Glycol Ethers and Glycol Ether Acetates for the Development of Latex Paint Film Formation

Coalescents are an inseparable component of latex paints, especially those based on acrylic polymer dispersions with a minimum film forming temperature (MFFT) higher than the typical temperatures at which the target paints will be applied and then dry. Examples of coalescents available on the market are ether glycols and ether glycol acetates, which, although classified as VOCs, are still often used as traditional additives for developing coatings.
Knowledge about such coalescing agents is needed to obtain even more performance consciously, knowing their effectiveness in forming dispersion coatings, as well as their impact on secondary parameters such as scrubbability, gloss, hardness, etc. The article may also be helpful when it is necessary to replace the coalescents in question with more "green," and this requires appropriate knowledge about the formation of coatings and the influence of coalescing agents on many properties. The use of such ether glycols and ether glycol acetates is wider and includes, for example, paint removers, and also as a solvent in solventborne coatings.
The impact of these solvents on health and the environment should influence the subsequent use and labeling. In this article, however, we will focus on the technical aspect and performance in formulations, which can also be methodologically translated into tests of other coalescents.
Film-Forming Properties of Latex Binders
The inseparability of these binders is related to the process of forming acrylic polymer coatings, which are formed before the evaporation of water and the progressive increase in the concentration of binder particles in the coating, as a result of which the polymer particles deform and stick together, as well as connecting other components of the coating, including pigments, fillers, and non-volatile additives.1 This drying takes place according to the Vanderhoff model (Figure 1).
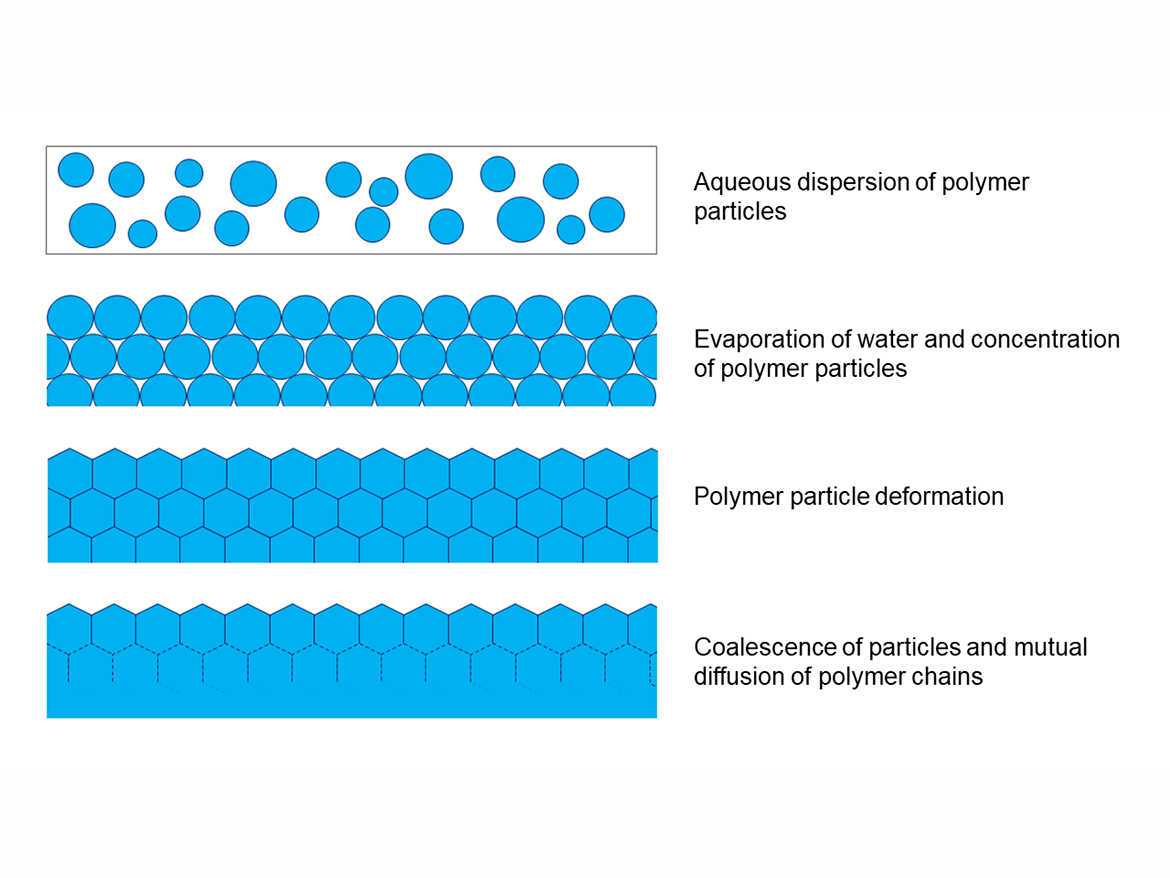
This deformation occurs above a certain temperature, the limit of which (or temperature region) is called the minimum film forming temperature (MFFT). The MFFT for a polymer dispersion is generally calculated similarly to the glass transition temperature (Tg) from the ratio of monomers used, but theoretical calculations are usually quite approximate. For the practical determination of the MFFT of polymer dispersions, the ASTM D2354-10(2018) Standard Test Method for MFFT of emulsion vehicles is used. This method uses the MFFT bar apparatus, which is a plate with a temperature that smoothly changes from one end to the other, to which is applied by draw-down polymer dispersion, and then, after it dries, the place where the cracks disappear is determined by taking a temperature reading, which is also the result of the MFFT (Figure 2).2
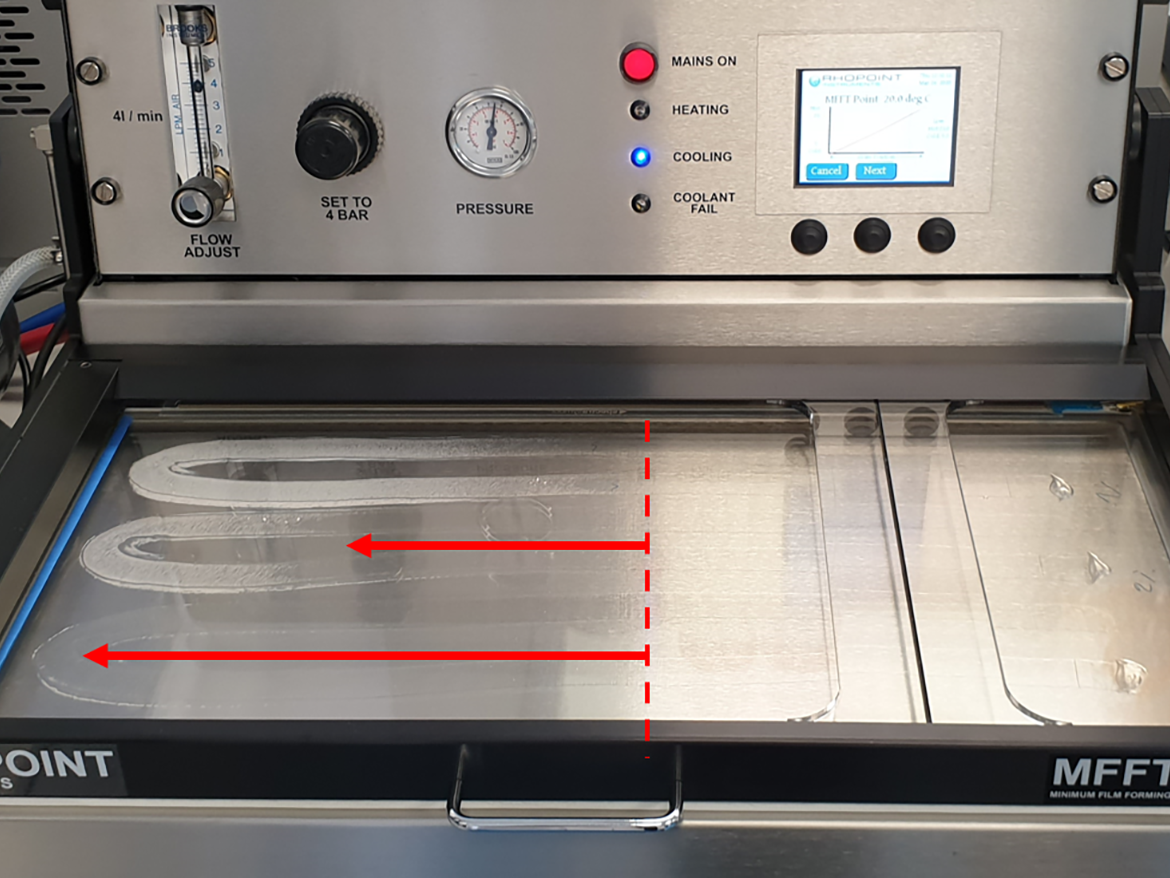
The point at which the MFFT is read is usually visible to the naked eye and takes the form of a colorless film that is formed from film cracks that characterize the lack of film formation at lower temperatures (Figure 3). However, this point is often clearly visible. Sometimes it is an area, and sometimes it is a completely clear polymer film formed just behind the flaking, unformed area.
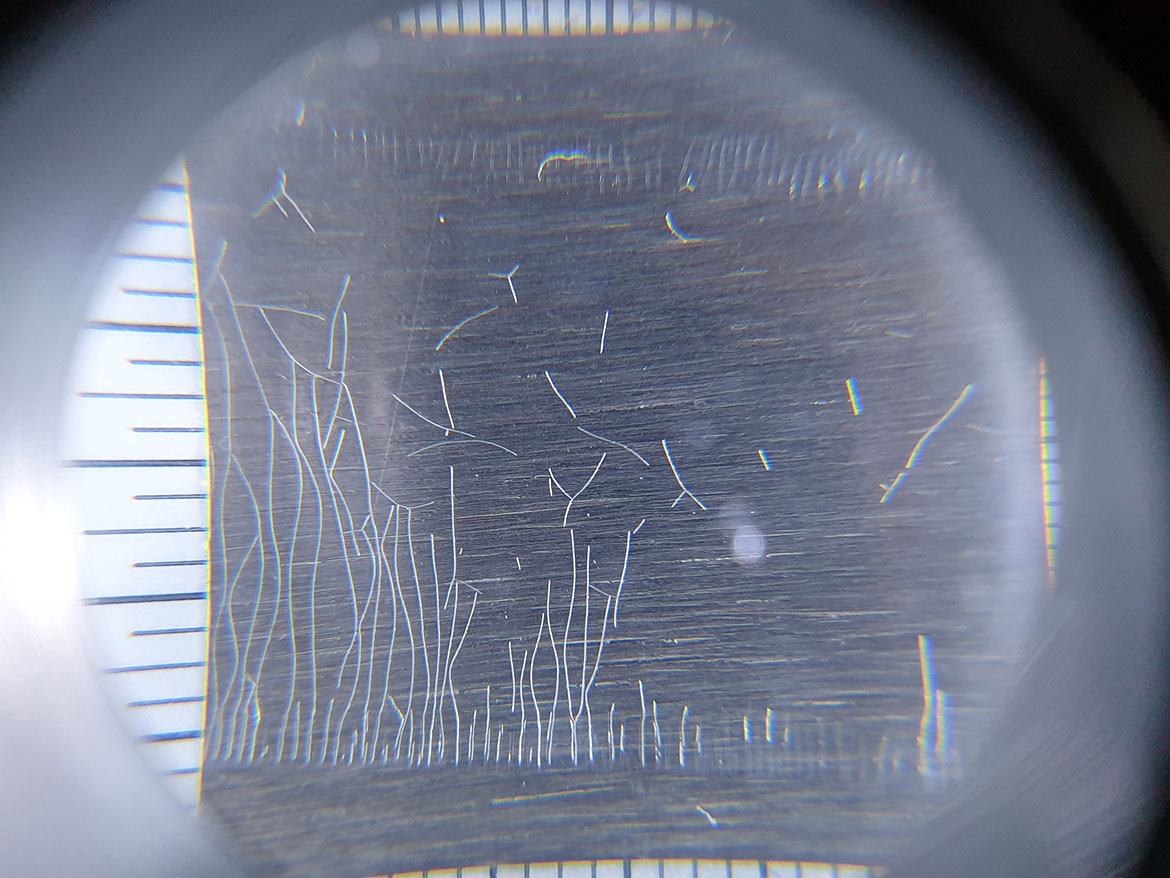
The formation of waterborne dispersion paints (latex paints) depends on the temperature at which the paints are applied. The quality of the formed coatings depends on the temperature at which the process of their formation took place, from application, through evaporation of water, to the final phases of coalescence of dispersion particles and the final formation of the coating.
Difficulty in forming coatings can be seen at low temperatures, which is the case in the northern regions and fall/winter seasons, but also in early spring, where temperatures drop in the evening and night close to 0 °C (32 °F) and even below. As latex paints are waterborne paints, a drop in temperature near the freezing point of water is dangerous both for the destruction of liquid paints, but above all when forming coatings at these temperatures.
Therefore, the use of coalescents is necessary to formulate latex paints. Zero-VOC coalescents are usually used, however, this article discusses the issues on the example of ether glycols and glycol ether acetates. The addition of coalescents is necessary not only in the case of polymer dispersions whose MFFT is higher than the paint application temperature. Coalescents in small amounts (0.5-1%) in formulations using polymer dispersions with MFFT near or below 0 °C (32 °F) have a positive effect on coating formation and water evaporation, which translates into better coating properties.
Experiment
The aim of the experiment was to provide knowledge about the performance of ether glycols and ether glycol acetates most-often used as coalescents in latex paint formulations, with differences in the type of formulation and the scope of PVC, and thus the share of polymer dispersion in the formulation.
It is known that these types of solvents are effective in the development of low-temperature film formation of latex paints, however, their use is often associated with various problems and failures regarding the properties of the obtained coatings.
Coalescing Agents for Case Studies
The solvents used for the case studies were glycol ether and glycol ether acetates from the global paint market, shown in Table 1. The characterization of parameters that will be the basis for further discussion of the properties of solvents as coalescents, as well as GHS and NFPA704 labeling, is also presented.
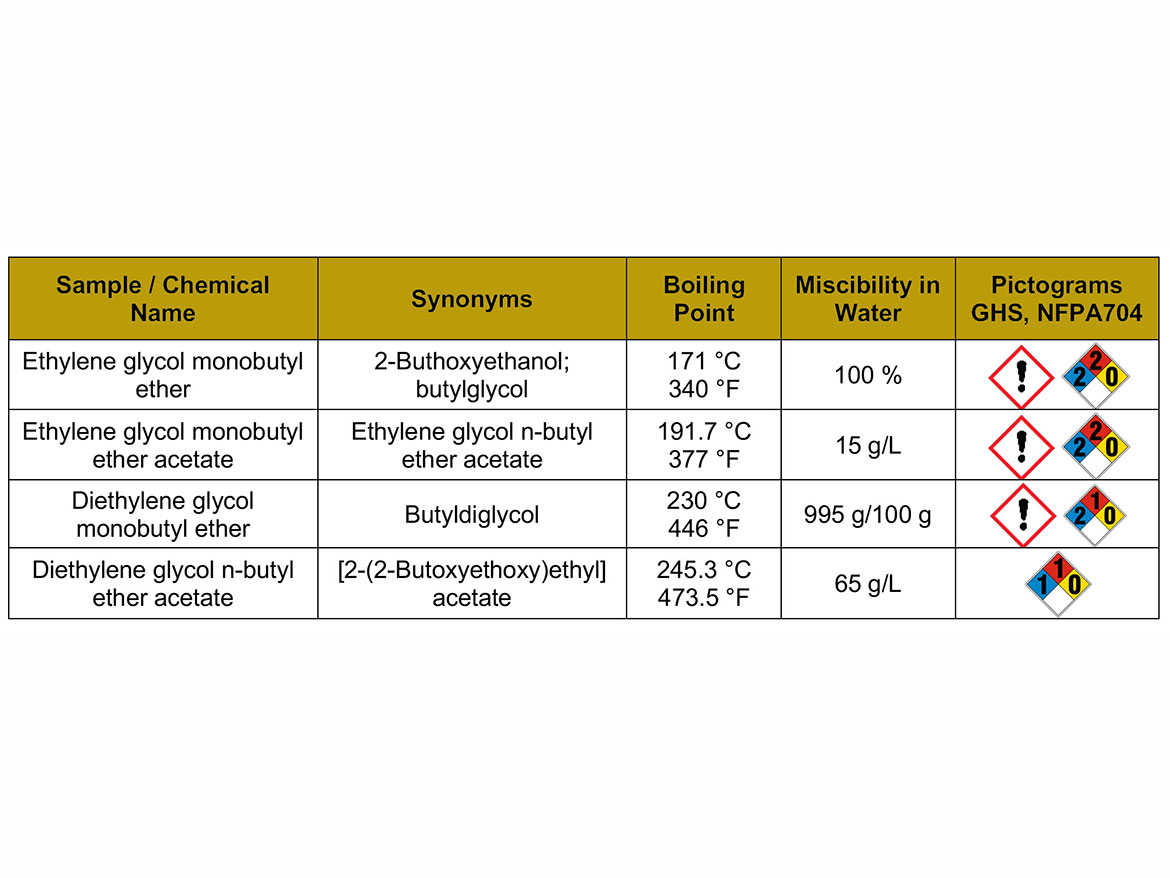
Miscibility in Water
Miscibility in water is one of the parameters that should be taken into account when selecting coalescents due to its impact on the effectiveness of reducing MFFT when coatings are applied to an absorbent substrate. As is known, latex coatings dry by evaporation of volatile components, i.e. water and coalescent, into the atmosphere. However, as the coating dries, water is also partially absorbed into the substrate, which occurs with varying intensity depending on how absorbent the substrate is. If the coalescent is fully miscible with water, when it dries it is absorbed together with the water, which is why it can often be noticed that in the case of forming coatings at low temperatures on very-absorbent substrates, a situation may arise where part of the coalescent dose is "missing" for properly forming a coating by its "escape" into the absorbent substrate along with water.
I described this extensively in the article Water Miscibility Differences in Coalescing Agents and the Influence on Latex Paint Properties, published in PCI Magazine in 2021.3 However, can high miscibility with water mean that the formation of coatings on an absorbent substrate will be impaired? It turns out no, as discussed further in the experimental section.
Figure 4 shows photos of the test tubes with coalescents used for testing and the water miscibility results. You can see the translation of data from Table 1, but also additional haze in the test tube with diethylene glycol monobutyl ether.
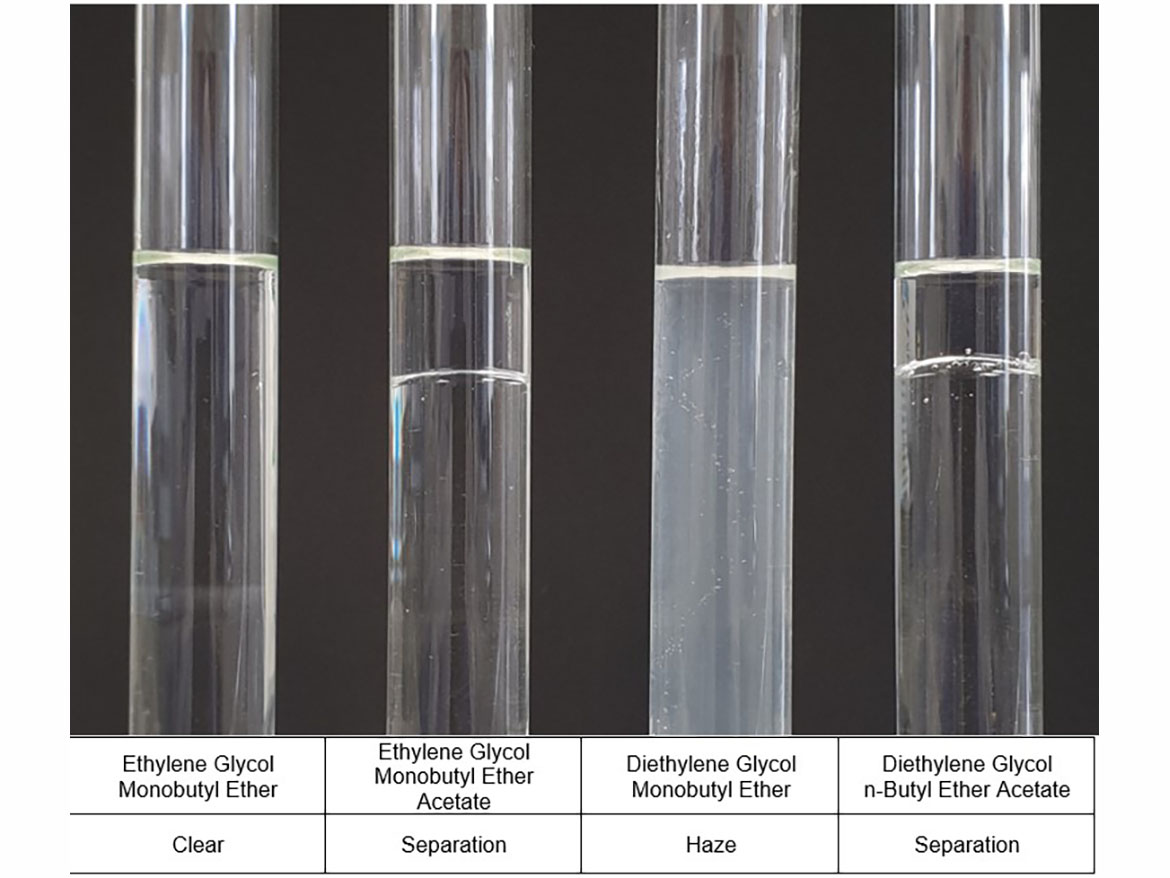
Determination of MFFT and Selection of Dosage Level
The first step in selecting coalescents and searching for a dose to use in the formulations is to determine the coalescence curve. The prepared mixtures of polymer dispersions with coalescents in ladder doses are subjected to MFFT determinations, determining the development of film formation for a particular dose used for a specific polymer dispersion. The project used polymer dispersions dedicated to use in waterborne latex paints with different MFFT, on which the formulations prepared later were based. Typical dispersion characteristics of polymers used in the project are presented in Table 2.
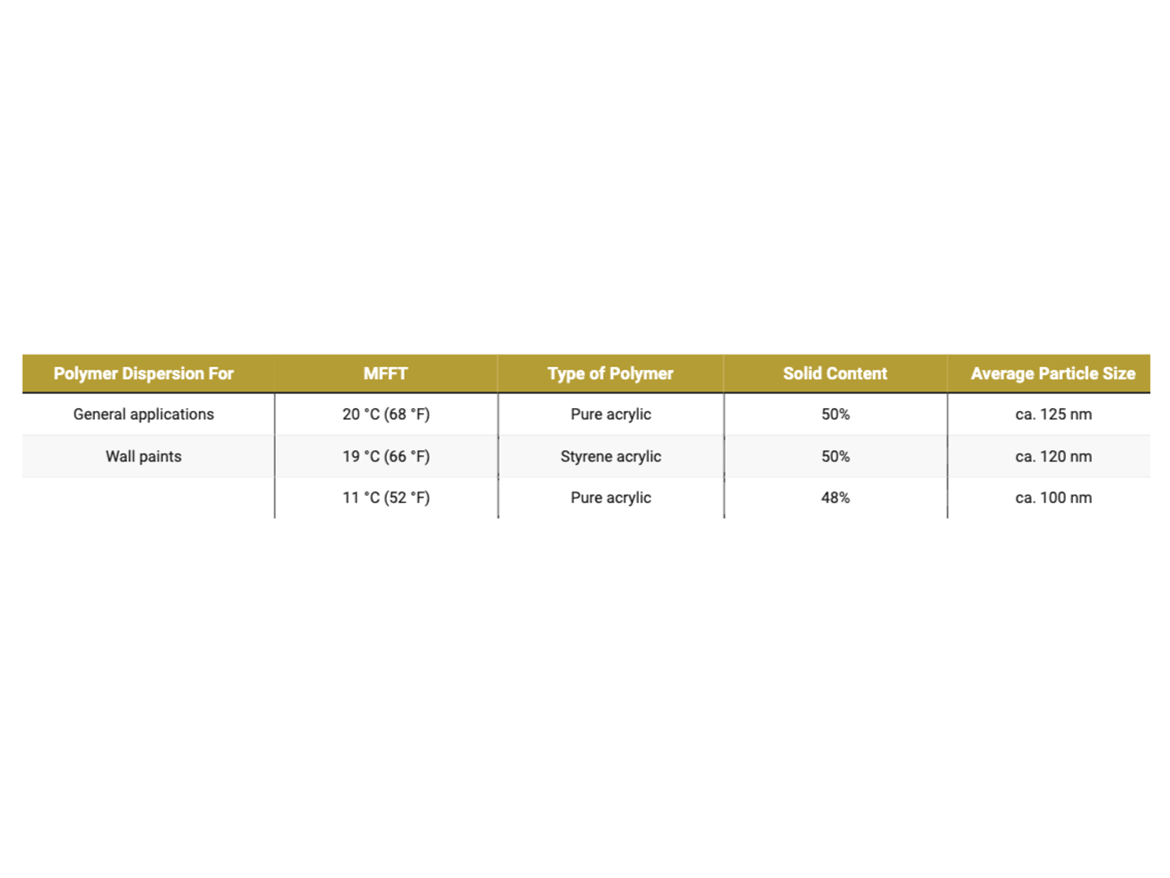
The idea behind determining the coalescence curve was to find a dose for each coalescent that would reduce the MFFT to the range of 0–2 °C (32–36 °F) for each of the three polymer dispersions used for testing. Coalescence development graphs using the tested ladder dose coalescents for each of the polymer dispersions are shown in Figures 5-7.
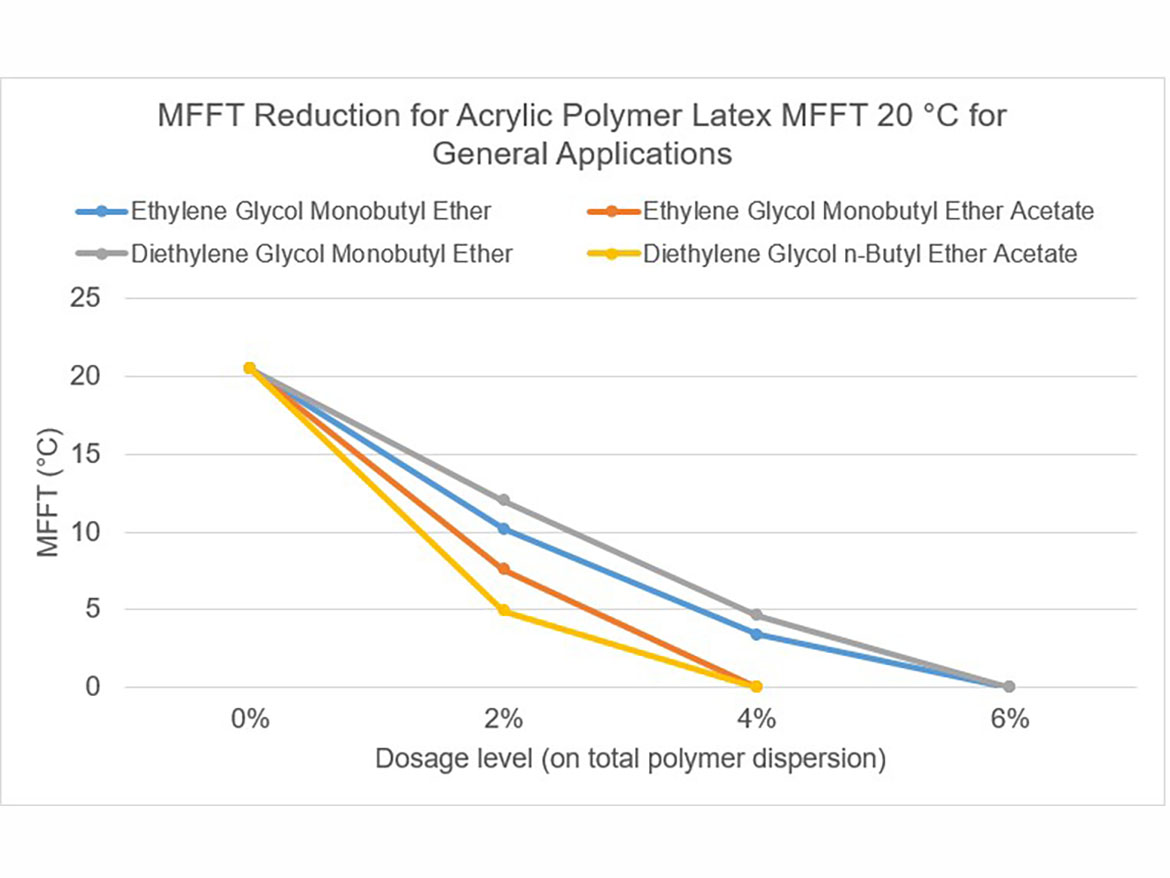
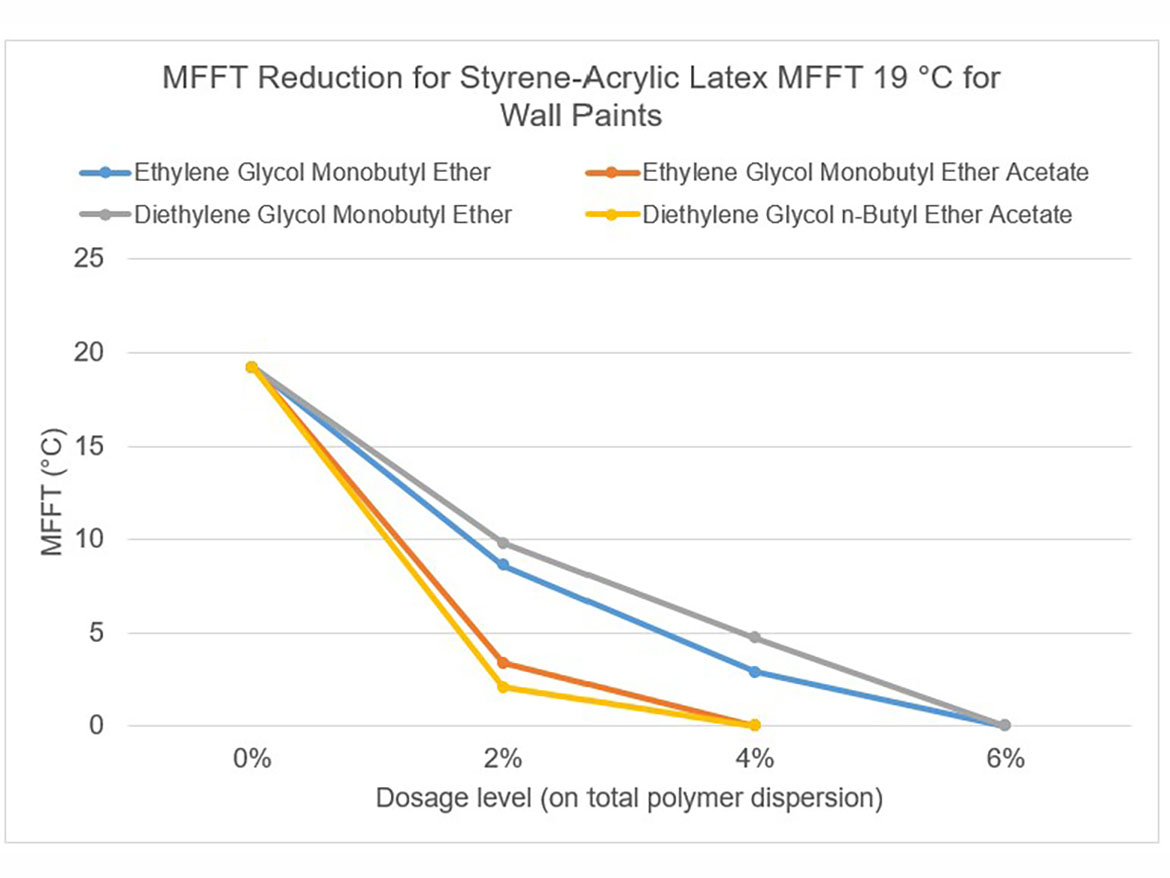
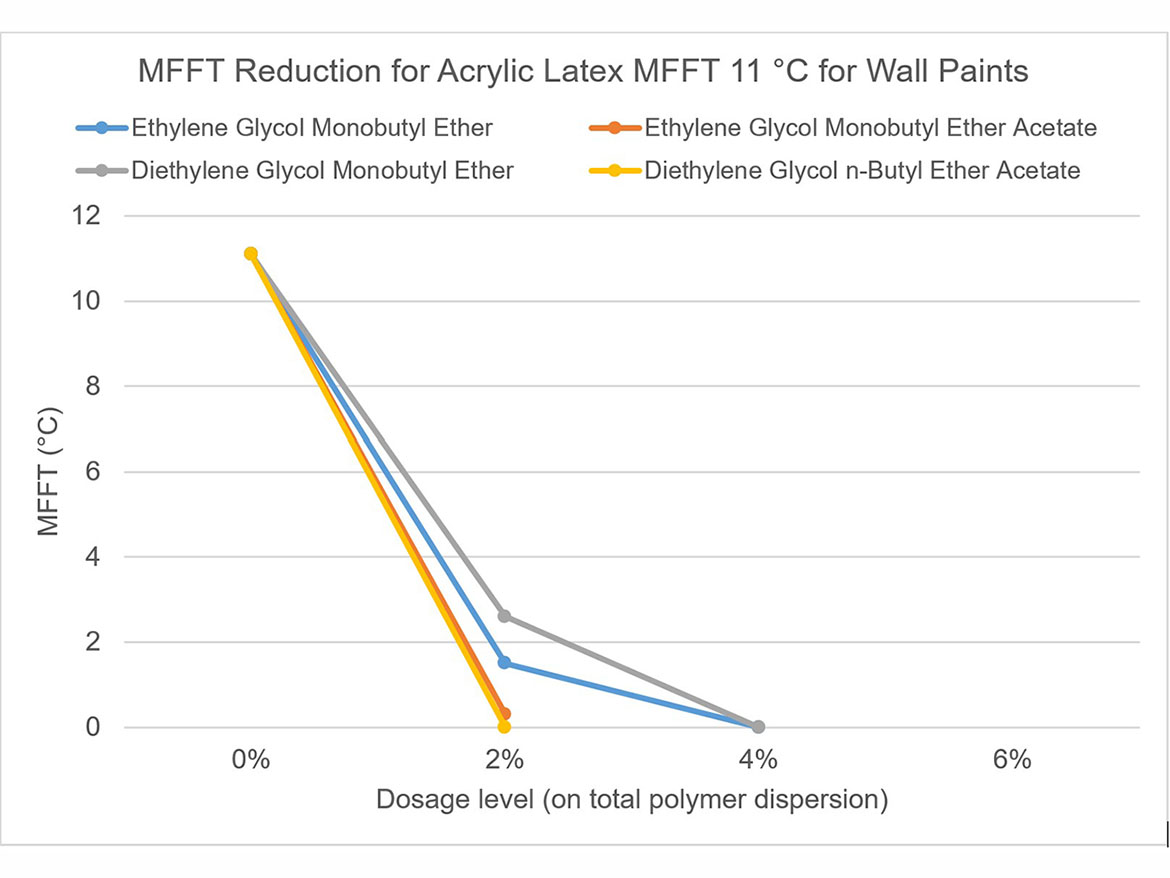
By determining coalescence curves, doses were selected for individual coalescents and polymer dispersions to be used to prepare paints. Selected doses that meet the assumptions of MFFT reduction are presented in Table 3 and marked as Dosage Level I.
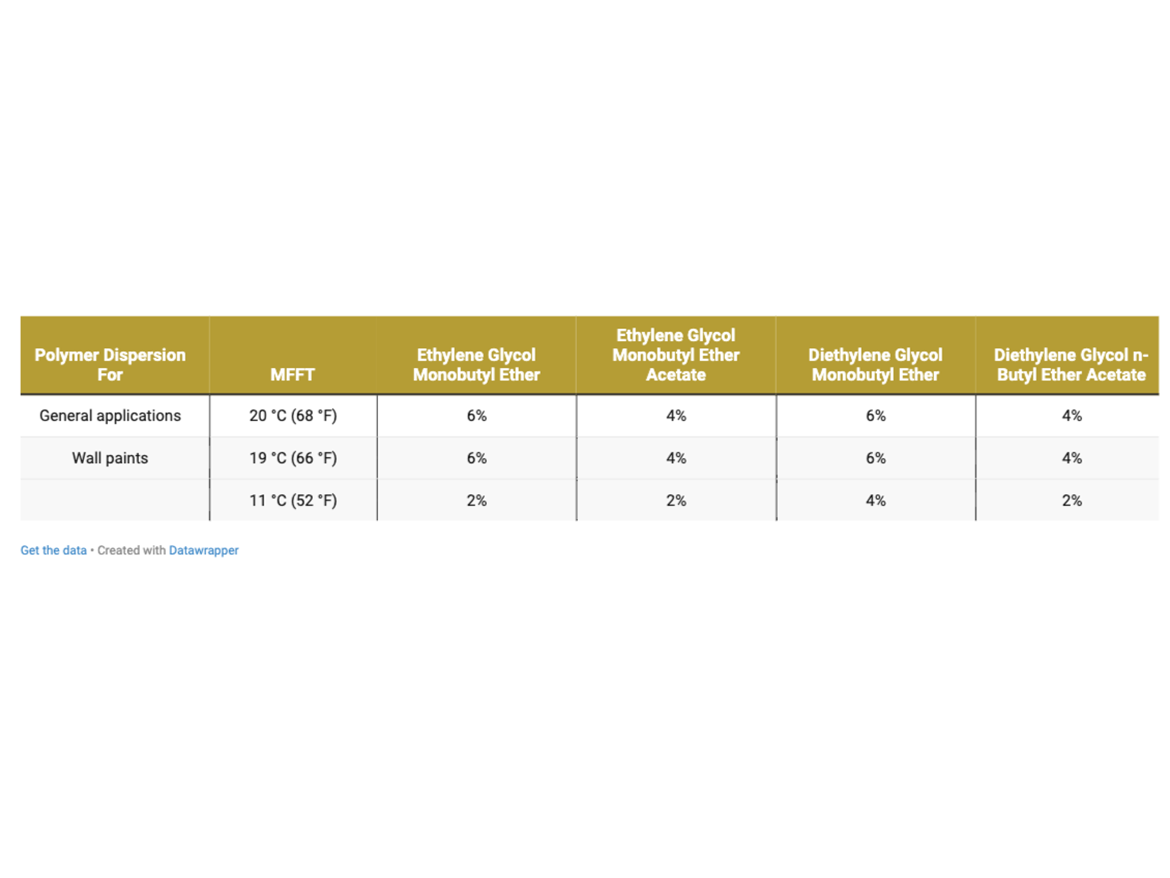
The determined doses meet the assumptions established by the MFFT test in accordance with ASTM D2354, which is performed on the apparatus plate (on polyester foil), i.e. on a non-absorbent substrate from which water and coalescents evaporate only into the atmosphere. Therefore, a second level of coalescent dosing was assumed, which included increasing the set doses as an additional level to prepare additional samples extending the scope of tests. Additional doses were determined as +2% by weight to the doses established above in Table 3. The additional dosing described as Dosagel Level II is shown in Table 4.
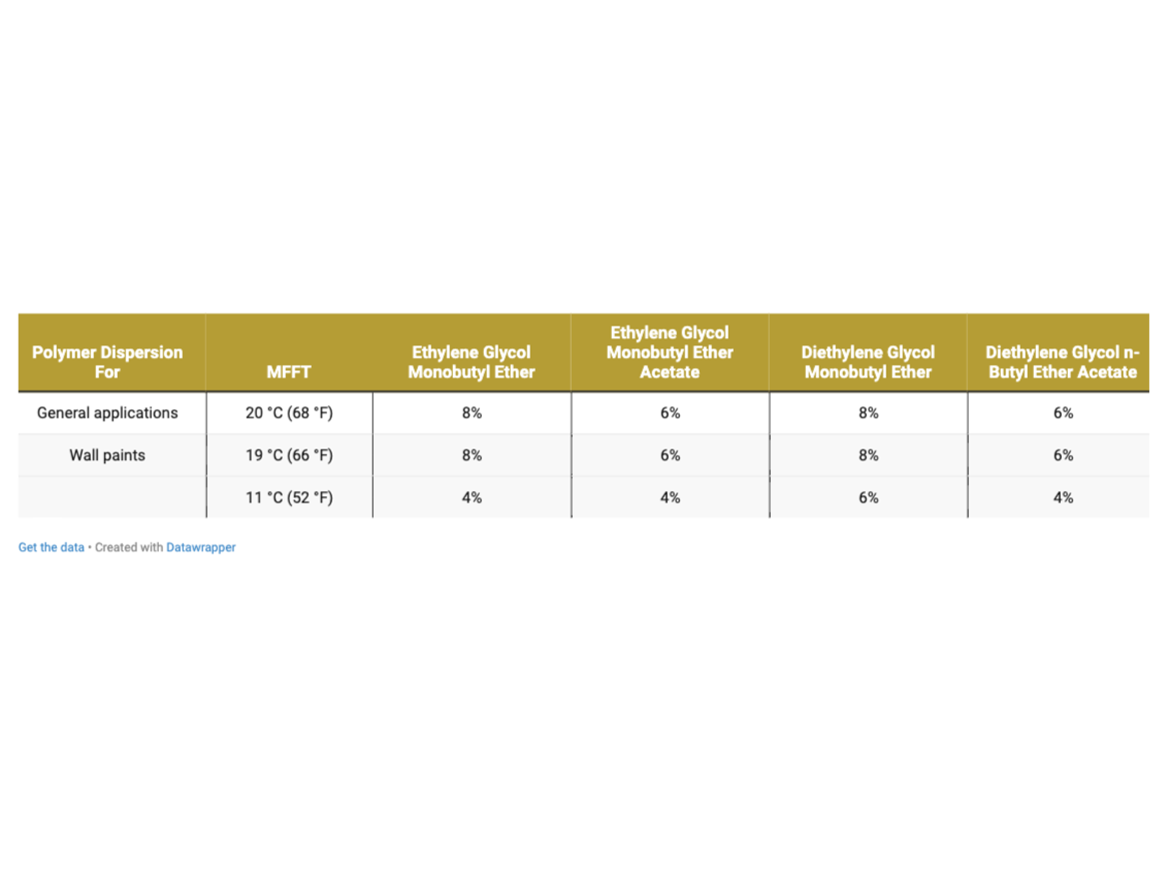
Paint Samples Preparation
For the case studies, a set of sample latex paints based on polymer dispersions was prepared, to which coalescents were selected by determining coalescence curves, along with coalescing additives in Dosage I (dose ensuring film forming temperature 0–2 °C / 32–36 °F) and Dosage II (dose as I +2% coalescent). White gloss paints were prepared on the basis of polymer dispersions for general applications, while flat paints were prepared on the basis of polymer dispersions for wall paints as transparent bases (ultra-deep) tinted with pigment concentrates (a mixture of PR 112 and PB 15:3).
The paints were prepared on a laboratory scale from the formulations shown in Table 5.
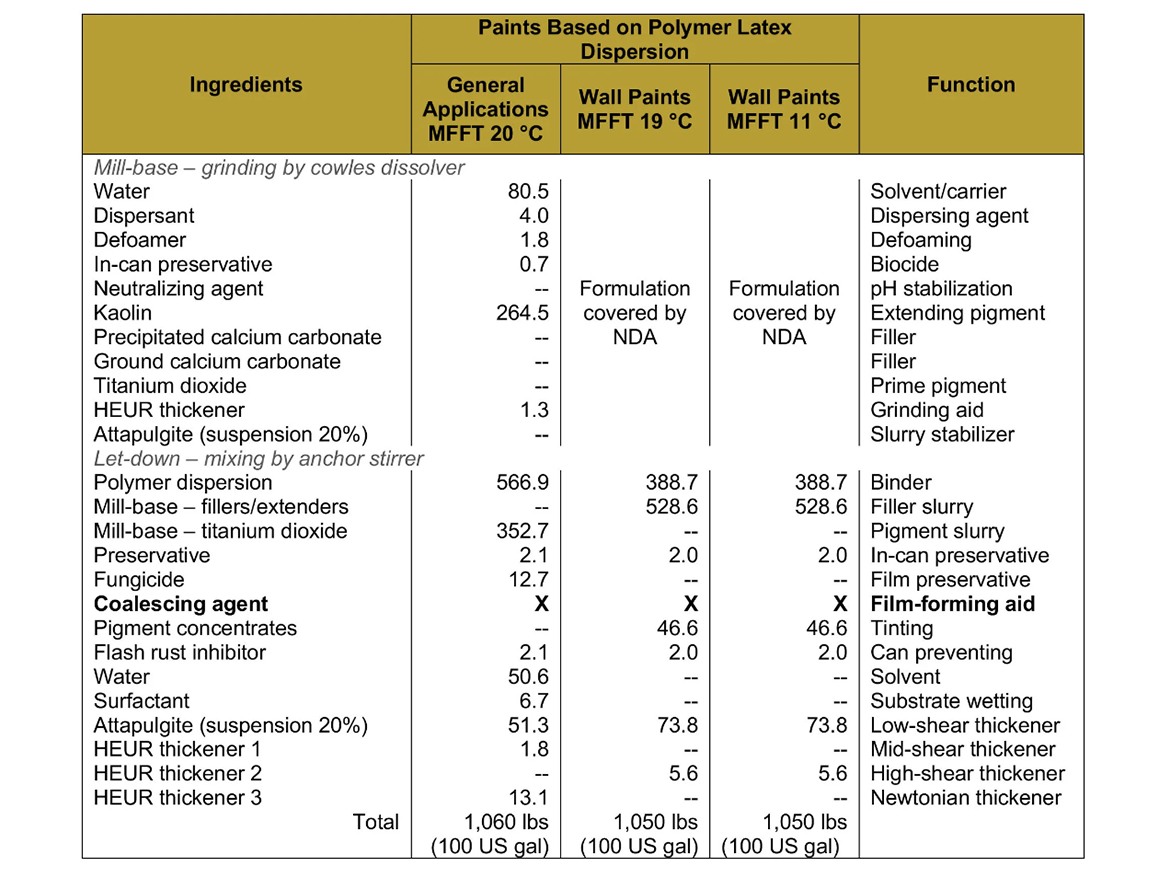
Table 6 provides a summary of the calculated formulation constants.
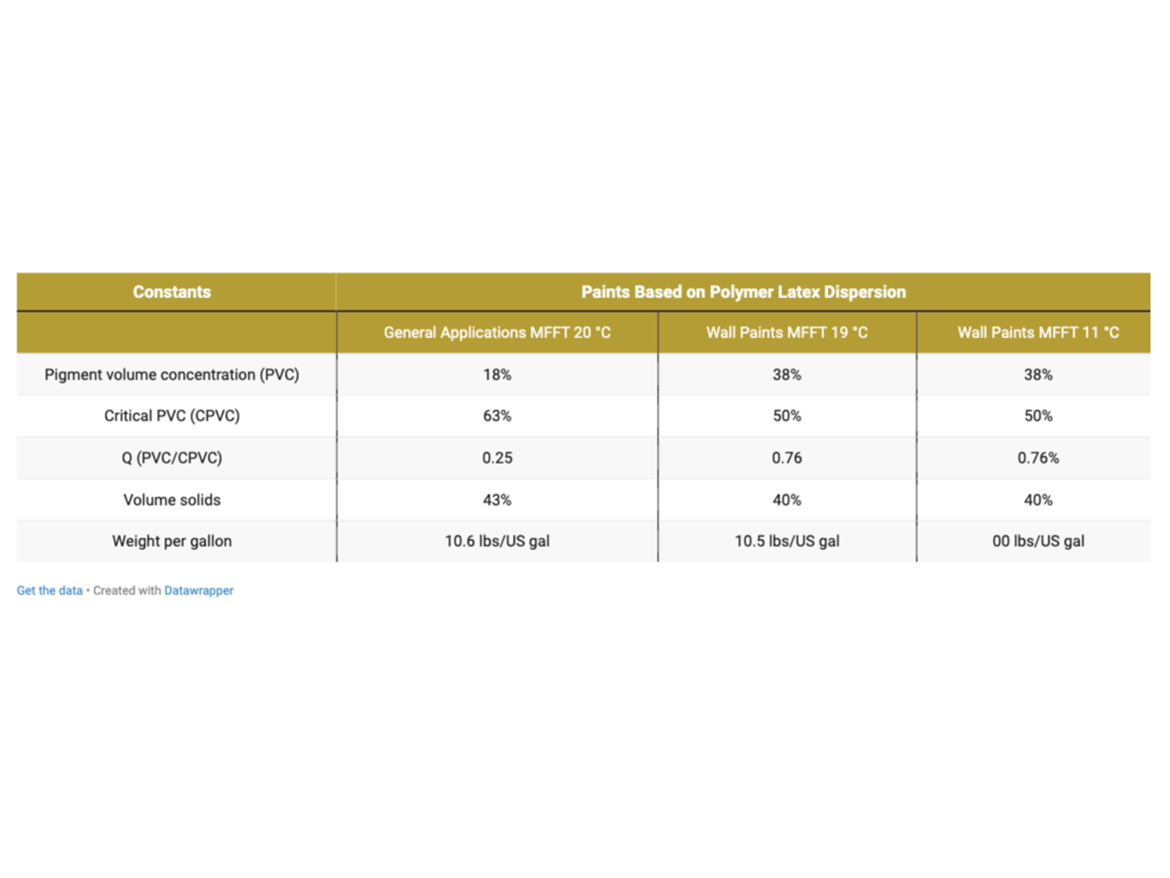
Testing Program
Tests were carried out for the prepared paints in accordance with the program presented in Table 7.
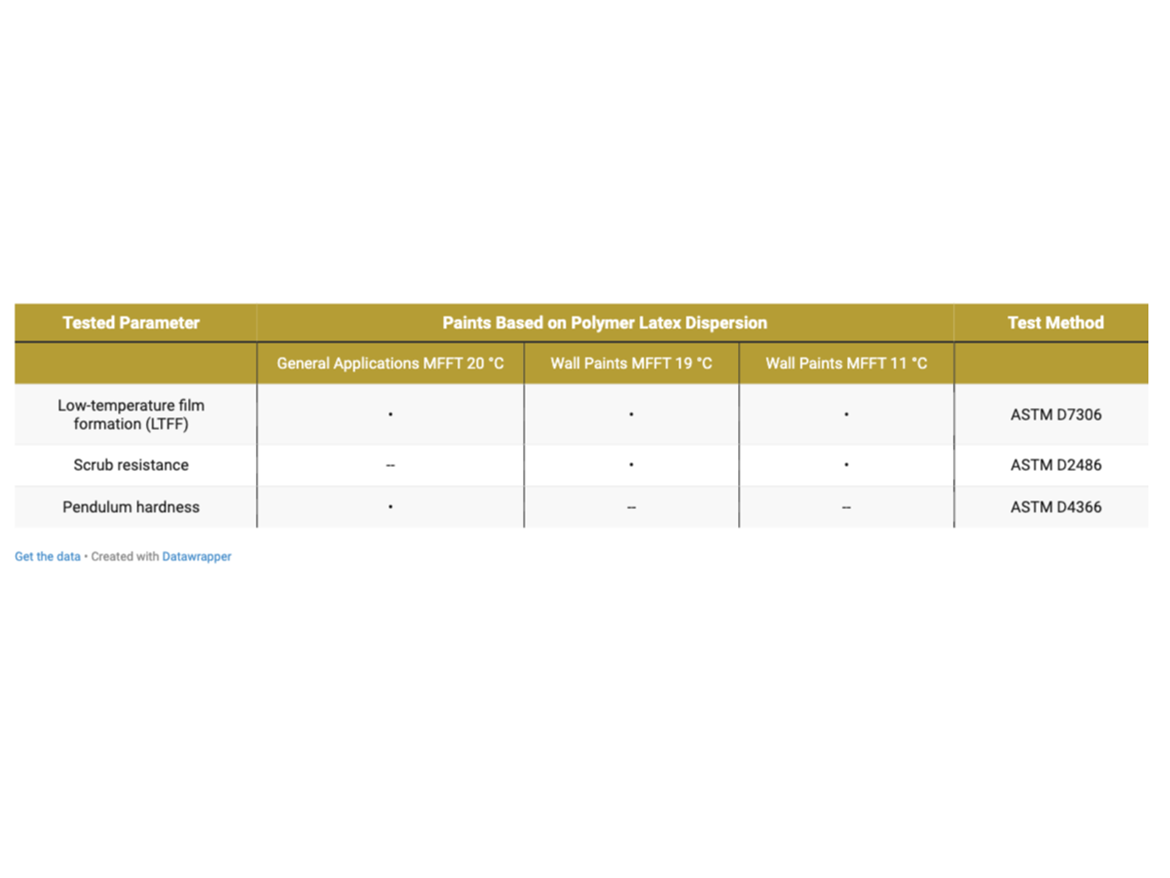
Test Results
The test results are discussed and interpreted below.
Low Temperature Film Formation (LTFF)
The LTFF test is performed for prepared paints, and not the MFFT test for polymer dispersions (and its mixtures with coalescing agents). Paints cooled to the test temperature are applied by automatic drawdown to a substrate divided into two areas, the first of which is non-absorbent and the second absorbent. Drawdown is performed in a rather thick, wet layer, which further tightens the test conditions, causing the coating to release a lot of water into the substrate. After application, the coatings are immediately placed at low temperature and after 16 hours removed from the refrigerator and assessed. The rating includes cracking of the coating, which is assessed separately on the absorbent and non-absorbent surfaces, and the test result is added up to obtain the highest rating of 10. The rating is defined by ASTM D7306 and is as follows:
5 – No cracking
4 – Slight cracking (visible with magnifying glass only)
3 – Some cracking (just visible with eye)
2 – Moderate cracking
1 – Severe cracking
0 – Film chips off completely
For the prepared paints, LTFF tests were performed at 4 °C (39 °F) and the results are presented in Figure 8 below.
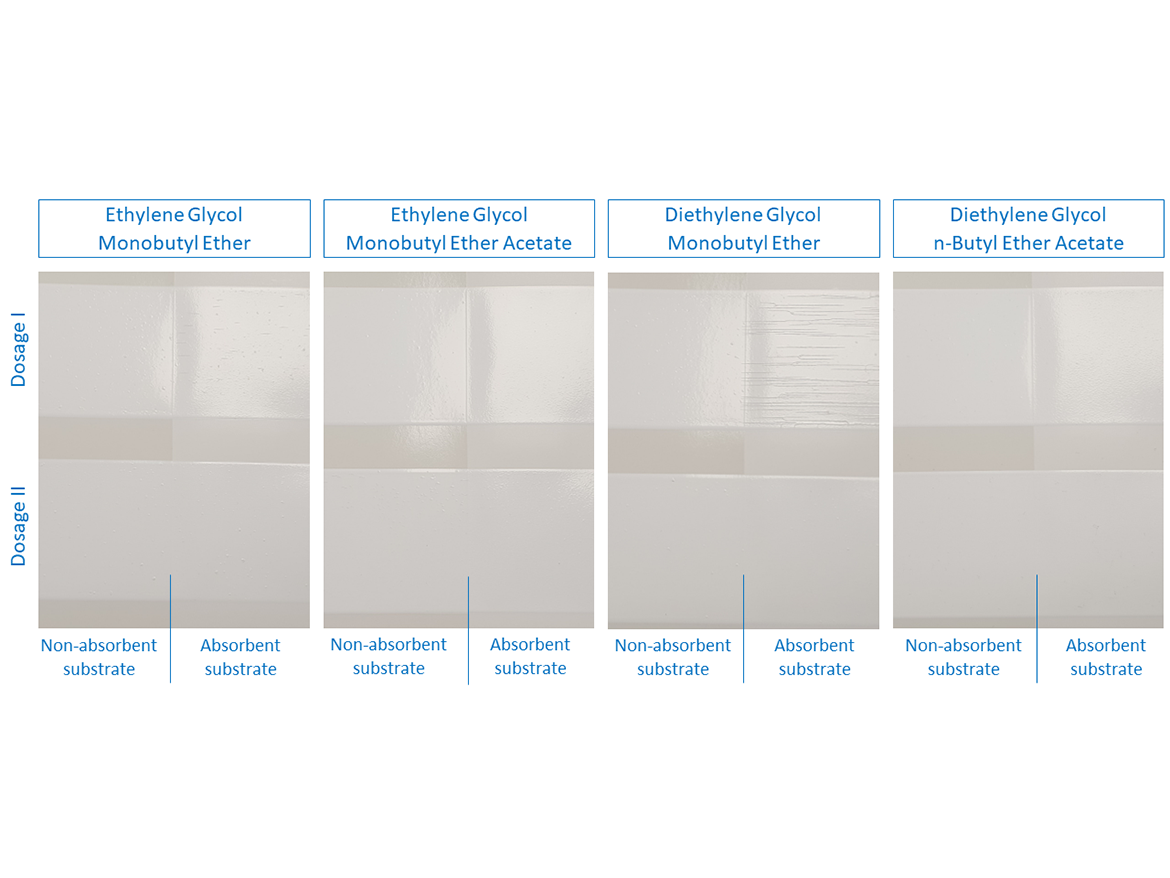
Table 8 presents the cracking assessment of gloss coatings after LTFF test.
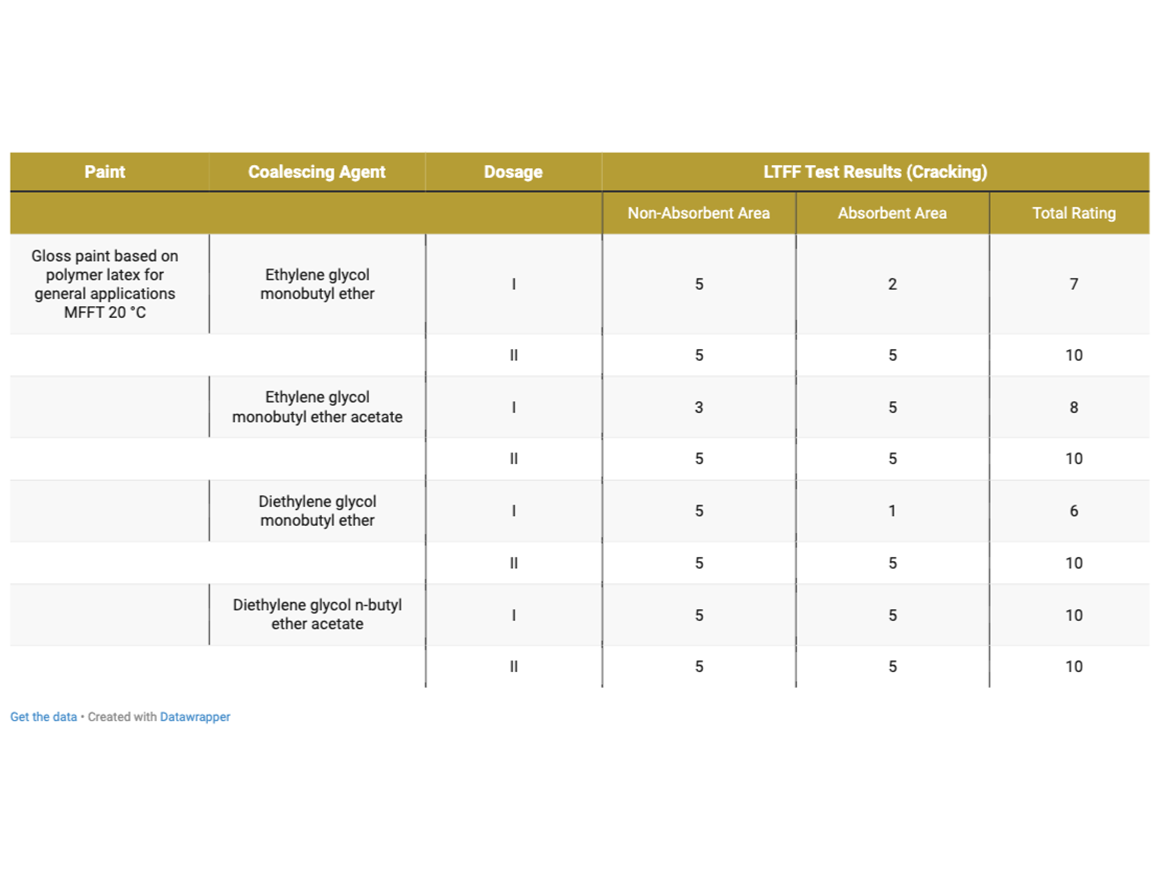
As can be seen in the photos after LTFF tests in Figure 8, gloss coating with a dose of diethylene glycol monobutyl ether in Dose I showed very-severe cracking on the absorbent substrate, while the coating was uncracked on the non-absorbent substrate. Dose II, increased by an additional 2%, eliminated cracking on the absorbent substrate. It should be recalled that this coalescent has a miscibility with water of 995 g/100 g and the dosage set at Level I was intended to ensure film formation in the range of 0–2 °C (32–36 °F), as demonstrated during MFFT tests. In reality, i.e. in the paint formulation, it turned out that no coating formation occurred on the absorbent substrate, it should be noted that the LTFF test was conducted at 4 °C (39 °F).
After carefully assessing the photos after LTFF tests for gloss coatings, it is also visible that the ethylene glycol monobutyl ether coating shows smaller, but still visible cracks on the absorbent surface. In this case, Dose I also did not show effectiveness in forming a coating at low temperature on an absorbent substrate, while forming a coating on an absorbent substrate was carried out without any problems. Here we are also dealing with a coalescent with 100% miscibility with water. Also in this case, the increase in Dose II helped to form a low-temperature coating on the absorbent substrate.
An interesting case is the LTFF result for the gloss coating with ethylene glycol monobutyl ether acetate, which shows that the coating was not formed properly but on a non-absorbent substrate, while on an absorbent substrate the coating was formed without cracking. This coalescent is characterized by very low miscibility with water (15 g/L) and a relatively low boiling point, which could result in its Dose I being insufficient in a given case, even on a non-absorbent substrate. Increasing to Dosage Level II eliminated cracks on the non-absorbent surface. The remaining gloss coatings formed without cracking under the test conditions at 4 °C (39 °F).
Then it was time to test flat paints for walls, which were based on two polymer latex dispersions with different MFFT. These paints were prepared in deep colors to notice, in addition to cracking, also the effect on color differences after forming the coatings at low temperature. The results are shown in the photos for paints based on polymer latex MFFT 19 °C (66 °F) in Figure 9 and for paints based on polymer latex MFFT 11 °C (52 °F) in Figure 10.
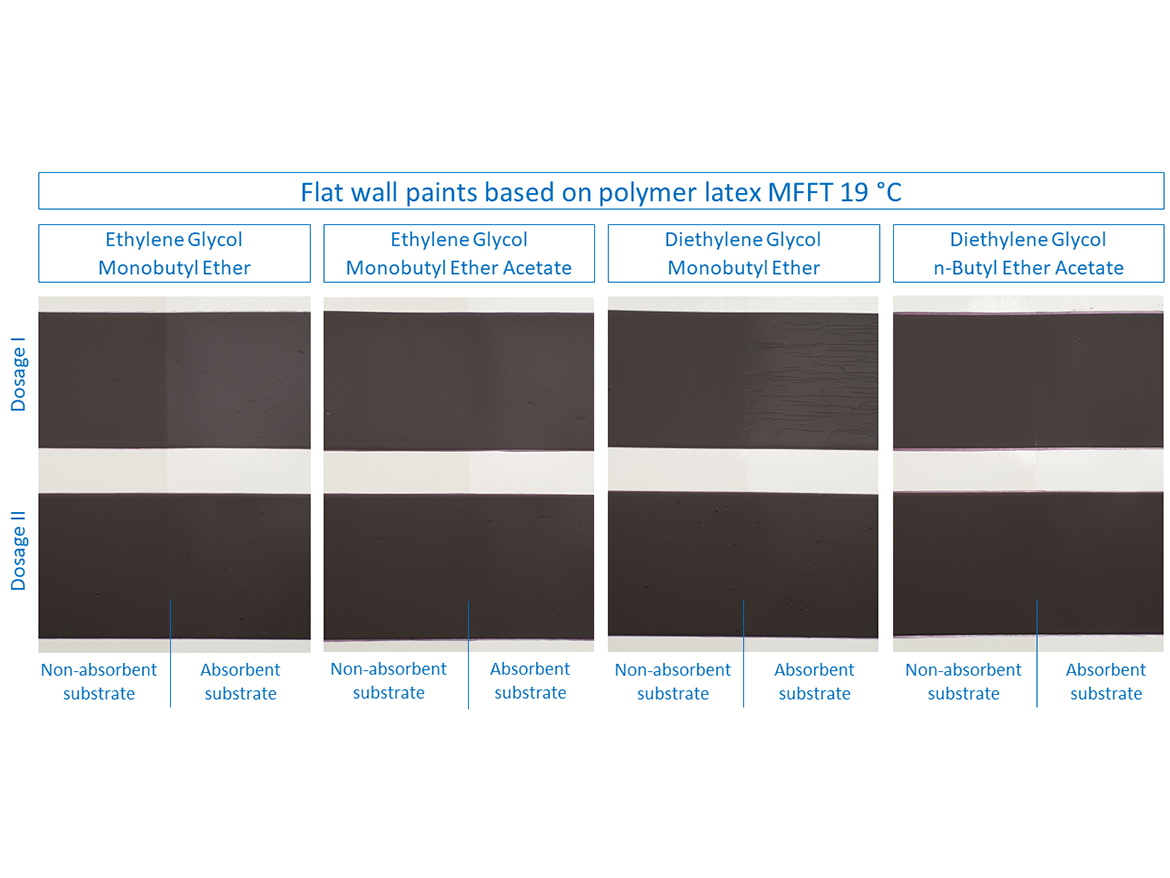
In the case of flat paints based on polymer latex MFFT 19 °C (66 °F) it can be seen that, as in the case of gloss paints, the sample with Dose I for diethylene glycol monobutyl ether showed very severe cracking on the absorbent surface during the LTFF test. Also, the sample with ethylene glycol monobutyl ether showed cracks on the absorbent surface for Dose I, which can be correlated with gloss coatings and it can be concluded that high miscibility with water is responsible for the absorption of the coalescent together with water into the substrate during the low-temperature test, especially since in both of them, in some cases, increasing the dose eliminates the problem of forming a coating on an absorbent substrate. These two examples show something else very important, namely that you cannot base the coalescent dose determined on the basis of the dispersion-coalescent mixture test for MFFT on the paint formulation and the formation of the finished paint film. Determining the dose by determining the coalescence curve may be the beginning of determining the dose through further tests, including: LTFF, because, as the above cases show, the dose may be incorrectly determined, which will result in improper coating formation.
It should also be noted here that in the photos presented, in addition to cracks in the case of two flat paint samples, differences in color are also visible on the first polymer dispersion, for which coalescent and the process of forming the coating at low temperature are also responsible. After the LTFF tests, additional measurements of color coordinates and color difference were made, and the results are presented in the photos and in Table 10.
The greatest difference in the color on the absorbent substrate can be seen in samples with Dose I of the coalescent ethylene glycol monobutyl ether (ΔE*ab = 9.49) and with Dose I of diethylene glycol monobutyl ether (ΔE*ab = 8.88). These values drop dramatically after increasing to Dose Level II, which also shows that the dose originally determined based only on the MFFT determination is not the appropriate one also in terms of color saturation after drying at low temperature for coalescents that are well miscible with water.
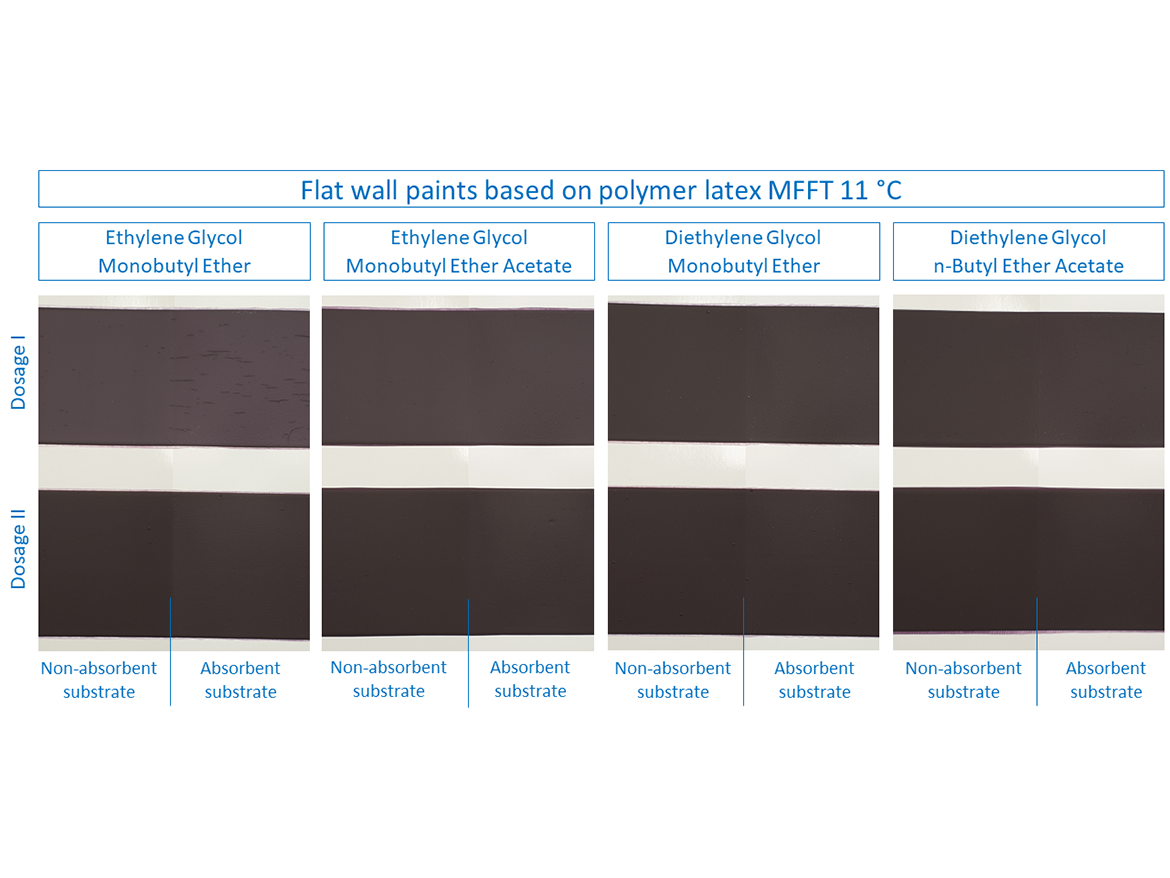
In the case of paints based on polymer latex MFFT 11 °C (52 °F), slightly different results can be observed compared to the previously discussed examples. For flat paints prepared with it, cracking occurred during the LTFF test only for ethylene glycol monobutyl ether in Dose I on both absorbent and non-absorbent substrates (see Figure 10 and Table 9). All other doses of coalescents, both for Doses I and II, formed coatings without cracking. Interestingly, also diethylene glycol monobutyl ether, which has so far shown that its use in Dose I would seem to be the rule that it will crack, obtained different results with a good result of forming the coating.
Table 9 presents the cracking assessment of flat wall coatings based on polymer latex MFFT 19 °C (66 °F) and MFFT 11 °C (52 °F) after LTFF test.
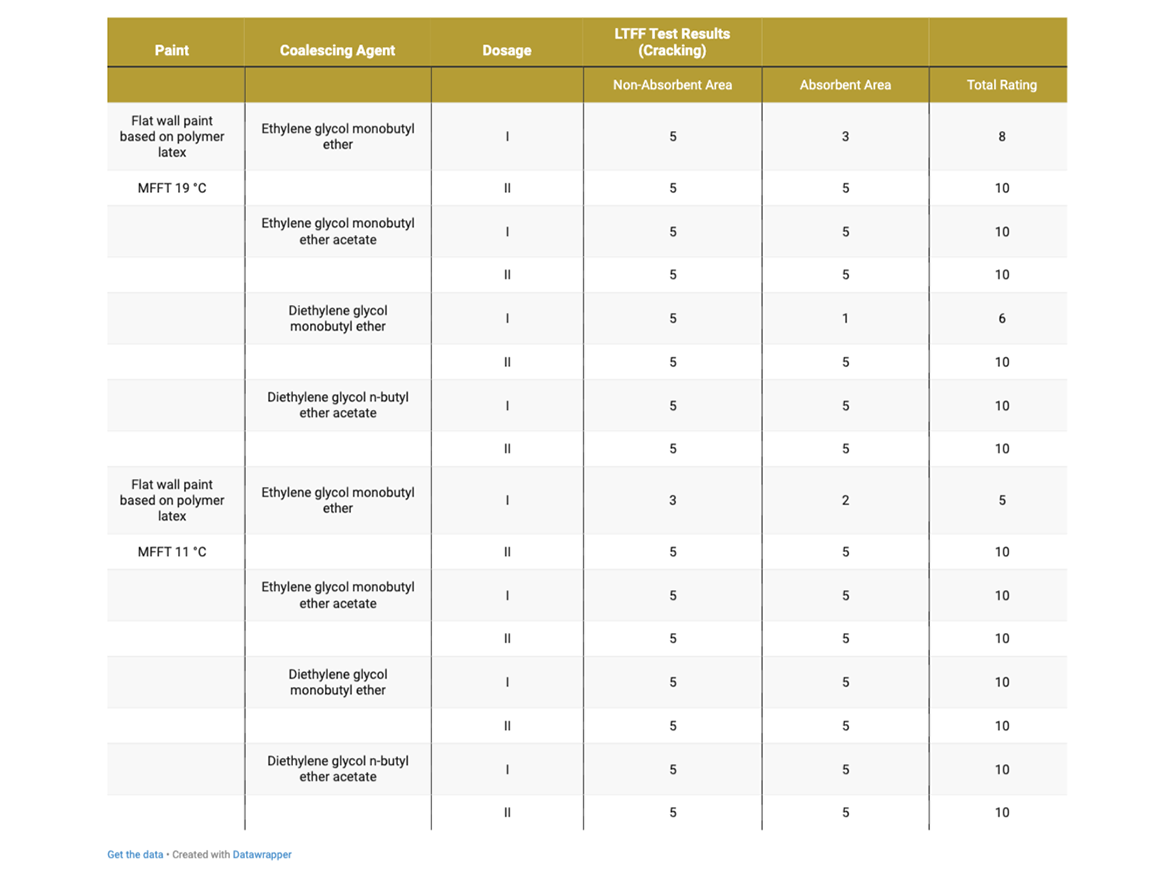
In the analysis of the impact on the color difference for paints based on polymer latex MFFT 11 °C (52 °F), it can be noticed that the greatest tendency to difference in color was achieved by the coalescent ethylene glycol monobutyl ether and diethylene glycol monobutyl ether, both in Doses I and II, which would confirm the previous results depending on miscibility with water, however, the shade differences are not as large as in the case of the polymer dispersion with an MFFT of 19 °C (66 °F) and are present in both doses, not just one.
This means that coalescent can be a silent cause of color differences after coating formation at low temperatures, where it is not usually considered to be the "culprit" of such coating behavior.
At the same time, it can be concluded that despite the noticeable rules and relationships between miscibility with water and problems with film formation and color differences, it is clear that they may look different depending on the polymer dispersion.
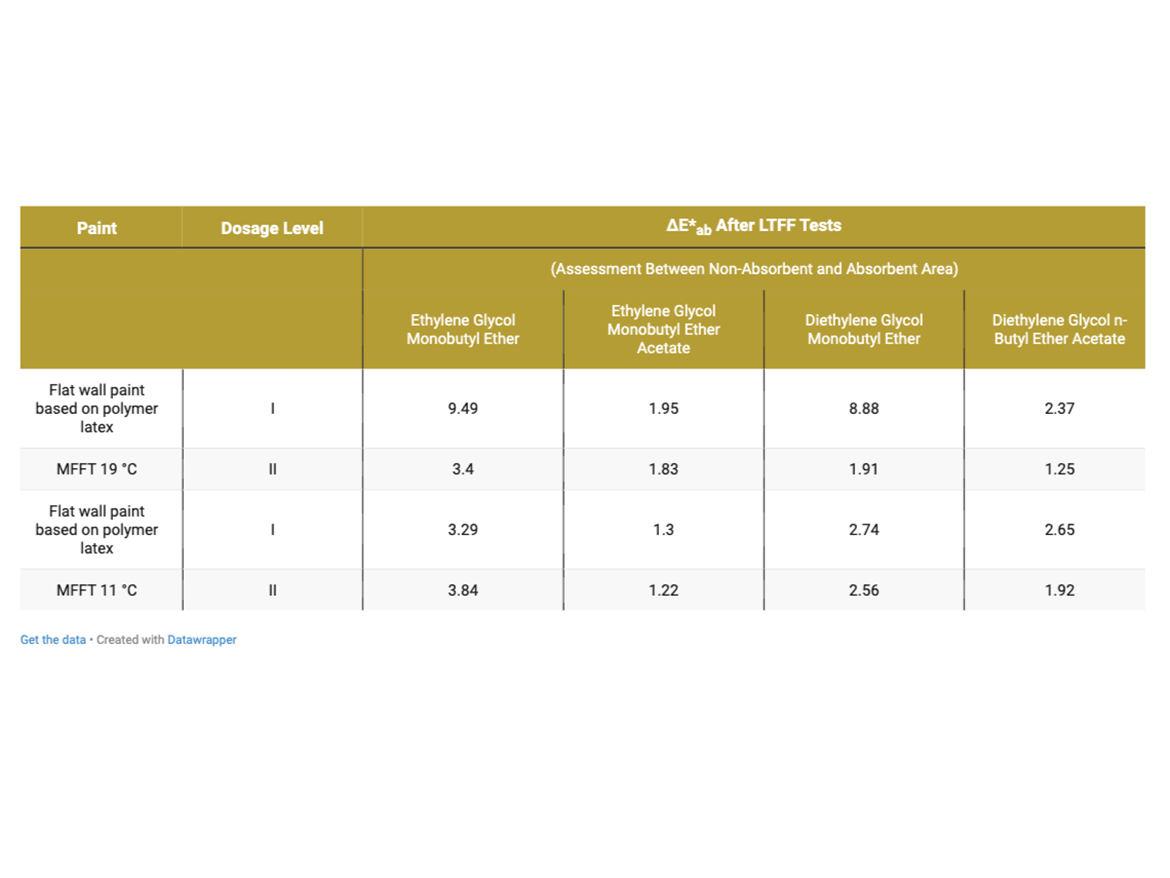
Scrub Resistance
Another test comparing coalescents in flat paints was scrub resistance. The standard test was conducted in accordance with ASTM D2486 using a nylon brush and an abrasive medium that is passed a number of cycles to failure on a previously wetted coating in accordance with the test conditions. The test coating is conditioned on P121-10N panels for 7 days at a temperature of 23 °C ± 2 °C (73.5 °F ± 3.5 °F) and a relative humidity of 50% ± 5%. Scrub resistance was compared between Doses I and II as well as for individual coalescents. The test results are shown in Figure 11.
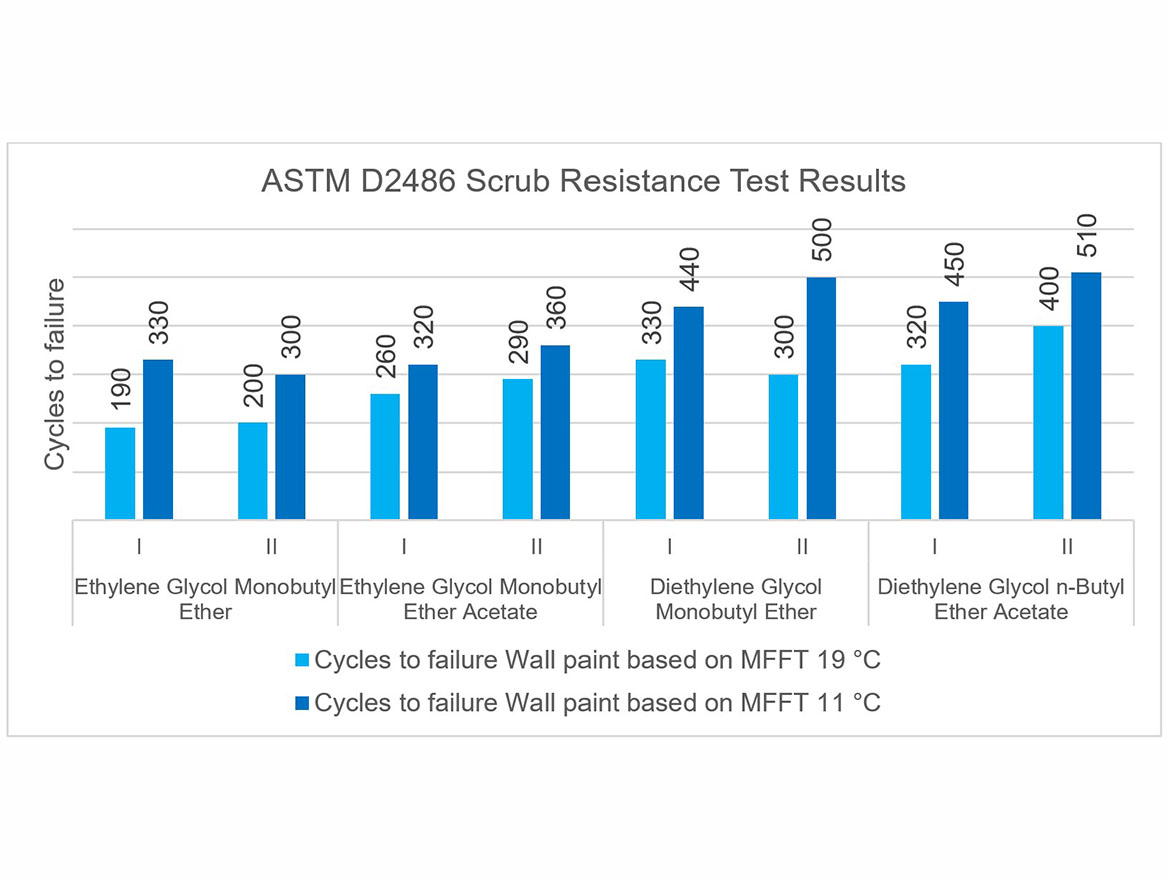
As can be seen in the scrubbability chart, the results for Doses I and II do not differ significantly, as their value is within the repeatability limit of the test method. However, a clear influence of the coalescents used in the tests on the results can be noticed, depending on the polymer dispersion in which they were used. The highest scrub resistance results were achieved by the coalescents diethylene glycol monobutyl ether and diethylene glycol n-butyl ether acetate used in flat paints with polymer dispersion MFFT 11 °C (52 °F).
These results show the relationship between the obtained scrub resistance and the type of dispersion (not necessarily with a higher MFFT, and therefore with an assumption of higher coating hardness due to the higher Tg), and the coalescent used for the formulation.
Pendulum Hardness
The development of coating hardness was determined as a pendulum damping test in accordance with ASTM D4366 using a fully automatic device with a König pendulum. Tests were performed on coatings conditioned at a temperature of 23 °C ± 2 °C (73.5 °F ± 3.5 °F) and a relative humidity of 50% ± 5%, 24 h after application on glass plates and 7 days after drawdown (using a 3-mil gap applicator). The tests were performed for gloss paints, and the results are presented in Figure 12.
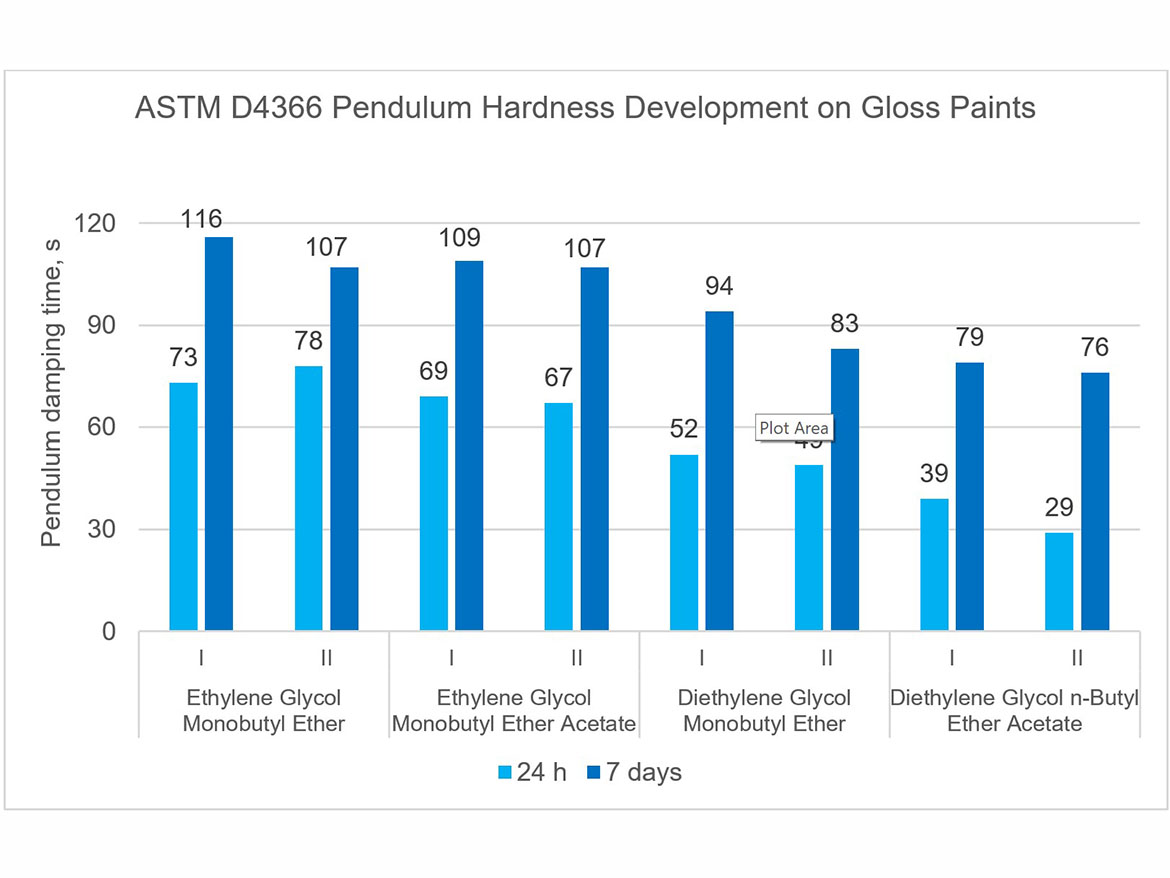
The presented graph clearly shows the development of the hardness of the coatings in the period between 24 hours and 7 days after the application of the coatings. It is also visible that the type of coalescent also influences the obtained pendulum damping time result. One can notice a clear influence of the boiling point of coalescing; the higher it is, the lower the initial hardness after 24 hours and after 7 days. Hardness development rates as shown in Figure 12 can be used to control the hardness of coatings and their rate of development, as well as to design architectural coatings that dry faster to withstand early rain.
Summary
The presented results show a comprehensive guide to the impact that 100%-VOC coalescents that are still present in the paint industry (such as glycol ethers and glycol ether acetates) have on the properties of coatings with different PVC based on various dispersions and for various applications. The presented compendium on them does not only apply to these types of coalescents, but is a guide to case studies that are performed for each type of coalescent, showing its effectiveness and potential areas of use where problems with coating formation processes may occur. The research results and application study procedures discussed here are universal and basic for conventional coalescents and green film-forming aids, the appropriate testing of which at the R&D stage and before introducing them to the market will allow for reduced problems and easier troubleshooting in the event of an occurrence.
The obtained results showed certain rules that can be carefully translated into miscibility with water, although, as shown, there are also cases in which these rules do not apply and are not related to miscibility with water. It should be remembered that the more extensive testing of a raw material at the R&D stage during its development or before introducing it to the market when it is ready, the less expensive it is to withdraw an additive that causes problems from the market.
References
1 Mischke, P. Film Formation, European Coatings Tech Files, 2010.
2 ASTM D2354-10(2018) Standard Test Method for Minimum Film Formation Temperature (MFFT) of Emulsion Vehicles.
3 Palasz, A. Water Miscibility Differences in Coalescing Agents and the Influence on Latex Paint Properties, PCI Magazine, 37, 2021.
Looking for a reprint of this article?
From high-res PDFs to custom plaques, order your copy today!