other components into the brilliant spectrum of fluorescent colors, examples of which are shown below. The dye molecules responsible for generating fluorescence can exist in several molecular forms, only one of which is fluorescent. The chemical structure of the polymer in which the dye is encapsulated must itself be capable of trapping and holding the dye in its fluorescing form, in a way that maximizes the daylight fluorescent effect for the long term. The polymer must also provide a protective "cage" that shields the dye molecule from the various physical and chemical stresses to which it is exposed in the initial manufacturing process. It must form a stable colorant product that maintains target properties during subsequent stages of product formulation and use. In many of these coating systems, the dye-pigment particle is suspended, dispersed, or emulsified in a liquid carrier designed for the specific method of application. In fact, there are even product applications in which the dye-pigment system is actually manufactured directly in the liquid vehicle, resulting in a "ready-to-use" daylight fluorescent emulsion system. These complex multi-component structures have a layered Russian-doll molecular design that must remain stable in storage and later formulation. That stability must not be disrupted by the addition of reactive components, often referred to as "driers," designed to convert the liquid system into durable, solid polymer films once applied to surfaces in the form of prints and coatings.
Properties of daylight fluorescent products targeted to specific applications require detailed experience with regard to formulation protocols and compounding conditions in order to protect and preserve their signature optical characteristics and performance properties. The enormous variation in application-specific and post-manufacture formulation is just one of the reasons why state-of-the-art technical expertise and long-term familiarity of the manufacturer with the novel properties of these materials is essential in their successful design and deployment.
Protecting and Extending Daylight Fluorescence Lifetimes
A briefly mentioned impediment to which daylight fluorescents are exposed post application are the degradative aspects of the environment in which they are employed, and that is responsible for their amazing brilliance. Over time, components of sunlight, especially highly energetic UV in conjunction with atmospheric oxygen, can cause degradation and loss of fluorescence by converting the dye molecules into non-fluorescent products. This results in a gradual reduction in luminance over time that is perceived as a loss of brightness or color fading (Figure 2). It also creates an appearance of lost color purity. Because the color and luminosity imparted by daylight fluorescent materials are so intense, this loss of brilliance and "dirtying" of hue is seen as a major impediment in extending the luminous lifetimes of these products. It's almost as if the magic is gone.
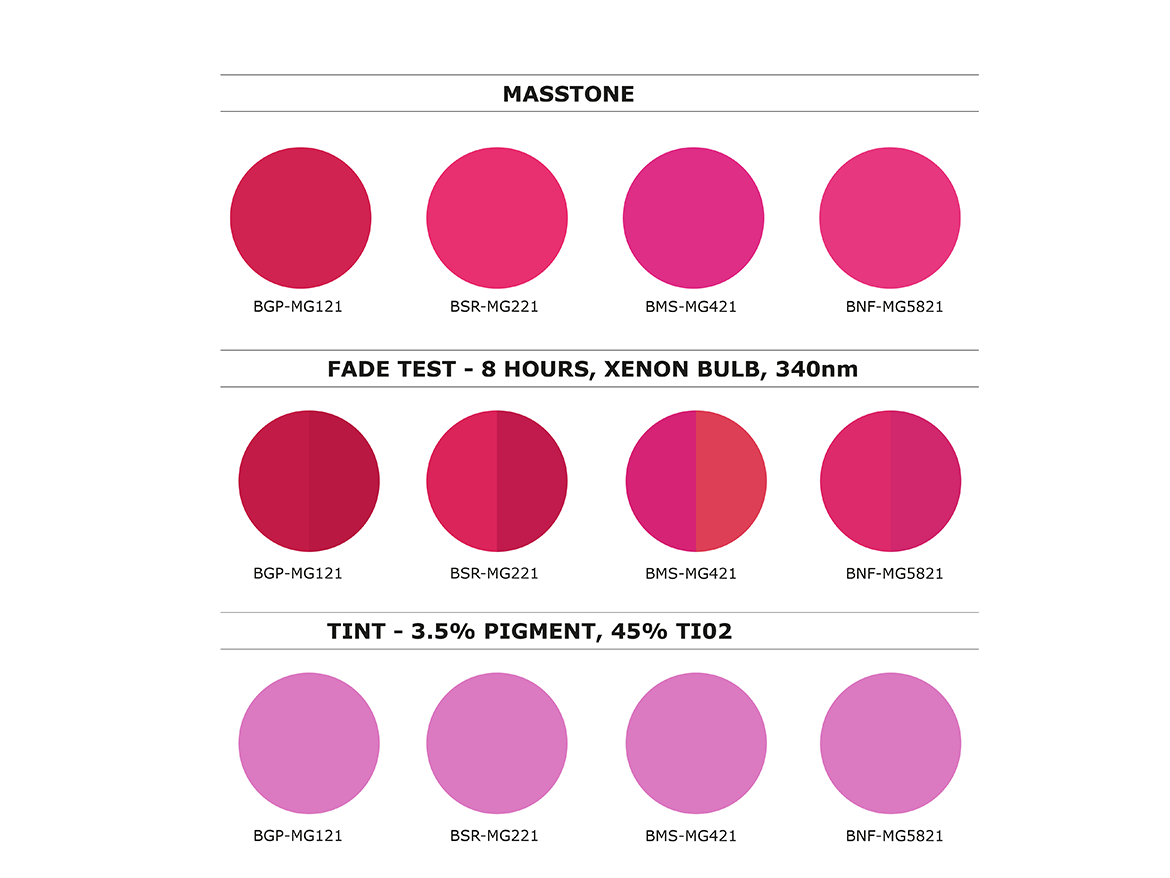
Accordingly, and depending on the application, daylight fluorescent colorants are formulated with a variety of additives specifically designed to scavenge reactive environmental agents and shield fluorescent surfaces from energetic light-activated decomposition. Further protection can be accomplished by applying a clear barrier coating containing UV-screening agents over the daylight fluorescent film, print, or coating. This further isolates the finished product from corrosive environmental contaminants and reduces exposure to the negative influence of UV. Pigment applications are also field tested under extended conditions of use to provide real-world guidance in the selection of incorporated protective agents best suited to extend the daylight fluorescent lifetime.
8-Hour Fading Profile for Four Representative Daylight Fluorescent Pigment Samples in Three Shades
Differential fading results from a combination of effects including relative dye concentrations, intrinsic susceptibility to loss of fluorescence, post-faded residual color, nature of the pigment matrix, and any protective additives or overlay coatings. Notice in Figure 3 that differential color change over time is highly dependent on dye formulation and pigment-polymer matrix. Technical guidance by the supplier becomes essential in gauging colorant selection and conditions of usage.
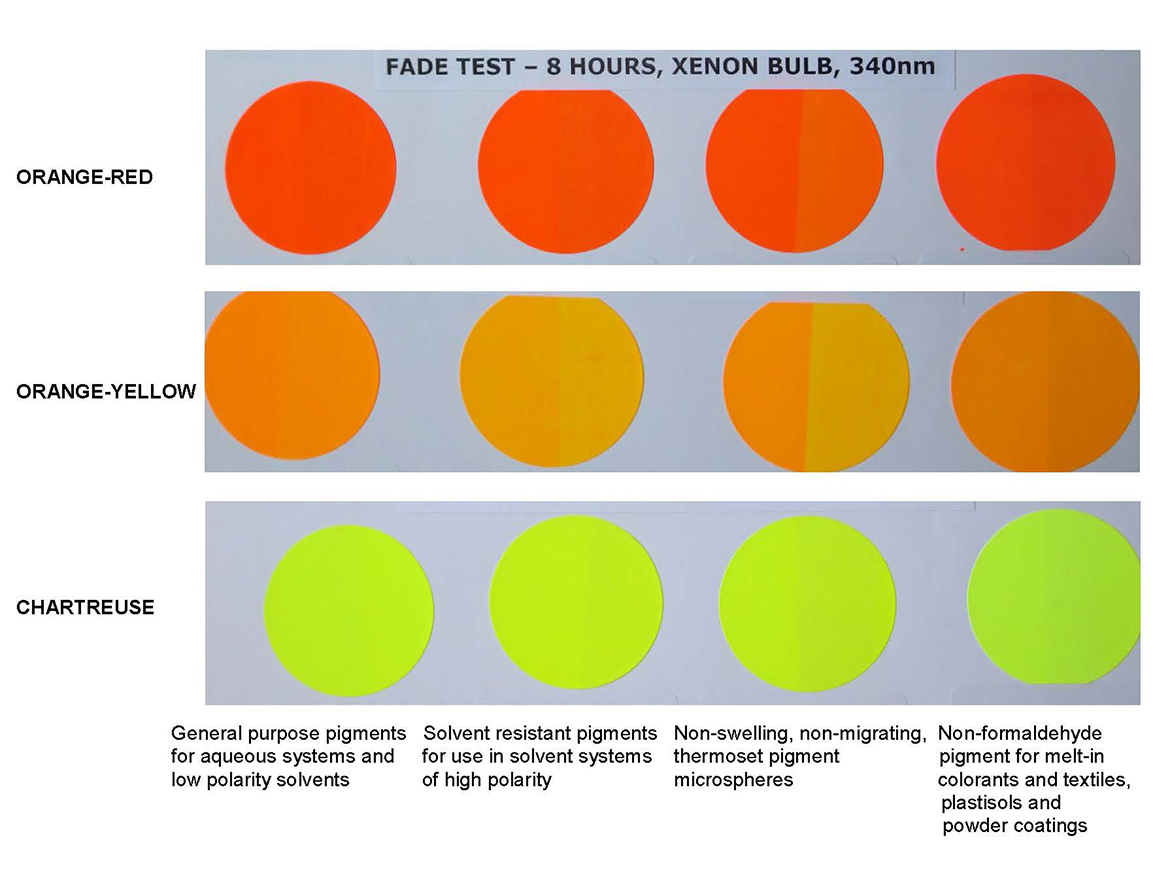
Daylight fluorescent products not only outshine the non-fluorescent competition, but are designed to compete in functional printing applications. In Figure 4, inked letterpress rollers demonstrate daylight fluorescent ink uniformity of flow and distribution, which not only delivers exceptionally strong printed impressions, but yields on-press image fidelity and performance that translates into longer trouble-free printing and easier post-run press cleanup. Printed color swatches alongside illustrate the resulting color purity, brilliance, and strength of the resulting print.
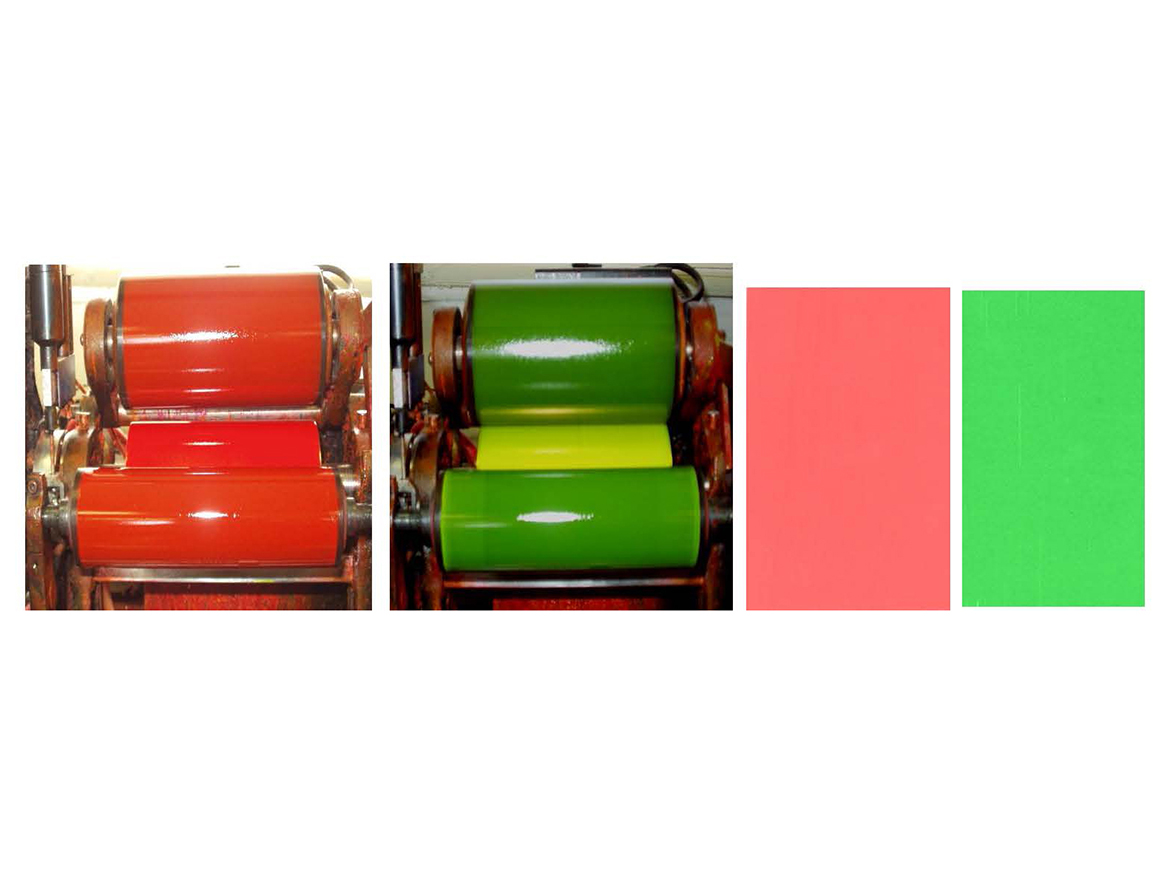
Quality Control is Key
Because of the combined brilliance, transparency, and cleanliness of daylight fluorescent colorants, they are more susceptible to color contamination than conventional pigments. As a result, batch-to-batch quality control of color consistency and processing properties is rigorously practiced in both manufacture and out-the-door formulation. This is not meant to imply that the products and their colors are so sensitive as to make them difficult to work with, but rather that the extra dimension of daylight fluorescence requires highly rigorous standards of color fidelity and performance properties in sequential production, and this sort of quality control is required practice (Figure 5).
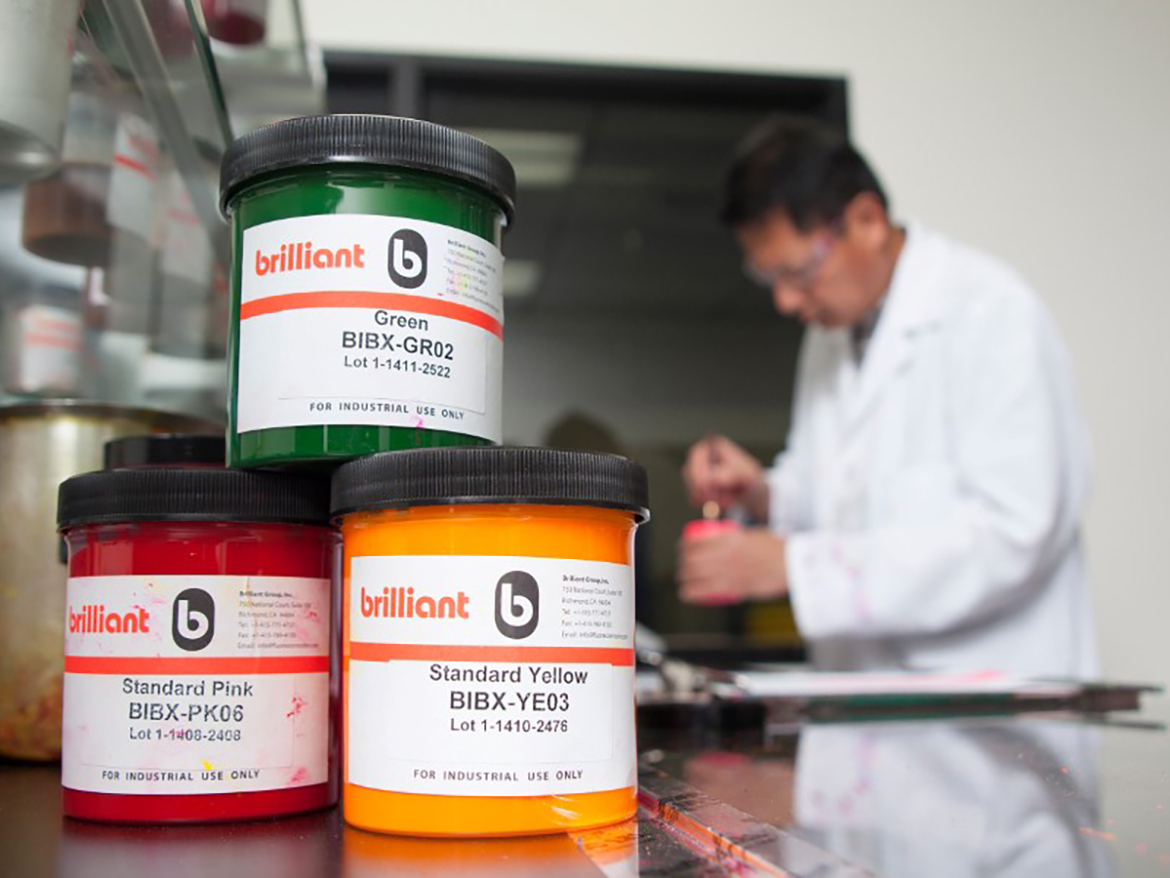
Light, Color and Fluorescence - the Science
What we call light is a very small slice of the spectrum of electromagnetic radiation reaching the earth from the sun and from outer space. Thankfully, most of the more energetic components of this radiation never make it into our environment, as it is deflected by the earth's magnetic field or absorbed by the ozone layer in the upper atmosphere. The area of the spectrum that does reach ground level and on which all life requires to survive, begins with the ultraviolet or UV region, which is invisible to us, but necessary in moderate doses to maintain health. Below the UV is the visible region of the spectrum with which this discussion is most concerned. At successively lower energies we have infrared (heat), microwaves, and radio waves, all of which serve important functions in both our natural and fabricated environment. And although we have a number of sensory organs to help us make our way in the world, (smell, taste, touch, hearing) it is the biological ability to detect and discriminate energy within the visible spectrum – wavelengths from about 450 to 700 nanometers (Figure 6) – that makes it possible to organize our environment and function in it.
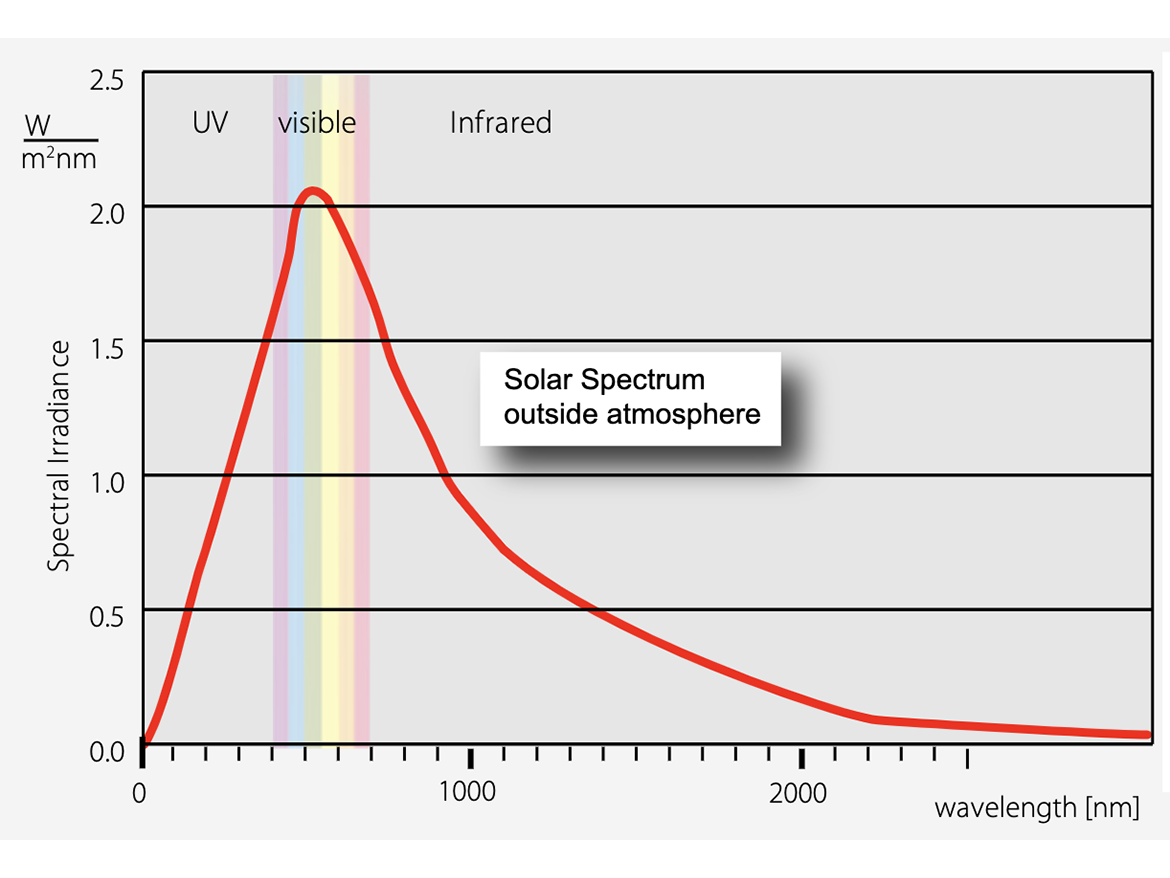
Source: https://www.greenrhinoenergy.com/solar/radiation/characteristics.php
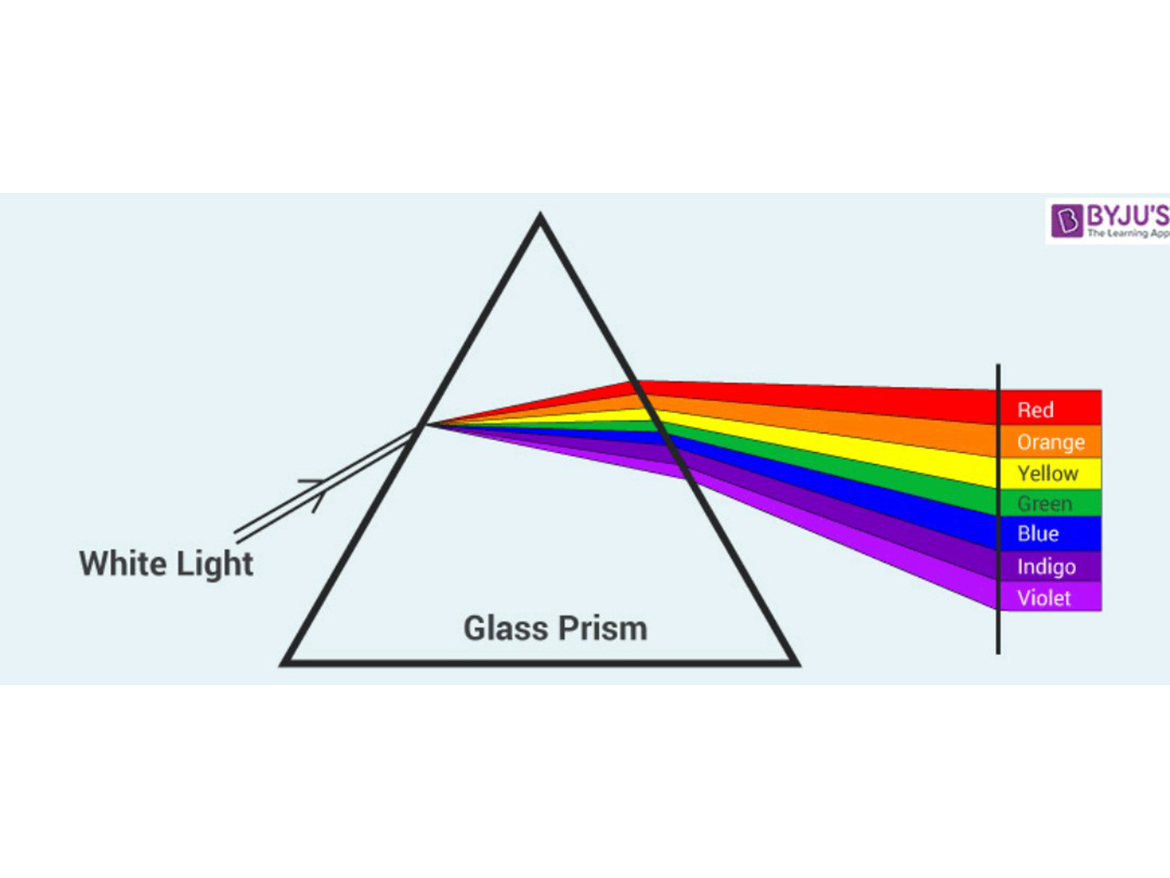
How does color emerge from daylight, which we experience as "white" light? Where does the color come from? The answer – it's there all the time! And this can be easily proved by allowing sunlight to pass through a glass prism. What comes out the far side is a rainbow of color (Figure 7). When we experience daylight or "white" light, all three of the eye's red, blue, and green photoreceptors are being stimulated.
Conventional Colors Are Produced by Subtraction
When daylight or "white" light from any source interacts with a pigmented surface or passes through a pigmented medium, the resulting visible color of the light, reflected or transmitted, is actually the residual components of that light that have not been absorbed. That means when you see a red flower or a green leaf, it is because, in the case of the red flower, more of the blue and green components of sunlight have been absorbed, leaving light primarily in the red region of the spectrum reflected to reach the viewer. In the case of the green leaf, more of the red region of the spectrum is absorbed, and the reflected or transmitted light is seen primarily as green (Figure 8). In both cases, the colors of the light that emerges are the wavelengths of light that have not been absorbed. With conventional pigments, the energy of the absorbed light is typically dissipated as invisible heat through enhanced molecular vibrations.
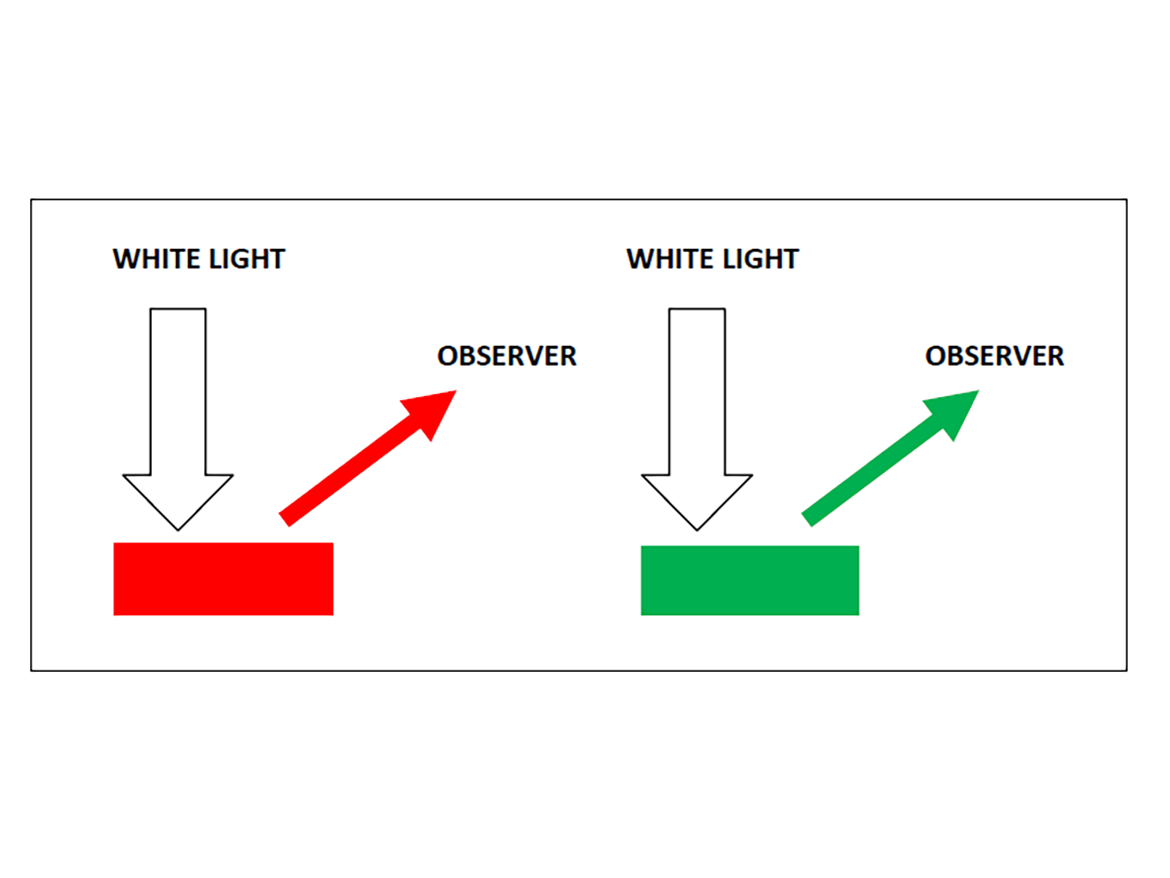
Source: Image constructed by Alan Schein.
The Phenomenon of Daylight Fluorescence
The two super-imposed curves in Figure 9 are the absorption (blue) and emission (red) spectra of a daylight fluorescent colorant. Like a conventional pigment, the daylight fluorescent colorant absorbs and reflects light, but unlike its conventional counterpart, some of the absorbed light energizes the contained fluorescent dye in a way that enables it to re-emit some of that absorbed radiant energy at a longer wavelength (color). The additional emitted light, a product of the fluorescent process, is what gives daylight fluorescent materials their extra luminous appearance.
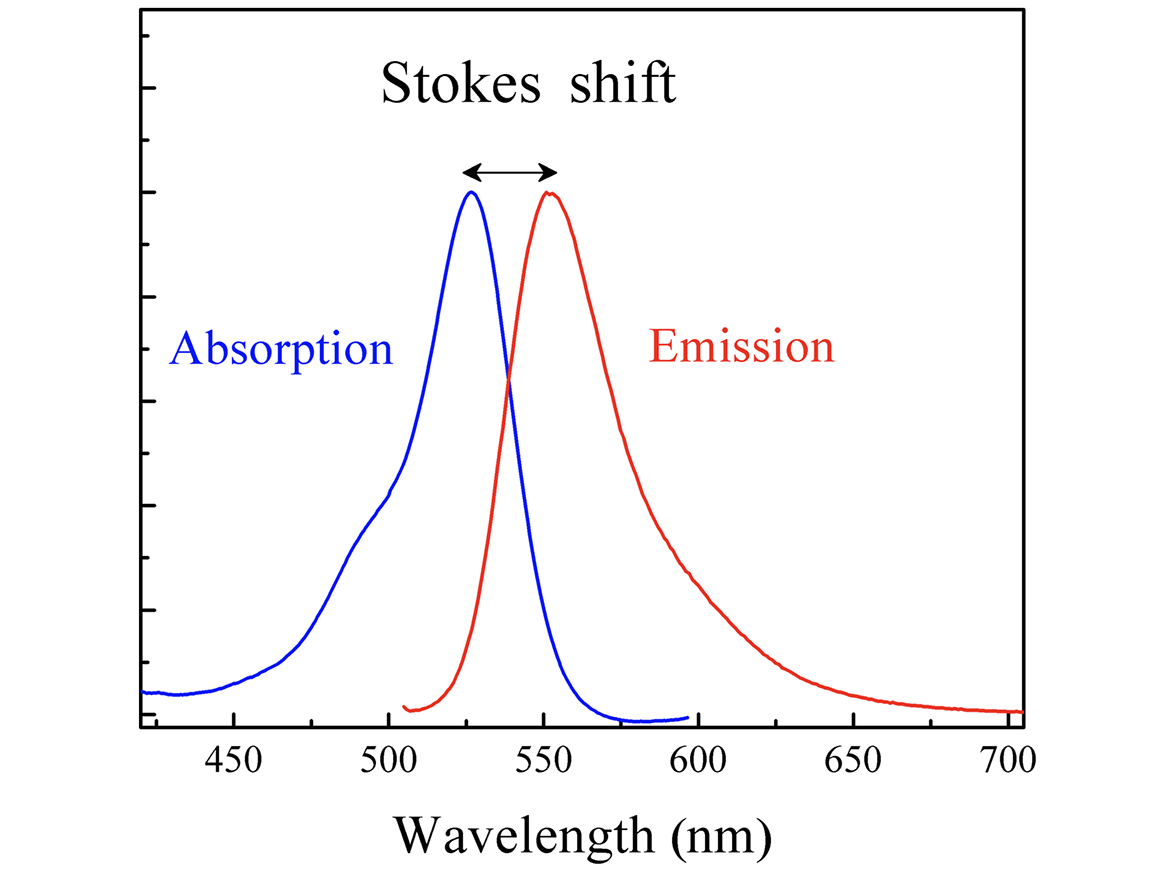
Source: https://en.wikipedia.org/wiki/File:Stokes_shift-_Rh6G.png
More and Brighter Light
Comparison spectra of the light output of comparably colored conventional and daylight fluorescent pigments document the relative intensity of the visual experience produced by daylight fluorescence with as much as four times the light intensity reaching the observer's eye (Figure 10). It's an experience that demands attention!
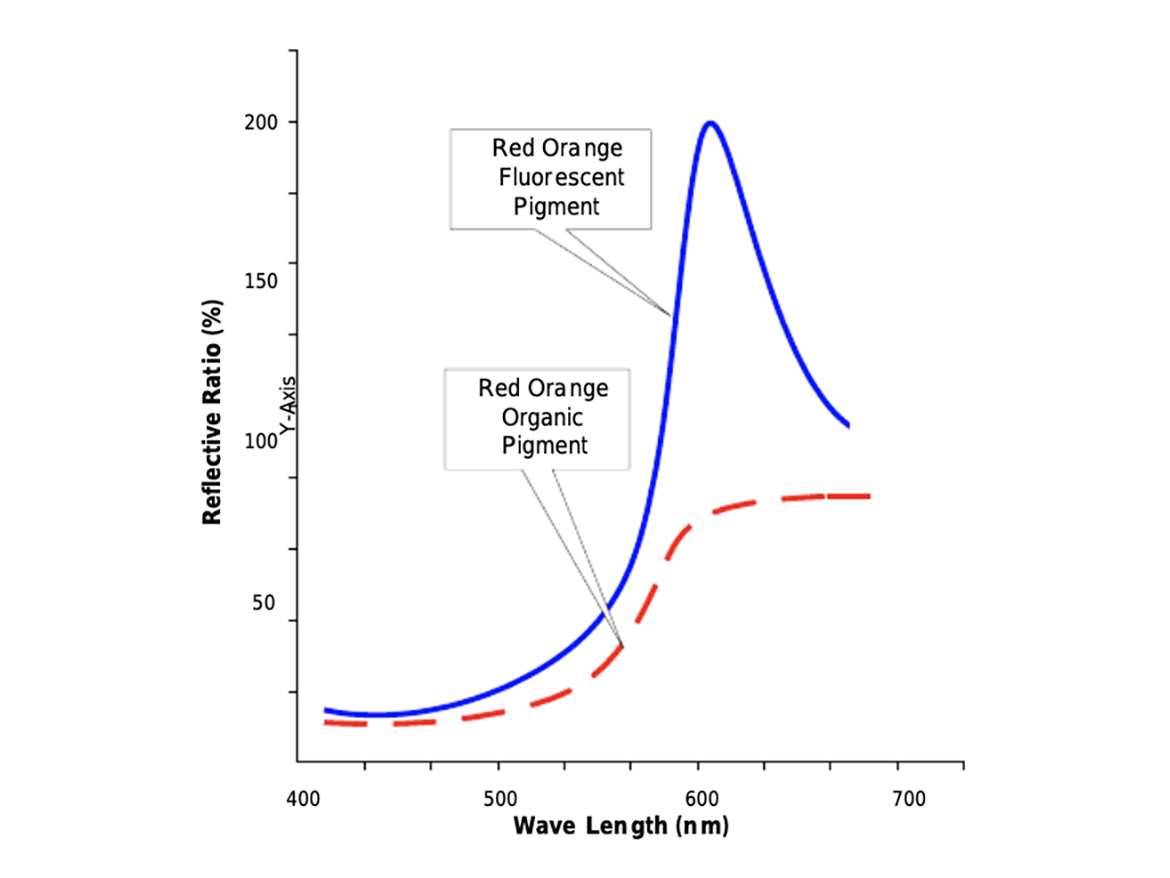
References
- AMC Staff. (2010 June 28). The Brightest Most Visible Safety Colors for Cyclists and Runners. Appalachian Mountain Club. https://www.outdoors.org/resources/amc-outdoors/outdoor-resources/the-brightest-most-visible-safety-colors-for-cyclists-and-runners/?gad=1&gclid=CjwKCAjwjOunBhB4EiwA94JWsH3hlleRf1IbKnNQtAV3_EBHGyEKrYJD0ZXKsuEnDBDOLUt1-jyxLBoCT0sQAvD_BwE
- Juskalian, R. (2009, October 14). Staying Safe as Days Darken. Newsweek. https://www.newsweek.com/staying-safe-days-darken-81459
- Lozovik, A. (2018, September 13). Fluo Green is the Most Visible Color for Swimmers, Triathletes, Cyclists and Runners for Road and Waterway Safety. New Wave Swim Buoy. https://www.newwaveswimbuoy.com/blogs/news/brightest-on-water
- Majid, S. (2011, September/October). Living Colour. WorkSafe Magazine. https://www.worksafebc.com/en/resources/health-safety/articles/living-colour
Looking for a reprint of this article?
From high-res PDFs to custom plaques, order your copy today!