What is the best way to specify powder coating performance on steel substrates?

Our popular Ask Joe Powder blog has made its way to the pages of PCI magazine. What are your powder coating questions and challenges? Joe Powder, aka Kevin Biller of ChemQuest Powder Coating Research, shares his powder coating knowledge and expertise by answering questions sent in from around the world.
Hi Joe,
What is the best way to specify powder coating performance on steel substrates? With aluminum, I can use AAMA 2604. Is there something similar for steel?
Dennis L. Hacker
Columbus, Ohio
Hi Dennis,
Defining corrosive environments is a critical component in specifying and selecting the appropriate material to meet the rigors expected in the life of a coated product. Two specifications capture the requirements of a corrosion-resistant industrial coating, whether it is a powder coating or some other form of organic finishing.
ISO 12944-6 provides an excellent delineation of typical environments where corrosion occurs. Its categories span from C1 (essentially a dry indoor environment) to C5-M (highly corrosive coastal and marine conditions).
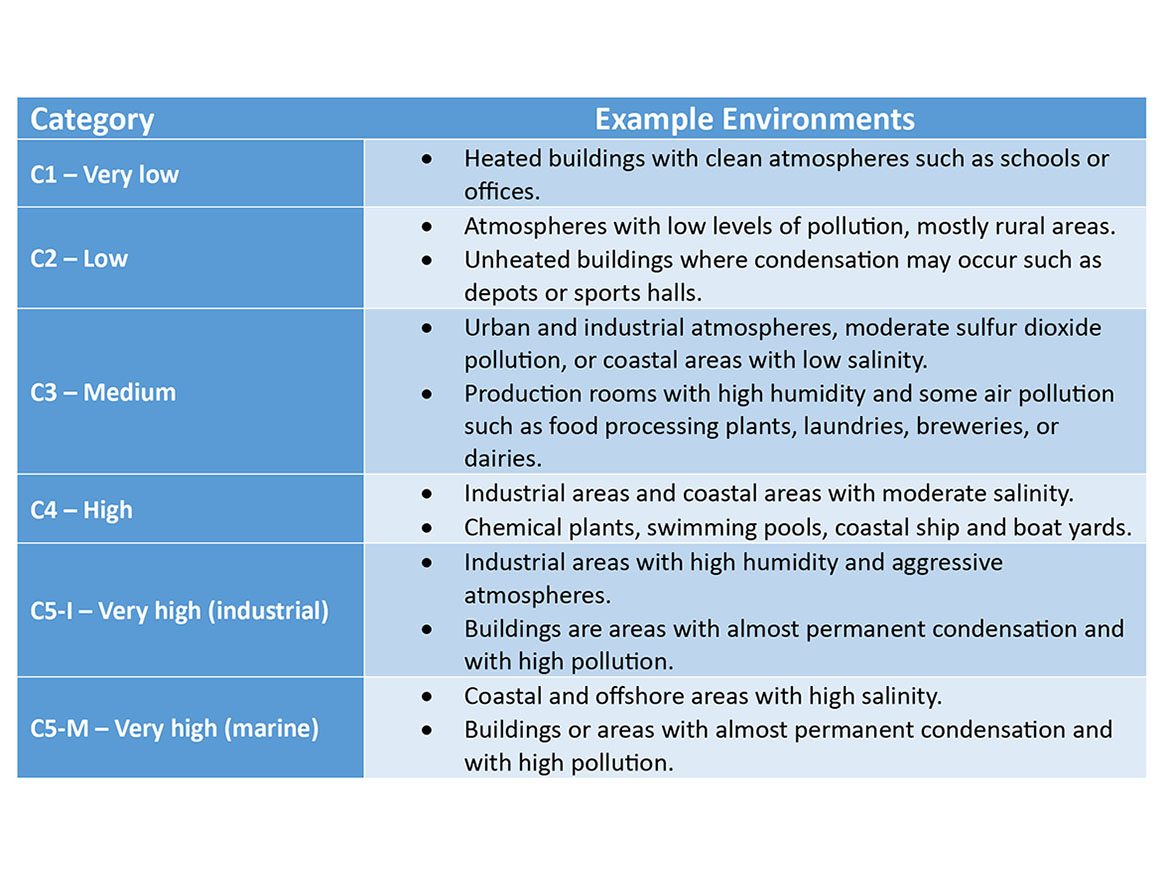
These categories are commonly specified in European and other overseas locations; however, the classes depicted in ISO-12944-6 are representative throughout the world.
Another useful corrosion-resistance specification is provided by the SSPC (Society for Protective Coatings), although its focus is the performance of exterior-grade liquid paints. The SSPC Paint Specification No. 36, “Two-Component Weatherable Aliphatic Polyurethane Topcoats,” delineates three levels of coating durability:
SSPC Environmental Zones
- 1A (interior, normally dry)
- 1B (exterior, normally dry)
- 2A (frequently wet by fresh water, excluding immersion)
- 2B (frequently wet by salt water, excluding immersion)
- 3B (chemical exposure, neutral)
- 3C (chemical exposure, alkaline)
Both resources are scant on any metal-preparation specifications beyond galvanizing, blasting, and the use of primers. Specifying chemical metal pre-treatment requires another guide, perhaps directly from a vendor of these products.
In addition, NAAMA (National Association of Architectural Metal Manufacturers) has published the “Metal Finishes Manual for Architectural and Metal Products.” This manual focuses on a variety of coating technologies, including powders. Powder and other organic coatings are described in Chapter 5. This is less a specification and more a thorough explanation of coating options and processes to finish a wide array of substrates, including various steel grades.
Some day, the industry will provide a comprehensive architectural specification for powder coating performance on ferrous metal surfaces. Perhaps we should join a committee at one of these associations and get to work on this.
Warm regards,
Joe
Hi Joe,
I have a question about the influence of acrylic-polyurethane wet paint on powder coating applications (polyester, epoxy-polyester, and epoxy). Since acrylic powders are a known contamination that can form craters, would we have a problem if we painted parts with acrylic-polyurethane wet paint near (approx. 30 meters) our powder paint installation?
Thank you in advance!
Ivan Cvetkovic
Serbia
Dear Ivan,
Thank you for your question. The answer is maybe. I have encountered contamination from liquid paint sprayed about 30 meters from a powder booth that caused crater defects in the finished coating. In this case, it was silicone paint that was sprayed into the environment near a powder spray operation. The paint mist would drift toward the air intake of the powder coating system and contaminate the spray booth air. This only happened when the liquid paint was sprayed on parts in a common area of the facility.
Whether a liquid acrylic urethane would do the same is unknown. I recommend that you obtain a sample of the liquid acrylic paint and conduct a test. Spray a fine mist of the paint onto a scrap part or test panel then apply a powder coating to it. Just use a light mist to simulate what could happen in the nearby environment. Cure the powder and observe the results.
If the acrylic-polyurethane paint contaminates the powder coating, then isolate your liquid spray area and filter the incoming air for the powder coating system.
I hope that this helps. Please let me know if you have any questions.
Best regards, Joe Powder
Do you have a question for Joe Powder? Email kbiller@chemquest.com. And be sure to listen to the Ask Joe Powder “Powdcast” for all the latest news, insights and technology in the powder coatings industry. Click here to listen!
Looking for a reprint of this article?
From high-res PDFs to custom plaques, order your copy today!